In this article, we’ll focus on what distortion in welding means, what causes it, and how you can minimize its effect. You’ll also discover effective tips to help you fix the effects of deformation in welding.
What is Laser Weld Deformation?
Weld distortion or deformation involves changes in the shape and dimension of a metal structure. It is a natural effect of welding. When metals go through laser welding, they are subjected to extreme heat that causes them to melt. This causes the material to expand.
As the melted metal cools to room temperature, it solidifies and starts to contract. This is the residual stress. If the heating is localized and the rest of the metal surface is not heated, it won’t expand or contract in the same way. This will cause distortion.
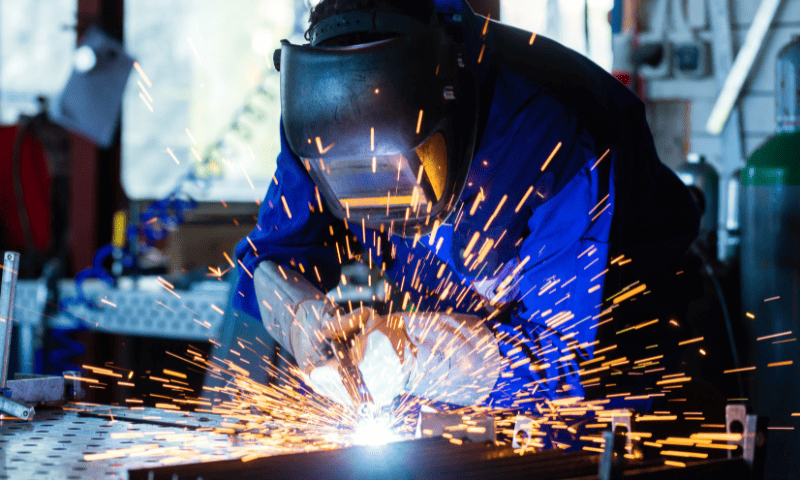
About Laser Welding
To get a better understanding of how the deformation happens, it’s important to understand what laser beam welding is.
The National Institute of Standards and Technology has deemed this technique to be quite popular in the world of manufacturing. It’s so prevalent that the US government agency has spent valuable resources to “improve simulations” of laser welding procedures in hopes that it’ll streamline manufacturing processes in the future.
Unlike arc welding which uses heat input from an arc, laser welding uses heat input from a laser beam. The laser reaches a metal’s melting point to create a strong joint and fuse materials together.
Both of these are effective in infusing even high-strength steel. However, the laser power welding process is deemed to be more effective in producing a precise finish thus producing a higher weld quality.
Materials Prone to Distortion After Welding
To identify what makes a material susceptible to weld distortion, you have to understand the properties that affect distortion. Some materials are more prone to deforming because of 2 properties, the physical and mechanical properties.
1. The physical property is the measure of thermal expansion and thermal conductivity.
- Thermal expansion is the movement of the metal as it expands when heated and contracts while cooling. If there’s a high coefficient, the material is more likely to expand and contract – thus it’ll distort more.
- Thermal conductivity, on the other hand, measures the flow of heat along the material. A high conductivity dissipates heat more quickly. Since the presence of heat makes a material prone to distortion, low conductivity increases the chances of deforming during welding.
2. In terms of mechanical properties, there are two things to consider, yield strength and modulus of elasticity.
- Yield strength refers to how much it can be stressed in reaction to external forces. So a material that has a higher yield strength has a higher residual stress – which is more prone to distorting.
- Modulus of elasticity refers to the ability of a material to expand and contract. A higher modulus of elasticity means a material has a greater ability to resist distortion.
Given these properties, you can assume that materials are prone to distortion if they have a higher coefficient of thermal expansion, low thermal conductivity, higher yield strength, and lower modulus of elasticity.
To give you context, take a look at these materials.
MATERIAL | COEFFICIENT OF THERMAL EXPANSION | THERMAL CONDUCTIVITY | YIELD STRENGTH | MODULUS OF ELASTICITY |
Stainless Steel | 10 | 0.04 | 45 | 29 |
Carbon Steel | 7 | 0.12 | 38 | 30 |
Aluminum | 12 | 0.50 | 20 | 10 |
Copper | 9 | 0.90 | 10 | 15 |
Comparing stainless steel with carbon steel, you can assume that the former is more prone to distorting because it has a higher yield strength and coefficient of thermal expansion plus a lower thermal conductivity.
Between aluminum and copper, the former is prone to distortion because it has a higher yield strength and coefficient of thermal expansion plus a lower thermal conductivity.
Types and Causes Laser Welding Deformation
Several studies have been conducted to pinpoint the real cause of distortion after a laser welding procedure. According to one study, 3 factors significantly affect the laser welding output: material, process, and geometry.
For instance, laser welding deformation happens because the welding parameters are applied differently across the surface of the metal. The welding speed, current, angle, etc will be concentrated on the part being welded. As you go further from the welding area, the heat will gradually go down and the thermal effects like metal expansion will be lower as well.
Because of this, it’s safe to assume that the expansion would vary depending on the heat intensity received by the metal. In the example given, the welded part will expand the most because it receives the most heat from the laser source.
When the welding procedure is over, the metal will start to cool and contract. The metal will keep contracting the same amount that it expanded. This is called residual stress.
If the stress is greater than the yield strength of the parent metal, two types of stresses may occur.
- Compressive stress happens on the surrounding area of the parent metal edges.
- Tensile stress happens when the contraction of the heated metal receives resistance from the rest of the metal’s surface (the one that’s not heated).
To understand this further, it’s best to consider the different ways that distortion can happen as the welding is completed.
1. Longitudinal Distortion
As the name suggests, this type of deformation happens along the length of the material being welded. When it cools, the weld and the area around it will contract. As a result, the workpiece will shorten. This will cause the outer edges to look longer and make the middle part look like an arc.
The deformation will be greatest especially if the workpiece isn’t secured properly.
2. Transverse Distortion
This type of distortion happens when the edges of the metal are pulled toward each other. This deformation is caused by too much contraction that exceeds the expansion that initially happened during the process of laser welding.
3. Angular Distortion
Angular distortion happens when the angles of the metal sheets are altered by the contraction after the welding task is completed. The edges of the metal sheet are pulled towards each other on one side – causing the material to look bent.
If the welding connects metal at a perpendicular angle, the vertical metal won’t appear straight but bent.
If you want to learn more about these three types of welding distortion, read this article.
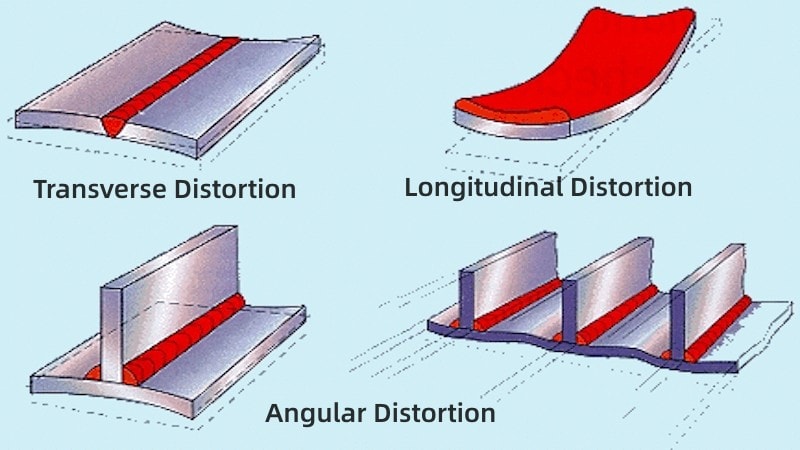
4. Complex Distortion
This type is a combination of the previous distortions discussed. It would look like buckling, bowing, or warping. These are all different types of curving and deforming that can compromise the integrity of the welded material. No matter how strong the metal is, if the laser weld causes it to deform, this will render the welding useless.
10 Ways to Minimize Weld Deformation
While distortion is unavoidable, that doesn’t mean there’s nothing you can do to minimize it. Just as there are different distortions, there are also various ways you can stop the deformation of stainless steel and other metals. It’s not about choosing the strength of steel. It’s more about what you do before, during, and after the welding task.
Here are 10 different weld ideas that you can use.
1. Avoid Overwelding
Welding a huge area would increase the contraction that will occur. This is why you should plan the laser weld process especially if you need to work on a huge surface. Sizing the surface will minimize the welding distortion and residual stress to keep you from wasting metal and time.
2. Use Intermittent Welding
This is a technique wherein you put space in between welds. Instead of a continuous weld, you’ll weld an inch, then leave space for unwelded metal, and then another weld. This is effective in minimizing deformation after the welding is done.
3. Do Fewer Passes
Another way to avoid distortion is to limit the number of passes during welding. Make sure one pass is enough to avoid deformation. You can try to perform a big weld pass instead of making several small passes. According to TWI, larger single weld deposits produce less angular distortion than welds made with multiple small weld passes
4. Think About the Welding Placement
The placement of the welding is also important. Ideally, you should place welds near the center or neutral axis of the material. This will minimize distortion in laser welding when it starts to contract because there will be less leverage when the shrinking forces try to pull out of alignment.
5. Try the Backstep Welding Technique
Backstep welding is a technique wherein the welding direction goes from left to right, but the bead segments are deposited from right to left. Doing this will expand the edges where the bead segments are placed to temporarily separate the metal plates.
As the movement of going left to right is completed, the succession of beads will cause the expansion to be less as the process is completed. This is an effective way to minimize distortion.
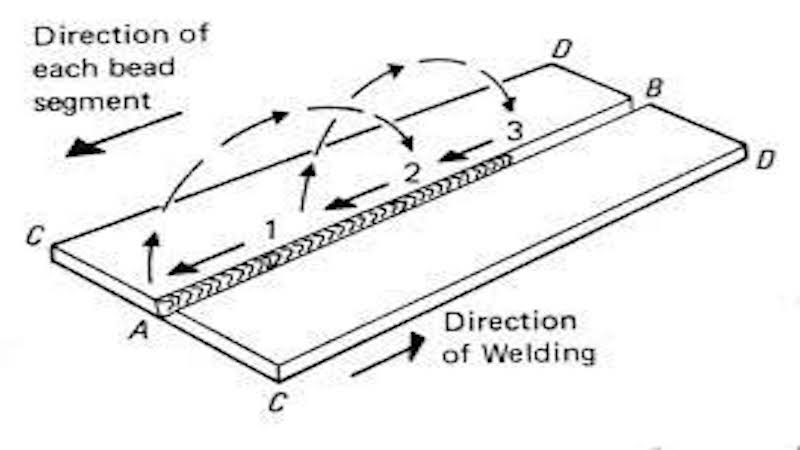
6. Preset Welding Parts
This would involve a few trials to ensure that you’re minimizing the distortion after the welding is completed. Determine the preset that was needed in those prior welds so you can estimate the shrinkage that you’ll encounter. This will allow you to make adjustments to minimize contraction and distortion.
7. Create A Welding Sequence
Don’t just weld parts using one straight line. Create a planned welding sequence that can counteract the shrinkage in another part of the material being assembled. With your knowledge of how the metal shrinks, you can create a sequence to balance the reaction to prevent distortion.
8. Clamp Parts to Lock in Place
Another option is to use a fixture while you’re welding parts together. This will hold them and keep the expansion or contraction from distorting them. Keep the parts clamped in place until the process is completed. The lack of movement will keep distortion down.
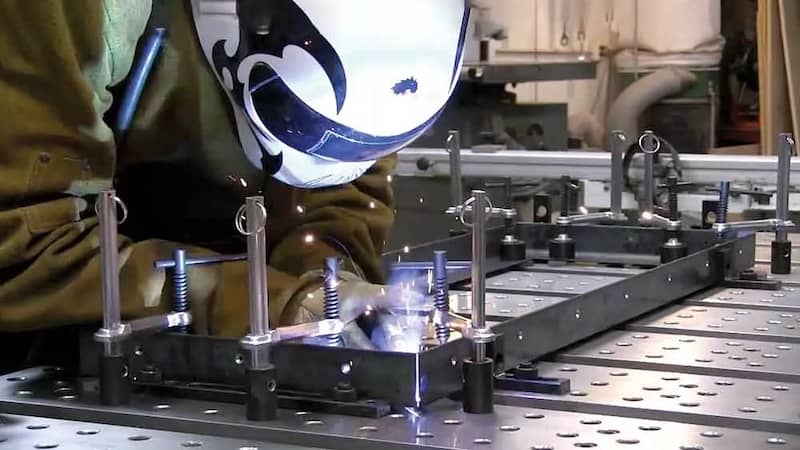
9. Consider Thermal Stress Relief
This is a technique where you control the heating and cooling of the parts connected by welding. It’s when you elevate the temperature and control the cooling to manage the stresses put on the product as it’s being welded.
10. Shorten the Welding Time
You can also shorten the welding time to lower the risk of distortion. This will be challenging if you do it manually. The parts you welded first would have cooled before you were done. However, if you have mechanized equipment used for welding, it can decrease the process time and keep the distortion at a minimum.
Can You Fix Welding Distortion?
In case distortion already occurred, don’t worry, there are ways to fix it without throwing away the project. Of course, you’ll have to analyze the damage to see if it can be reversed. Some distortions are too severe to rectify.
But in most cases, distortions can be fixed. There are two ways you can do this.
I. Thermal Correction
This corrective measure involves the use of thermal or heat to create local stress that’s high enough to pull a component back into the right shape. Some welders call this flame straightening and it can be applied in different ways.
- Spot heating. This is an effective way of removing buckles in metal sheets. The heat is applied to the convex or rounded part of the distortion. If the spots are small, this corrective measure can easily correct distortion after welding.
- Line heating. This heats the distorted part in a straight line – usually, this is along the welded joint. Make sure the heat is applied on the opposite side to correct any angular distortion.
- Wedge heating. This heats the wedge shapes found on the component to correct the distortion. This is used when large components are involved.
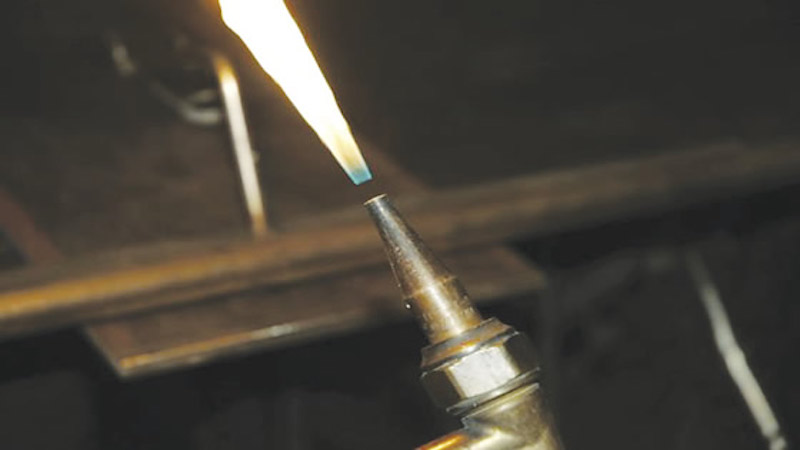
II. Mechanical Correction
Mechanical correction involves the use of force to fix distortion after welding. Depending on the gravity of the distortion or the thickness of the metal, you can use force to make the component flat.
There are two ways this can be applied, hammering and pressing. Among the tools that can be used to straighten the distortion include a hammer, pneumatic arm, wedge, or machine press. There are other tools that you can use.
FAQs About Welding Distortion
Dealing with distortion during the welding process is a common occurrence. But if you understand enough about how and why it happens, you can set up parameters that’ll allow you to minimize it.
Here are the common questions encountered when dealing with distortion during welding.
1. Why Does Weld Deformation Happen in Stainless Steel?
Due to the low thermal conductivity of stainless steel plates, it’s more prone to thermal expansion. The low conductivity means only a small part of the material is heated and expanded. The rest remains cooler and thus won’t change while the welded joint is being completed.
Once the welding is done and the welded part is cooling, it can pull the rest of the material as it contracts. This is what causes it to distort more. This can be solved by countering the rapid heating and cooling during the stainless steel laser welding.
2. Can You Control Metal to Avoid Distortion Through Welding?
You can’t control how metal reacts to heat or laser while it’s being welded. However, you can understand the factors that contribute to the distortion so you can minimize its effects. With careful planning, these factors can be controlled so the heating from the laser weld will balance the cooling process to avoid deforming the metal.
3. Do You Need An Expert Welder to Avoid Distortion?
Having an experienced welder will help avoid distortion while welding. Experts have sufficient knowledge and experience to minimize or completely avoid distortions during welding. However, it’s not the only solution. As long as you understand the techniques that can minimize the distortion, it shouldn’t compromise the material you’re welding.
Don’t Let Welding Deformation Compromise Your Metals
Distortion is a common effect of laser welding. It’s a result of metal’s reaction to heat. However, you can minimize its impact as long as you understand how the distortion happens. There are things that you can do to balance or counteract these natural reactions.
You can use clamping or specific welding techniques like backstep, sequences, etc. These can keep distortion from happening. Using the right tools will also make it easier to maintain the integrity of the metal structure.
Of course, you can also partner with an expert or professional welder to make things more convenient for you.
Get Effective Solutions From Baison to Minimize Welding Distortion!
Dealing with distortion during the welding process can be challenging – but only if you’re not using the right tools. Don’t compromise your production and projects by using sub-standard tools. Baison Laser provides high-quality solutions to your laser welding needs.
Ensure precision and efficiency by minimizing distortion. Get in touch with Baison Laser so we can help bring your projects to completion through state-of-the-art laser technology.