Laser cutters and exhaust systems are inseparable. A top-notch exhaust system isn’t just vital for worker safety; it also enhances cutting efficiency and extends machine lifespan.
Yet, many business owners grapple with creating an effective exhaust setup. To assist, we’ve compiled a comprehensive guide on laser cutter exhaust systems. Let’s dive in!
What Is a Laser Cutter Exhaust System?
Laser cutters are versatile machines that can perform cutting, engraving, and marking processes. However, they produce toxic fumes, smoke, and particulates as a by-product due to the burning of the material. Laser cutter exhaust systems extract and expel these toxic fumes responsibly, keeping the workers and environment safe.
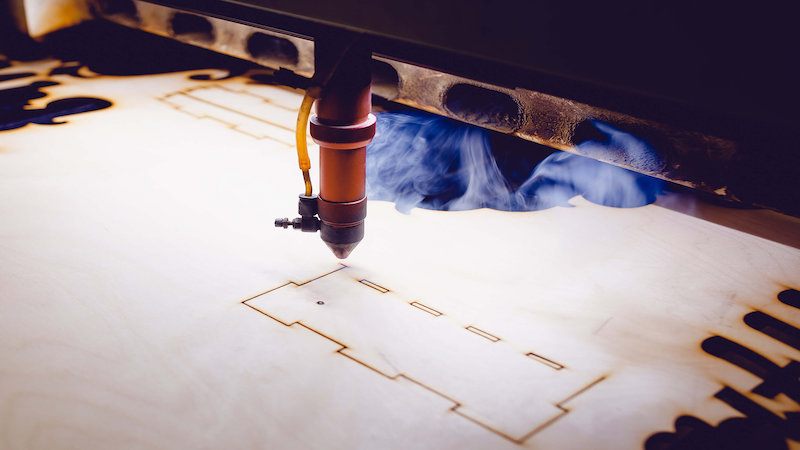
The resulting smoke and fumes during the process can also damage the laser machine components, specifically the optical lens, resulting in frequent maintenance and increased downtime.
Laser cutter exhaust systems are of multiple types and require some considerations on the user end before installing them, which we will discuss in detail in the following sections.
Do You Have Any Questions?
Let Us Solve Your Problem
Why Are Exhaust Systems Sold Separately?
Exhaust systems are sold separately from Laser cutting machines because there is no one-size-fits-all. Some machines do come with basic exhaust accessories but it’s better to set up one of your own.
Each operation produces different kinds of toxic gases and requires customized solutions. Here are the basic factors that decide the type of Laser exhaust solution needed.
- Types of material processed, e.g., wood, acrylic, glass, or aluminum.
- Type of laser cutting machines, e.g., fiber laser or CO2 laser.
- Different cutting intensities produce different volumes of toxic fumes.
- Safety compliance with your area’s operational codes
- Budget and operational constraints.
Why Exhaust Systems are Essential for the Laser Cutting Process?
An exhaust system is essential for any laser engraving machine or cutting machine; without it, the operation can be a serious health risk for workers and the machine itself. Here are the key parameters that drive the need for effective exhaust systems.
I. Effects on Human Health
It’s a no-brainer that the fumes produced during laser cutting are hazardous. Mind you, it has nothing to do with the laser beam itself but rather the vaporization of material that causes toxic smoke.
It can cause respiratory issues, adverse effects on internal organs, and, in worse cases, can be fatal.
Smaller desktop laser cutters are safe and classified as laser class 1 types. Bigger laser cutters like 50 W and above require proper ventilation and are classified as class 3 and class 4 types, describing the danger level. Such systems should not be run without an adequate ventilation system.
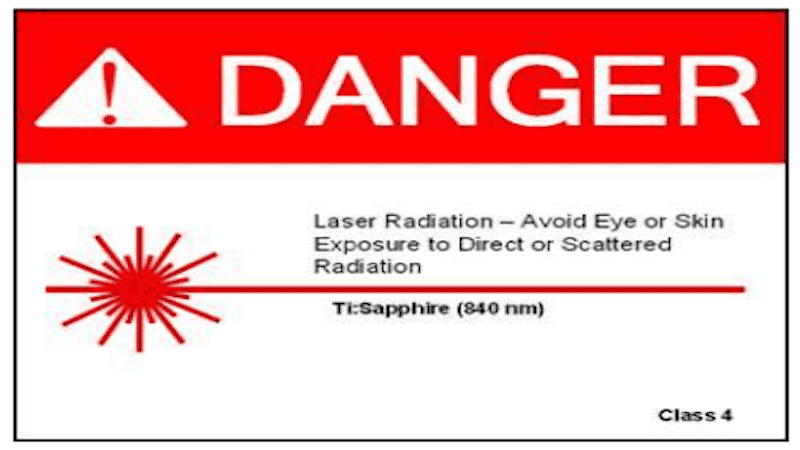
II. Worker Safety
People in the laser cutting business have to follow certain protocols to ensure the safety of their working staff. Everyone should follow the safety protocols, whether it’s a medium-scale laser-cutting business operating from a garage or a large laser-cutting industry.
The standards also define the protocols for expelling pollutants into the environment. In extreme cases, the fume must be pretreated before being released into the air.
Here is the list of organizations that monitor and develop protocols for safe laser-cutting operations.
- Occupational Safety and Health Administration (OSHA) Standards (US)
- Environmental Protection Agency (EPA) Regulations (US)
- National Emission Standards for Hazardous Air Pollutants (NESHAP) (US)
- European Union Emissions Standards (Europe)
- Health and Safety at Work etc. Act 1974 (UK)
- Control of Substances Hazardous to Health (COSHH) (UK)
Depending on your location, additional local or regional regulations specific to air quality, emissions, and workplace safety might need to be followed.
III. Laser Machine Safety
Laser cutting machines also get affected by residual smoke, and without a proper exhaust system, the machines can get damaged, which results in business loss.
Do You Have Any Questions?
Let Us Solve Your Problem
Types of Laser Exhaust System
The two major kinds of exhaust systems for laser cutters are as follows.
1. Duct Or Vent Exhaust

The most simple, economical, and effective way to exhaust dangerous fumes is by using metal or PVC ducts to direct the fumes out of the area through a window or a vent. Usually, an inline exhaust fan system drives the fumes out of the working area and expels it outside.
Smaller systems are typically easy. However, medium to large-scale exhaust systems require a bit of structural designing.
2. Fume Extractor
Fume Extractor works like a vacuum cleaner in the sense that it sucks all the dangerous fumes, aerosols, and particulates from the laser cutter and passes them through a series of filters like polypropylene filters, high-efficiency particulate air (HEPA) filters, and activated carbon filters to remove all the harmful elements from the expelled gasses.
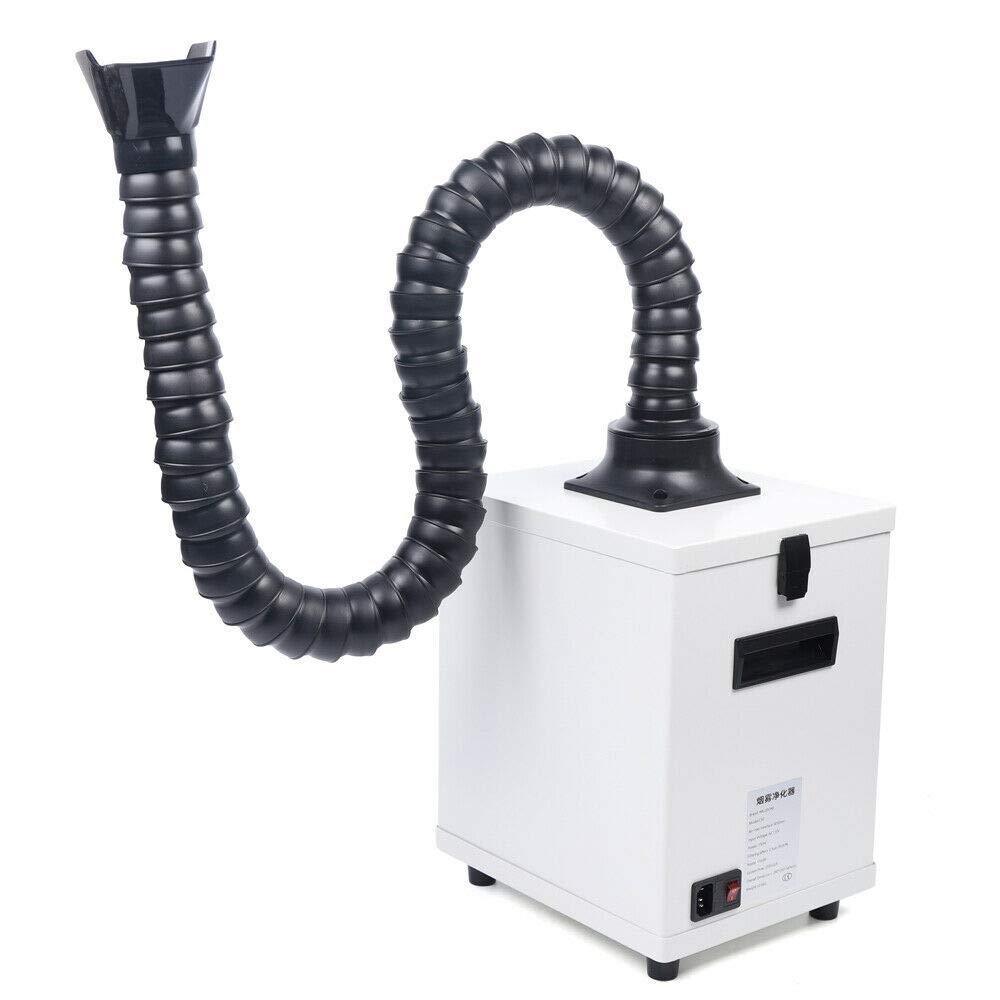
After cleaning the dangerous gases and airborne particles, it simply releases the air back indoors, making it perfectly safe to work in the environment. Even though the fume extractor is convenient and eco-friendly, it comes at a higher cost.
How Do You Set Up a Laser Cutter Exhaust System?
Here is the step-by-step guide to designing a functioning exhaust system for your laser cutting machine.
I. DIY Laser Cutter Exhaust System
We are going to present it in a comprehensive manner in 3 steps.
Step 1: Determine the Air Flow and Pressure Needed
You need the correct airflow and static pressure in your vent to support uninterrupted and effective exhaust. Typically, a 12” by 24” laser cutter bed requires at least 500 cubic feet per minute (CFM) of airflow and 1.49 kPa or 6 inches of water static pressure.
This is the bare minimum static pressure that will ensure the particles don’t get stuck in the laser table or in the duct and are effectively expelled into the air.
Depending upon the size of the table and exhaust port, these specifications can increase or decrease. You can find it easily on the product description of inline fans when you buy it in a store.
Step 2: Select the Right Type of Duct
For small to medium-scale workshops, PVC ducts or tubes with metal rings work fine. They are strong enough to withstand vacuum pressure.
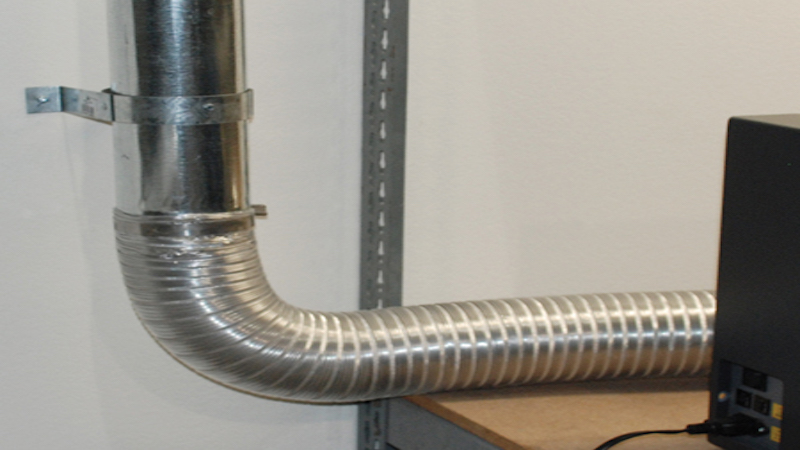
However, metal ducts are more suited for workshops with bigger laser cutters and higher workloads. They are also easy to ground as the particulate in the exhaust can build up a static charge, which can react to cause fires and, in the worst case, explosions. Commonly, 4” or 6” duct sizes (diameter) are used.
Keep the ducts as straight as possible because even a few bends (elbows) can significantly reduce the air pressure due to friction.
Step 3: Selecting Inline Fan and Proper Outlet
These are important for the safe use of the exhaust system.
1) Selecting Inline Fan
When in doubt about which size for an inline fan you should choose, always go for a bigger one. For example, if your requirement is 500 CFM, it’s better to install a fan with 660 CFM, ½ horsepower fan to account for friction.
Also, make sure the fan doesn’t produce too much noise and vibrations, as it can disrupt the working environment.
2) Selecting the Proper Outlet
- Place the fan as close to the outlet as possible so that the contaminants don’t get released into the environment in case of unforeseen leakage.
- For an outlet, you can simply place the exhaust duct out of the window or door, but it’s not feasible in winter or may give unwanted access to wildlife. You can install a proper dryer vent and connect your laser exhaust system to it. Ensure it has a screen to deter animals and insects from entering the duct.
- Use proper caulks or sealants to secure metal duct seams. In some cases, special aluminum tape also works best to prevent any leaks.
- As a rule of thumb, the amount of exhaust air removed should be supplemented with an equal volume of fresh air introduced into the work area, also called “Make-up Air.” Otherwise, it will create a vacuum-type situation, causing nausea and lightheadedness. It also drastically reduces the efficiency of the exhaust system as it fails to move fumes in vacuum conditions.
- In most cases, opening a door or window will suffice, while in heavier laser-cutting operations, a proper blower is needed to supplement the exhaust fan.
- For larger workshops and industrial settings, we strongly advise consulting HVAC experts to ensure proper ventilation and exhaust system design.
II. Laser Cutter Fume Extractor
Laser fume extractors are easier to install. The initial setup requires some time, which includes installing all the filters, plugging in all the setup, and configuring all the components. Once set, it’s ready to go. However, you must monitor its performance regularly and replace the old filters in time to avoid mishaps.
Do You Have Any Questions?
Let Us Solve Your Problem
Considerations When Choosing a Laser Cutter Exhaust System
You need to consider a few things for a long-lasting and maintenance-free laser cutter exhaust system.
1. Total Length and Bends in the Duct
Keep the air ducts as straight as possible. Frequent elbows and bends drastically reduce airflow, so much so that a pair of 90-degree elbows can reduce airflow volume equivalent to 12’ of straight pipe. So keep the number of bends to an absolute minimum.
2. Environmental Effect
Position exhaust vents far away from the workspace to prevent expelled air from re-entering the workshop. Consider extending the exhaust vent on the roof by 2′ or 3′ for added safety and effectiveness. Additionally, the vent should not be near the higher story of the building.
Ensure the materials you’re using don’t produce dangerous fumes that should be kept from entering the air. If they do, take a look at your state’s environmental guidelines for direction.
3. Workload and Budget
Many folks rush into buying costly fume extractors without considering their upkeep expenses. Prioritize a financial feasibility report before investing in an expensive exhaust system.
The duct exhaust and ventilation systems are the preferred choice if the workload is higher, and budget is a concern.
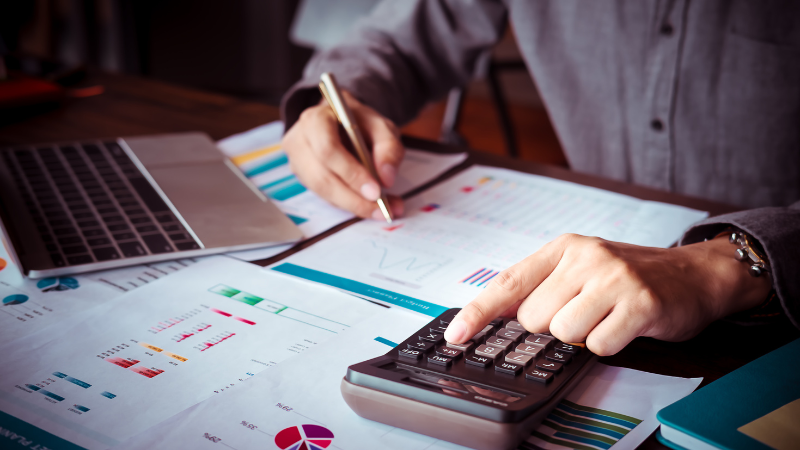
Maintenance and Troubleshooting
For a smooth-running laser cutter exhaust system, you need to be vigilant about the following things.
1. Exhaust Fan Maintenance
The inline exhaust and ductwork collect dust and material residual on them over time and will start to perform poorly. A clear indicator for a performing fan and clogged duct is that you would need frequent maintenance of the laser cutting lens. So, we recommend regular maintenance checks to ensure everything is on point.
2. Check for Leakages
If you detect fumes inside the working area, even with the exhaust system, then there might be a leakage in the exhaust duct. The metal ducts usually leak from joints, which can be detected by examining the said area. Reapplying sealant or metal tape usually does the trick.
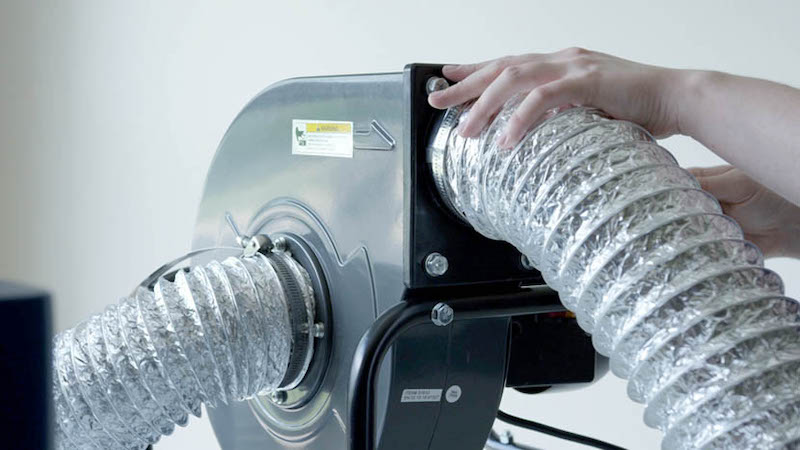
To check flexible pipes, visually inspect them for any physical signs of leakage. If you suspect small pinholes, disconnect the pipe from the exhaust and shine a flashlight through one end. Turn off the room lights; any escaping light rays will reveal a leak in the duct.
3. Replace Filters
Regularly replace filters in your fume extractor. Faulty filters can lead to toxic fumes leaking into your workspace, making it difficult to work.
Invest in a laser fume extractor featuring layered, easily detachable filters. This way, if one filter type needs changing, you can replace it without disturbing the others. Such a setup will significantly reduce maintenance efforts down the line. And prevents potentially harmful particles from entering the working environment.
FAQs
1. Do You Have to Vent A Fiber Laser?
Yes, just like any other laser system, the Fiber laser machines also require proper ventilation. Depending on the volume of hazardous emissions, the size of the exhaust system may vary.
2. How Do You Ventilate a Laser Cutter?
You can ventilate the laser cutter by using ducts and an inline fan to direct smoke outside the house or workshop. Alternatively, install a fume extractor to treat toxic fumes on-site, releasing safe, breathable air within the same area.
3. How Much Ventilation Does a Laser Cutter Need?
All the enclosed laser cutter machines need proper ventilation, with no exception. The exhaust system must make sure to transfer all the fumes outside the environment completely. A well-ventilated laser cutting bed increases laser cutting efficiency and results in greater yield.
Do You Have Any Questions?
Let Us Solve Your Problem
Conclusion
Now equipped with the basics of laser cutter exhaust systems and setup, you can create your customized system for laser engraver or cutter. Remember, perfecting an exhaust system for your laser cutting operation may take multiple attempts, so focus on the considerations we discussed.
Elevate Your Precision: Explore Laser Cutting Excellence at Baison Laser Today!
Uncover the potential to revolutionize your business alongside Baison – the foremost innovator in state-of-the-art laser machine systems. Trusted by enterprises spanning over 100 countries and regions, our cutting-edge laser technology surpasses industry benchmarks, delivering excellence in laser cutting, welding, marking, and cleaning.
Our meticulously engineered Fiber and CO2 laser machining solutions will enhance your manufacturing prowess. Attain a competitive advantage through our Free Application Evaluation and Sample Proofing. Take the leap with Baison today to maximize your production efficiency!