Looking at the context of laser welding techniques, it is usually assumed that dissimilar material welding is a challenging task; however, it is not.
This guide captures all the details that help you clearly understand welding dissimilar materials, their benefits, and important considerations to keep in mind. Moreover, you will also learn about how Baison laser machines play an essential role in dissimilar metal welding processes that make industry professionals trust them.
Challenges in Joining Dissimilar Metals
When joining dissimilar metals together, various challenges come across in different industrial applications. Some of the combinations of dissimilar metals and the challenges with such combinations are discussed below:
1. Aluminum and Steel
When joining aluminum alloys and steel, the challenge that comes across is their different melting point and the variations in thermal expansion, which leads to the creation of brittle compounds. Such a challenge can be addressed by adding some intermediate layers of aluminum-silicon that reduce intermetallic formation and strengthen the joint.
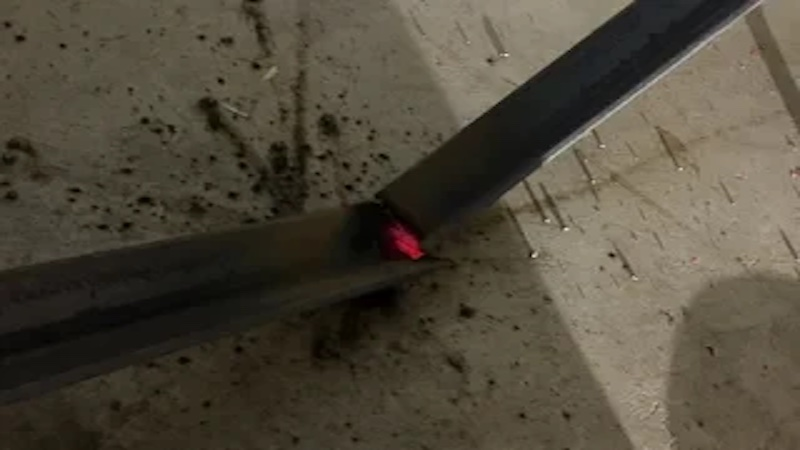
2. Copper and Aluminum
Copper and aluminum alloys comprise a difference in electrical conductivity that results in galvanic corrosion. Hence, the mechanical characteristics of the joint may be compromised, leading to an impact on its strength.
By treating the surface with coatings, the galvanic corrosion can be resisted, and the joint can be strengthened.
3. Stainless Steel and Carbon Steel
Stainless steel and carbon steel are materials that possess different corrosion resistance properties, which leads to the weld seam being subjected to galvanic corrosion. To mitigate this challenge, corrosion-resistant coatings should be introduced, and the joint design must be minimized with the help of galvanic cells.
4. Titanium and Aluminum
When titanium alloys are joined with aluminum alloys, a fragile intermetallic compound that lacks flexibility and strength is created. Filler materials can be used to minimize the weakness in the joint.
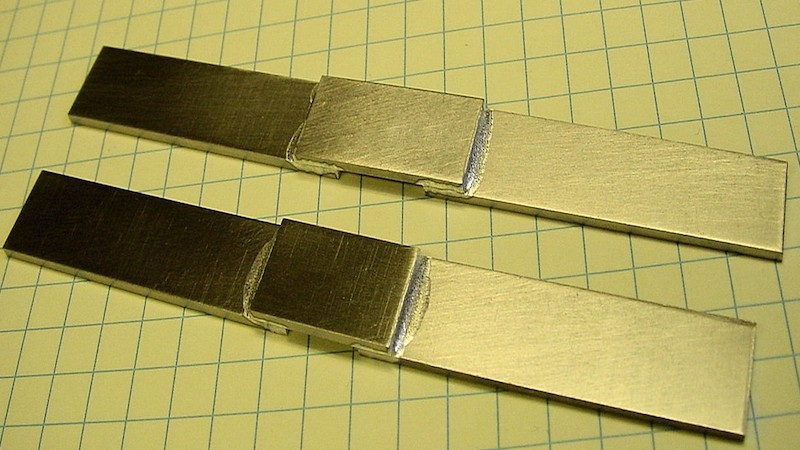
In general, when similar materials are welded together, the bond formed is powerful at the weld seam. This is because the zone that is combined has the same composition and the same physical properties. However, depending on the nature and mechanical and chemical properties of the materials, they do form strong bonds.
On the other hand, in cases where a true metallurgical bond is not formed between the metal parts, then by creating a mechanical entanglement. Mechanical entanglement is the mixing of alloy elements that are not similar, but they are physically held together in a way that the joint holds mechanical strength.

Benefits of Laser Welding Dissimilar Metals
There are various benefits of laser welding different metals, and some of these are discussed below:
- The laser welding process is equipped with high precision and accuracy, and hence, it helps create complex joints with intricate outcomes. Hence, when different alloy elements come together having unique properties, they blend very well.
- Laser welding is a method of joining dissimilar metals that uses laser beams on the point of welding; this results in a minimal amount of heat input, reducing the chances of damage in such combinations that have different melting points.
- Laser welding technology uses a narrow beam of laser and hence results in a small heat-affected zone; it proves to be an advantage when different metals are welded because the surrounding material is not impacted, and the chances of formation of an intermetallic compound are also reduced.
- Laser welding offers high welding speeds, which leads to increased productivity, and the quick heating and cooling cycles minimize the time dissimilar metals spend in a critical range of temperatures.
- A laser welding method can be chosen for multiple materials, which include similar and dissimilar materials. Hence, materials with different physical and chemical properties can easily be welded together.
- Since laser welding uses a non-contact process, in the case of dissimilar welding, it helps to ensure that the metal surface comes out clean due to precisely controlled laser welding.
- Laser welding process parameters are equipped with high precision and less heat input; hence, when the dissimilar metal welding process takes place through laser energy, the integrity of joints is maintained, and the post-weld processing requirements are eliminated.
- The laser welding process is known for producing high-quality welds that are free from defects, and hence, it ensures consistency and reliability when dissimilar metal welding is carried out.
- Laser welding is capable of being carried out in various environments, which also comprise inert gas atmosphere or vacuum conditions, hence proving to be a flexible process for welding metals that are sensitive to different environments.
- Laser welding can be integrated into automation, and hence, industries that need efficient and repeatable manufacturing processes through laser welding of dissimilar materials may find it beneficial.
Methods of Laser Welding of Dissimilar Metals
There are various methods of laser welding of dissimilar metals, and some of the standard methods are as follows:
I. Fiber Laser Welding
Fiber laser welding uses a fiber laser beam and provides a perfect quality beam, which is also suitable for dissimilar materials. It is used widely in the aerospace and automotive industry due to the high-end precision needed.
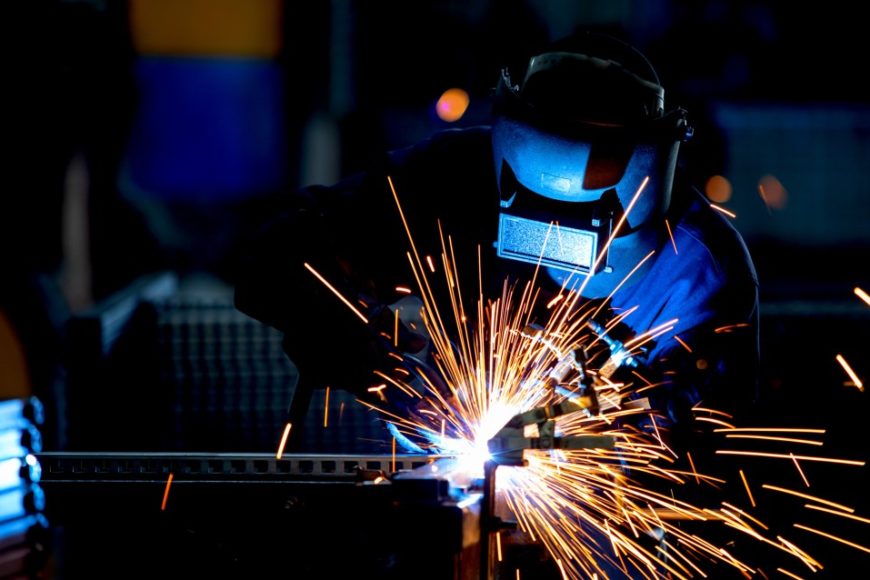
II. Keyhole Mode Laser Welding
Keyhole mode laser welding is a high-power density welding process that is suitable for thicker materials. In such a method of laser welding, materials that need penetration depth form a keyhole that is then filled with molten material, creating a very strong weld.
III. Laser Brazing
Laser brazing uses a basic technique of welding that involves melting filler materials, which is usually done for a metal that has a low melting point. It creates strong joints without distorting the joints.
IV. Laser Cladding
In the process of laser cladding, a layer of material is added to the metal surface as a substrate with the help of a laser beam, and it helps to clad metals that are not similar, offering them properties like corrosion resistance.
V. Conduction Mode Laser Welding
Conduction mode laser welding uses its laser beam to weld thin materials; in this princess, the metal conducts the heat and melts the interface between the dissimilar metals to create a joint.
VI. Hybrid Laser Welding
Hybrid laser welding is a combination of welding methods, which are gas tungsten arc welding or metal inter-gas welding. This technique of laser welding is used for dissimilar metals to create a balance between heat input and penetration, as it offers better control over the welding process.
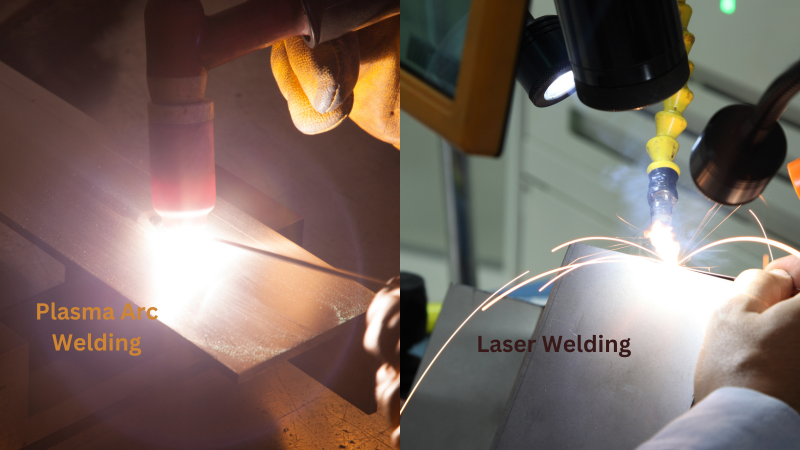
VII. Continuous Wave Laser Welding
In continuous wave laser welding, a laser beam is continuously applied to the joint. It helps create an effective weld by offering high welding speed and is suitable for joining dissimilar metals that are thin.
VIII. Pulsed Laser Welding
Pulsed laser welding applies laser energy in short pulses, which you can precisely control. It is suitable to join dissimilar alloys through a controlled heat input, and metals that have different melting points are easily welded together.

Factors Affecting Laser Welding of Dissimilar Metals
When the welding of dissimilar materials is carried out, various factors affect the process; some of these are as follows:
- During the welding process of dissimilar materials, the metals need to have a solid solution. This solution helps produce a stable metallurgical phase and determines the amount of dilution.
- If the dilution is excessive in the event of joining dissimilar metals, there is a risk of hot cracking. It is essential to measure suitability to avoid such cracking.
- When metals go through a transition from one to another during the welding process of dissimilar metals, there is a chance of corrosion to take place. In cases where the electrochemical characteristics are different, the risk of corrosion increases.
- Every metal has a different melting point; hence, during the process of welding, some metals may need preheating, which brings all the metals to their melting points.
- When metals are heated, they expand, and there is a change in their shape and size. In cases where two metals are welded, and they change shape at different temperatures, the metals may lead to thermal cracking.
What Metals Can’t Be Welded?
Certain metals can be welded through different techniques, and some metals are difficult to weld because of their properties. Some of these metals that cannot be welded together easily and may require alternate solutions include the following:
1. Low-melting metals that consist of lead and alloy elements having low melting points are difficult to weld with a laser beam. When the heat input is excessive, it leads to thermal damage.
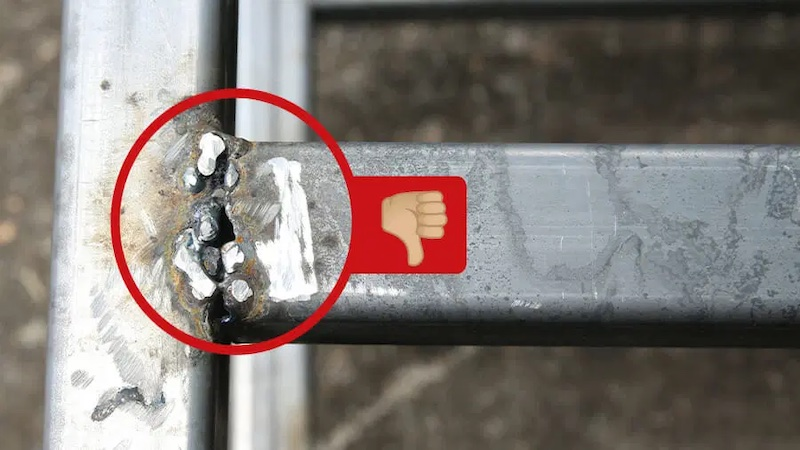
In such cases, joining methods like mechanical fastening and soldering are more suitable for alloys that have low melting points.
2. Highly reactive metals like sodium and potassium pose safety risks because they react with moisture and air during the welding process.
Due to the risk of the hazard of welding such materials, alternate solutions like diffusion bonding are opted for.
3. If materials science is taken into consideration, it can be observed that magnesium is also challenging to weld using lasers. This is because magnesium is highly reactive, and it isn’t easy to weld due to its thermal conductivity and high reflectivity.
Instead of laser welding, the TIG welding process or friction stir welding is suitable for magnesium alloys.
4. Tungsten, when in its pure form, has a high melting point, and laser welding may not be suitable for it. The joining of tungsten is usually carried out using TIG welding, brazing, and electron beam welding.
Other Methods vs. Laser Welding to Join Dissimilar Metals
There are various methods other than laser welding that help to join dissimilar metals, and some of these are as follows:
I. Ultrasonic Welding
Ultrasonic welding uses ultrasonic vibration. The ultrasonic energy, when applied to the material, creates frictional heat, and it leads to melting the metal surface and welding together as a joint. The ultrasonic welding process for dissimilar metal welding is suitable for the medical industry as it ensures minimal impact of heat.
II. Friction Welding
Friction welding is a process of solid-state welding in which one metal component is rotated against the other, and heat is generated. It leads to applied pressure, and hence, a weld is created. Friction welding is used in association with dissimilar materials to create strong bonds in multiple applications, specifically the automotive industry, and aerospace.
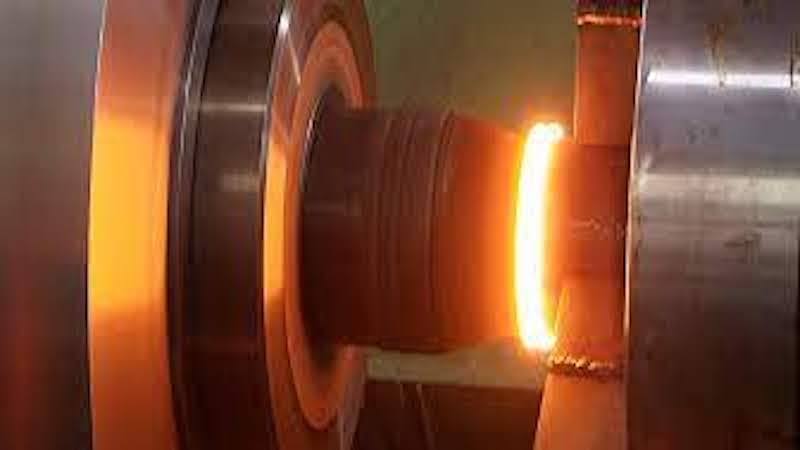
III. Butt Welding
Butt welding is a welding method in which the ends of two metal pieces are joined together without overlapping. This joint is created upon heat applications, and metal pieces are pressed together to create a joint. It is ideally suitable for dissimilar metals as it is a form of diffusion welding in which the ends diffuse into one another and is used for joining pipes, sheets, and multiple other components.
Difference Between Laser Welding and Other Methods at a Glance
When it comes to joining dissimilar metals, there is a difference between laser welding and other methods; the table below features the differences at a glance.
Features | Laser Welding | Friction Welding | Ultrasonic Welding | Butt Welding |
---|---|---|---|---|
Heat Input | Low | Moderate to High | Moderate to High | Moderate to High |
Precision and Accuracy | High | High | High | High |
Joint Strength | High | High | Moderate | High |
Distortion | Minimal | Minimal | Minimal | Minimal |
Speed | High | Moderate to High | Moderate | Moderate |
Material Compatibility | Versatile | Versatile | Limited by material type | Versatile |
Post-Weld Processing | Minimal | Minimal | Minimal | Minimal |

7 Tips for Successful Welding of Dissimilar Metals
To attain successful welding of dissimilar metals for various manufacturing processes, some of the essential tips are provided below:
- Make sure to assess the compatibility of the metals and consider factors like thermal conductivity, melting points, and other factors relating to the physical and chemical properties of metal parts being welded together.
- Surface preparation is an important aspect when welding dissimilar materials; make sure to clean the surface and remove any coatings and contaminants for a better result free from defects.
- Taking the metal properties and process parameters into consideration, design the joint to distribute heat evenly and reduce the risk of cracking.
- The heat transfer must be monitored continuously during the welding processes so the creation of brittle intermetallic compounds is avoided.
- The filler material chosen should be compatible with both base metals to achieve a sound joint.
- In many cases, preheating of metals is required due to dissimilar melting points of metal parts and differences in thermal conductivity. It should be analyzed, and if needed, preheating of such metals must be carried out.
- The chosen welding techniques need to be suitable; for instance, in dissimilar metal welding processes, pulsed welding and hybrid welding are beneficial as they offer better control of heat input to help minimize the risk of defects.
Application of Laser Welding of Dissimilar Metals
The application of laser technology in welding dissimilar materials can be seen in various industries; some of the common applications of industrial lasers are discussed below:
1. Automobile Industry
In the automobile industry, the joining of aluminum and steel components is required to create the structures of the automobile. Laser welding is beneficial because it uses aluminum, which is a lightweight metal and ensures that the structural integrity of steel is maintained.
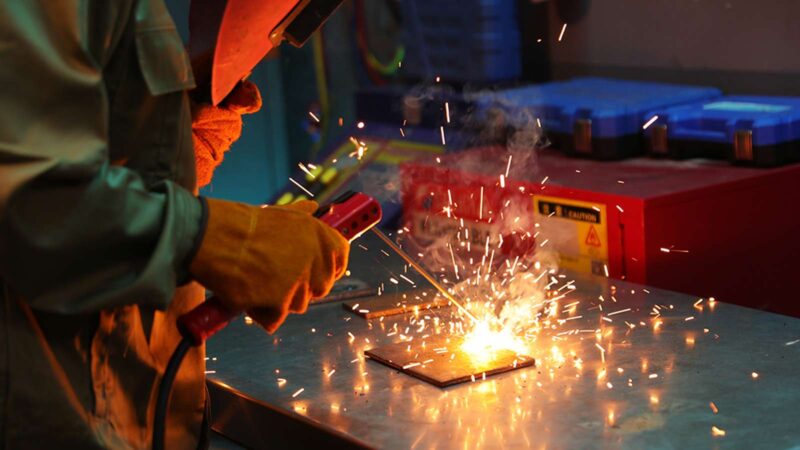
2. Aerospace Industry
In the aerospace industry, aluminum and titanium metal parts are joined together to create the structure of aircraft. It helps provide a precise joint that is robust, and it even helps reduce the weight by using laser welding technology.
3. Consumer Electronics
The consumer electronics industry makes various electronic devices in which copper and aluminum are welded together to create heat sinks. In such applications, laser welding helps to preserve the components by minimizing thermal distortion.
4. Medical Industry
Medical implants and other devices use different metals like titanium and steel joints together. By using laser welding, precise and accurate implants and devices can be manufactured with minimal heat input.

FAQs
1. What is the maximum amount of gap between dissimilar metals when welded through laser welding?
The maximum gap between the dissimilar metals when welded through laser welding is 10% of the material thickness.
2. Is it possible to weld dissimilar metals having different thicknesses together?
Yes, it is possible to weld dissimilar metals having different thicknesses to be welded together; some of the considerations that are needed in this case are assessing welding process parameters, laser power, welding speed, etc.
3. What are the common challenges faced while welding dissimilar materials using laser welding?
The common challenges faced when dissimilar metals are welded together include the creation of brittle intermetallic compounds, variations in thermal expansion coefficients, and melting points.

Conclusion
In this guide, every important detail regarding the process of welding dissimilar materials is captured. After going through it, you must be well equipped with a clear understanding of the factors and challenges that are possessed by the process and how to mitigate the chances of distortion in the welds.
Welding with High Precision Using Baison Laser Equipment!
If you are looking for a high precision and high power welding machine that provides you with an exceptional experience of welding dissimilar materials together. In that case, your go-to place is Baison Laser!
We have a wide range of laser welding equipment covering all types of laser processes and techniques to ensure you get clean and perfect welds. To make your welding projects successful, get in touch with us today!