Laser-cutting machines are powerful cutting tools that can efficiently cut through various materials. These machines have replaced other cutting machines due to their ease of use, efficiency, and precise cutting. Fiber lasers are a further step ahead in laser cutting machines and are used in industries where precise and accurate laser cutting is required.
This article is all about the fiber laser cutting process. We will discuss all-fiber lasers, their benefits, and how you can have better product quality and consistent performance.
What is a Fiber Laser Cutting Process?
A fiber laser cutting machine is a powerful tool that uses a high-intensity laser beam to cut through hard and thin materials. These machines are used in small to big-scale industries requiring high-precision cutting.
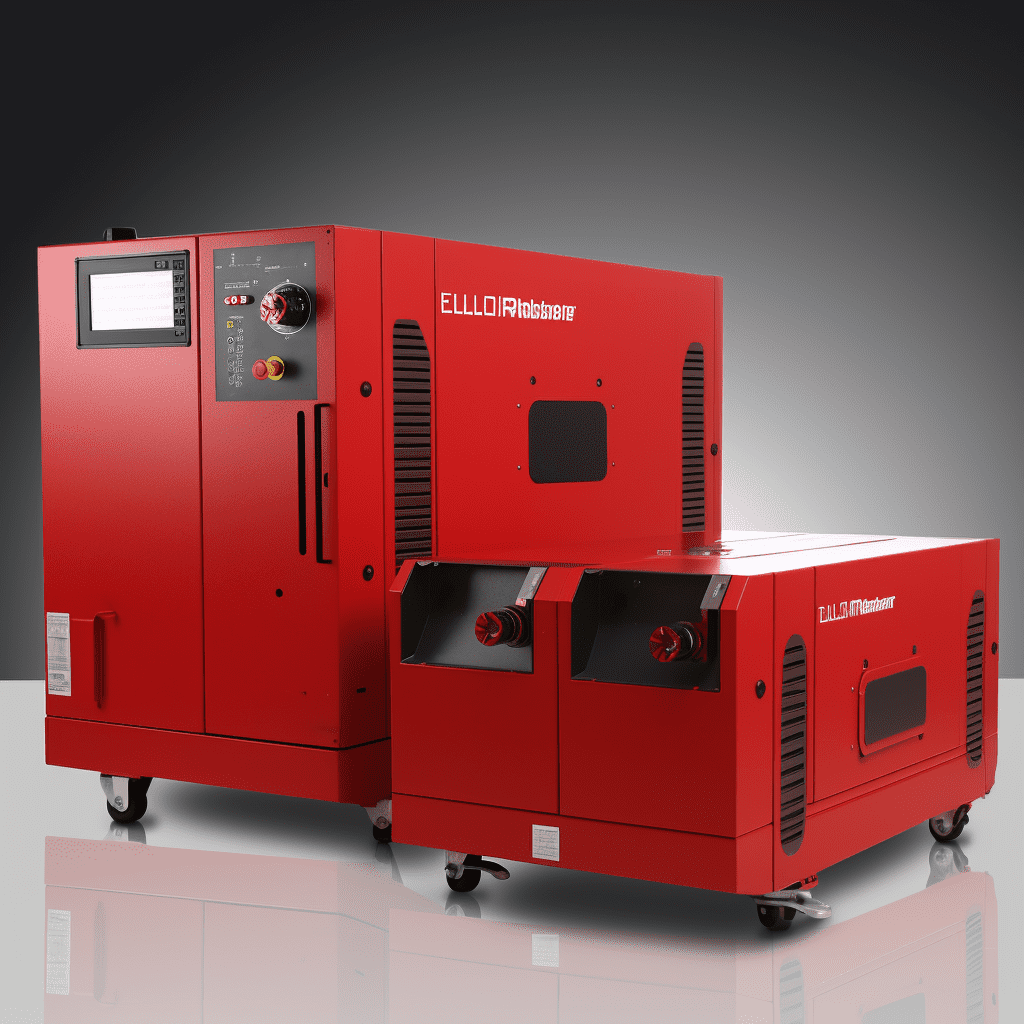
A fiber laser cutting machine works like any other, but the difference is that a laser beam is passed through a lens. Fiber laser cutters use a process of stimulating emission. The laser head emits a highly powerful laser beam passed through a lens or mirror that repeatedly reflects the beam until it is concentrated enough to cut through the toughest materials easily.
Fiber lasers utilize thin fiber cables that transmit the wavelengths to the material’s surface. The focused heat of the laser beam immediately melts the material and vaporizes it. The laser beam moves through a CNC system (computer numerical control system) that moves the beam according to the required design. The beam cuts through the material, moving with precision and accuracy and cutting through different materials.
Ready to Get Your Own Laser Machines?
Boost your operations with Baison Laser's advanced, customized technology!
Advantages of Using Fiber Laser Processing
Here are a few advantages of fiber laser cutting machines:
1. High Precision
Fiber laser cutters are more expensive than other laser cutting machines like CO2. They offer high precision and are capable of cutting complex shapes with precision. Whether handling thick plate cutting or delicate materials, fiber laser technology does justice to both.
2. High Processing Speed
Fiber lasers are high-tech machines that work with unmatched speed. They reduce the production time drastically if we compare these machines with traditional means of cutting. They can process material of high volume.
3. Low Operating Cost
Laser machines may be costly, but they offer low operating costs. These are modern machines that are capable of handling mass production. The operating cost is much less than other machines, and the precision rate is much higher. These machines reduce production costs by processing more material in less time. They also require less maintenance.
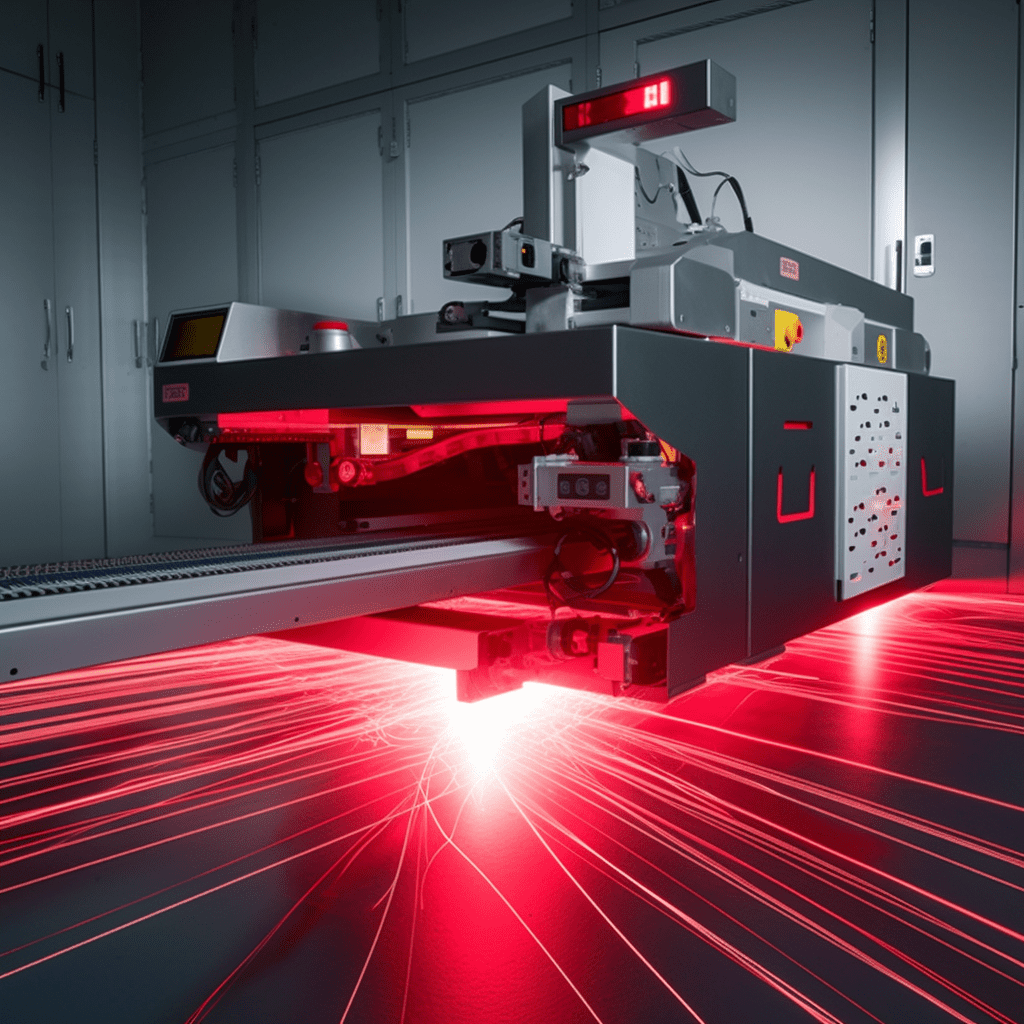
4. Versatility
Laser machines are great for metal or alloys and can cut various materials. Many industries must cut materials like ceramics, plastic, glass, and even paper. A fiber laser machine is one solution for different materials. It can work with the same precision on almost all materials.
5. Minimal Waste
Fiber laser uses a focused beam to cut material. The size of the beam is extremely narrow, which not only suits the need to cut thin material but produces minimal scraps. The metal sheets or tubing are cut to the maximum accuracy, so there is minimal loss. Fiber laser cutting machines produce minimal waste compared to other cutting methods.
6. Automation
Modern machines in industries have limited manual jobs. Fiber laser machines can also be fully automated. They can process high-volume material with less manual intervention. Almost all processes are automatic. Even for feeding, you can use Coil-fed fiber laser machines, eliminating the need for manual feeding.
How Does Laser Beam Melt the Material During Cutting Process?
We have already mentioned how laser machines produce a high-power beam to cut through the material as the laser beam is passed through the mirrors or lenses and gets concentrated. This concentrated beam hits the surface of the material. Fiber laser beam uses laser-active ytterbium ions that operate at 1,060–1,080 nm spectral range.
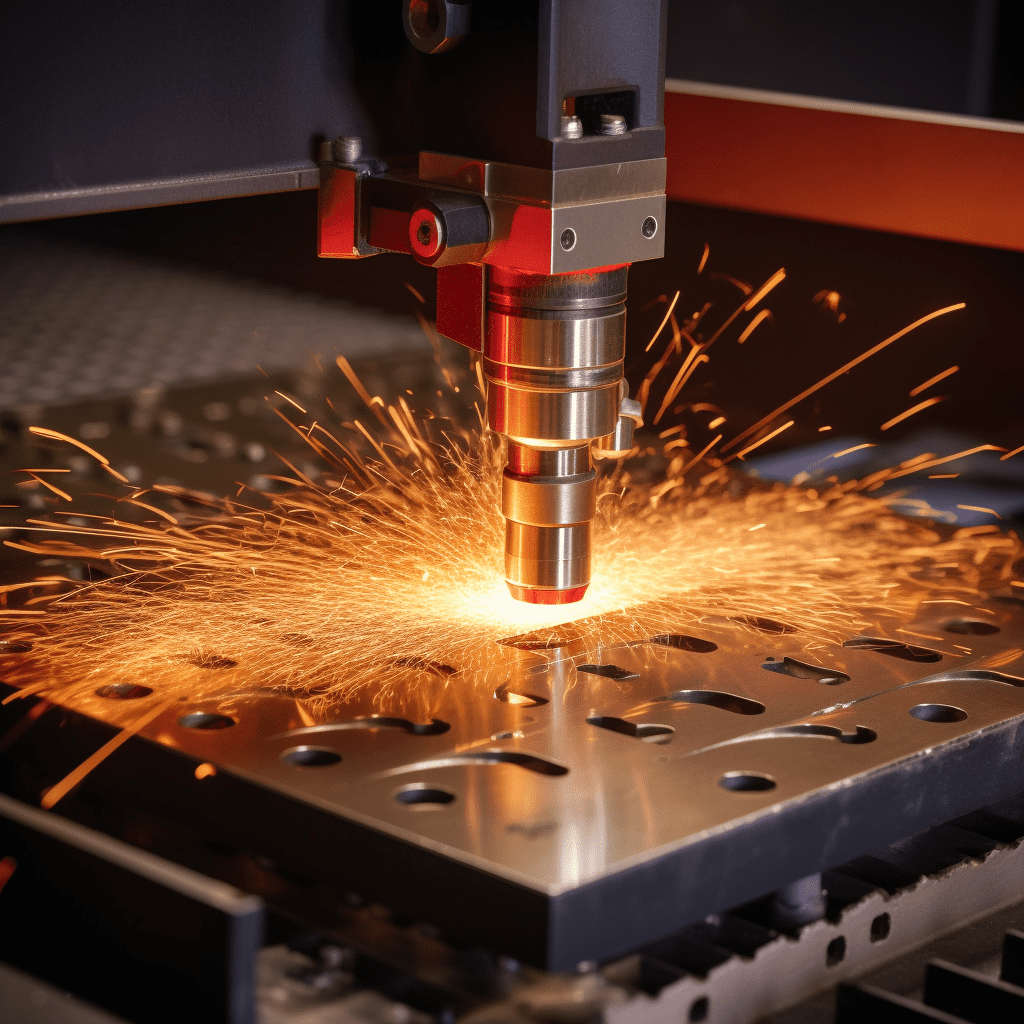
It’s a unique combination of high-powered beam quality and near-infrared wavelength. This ability offers it a unique capability to process different types of materials. The beam quality offers higher absorptivity than other laser systems. It has more energetic photons that are better absorbed by the electrons of the sheet metal surface.
Fiber laser cutting machines offer more flexible beam handling. The workpiece absorbed the laser beam at a higher rate, which caused the melting of the laser beam and material interaction zone. It not only enhances the cutting speed but is a speedier process.
Ready to Get Your Own Laser Machines?
Boost your operations with Baison Laser's advanced, customized technology!
How to Improve the Quality of Laser Cutting?
Laser cutting machines are precise and accurate though there are several ways to improve the cutting quality.
1. Select a Suitable Laser
Even laser cutting machines come in different types. Instead of choosing a high-powered laser, choose the power that suits the material you need to process. Each one has its advantages. Choose the laser system that suits the material you need to process.
2. Optimize Cutting Parameters
Laser-cutting matches have different parameters that operators or trained staff need to adjust. These parameters are the power; speed can determine the cutting quality.
3. Keep the Lens Clean
The laser beam is directed through the lenses. Make sure these lenses or mirrors are dirt and debris. During production, dirt and debris can accumulate on these lenses. They can affect the power and intensity of the beam.
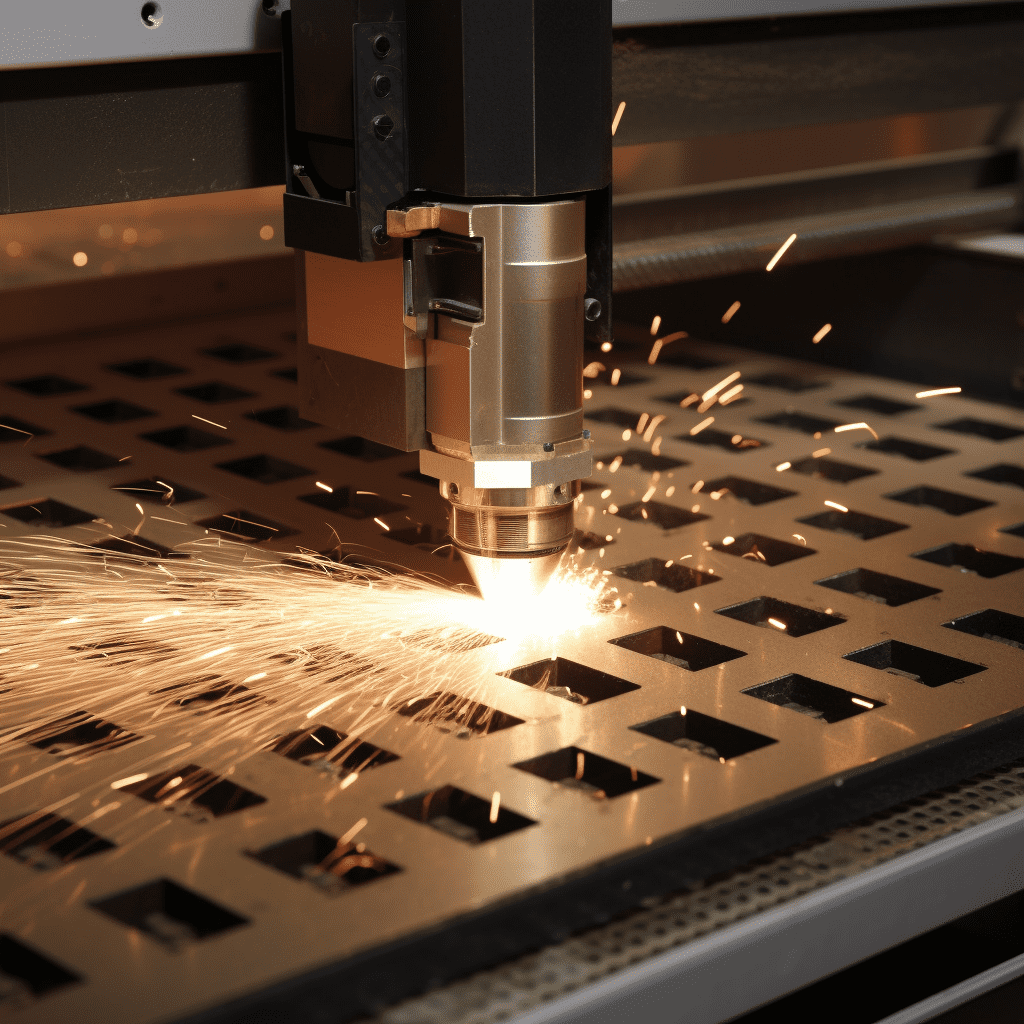
4. Check the Nozzle
Nozzles are among the consumables. It should be regularly checked to ensure high production quality.
5. Use High-quality Materials
Good material is essential for a good quality end product. Make sure the material is clean of oil, polish, or rust. It should have consistent thickness and composition for a clean cut.
6. Minimize Thermal Distortion
As we have said, cutting parameters should be adjusted according to the type of material. Thermal distortion can occur during cutting, particularly when cutting thin materials. The right speed and power can minimize thermal distortion.
7. Use a Proper Cutting Table
A proper one is essential for processing material. It should not reflect the laser light, and the cutting surface should be even.
8. Optimize the Dimensional Accuracy
The dimensional accuracy of fiber laser machines can be optimized by adjusting the laser power, speed, and focus point. The operator should ensure the beam is focused on the optimal position before processing. A poorly focused beam can affect the accuracy and distort the material. Finding the right balance between speed and accuracy is key.
- Nozzle Diameter: The nozzle diameter used during cutting can also affect accuracy. A smaller diameter nozzle will produce a narrower kerf, leading to better accuracy, but it may also slow down the cutting process.
- Material Thickness: The thickness of the material being cut can also affect the accuracy of the cut. Thicker materials may require more laser power, increasing the heat-affected zone and leading to distortion. Be sure to adjust laser power, speed, and focus point to the specific thickness of the cut material.
- Material Type: Different materials have different properties, which can affect the accuracy of the cut. Be sure to choose the appropriate laser settings for the cut material.
- Machine Calibration: Ensure the machine is calibrated and aligned correctly to avoid errors during cutting. Regular maintenance and calibration can help ensure accurate cuts.
What are the Cutting Parameters for Fiber Lasers?
The cutting parameters for fiber lasers depend on several factors, such as the material being cut, its thickness, the power of the laser, the type of nozzle being used, and the speed of the cutting process.
Some of the cutting parameters that are typically considered for fiber lasers are:
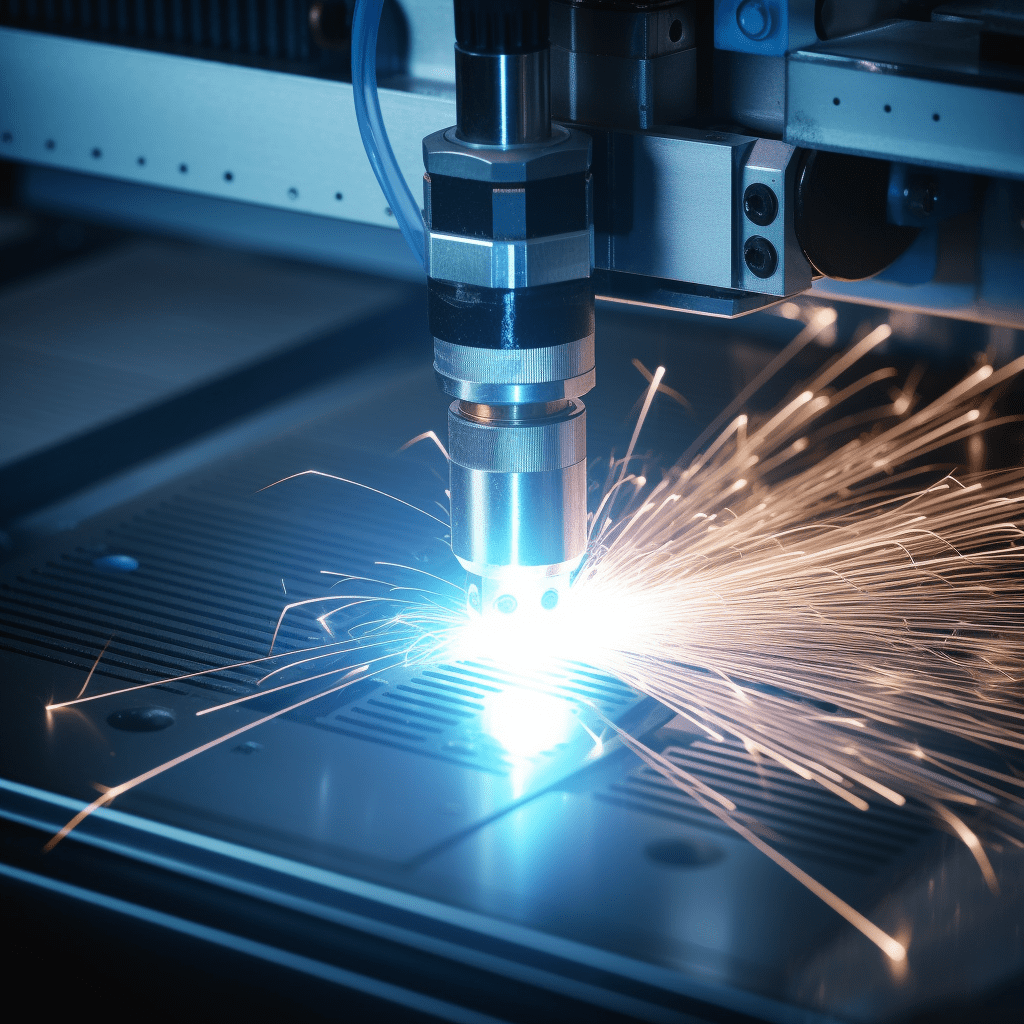
Power: You may not need h higher fiber laser powers for every material. The power density of the laser is one of the most critical cutting parameters. It determines how much energy the laser can deliver to the cut material. The higher the power, the faster the cutting process.
Cutting speed: The cutting speed is the speed at which the laser moves across the cut material. It is usually measured in meters per minute (m/min) or inches per minute (rpm). The cutting speed should be optimized for the cut material to achieve the best cutting quality and efficiency.
Focus: The focus of the laser beam is essential to achieve the desired cutting results. The focal point of the laser beam should be set at the right distance from the surface of the material being cut to obtain the best cutting quality.
Gas pressure: The gas pressure used in the cutting process is critical in determining the quality of the cut. The assist gas used in laser cutting can be oxygen, nitrogen, or a mixture of both, and the pressure can be adjusted based on the material being cut.
Nozzle diameter: The diameter of the nozzle also determines the cutting quality. A small nozzle will give finer cuts and is more suitable for intricate thin-cutting. A larger diameter nozzle will produce a coarse cut but may produce better results in tough metals, whereas a thin nozzle may take longer to cut. The nozzle selection should depend on the material type and cut quality.
Piercing time: It takes time to pierce through the material also matters. It should be set according to the type of material. Slow time may not produce the desired results, and fast time may damage the material.
Ready to Get Your Own Laser Machines?
Boost your operations with Baison Laser's advanced, customized technology!
How Do You Have a Better Laser Cut Edge while Sheet Processing?
Despite all the speed and accuracy of laser-cutting machines, the processed parts are of little use if they have poor cut-edge quality. Sharp edges will need deburring and may cause safety concerns for the operating staff. The cut-edge quality of the fiber laser machine also depends on the right parameter setting, the right nozzle size, and good material.
How to Have Consistency in Precision Cutting from Fiber Laser?
Here are a few tips for manufacturers to have consistent cutting results from fiber laser systems.
Machine Calibration: Make sure that the fiber laser machine is calibrated correctly. Check the machine’s laser beam focus and alignment and correctly calibrate it.
Material Preparation: Make sure the material does not have anything on the surface. It should be clean of debris, oil, or polis, and the consistency should be for even and uniform cuts.
Maintenance: Laser machines do not require frequent maintenance but also regular maintenance. It is to ensure the machines are in perfect working condition.
Operator Skill: Cutting quality, machine life, and safety depend on a trained operator. Make sure you have trained staff around laser cutting machines. They should have professional knowledge of different materials, machines, and their parts and how to identify and solve problems.
CO2 Laser vs. Fiber Laser
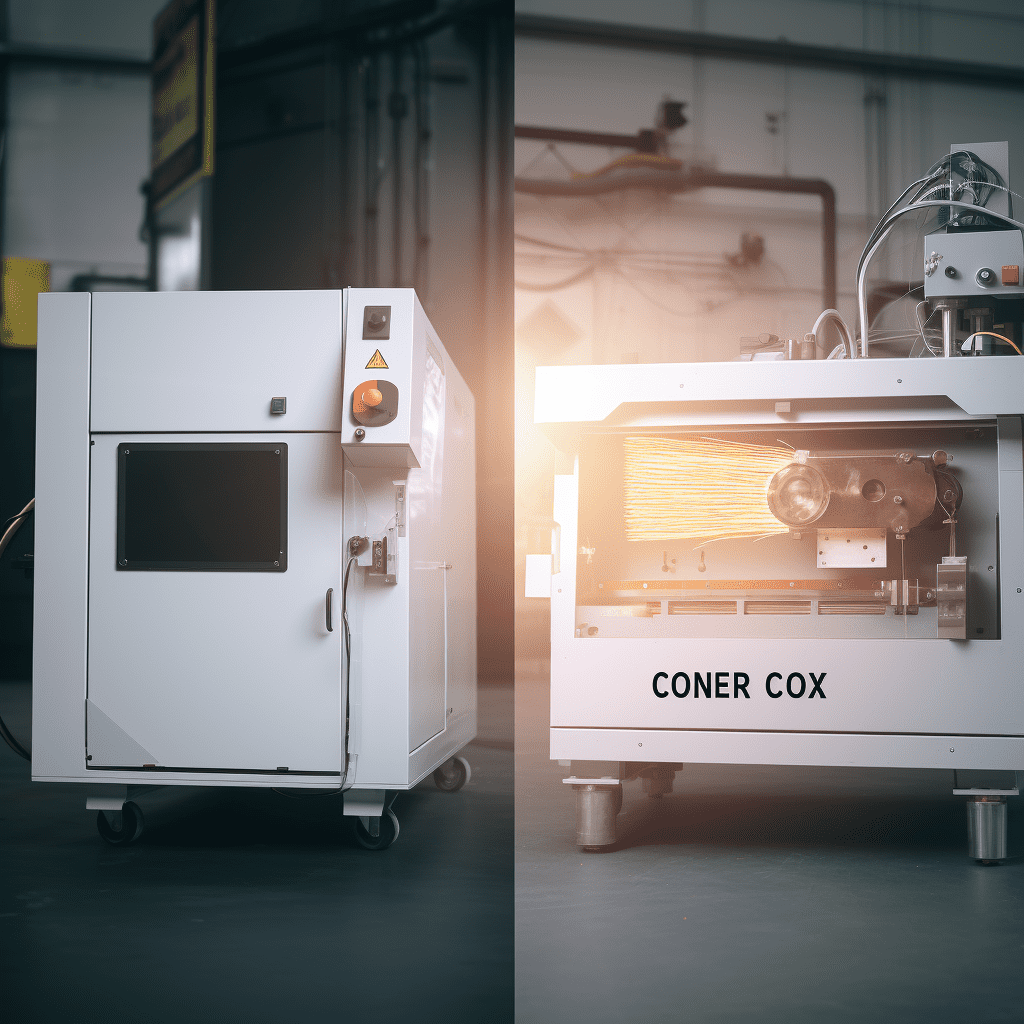
CO2 lasers also use a laser beam to cut through the material. However, they use an electronic driven gas laser. They use gas like oxygen or nitrogen for laser power. The choice of gas depends on the type of material to be cut. As compared to a fiber laser system, CO2 has a larger wavelength. The wavelength of fiber laser is in the infrared range and, thus, suits the cutting of reflective materials like stainless steel.
Here are the advantages of Fiber lasers vs. CO2 lasers:
- Fiber laser has high power output.
- They have short wavelengths that make them ideal for cutting tough metals. CO2 is better for engraving or cutting non-metals such as wood, acrylic, and glass.
- Fiber laser machines are smaller in size than CO2 machines.
- Fiber laser machines are high-speed compared to CO2 machines
- They offer fine and clean cuts.
Plasma Cutting vs. Laser Cutting: How to Choose
Plasma cutters are another type of machine that is used in metal fabrication. It uses a high-temperature plasma arc to melt the material. The torch creates a high-velocity jet of plasma gas that melts the material. Plasma cutters cannot match the speed and accuracy of laser-cutting machines. Cutting thickness: CO2 lasers are better suited for cutting thicker materials than fiber lasers.
1. Material Thickness
Plasma cutting is suitable for thick metals; It can cut up to 1.5 inches thick metal sheets. While laser cutting can cut thick and thin materials. It can handle even half an inch of aluminum, three-quarters of stainless steel, and one inch of steel.
2. Material Type
Plasma cutters can only cut material that conducts electricity. Laser cutters can cut even plastic, wood, and stone.
Laser cuts have difficulty cutting highly reflective metals like copper and brass, and plasma cutters are more suitable for them.
3. Cut Quality
Plasma cutting is rough and simple. At the same time, laser cutters are great for fine and accurate cuts.
Ready to Get Your Own Laser Machines?
Boost your operations with Baison Laser's advanced, customized technology!
How to Choose a Fiber Laser Cutting System?
Here are a few things you should consider while selecting the fiber laser cutting system,
1. Power
Fiber laser machines are available with different power options. There are small-scale fiber laser systems and medium and high-power laser systems designed for heavy industrial use. Consider the type of laser cutter that suits your manufacturing needs.
2. Material
Consider the type of material you want to cut and versatility if your manufacturing needs require more than one material type to process.
3. Price
The price of the machine is an important factor to consider. Make sure you choose a machine that fits within your budget.
4. After-sales Support and Brand Reputation
Laser machines are expensive, so make sure you invest in a brand that has a good reputation and offers after-sales support. You may need assistance with maintenance and repairs in the future.
5. Cutting Bed Size
The cutting bed size determines the material size you can cut. Choose a machine with a cutting bed that suits your needs.
6. Auxiliary Equipment
Consider the auxiliary equipment that comes with the machine, such as the software and the exhaust system.
Baison’s Fiber Laser Cutting Machines
Baison offers high-tech fiber laser cutting machine for small, medium, and large industrial needs. Our laser cutting machines are built on modern technology.
These machines can be fully automated, and manufacturers require less workforce for the fabrication process. They are user-friendly and require less maintenance. We offer small fiber laser cutters to high-power laser systems built for heavy industrial use.
Entry-level Sheet Metal Laser Cutter: Easy to Operate
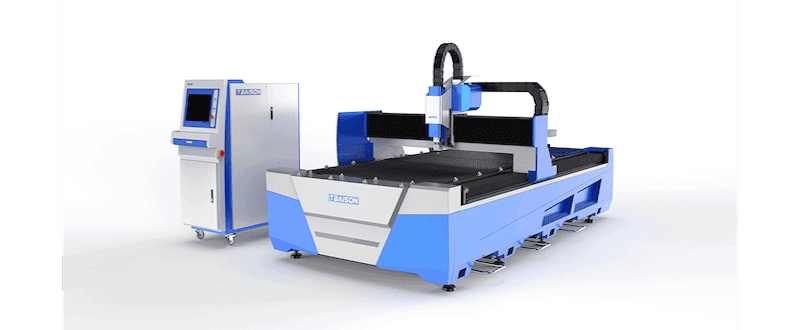
High Power Sheet Metal Laser Cutting Machine: Built for Heavy Industrial Use
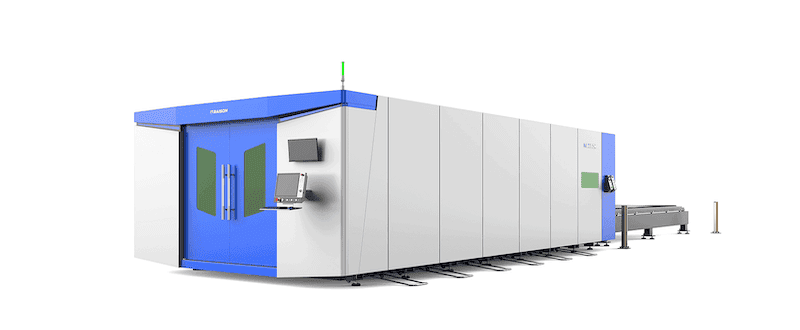
Conclusion
In summary, fiber laser cutting offers unmatched precision, speed, and versatility in manufacturing, making it indispensable for industries aiming for high-quality production. As technology advances, its role in revolutionizing precision cutting will only grow, underscoring its value in modern manufacturing.
Upgrade Your Manufacturing Needs with Baison’s Fiber Laser Cutting Machines
If you are looking for an efficient fiber laser cutter for your business, Baison offers advanced machines that are unparalleled in accuracy and precision. Our fiber laser machines can process many materials, including ceramic, wood, glass, metal, and plastic.
Our customer services are always there to answer your queries. We offer free sample proofing and free application evaluation to help you choose a laser machine that suits your industrial needs. Get in touch with us.