Imagine two industry leaders in a standoff: Laser Welding, with its precise, high-energy beam and ability to fuse dissimilar metals seamlessly. On the other side is Brazing, an old-school craftsman wielding molten filler material that capillary action draws into gaps between tightly fitting parts.
This blog post unveils these industry-leading technologies – Laser Welding vs. Brazing. The clash may seem technical, but it’s crucial for industries worldwide. From automotive manufacturing to electronics assembly, from joining large assemblies to creating small spot joints – their influence spans wide and deep. Let’s take a deep dive into their functioning, uncovering the strengths they possess.
Understanding Laser Welding
Laser welding, a modern metal joining process, uses a concentrated laser beam to create strong bonds between base metals. The high temperatures generated by the focused laser beam are localized to spot joints, reducing distortion in large assemblies.
The welding process is often used to join dissimilar metals because of its precision. This makes it particularly suitable for industries where accuracy is paramount, such as electronics manufacturing and automotive production.
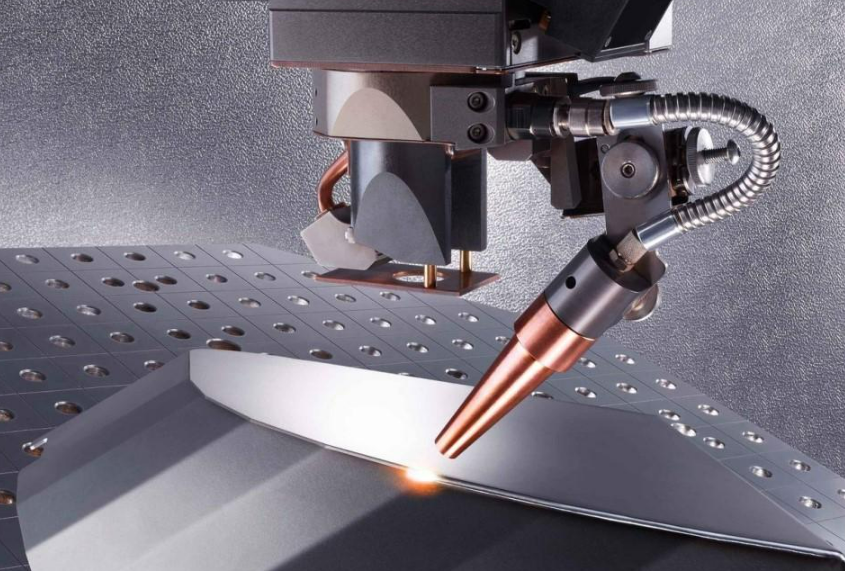
Optimizing Laser Welding: Addressing Limitations
Laser welding stands out in the tech landscape, catering especially to certain applications. It’s reshaping numerous industries with its unique features. However, there are some things that initially come off as limitations. We are here to break these down and show you how you can actually benefit from them in the bigger picture.
I. The Initial Cost is Worth the Value
Yes, the upfront expense of laser welding gear is high, but its precision and capabilities justify it. Industries like automotive and construction prioritize quality and durability; hence, the cost balances out with excellent welding results and lesser maintenance.
Safety is paramount in this tech, highlighted by the essential protective gear. This ensures steady operations even in challenging conditions, making laser welding a reliable choice for large enterprises.
II. Material Compatibility is Key
Laser welding excels with compatible metals, producing strong and enduring welds. Some metal combinations, like copper and aluminum alloys, can be tricky, but ongoing research is widening material compatibility and refining the welding process.
Continuous advancements in the field are paving the way for more seamless welds. By grasping these intricacies, industries can unlock laser welding’s full potential, aiming for unparalleled quality and efficiency.
Do You Have Any Questions?
Let Us Solve Your Problem
Laser Welding Benefits Across Industries
The dynamic world of manufacturing and production has seen laser welding stand out as a beacon of precision and durability. As industries evolve, the versatility of this technology becomes increasingly evident. Let’s see how laser welding shapes and supports these diverse domains.
- Automotive: In the automotive sector, laser welding is pivotal. It not only ensures reduced metal distortion but also enhances the overall strength of the components. This is particularly advantageous in the production of durable electric car frames.
- Electronics: The electronics industry benefits from the precision of laser micro-welding. This technology is ideal for joining miniaturized components, ensuring devices like smartphones and wearables are both functional and durable without compromising on design.
- Shipbuilding: The shipbuilding industry requires resilient, watertight seams for marine vessels. Laser welding answers this demand, providing robust joints that withstand the challenging marine environment, ensuring both safety and longevity.
- Construction: In the realm of construction, structural integrity is paramount. Laser welding is employed to seamlessly join steel components in large infrastructures, from skyscrapers to bridges, ensuring both durability and aesthetic appeal.
- Aerospace: The aerospace industry has rigorous standards that laser welding adeptly meets. By creating lightweight yet incredibly strong aircraft components, the technology is instrumental in ensuring aircraft durability and lifespan.
- Healthcare: The medical field demands precision and reliability. Laser welding plays a vital role in crafting intricate medical devices, from surgical instruments to implants, ensuring they’re both safe for use and functionally optimal.
Brazing Basics and Its Versatility
Torch brazing, induction brazing, furnace brazing, and arc brazing are all methods of brazing.
When it comes to joining metal parts, brazing shines with its unique versatility. This method has a wide range of applications and is preferred for many tasks where other traditional welding methods fall short.
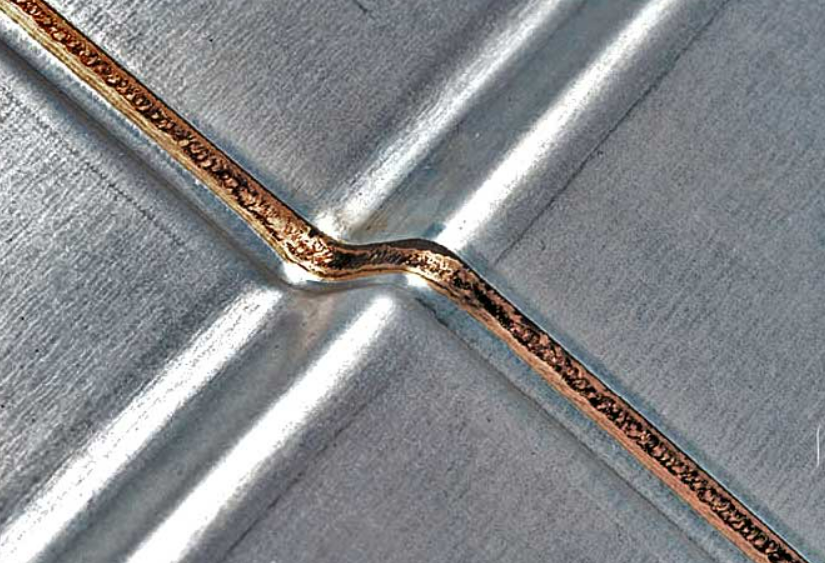
1. Brazing’s Energy Efficient and Strong Bonds
The efficiency of brazing stems from its energy-conscious process. It doesn’t require high temperatures like welding, which makes it an environmentally friendly option in industries looking to cut down on energy use.
But don’t mistake this lower temperature requirement as a compromise on strength. Brazed joints are known for their robustness, and ability to withstand significant stress without giving way. Studies show that the bonds created through brazing can be stronger than the base metals they join.
2. The Need for Filler Materials in Laser Brazing
Metal joining processes are a diverse lot, and in this realm, brazing filler metals stand out, especially in brazing. Let’s dive deeper into why these materials are so pivotal.
The Role of Melting Points
For brazing to be effective, the filler material’s melting point should be lower than that of the base metals in question because brazing involves melting. Once the filler material reaches its melting point, it begins its journey into the minuscule gaps between components. This is courtesy of capillary action—a phenomenon akin to how water ascends against gravity when traveling up paper towel fibers.
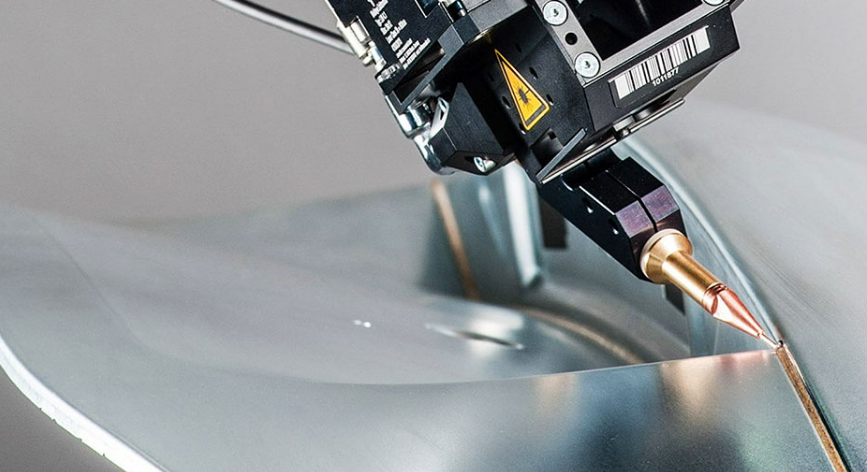
3. Benefits of Using Filler Materials in Brazing
Two reasons why it stands out in the industry:
- Capillary Action: Some may perceive brazing’s dependence on filler material as a disadvantage when compared to welding. Yet, this is one of its most profound strengths. The capillary action, not only draws the molten filler material into the joint area but also disperses it over a broader surface. This spread ensures the joints are resilient and less prone to succumbing under pressure.
- Versatility with Temperature: The brazing filler metal, by design, does not require exorbitant temperatures to melt and flow. This trait makes them the go-to choice when working with materials that are vulnerable to heat. It’s a game-changer, especially in industries like electronics where precision isn’t just desired; it’s demanded.
The Challenges of Laser Brazing
While laser brazing can be an effective method for joining metals, it’s not without its challenges. The process involves using a filler metal with a lower melting point than the base materials to join them together. But when these temperatures fluctuate too much or are improperly controlled, issues can arise.
Weak Points Under High Stress
Brazed joints may become weak points under high stress due to the difference in physical properties between the base materials and the filler metal used in brazing. This is especially true if there’s any misalignment during joint formation or finishing operations that don’t smooth out visible seams properly.
In applications where strong bonds are essential – such as jet turbine blades or air conditioning systems – this potential weakness could lead to catastrophic failures over time. In fact, one study found that about 8% of all equipment failures were related directly to problems at brazed joints.
Do You Have Any Questions?
Let Us Solve Your Problem
Laser Welding vs. Laser Brazing: A Side-by-Side Comparison
In metal joining applications, both laser welding and laser brazing have carved out their distinct places. Understanding the nuances and differences between these two advanced processes can guide industries in selecting the optimal technology for their specific needs. Let’s explore them in a comparative manner:
1. Process Mechanism
- Laser Welding: This technique primarily involves melting and fusing two pieces of metal together, using the laser’s intense heat. The result is a deep penetration weld that provides a strong joint, often stronger than the parent material itself.
- Laser Brazing: Here, the laser is used to melt a filler material which, upon cooling, binds the two base materials together without necessarily melting them. The resulting joint has a superficial depth compared to welding, but it offers an aesthetic, smooth appearance, especially valuable in industries where surface finish is pivotal.
2. Material Versatility
- Laser Welding: This method demands metallurgical compatibility between the metals. It’s excellent for similar materials, though certain dissimilar pairs might pose challenges.
- Laser Brazing: Given its reliance on filler material, laser brazing can be more forgiving when joining dissimilar metals. The filler can bridge the differences in metallurgical properties, offering more flexibility in material combinations.
3. Application Areas
- Laser Welding: Highly favored in sectors like automotive, shipbuilding, and construction, where joint strength is paramount. Its ability to create robust joints makes it ideal for structural applications.
- Laser Brazing: This is popular in the electronics industry and automotive finishing, where the appearance of the joint is as crucial as its strength. It’s particularly beneficial for surface attachments and areas visible to end users.
4. Equipment Investment
- Laser Welding: Generally demands a higher investment due to its advanced machinery and associated safety gear. However, the longevity and quality of joints can often justify this initial outlay, especially for large-scale industrial applications.
- Laser Brazing: While still requiring specialized equipment, the investment can be slightly less intensive compared to welding, given its surface-level nature and reduced safety concerns related to deep penetration heat.
Conclusion
Wrestling with the decision between laser welding and brazing isn’t easy. You’ve got to weigh your options carefully – take into account everything from material compatibility to energy efficiency. It’s about finding the ideal solution for your requirements. Keep asking questions, and keep exploring possibilities because understanding these processes will only make you better equipped to make the right choice!
Elevate Your Manufacturing with Baison Laser Solutions!
Keen to harness the precision and strength of laser welding or explore the versatility of brazing for your projects? Baison Laser is your trusted partner in delivering unparalleled laser solutions tailored to your needs. Dive deeper into our expertise by contacting us today!