While LBW uses photons and EBW makes us of focused stream electrons, the kinetic energy of both electrons and photons changes to heat as soon as they come into contact with the metal surface. This is why most people believe LBW and EBW are similar, but they have different techniques and applications.
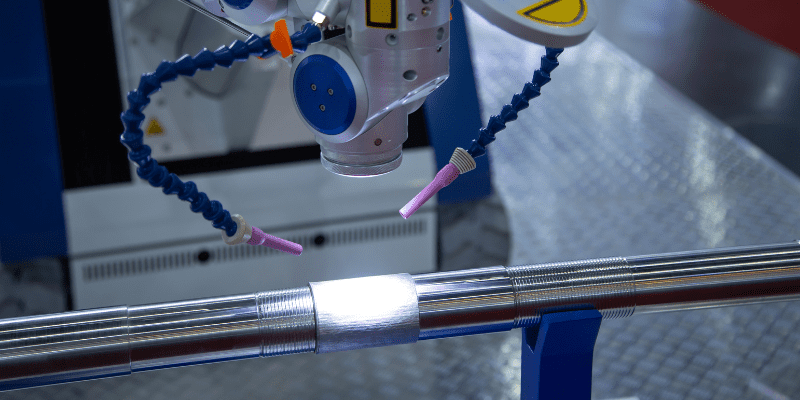
There is no question about the power and flexibility of both EB welding and LB welding techniques. They can weld with pinpoint accuracy while delivering enough power to weld even huge parts together. Automating the process is also possible for both welding approaches.
On top of these, they even produce amazing works both from an aesthetic and metallurgical point of view, but they still have unique differences that set them apart.
Let’s look at each of them to understand their pros and cons.
Laser Beam Welding (LBW)
Laser Beam Welding uses either a pulsed output or a continuous wave (CW) of photons to make the weld.
Lasers work rather simply – the process involves an increase and decrease in the energy state of a material. When done in quick succession, the by-product is photons. CW is mainly characterized by the laser being always on throughout the process, while pulsed output has an off time between pulses to modulate laser output.
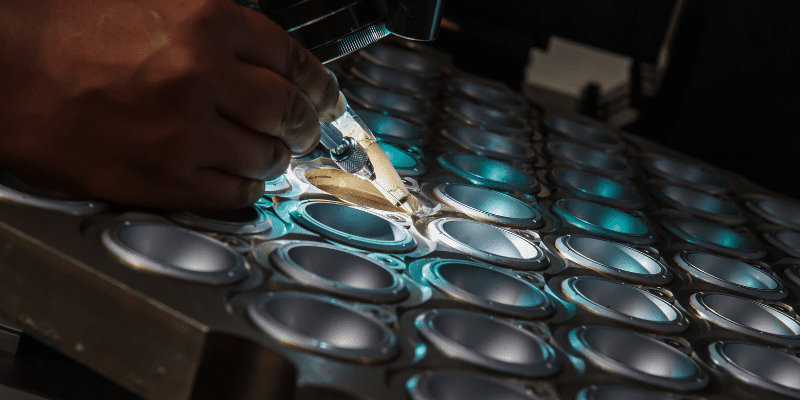
For both pulsed and continuous wave systems, the focus of the laser beam is always on the surface of the workpiece that is to be welded together. Delivery of the beams could be through fiber optic cables which are highly flexible or the more common hard optics. The difference between the two is that the flexible fiber optic delivery allows you to bring your laser to workstations far from the main machine.
Nowadays, automating and controlling the LBW operation and the whole process design routines is through the help of Computer Aided Manufacturing (CAM). Robotic welding applications use fiber optics to deliver the laser to weld components. The speed and versatility of LBW increase with the use of laser scanning, especially along the joints of the weld.
Is laser welding better than arc welding?
Arc welding’s power comes from a DC or AC supply to create heat at about 6500°F. This allows the metal to melt and achieve a weld together. This works for most jobs, but the high energy density of laser beam welding is much faster. The LBW technique brings the material’s surface to liquidus temperature much faster than compared to Metal Inert Gas Welding (MIG), Gas Tungsten Arc Welding (GTAW), or Tungsten Inert Gas Welding (TIG).
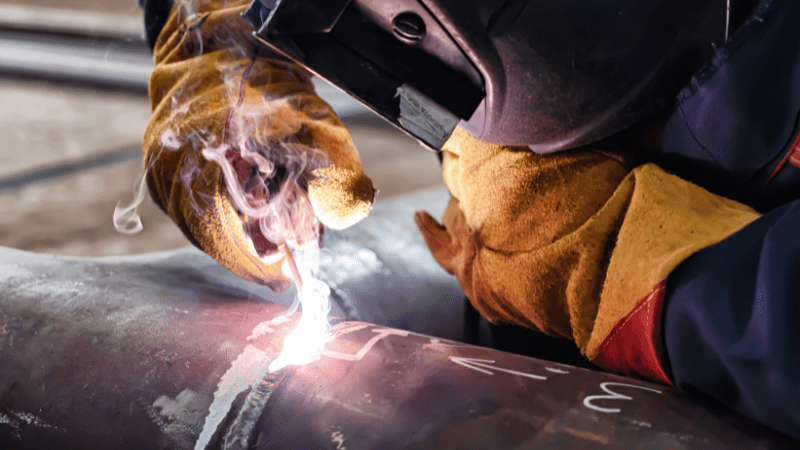
It also helps that the energy from the laser only has a small amount of time to dissipate inside the materials or the pieces. As a result, LBW has a smaller heat zone and puts less stress on the component. A big advantage of LBW over traditional arc welding techniques is the pulsed output – the quick cooling cycles in between the pulses work well for materials that are heat sensitive.
What is the edge of LB welding over EB welding?
The most evident advantage that laser beam welding has over EB welding is the absence of a vacuum chamber in its operations. Unlike the physical enclosure needed by the EBW, laser beam welding is much more flexible. LBW also has simpler tool requirements when you compare it with EBW requirements.
Since electron beam welding requires more precise and unique components to work, laser beam welding is much more scalable. There are plenty of choices for parts for the assembly. As a result, the construction and maintenance of laser beam welding are less expensive when compared with electron beam welding.
Is laser welding better?
Laser beam welding is better if you are working and joining parts that are not suitable or won’t even fit in a vacuum chamber of an electron beam welding. There are even some welding fixtures that may not fit inside the welding chambers for EBW. And since electron beam welding happens in a vacuum, the presence of liquid in the components would prove disadvantageous inside the chamber. This is where laser welding can come in and do the job.
Cons of using laser beam welding
Keeping the weld area free of oxygen requires LB welding using a cover gas. But as a result, this helps increase the process’s efficiency and the work’s purity. Another challenge is the reflectivity of aluminum, gold, copper, and silver materials, which you join together. The more reflective it is, the more it can deflect and minimize the laser penetration of the weld.
This is where pulse output comes in and breaks the surface with varying energy outputs. This lowers the chance of part deformation in the material. Of course, you can still use continuous waves in the process but run the risk of deformation. But the small heat-affected area of laser beam welding helps ensure other areas in the material are not affected. This is helpful when applying heat to electronic components, surgical devices, and other precision instruments.
Electron Beam Welding (EBW)
Electron beam welding uses the massive kinetic energy from fast-moving electrons to weld components together. The process begins by heating a tungsten filament until it gives off electrons. With the help of magnetic lenses and electrical fields, these accelerated electrons are then focused on the areas which heat up and weld together.
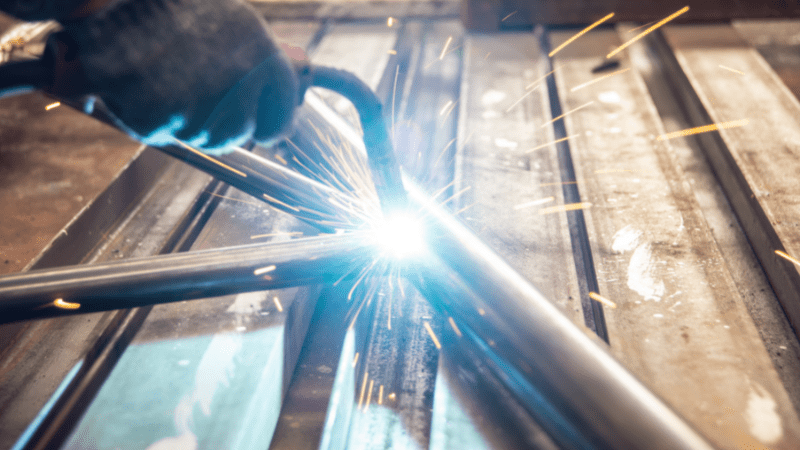
Several industries quickly used EBW from its release during the late 1950s. The reason is that it helps deliver unmatched strength and uncanny precision in its welds. A big part of this is because you can accurately place an electron beam, and even after welding, it leaves the welded material with up to 97% of its original strength.
More than the purity and strength of the material, electron beam welding also helps eliminate impurities in the weld. This is because the process happens inside a tightly controlled vacuum chamber. Oxidation is less because no air or other gases react to welding.
More than preventing oxidation, the vacuum chamber helps better control the precise location of the electron beam during welding. Lower ambient pressure results in better control of the electrons. This is why EB weld is the choice for several industries, such as power generation, aerospace, and nuclear industries.
One unique advantage EB weld has over LB welds and even arc welds is its ability to weld dissimilar materials with varying melting points. Done outside EB weld, the materials joined together could come out brittle. EB weld can melt the lower-temperature material and weld it to the unmelted high-temperature material. The result is a vacuum-tight and compact welding job.
It is also helpful to know that EBW is further classified into two (2) classifications according to power. When working with a 60 kilovolt (kV) or power, that is low voltage EBW. High voltage EBW is at a rate of 150 kilovolts (kV).
What is the edge of EB welding when compared with LB welding?
Electron beam welding works best when materials you are welding together have difficulty coupling, like in aluminum alloys. Working with nickel alloys and even titanium is better when welded in a vacuum chamber.
The process of working and welding in a vacuum enclosure helps ensure that there are zero contaminants on the weld. EBW also offers deeper penetration of the materials it works on. As a result, electron beam welding is more widely accepted and part of most welding specifications.
Is electron beam welding better than arc welding?
Some hard-to-weld materials need to be joined together, and EB welding is a great technique for the job. Especially when you are working with the likes of aluminum alloys or even nickel alloys. But the required vacuum chamber makes it a lot more difficult to come by, especially when you have a simple welding job. In those instances, arc welding could be a better option.
Is electron beam welding better?
Electron beam welding is better when joining materials with different melting points. EB weld will also be better since oxidation goes down since the whole process happens inside a vacuum chamber.
Cons of using EB welding technique
The need for a vacuum enclosure is also a major challenge with electron beam welding. The logistics and components needed to put the chamber together will vary on the material you are welding together. The size of the chamber dictates the size of the parts it can work on. If you need to work on huge parts, you must create a big vacuum chamber.
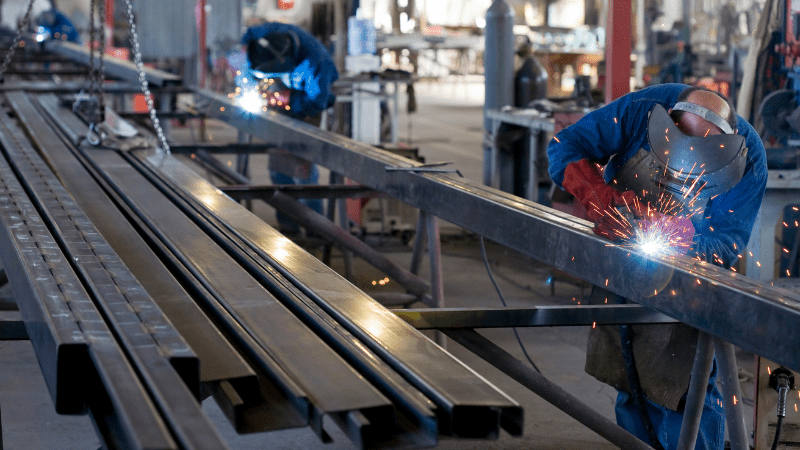
EBW has also been fully computer-controlled for decades now. Part of this is because the use of vacuum and X-radiation presence in the process makes it impossible for human handling. As a result, computers need to run the whole process. This means EB welding needs well-trained operators running the computers. Maintenance on the parts and the computers that run it must also be precise. Not to mention that setting up the process and running it could be quite expensive.
The process can also fall into three phases – welding chamber loading, vacuum pump down, actual welding of the parts, and the need to vent the vacuum. The challenging areas for operators are the pump down and loading of materials you are welding together. This takes the most time.
Does EB welding and LB welding have an edge compared to arc welding?
Sometimes you are looking for specific welding jobs for your projects. If this is the case. LB and EB welding techniques should be your go-to process. LB welds can work in precise and small locations in the materials you are joining together. EB welds eliminate oxidation and can work with materials with different melting points.
But arc welding is best for jobs that require mobility. LB welding and EB welding require many more components for the welds. EB welding even needs a vacuum chamber to help guide and focus the electrons on the welding job.
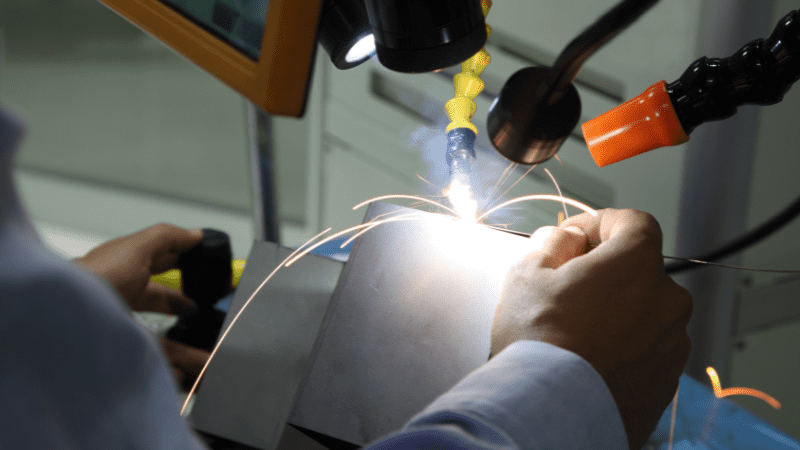
Which is better, Electron Beam Welding vs. Laser Beam Welding?
If you are working with huge materials which will not fit in a vacuum chamber, laser beam welding is better than electron beam welding. The flexibility it offers is far superior when you are restricted to working inside a chamber.
But if you need to manage contamination in the weld and you are working with nickel or aluminum alloys or other materials which has difficulty coupling, electron beam welding is better. You achieve deeper penetration in the weld.
Baison has nearly 20 years of experience in the welding industry and is a world-renowned welding equipment manufacturer. If you need welding equipment, move your fingers to contact us now, we will provide the most professional guidance!