Our goal is to shed light on the versatile potential of laser welding technologies and showcase their relevance across a range of sectors.
What Is Laser Welding?
Laser welding, a sophisticated joining technique, employs a highly concentrated beam of light to fuse materials together. Focusing the laser’s energy on a specific area generates localized heat, which melts and solidifies the workpieces to create a strong bond. This leading-edge process is highly valued for its precision, speed, and adaptability, making it an ideal solution for a wide array of industries.
The remarkable accuracy of laser welding ensures minimal distortion and reduced thermal stress on the materials being joined. As a result, this method is highly suitable for intricate designs and delicate components.
Furthermore, its non-contact nature allows for welding hard-to-reach areas, enabling manufacturers to expand their production capabilities and optimize their processes.
What Is Conduction Welding and How Does It Work?
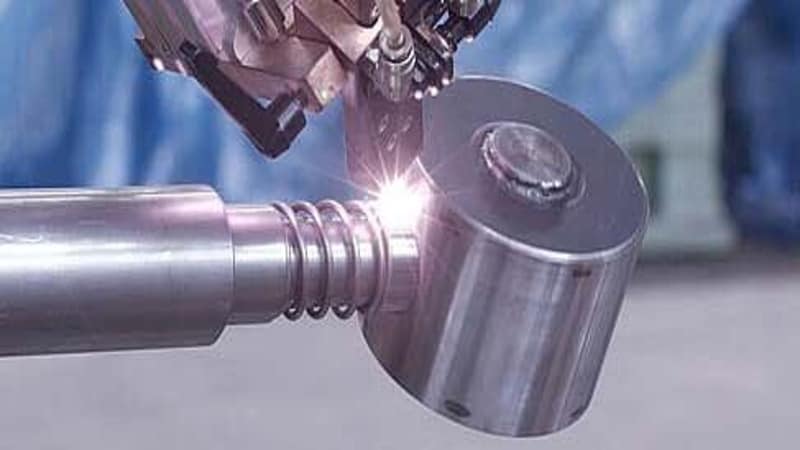
Conduction welding, one of the primary modes of laser welding, is a low-energy-density process that results in a shallow, wide weld. This method suits materials with low melting points or when a minimal heat-affected zone (HAZ) is desired. Conduction welding is commonly used in industries such as electronics, automotive, and medical devices.
How Does Conduction Welding Work?
1. Laser Energy Control: In conduction welding, the laser power energy density is carefully regulated to ensure that it remains below the threshold required for deep penetration. This control helps to prevent excessive heat from damaging the workpieces and surrounding areas.
2. Material Melting: The laser beam heats the material’s surface, causing it to melt and form a molten metal pool. The energy from the laser is conducted through the material, leading to a smooth, uniform weld bead.
3. Solidification: As the laser moves along the intended welding path, the molten pool cools and solidifies, creating a durable bond between the workpieces. This process results in a weld characterized by its wide, shallow profile and minimal HAZ.
What Is Transition Welding and How Does It Work?
Transition welding, also known as conduction-to-keyhole welding, occupies the middle ground between conduction and keyhole welding modes. This intermediate process combines the benefits of both methods, resulting in welds with moderate penetration depth and limited heat-affected zones with the transition period.
Transition welding is well-suited for applications requiring a balance of strength and minimal thermal impact, making it a popular choice in the aerospace, automotive, and electronics industries.
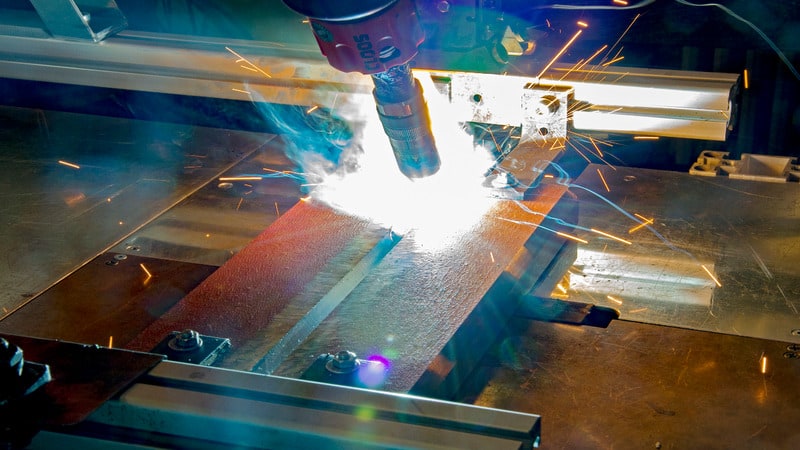
How Does Transition Welding Work?
1. Laser Energy Adjustment: In transition welding, the laser’s energy density is fine-tuned to strike a balance between the low-energy-density conduction mode and the high-energy-density keyhole mode. This precise control allows for moderate penetration depth while minimizing workpiece thermal stress.
2. Partial Keyhole Formation: The laser heats the material, creating a partially formed keyhole surrounded by a molten pool. This semi-keyhole state enables the weld to achieve greater penetration depth than conduction welding while limiting the heat-affected zone.
3. Controlled Solidification: As the laser progresses along the welding path, the partially formed keyhole and surrounding molten pool cool and solidify, establishing a strong bond between the workpieces. The resulting weld exhibits a balance of strength, depth, and minimal thermal impact on the material.
What Is Keyhole Welding and How Does It Work?
Keyhole mode welding, the third primary mode of laser welding, is a high-energy-density process that enables deep penetration welding with narrow weld profiles. This method is ideal for applications that demand strong, durable bonds with minimal material distortion. Keyhole welding is commonly utilized in heavy machinery, shipbuilding, and aerospace industries.
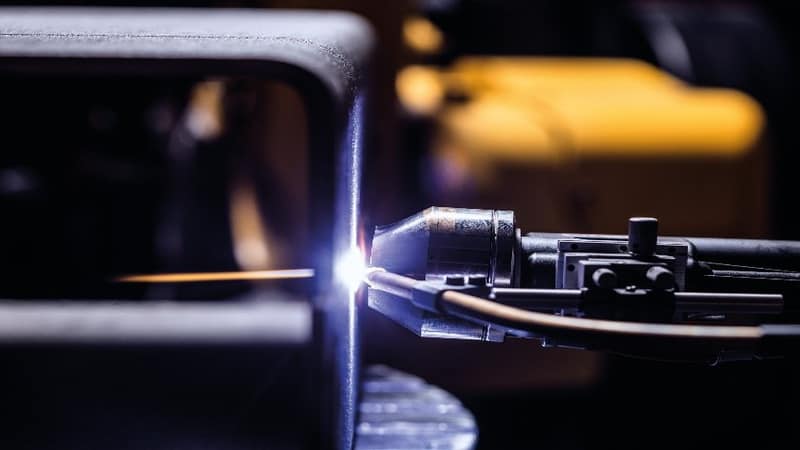
How Does Keyhole Welding Work?
1. High Laser Energy Density: In keyhole welding, the laser’s energy density is significantly higher compared to conduction and transition welding modes. This increased energy allows for deep penetration into the materials, resulting in strong welds.
2. Keyhole Formation: As the laser beam interacts with the material, it vaporizes a portion of it, forming a narrow, deep cavity called a keyhole. The keyhole’s walls are lined with molten material, which absorbs the laser energy and maintains the keyhole’s stability.
3. Weld Pool Formation and Solidification: The molten material surrounding the keyhole flows and fills the space behind it as the laser moves along the welding path. This process forms a continuous weld pool, which subsequently cools and solidifies, creating a strong, durable bond between the workpieces.
Advantages & Disadvantages of Conduction, Transition, and Keyhole Welding
The table below lists the advantages and disadvantages manufacturers face with each type of welding:
Welding Mode | Advantages | Disadvantages |
Conduction Welding | · Minimal heat-affected zone (HAZ) · Low distortion and thermal stress · Ideal for materials with low melting points · Suitable for delicate components and intricate designs | · Shallow penetration depth · Lower strength compared to other modes · Not suitable for thick or highly conductive materials |
Transition Welding | · Moderate penetration depth Limited heat-affected zone (HAZ) · Balances strength and minimal thermal impact · Applicable to a wide range of industries and applications | · Not as strong as keyhole welding · More HAZ than conduction welding · Less control over weld profile compared to other modes |
Keyhole Welding | · Deep penetration depth · Narrow weld profile · High strength and durability Suitable for thick or highly conductive materials | · Greater heat-affected zone (HAZ) than conduction welding · Potential for material distortion and thermal stress · Not ideal for delicate components or materials with low melting points |
Different Applications of Conduction, Transition, and Keyhole Welding
We have listed all the relevant industrial applications for all three types of laser welding techniques:
Welding Mode | Applications |
Conduction Welding | · Electronics · Aerospace · Medical Devices · Jewelry · Precision Equipment |
Transition Welding | · Automotive · Shipbuilding · Construction · Consumer Goods · Defense |
Keyhole Welding | · Heavy Equipment Manufacturing · Shipbuilding · Aerospace · Automotive · Construction |
Best Practices for Choosing the Right Laser Welding Mode for Your Job
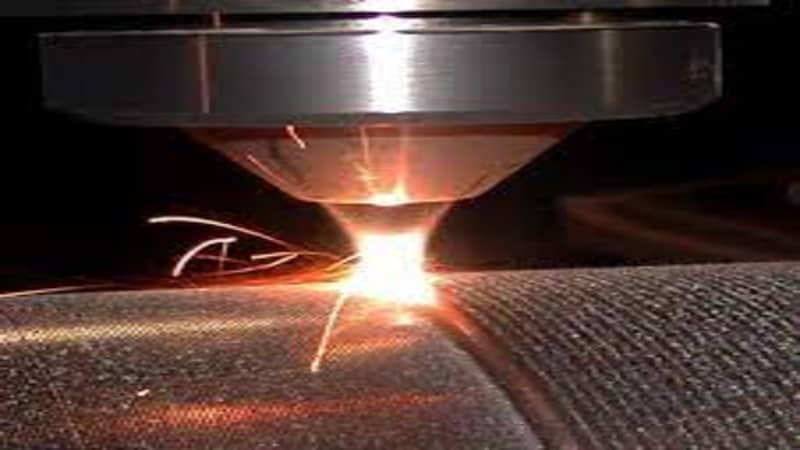
1. Analyze Material Properties: Assess the properties of the materials you intend to weld, including their melting points, thermal conductivity, and thickness. This analysis will help you determine your specific materials’ most appropriate welding mode.
2. Assess Heat-Affected Zone (HAZ) Tolerance: Understand your components’ acceptable thermal stress and distortion level. If minimal HAZ is crucial, consider using conduction or transition welding. Keyhole welding may be a viable option for applications that can tolerate more significant HAZ.
3. Consider Component Sensitivity: Consider the sensitivity and intricacy of the welded components. Delicate and intricate parts may require conduction welding, while more robust components may be better suited for transition or keyhole welding.
4. Consult an Expert: Seek advice from laser welding professionals who can guide on selecting the most suitable welding mode for your specific project. Their expertise can help you optimize your welding process for the best possible results.
5. Evaluate Desired Weld Strength: Determine the required strength of the weld for your application. For projects demanding high-strength bonds, keyhole welding might be the best choice. In contrast, conduction or transition welding may be sufficient for applications with lower strength requirements.
Tips on Achieving Optimal Results with Laser Welding
Here are five tips to help you achieve optimal results with Laser welding:
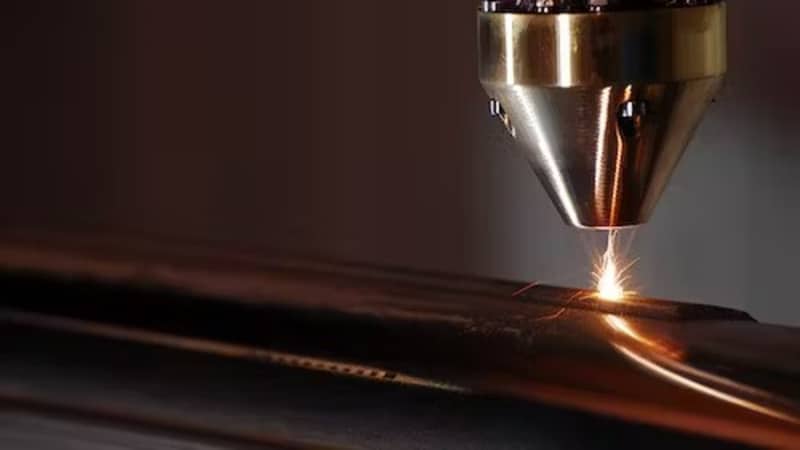
1. Proper fit-up and joint preparation are crucial for achieving optimal results with laser welding.
2. Use the correct laser parameters and settings for the specific material being welded.
3. Maintain cleanliness of the workpiece and surrounding area to prevent contamination.
4. Use shielding gases to protect the weld area from oxidation and improve weld quality.
5. Monitor and control heat input to prevent overheating and distortion of the workpiece.
Conclusion
Laser welding is a highly precise and efficient welding technique used in various industries to join different materials.
To achieve optimal results with laser welding, it is essential to ensure proper fit-up and joint preparation, use the correct laser parameters and settings, maintain cleanliness, consider using shielding gases, and monitor and control heat input.
If you are interested in learning more about laser welding machine, be sure to check out our website for additional resources and information.
Discover the Perfect Solution for Your Business with Baison
With Baison‘s expertise in laser technology, we can provide you with state-of-the-art laser machines and reliable technical support to ensure that your production runs smoothly. Our team of skilled engineers can work with you to understand your specific needs and develop a customized solution that meets your budget and timeline. Contact us today.