Titanium, renowned for its strength and aerospace applications, presents unique challenges when it comes to joining. Laser welding has successfully been able to wield high-precision beams to create robust, aesthetically pleasing welds.
In this article, we are going to delve deep into how to go forward with laser welding titanium, what the challenges are, and how to deal with any pre- and post-welding issues when working with this type of special metal. This guide delves into the intricacies of laser welding titanium.
The Challenges of Welding Titanium
Welding titanium requires a delicate dance between its incredible properties and its inherent vulnerabilities.
Laser welding techniques can vary with the type of welding you want to proceed with. There are quite a number of different types, such as electron beam welding, gas tungsten arc welding, laser beam welding, etc. Whatever the type may be, there are some challenges in welding titanium.
1. Oxygen Embrittlement
At high temperatures, titanium develops a tenacious oxide layer due to its great affinity for oxygen. This layer contaminates the weld pool, hindering fusion and resulting in weak, brittle connections. This problem can be solved during the laser welding process by shielding the weld zone with inert gases like argon or helium.
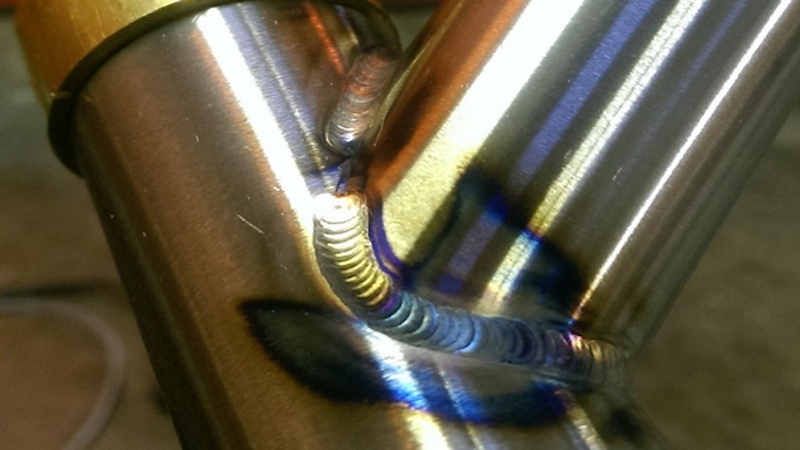
2. Distortion and Warpage
Welding heat can cause thin titanium sheets to bend and distort significantly. This degrades the product’s ultimate functioning in addition to its appearance. This problem can be reduced with careful clamping methods and low laser welding heat input.
3. High Thermal Conductivity
Titanium efficiently conducts heat which makes it difficult to achieve the deep penetration needed for strong welds. Traditional welding methods often struggle to overcome this challenge which results in shallow welds prone to failure.
Laser welding, with its concentrated and powerful laser beam, excels at overcoming this challenge. This process can create deep and narrow welds with minimal heat-affected zones.
4. Cost Considerations
Laser welding systems require a higher initial investment compared to traditional methods. However, their precision, speed, and minimal post-weld finishing often offset the cost in the long run, especially for high-volume production.
Ready to Get Your Own Laser Machines?
Boost your operations with Baison Laser's advanced, customized technology!
Basics of Laser Welding
Modern technology, such as laser welding, allows for accurate and effective material joining. High-powered laser beams are used in laser welding to melt and fuse materials through deep fusion. Metal vapor is produced during the process by using lasers, and the vapor melts and fuses the materials.
When the laser beam is directed toward the joint, it produces a strong bond between the materials by melting them with extreme heat. The high accuracy of this method enables exact control over the width and depth of the weld. Laser welding is also used for welding stainless steel and gas metal arc welding.
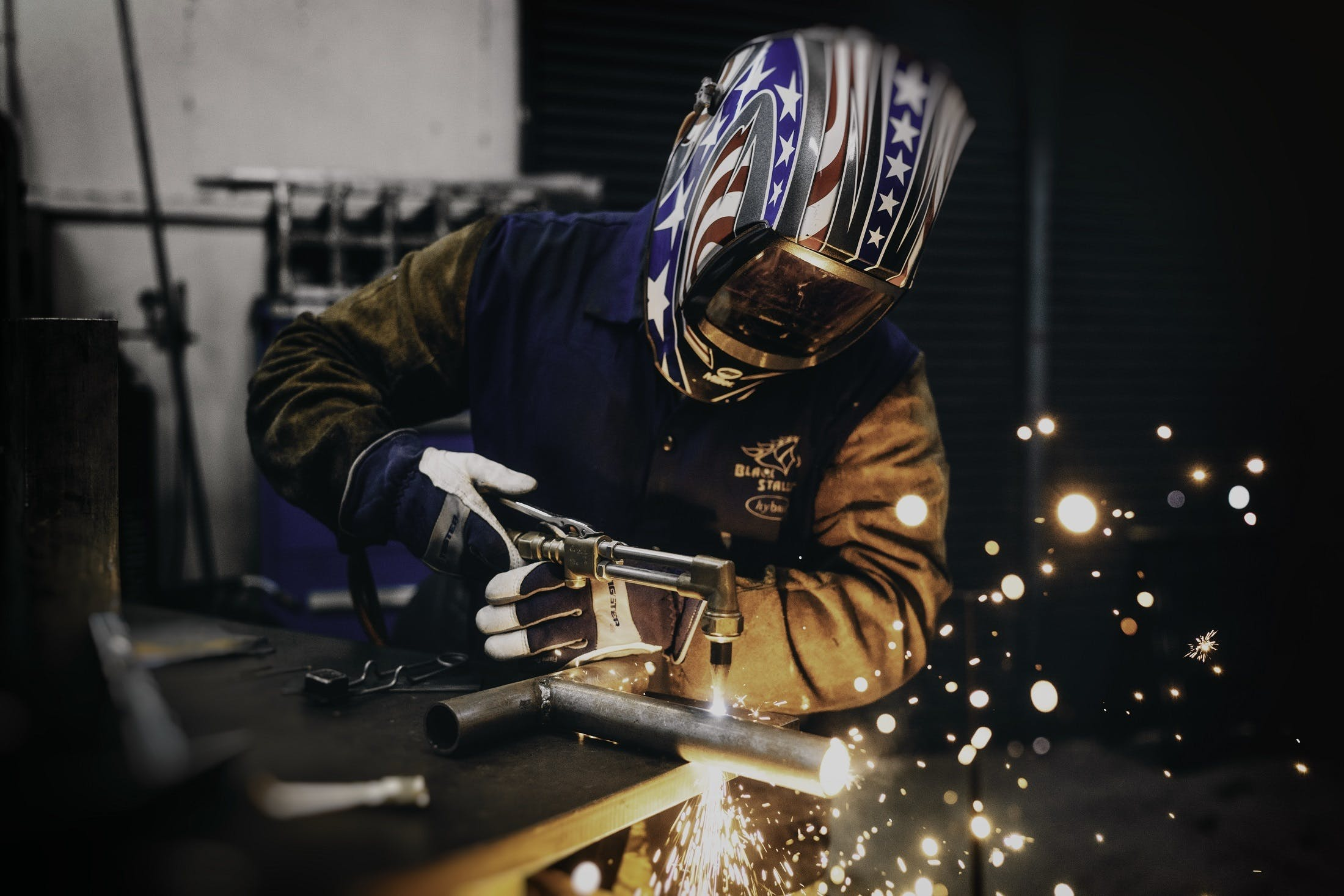
How Laser Welding Works?
The term laser welding has become so commonly known that almost everyone who has even the slightest relation to construction, metals, or engravings knows about laser welding. But the more in-depth details are sometimes lost to them. Laser welding is a combination of multiple elements that come together to create something great!
- Energy Source: A powerful laser generator, like a fiber laser or CO2 laser, produces a concentrated beam of light.
- Melting and Fusion: The intense heat of the focused beam melts the metal at the joint, creating a molten pool.
- Shielding Gas: An inert gas, like argon or helium, surrounds the weld zone to prevent contamination from oxygen and other atmospheric gases.
- Solidification: As the beam moves along the joint, the molten metal cools and solidifies, forming a strong and permanent weld.
- Beam Focusing: Lenses and mirrors precisely focus the beam onto the joint line between the two metal pieces.
Benefits of Laser Welding Titanium
Titanium possesses exceptional strength, lightweight, and corrosion resistance. There are many benefits of using laser welding titanium. Some of the major advantages are given as follows.
The welding processes and the needed outputs vary depending on the material and uses. But welding titanium has quite a lot of advantages. As titanium has a natural passivity created by a layer of oxides, it has superior corrosion resistance. Other benefits come with this as well.
1. Strength and Precision
Laser welding creates deep, narrow welds with minimal heat-affected zones. This translates to superior strength and fatigue resistance, which is important for applications like aircraft structures and medical implants.
Unlike traditional methods, the concentrated heat minimizes distortion and warpage, allowing for the precise joining of thin sections and intricate geometries.
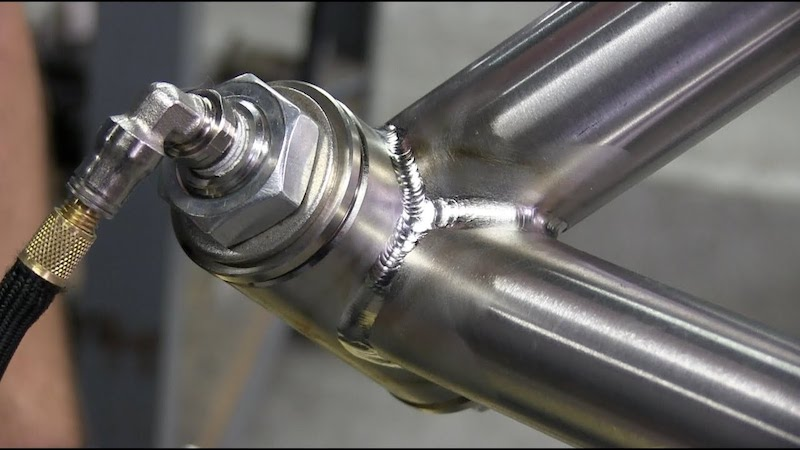
2. Minimal Heat, Minimal Problems
Titanium’s affinity for oxygen raises its vulnerability to embrittlement during welding. Laser welding’s targeted heat input and protective inert gas shields minimize oxidation, eliminating this major hurdle and ensuring high-quality, clean welds. Additionally, the minimal heat input prevents grain growth, preserving the inherent strength of the titanium alloy.
3. Speed and Efficiency
Compared to traditional techniques, laser welding boasts significantly faster welding speeds. This translates to increased production efficiency and reduced costs, especially for high-volume applications. The automated nature of laser systems further enhances efficiency and ensures consistent weld quality.
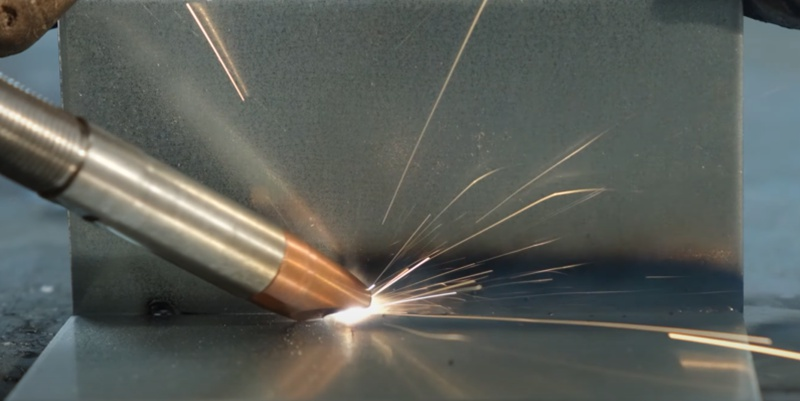
4. Versatility and Customization
Laser welding readily adapts to various joint types and thicknesses, which makes it ideal for diverse applications. Whether lap joints or intricate tube assemblies, laser welding handles them with finesse. Additionally, laser parameters can be fine-tuned to achieve specific weld properties, tailoring the process to precise needs.
5. Sustainability and Aesthetics
Laser welding’s minimal heat input and reduced material consumption contribute to environmentally friendly manufacturing practices. The narrow and clean welds require minimal post-processing.
Thus, it contributes to a sleek and aesthetically pleasing final product. Its ability to overcome the wonder metal’s welding challenges while reaping numerous benefits makes it the go-to technique for pushing the boundaries of engineering and design.
Ready to Get Your Own Laser Machines?
Boost your operations with Baison Laser's advanced, customized technology!
Preparing for Laser Welding Titanium
Titanium alloys and other types of specialized metals require an extra layer of preparation. First, the metal parts need to be prepared so that the welding can be done perfectly. For that, there are a few steps that are followed:
Step 1: Joint Design
Optimize joint geometry for laser accessibility and weld strength. A good joint design can ensure better durability on the finished project, as well as make the welding process easier.
Step 2: Cleaning and Degreasing
Remove contaminants to ensure proper fusion and prevent gas reactions. Even though the surface looks clean, it is better to clean and degrease it again before going into welding. This step is true for other metals as well. Use a stainless steel wire brush to clean the metal surface.
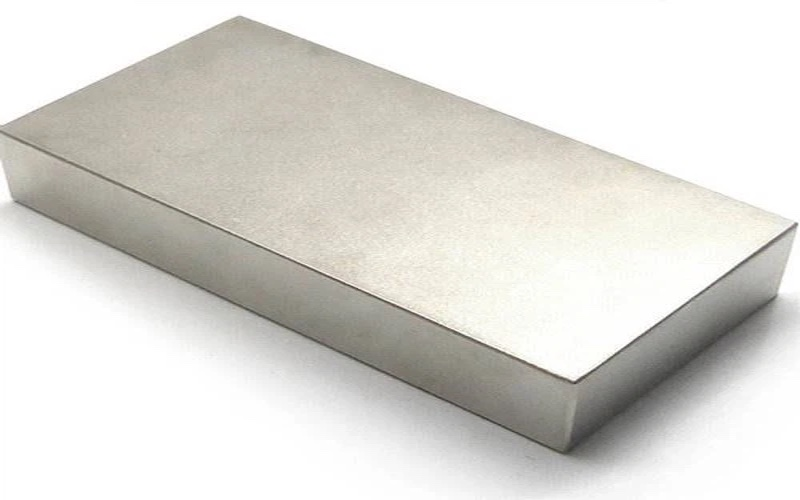
Step 3: Shielding Gas
Select the appropriate inert gas (argon or helium) to protect the weld zone. The weld power and temperature both need to be in control for the perfect thermal conductivity and reduced heat-affected zone.
Welding Process Parameters
There are a few things that need to be made sure before embarking on the welding process. To get the best results out of the finished product, some parameters need to be properly maintained, such as power, heat, pulse frequency, etc.
1. Power
Power plays a huge role in getting the required precision in laser welding. Too much power in delicate work can damage the material as well as the output. Determine the optimal laser power based on material thickness and desired penetration depth.
2. Pulse Frequency
Similar to power, pulse duration can make sure that the elements can come together seamlessly to get the job done. Control heat input and weld characteristics by adjusting the laser pulse characteristics.
3. Speed
Especially when it comes to titanium engraving and generalized optimization of travel speed for desired weld depth and bead formation. Accurate laser welds happen when the speed of the laser perfectly balances with the power and pulse rate.
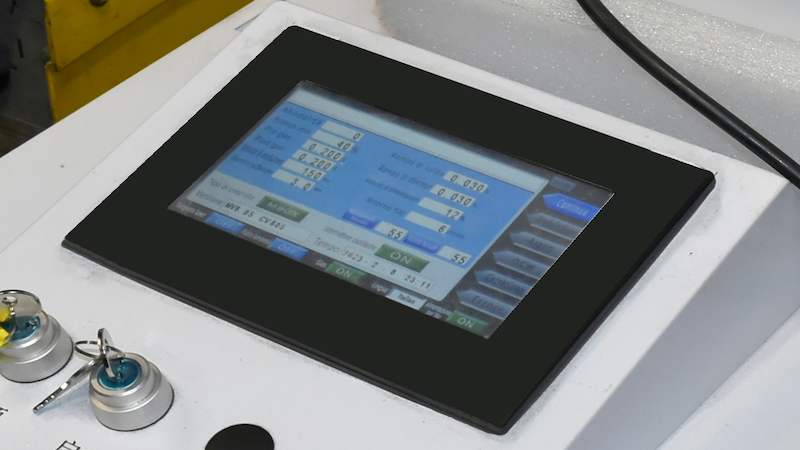
Post-Welding Practices
Being done with the main welding process does not mean that the whole process is completed. Before finishing the procedures, there are some post-welding practices and checks that need to be carried out. When it comes to titanium welding, this special-grade metal requires even more of such attention.
1. Inspection and Testing
Visual inspection followed by non-destructive testing methods like radiography or ultrasonic testing ensures weld integrity. A thorough check is needed to find any discrepancies.
2. Post-Weld Treatments
Some applications may require post-weld treatments like stress relieving or pickling to optimize properties. Whatever is needed, the process amplifies the quality, durability, and aesthetics of the welded joint of the titanium beam.
3. Equipment Maintenance
If there are any issues with the machine or any part of the equipment, the procedures will be hampered. Proper maintenance of the laser system guarantees consistent performance and weld quality.
Ready to Get Your Own Laser Machines?
Boost your operations with Baison Laser's advanced, customized technology!
Applications of Laser Welding Titanium
From medical implants and aerospace components to high-end bicycles and architectural frames, laser welding titanium unlocks a vast array of possibilities for this versatile metal. Laser welding plays a crucial role in crafting lightweight yet incredibly strong components.
1. Aircraft
From jet engine pods to landing gear, every weld must withstand extreme temperatures, pressures, and vibrations. The narrow heat-affected zones and minimal distortion of laser welding ensure structural integrity and fuel efficiency, propelling aircraft further and faster.
2. Medical Implants and Tissue Replacements
When it comes to replacing or repairing the human body, nothing takes center stage like biocompatible titanium. Laser welding allows for the creation of custom medical implants, like hip replacements and dental implants, with exceptional precision and minimal heat, minimizing tissue damage and ensuring long-term functionality.
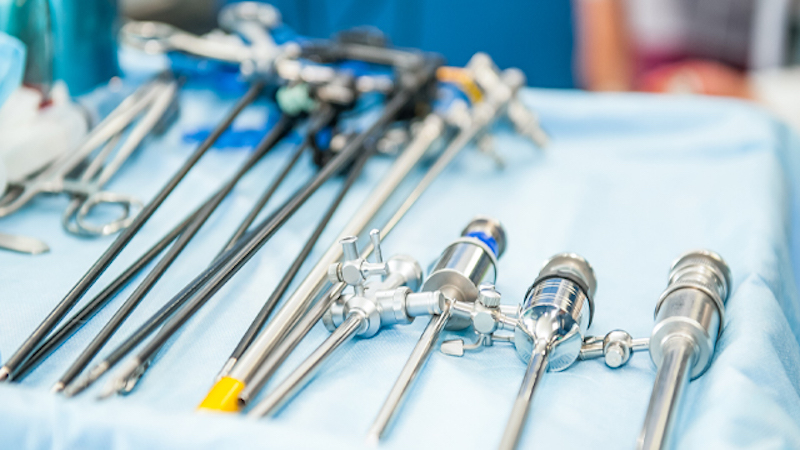
3. Chemical Processing
When dealing with aggressive chemicals, titanium’s resistance to corrosion shines. Laser welding enables the fabrication of tanks, pipes, and reactors from this robust metal, ensuring the safe and efficient handling of even the most potent chemicals.
4. Marine Engineering
Diving into the depths, laser welding helps titanium conquer the corrosive nature of the marine environment. From oil rigs and submarines to desalination plants, titanium components welded with laser precision resist corrosion and maintain structural integrity, ensuring safety and longevity in even the harshest underwater environments.
5. Automotive Industry
Speeding towards the future, laser welding titanium helps automobiles shed weight and gain strength. From high-performance race car chassis to lightweight brake systems, laser-welded titanium components contribute to enhanced fuel efficiency, improved handling, and increased safety.
6. Architectural Design
Reaching for the sky, laser welding titanium allows architects to create awe-inspiring structures. From intricate building facades and lightweight bridges to self-supporting sculptures and artistic installations, titanium, shaped by the precision of laser beams, adds a touch of both strength and elegance to the urban landscape.
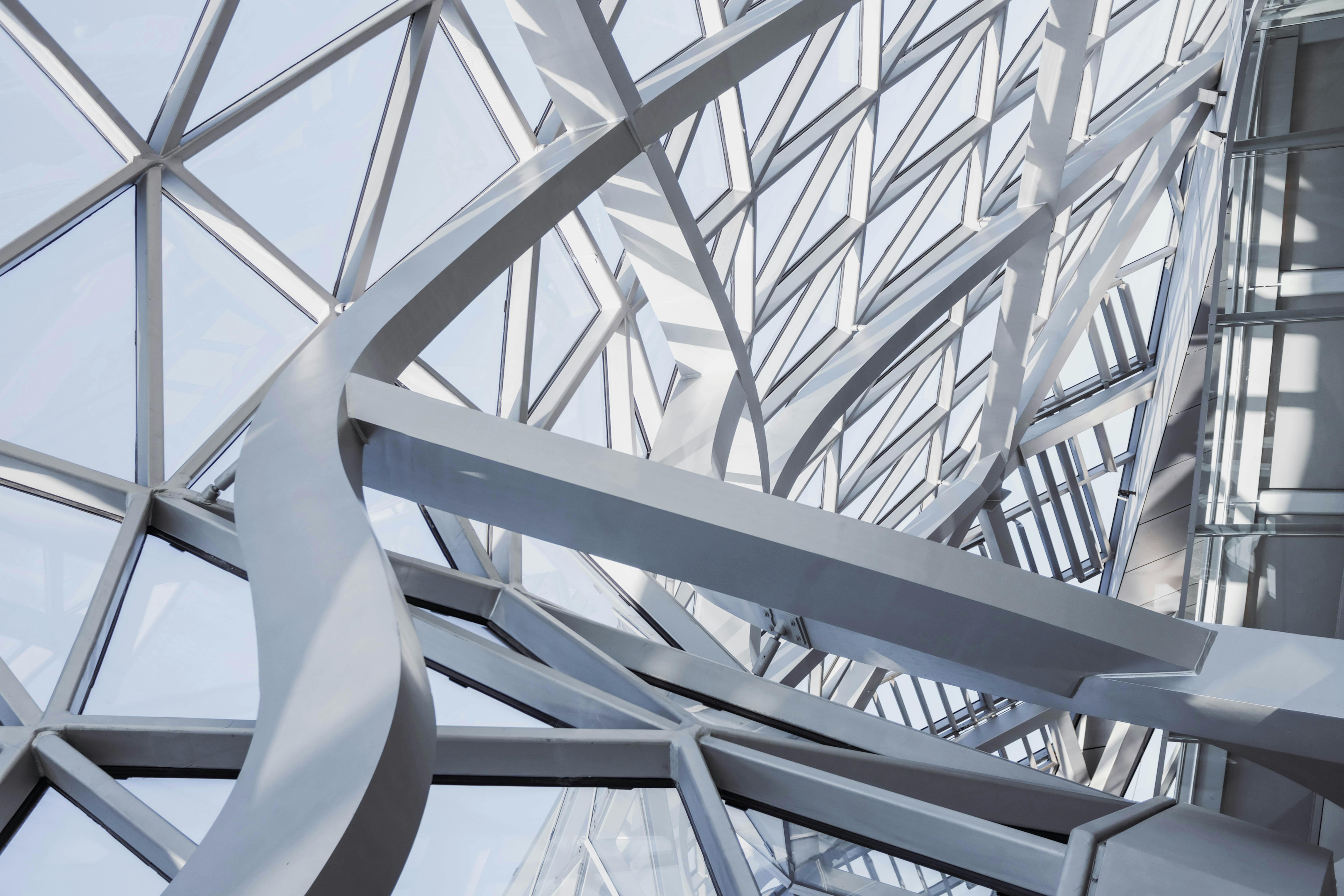
7. Sporting Goods
For athletes seeking the ultimate edge, laser-welded titanium equipment provides a winning combination of strength and lightness. From golf clubs and bicycle frames to baseball bats and ski poles, titanium, tamed by laser welding, elevates performance and pushes the boundaries of possibility.
FAQs
1. Can titanium be welded and joined with other materials?
Welding titanium with other metals is difficult because the joining point can become brittle and weak. But if you must fuse titanium with another metal, it is better to use different titanium alloys. As the structure is similar in these metals, the joining is stronger.
2. Do I need to have special licenses to start a business welding titanium?
This mainly depends on your location and what the laws and terms are there. In most cases, a general business license is required in most places. Depending on your line of work, which industry you work in, and the complexity of the job, there might be some added regulations in place.
Ready to Get Your Own Laser Machines?
Boost your operations with Baison Laser's advanced, customized technology!
Conclusion
Laser welding titanium represents a leap forward in joining technologies. Because of the higher barrier to entry, adding titanium welding to your business roster will certainly give you a new edge. Titanium and titanium alloys are still very lucrative in a lot of industries, and as a business, now is the time to grab the opportunities and work ahead towards the future.
Learn Everything You Need to Start a Successful Business Welding Titanium!
At Baison, we always try to solve any issues you might have. Please bring all your problems and inquiries to us, and contact us now! If you are starting a new business in welding, all types of knowledge are available at Baison to help you become successful as soon as possible.