Understanding Arc Welding
Before diving into the specifics, let’s begin with a fundamental understanding of what arc welding is and how it operates.
Working Principles of Arc Welding
Arc welding is a widely used method of joining metals through the application of heat generated by an electric arc. This process involves striking an electric arc between an electrode and the base material, melting both to form a strong bond upon cooling.
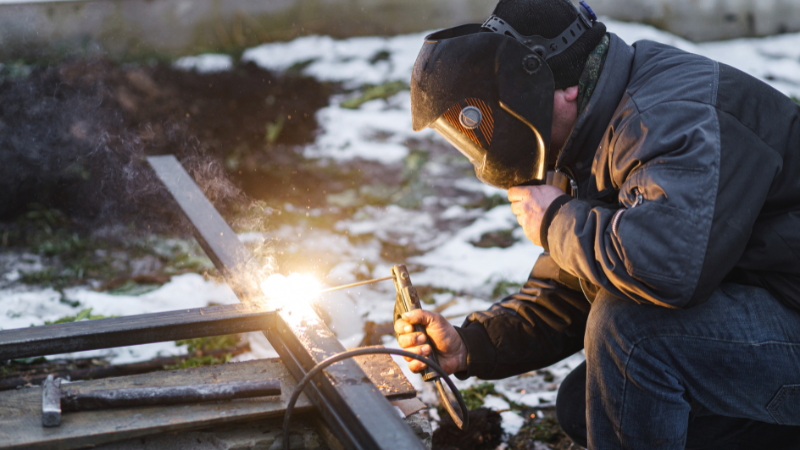
The electrode can either be consumable, providing filler material for the weld, or non-consumable. Inert or semi-inert gases are often used to shield the weld from atmospheric contamination, a process known as shielded metal arc welding (SMAW) or gas tungsten arc welding (GTAW) respectively. The adaptability of arc welding to various equipment and settings makes it a versatile choice in numerous industries.
Applications of Arc Welding
Arc welding is favored for its versatility and strength in various sectors, including:
- Construction: Used in building structures and bridges.
- Automotive: Essential for assembling vehicle frames and body parts.
- Industrial Repair and Fabrication: Ideal for repairing and creating metal equipment and pipelines.
- Shipbuilding: Widely used for constructing and repairing ships.
Its adaptability to different metals and alloys makes arc welding a preferred choice in many industrial applications.
Exploring Laser Welding
To fully appreciate the contrasts with arc welding, it is essential to delve into the realm of laser welding and its unique attributes.
Working Principles of Laser Welding
Laser welding uses a focused laser beam to join materials, offering a high level of precision. This method concentrates a laser on a small point, melting the material quickly to form a weld.
The laser welding process is a contactless process, reducing material distortion and enhancing accuracy. The process is fast and efficient, perfect for detailed welding tasks. Its main advantage lies in the ability to adjust the laser’s intensity and duration, allowing it to be used with a variety of materials and for intricate welding jobs.
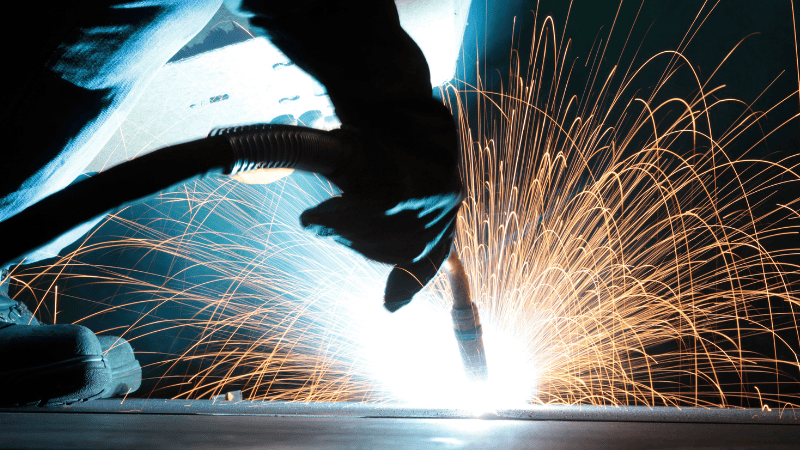
Applications of Laser Welding
Laser welding’s precision and versatility allow it to be employed in a variety of industries, some of which include:
- Electronics and Microfabrication: Ideal for joining small components in electronic devices and micro-assemblies.
- Automotive Industry: Used for high-precision welding of engine components and intricate automobile parts.
- Aerospace Industry: Crucial for fabricating and repairing critical aerospace components with high precision.
- Medical Equipment Manufacturing: Applied in the production of surgical tools and medical devices requiring exact welds.
The non-contact nature and precision of laser welding make it an indispensable tool in fields requiring detailed and precise welding work.

Advantages and Disadvantages of Arc Welding
In any comparison, understanding the strengths and limitations of each method is crucial. Let’s examine the advantages and disadvantages of arc welding.
Advantages of Arc Welding
Arc welding offers many advantages that benefit the industry:
- Cost-Effectiveness: Arc welding equipment is generally more affordable compared to other welding methods. This affordability extends to both the initial investment and the ongoing operating costs.
- Versatility: It can be used on a variety of metals and alloys, making it suitable for a wide range of applications in different industries.
- Portability: Arc welding equipment is often portable, allowing for welding tasks to be performed in various locations, including outdoors.
- Robust Welds: Arc welding is known for producing strong and durable welds, which is particularly important in heavy-duty applications like construction and shipbuilding.
Disadvantages of Arc Welding
Of course, there will inevitably be some shortcomings:
- Skill Requirement: It requires a significant level of skill and experience to achieve high-quality welds, which can be a barrier for beginners.
- Safety Concerns: The process generates intense heat, sparks, and UV radiation, posing safety risks that require strict protective measures.
- Limited Precision: Compared to methods like laser welding, arc welding is less precise, making it less suitable for applications requiring high accuracy.
- Environmental Impact: Arc welding can produce fumes and gases that may be harmful if not properly ventilated, raising concerns about its environmental and health impacts.
Advantages and Disadvantages of Laser Welding
To provide a balanced perspective, it’s essential to explore the pros and cons of laser welding, a technology known for its precision and advanced capabilities.
Advantages of Laser Welding
Laser welding is a popular technology that excels in many ways, including speed and accuracy.
- High Precision: Laser welding offers superior precision, especially beneficial for delicate and intricate welding tasks.
- Speed: The process is typically faster than traditional welding methods, increasing productivity.
- Low Heat Input: Laser welding minimizes the heat affected zone, reducing material distortion and allowing for the welding of heat-sensitive components.
- Versatility: It can be used on a wide range of materials, including metals, plastics, and composites.
- Automated Operations: Laser welding can be easily automated, enhancing consistency and reducing labor costs.
Disadvantages of Laser Welding
There are some drawbacks to laser welding that need to be understood clearly.
- High Initial Cost: The equipment for laser welding is generally more expensive than traditional welding setups.
- Technical Expertise Required: Operating and maintaining laser welding equipment requires specialized knowledge and training.
- Limited Thickness Range: It is less effective on very thick materials compared to methods like arc welding.
- Safety Concerns: The intense laser beam can be hazardous, requiring strict safety protocols and specialized equipment.
- Limited Joint Accessibility: Due to the nature of the laser beam, welding certain joint configurations can be challenging.

Arc Welding vs. Laser Welding: Key Difference
Understanding the distinct characteristics of arc and laser welding is crucial for making informed decisions about their application. Let’s delve into their key differences.
Aspect | Arc Welding | Laser Welding |
Technique | Electrical arc melting | Laser beam melting |
Precision | Less precise | Highly precise |
Cost | Lower cost | Higher cost |
Speed | Slower | Faster |
Material Thickness | Thicker materials | Thinner materials |
Safety | More safety risks. | Less fumes, laser safety. |
Applications | Heavy industries, construction. | High-tech, delicate tasks. |
1. Precision and Control
Arc Welding typically offers less control over the weld bead and is generally less precise, which can be a limitation for tasks requiring fine detail or precision. On the other hand, Laser Welding provides high precision with controlled heat input. This makes it especially suitable for delicate tasks where precision is crucial, such as in electronics or medical equipment manufacturing.
2. Material Thickness
Arc Welding is more effective for thicker materials, making it a common choice in heavy industrial applications like construction and shipbuilding. Laser Welding, however, is better suited for thinner materials and applications requiring precise, fine welds. Its precision makes it ideal for industries like aerospace and electronics, where the thickness and delicacy of materials are major considerations.
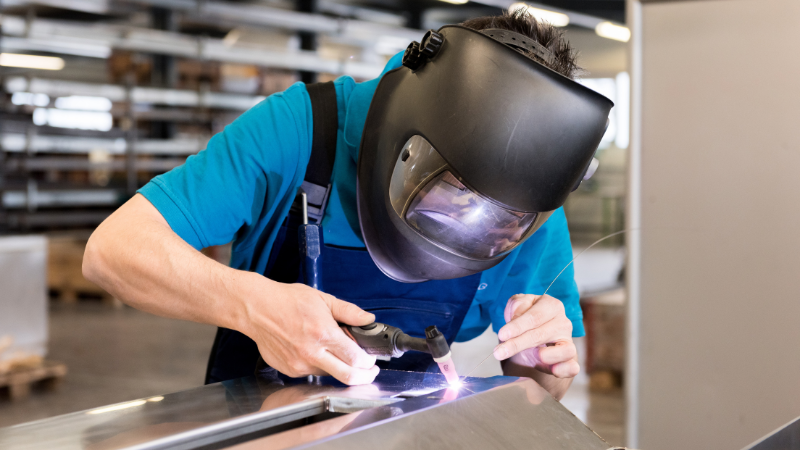
3. Equipment and Setup Costs
The cost difference between arc welding and laser welding equipment is notable. Arc welding setups are more affordable, professional-grade arc welding systems can range from $1,000 to $5,000, depending on the specifications and capabilities required.
On the other hand, laser welding systems, due to their advanced technology, start at around $10,000 and can go beyond $100,000 for industrial-grade equipment. This significant cost disparity is a key factor in deciding which method to use, as laser welding’s higher precision comes with a much greater initial investment.
Choosing the Right Method for Your Needs
When deciding between arc welding and laser welding, it’s important to consider a range of factors beyond just the basic differences between the two methods.
1. Project Complexity
Assess the complexity of the welding project. Arc welding is typically more suited for straightforward, robust welding tasks, especially in construction or heavy industry. Laser welding, with its high precision, is ideal for complex, intricate designs, or where detailed work is required, such as in electronics or medical device manufacturing.
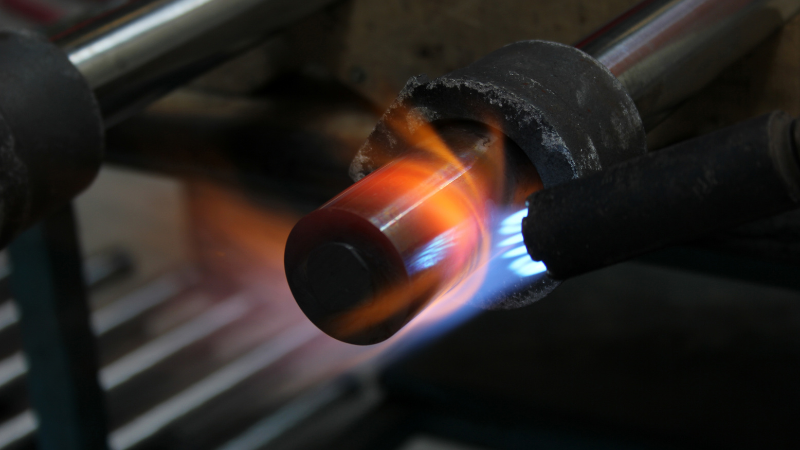
2. Future Scalability
Consider the scalability of your welding needs. If your project or production line is likely to scale up, laser welding, with its potential for automation and consistency in high-volume applications, might be more beneficial. Arc welding is more adaptable for small-scale, custom, or one-off projects.
3. End-Product Quality and Specifications
Reflect on the quality and specifications required for the final product. For projects requiring high-strength, durable welds, such as in structural applications, arc welding is often sufficient. However, for products where aesthetics or minimal distortion is important, like in consumer electronics, laser welding might be more appropriate.
By considering these aspects, you can choose a welding method that not only fits your immediate project requirements but also aligns with your long-term operational goals, workforce capabilities, and budget constraints.

FAQs
1. Can Arc and Laser Welding Be Used Together?
Yes, in some advanced applications, arc and laser welding can be combined to leverage the advantages of both. This hybrid approach can enhance welding speed, precision, and strength, particularly in complex manufacturing scenarios. However, it requires careful planning and specialized equipment.
2. Can Both Arc Welding and Laser Welding Be Used on All Types of Metals?
Arc welding is versatile for various metals and ideal for thicker materials. Laser welding suits thinner metals and offers precision, but each method has material limitations.
3. How Do I Determine the Cost-Effectiveness of Arc Welding vs. Laser Welding for My Project?
Consider equipment costs, operational expenses, and project scale. Arc welding is more affordable upfront, and suitable for small projects. Laser welding, while costlier initially, is efficient for large, precision tasks.
Conclusion
In summary, both arc welding and laser welding have unique strengths and applications. Arc welding is cost-effective and versatile for heavy-duty tasks, while laser welding offers precision and speed for high-tech projects.
The choice between them depends on factors like budget, material type, and project complexity. Sometimes, combining both methods can be beneficial. The key is to align the welding method with your specific project needs and resources, ensuring optimal quality and efficiency.
Elevate Your Welding with Baison Laser!
Looking to take your welding projects to the next level? Explore the cutting-edge solutions offered by Baison Laser. With our expertise and innovative technology, we’re here to assist you in choosing and implementing the ideal welding method for your unique requirements. Contact Baison Laser today, and let’s create something extraordinary together!