So we decided to demystify this process by breaking down the differences between laser and TIG welding. Continue reading the article to find out which welding process is the best for your applications.
What is Laser Welding?
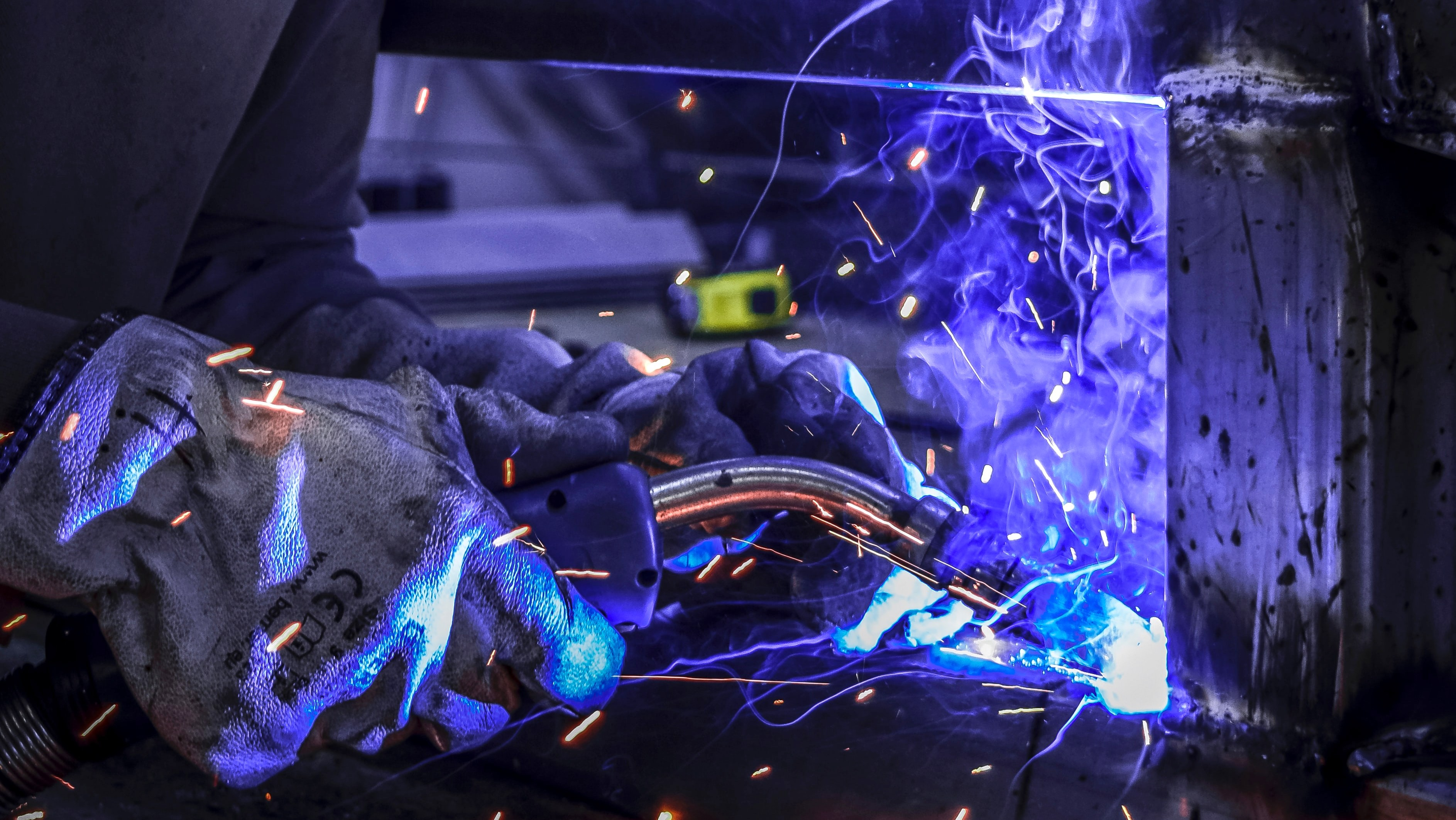
Laser welding is the process of joining metals, plastics, and composites through the use of a high-powered laser beam. The laser beam provides a concentrated and continuous blast of energy onto a very small point that selectively brings the workpiece to its melting point. This process is also known as laser beam welding.
Laser is an acronym for “light amplification by stimulated emission of radiation.” If the laser is too powerful, it will cut through the workpiece. Laser cutting and welding operations work on the same basic principle but differ in application.
7 Key Advantages of Laser Welding
Laser welding is a highly versatile and adaptable welding process that can be utilized in several manufacturing sectors. Its unique approach to metal bonding will allow you to tackle several challenging projects.
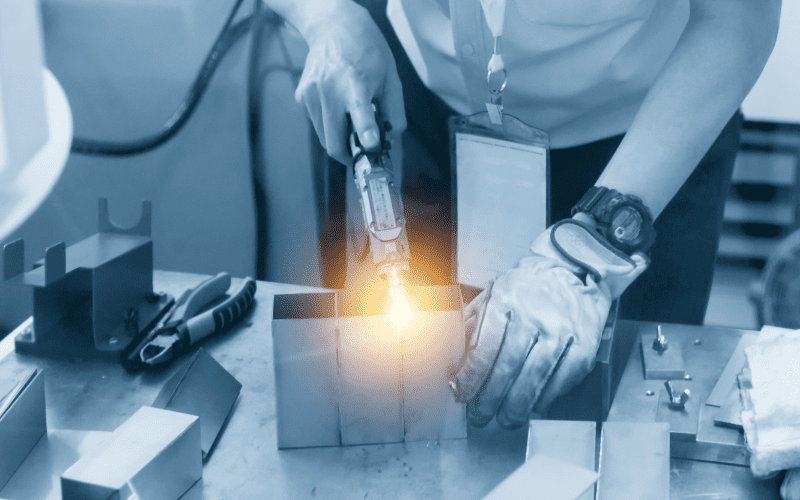
1 – Easy Automation
Unlike TIG welding, laser welding excels in automated manufacturing processes. The laser component here is more compact and easier to mount on a CNC-controlled machine. This welding method’s lack of filler material also helps with automation.
2 – No Filler Material Required
Many welding techniques require a filler material that is melted and filled between two adjacent workpieces to create a bond. TIG welding uses consumable tungsten filler rods that need to be replenished regularly. However, laser welding avoids this step and offers a more convenient option.
3 – Less Heat Generation
Laser welding is a very controlled process. You only use the minimum amount of energy needed to weld materials together. Traditional welding processes lack fine control, which can lead to a significant amount of energy wasted as excess heat.
4 – Precision Welding
The laser contact point in this process is very small. All the energy required to weld materials is concentrated in a single point. The smaller contact surface can help fine-tune the welding process. You have full control of the laser beam and can use it for precision welds on small parts.
5 – Better Weld Quality
Laser welding produces high-quality welds with a nice and even surface finish. You don’t have to compromise on the welding speed to achieve those excellent results. The only other welding technique that produces better welds would be resistance spot welding.
6 – Wider Material Compatibility
Laser welding is a compact, considered, and controlled process. It’s compatible with both metal and non-metal materials like thermoset plastics. Traditional welding would end up melting plastics before you can even begin to start the weld. Even thin materials like aluminum foils can be welded together using lasers.
Laser welding is compatible with the following metals and their alloys.
- Carbon Steel
- Stainless Steel
- Copper
- Aluminum
- Magnesium
- Plastics
- etc.
However, lasers are primarily used for steel and aluminum welding in most industrial sectors.
7 – Diverse Operation Techniques
The term laser welding machine can refer to several different configurations of welding equipment. You can weld using three different types of lasers, operate the laser in two different modes, and run the laser continuously or in pulses.
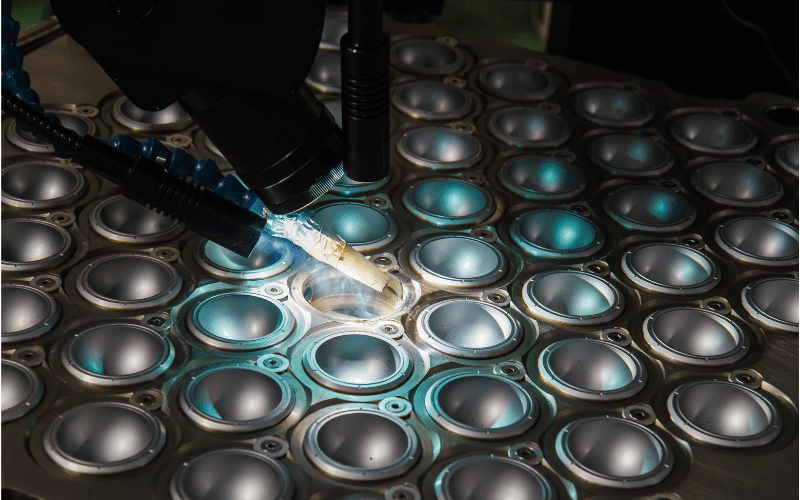
Different Approaches to the Laser Welding Process
Laser welding is a diverse and complex process, and you can use different variations and operational techniques to get the most out of your laser welding machine. We can take three approaches based on laser choice, power output, and operations.
1 – Different Types of Laser Welding Equipment
Laser welding methods can be categorized based on the type of laser used in the welding process. The following are three major types of laser welding methods.
Gas Laser Welding
Gas lasers use a carbon dioxide and nitrogen gas mixture heated inside a quartz tube using an electric current. The gas mixture goes through a chain reaction, producing a watery discharge of photons. Mirrors on the ends of the quartz tube reflect the photon beam until it is applied to a sufficient degree.
Gas lasers have a lower upfront cost but wear out quickly after continuous use. CO2 gas lasers are commonly used in the automotive industry for welding large pieces of the car frame.
Solid-state Laser Welding
Solid-state lasers rely on a glass or crystalline material as a gain medium instead of a gas mixture. Here the crystalline medium is exposed to a bright light that excites its internal atoms leading to a discharge of photons. Mirrors on the ends of the crystal amplify the photons until a concentrated laser beam is achieved.
Solid-state lasers are commonly used for thicker materials that require deeper penetration of the laser beam. Neodymium-doped Yttrium-Aluminum-Garnet (Nd: YAG) is a commonly used gain material in solid-state laser welding.
Fiber lasers are a subcategory of solid-state lasers that rely on an optic fiber as a gain medium. The fiber optic wire is pumped with a light source, and the internal reflections of the light beam amplify it into an intense laser. Fiber lasers have a higher upfront cost, but they are also very long-lasting. This makes fiber optic laser welding systems the most cost-effective option in the long run.
Semiconductor Laser Welding
Semiconductor lasers pass an electric current through a semiconductor diode to generate radiation. The radiation is then amplified into a concentrated laser beam. Such lasers are quite compact as they don’t rely on large lamps to excite the diodes.
Semiconductor laser welding is a powerful manufacturing tool rarely used due to its lower efficiency and complex construction.
2 – Different Laser Welding Modes
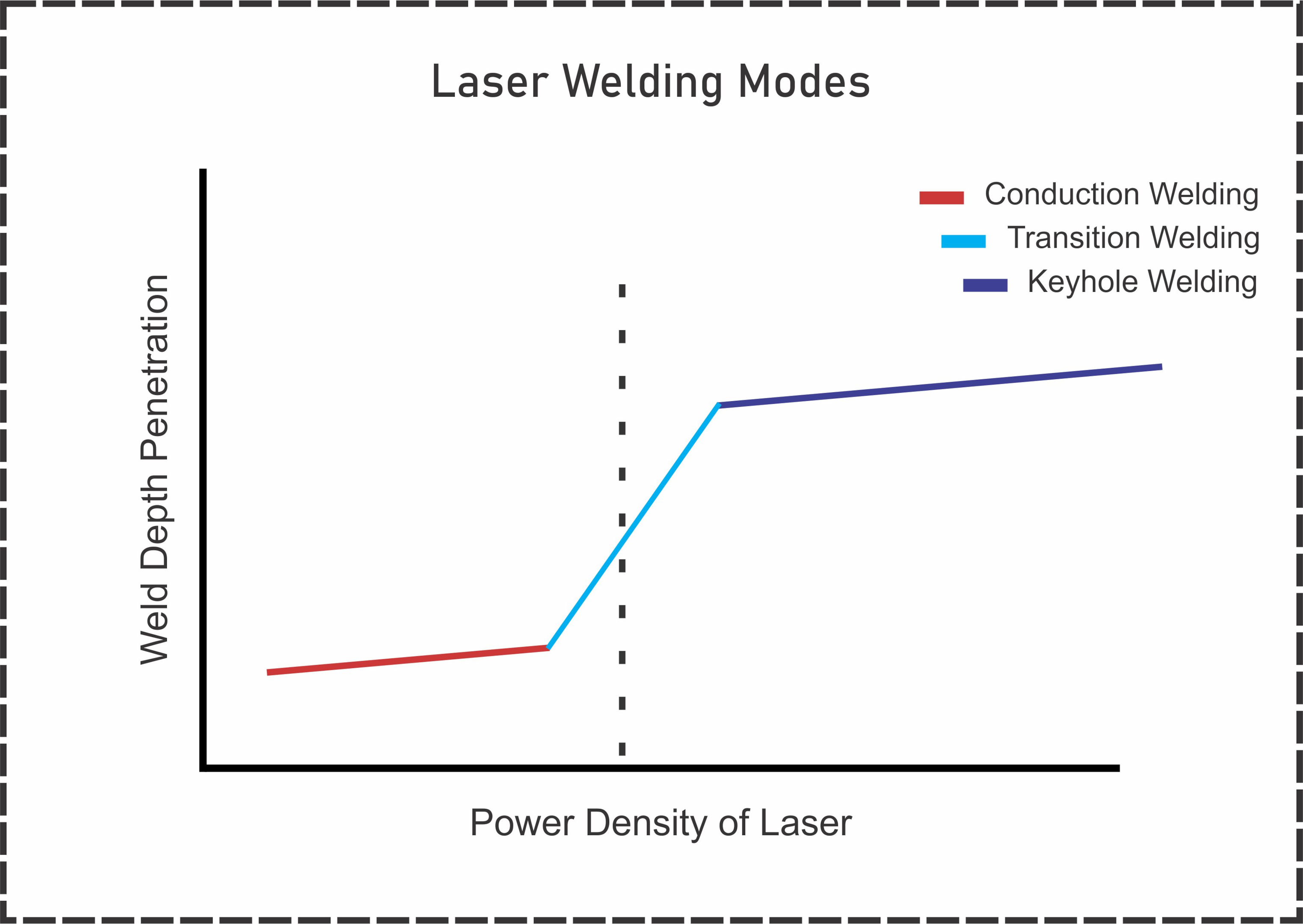
Laser welding techniques can help maximize the efficacy of your weld. You can change the welding process by changing the power density of the laser beam. The different power density options for laser welding are called modes.
Here are three laser welding modes that will help elevate your fabrication skills.
Conduction Welding Process
This welding process uses lower-powered laser beams, approximately 500kW/cm2. As you are using much smaller amounts of energy to melt the workpiece, you will not be able to get deeper penetration. All the excess energy is absorbed by the surroundings, leading to a wider weld area. This type of welding produces a more aesthetically pleasing and even weld.
Keyhole Welding Process
This laser welding process is the exact opposite of the condition method. Here the laser is cracked up to its maximum power, generally around 1500kW/cm2. The higher energy output leads to much deeper penetration into the workpiece. This welding method can lead to workpiece temperatures of over 10,000 K or approximately 17,500 °F.
Transition Welding Process
The jump between condition and keyhole welding is a gradual one. Staying between the two laser power densities can lead to a median laser welding process. Transition welding has better material penetration than the conduction welding method and maintains a wider weld surface finish.
3 – Different Laser Welding Operation Techniques
A typical laser welding system is quite versatile and can vary based on the type of laser or the welding mode. However, there is another method you can use to expand the laser welding applications further. You can use the laser in a pulse mode for a quick and effective laser weld.
Continuous Wave (CW) Laser Welding
The continuous laser welding method is your standard operating procedure. Here the laser will continuously contact the workpiece while it is welded together. You will need continuous laser welding when dealing with thicker materials, as this method will lead to deeper penetration.
Metals like high-carbon steel will crack under certain welding conditions. All the heat input from the continuous laser beam keeps the carbon steel in a more stable condition.
Pulsed Laser Welding
Pulsed laser welding involves minimum laser-to-workpiece surface contact. The laser spot welds the workpiece in short discontinuous bursts, where all the heat input takes place in a fraction of a second. You can create seam welds by overlapping the spot welds.
The pulse laser welding process is favored for its quick and durable spot welding capabilities. Sensitive materials like plastics can easily melt due to the high heat input of laser welding. Pulsed laser welding solves this problem as the material is only exposed to the laser beam for a short time.
You may want to learn some of the basics of laser welding.
Magnesium Alloy Welding Capabilities and Limitations
Laser welding can often run into challenges when dealing with sensitive metals. Magnesium alloys, in particular, have multiple points of welding failure attributed to their microstructure. The following is a brief overview of the magnesium welding capabilities and limitations of laser welding.
Magnesium can exhibit several post-weld problems like high porosity, weld defects, sag, solidification cracking, etc. Many of these issues cannot be rectified using post-processing options. So, we generally advise against using magnesium alloys with your welding machine.
A joint study conducted by several Canadian research institutes goes through several laser welding techniques and summarizes their compatibility with magnesium alloys. It concluded that magnesium alloy welding is a very unreliable process with high porosity, oxidation, and solidification crack generation rates. The researchers hope future investigation into the topic will improve magnesium alloys’ weldability.
Commercial-only CO2 and Nd: YAG (neodymium-doped yttrium aluminum garnet) are used for magnesium welding. However, with continuous advancements in manufacturing techniques, we may soon see other laser welding techniques take over.
What is TIG Welding?
TIG or tungsten inert gas welding is a traditional method that uses powerful electric currents to facilitate the welding. In this process, the two metal electrodes are the workpiece and the non-consumable tungsten electrode. As the current passes through the tungsten rod, it generates a powerful electric arc of around 6000 °F (~3300 °C). A consumable filler metal rod is placed at the center of the arc, where it melts and welds the workpiece.
The entire process is performed under the high-pressure flow of inert gasses. The inert gas shielding helps keep debris, rust, and other impurities away from the weld. Tungsten inert gas welding typically uses argon or helium for shielding.
You can TIG weld without using a filler material. Such a process is called autogenous fusion welding. This process relies on the heat input to melt and fuse the workpiece. Like other traditional welding methods, TIG welding is more difficult to automate.
6 Key Advantages of TIG Welding
TIG welding has been around for almost 80 years now. During this time, several optimizations and innovations in the welding method have led to a more mature manufacturing process.
The following are some of the most critical advantages TIG welding has over its competition.
1 – Wider Metal Compatibility
Though it can’t weld plastics, TIG welding makes up for this by offering a much wider range of metal options. The following are popular metal options that are used with TIG.
- Steel
- Stainless Steel
- Aluminum
- Nickel
- Magnesium
- Copper
- Bronze
- Gold
- Chromoly
This traditional welding process can accommodate both thin sheets and thick plates. Thinner metals are always challenging to weld, as their low thermal mass can cause defects, warping, and thermal distortion. But TIG welding is more than capable of adapting to these challenges.
2 – Enables More Detailed Welds
TIG welding relies on a non-consumable tungsten electrode and a consumable metal filler material. This filler flows into small gaps and crevices, providing better weld coverage. It enables the operator to use the welding machine more versatilely to get high-quality welds.
3 – Decreased Chances of Post-Weld Cracking
Traditional welding outputs more heat into the metal workpiece, which takes a long time to dissipate. The slower cooldown rate allows the post-weld materials to avoid thermal shock. Thermal shock occurs when the material undergoes rapid temperature changes, often leading to crack formation and warping.
4 – Cost Effective
All traditional welding techniques are more cost-effective than laser welding options. This comes down to the lower upfront investment required to set up a traditional welding machine. The cost of TIG-welded parts is considerably less than laser-welded ones.
5 – Fast Operator Adoption
Most experienced welding machine operators have been trained on traditional welding equipment. Therefore, they face a harsh learning curve when suddenly asked to operate a laser welding machine.
If you have legacy welders employed, it might be more convenient to use TIG welding. Their experience can help compensate for the shortcomings of traditional welding. An experienced TIG welder will always be faster than an amateur laser welder.
6 – Diverse Welding Techniques
Traditional TIG (inert tungsten gas) welding is a small part of the larger arc welding method. You have the option of using several different variations of the existing TIG welding process. You can use flux-coated filler rods, change the tungsten electrode for another metal, and switch between AC & DC power supplies.
Variations on the TIG Welding Process
1 – Traditional Welding Alternatives to TIG Welding
Arc welding is a simple process that varies based on the type of metal used. TIG is a specialized form of arc welding that can turn into a completely different arc welding method with slight changes.
MIG Welding
MIG or metal-inert gas welding is a traditional arc welding process that uses a consumable non-tungsten electrode to carry out the operations. Here, instead of separate filler material, the MIG electrode is consumed during the welding process. MIG welding uses the same gas shielding techniques and electric current as TIG.
Stick Welding
Stick and TIG are two very similar arc welding methods with only one small change between them. TIG uses inert gasses for shielding, while Stick uses a flux-coated filler metal. As the filler material melts, the flux coating vaporizes and forms a protective layer over the welded metal.
Flux-cored ARC Welding
This arc welding technique uses a special tubular electrode with a flux filling inside. Flux-cored arc welding is MIG welding but with a specialized filler rod instead of gas shielding. You can think of flux-cored welding as a combination of Stick and MIG welding methods.
2 – Different Current Modes for TIG Welding
As the primary driver of arc welding is electricity, you can use AC or DC supplies to power your welding machine.
Alternate Current
Alternating current (AC) is a unique method of transmitting electrical power over a large distance. Here the current constantly flips its polarity following a sine wave pattern. AC current-generated arcs can penetrate much deeper into the metal.
Direct Current
Direct current (DC) transmits electrical power in a single continuous run. This method can penetrate deep into the workpiece. Hence the excess energy accumulates at the surface leading to higher arc temperatures.
Both AC & DC arc welding methods can overcome the magnetic fields of ferrous metals.
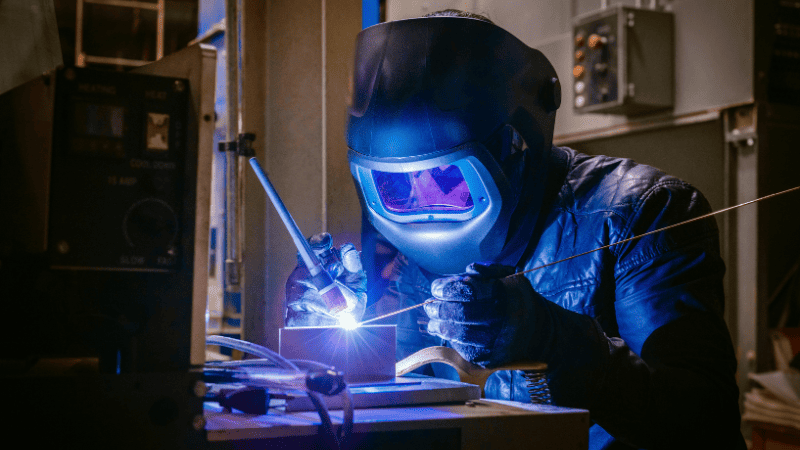
3 – Various Arc Starting Options
Traditional welding often requires a starter to get an initial arc going. This arc needs to be ignited quickly and conveniently to avoid welding hassles.
Scratch Start
This older method involves scratching the electrode against the workpiece to start an arc. After the arc starts, the operator needs to lift the electrode. If the electrode is not lifted quickly, it will stick to the workpiece, and if it’s lifted too high, the arc will dissipate.
Lift Start
Lift start involves a smart sensor that can tell when an electrode comes in contact with the workpiece. This method involves gently pressing the electrode against the workpiece and immediately lifting it. The control circuit will ignite the arc once it senses that the electrode has been lifted off.
HF Start
HF (high frequency) starters use a separate circuit to ignite the arc with a button. You bring the electrode close to the workpiece and press the HF starter button.
We do not recommend scratch start methods for TIG welding as they are less reliable. Ideally, you should be using a lift or HF arc starter option.
Low Penetration of TIG Welding
All traditional welding techniques suffer from a lack of decent weld penetration. You can compensate for much of this shortcoming by using different tricks, but the results might not be consistent.
A review paper from 2017 went through the various arc welding methods to outline the improvements to the TIG welding process. Their research leads them to three TIG welding methods with significantly better weld penetration.
A-TIG
Activated flux TIG welding shows significant improvement over the base TIG process. The flux leads to a narrower but deeper weld pool, leading to better weld penetration.
FB-TIG
Flux-bounded TIG welding also provides significant improvements in weld penetration. But it comes with a major drawback. Increasing the contact distance between the electrode and the workpiece will immediately reduce the weld depth.
PC-TIG
Pulsed-current TIG welding will increase weld penetration if the peak current is quite high. A longer pulse duration will also lead to more uniform thermal distribution on the workpiece.
What is the Difference Between Laser Welding and TIG Welding?
There are several differences between these two welding options. And we can’t possibly list every single one in this article. Instead, here is a table comparing the biggest differences that will affect your welding applications.
Operation | Laser Welding | TIG Welding |
Gas Shielding | Requires the use of a separate CO2 nozzle over the weld area. | Uses inter gasses, like Argon or Helium |
Filler Material | Does not require the use of a filler metal | Use of a filler metal is very common |
Gap Coverage & Bridging | The lack of molten filler metal leads to lackluster gap coverage | The filler metal fills in neighboring gaps and bridges them. |
Welding Process | Uses a concentrated laser beam to selectively melt the workpiece | Uses heat generated from an electric arc to melt and fuse the workpiece |
Thermal Stresses & Distortions | Less energy is input into the workpiece leading to smaller stresses and fewer distortions | High thermal energy is input into the workpiece leading to high stresses and more thermal distortions |
Applications | Industrial Work | Personal Projects |
Automotive | Automotive | |
Jewellery Making | Construction | |
Medical Equipment | Petroleum | |
Electronics | Metal Repairs | |
Aerospace | ||
Productivity | Faster welding speeds lead to quicker production times | Slower welding speed can result in lower productivity |
Cooling Rate | Faster cooling due to the low amount of heat input into the workpiece | Slower cooling rate |
Crack Formation | Can occasionally lead to brittle phases in the workpiece | Higher chance of cracking on solidification |
What is Laser Welding Good for?
Laser welding is a great option for large-scale manufacturing facilities that regularly use welding to join metals. Laser welding is quicker and more versatile than a TIG torch. The cost of the laser beam welding machine is negligible for a large manufacturing operation.
What is TIG Welding Good for?
TIG welding is great for small-scale metal workshops that occasionally need welding services. This process is less costly than laser welding and is generally more compact. Replacing filler material rods is cheaper than buying a laser welding machine.
If you deal with different metal alloys, you will benefit more from TIG welding.
Is Laser Welding Better than TIG Welding?
The short answer is “Yes.” Laser welding is better than traditional TIG welding. However, we cannot see label lasers unanimously as the best solution, as there are some applications that benefit more from TIG welding.
If you don’t mind the constant need for replenishing the filler metal and your applications involve welding various metal alloys, you should use TIG. But for everything else, your best option is to use laser welding.
When Should You Use Laser Welding instead of TIG Welding?
The choice between TIG and laser mainly comes down to your particular application. The following is a list of laser welding-suited scenarios. If your applications align with this list, we recommend you choose laser welding.
- Precision and Detailed Welding
- Faster Welding Times
- Less External Contamination
- Vertical and Overhead Welding Applications
- Smaller Heat-Affected Zone
- Automated Welding Setup
- Negligible Deformation and Shrinkage
- Higher Quality Welds
Laser-Hybrid Welding
You may need a hybrid welding approach if you have gone through this entire article and have not found a satisfying answer. Laser hybrid welding involves using lasers and electric arcs to weld materials.
The laser brings the workpiece close to the vaporization temperature, and the arc adds the required heat. Filler metal then fills in the gap between the workpiece.
Applications
Hybrid laser welding is a specialized technique that is partially useful for high-carbon and stainless steel alloys. The following industries primarily use this technology.
- Heavy Machinery Manufacturing
- Automotive Industry
- Ship Building Work
- Large Scale Projects
Studies have tried to find more applications for hybrid laser welding. The consensus is that you should pair a high-powered laser with a low-powered electric arc for the best results.
Advantages
- Excellent for welding thicker materials.
- Faster than TIG welding.
- Produces high-quality welds.
- Reduce chances of cracking.
- Easy to automate.
- Cost-effective for large-scale productions.
Disadvantages
- Unfit for small-scale welding applications.
- Requires significantly large upfront investment.
- Operators require advanced welding training to handle this hybrid approach.
From its name, you might conclude that laser hybrid welding is the best of both worlds. But in reality, this approach has less versatility than TIG or laser welding. This is a very specialized approach to metal welding and is generally not applicable to most welding applications.
Conclusion
So there you have it, folks, a complete and detailed guide to laser and TIG welding. However, both methods are helpful in their own right. Their benefits can significantly increase or decrease based on the application and the work environment.
Remember that TIG has a smaller initial investment cost and frequently requires you to replenish the filler metal rods. While Laser welding is more expensive, it’s also faster, more versatile, and hassle-free.
Get Laser Welding Machines from Baison Laser
Baison Laser is one of the leading fiber laser system manufacturers. We offer high-quality, reliable, and durable laser systems for all industries. Without a doubt, our laser welding machines are the best in class. We have a diverse range of products that will accommodate all your laser cutting, welding, marking, and cleaning needs.
For more information on our products and to get your laser welding machine, Contact us Today!