In the world of manufacturing and design, precision and versatility is paramount. Choosing the right cutting method can make all the difference in achieving the desired results efficiently and effectively. Laser cutting has slowly become the go-to solution for most businesses. However, it’s essential to explore how laser cutting stacks up against other cutting methods to make informed decisions for various applications.
This comprehensive guide simplifies the basics of laser cutting and compares it with a range of alternative cutting techniques.
I. Laser Cutting
Laser cutting is an advanced manufacturing technique that uses a powerful CNC (Computer Numerically Controlled) laser beam to melt and cut through materials. High-wattage laser cutters can quickly cut through thicker materials while maintaining high precision and accuracy.
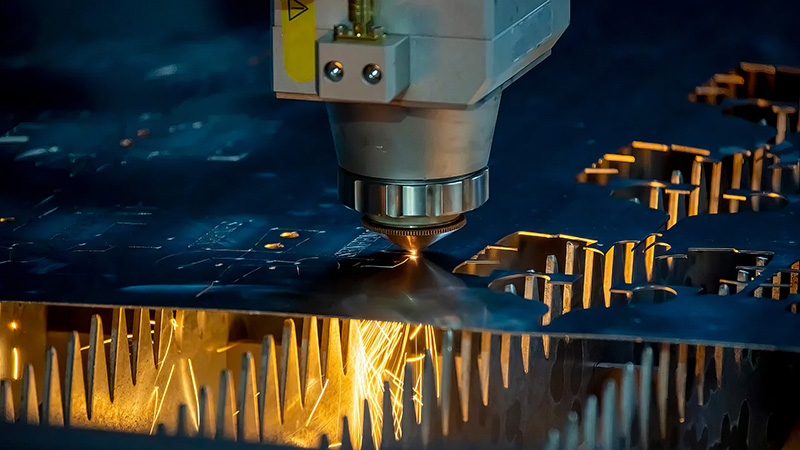
The entire laser cutting process is highly efficient compared to traditional methods. Electricity is converted into light through a gain medium, which is then amplified into a powerful laser. Laser beams input lots of heat into a small contact point on the workpiece for cutting, resulting in minimal energy waste.
Types of Laser Cutting Machines
The laser cutting machines can be categorized into several categories based on laser source and mode of operation.
1. Laser Source
- Gas Laser Cutting – Uses a tube of CO2 gas to generate and amplify the laser beam.
- Solid State Laser Cutting – Uses a crystal core for light amplification.
- Fiber Laser Cutting – Specialized solid-state cutting technique that uses optical fiber cables.
- Diode Laser Cutting – Uses semiconductors for light amplification.
2. Laser Cutting Processes
Various laser cutting processes help improve cutting efficacy for complex materials.
- Fusion Laser Cutting – Involves heating and melting of the metal material along the desired path. Uses an inert gas jet to blow away the molten material.
- Vaporization Laser Cutting – Uses high energy to vaporize non-metal materials. Uses a gas jet to blow away vaporized material.
- Remote Laser Cutting – A metal vaporization process that doesn’t require a gas jet.
- Oxygen Laser Cutting – Uses an oxygen gas jet with the laser beam for higher energy output, increasing laser depth penetration.
- Flame Laser Cutting – Uses an oxygen-acetylene gas mixture with the laser beam to generate a high-temperature concentrated flame for increased metal penetration.
- Zero Width Laser Cutting – Uses fiber lasers in short bursts to generate internal thermal stresses in brittle materials, resulting in micro-cracks along a desired path.
- Controlled Fracture Laser Cutting – Uses CO2 lasers to generate micro-cracks in brittle materials. Occasionally uses a fiber and CO2 laser together to achieve higher efficiency.
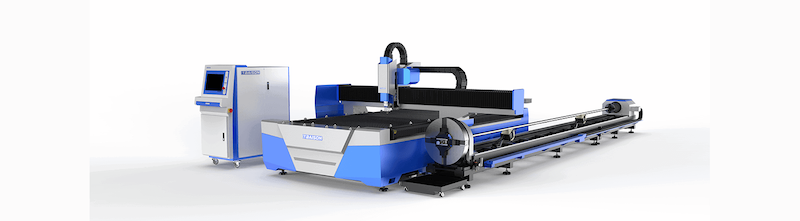
Material Compatibility
Perhaps the biggest advantage of laser cutting lies in the sheer amount of materials it can cut. Material thickness is also not an issue for modern laser cutting machines.
Here are all the materials laser cutters support.
- Metals – Carbon Steel/Mild Steel, Stainless Steel, Aluminum, Copper, Nickel, Titanium, and their Alloys.
- Woods – Hardwoods, Softwoods, and Engineered Wood (MDF, Fiberboard, Plywood, etc.)
- Plastics – Acrylic, Styrene, Nylon, Polypropylene (PP), Polyethylene (PE), and Polystyrene (PS).
- Textiles – Leather, Denim, Linen, Felt, Satin, Silk, Polyester, Cotton, and Fleece.
- Rubber – Natural Rubber, Silicone, Neoprene, and Latex.
- Foam – EVA Foam, Polyethylene Foam, Polyester Foam, and Polyurethane Foam.
- Paper – Paper (up to 150 g/m²), Cardboard, Corrugated Cardboard, Card Stock, and Foam Board.
- Ceramics – Glass, Tiles, Stone, Marble, and Granite.
While laser cutting plastic is a popular option, it should be noted that many plastics produce toxic fumes on melting. An initial investment into a fume hood or ventilation system is recommended for laser cutting plastic.
Benefits
The advantages of laser cutting are too many to list. So, we have highlighted some select ones that have the biggest impact on your business’ success.
- Highly Energy Efficiently Process
- Excellent Precision & Accuracy
- Faster Cutting Speed
- Wider Material Compatibility
- Can Cut through Thicker Materials
- Ease of Automation
- Zero Tool Wear
- Little Post-Processing Required

II. Plasma Cutting
The plasma cutting process uses a high-voltage electric arc to ionize a gas mixture (usually 35% hydrogen and 65% argon) which generates large amounts of heat. A gas jet keeps the plasma concentrated at the cutting point.
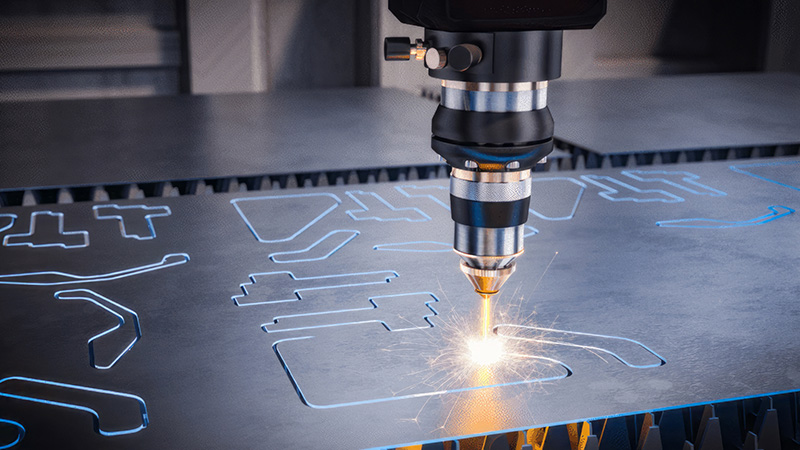
Plasma cutting is an incredibly hot process. As a point of comparison, the sun is a giant cosmic plasma sphere.
- Plasma Arc: 50,400 °F (28,000 °C)
- Electric Arc: 9,930 °F (5,500 °C)
- Gas Flame: 5,600 °F (3,100 °C)
- Laser Beam: >2,000 °F (>1,000 °C)
However, it should be noted that lasers can cut the same material thickness as plasma, without the need for such high temperatures.
Material Compatibility
Few materials can withstand the high temperatures of a plasma cutter. As such its material compatibility is limited to metals.
- Carbon steel
- Copper
- Aluminum
- Steel
- Iron
- Alloys
Benefits
Plasma cutting sits between the expensive fiber lasers and the low-cost CO2 ones. Offering a healthy middle balance of cost and performance.
- Cost Effective
- Fast Cutting Speed
- Material Thickness Compatibility up to 150mm
- CNC Automation
- Zero Tool Wear
Plasma cutting machines enjoy many of the benefits provided by CNC advancements.
As our topic shows, you can learn more about laser cutting vs. plasma cutting in detail here.
III. Water Jet Cutting
Water jet cutting is a unique material processing technique that uses abrasion to cut through materials. A mixture of water and abrasive material is shot out of a small nozzle at an incredibly high pressure (up to 60,000 psi). The water saws through the material with extreme precision and accuracy due to its computer-controlled cutting head.
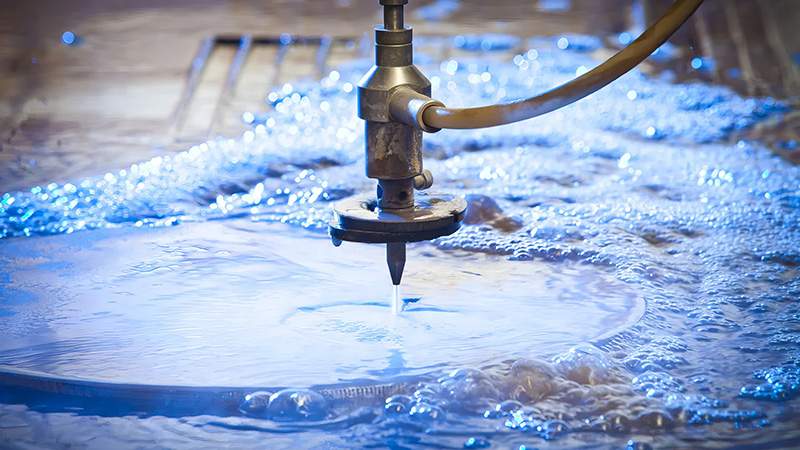
Waterjet cutting abrasive material options.
- Silicon Carbide
- Aluminum Oxide
- Sand
- Garnet
Material Compatibility
Water jet cutting has probably the highest material compatibility next to laser cutting.
- Metals – Aluminum, Brass, Carbon Steel, Copper, Stainless Steel, Tool Steel, and Titanium.
- Composites – Aero Fiber, Carbon Fiber, Fiberglass, and Kevlar.
- Plastics, Rubber, and Foam – As it is a cold-cutting process, all materials are compatible.
- Ceramics – Quartz, Granite, Marble, Cement, and Man-made Stone.
Benefits
Unlike other processes that use or generate heat that can damage materials, water cutting keeps the workpiece cool and safe.
- Wider Material Compatibility (even more than laser cutting)
- CNC Precision & Accuracy
- Fast Cutting Speed
- Excellent Material thickness Range (10-12 in. or 250-300 mm)
- Zero Tool Wear
- Little Post-Processing Required
I’m sure you’re also interested in the differences between laser cutting and water jet cutting.
IV. Die Cutting
Die cutting is a manufacturing process that cuts materials by pushing them through a custom-made template (die). It’s a cold-cutting process that is generally used for high-volume productions.
The die-cutting process can be manual, automatic, mechanical, or hydraulic.
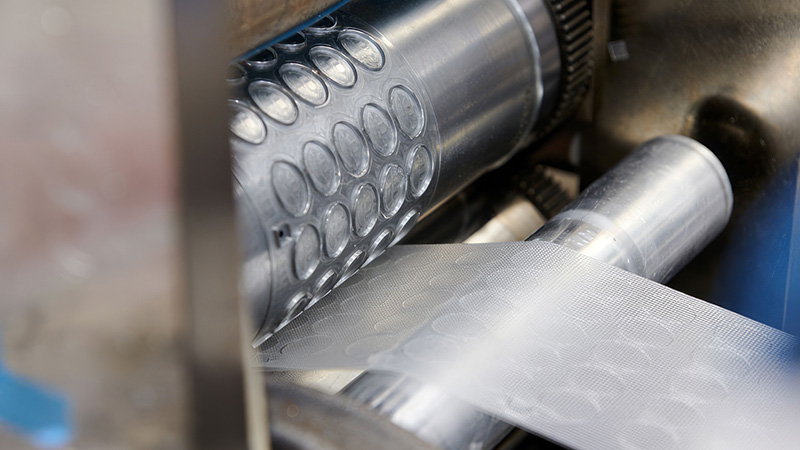
Material Compatibility
Here are some of the most popular materials machined by Die cutters.
- Paper
- Cardboard
- Plastics
- Textiles
- Metal (Thin Sheets)
Benefits
- Great for Mass Production
- Uniform Cuts
- Cost Effective
Our blog post on the difference between laser cutting and die cutting can help clear up the confusion.

V. Flame Cutting
Flame cutting, also known as gas cutting, is a thermal cutting method that ignites a gas mixture to generate a jet of hot flame. A mixture of oxygen and fuel (usually acetylene) is shot through a small nozzle and set aflame.
It is one of the few low-precision cutting methods on this list. Flame cutting is primarily limited to heavy-duty industrial applications where thick plates of metal need to be rough cut. It is a good alternative to plasma cutters if you don’t mind the loss in cutting precision.
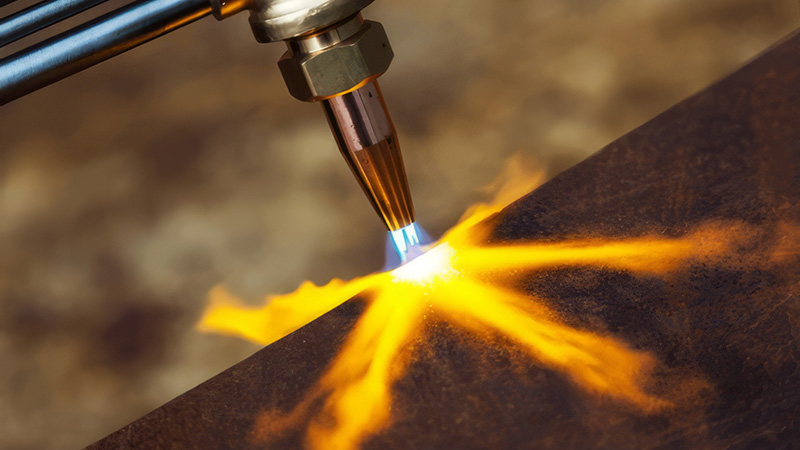
Flame cutting has several fuel options each with its own benefits and drawbacks.
- Acetylene
- Propane
- MAPP
- Propylene
- Natural Gas
Material Compatibility
Flame cutting is primarily limited to ferrous metals with low melting points.
- Carbon Steel
- Mild Steel
- Cast Iron
Benefits
Despite its shortcomings, flame cutting is still a popular option in the metal fabrication industry.
- Cost Effective
- Portable
- Excellent Thickness Range
Similarly, we have prepared an article on laser cutting vs. flame cutting.
VI. CNC Machining
CNC machining is a mechanical cutting process that uses a spinning metal tool to cut through materials. As it is a subtractive process, there isn’t a hard material thickness limitation. With enough vertical headroom, CNC mills can cut through several inches of thick metal.
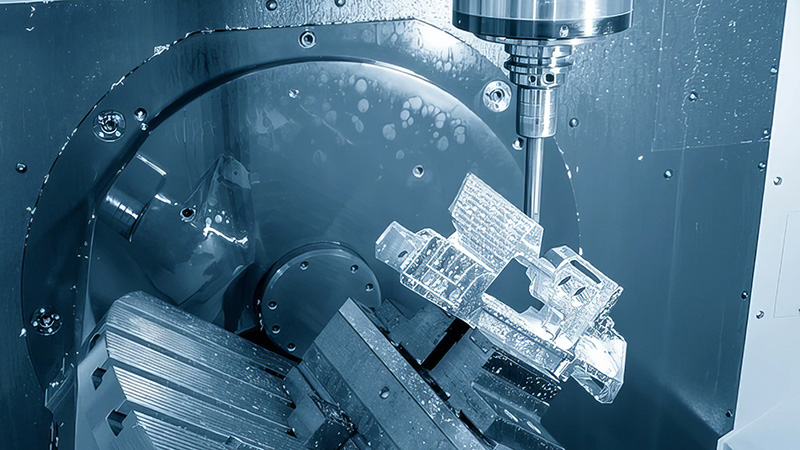
Types of CNC Cutting Machines
Laser cutting falls under the category of CNC cutting but for this section, we will be limiting this list to mechanical cutting only.
- CNC Milling – The workpiece stays stationary and the cutting tool is vertically mounted to a spindle.
- CNC Lathe – The workpiece is mounted to a spindle and the cutting tool is horizontally mounted to the carriage.
- Multi-Axis CNC Cutting – The spinning cutting tool is mounted on an adjustable gimbal similar to a robot arm.
Material Compatibility
CNC machining can cut through most rigid materials with ease. Unlike laser cutting, it is incompatible with soft materials like fabrics, rubber, paper, and sheet metal.
- Metals – Aluminum, Stainless Steel, Copper, Titanium, and their alloys.
- Woods – Hardwoods, Softwoods, and Engineered Wood (MDF, Fiberboard, Plywood, etc.)
- Plastics- Acrylics, Nylon, Nylon, HDPE, and PTFE.
Benefits
CNC machines paved path for the modern day manufacturing and played a pivotal role in its advancement. Here are its biggest plus points.
- High Precision & Accuracy
- Good Material Range
- Fast Processing Speed
- Little Post-Processing Required
Laser cutting machines versus CNC machines are certainly a hot topic in the industry right now.
VII. Saw Cutting
Saw cutting is a diverse range of cutting methods comprising hand and motor-operated options. A saw is a metal tool with a distinct teeth-like pattern on the cutting edge. The cutting style uses reciprocating motion, moving back and forth against the workpiece as it tears into the material.
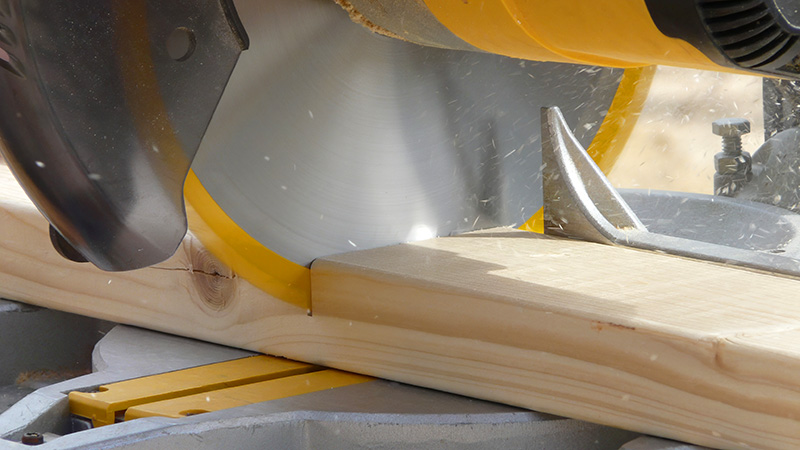
Here is a short list of the most popular saw-cutting tools.
- Hand Saw (Wood Saw)
- Hacksaw
- Circular Saw
- Table Saw
- Jigsaw
- Band Saw
- Scroll Saws
- Chainsaw
Material Compatibility
Unlike laser cutting which has near-universal cutting capabilities, sawing is mostly relegated to woodwork.
- Hardwoods
- Softwoods
- Engineered Wood (MDF, Fiberboard, Plywood, etc.)
- Stiff Rubber
- Plastics
- Some Softer Metals
Benefits
- Portability
- Low-Cost Cutting
- Electricity is Optional
Check out the detailed comparison guide between laser cutting and saw cutting here.
VIII. Punching
Punching is the process of pushing a metal cutter through the workpiece to get the desired shape. This cold-cutting technique is a small variation on die-cutting.
Die-cutting uses a metal template (die) and a piston (punch) to cut materials. Punching can occur without the need for a die. You can punch a metal sheet as long as it has some support structure underneath.
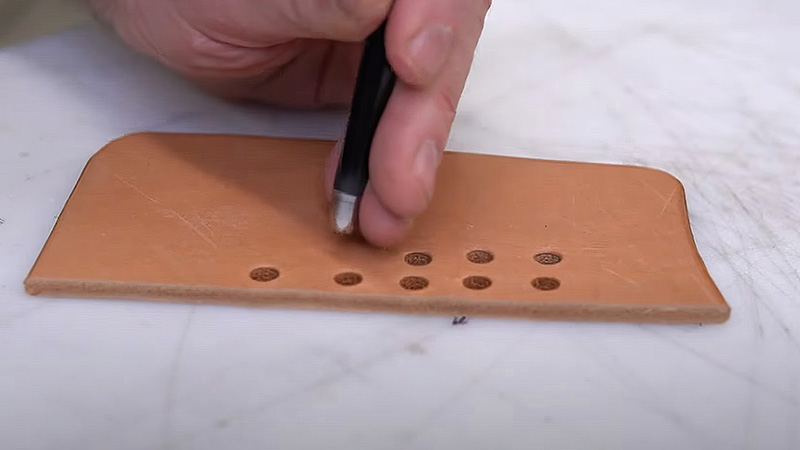
Manual punching involves hammering a metal punch through a flat surface, a technique very common in leather working.
Material Compatibility
Punching is generally limited to thinner materials.
- Thin Metal Sheets
- Fabrics
- Plastics
- Rubber
- Foam
- Paper
Benefits
- Very Low-Cost Cutting
- Versatile
- Good Scalability
- Can be used for Embossing
It is recommended that you read the article on punching vs. laser cutting in order to make a better choice.
IX. Ultrasonic Machining
Ultrasonic machining is an abrasion-based mechanical process. It uses piezoelectric transducers to vibrate the cutting tool at high frequencies (15-25 kHz). In this process, the workpiece is covered in a slurry of liquid and abrasive particles. As the cutting tool vibrates it pushes the slurry back and forth, sanding the material at the contact point.
Unlike a fiber laser cutter, where the area around the workpiece is also heated, ultrasonic machining only heats a small section of the surface.
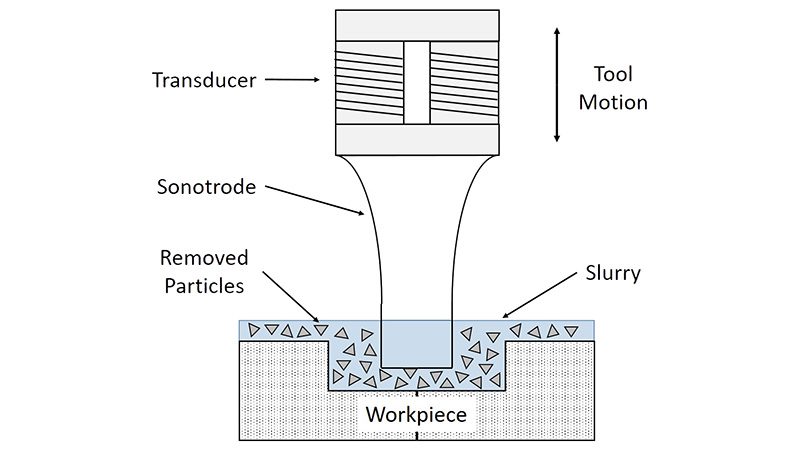
Material Compatibility
A big drawback of ultrasonic cutting is its limited material removal rate. However, it has one big advantage over the competition, it can cut through the hardest materials with ease. So while a laser cutter is an all-purpose machine with near-universal material compatibility, ultrasonic machining is limited to brittle and high-hardness substances.
- Ceramics
- Carbides
- Glass
- Precious Stones
- Hardened Steels
Benefits
Ultrasonic cutters cover an important section of manufacturing not fulfilled by laser cutting machines which is processing brittle materials.
- Can Process Hard Materials
- Negligible Heat Generation
- Minimal Tool Wear
- No Post-Processing Required
After learning the basic information, you may want to know the difference between laser cutting and ultrasonic cutting.

X. EDM
EDM (Electric Discharge Machining) is an innovative metal processing technique that uses an electrically charged metal wire to remove material. A thin wire made of special steel alloys is connected to two electrodes. As the current flows through the wire, electric sparks jump from the wire to the metal workpiece.
These sparks have a momentary temperature of 21,600°F (~12,000°C). The electric spark erodes the workpiece on an atomic level. The workpiece and the wire are submerged in a dielectric solution (non-conductive liquid) to prevent the spark from jumping to unwanted atoms in the air.
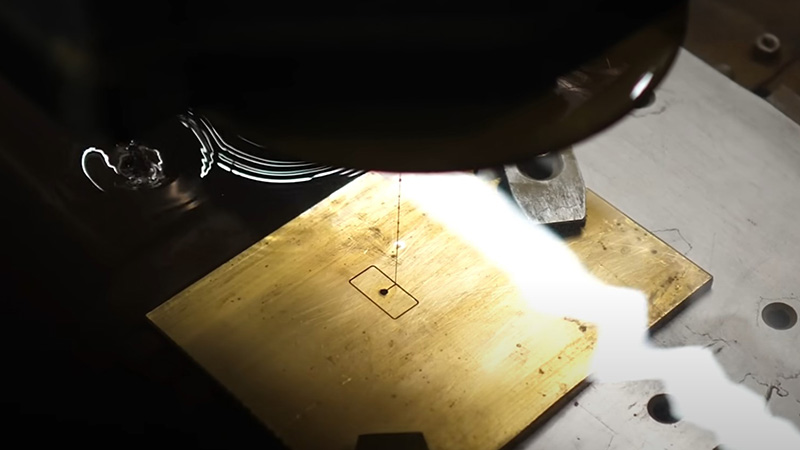
A big advantage wire EDM has over laser cutting is precision. While laser cutting machines are known for their excellent cutting tolerances, EDM is over ten times more precise.
- Laser Cutting Precision – 0.01″ (0.25 mm).
- Wire EDM Precision – 0.0002″ (0.005 mm).
Material Compatibility
Wire EDM is compatible with all conductive substances, including non-metals like graphite.
Metals
- Steel
- Stainless Steel
- Aluminum
- Brass
- Copper
- Titanium
Non-Metals
- Graphite
- Semiconductors (Silicone, Gallium, Arsenide, etc.)
Benefits
- Extremely Fine Machining Tolerances
- High Cutting Speed
- Decent Material Compatibility
- Enables More Complex Cutting Methods
- Zero Tool Wear
- Little Post-Processing Required
This is a detailed comparison guide between EDM and laser cutting.
XI. Metal Stamping
Metal stamping is one of the most common sheet metal cutting methods. It relies on a continuous feed of sheet metal and high-speed punches to stamp-cut basic shapes. Unlike other cutting techniques on this list, metal stamping is also capable of bending and forming flat metal sheets into 3D designs.
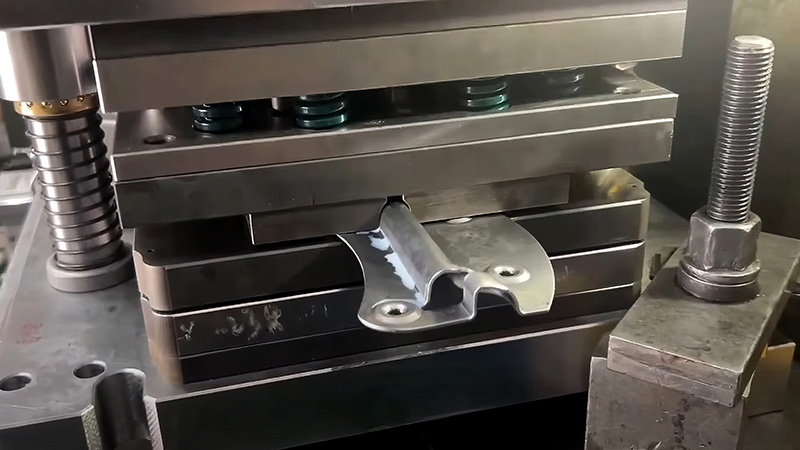
Sheet metal fabrication using stamping is an expensive process, due to the initial investment in dies and punches. However, the process becomes more cost-effective as the number of parts increases. Laser cutters are still the go-to solution for small-volume production.
Material Compatibility
- Steel
- Aluminum
- Copper
- Brass
Benefits
The advantages of metal stamping are many. So, we have highlighted some select ones that have the biggest impact on your business’ success.
- Energy Efficiently Process
- Fast Cutting Speed
- Low Cost Per Unit
We have also prepared a detailed comparison guide between metal stamping and laser cutting.
XII. 3D Printing
3D printing (or Additive Manufacturing) is a highly efficient manufacturing technique that builds parts by fusing layers of material. The most popular 3D printers use a roll of plastic filament wire that is melted and shot through a CNC nozzle onto a heated work bed.
As the molten plastic exits the nozzle it cools down to a solid state. Then another layer is built on top of the first one. This process repeats until a complete shape is produced.
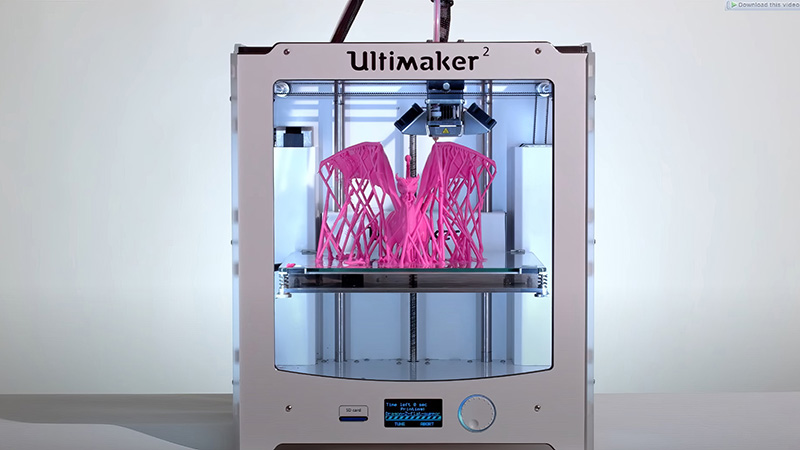
In comparison, a laser cutter is a subtractive manufacturing process that removes material from a base metal to reveal a final shape.
Material Compatibility
Most 3D printers use plastic filament or a resin that hardens under UV light. However, some advanced machines use metal powder.
Here are some of the most popular materials used in the 3D printing process.
- Plastics – ABS, PLA, PETG, Nylon, TPU, PVA, and HIPS.
- Resins – Clear, Flexible, Heat-Resistant, Dental, etc.
- Metals – Steel, Aluminum, Stainless Steel, Copper, Cobalt, Tungsten, Titanium, Nickel, and, their alloys.
Benefits
- No Material Waste
- Rapid Prototyping Capabilities
- Enables More Complex Designs
- Wider Material Compatibility
The choice of laser cutter and 3D printer is also a problem that plagues many companies.
XIII. Blade Cutting (CNC)
CNC Blade cutting is a slightly different type of machining process. It uses a 3-axis cutting head similar to a milling machine. The most popular type of blade-cutting machine is the Cricut Cutter, a hobbyist arts and crafts machine. It is commonly used for cutting, marking, engraving, and debossing fabric, stickers, foam board crafts, etc.
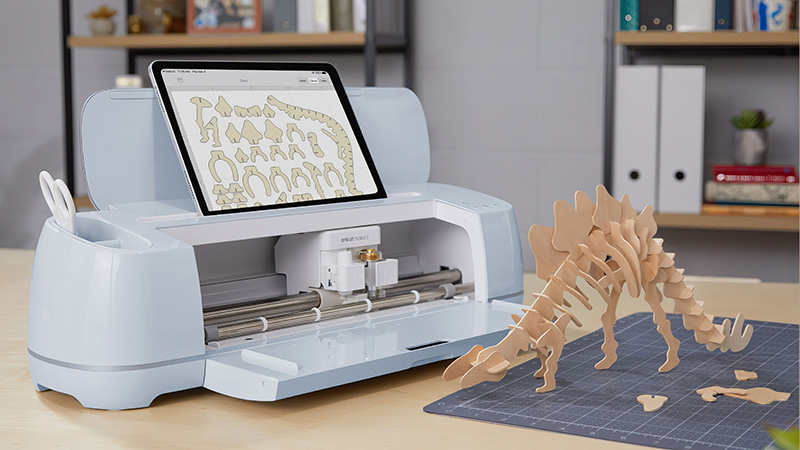
Material Compatibility
You can only cut thin non-metal sheets using these hobbyist machines.
- Paper
- Cardstock
- Fabrics
- Leather
- Thin Foam
- Vinyl
- etc.
Benefits
- Very Low-Cost
- Decent Precision & Accuracy
- Easy to Use

Comparison List of Different Cutting Methods
The various cutting methods discussed above offer a unique solution to a unique problem. Saws are excellent for woodwork, EDM is great for microscopic precision, ultrasonic machining can deal with hard and brittle materials, and so on.
In contrast, a laser cutter is designed to give you the most broad set of features. It can cut, mark, and engrave metals and non-metals, thicker materials, soft foams, stretchy rubber, etc. The best part is laser cutting can do all this and more at a relatively small price premium over other cost-effective solutions.
Table 1 - Comparing the Laser Cutting Process to Other Cutting Methods
CuttingMethod | Speed | Precision | ThicknessLimitation | CompatibleMaterials | InitialInvestment |
---|---|---|---|---|---|
Laser Cutting | Very Fast | Very High | 0.25"(6 mm) | Metal, Alloys, Woods, Plastics, Textiles, Rubber, Foam, Paper, and Ceramics | Low to High |
Plasma Cutting | Very Fast | High | 2.0"(50 mm) | Carbon Steel, Copper, Aluminum, Steel, Iron, and Alloys | High |
Water Jet Cutting | Slow | Very High | 10-12"(250-300 mm) | Metals, Alloys, Composites, Plastics, Rubber, Foam, and Ceramics | High |
Die Cutting | Medium | Medium | 0.50"(12 mm) | Paper, Cardboard, Plastics, Textiles, and Metal (Thin Sheets) | Medium |
Flame Cutting | Very Fast | Low | 10.5"(270 mm) | Carbon Steel, Mild Steel, and Cast Iron | Very Low |
CNC Machining | Fast | Very High | Determied byCutting Tool | Metal, Alloys, Woods, and Plastics | Medium |
Saw Cutting | Medium | Low | Determied bySaw Diameter | Hardwoods, Softwoods, MDF, Fiberboard, Plywood, Stiff Rubber, Plastics, etc. | Low |
Punching | Medium | Medium | 0.20"(5 mm) | Thin Metal Sheets, Fabrics, Plastics, Rubber, Foam, and Paper | Very High |
Ultrasonic Machining | Slow | Very High | Determined byTool | Ceramics, Carbides, Glass, Precious Stones, and Hardened Steels | Very High |
EDM | Slow | Very High | Determined byTool Size/Wire Length | Steel, Stainless Steel, Aluminum, Brass, Copper, Titanium, Graphite, and Semiconductors | Very High |
Metal Stamping | Fast | Medium | 0.625"(16 mm) | Steel, Aluminum, Copper, and Brass | High |
3D Printing | Very Slow | Medium | Manufacturing Height is Determined by the Printer Height | Plastics, Resins, and Metals | Low to High |
Blade Cutting | Fast | High | 0.09"(2.4 mm) | Paper, Cardstock, Fabrics, Leather, Thin Foam, and Vinyl | Very Low |
Although a quick comparison table showcasing the properties of various cutting processes next to laser cutting is convenient it doesn’t paint the full picture.
For a more accurate look at all the benefits a laser cutter offers. We have to make a more direct comparison of properties.
Table 2- The Advantages and Disadvantages of Laser Cutting over Other Processes
CuttingMethod | AdvantagesOver Laser Cutting | DisadvantagesOver Laser Cutting |
---|---|---|
Plasma Cutting | Compatible with thicker metal plates. | Incompatible with non-metals. Lower precision. Required post processing. |
Water Jet Cutting | Better edge finish.Compatible with brittle materials. | More expensive. Limited material compatibility. High water consumption. |
Die Cutting | Lower per-piece costFaster mass production | Expensive at small volumes. Limited mateiral compatibility. Struggles with thicker materials. Lower precision. |
Flame Cutting | PortabilityConvenientLower equipment and operation cost | Incompatible with non-metals. Lower precision. |
CNC Machining | No limit to material thickness. | Limited material compatibility. |
Saw Cutting | PortabilityConvenientLower equipment and operation cost | Very limited material compatibility Lower precision. |
Punching | Lower per-piece costFaster mass production | Expensive at small volumes. Limited mateiral compatibility. Struggles with thicker materials. Lower precision. |
Ultrasonic Machining | Better at cutting ceramics.Minimal heat generation | Limited metal compatibility. Slower cutting speed. |
EDM | Higher precision.Better depth penetration | Limited to metals. Higher equipment cost. Slower cutting speed. |
Metal Stamping | Lower per-piece costFaster mass production | Limited material compatibility. Lower precision. Limited to simple designs |
3D Printing | Enables more complex designs.Minimal material waste | Much slower manufacturing speed. Lower manufacturing precision. Metal printing is extremely expensive. |
Blade Cutting | Easy to use.Lower equipment cost. | Very limited material compatibility. Limited to very thin sheets. Lower precision. |
Conclusion
Manufacturing techniques have matured significantly over the last two decades, partly due to the advancements in computer technology and material science. There is an ideal cutting method that best suits your application, budget, and creativity. Laser cutting offers a complete package that has a little bit of everything, precision, cutting speed, convenience, scalability, and cost savings.
Cut Through the Competition with Baison Laser!
Baison is the premier manufacturer and supplier of fiber laser machines. Our state-of-the-art fiber laser machines are designed with the utmost care and diligence. We offer laser cutters that are built to last and operate with incredible precision and stability, all while being price competitive.
Our FREE Application Evaluation program is designed to help customers get the most out of their laser cutter. Connect with our team of experts for a crash course on laser cutting.
Elevate your production to a whole new level with Baison. Contact Us Now!