The subject of laser welding comprises multiple laser welding techniques, which you might need to be aware of.
This guide below explains welding processes using focused laser beams in detail. Each process consists of different methodologies, and we have clarified them comprehensively. You can learn about the laser welding process and how it differs from the traditional welding methods in each way.
Basics of Laser Welding
Laser welding is a process that uses a laser beam to carry out the welding process. It has an essential significance in our everyday lives.
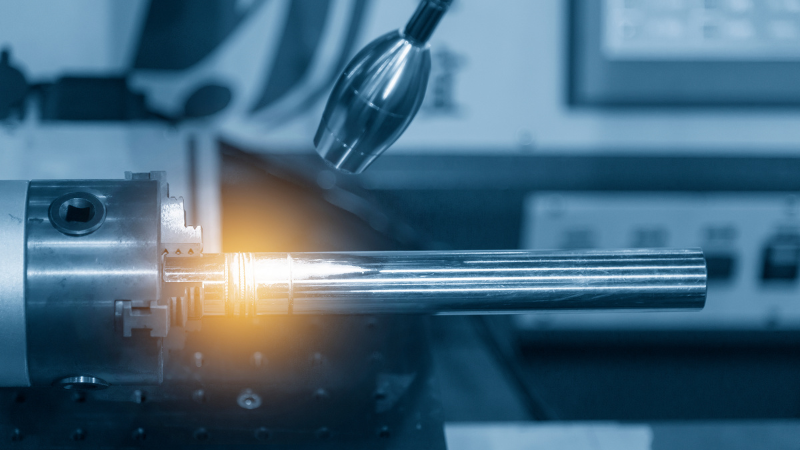
Laser welding is a method that uses a heat source in the form of a laser. It leads to melting the material, which helps fuse it upon cooling down. It is a process that allows the welding of all kinds of materials. It also helps in multiple ways in the manufacturing industry at a faster speed.
Compared to traditional welding methods, laser welding is a fast process, and the cost of operating the machines is low. Hence, a high volume of products can be manufactured through this process in less time.

7 Different Types of Laser Welding Methods
Laser welding consists of many methods, each with pros and suitability. Below, you will learn about different laser welding methods.
1. Fiber Laser Welding
Fiber laser welding is a process of welding that uses fiber laser beams as a source of energy. It helps to combine the metal pieces. This method uses a focused laser beam that melts the material. It offers a concentrated heat source and welds the metals together.
In this process, the diode lasers produce light emission. The emitted light is then subjected to a fiber optic cable after amplification. The entire process shapes the laser beam suitable for the application by manipulating its wavelength.
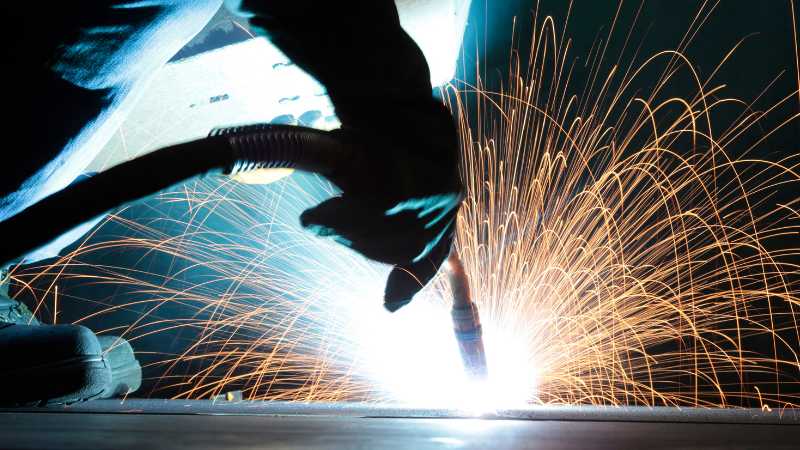
Fiber laser welding machines create a robust weld, ensuring that the welded materials are precisely joined with a massive speed and high control. It is a suitable process for fusing thin materials that are delicate. Since this process comprises quick heating and cooling, the welding time is shorter than traditional welding methods. Since this laser welding has a high power density, the achievement of deep penetration laser welding is possible.
The applications of fiber laser welding are present in the automotive, defense, construction, and electronic industries.
2. Keyhole Laser Welding
Keyhole welding is an advanced method that forms a narrow and deep hole in the workpiece while welding. The keyhole welding process uses a high-power laser beam so that an intense source is created to create a keyhole.
The keyhole passes through the thickness of the workpiece and allows deep penetration laser welding. During this process, the material of the workpiece is vaporized due to the vapor pressure, which helps keep the keyhole stable.
The keyhole welding process has multiple benefits, as it penetrates thick materials, and applications that need a fully penetrated weld may achieve them through this technique. The joints created by this process are of high-quality welds with minimal distortion.
Industries that use keyhole welding processes for different applications consist of aerospace and automotive, as they have to produce heavy components using thicker materials.
3. Conduction Welding
Conduction laser welding is a process in which metal pieces are joint through heat conduction. The method of conduction welding is suitable for welding thin materials or materials with low heat conductivity.
A laser beam passes through the metal components at the joining point. The component absorbs the energy of the laser beam. The absorption of energy leads to heating; the molten material then spreads out and forms a weld.
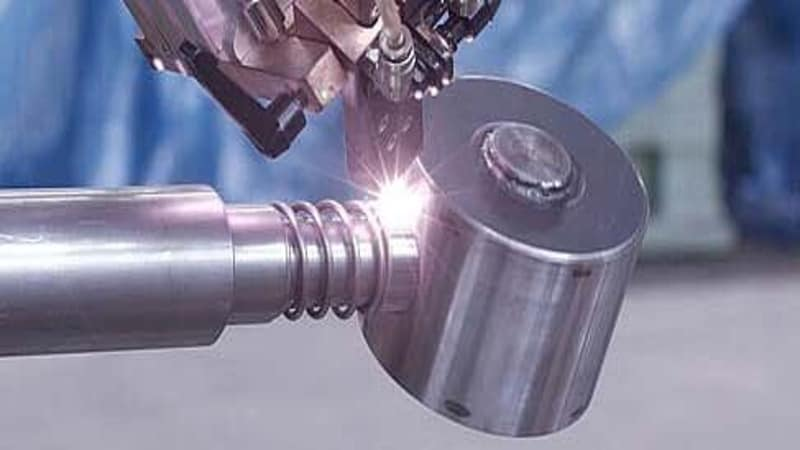
Hot conduction welding uses low-powered lasers, and due to controlled heat conduction, the joint welds. It is a suitable process when it comes to delicate welding materials.
There are many advantages associated with the heat conduction welding process. It offers precise control over the welding process. Due to this, the defects on the final weld are also minimized. This welding process is popular with applications in medical device, electronics, and jewelry manufacturing industries.
We have prepared articles on laser welding modes. It covers Conduction Mode and Keyhole Mode Welding.
4. Deep Penetration Welding
Deep penetration laser welding is a method that, unlike traditional welding methods, uses high-power laser beams so that the workpiece can be welded in depth. Due to its high-energy laser beam, it is used to weld thick materials.
A focused laser beam of high power density is subjected to the joint between the metal workpieces to create deep welds; the laser energy’s intensity leads to the desired welding depth. The laser beam heats the material, then vaporizes and forms a cavity in the workpiece.
Deep penetration laser welding has many benefits compared to traditional welding processes. It allows the welding of thick materials in just one go, eliminating the need for multiple laser welds. Materials with a high melting point are commonly welded through deep penetration laser welding.
This method is commonly used in multiple industries like heavy equipment manufacturing and the automobile sector, where components that have thick structures are welded.
5. YAG Laser Welding
YAG laser welding is a form of welding that uses solid-state lasers known as neodymium-doped yttrium aluminum garnet lasers, which lead to joining metal components. This method is famous for its versatility as it welds various metals together.
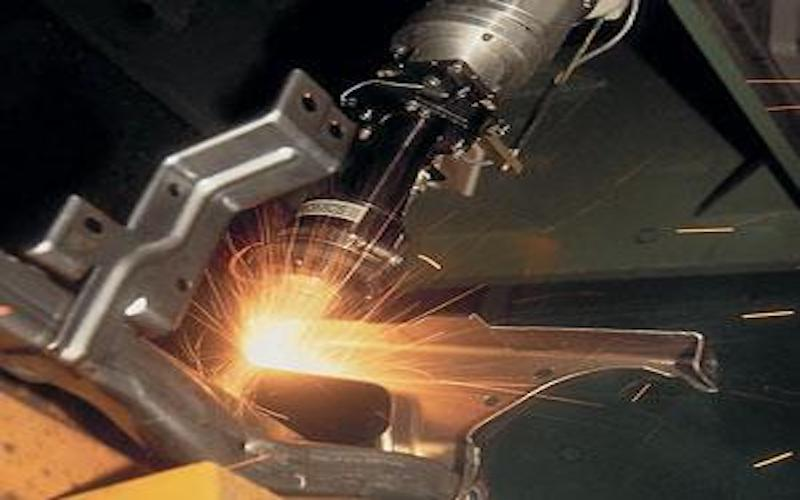
A high-energy laser beam is subjected to the joint between components in this kind of laser welding. The laser beam melts the metal upon heating it, and a weld pool is created; as soon as the molten metal solidifies, a strong weld is formed.
YAG lasers offer precise control of the welding process and allow for attaining high-quality welds. The laser beam allows for deep penetration welding. This process is highly suitable for thick materials. YAG welding offers control of laser welders on the shape of the pulsed laser, duration, and power of the welding.
YAG laser welding is used in multiple industries like electronics, automotive, and medical devices. It is used for joining intricate parts and leaves behind strength-oriented welds. It emits a wavelength of 1064 nanometers and is highly suitable for welding materials like aluminum, copper, and various other alloys.
6. Laser-Hybrid Welding
Laser hybrid welding is an advanced welding technique that combines arc welding and laser welding and helps create highly efficient and precise welds for metal-based components. The process of laser welding simultaneously uses arc welding and laser beam.
In this process, the laser beam is a heat source, a heat-affected zone that allows it to melt, and arc welding supplies the filler material, adding heat to the weld pool.
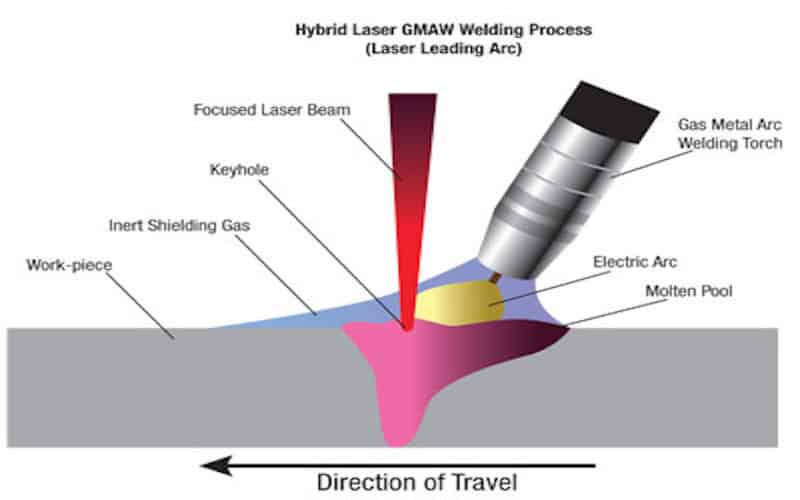
This combination of arc welding process and laser welding offers several benefits, and the laser beams provide a precise heat source, which leads to carrying out precise welds with deep penetration at a fast speed. The process also offers better welding control and helps reduce distortion.
The application of laser-hybrid welding can be seen in shipbuilding, aerospace, and heavy equipment manufacturing industries. It offers thick joining materials with complex geometries and large structures requiring high welding speeds.
7. CO2 Laser Welding
CO2 laser welding is a process that uses a carbon dioxide laser beam as a source of energy, and it helps join metals together. It is used in multiple industries, being a practical and versatile welding method.
CO2 laser welding involves a combination of nitrogen, carbon dioxide, and helium gas in a laser beam, which is then focused on the workpiece with the help of lenses and mirrors so that a heat source can be generated. The heat generated by the laser beam helps the metal melt and allows the fusing of the workpieces together.
This kind of laser welding gives the welder more control over the process because the laser beam is focused and ensures the welding of delicate materials together with deep penetration. Multiple industries have been using CO2 laser welding, like electronics, manufacturing, aerospace, etc.

Advantages of Laser Welding Technology
There are multiple advantages offered by laser beam welding technology, some of which are provided below:
- Laser welding offers high accuracy and precision, such that the tiniest parts can also be welded together without any distortion caused by heat.
- Laser welding offers consistency. Hence, in the case of repeatable welds, it provides efficiency in manufacturing by reducing the scrap.
- Laser welding methods that use low-power lasers help minimize the chances of thermal distortion, making joining a contact-free process.
- The laser welding process is very fast and helps produce high volumes of components joined in no time.
- The process of laser welding can accommodate all kinds of materials, ranging from thick to thinner ones. It also allows the welding of dissimilar materials.
Disadvantages of Laser Welding Technology
Alongside advantages, there are some limitations of laser welding technology, which comprises the following:
- Laser machines are expensive compared to traditional welding machines like tig welding and mig welding. You need a high initial investment cost, and maintenance expenses follow this. (Maybe you want to know the difference between laser welding and TIG welding, and the comparison between laser welding and MIG welding.)
- The laser welder must have sufficient skills and expertise to operate the laser welding equipment. It requires appropriate pulse duration, beam focus, and relevant training.
- Safety measures are essential for laser welding, as some processes use high-power lasers. Hence, protective gear and a safe working environment are a must when laser welding is undertaken.
Comparison Between Different Laser Welding Methods
By describing these three laser welding machines in the table below, we aim to provide you with an insight into the specific strengths and weaknesses these three methods have. These methods represent the three core technologies.
Type of Laser | Fiber Laser | Co2 Laser | YAG Laser |
Wavelength | 1.06 μm | 10.6 μm | 1.06 μm |
Power Range | 500W-2000W | 1000W-4000W | 200W-1000W |
Materials | Aluminum, Steel etc | Ceramics and Plastics | Plastics and Metals |
Maintenance | Low | Moderate | Moderate |
Precision | High | Moderate | High |
Strength | Ideal for creating precise welds, has a high range of power and releases minimal heat. | Affordable cost and offers material versatility. | Intuitive interface, cost-effective solution for welding. |
Weaknesses | It is expensive and is used for specialized applications. | Emits carbon dioxide gas and has a complex setup. | It has a moderate range of power and hence doesn’t suit all materials. |

Which Laser Welding Method to Choose?
When opting for a laser weld, various factors must be kept in mind so that the right kind of laser welding type is decided for the correct application. Some of the factors to consider in this regard are as follows:
1. Material Compatibility
Different types of materials are welded with one another when it comes to creating components; every material has a different thickness level and different characteristics. Hence, when choosing the laser type, assessment of the material is important. Fiber lasers are highly compatible with almost all kinds of materials, and deep penetration or keyhole welding may be suitable for the thicker ones.
2. Joint Configuration
The nature of the joint or weld also influences the selection of laser welding methods. Some laser types are suitable specifically for certain kinds of welds, and some may not.
3. Welding Speed
The production requirement and volume help determine the type of laser welding that must be opted for. Some of them help produce in high volume at a fast speed, and specific applications require using them. The disk lasers offer a high laser beam quality; hence, they have high laser power that helps produce welds at a high speed.
4. Impact of Heat
The impact of heat on the surrounding component material is also a factor to consider; some methods can produce less heat, and hence, the size of the heat-affected zone is reduced, and accordingly, the laser welding method is chosen. Pulsed laser welding is suitable as it helps minimize the impact of heat on the surroundings.
5. Cost of Laser Welding
Laser welding equipment costs must be assessed; depending on your budget, the laser selection is done accordingly. Diode laser welding is one of the most cost-effective welding solutions. At the same time choose the right laser welding machine manufacturer.
Industrial Applications of Laser Welding Technology
The applications of laser welding technology can be seen in multiple industries, and some of these applications are discussed below:
1. Automobile Industry
The automobile industry is highly dependent on laser welding technology for manufacturing its components, including engine parts, fuel injectors, filters, and many more. Multiple kinds of laser welding methods are used when it comes to the automobile industry. Fiber lasers are a popular type for manufacturing welded components.
2. Medical Industry
The healthcare industry uses multiple equipment for the patients, which comprises medical implants, surgical blades, and various other parts. Laser welding is a suitable process for manufacturing such components in cases where high precision is needed, and thin metal is used. YAG lasers are popular in the medical industry, helping to manufacture medical equipment and tools.
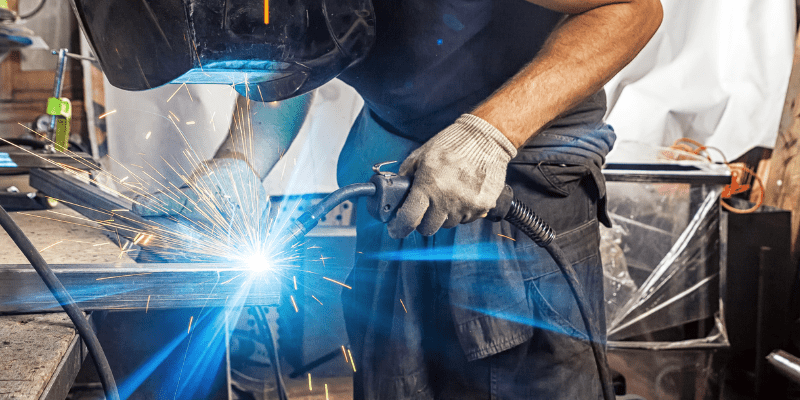
3. Aerospace Industry
The aerospace industry uses laser welding to produce parts that need high-quality welds, followed by high accuracy and precision. The manufactured components usually consist of metal detectors, airframes, and other parts. Aircraft parts pass through a lot of stress, and there is no margin to compose; hence, multiple laser welding techniques opt to manufacture high-quality components.
4. Jewelry Industry
The jewelry industry also uses laser welding to manufacture jewelry pieces that consist of precious stones with intricate layouts.
The accuracy of design is one of the primary considerations in this industry; hence, a proper welding process is essential to produce and repair the jewelry piece.
The concept of laser welding used in the jewelry industry is free moving, where the laser beam is intact at one position, and to weld the pieces together, the welder moves them according to the requirement. The application of laser welding in the jewelry industry can be seen in bracelets, necklaces, and rings.

FAQs
1. How is heat generated by a laser beam by a laser welding machine?
The laser beam provides a source of heat concentrated on the joint between the two pieces that must be welded together.
2. Which materials can be welded through laser welding?
Laser welding work is suitable for multiple materials like titanium alloys, nickel, stainless steel, aluminum, ceramics, and plastics using gas lasers specifically.
3. What sizes are available for laser welding wires?
Laser welding wires may have varied diameters, including 0.15mm, 0.25mm, 0.1 mm, and so on, up to 1.0mm.
Conclusion
As you have read the detailed guide above, many things about laser welding technology must have been cleared now, and you now know the different kinds of laser technology available to choose from and how it suits various applications. As time passes, new and improved methods in the field of laser welding are developing, and we look forward to incorporating them into our machines.
Baison Laser Welding: Precision Meets Innovation!
Have you geared up to opt for high-quality and reliable welds for your product components? At Baison Laser, you will get your hands on the most promising laser welding machines equipped with efficiency and accuracy. So, contact Baison Laser today and incorporate a seamless and long-lasting weld!