In the ever-evolving landscape of manufacturing and fabrication, precision welding is a highly sought-after technique. Recent years have seen laser welding rise to the top of the competition as a go-to solution. As industries seek to optimize their production processes, assessing the strengths and limitations of different welding techniques has become critical.
In this article, we highlight the differences between laser welding and traditional welding techniques.
What is Laser Welding?
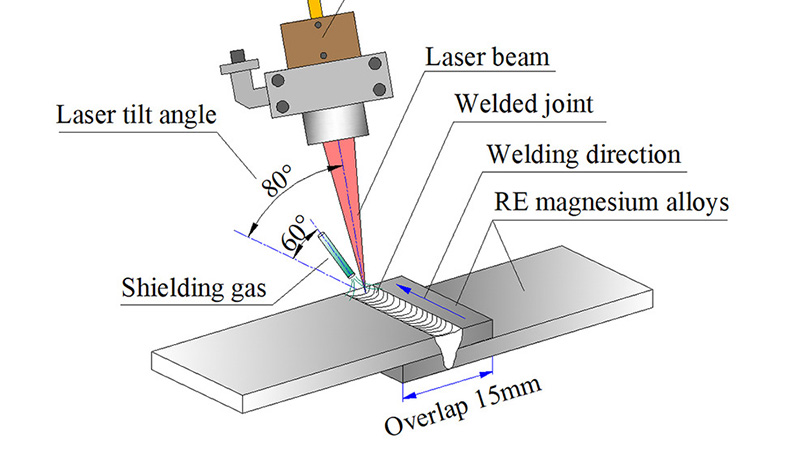
The laser welding process uses a concentrated laser beam to selectively melt and join two or more materials together. Except for some handheld laser welders, most laser welding is CNC (Computer Numerically Controlled), resulting in higher precision across the board.
A key design feature of laser welding is its ability to focus lots of energy into a single point and input high heat into the workpiece in a fraction of a second. The short burst of high heat input results in deep laser penetration while minimizing the heat-affected zone (HAZ).
Types of Laser Welding Machines
The laser welding system can be categorized into several categories based on laser source and mode of operation.
Laser Source
- Gas Laser Welding – Uses a CO2 gas mixture to amplify the laser beam.
- Solid State Laser Welding – Uses a crystal core for light amplification.
- Fiber Laser Welding – Specialized solid-state welding technique that uses optical fiber cables.
- Diode Laser Welding – Uses semiconductors for light amplification.
Laser Operation
- Conduction Laser Welding – Involves heating and melting the material’s surface until it fuses.
- Keyhole Laser Welding – Uses a high-intensity focused laser beam to vaporize metal, creating a hole in the material.
- Pulsed Laser Welding – The laser beam rapidly turns on and off, hitting the work material in pulses. Uses less energy and reduces the heat affected zone.
- Continuous Laser Beam Welding – The laser beam stays on during the entire welding process. Primarily used for welding thicker materials.
Material Compatibility
Unlike traditional welding methods that rely on electrical conductivity to heat and fuse metals, lasers rely on heat generated through light. Meaning, lasers can effectively weld metals and non-metals.
Here are some of the most popular laser welding materials.
Metals
- Carbon Steel
- Stainless Steel
- Copper and Alloys
- Aluminum and Alloys
- Magnesium and Alloys
- Nickel and Alloys
- Titanium
- etc.
Non-Metals
- Ceramics (Alumina Ceramic)
- Polypropylene (PP)
- Polystyrene (PS)
- Polycarbonate (PC)
- Acrylonitrile Butadiene Styrene (ABS)
- Polymethyl Methacrylate (PMMA)
- Polyethylene Terephthalate (PET)
- Polybutylene Terephthalate (PBT)
- etc.
Benefits
The advantages of laser welding are too many to list. So, here are some select ones that have the most significance to a business.
- Higher Quality and Stronger Welds
- Better Weld Finish
- Fast Welding Speed
- More Energy Efficient
- Ease of Automation
- Wider Material Compatibility
- Can Weld Dissimilar Materials (Metals to Non-metals)

I. TIG Welding
TIG welding (Tungsten Inert Gas Welding) is a traditional metal-only welding process that utilizes powerful electric currents to heat and melt the workpiece. This process passes an electric arc through two electrodes. The first electrode is a tungsten stick wrapped in insulating materials for handheld use and the other is the metal workpiece.
TIG welding machines can use direct current (DC) and alternating current (AC) to initiate the electric arc.
The tungsten electrode is surrounded by a gas nozzle that continuously jets an inert gas (helium or argon) over the weld pool. During the welding process, the motel metal is susceptible to oxidation. Hence, a shielding gas must be deployed to keep the weld clean of impurities. This welding process is also known as Gas Tungsten Arc Welding (GTAW).

TIG welding can be performed with or without a filler material. The filler material is a compatible metal, typically in the shape of a rod, that is slowly fed to the weld area. It fills in the gap between the two metal pieces, creating a stronger bond.
Unlike other electric arc welding methods, TIG welding doesn’t necessitate a filler material.
Material Compatibility
TIG welding is limited to metal and metal alloys.
- Steel
- Stainless Steel
- Aluminum
- Nickel
- Magnesium
- Copper
- Gold
Benefits
- Wide Metal Compatibility
- Filler Material is Not Necessary
- Cost Effective Welding
- Easy to Learn
- Excels at Welding Thicker Materials
Click here for a comparison of laser welding and TIG welding.
II. MIG Welding
MIG welding (Metal Inert Gas Welding) is a type of gas metal arc welding (GMAW), similar to TIG. In this process, a consumable filler metal wire acts as the second electrode. As the electric current passes through the two electrodes, the filler material melts and flows into the spaces between the two workpieces.
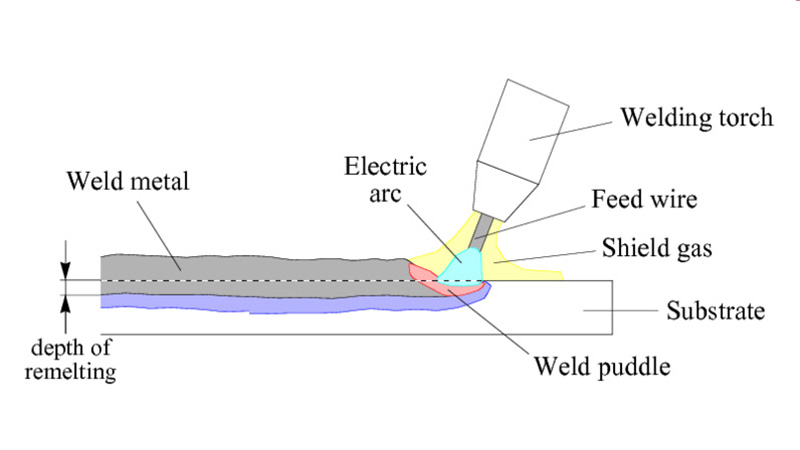
A shielding gas (usually argon) blows away unwanted vaporized metal and prevents metal oxidation. This welding technique requires a continuous feed of filler material for consistent and accurate welds.
Material Compatibility
MIG welding is ideal for metal plates that are over an inch in thickness.
- Aluminum
- Carbon Steel
- Stainless Steel
- Alloys
- etc.
Benefits
- Faster Welding Speed
- Cleaner Finish
- Cost Effective
Don’t forget to learn how laser welding compares to MIG welding.
III. SMAW
SMAW, or Shielded Metal Arc Welding, is an off-shoot of the gas metal arc welding method. The key difference between the two traditional welding techniques is a flux-coated consumable electrode.
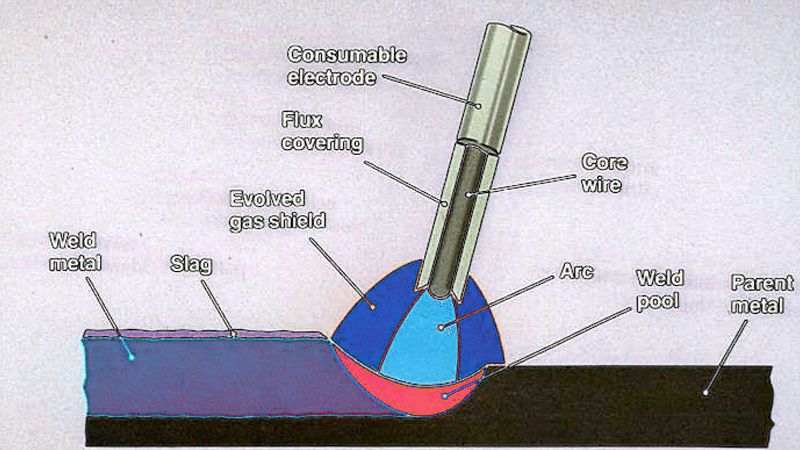
Unlike MIG welding, which uses a simple metal wire and a gas jet, SMAW uses a specialized electrode rod with a flux coating. As the electric arc heats the electrode, the flux coating evaporates into a shielding gas. The flux shielding removes the need for an external gas cylinder, making the welding process more mobile and versatile.
The portability and built-in shielding make SMAW the perfect choice for underwater welding. Despite being an older welding technique, it is still prominently used in pipeline manufacturing, shipbuilding, and other construction applications.
However, as the flux-coated electrode is comparatively short, frequent replacements reduce the overall welding speed.
Material Compatibility
Shielded metal arc welding is primarily used for ferrous metals.
- Carbon steel
- Low Alloy Steel
- High Alloy Steel
- Stainless Steel
- Cast Iron
- Ductile Iron
Benefits
- Portable and Lightweight
- Built-in Gas Shielding
- Low-Cost Solution
We have also prepared a comparison post between laser welding and SWAM.
IV. Electron Beam Welding
EBW (Electron Beam Welding) is a high-tech welding process similar to laser welding. Like laser welding, it’s a contactless welding process reliant on energy deposition from a distance. The source of electrons is a tungsten core that is superheated until free electrons flow off of its surface. These loose electrons get condensed and accelerated into an electron beam that has exceptional metal penetration.
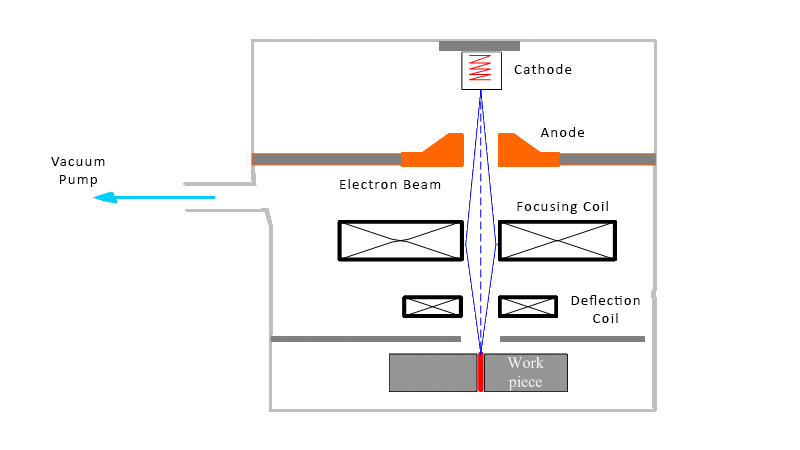
Just like laser welding, EBW stands above most traditional welding methods, as it doesn’t require a filler material to bridge the gap between the workpieces.
However, despite its several benefits, electron EBW has a major drawback. Electrons are so small that a collision with oxygen or nitrogen atoms (main components of air) will scatter them and de-focus the beam.
Material Compatibility
EBW is incompatible with non-metals and volatile metals with high vapor pressure (Calcium, Zinc, Magnesium, etc.).
- Carbon steel
- Stainless Steel
- Aluminum Alloys
- Nickel Alloys
- Copper Alloys
- Titanium
Benefits
- Welding Dissimilar Materials (Two Different Metals)
- No Filler Material Needed
- No Risk of Metal Oxidation
- High Precision Welding Applications
- Excellent Weld Finish
Perhaps you’d like to know what the difference is between laser welding and EBM?
V. Gas Welding
Gas Welding or Oxy-Acetylene Welding is a traditional welding method that relies on gas combustion to generate heat and melt the workpiece. The acetylene gas is the fuel that gets ignited, and oxygen gas enables the flame to burn hotter and longer.
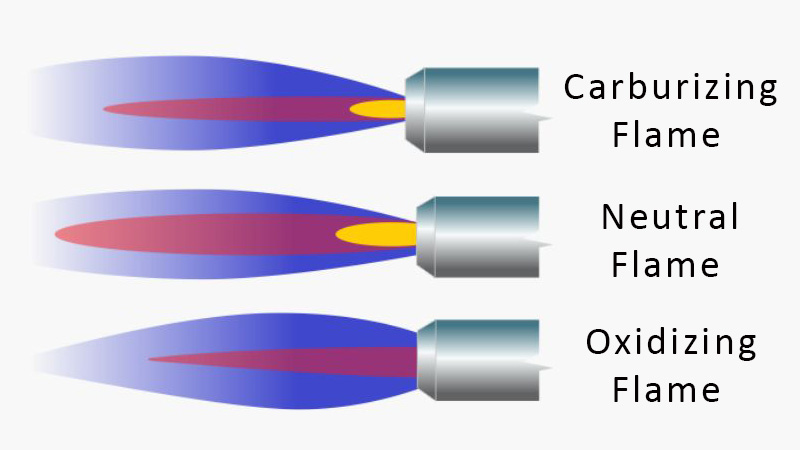
The ratio of oxygen to acetylene determines the temperature and type of the flame.
- Carburizing Flame – More acetylene, less oxygen. (~5200°F or 2900°C)
- Neutral Flame – Equal parts acetylene and oxygen. (~5600°F or 3100°C)
- Oxidizing Flame – More oxygen, less acetylene. (~6000°F or 3300°C)
Similar to most welding processes, gas welding utilizes a filler rod to fill the gap between workpieces.
Gas welding equipment is bulky as it requires not one but two gas cylinders. However, despite its inconvenient size, its popularity as a welding process is attributed to its portability. It trades welding precision for convenience and portability.
While acetylene is the most popular fuel gas, other options include butane, hydrogen, and MAPP gas.
Material Compatibility
Gas welding is compatible with most metals.
- Carbon steel
- Stainless Steel
- Aluminum Alloys
- Nickel Alloys
- Copper Alloys
- Cast Iron
Benefits
- Welding Dissimilar Metals (Ferrous and Non-Ferrous)
- Portable Welding Equipment
- Cost Effect Welding Process
- Not Reliant on Electricity
VI. Brazing
Brazing is a slight variation on the gas welding process. It uses a low melting point filler material and thus consumes less energy. Gas welding occurs at high temperatures as needed to melt the base metal and the filler. In contrast, brazing only melts the filler metal, which acts like glue between the two base metals.
The filler metal is generally a softer alloy of the base metal. Brazing is a nice middle point between welding and soldering. In fact, brazing copper joints look a lot like soldering.
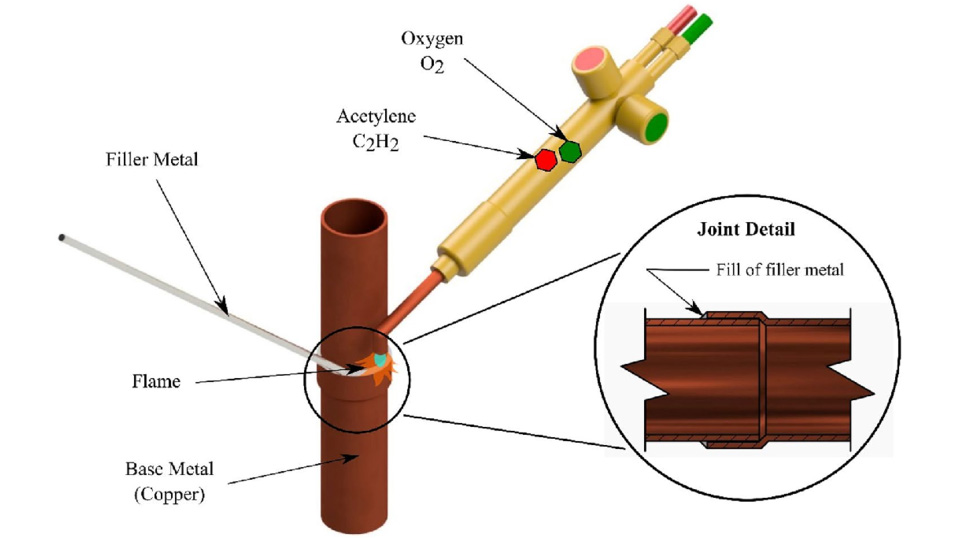
Material Compatibility
Gas welding is compatible with most metals.
- Carbon Steel
- Stainless Steel
- Aluminum Alloys
- Nickel Alloys
- Copper Alloys
- Tungsten
- Cast Iron
- Galvanized Iron
Benefits
- Join Dissimilar Materials (Here’s a post on laser welding dissimilar metals for expansion.)
- Low-Temperature Process
- Fast Bonding Process
- Join Metal Components of Differing Thickness
Click to continue reading about the differences between laser welding and brazing.
VII. PAW
PAW or Plasma Arc Welding is a unique technique that combines gas and arc welding methods. It uses a tungsten electrode to generate an electric arc to ignite an inert gas jet, typically a mixture of argon or helium. The gas gets ionized (broken down on an atomic level). It also uses a filler metal like most gas and arc welding methods.
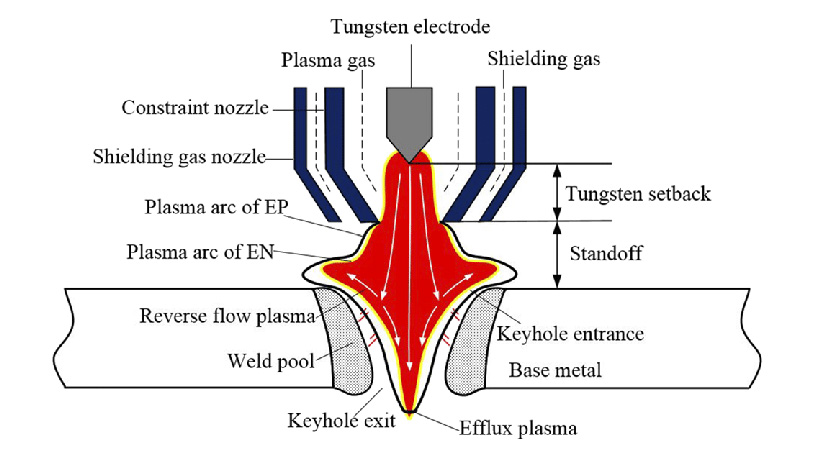
An oxygen-shielding gas is used to protect the weld pool and reinforce the plasma arc. Plasma is several magnitudes hotter than a gas flame or even arc welding.
- Plasma Arc: 50,400 °F (28,000 °C)
- Electric Arc: 9,930 °F (5,500 °C)
- Gas Flame: 5,600 °F (3,100 °C)
- Laser Beam: >2,000 °F (>1,000 °C)
It should be noted that the laser welding process is highly efficient and thus doesn’t need to reach high temperatures. A majority of the electric arc heat is lost to the surroundings. The thermal output of laser welding can’t be compared with traditional welding methods.
Material Compatibility
Gas welding is compatible with most metals.
- Carbon Steel
- Stainless Steel
- Aluminum Alloys
- Titanium
Benefits
- Excels at Precision Welding
- Great for Deep Welds
- Negligible Thermal Distortion
Learn more about choosing between laser welding and PAW here.
VIII. RSW
RSW, or Resistance Spot Welding, is an electricity-driven metal joining process. The two halves of a base metal are sandwiched between electrodes. A powerful electric current is forced through the base metals as it flows from one electrode to another.
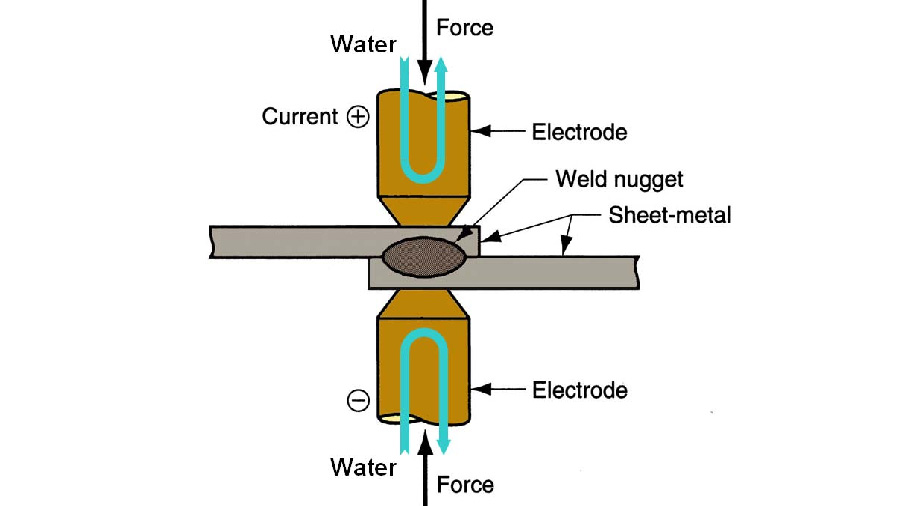
The electrical resistance of the base metal causes it to heat up and fuse with the other half. The weld joint created from RSW is incredibly robust. However, due to the nature of this welding process, it cannot be used for long continuous welds.
The manufacturing industry rarely uses RSW for high-performance applications. Instead, it’s mostly relegated to quick boning of thin sheets of metal.
Material Compatibility
Resistance spot welding is generally limited to metals with low electrical conductivity.
- Steel
- Copper
- Aluminum
- Magnesium
- Titanium
Benefits
- Strong Weld Joint
- High Quality Welds
- Fast Welding Process
- Cost Effective Welding
By this point, I’m sure you’re wondering which is better, laser welding or RSW?

Comparison List of Different Welding Methods
Laser welding is one of the most versatile manufacturing techniques available to small and medium businesses. It’s incredibly efficient and very easy to use. In contrast, traditional welding methods often require years of training and skill development.
Welding processes such as MIG or EBW are better suited to thicker materials. However, MIG compromises on welding precision, and EBW is generally more expensive than an equivalent laser welding machine.
Table 1 - List of Different Welding Techniques and their Capabilities
WeldingTechnology | WeldSpeed | WeldPrecision | ThicknessLimitation | CompatibleMaterials | Application | EqupimentCost |
---|
Laser welding applications can’t fully be showcased in this table. Even though most of the mentioned welding processes are used in the automotive industry, laser welding is the only one that can be used for metal and non-metal welding.
A better illustration of laser welding prowess is to compare its advantages and disadvantages to the various welding processes.
Table 2 - Comparing the Advantages and Disadvantages of Different Welding Techniques
WeldingTechnique | AdvantagesOver Laser Welding | DisadvantagesOver Laser Welding |
---|
Conclusion
Laser welding has slowly grown in popularity over the last few years.
While traditional welding methods remain useful for most industrial applications, laser welding has highlighted their shortcomings. Laser welding is a jack of all trades. It can outperform traditional welding methods in most applications. The only two major drawbacks of laser welding are its lack of portability and its limited compatibility with thick metal plates.
Let Baison Be Your Ticket to Success!
Baison is the premiere fiber laser solutions provider in the global market. Our state-of-the-art laser welding machines are built to last a lifetime. We use only premium-quality components, and each machine undergoes rigorous testing by our expert technicians and engineers.
Take a look at our FREE Application Evaluation program before making a purchase. Our team of experts will help you get the best machine for your business.
So, let Baison take your business to new heights. Contact us Now!