Prototyping is a stepping stone for product development; in the world of today, before the final product is manufactured, making prototypes proves to be the initial stage. A prototype is a physical representation of the product that will be created in the future.
Prototype parts are manufactured through various processes, among which CNC machining and 3D printing have always played an essential role. However, apart from CNC machines and 3D printers, the prototype parts can also be manufactured through laser cutting technology.

This guide below features the manufacturing processes associated with making prototype parts through laser cutting and how Baison laser cutting machines offer precise cuts and exceptional finish.
What are Laser Cutting Prototypes?
Laser cutting is an art, and laser cutters have revolutionized the world of prototypes. The main reason behind opting for laser cutting for these prototypes is because of the low chances of human error in the design.
Laser cutting uses CAD software known as computer-aided manufacturing, which is a computer-controlled machine that helps in prototyping. The CAD program instructs laser cutters to carry out the required movements to cut materials and activate the necessary prototypes. Laser cutter settings are incorporated through the computer-controlled program in the form of exact measurements, and the program communicates with the laser cutting machine.
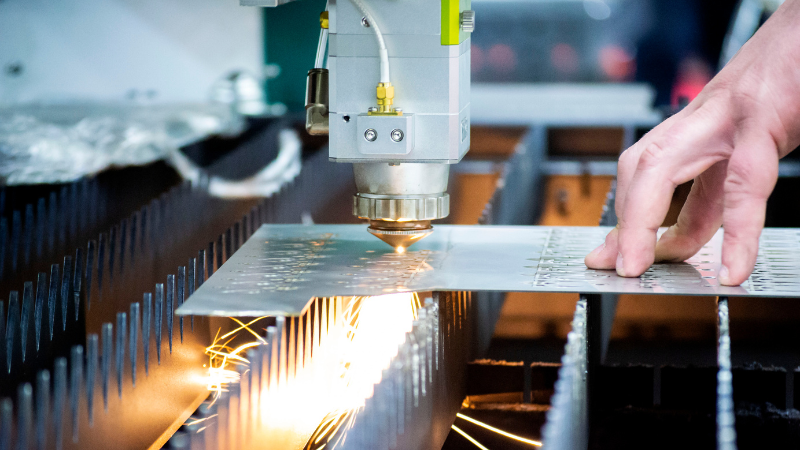
Laser cutting product prototypes are used in many industries, and producing parts that require precision makes the most of this cutting method. Due to the versatility and customization features, laser cutting technology helps cost-effective prototypes. The rapid prototyping offered by laser cutting technology has made it easier for suppliers, manufacturers, and designers to create parts they need for various applications using various materials.
Advantages and Disadvantages of Laser Cutting Prototypes
Laser cutting service is equipped with many benefits and downsides when it comes to creating prototype parts, and the advantages and disadvantages of these are discussed below:
Advantages of Laser Cutting Prototypes
- Laser cutting offers the ability to produce parts having complex patterns and the laser cut edges are also more finished as compared to other methods. However, in the case of creating parts with a laser cutting prototype, the response to changes is quick, and it leads to reducing the lead times.
- Laser beams being smaller in size and concentrated beam offer the ability to create parts that are equipped with innovation and intricate designs. The edges of the laser-cut parts are more polished and need less maintenance. The laser cutting process works with automation, and hence, no supervision is required.
- Laser cutting machines need no retooling, and hence, the modification of the parts is quick, making the process of creating prototypes a rapid one.
- In most cases, when it comes to cutting metal parts, CO2 lasers are used; however, fiber lasers are also gaining popularity with applications in aerospace and automotive parts for prototyping. Due to the efficiency offered by fiber lasers, it is expected to take the place of CO2 lasers in the future.
- By having a laser-cut prototype created, a physical representation of the design comes to the ground, and the investors may believe in your work by having a look at the concept physically.
Disadvantages of Laser Cutting Prototypes
- Laser cutting for prototypes may prove to be challenging with certain material types, although it is used for cutting plastic, wood, and metal. In some cases, certain materials may give undesirable results with the laser cutting process.
- Laser cutting is suitable for extremely thin materials like sheet metal. Hence, the thickness restrictions remain intact. The thicker materials need multiple passes, and this leads to an increase in the processing time.
- The process of laser cutting also generates heat, which causes thermal stress on the material which is being cut, and the issues like burrs on the edges or melting may be encountered.
- Laser cutting machines are expensive and need a hefty investment; hence, small businesses need to choose carefully. Moreover, they also have a complex setup that requires trained staff to operate the machine.
- The laser-cut prototypes need some post-processing, like surface finishing or deburring.
Materials for Laser Cutting Prototypes
There is a large range of material types used in laser cutting to create prototype parts, and these different materials and their suitability are discussed below:
- Acrylic sheets are widely used in laser cutting as they offer ease of cutting and are quite versatile. There are various colors of acrylic sheets, and creating transparent or colored prototypes proves to be suitable.
- Wood, which comprises solid wood as well as plywood, is a common form of material that is used for laser cut prototyping, and various art projects are made using it.
- Lasers also cut thin paper and card stock to create lightweight prototypes; these are widely used for architectural models.
- To create prototype parts for accessories or leather goods, leather can also be cut precisely through the process of laser cutting. The flat pieces of leather are cut with intricate detailing and clean edges.
- Metal is also among the laser cut materials, which may include sheet metal such as aluminum or stainless steel, which helps create prototypes for signage or decorative.
- Plastic in various forms may also be cut using lasers, and with ample speed, they help create parts with variations.
How to Laser Cut Prototypes?
Laser cut prototyping comprises some steps, and these are provided below:
1. Specify the Purpose of the Prototype
The very first thing is identifying the main aim of the prototype, the purpose it will serve, and what features it must have. You need to identify the state of the prototype. You need that whether it is a visual prototype or functional or a combination of both. At this step, you will be able to have an idea of the components required and the vision you have to accomplish.
2. Create a Design of Prototype
The second stage requires you to create a drawing or sketch of a prototype; it comprises a CAD model as well, which helps you visualize the product and the areas that need improvement.
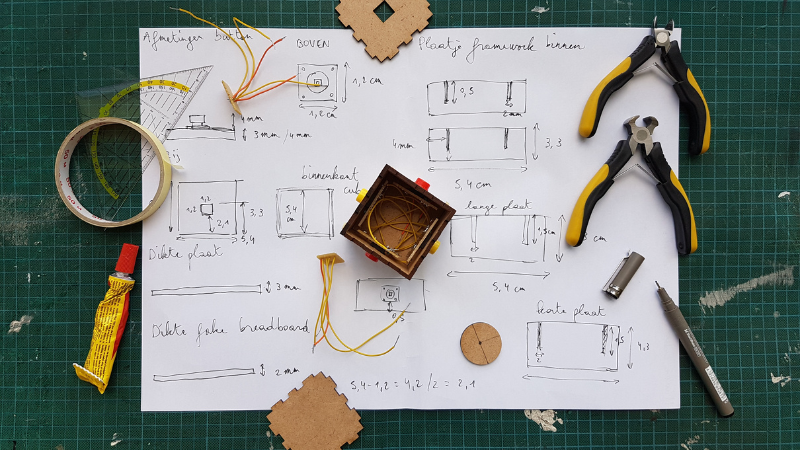
3. Selection of Materials
The materials you need to create the prototype must be chosen; there could be various forms to choose from, like cardboard, plastic, wood, or metal. The functional prototype will produce the material to be selected.
4. Creating the Prototype
With the sketches and designs you have created, you can use and create a prototype with the materials chosen; the process used is laser cutting, and through this, you can easily attain the design you want to make.
5. Testing the Prototype
After the prototype has been created, you must test it and ensure that it meets the design requirements and also make the required adjustments by taking feedback from the customers to make changes.
6. Making the Final Prototype
Once you have got the prototype approved, you can now create the final product with the help of high-quality materials as well as the finest manufacturing process.
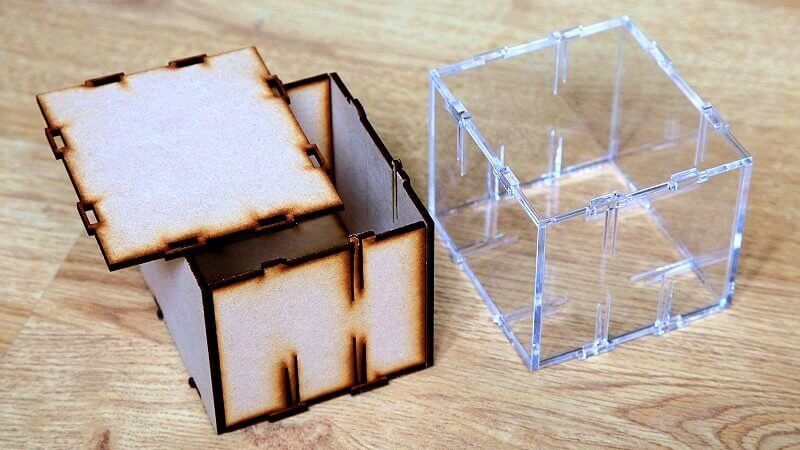
Application of Laser Cutting Prototypes
When new products are created, the prototype may be required for the final product creation when manufactured in mass volume. Initially, the prototypes are manufactured in low volume to verify the design and test it; if approved, the designers create the final product.
There are various applications of laser cutting prototyping, and some of these are as follows:
- Engineers make use of laser cut prototyping so that mechanical components can be created and tested based on the digital designs. Industries like machinery production, automobiles, automobiles, and many more develop prototypes before the actual product.
- Architectural models are also created by architectural firms by laser cutting to create models of buildings; it helps in visualizing the design before the construction starts.
- Electronic enclosures, components, and labels also make prototypes beforehand; it is commonly observed in the development of gadgets and electronic equipment.
- In the field of medicine, highly precise components are required, like surgical devices, prosthetics, etc., and the prototyping for such components is carried out through laser cutting tools.
Comparison of Laser Cutting Prototypes and Other Methods
Some methods are used when it comes to prototyping. Some of them are CNC machining, waterjet cutting, and 3D printing, and these are alternatives to laser cutting. Each of these methods has its own characteristics, and these are discussed in the table below.
Features | Laser Cutting | CNC Machining | 3D Printing | Waterjet Cutting |
---|
Safety and Best Practices
When it comes to creating laser-cutting prototypes, some of the safety precautions that you must take are as follows:
- Always read the manual that comes with the laser cutting machine and learn about the safety guidelines and other details on operating the machine.
- While you are carrying out the laser cutting process, make sure to wear PPE followed by safety glasses for protection against the laser.
- Laser cutting must be performed in an area that is well-ventilated; make sure to have exhaust systems so that any fumes and particles do not cause a problem.
- Make sure that the area where laser cutting machines work is restricted to authorized personnel only to avoid any hassle.
- Implement measures for fire prevention, and for this, you can use flame-resistant materials or have a fire extinguisher in your surroundings.
- Always carry out regular inspections and maintenance of the laser cutting machine and make sure the components are always working fine. In case it has any worn-out parts, make sure to replace or repair them.
FAQs
1. Is it possible to create 3D prototypes using laser cutting?
Laser cutting is a process used for 2D prototyping. These 2D components need to be manually assembled to form the desired 3D structure, rather than being cut directly.
2. Does the laser-cutting process have any thickness limitations?
Ans. Yes, the laser cutting process has limitations on the thickness of materials it can cut, and this effect depends on the laser power. If the machine offers lower-power lasers, then thick material may need to go through multiple passes.
3. Is laser cutting a suitable method for mass production?
Ans. Laser cutting is suitable for low-volume prototyping, and for large-scale prototyping, methods like stamping and molding are convenient.
Conclusion
The guide above must have been of great help to you and would have given you an insight into every aspect that is related to laser cutting technology and how it can be useful for prototyping. You can make the most of the details shared above and implement them in your upcoming project to attain seamless results.
Breakthrough Prototypes with Baison Laser Cutters!
Baison laser cutting machines have been the talk of the town, offering the finest cuts with high precision and optimum results. These machines provide a lot of relevance when it comes to catering to your prototyping task. They are being chosen industrywide for multiple laser-cutting projects, so get in touch with Baison Laser today!