Laser welding technology revolutionizes the traditional methods of joining stainless steel components by utilizing a focused beam for deep penetration. This innovative laser technology showcases exceptional penetration depth, resulting in strong and reliable joins.
The weld region exhibits a refined structure, thanks to the small laser beam diameter and high feed rate, ensuring a strong bond point by point. Dive deeper into this groundbreaking method and explore its endless possibilities in joining stainless steel components.
The Science Behind Laser Welding of Stainless Steel
Laser welding is a highly efficient and precise method used to join stainless steel parts together. By harnessing the power of a high-energy laser beam, this laser welding process offers numerous advantages over traditional welding methods. You can see the difference between laser welding and various traditional welding methods such as MIG welding in our blog. Let’s delve into the science behind laser welding of stainless steel and explore its metallurgical aspects.
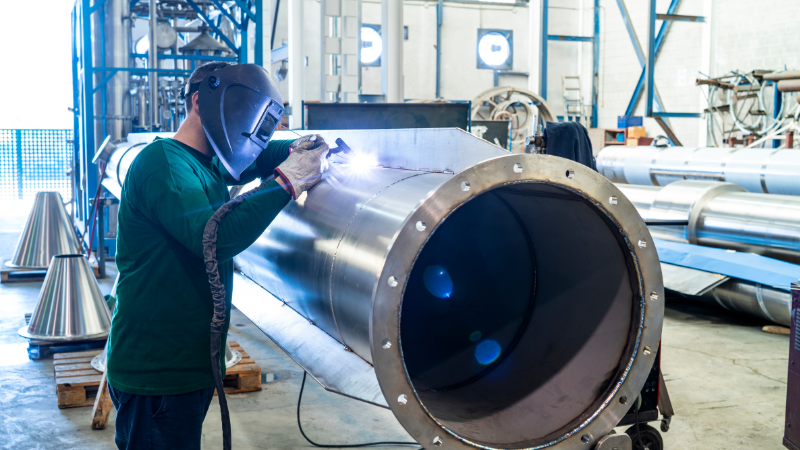
I. High-energy Laser Beam for Melting and Fusion
One of the key elements in laser welding is the utilization of a high-energy laser beam. This focused laser beam heats the targeted area, and delivers an intense amount of heat, causing the stainless steel parts to melt and fuse the molten material together in the fusion zone.
Unlike traditional welding methods, such as arc welding or gas welding, laser welding provides exceptional control over heat input due to its concentrated energy source.
II. Minimizing Distortion Through the Localized Heat Source
The use of a laser beam as a heat source offers significant benefits during stainless steel welding. Since the laser energy is precisely directed at the weld joint, it creates a localized heat source. This minimizes distortion in surrounding areas, resulting in a higher quality weld with reduced warping or deformation. As a result, post-welding treatments like straightening or stress relieving are often unnecessary.
III. Rapid Solidification and Minimal Microstructural Changes
During laser welding, rapid solidification occurs due to the high cooling process involved, which can result in hot cracking. This leads to the formation of a narrow heat affected zone (HAZ) around the weld joint.
The HAZ experiences minimal microstructural changes investigated by the optical microscope compared to other welding methods, preserving desirable material properties such as corrosion resistance and mechanical strength.
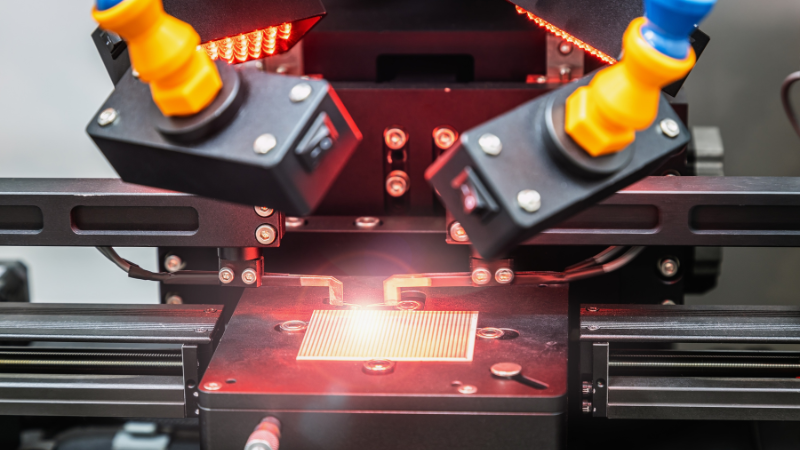
IV. Optimizing Weld Quality Through Metallurgical Understanding
Understanding the metallurgical aspects associated with laser welding is crucial for optimizing welding quality and performance. Factors like alloy composition, thermal conductivity, tensile strength requirements, and even heat treatment processes play vital roles in achieving desired results when working with different types of stainless steel. The microstructure and surface characteristics of the materials also contribute to the overall welding process.
For instance, austenitic stainless steels like 316L exhibit excellent weldability due to their low carbon content and high nickel content. The laser welding process helps maintain the desired austenitic stainless steel microstructure, ensuring optimal corrosion resistance and mechanical properties. Additionally, the liquid welding process helps prevent oxidation and ensures a strong bond.

Benefits of Laser Welding Stainless Steel
Laser welding stainless steel offers several significant benefits such as high weld strength and resistance to heat treatment, making it a preferred choice for various applications. Let’s explore these advantages in detail.
1. Excellent Weld Quality with Minimal Distortion
One of the key advantages of laser welding is its ability to provide excellent weld quality while minimizing distortion. This is primarily due to the concentrated heat source generated by the laser beam.
Unlike traditional welding methods, which often result in significant distortion and warping, laser welding allows for precise control over the heat input. As a result, the welded lap joints maintain their structural integrity and dimensional accuracy.
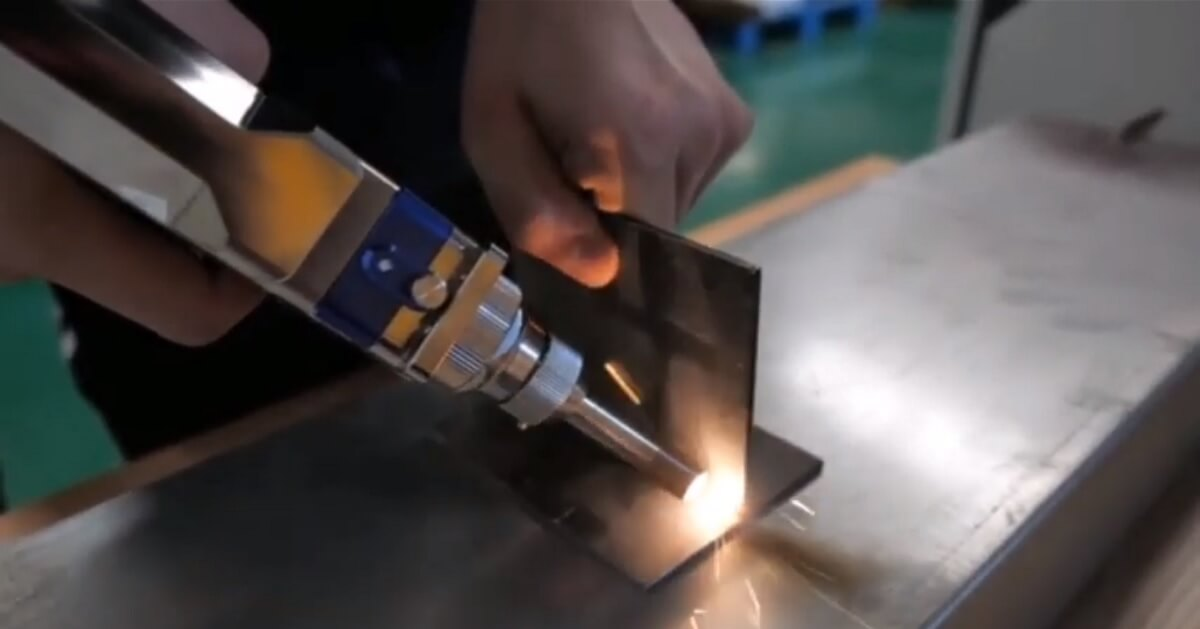
2. High Productivity with Fast Travel Speeds
Compared to traditional welding methods, laser welding enables faster welding speed, leading to higher productivity. The focused laser beam delivers high energy density of laser beam to the workpiece, allowing for rapid melting and solidification of the stainless steel material. This increased speed translates into reduced production time and improved efficiency.
Laser welding also reduces the risk of cracking in the stainless steel material, thanks to its ability to penetrate deeper into the medium compared to other welding methods. The use of 316L stainless steel is particularly beneficial when using laser welding due to its high resistance to cracking.
3. Superior Corrosion Resistance
Laser-welded joints exhibit superior corrosion resistance due to the reduced heat input during the fusion process. Traditional welding methods often introduce excessive heat, which can alter the chemical composition of stainless steel and compromise its corrosion-resistant properties.
In contrast, laser welding minimizes heat-affected zones (HAZ), preserving the material’s original characteristics and ensuring long-term durability.
4. Non-contact Nature Eliminates Physical Contact
Another advantage of laser welding is its non-contact nature, eliminating physical contact between the tooling and the metal surface.
Traditional welding processes involve direct contact between electrodes or filler materials and the metal being joined. Such contact can lead to contamination or damage to sensitive components. Laser welding eliminates this concern by utilizing a focused laser beam that melts and fuses metals without any physical interaction.
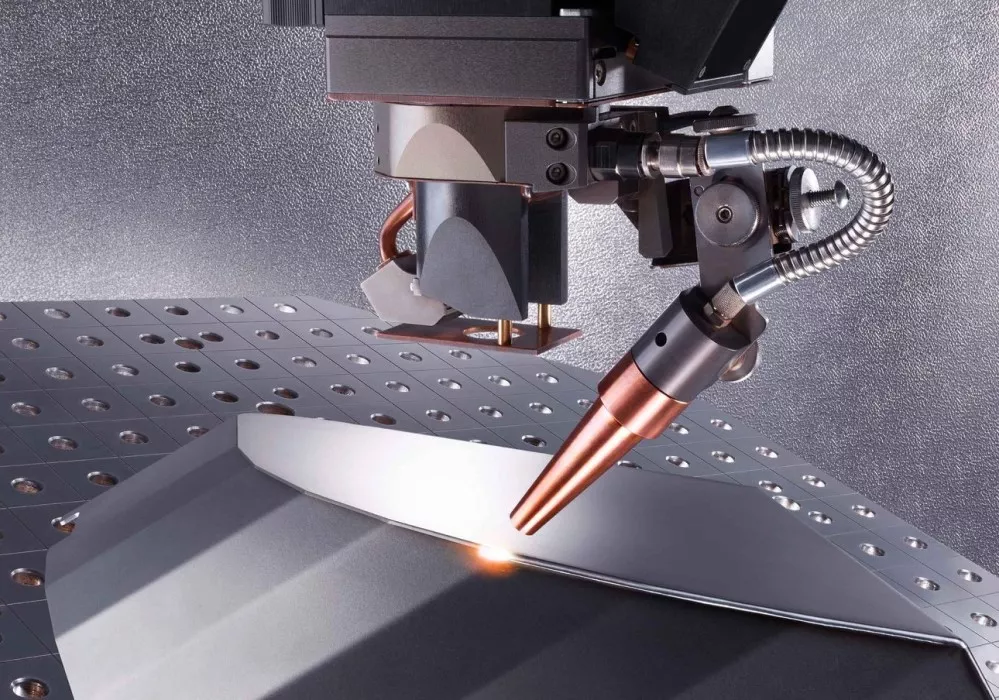
Factors to Consider When Selecting a High-powered Laser for Stainless Steel Welding
Several factors need to be considered when selecting a high-powered laser system. The right choice can significantly impact the quality and efficiency of the welding process. Let’s explore some key factors that should be taken into account.
1. Power Output
Laser power plays a crucial role in determining the effectiveness of stainless steel welding, especially when dealing with 316l stainless steel and duplex stainless steel. Higher laser power offers deeper penetration capabilities, allowing for the efficient joining of thick sections. However, it is important to note that thin materials may require additional precautions due to the increased energy density.
Therefore, while considering laser power output, one must carefully assess the base material thickness and select an appropriate laser power level for medium depth welds. Additionally, it is important to consider the microstructure of the stainless steel to ensure optimal welding results.
2. Beam Quality
The beam quality of a laser is another critical consideration when choosing a system for stainless steel welding. A well-focused beam with good spatial intensity distribution enhances welding precision and reduces defects such as porosity or undercutting. This ensures high-quality welds with excellent joint strength and aesthetics. Hence, it is essential to opt for a laser system that provides high beam quality.
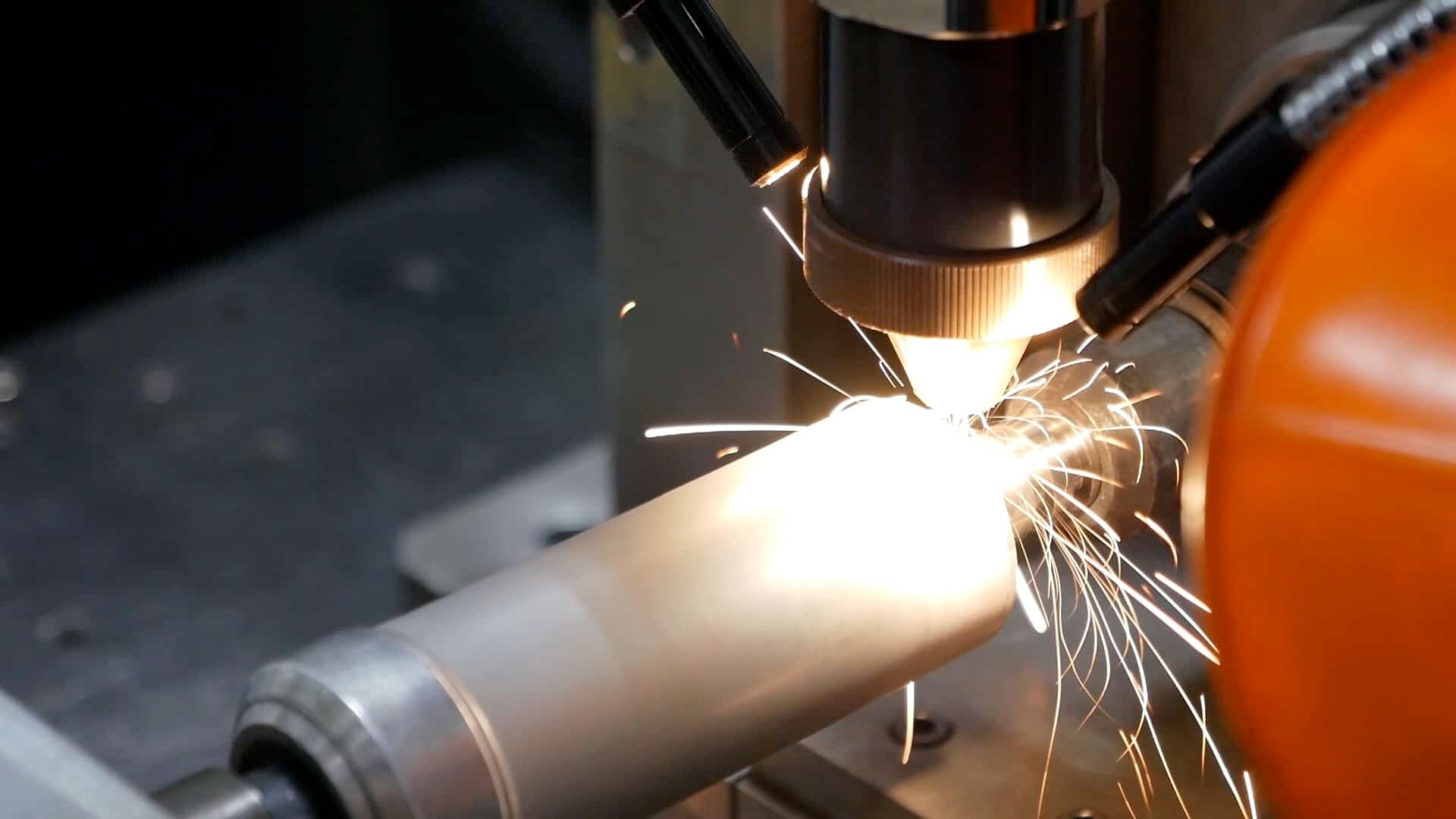
3. Pulse Duration
Pulse duration refers to the length of time during which energy is delivered by the laser source. It has a significant impact on the welding process’s outcome, depending on the thickness of the stainless steel being welded. Shorter pulses are suitable for thin materials as they minimize heat input and reduce potential distortion or burn-through issues.
On the other hand, longer pulses are effective for thicker sections since they allow better control over heat dissipation and fusion depth.

Tips for Right Settings in Laser Welding Stainless Steel
Finding the right settings is crucial for achieving high-quality welds. One of the first steps in the welding process is conducting initial trials to determine the optimal laser parameters for the specific stainless steel grades and joint configurations you are working with.
Each grade of stainless steel may require different settings due to variations in composition and metallurgical properties. Click here to see the relationship between parameters and welding results.
1. Focus Position
Adjusting the focus position can help control weld width and depth, ensuring proper fusion without excessive heat input.
The focal position plays a significant role in laser welding stainless steel. By adjusting it, you can control the weld geometry, width, and depth of the weld. A focused beam allows for precise energy concentration at a specific point, resulting in deep penetration. However, if the focus is too narrow or shallow, there may be insufficient fusion between the base materials.
On the other hand, if the focus is too wide or deep, excessive heat input can lead to distortions and defects in the welded joint. Fine-tuning the focal position enables you to strike a balance between penetration depth and thermal distortion.
2. Fulse Frequency and Power Levels
Fine-tune pulse frequency and power levels to balance penetration depth with minimal thermal distortion.
In addition to adjusting the focal position, fine-tuning the pulse frequency and power levels is crucial for achieving optimal results when laser welding stainless steel. The pulse frequency determines how often energy is delivered during laser beam welding. Higher frequencies provide rapid heating cycles that result in shallow welds suitable for thin materials or surface treatments.
Conversely, lower frequencies allow for deeper penetration into thicker welding materials but increase heat input. Balancing the pulse frequency and power levels ensures that the desired penetration depth is achieved without causing excessive thermal distortion. It is important to note that the specific pulse frequency and power levels may vary depending on the stainless steel grade, joint configuration, and other parameters.
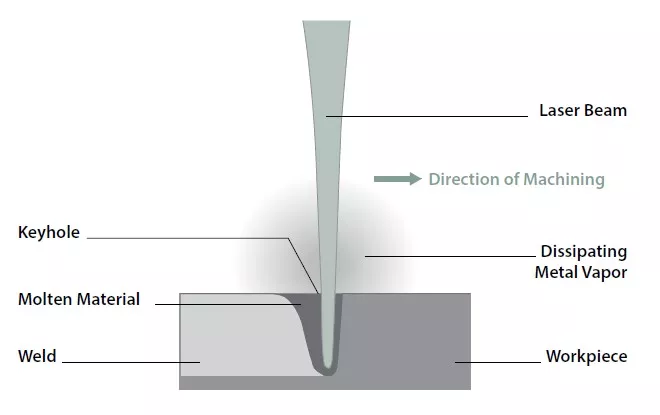
3. Assist Gas
Consider using assist gases like argon or helium to improve shielding effectiveness and prevent contamination.
To enhance the welding environment during laser welding of stainless steel, it is common practice to use shielding gases such as argon, carbon dioxide, or helium. These gases provide effective shielding, protecting the weld pool from atmospheric contamination, which could lead to defects in the final weld.
Argon is commonly used for non-reactive metals like stainless steel and mild steel due to its inert properties, while helium offers high thermal conductivity, making it suitable for high-power laser applications. The choice of shielding gas depends on factors such as material thickness, laser power, and desired weld quality.
FAQs
1. Can I use any type of stainless steel for laser welding?
While most types of stainless steel are suitable for laser welding, certain grades with high carbon content or low thermal conductivity may pose challenges. It is important to select the appropriate laser welding parameters and laser technology for each specific grade.
2. How does laser welding stainless steel compare to other welding methods?
Laser welding offers advantages such as precise control, minimal heat-affected zone, and faster processing times compared to traditional welding methods like TIG or MIG. However, the initial setup cost of laser welding equipment can be higher.
3. What are some common defects in laser-welded stainless steel?
Common defects include porosity, lack of fusion, excessive spatter, and weld cracking. These can be minimized by optimizing different laser parameters and ensuring high quality joints. This includes considering factors like penetration depth, SPE, and laser energy.
4. Can I weld dissimilar metals using laser welding?
Yes, laser welding can be used to join dissimilar metals including stainless steel with other materials like aluminum alloy, copper alloys, or titanium alloy. However, careful consideration must be given to material compatibility and the selection of appropriate filler materials.

Conclusion
In conclusion, laser welding stainless steel offers numerous benefits but also comes with its fair share of challenges and limitations. By understanding the science behind laser welding, you can enhance your proficiency in laser welding stainless steel and achieve high-quality results in your projects.
Baison – The Best Laser Welding Provider
If you need to weld various metals including stainless steel, Baison has the best manufacturing technology. Our laser welding machines provide better welding process stability and higher weld depth for welding. With Baison, the welder works to maintain a consistent weld molten pool.
We also provide fiber laser cutting machines and laser cleaning machines and other equipment, becoming an ideal partner for modern manufacturing. We have experts in the fields of sheet metal fabrication, machining, mechanical engineering, and machine tools for metals. Now you can contact us to find out and get a free sample proofing!