In this definitive guide to laser welding parameters, we will explore how these factors impact the quality of welds. In this blog post, we’ll explore the intricacies of laser power control and the role of lasers in delivering consistent energy output. We’ll also examine the importance of maintaining an optimal balance between power density, focus, light, and strength.
Understanding the Basics of Laser Welding
Laser welding is a cutting-edge technology that offers precise and efficient joining of materials. There are various types of laser welding processes, each with its own advantages and applications. Let’s delve into the basics of laser welding to gain a better understanding.
Brief Overview of Laser Welding Technology
- Laser welding utilizes lasers, high-powered laser beams, to melt and fuse materials together through brazing and deep fusion. The process involves the use of lasers to create metal vapor, which then melts and fuses the materials.
- The laser beam is focused on the joint area, generating intense heat that causes the materials to melt and form a strong bond.
- This process offers exceptional accuracy, allowing for precise control over the weld depth and width. It is an automatic laser welding system that provides efficient welding automation.
- Laser welding is a versatile process that can be used for welding stainless steel, as well as other materials such as plastics, ceramics, and even dissimilar workpieces.
Types of Laser Welding
- Laser Beam Welding: This method involves using a concentrated laser beam to join materials without any additional filler material. It is commonly used for brazing and deep fusion of steel workpieces. It is commonly used for brazing and deep fusion of steel workpieces. Laser Beam Welding is commonly used in industries such as automotive, aerospace, and electronics.
- Laser Fusion Welding: In this technique, the laser beam generates enough heat to completely melt the base metals being joined. A filler material may be used for added strength if necessary.
- Automatic Laser Welding: This type of laser welding is performed using robotic systems or automated machinery. It ensures consistent weld quality and high production rates. Whether it’s heat conduction welding or deep penetration welding depends on the specific settings and intended application.
- Handheld Laser Welding: Handheld laser welder offers flexibility and ease of use for smaller-scale applications or on-site repairs of the workpiece. These handheld laser welders are efficient and reliable.
- Laser Deep Fusion Welding: This advanced technique enables deep penetration into thick materials while maintaining excellent weld quality.
- Laser Welding Services: Many companies provide specialized services for laser welding projects, offering expertise and equipment for various applications.
Understanding the fusion process in laser welding machines is crucial for exploring the vast possibilities of working with steel workpieces. Whether it’s power laser welding technology in industrial settings or handheld laser welders for smaller tasks, laser welding machines, and equipment can revolutionize the way workpieces are joined. With the fusion of laser light energy, materials can be seamlessly combined.
Key Factors to Consider for Optimal Laser Welding Parameters
Choosing the right laser welding parameters is crucial for achieving optimal results. Several key factors should be taken into consideration throughout the process.
Importance of Material Selection
The choice of materials and workpiece plays a significant role in determining the ideal laser welding parameters. The right equipment and plasma technology are crucial for achieving optimal results. Different materials have varying melting points and thermal conductivities, which directly impact the laser welding and laser brazing processes.
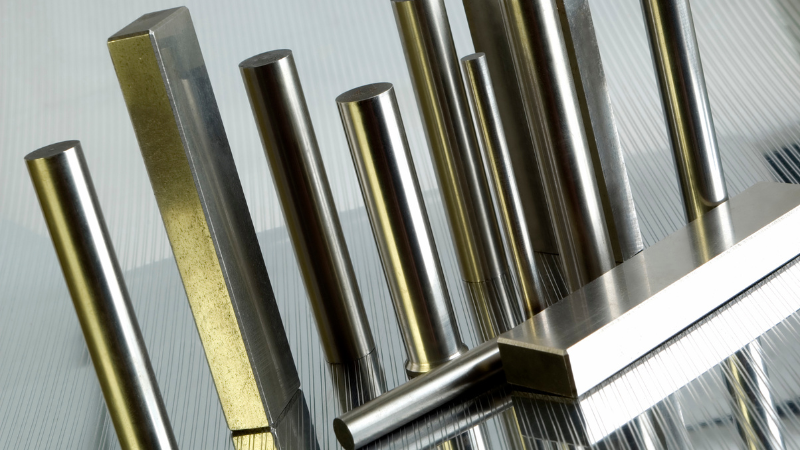
The laser welder and laser brazing fusion are used to join the workpiece together. For instance, certain welding technology laser powers may be more suitable for specific materials in the composite welding process, ensuring efficient joining without compromising structural integrity using the welding machine.
Impact of Joint Design
The weld joint design also influences the selection of laser welding parameters for the workpiece. This is because different technology and equipment are used for different workpieces and machines. Factors such as joint geometry, fit-up, accessibility, welding process, welding speed, and laser welder affect heat distribution and weld quality in composite welding.
By carefully considering the welding process and using the right composite welding techniques, welders can optimize their settings to achieve strong and reliable joints while minimizing defects like porosity or lack of fusion. This can be achieved by adjusting the welding speed and using the appropriate laser welding equipment.
Controlling Heat Input
Controlling heat input during laser welding is essential to prevent undesirable outcomes such as excessive distortion or damage to the workpiece surface. Various parameters contribute to regulating heat input effectively:
- Focal length: Adjusting the focal length of the laser source enables precise control over energy concentration.
- Focus position: Properly positioning the focus point ensures optimal energy delivery at desired locations.
- Plate thickness: The thickness of the workpiece affects heat dissipation, penetration depth, and the welding process.
- Spot size: Modifying spot size allows for flexibility in managing power density.
- Melt depth: Monitoring melt depth is crucial in the laser deep fusion welding process to ensure consistent weld quality. This can be achieved by controlling the welding speed using advanced laser welding machines.
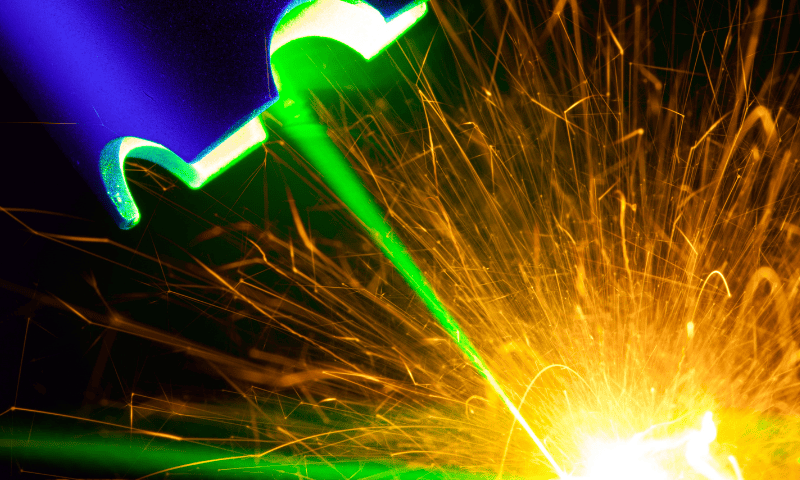
Additional Considerations
In addition to material selection, joint design, and heat control, several other factors influence laser welding parameters:
- Filler metal: Depending on the application requirements, filler metals can enhance strength or improve corrosion resistance.
- Shielding gas: Choosing appropriate shielding gases in the welding process helps minimize spatter formation and maintain arc stability with laser welding equipment. Handheld laser welding machines can also benefit from the use of shielding gases.
- Machine labor cost: Optimizing laser welding machine parameters can reduce labor costs by improving efficiency and minimizing rework on the equipment.
By considering these key factors, welders can determine the optimal laser welding parameters for each specific application. This ensures high-quality welds with minimal distortion and reliable performance.
Key Parameters in Laser Welding and Their Significance
Laser welding parameters play a crucial role in determining the quality and efficiency of the welding process. Understanding these key parameters is essential for achieving optimal results. Let’s explore the significance of each parameter:
Power Density
The power density of the laser beam has a direct impact on the penetration depth and weld width. Higher power densities in laser welding machines result in deeper welds with wider fusion zones, while lower power densities produce shallower welds. Laser welding equipment uses a welding process that melts the materials together to create strong and durable welds. Adjusting the power density allows for precise control over the weld characteristics.
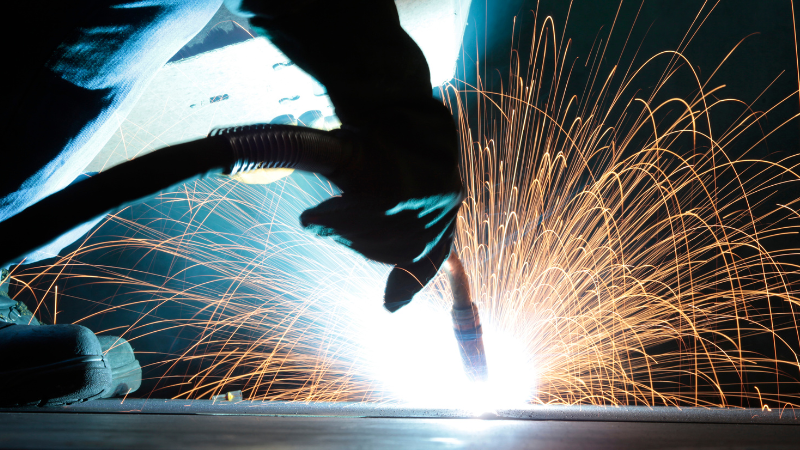
The laser power density used during welding can reach up to 10^7 watts per square centimeter! This immense power of laser welding machines enables precise and efficient melting of metals, resulting in strong and durable welds. Laser welding equipment, such as handheld laser welders, is used for this purpose. Different types of lasers, such as semiconductor lasers, CO2 lasers, and YAG lasers, offer varying power capabilities for different applications.
Pulse Duration
The pulse duration of the laser beam influences the size of the heat affected zone (HAZ). Shorter pulse durations minimize heat transfer to surrounding areas, forming small heat affected zones. Conversely, longer pulse durations can lead to larger HAZ, potentially affecting material properties. Optimizing pulse duration ensures minimal distortion and maintains desired mechanical properties.
Beam Diameter
The overall diameter of the laser beam also affects welding outcomes. A narrower beam diameter from a laser welding machine concentrates more laser energy onto a smaller area, resulting in increased penetration depth. This is why laser welding equipment is highly effective. Conversely, a wider beam diameter from a laser welding machine spreads energy over a larger area, leading to shallower welds but covering more surface quickly with the equipment.
Welding Speed
Welding speed determines how fast two materials can be joined together using laser technology. Faster welding speeds increase productivity but may compromise penetration depth or fusion quality if not optimized properly. Slower speeds allow for better control but might result in longer production times.
By carefully adjusting these laser welding parameters – power density, pulse duration, spot size, beam diameter, and welding speed – manufacturers can achieve the desired weld characteristics, optimize productivity, and ensure high-quality welding results.
The Interplay of Parameters
Laser welding parameters play a crucial role in the overall welding process. Understanding how different parameters interact with each other is essential for achieving optimal results. Here, we explore the interplay of parameters and their impact on laser welding.
During laser welding, various process parameters come into play, affecting the stability, deformation, penetration, power, temperature, and properties of the weld. Let’s delve into some key aspects:
Parameter Combinations
Different parameter combinations yield varying outcomes in specific applications. For example:
- Higher power settings on a laser welding machine increase weld penetration but may also lead to increased heat input.
- Adjusting the focal point of a laser welding machine can significantly impact surface quality and allow for precise control of heat distribution.
- Motion system speed influences the overall welding speed and precision.
An increase in laser power might demand a corresponding adjustment in welding speed to maintain the desired weld depth and quality. Similarly, modifying the pulse duration can impact the heat affected zone and require alterations in shielding gas flow rate or type.
Consider another example: If the beam diameter is decreased (resulting in a more concentrated focus), the laser’s intensity increases. This may necessitate a reduction in laser power or an increase in welding speed to prevent burn-through or excessive weld width.
Balancing Trade-offs
When selecting parameters, it’s crucial to strike a balance between speed, quality, and cost. This involves considering factors such as:
- Welding speed: Faster speeds may compromise weld quality.
- Heat input: High heat input can affect material properties.
- Surface preparation: Proper cleaning and preparation contribute to better results.
Instead of adjusting parameters in a piecemeal fashion, professionals should consider the entire system. Leveraging computer simulations or modeling software can be invaluable when working with lasers, allowing technicians to predict outcomes based on various parameter combinations before actual laser welding.
Material Considerations
While machines and lasers function based on set parameters, the materials being welded have their own intrinsic properties, like melting point, reflectivity, and thermal conductivity. These can introduce another layer of variability into the welding process. Thus, understanding material responses and adjusting parameters holistically becomes paramount.
Different materials require specific parameter adjustments due to variations in their thermal conductivity and melting points. Factors to consider include:
- Material surface condition: Surface roughness affects laser absorption.
- Composite materials: Welding dissimilar materials requires careful parameter selection.
Understanding how these parameters interact enables welders to optimize their processes for desired outcomes while minimizing defects or issues that may arise during laser welding.
Practical Tips for Setting Laser Welding Parameters
Setting the right parameters is crucial for achieving optimal results. Here are some practical tips to help you navigate this process effectively:
1 – Starting with manufacturer recommendations
- Manufacturers often provide recommended parameter ranges for different materials and thicknesses.
- Begin by referring to these guidelines as a starting point for your specific welding application.
2 – Selecting initial parameter values based on material thickness
Consider the thickness of the material being welded when determining initial parameter values.
Thicker materials generally require higher laser spot power density, while thinner materials may need lower power density.
Adjust other parameters such as pulse duration and frequency accordingly for laser welding to ensure proper weld penetration and quality.
3- Techniques for monitoring key variables during the welding process
- During laser welding, it is essential to monitor certain variables to maintain control over the process.
- Use sensors or cameras to measure factors like temperature, melt pool size, and beam pattern. You can learn about how to monitor the laser welding process via a coaxial pyrometer.
- Real-time monitoring in laser welding allows you to make necessary adjustments and ensure consistent weld quality throughout the operation.
4 – Strategies to troubleshoot common issues related to incorrect parameter settings
- Incorrect parameter settings can lead to various welding issues such as incomplete fusion or excessive spatter.
- If encountering problems, consider adjusting one parameter at a time while keeping others constant until desired results are achieved.
- Analyze laser welding samples under a microscope or perform non-destructive testing techniques like ultrasonic inspection to assess laser weld integrity.
By following these practical tips, you can optimize your laser welding parameters and enhance overall productivity and quality in your welding processes. Remember that finding the ideal parameters may require experimentation and fine-tuning based on your specific requirements.
Advanced Techniques and Innovations
In the world of laser welding, technology is constantly evolving to meet the demands of various industries. Here are some advanced innovations.
Emerging Trends in Adaptive Control Systems
One of the emerging trends in the development of adaptive control systems is the integration of laser technology, allowing for real-time adjustments to welding parameters. These advanced automation technologies enable precise control over the laser welding process, ensuring high quality and efficient production.
With adaptive control systems, manufacturers can optimize parameters such as power, speed, and beam shape for laser welding based on real-time feedback from sensors. This level of laser welding automation technology not only improves productivity but also enhances the overall quality of welded products across different materials and industries.
Application-specific Advancements in Laser Beam Shaping Technologies
Another area where innovation is taking place is in laser beam shaping technologies. Manufacturers are continuously developing methods to shape laser beams according to specific application requirements.
By tailoring the shape and intensity distribution of the laser beam, precise control over heat input can be achieved. This allows for deep penetration welding while minimizing distortion or damage to surrounding areas. Such advancements in laser beam shaping technology offer a high degree of flexibility and enable efficient laser welding across a wide range of materials and product types.
The Advent of Hybrid Laser Welding
Hybrid laser welding combines the benefits of both conventional arc welding and laser welding techniques. By integrating welding lasers with traditional arc-based welding processes, manufacturers can take advantage of the advantages offered by each welding method.
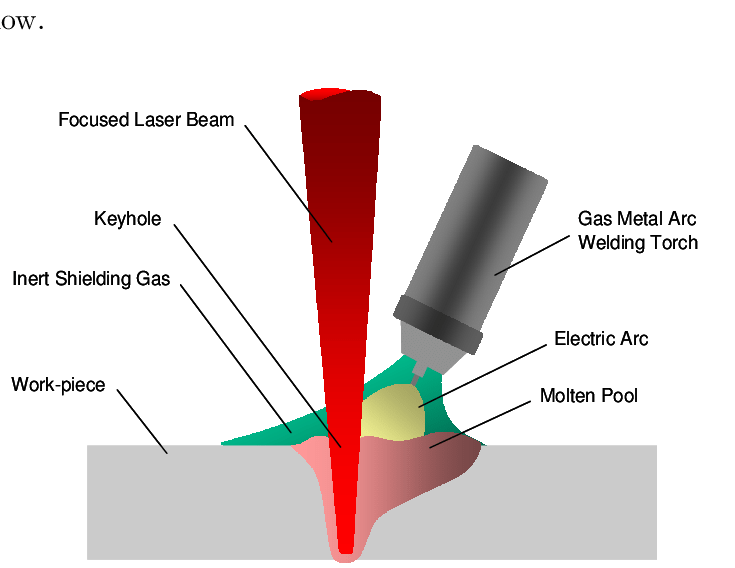
Hybrid laser welding provides a high-power heat source combined with precise control from lasers, resulting in improved weld quality and increased productivity. This laser welding technique is particularly advantageous when working with thicker materials or when deep penetration is required.
Integration of Artificial Intelligence Algorithms
Artificial intelligence (AI) algorithms are being integrated into laser welding equipment to optimize parameter selection automatically. These algorithms analyze data from sensors and make intelligent decisions regarding laser welding power levels, feed rates, focus positions, etc., based on predefined criteria or machine learning models trained on historical data.
By leveraging AI, manufacturers can achieve higher efficiency and accuracy in parameter selection for laser welding, leading to improved weld quality and reduced production costs.
FAQs
What materials can be welded using laser welding?
Laser welding is versatile and compatible with a wide range of materials such as stainless steel, aluminum alloys, carbon steels, titanium alloys, nickel-based alloys, and more. However, it’s important to note that different materials may require specific parameter adjustments for optimal results.
Can I adjust the pulse duration during laser welding?
Yes! Pulse duration affects both heat input and cooling rate during the welding process. Shorter pulses in laser welding provide higher peak powers and faster cooling rates, which are beneficial for minimizing heat-affected zones and achieving precise welds. Adjusting pulse duration allows you to optimize the welding parameters for different applications.
What is the significance of focal spot size in laser welding?
The focal spot size determines the energy density at the point of interaction between the laser beam and the material. Smaller focal spots in laser welding result in higher energy densities, enabling finer control over weld width and depth. However, when selecting the appropriate focal spot size for laser welding, it’s important to consider factors such as beam quality, material thickness, and laser welding.
How can I ensure consistent weld quality during laser welding?
Achieving consistent laser welding quality requires careful monitoring and control of parameters such as laser power, pulse frequency, travel speed, shielding gas flow rate, and focus position. Regular inspection of laser welding equipment, maintenance routines, and operator training also contribute to maintaining consistent results over time.
Conclusion
Congratulations! You have now gained a comprehensive understanding of laser welding parameters and their significance in achieving optimal results. By delving into the basics, exploring key factors to consider, and examining the interplay of parameters, you are well-equipped to set laser welding parameters effectively. We have provided practical tips for fine-tuning your settings and introduced advanced techniques and innovations that can take your laser welding capabilities to new heights.
Unlock the Full Potential of Laser Welding with Baison Laser!
If you’re ready to take your laser welding skills even further, we encourage you to explore our range of advanced laser machines. Whether you’re looking for the precision of our Handheld Laser Welding Machine, the automation of our Laser Welding Robot, or exploring other state-of-the-art laser solutions, we’ve got you covered. Dive deeper into the world of laser technology and let us elevate your operations. Click here to explore our top-notch laser welding equipment now!
