This article will discuss stainless steel and how to cut it with laser machines. We will discuss other methods of cutting stainless steel and see how they differ from laser cutting and how laser cutting surpasses every other method. We will explore the benefits of laser cutting stainless steel sheets and tubes, the different types of lasers used in the process, and how to optimize the cutting process to achieve the best results.
What is Stainless Steel?

Stainless steel sheets and tubes have a wide range of applications, from architecture to automotive, medicine to food and beverages; every industry does not involve cutting stainless steel sheets and tubes at some scale. Stainless steel cutting is generally difficult compared to other materials, such as aluminum or copper. That is due to several factors, including stainless steel grades.
Stainless steel is an alloy of iron, carbon, and other elements, including chromium, which gives it its characteristic resistance to corrosion. The addition of chromium makes the material much harder and more challenging to cut than other metals, such as aluminum or copper.
Stainless steels can be categorized into different grades depending on their composition and properties. The most commonly used grades are 304 and 316, often used in applications requiring corrosion resistance, such as in the food industry, chemical plants, and medical devices.
How Does a Laser Cutting Machine Work?
Laser cutting is the most excellent machine used in small and big industries for precisely cutting stainless steel and other materials.
A laser cutting machine uses a high-powered laser beam to melt, burn, or vaporize its cutting material. A laser resonator generates the laser beam, which contains a gain medium excited by an energy source, such as an electric arc, flash lamp, or diode.
When the laser beam is focused onto the surface of the stainless steel sheet, it heats the material to the point of melting or vaporization, creating a narrow kerf or cut. Mirrors and lenses guide the focused laser beam to ensure precise cutting, and the intensity and duration of the beam can be controlled to achieve different cutting depths and widths.
In some cases, a laser cutting machine may also use a gas, such as oxygen or nitrogen, to assist in cutting. The gas helps to blow away the molten material and can increase the speed and quality of the cut.
Laser cutting is a precise and efficient method for cutting stainless steel sheets, offering high accuracy and flexibility for various applications.
CO2 vs. Fiber Laser Cutting Machines
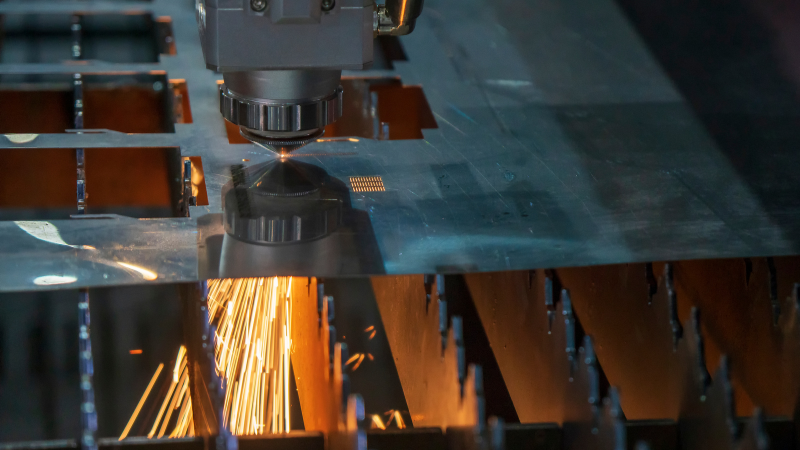
Here are two types of laser cutting machines for stainless steel.
CO2 Laser Cutting Machines
These machines use a gas laser to cut stainless steel. The laser is generated by exciting a mixture of carbon dioxide, nitrogen, and helium gasses with an electric current. CO2 laser cutting machines are versatile and can cut a wide range of materials, including stainless steel. They are typically more affordable than other laser-cutting machines, making them popular for industrial applications.
Fiber Laser Cutting Machines
These machines use a solid-state laser to cut stainless steel. The laser is generated by passing a high-intensity light beam through a fiber optic cable. Fiber laser cutting machines are more expensive than CO2 laser cutting machines but offer several advantages.
They are faster and more precise, and they are also more energy-efficient. Fiber laser cutting machines are ideal for cutting thin sheets of stainless steel and are widely used in the automotive and electronics industries.
Comparison of CO2 and Fiber Cutting Machines
Laser source: CO2 lasers use a gas mixture to generate the laser beam from the laser head, while fiber lasers use a diode and fiber-optic cable. Fiber lasers have higher conversion efficiency, producing more laser power with the same input energy. This can result in faster cutting speeds and lower operating costs for fiber laser machines.
Cutting speed: Fiber laser machines are generally faster than CO2 laser machines for cutting stainless steel, especially thin sheets. This is because fiber lasers have a higher power density and can quickly cut through the material.
Cutting quality: CO2 and fiber lasers can produce high-quality cuts on stainless steel, but fiber lasers are generally better for achieving precision. Cuts quality is also neat with minimal heat-affected zones (HAZ). Fiber lasers have a smaller spot size and can focus the laser beam more tightly.
Maintenance: CO2 lasers require more maintenance than fiber lasers because they have more components that can wear out or require adjustment over time. However, fiber lasers are more sensitive to dust and other contaminants, which can affect their performance if not properly maintained. You can read this guide to learn how to maintain laser cutters.
Cost: Fiber laser machines are generally more expensive than CO2 laser machines but offer faster cutting speeds and lower operating costs over time. However, the specific cost of each type of machine can vary widely depending on the manufacturer, model, and features.
Other Methods of Cutting Stainless Steel
Although hard to cut, stainless steel can be cut using different tools, carbide-tipped or diamond-coated blades, lubricating the cutting surface, and applying appropriate cutting speeds and feeds.
However, on an industrial scale, using hand tools has become obsolete. Machines are designed to cut stainless steel precisely, giving the end product more finesse.
Here are different methods of cutting stainless steel sheets and tubes.
Plasma Cutting
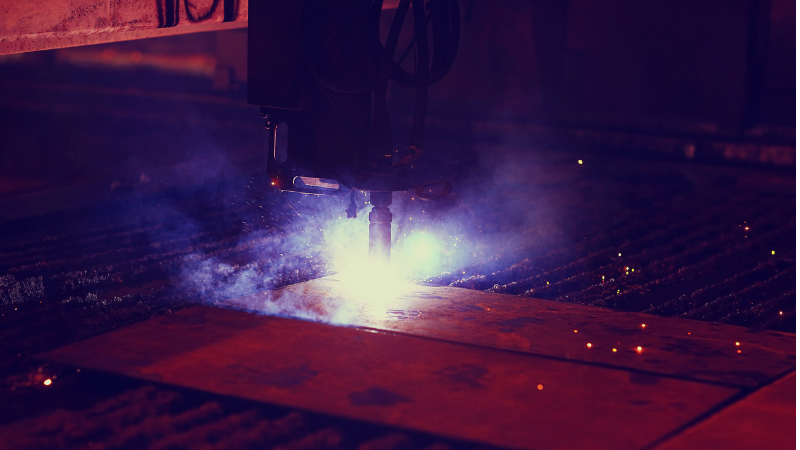
Plasma cutting is a metal cutting process that uses a high-temperature plasma arc to melt and cut through various types of metals. This process is commonly used to cut through stainless steel and other metals like aluminum, copper, and carbon steel. For more details about the difference between plasma and fiber laser cutting, you can read the blog we’ve written before: “Laser Cutting VS. Plasma Cutting: Which Procedure is Better for You?“
Even plasma cutting has two types of systems. The difference lies in the kind of gas from the plasma torch.
A lower cost Plasma CNC system uses only air. It cuts only 25mm thick stainless steel sheets. It uses 78% nitrogen and 20% oxygen which can lead to a black finish after the cut. The finish quality from the edges is also rough.
There are industrial-scale plasma systems that use a variety of gasses and combinations to give a smooth and shiny finish. The gas is passed through a small nozzle that focuses the arc and increases its temperature, reaching up to 30,000 degrees Fahrenheit. The choice of gas depends on the thickness of the material and application. The choice of gasses depends on whether you have a multi-gas, mechanized plasma, or dual-gas system. The common gasses used in a plasma system are:
- Nitrogen: This gas is commonly used in the plasma cutting of stainless steel because it produces a high-quality cut with minimal oxide buildup.
- Argon: Argon is another gas commonly used in the plasma cutting of stainless steel because it produces a smooth, clean cut.
- Hydrogen: Hydrogen is sometimes used in plasma cutting stainless steel because it produces a very high-temperature plasma, which can be useful for cutting thicker materials.
- Oxygen: Oxygen can be used in plasma cutting stainless steel, but it tends to produce a rougher cut with more oxide buildup than nitrogen or argon. Pure oxygen is not recommended as it can lead to an oxidized surface.
Advantages
- Plasma jets can generate temperatures as high as tens of thousands of degrees Celsius, which makes them suitable for various industrial processes such as Cutting, welding, and surface treatment.
- Plasma jet has a high energy density, allowing it to perform various impossible chemical reactions with conventional methods.
- Plasma jets can be used for various applications such as material processing, surface modification, and biomedical applications.
- A plasma jet does not require direct contact with the material, which makes it ideal for processing delicate materials.
- Plasma jets can be easily scaled up or down depending on the application requirements.
Disadvantages of plasma jet:
- It generates high temperatures and can cause severe burns or injuries if improperly handled.
- It can be expensive to acquire and maintain, which makes it less accessible for small-scale applications.
- Requires a continuous gas supply to maintain the plasma state, which can be costly.
- Its limited penetration depth makes it unsuitable for processing thick materials.
- It can cause damage to the material being processed due to the high energy density of the plasma.
Water Jet Cutting
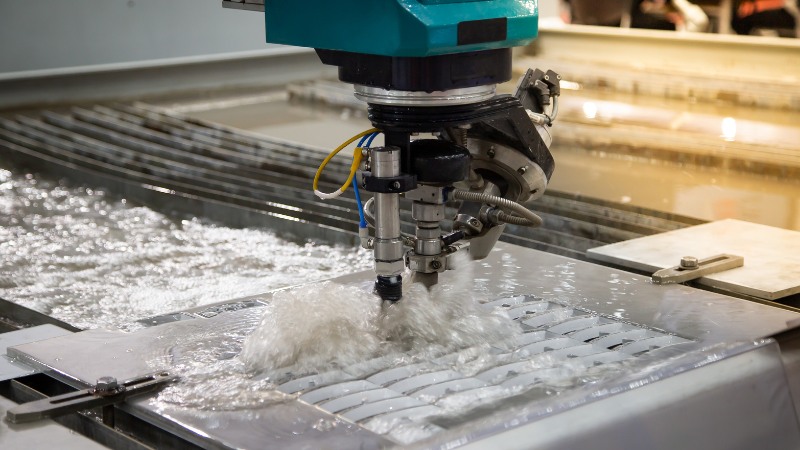
Water jet cutting is a precision cutting process that uses a high-pressure stream of water mixed with abrasive materials to cut through materials such as stainless steel. The process involves pressing water to extremely high levels (typically between 30,000 and 90,000 psi), which is then forced through a small nozzle.
The water stream is mixed with abrasive materials such as garnet, which helps to erode the material being cut. The stream of water and abrasive materials is directed at the material being cut, and the combination of high-pressure water and abrasives allows for precise Cutting. To know the difference between water jet and fiber laser cutting, you can read the blog we’ve written before: “Laser Cutting vs. Water Jet: Which One to Choose?“
Advantages
- Precise cuts with high accuracy make it an ideal choice for cutting intricate designs or shapes. Unlike other Cutting processes, such as plasma or laser cutting, water jet cutting does not produce a heat-affected zone (HAZ) in the material being cut
- Water jets can cut many other materials besides stainless steel, including metals, plastics, ceramics, and composites.
- The water-jet cutting process does not produce harmful fumes or dust, making it an environmentally friendly option.
Disadvantages
- Slow cutting speed makes it less suitable for high-volume production environments.
- It can be more expensive due to the high-pressure pumps and abrasive materials required for the cutting process.
- Water jet cutting can produce a wider kerf (the cut’s width) than other Cutting methods.
- Water jet cutting is limited in the thickness of the material it can cut and may not be the best option for materials over 6 inches in thickness.
Laser Cutting VS Other Cutting Methods
Here are several reasons why Laser cutting is an ideal process for cutting stainless steel sheets and tubes on an industrial scale:
Precision: Laser cutting offers high precision, accuracy, and essentials when cutting stainless steel sheets and tubes. They can cut through even the thinnest of materials with high accuracy, resulting in a clean and precise cut.
Speed: Laser cutting is a fast process that can quickly cut through stainless steel sheets and tubes, making it ideal for industrial applications.
Versatility: Laser cutting machines can be programmed to cut various shapes and designs, making it a versatile process that can be adapted to different industries and applications.
Reduced Waste: Precise Cutting produces less waste material, removing material only where necessary.
Cost-Effective: Although the initial investment in a laser cutting machine can be high, the cost of operating and maintaining the machine is relatively low.
Factors that Affect the Laser Cutting of Stainless Steel
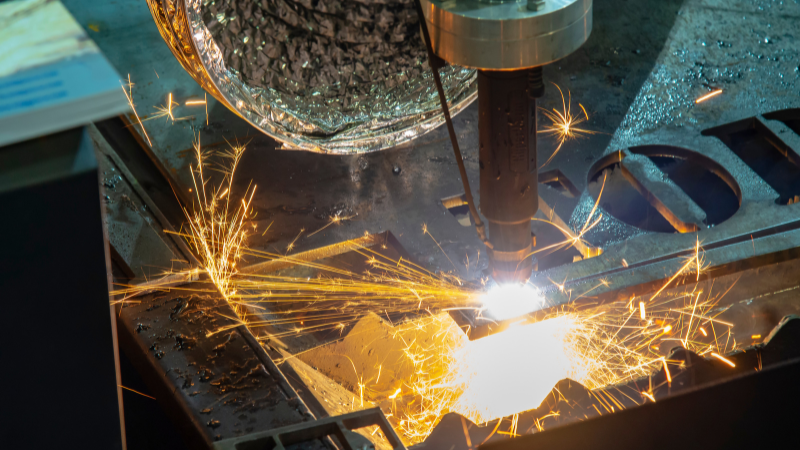
Material Thickness: The thickness of the stainless steel sheet affects the laser cutting process, as thicker sheets require more power and longer processing times to cut.
Laser Power: The laser power used in the cutting process affects the speed and quality of the cut. Higher-power lasers are capable of cutting thicker sheets.
Beam Quality: The quality of the laser beam affects the cutting process as well. A high-quality beam produces a cleaner, more precise cut.
Focus Position: The position of the laser focus affects the cutting process. The correct focus position is critical to achieving a precise and clean cut.
Gas Type and Pressure: The type and pressure of the gas used in the cutting process affect the quality of the cut. Oxygen, nitrogen, and air are commonly used gasses in laser cutting, and their pressure levels can be adjusted to optimize the cutting process.
Cutting Speed: The speed at which the laser moves across the material affects the quality and precision of the cut. A slower cutting speed generally produces a cleaner and more precise cut.
Cutting Assist Gas: The Cutting assist gas used in the laser cutting process helps to remove the molten material from the cut. This gas can affect the quality and precision of the cut, as well as the speed of the cutting process.
What are Post Processing Steps After Cutting Stainless Steel?
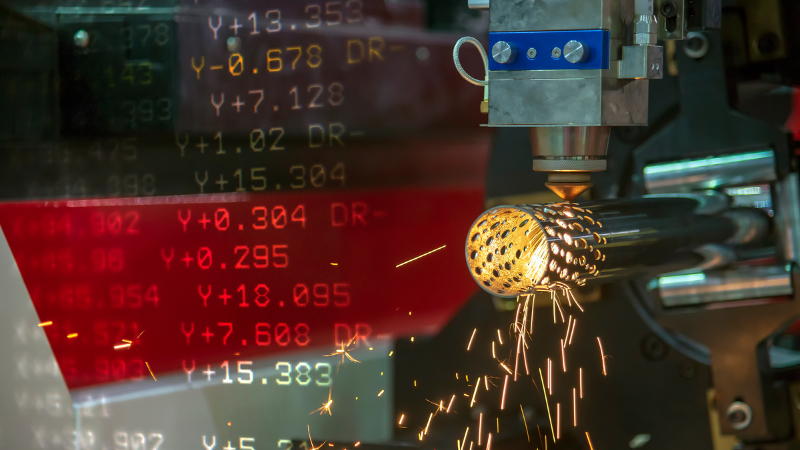
After cutting laser sheets and tubes from a laser cutting machine, several post-processing steps are necessary, including:
- Cleaning: The first step in post-processing laser cut parts is cleaning. It involves removing any slag, debris, or residue left on the parts after cutting. Cleaning can be done manually or with the help of automated systems, such as a wire brush or air compressor.
- Deburring: Laser cutting can create sharp edges and burrs on the cut parts. Deburring is the process of removing these burrs to create a smooth cut edge. Deburring can be done manually or with the help of automated systems, such as a vibratory deburring machine.
- Grinding: Grinding may be necessary if the cut edges require a specific finish or if the parts need to be modified to fit specific requirements. Grinding can be done manually or with the help of automated systems, such as a belt grinder or disc sander.
- Surface Treatment: Depending on the intended use of the parts, surface treatment may be necessary to improve their durability, corrosion resistance, or appearance. Some common surface treatment options include sandblasting, painting, powder coating, or anodizing.
- Inspection: Once the parts have been cleaned, deburred, and treated, they should be inspected for quality assurance. Inspection can be done visually or with the help of automated systems, such as a coordinate measuring machine.
Safety Measurements for Laser Cutting Machines
- Wear appropriate personal protective equipment (PPE) such as safety glasses, face shields, gloves, and clothing that covers your entire body.
- Ensure the laser cutting machine is in good working condition and has all the required safety features, such as emergency stop buttons, interlocks, and barriers.
- Ensure that the laser beam path is unobstructed and that the laser beam cannot reflect off any surface and pose a hazard to operators or bystanders.
- Never leave the laser cutting machine unattended while it is running. Stay alert and attentive at all times to observe any unusual behavior of the machine.
- Keep the work area clean and free of clutter. It helps prevent tripping hazards and ensures the laser-cutting machine can operate efficiently.
- Ensure that the workpiece is properly secured and clamped in place before starting the cutting process.
- Only trained and authorized personnel should operate the laser-cutting machine.
- Follow the manufacturer’s instructions for the laser cutting machine’s operation, maintenance, and repair.
Baison Laser Cutting Machines for Stainless Steel Sheets and Tubes
Baison is a worldwide trusted manufacturer of Laser cutting machines. Our machines offer hyper-fast production, user-friendly design, and flexible bevel operations to suit different tasks.
Our sheet-cutting metal machines come in the following types:
- Entry Level Sheet Metal Laser Cutting Machine
- Superior Sheet Metal Laser Cutting Machine
- High-powered Sheet Metal Laser Cutting Machines
Final Words
Stainless steel laser-cutting machines are accurate, precise, and speedy and reduce the overall maintenance and post-processing cost of production. The amount of production can boost the business and make them an ideal choice to cut stainless steel sheets and tubes of various thicknesses in any industry. Contact us for more information on our laser machines and laser cutting.
“Upgrade Your Stainless Steel Cutting Game with Our Precision Laser Cutting Machines – Get a Quote Today!”
Laser-cutting machines have proven to be a revolutionary addition to the industrial sector, enhancing productivity and output. Whether your business is large or small, Baison’s laser-cutting machines can increase your daily production. Our machines can cut through tough materials such as stainless steel and other materials such as ceramics, glass, PVC, and other metals.
Get a quote now to enhance your metal fabrication abilities. Our staff is readily available to assist you in selecting the machine that best meets your industrial requirements. You can also receive a free evaluation sample from us.