Here I have shared practical tips for laser cutting mild steel that can improve your machining process and overcome the previously faced challenges by machinists. Let’s get started.
What Are the Different Types of Mild Steel?
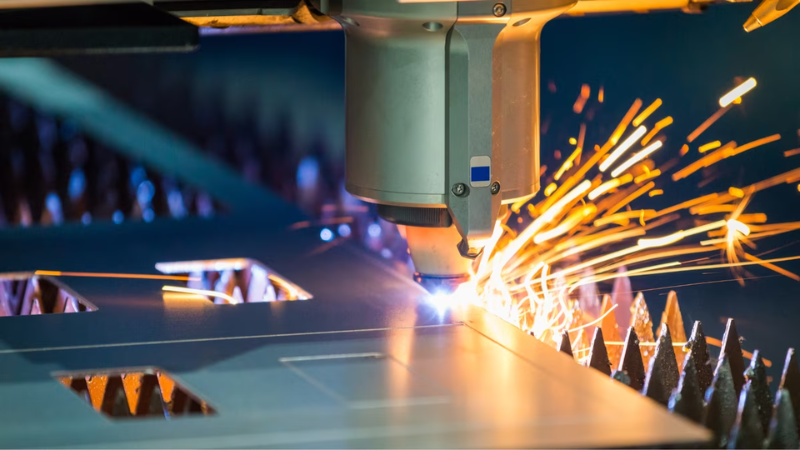
Mild steel is simply a type of carbon steel with the lowest carbon content. Typically, it has 0.04 – 3 percent by weight of carbon content which gives it unique properties. According to the American Iron and Steel Institute (AISI), other elements like chromium, cobalt, manganese, copper, silicon, etc., can be added to attain suitable properties of mild steel.
Mild steel is low-cost, thanks to modern manufacturing techniques, and you’ll find its use in almost all general engineering industries. Moreover, there are many grades or types of mild steel. Some are presented in this table.
Mild Steel Grade (AISI) | Composition (wt %) | Uses |
1010 | 0.1 C, 0.45 Mn | Automobile Parts. |
1020 | 0.2 C, 0.45 Mn | Sheet metal, Pipes. |
A36 | 0.29 C, 1.00 Mn, 0.2 Cu | Architecture, Bridges, Ships |
A516 | 0.31 C, 1.00 Mn, 0.25 Si | Pressure Vessel |
A440 | 0.28 C, 1.35 Mn | Knife, Blades |
A633 | 0.22 C, 1.35 Mn | Boiler, Chemical Industry |
S275 | 0.17 C, 1.02 Mn, 0.21 Si | Bridges, Buildings |
S355 | 0.16 C,1.3 Mn, 0.2 Si, 0.04Cu | Construction,n Offshore Industry |
Benefits of Laser Cutting Mild Steel
Laser-cutting technology has improved the mild steel machining process manifolds. Here are some key benefits.
Speed and Flexibility
Fiber and CO2 laser machines provide unparallel speed. These machines have a fast rail and gantry system, which is controlled by computer numeric control (CNC). Since there are no physical cutting tools involved, the movement is swift. Amazingly, laser machines are compatible with a vast range of metals. This flexibility allows you to process different grades of steel with minor adjustments.
High Precision
Laser beams, by default, are really precise. It’s an amplified light beam that melts and evaporates metals precisely. Since this is thermal cutting, you won’t have to be concerned with chip formation and rough edges.
Laser machining is so precise that it can achieve a tolerance of +-0.003 mm to 0.006 mm. In comparison, the precision of traditional methods lies within the range of +-0.015 mm to 3 mm.
Complex Jobs
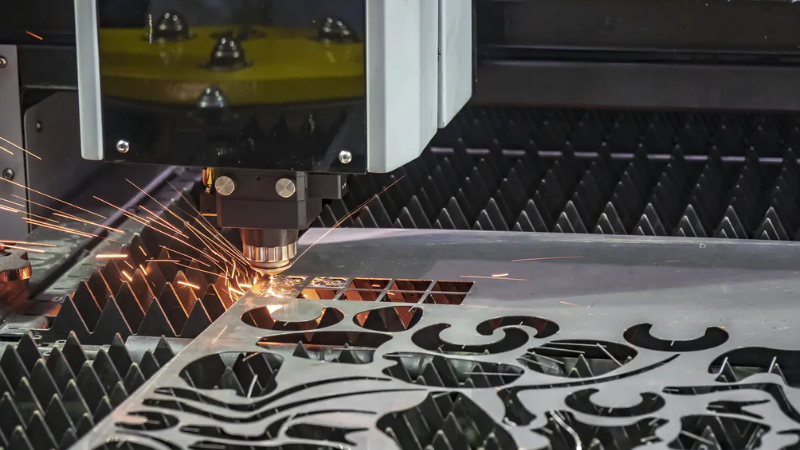
High precision enables the operators to perform complex and intricate jobs using mild steel. This brings better accuracy to the machining process while controlling the cost. Metal laser cutting helps make prototypes and test parts much faster than traditional cutters.
In olden times, complex geometries needed greater tool adjustment and a higher operator skill level. But it all changed with laser technology which can be easily adjusted with a press of a button.
Less Energy Consumption
Laser machines consume less energy than traditional cutters. Part of it is due to the lack of moving parts in machinery. As a result, losses in friction, heat, and vibrations are close to zero. There is also significantly less chip formation and wastage when mild steel is cut with lasers. So, fewer resources are used in cleaning and recycling the waste material. Overall, the laser cutting process is eco-friendly and sustainable.
Automation
Automation is where laser cutting truly shines. They are equipped with a software-based control system. As a result, these machines can operate automatically with minimum supervision.
There are several types of automation in laser technology. First is two-dimensional cutting using a gantry system. It’s fast and effective. Mild steel sheets are fed automatically, and the movement laser cutter is controlled.
Second is the use of Robotic Arms. These arms can weld or cut in three-dimensional space.
Damage Control
Experts say that laser cutting causes the least damage to the material out of all thermal cutting processes. Because even if the temperature of the laser beam rises to several thousand degrees, the point of contact is still narrow. Also, this doesn’t cause wrapping and distortion in the material.
The cuts are also of high quality, which reduces damage and saves a lot of revenue in the large-scale production of mild steel.
Since the cutting tool has no wear and tear, overall damage is minimized, reducing the operational cost.
Why Is the Process of Laser Cutting Mild Steel Challenging?
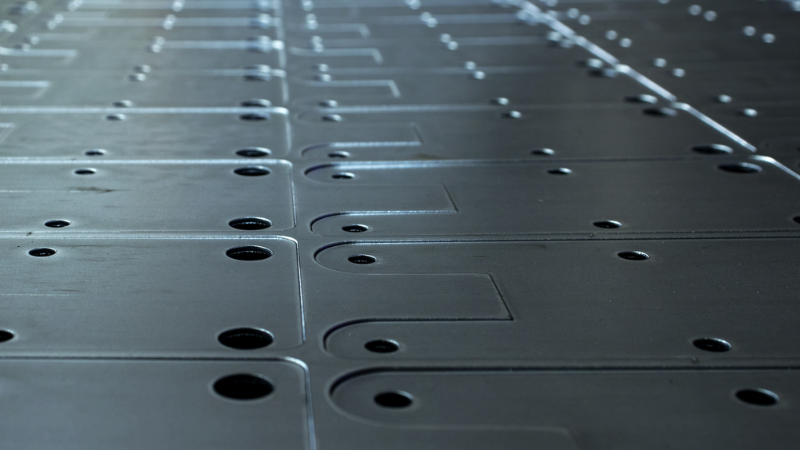
Mild steel is excellent for various machining processes and is widely used in daily life. It has applications in nearly every manufacturing sector. But some challenges come with its superior material properties.
Material Ductility
Mild steel has the lowest carbon content of any other type of steel. It makes the material extremely ductile, even more so than rubber. Low-carbon steel is also less brittle, which prevents fractures.
However, this has a side effect. It leads to long chip formation in the traditional cutting process. Not so much in laser cutting, though, as laser evaporates the metal. But still, the long chip can disrupt the machining process. To control this feed rate, depth of cut, cutting speed, and other parameters are re-adjusted.
Edge Build Up
Similarly, the edges build up during the machining process due to high ductility. It can easily damage the tool. Edge build-up also translates to poor kerf quality.
You might have to increase the maintenance frequency, which will lead to unnecessary stoppage of the process.
The edge build is also a hindrance in the automation process. Adjusting the insert, tool bit, and feed rate would fix the problem in traditional processes. Fortunately, with thermal cutting, this effect is reduced. So, laser cutting is less prone to this.
High Temperature and Vibrations
Laser cutting is a thermal process that can create high temperatures at the cut edge. In addition, laser cutting of mild steel with oxygen tends to burn the edges excessively. To counter that operator needs to select the laser power and assist gas pressure carefully.
Steel has higher strength than other metals, which means it’s more prone to vibrations during the machining process. In traditional milling and lath cutting, these vibrations affect the quality of the job.
However, in fiber laser cutting, these vibrations are due to the laser head’s and other components’ inherent play. Poor quality laser machines may cause saw tooth pattern in the edge cut.
Tips On Getting the Best Results When Laser Cutting Mild Steel Parts
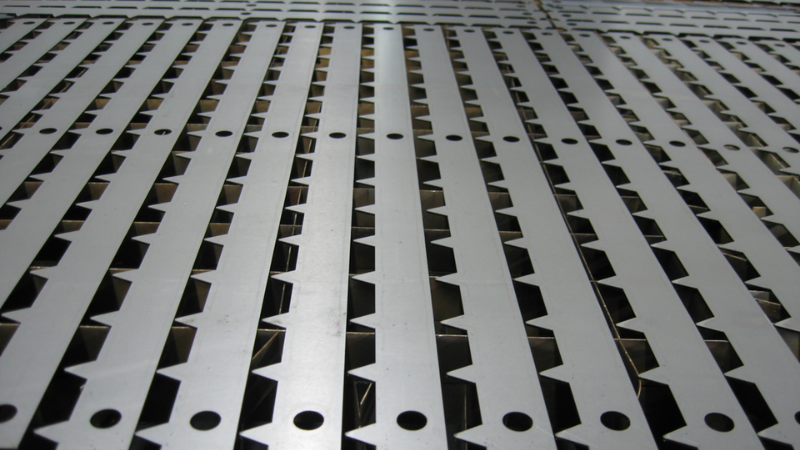
1. Design Criteria
Every project must have a solid base design. Fiber laser machines use design instructions in .dwg or .dxf file format. Clear instructions in the design phase may lead to faster operations and reduce the risk of damage to the material.
Since laser machines follow 2D vectors, make sure the lines are not disjointed. Close all the edges. Ensure the notch width is at least 1 mm of the thickness and away from the corner of the metal plate. This way, the integrity of the metal plate remains intact.
Fillets are encouraged instead of sharp edges as it reduces stress concentration. Typically, the fillet radius should be half the size of the thickness.
Suppose you have multiple interior and exterior features to cut in a single mild steel plate. Properly space them in place so that the quality remains intact. If two features are too close to each other, the laser might burn the edge between two features.
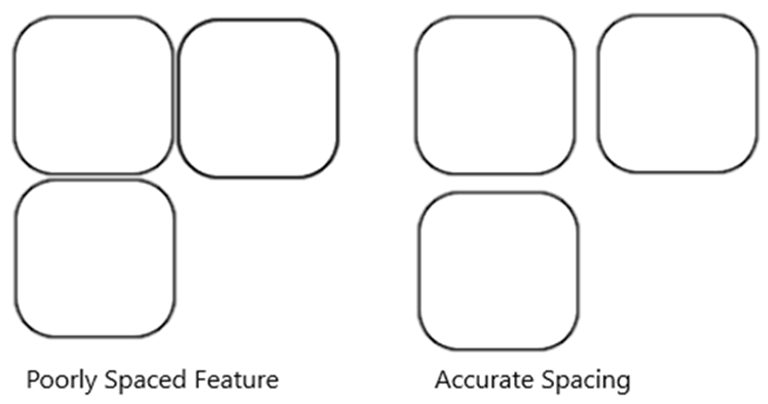
2. Surface Cleaning
As we know, mild steel has different grades, which means their properties differ. Some grades are less corrosion-resistant than others. As a result, rust and scale can build up on the surface of the metal. Even the smallest layer can negatively affect cutting quality. Make sure to clean the mild steel plate before the process properly.
3. Selecting Laser Power
Laser power is the most important parameter in laser cutting. Typical power outputs of laser machines are 1.5 KW, 2 KW, 3 KW, and 6 KW.
Laser power dictates the maximum thickness of mild steel plate you can cut. The best approach is the look into guidelines given by the machine manufacturer. That way, you’ll avoid unnecessary damage.
Fiber lasers need less power than CO2 lasers to cut the same depth considering all the other parameters remain the same. This is because fiber lasers have a higher absorption rate.
4. Damage Inspection
If your machine is running continuously for some days, it’s recommended to inspect any prior damage to the laser machine component before you start another job. The laser lens, nozzle, torch, gas flow, etc., are mainly prone to damage. Sometimes debris gets stuck in the laser and can affect the cutting performance.
5. Adjust Cut Setting
Mild steel cut settings include power output, cut speed, pierce setting, gas selection, pressure, etc. Adjust these according to the guidelines by the manufacturer for the specific grade of mild steel.
Piercing is the first and most important step, as it will set the right tone for the rest of the cutting.
Make certain you use only recommended power settings because higher intensity can leave burn marks on the material. It’s known through observation that from 1 mm to 4 mm, a laser with oxygen can create good pierce. But for thicker mild steel like 8 mm, compressed air is much more suitable for piercing through mild steel.
Piercing is done on the cut line if the diameter of the hole matches the line width. Otherwise, it’s done on the inner side of the cut line.
6. Right Gas Selection
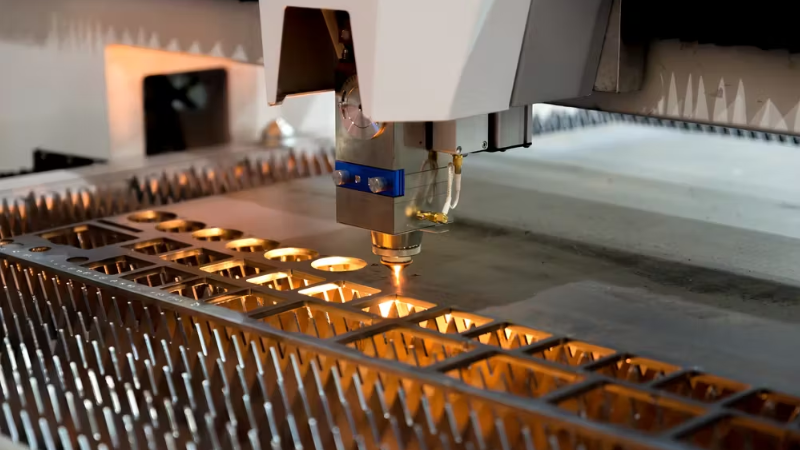
You must consider the assist gas selection, pressure, and flow rate. For mild steel, oxygen is most compatible. However, nitrogen and compressed air are also used in some cases.
Mild steel requires lower power and gas pressure settings for the same thickness compared to other types of steel. Surprisingly, the cutting speed is also higher for mild steel. Make sure you keep this in mind while selecting the gas parameters.
Oxygen produces a wider pierce hole than nitrogen. Moreover, research shows nitrogen can be used instead for piercing, and later the cutting can be continued using oxygen. With this combination, piercing can be done on the cut line, reducing material wastage.
Another research shows the optimum conditions for oxygen laser cutting of mild steel for different thicknesses.
Thickness (mm) | Average width (mm) | Power (W) | Cutting Rate (mm/s) | O2 pressure (bar) |
1 | 0.3 | 67 | 9.5 | 1 |
1.5 | 0.35 | 97 | 9.5 | 1 |
2 | 0.3 | 123 | 7.1 | 2 |
If you want to learn more about assist gases and their selection, read the article “Which Gas Is Best for Laser Cutting?- An Easy to Follow Guide.“
7. Calibrating the Nozzle
A laser beam flows through a copper nozzle in a standard laser machine. However, if the nozzle is miss aligned, the laser will get an obstruction. This is known as beam clipping. Therefore, always align the laser beam to minimize losses in cutting mild steel.
Another factor is the focal position of the laser beam. For mild steel, you have to set focus on the surface of the material. The height of the laser nozzle varies with material thickness and type of material. Ideally, the nozzle should be 0.2 mm – 0.5 mm away from the material surface.
8. Cutting Speed
Cutting speed is a crucial parameter in controlling the quality of the process. The most common issue with mild steel is the striation effect on the kerf edge, which is mostly related to the cutting speed.
Striation is the parallel lines and grooves that are formed during cutting. It increases the surface roughness and adversely affects the finish of the cut. Later on, it may pose a problem in welding as well.
Researches show a critical cutting speed at which the striation effect is minimal during oxygen laser cutting of mild steel.
Start by gradually increasing the cutting speed until you reach striation-free optimal speed. Then, maintain this speed for the rest of the job. Moreover, the machine should have at least 1KW output or higher.
9. Minimizing Heat Affected Zone (HAZ)
Uneven heat dissipation can cause defects in the material during fiber laser cutting. It’s especially true for mild steel. These zones originate where the heat doesn’t melt the material but is hot enough to change the microstructure.
It can pose all sorts of problems, such as reduced fatigue resistance, early fractures, and distortion. The right selection of assist gas also decreases the HAZ as it cools the surface.
The two most significant factors that affect the HAZ are cutting power and speed.
The rule of thumb is that HAZ can be minimized by increasing the laser cutting speed and decreasing the laser power. However, it’s not that simple. Higher cutting speed may also create greater surface roughness. So you have to balance the critical speed.
10. Create a Test Part
Nailing the fiber laser cutting setting on the first attempt is hard. Sure, you can achieve a base level of success, but you need to create test parts for higher quality. These are the prototype of the actual job. If you have to complete an order of hundred pieces, you first make a few test parts to get the ideal laser parameters.
11. Examine the Cut Part
The pattern on a cut edge can tell a lot about the deficiency in the laser machine settings. Ideally, a perfect balance of power, speed, and gas flow is key to a smooth cut edge. So start with a test cut and examine it visually.
Follow the recommended settings by the manufacturer. Optimize the cut settings by increasing or decreasing the feed rate, gas pressure, and power in small increments. Here are some of the defects to look out for.
Cut Defects | Possible Reasons |
Higher heat affected zone. | Power is too much. |
Narrow Kerf with oxidation at the bottom. Excessive dross at the lower cut edge | Low focal point, High Cutting Speed, Low gas pressure (oxygen), Small nozzle size. |
Wider Kerf, striation effect, greater roughness, burned edges. | Higher focal point, Higher gas pressure (oxygen), slow cutting speed, faulty nozzle. |
Concluding Thoughts
The aforementioned helpful tips are bound to increase your productivity and efficiency. Low-carbon steel or mild steel is the most common machining material you will come across. Knowing the right strategies can drastically improve the quality and production rate. This will help you generate larger profits and success. These tips apply to Fiber laser and CO2 laser machines alike.
Baison Laser Provides the Best solution for Mild Steel Laser Cutting
Creating the highest quality product usually depends on premium quality machinery and a skillful operator. At Baison Laser, we manufacture high-tech laser machines in our advanced production facility.
Our fiber laser and CO2 laser machines are equipped with superior-quality components, making the machining process much more efficient. You can browse through our vast catalog. We have laser cutting, welding, marking, and cleaning systems at market-competitive prices.
Moreover, our experts are ready to customize the order according to your project. You can have a free evaluation of your project and order free sample proofing as well.
So what are you waiting for? Let’s collaborate.