The shipbuilding industry is a relatively conservative one. However, in the current global situation of moving into the era of Industry 4.0, the technology required by the industry has advanced by leaps and bounds. Utilizing these new technologies can lead to increased processing speed and quality.
This post delves into a comprehensive comparison between laser and plasma cutting, while also recommending laser equipment tailored for the shipbuilding sector.
Processing Situation of the Shipbuilding Industry
In the ever-evolving landscape of the shipbuilding industry, a surge in demand for more efficient fabrication methods and advanced equipment is evident. This growth, fueled by continuous technological advancements, has led to significant improvements in shipbuilding materials and construction techniques.
Traditionally, the industry, predominantly reliant on steel plates, has extensively utilized plasma cutting. However, Amidst this progress, advanced laser cutting technology stands out for its remarkable efficiency, precision, and environmental sustainability, marking a pivotal shift in manufacturing processes. According to SCNafrica, laser cutting equipment becomes the best partner for shipbuilders and improves supply chain efficiency.
Highlighting this trend, a report from RESEARCH AND MARKETS projects the Laser Cutting Machines Market to reach a value of USD 7.29 Billion by 2023, growing at a CAGR of 4.89% and further expanding to USD 10.22 Billion by 2030. This growth trajectory underscores laser cutting’s potential to revolutionize sheet metal fabrication in the entire maritime industry, positioning it as a trend not to be overlooked.
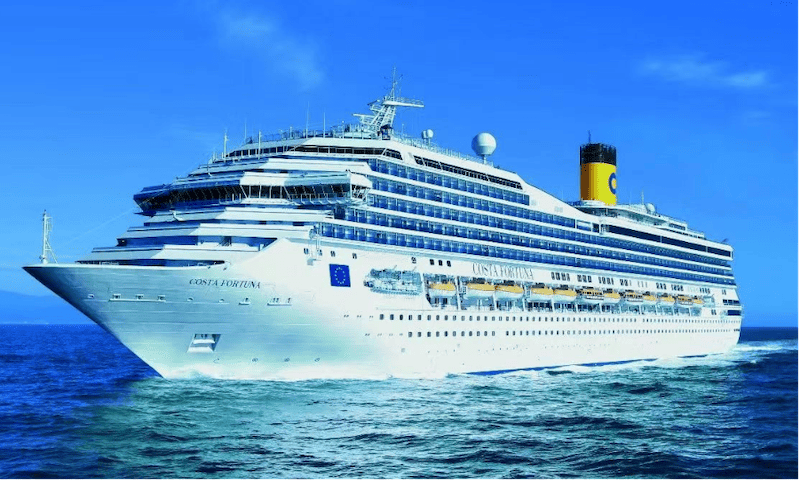
Difficulties in Shipbuilding Cutting
Understanding the pain points of cutting in the shipbuilding industry will be conducive to the follow-up work.
- Material Thickness and Hardness: Ship components often involve thick and hard materials, which can be challenging to cut through efficiently and accurately. This requires powerful cutting tools and techniques that can handle such demanding conditions.
- Precision and Accuracy: High precision is crucial in shipbuilding, as inaccuracies in cutting can lead to misalignments, affecting the overall structural integrity and safety of the vessel. Ensuring precision in cutting large and complex parts is a significant challenge.
- Environmental Impact: Traditional cutting methods often produce harmful emissions and waste materials, impacting the environment. The industry faces the challenge of adopting more environmentally friendly processes while maintaining efficiency and quality.
- Scale of Production: The sheer size of ship components makes cutting a challenging task. Handling and maneuvering large steel plates or sections for cutting requires specialized equipment and ample workspace.
- Cost and Efficiency: Shipbuilding is a cost-intensive industry, and the cutting process contributes significantly to these costs. Balancing the efficiency of the cutting process with the cost of materials, labor, and equipment is a constant challenge.
- Thermal Distortion: Techniques that use high heat, like plasma cutting, can cause thermal distortion in the metal, which can affect the shape and fit of the cut piece.
- Maintenance of Equipment: Cutting equipment in shipbuilding undergoes significant wear and tear due to the heavy-duty nature of the work. Regular maintenance and occasional replacement of parts are necessary, which can be costly and time-consuming.
Shipbuilding is a highly specialized industry, and the right cutting tools are critical to ensuring the success of the shipbuilding process. These tools are designed to address the unique challenges faced by the shipbuilding industry, including the need to accurately machine large components and engine parts. Learn more about the laser system for the specific needs of the shipbuilding industry below.

Overview of Laser Cutting
Laser cutting is a sophisticated technology that employs a high-powered laser beam to precisely cut or engrave materials. This process stands out for its precision, versatility, and efficiency, making it a preferred method in various industries.
Working Principle
Laser cutting involves directing a high-powered laser beam from laser photonics(usually generated by a CO2 or fiber laser), usually through optics, onto the material to be cut. This laser beam is finely focused on a small spot, allowing for high precision. The intense heat and energy of the laser cause the material to melt, burn, vaporize, or be blown away by a jet of gas, leaving a high-quality surface finish on the cut edge.
The laser cutting process is controlled by Computer Numerical Control (CNC) technology, which precisely guides the laser beam along the desired cutting path. This automated and precise control is crucial for creating intricate patterns and shapes, especially in complex industries like shipbuilding or manufacturing. The combination of high-powered lasers and advanced motion control technology makes laser cutting a highly efficient and versatile tool for cutting a variety of materials.
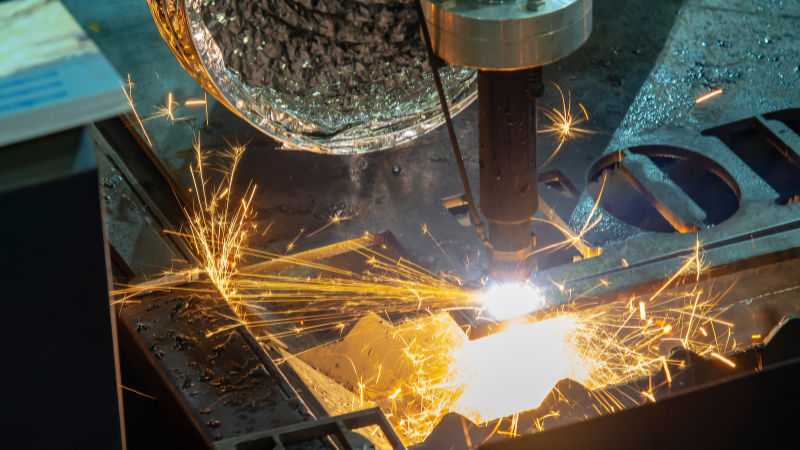
Applicable Materials
In the shipbuilding industry, laser cutting is particularly suited for processing a variety of materials, each chosen for their specific properties and roles in ship construction. The most common materials suitable for laser cutting in shipbuilding include:
- Steel and Steel Alloys: Steel is the backbone of most ships due to its strength and durability. Laser cutting is highly effective for cutting steel plates and sections of various thicknesses used in the hull and superstructure of ships. High-strength steel alloys, which provide greater resistance to corrosion and wear, are also well-suited for laser cutting.
- Stainless Steel: Known for its corrosion resistance, stainless steel is often used in parts of a ship that are exposed to harsh marine environments. Laser cutting can precisely cut stainless steel for use in ship fittings, railings, and other components.
- Aluminum and Aluminum Alloys: Aluminum is valued in shipbuilding for its lightweight and corrosion resistance, making it ideal for high-speed vessels and certain structural elements. Laser cutting can handle various aluminum alloys used in shipbuilding with precision and speed.
- Composite Materials: Modern shipbuilding increasingly uses composite materials for their strength-to-weight ratio and resistance to corrosion. Laser cutting can be used to shape composite panels and parts used in various sections of a ship.
- Titanium: Although less common due to its cost, titanium may be used in specific applications such as propellers and exhaust systems due to its high strength, lightweightness, and exceptional resistance to saltwater corrosion. Laser cutting is capable of handling titanium’s demanding cutting requirements.
- Brass and Copper: These materials are often used for decorative elements, electrical components, and in some cases, hull cladding. Laser cutting allows for intricate designs and precise cuts in these materials.
Each of these materials presents unique challenges in terms of cutting, such as varying levels of reflectivity, thermal conductivity, and thickness. Laser cutting technology, especially advanced fiber lasers, can efficiently and precisely cut these materials, making it a vital tool in modern shipbuilding processes.
Advantages Over Traditional Processing Methods
Laser processing technology shows incomparable advantages in the shipbuilding industry. Below we compare it with traditional processing methods, especially plasma cutting and flame cutting, which are most commonly used in the shipbuilding industry, to make clear the benefits of laser cutting.
1. Cutting Efficiency Comparison
Laser Cutting: Fast cutting speed, high precision. For thin and medium-thick plates, piercing takes 0.1-0.3 seconds. When cutting thin plates, speeds can reach up to 40m/min with an acceleration over 1G.
Plasma Cutting: Speeds below 5m/min, with about 0.3G acceleration. Piercing is measured in seconds. For the same cutting speed, if the cutting pattern is complex, the efficiency reflected by acceleration is more than twice as poor.
Material | Thickness (mm) | 12KW laser | 20KW laser | 300A plasma |
Stainless steel | 12 | 4.0-5.5 | 6.0-8.5 | 3 |
14 | 3.0-5.0 | 5.0-7.0 | 2.67 | |
20 | 1.0-1.6 | 1.5-3.2 | 1.93 | |
25 | 0.5-0.8 | 1.5-2.0 | 1.43 | |
30 | 0.3-0.6 | 1.0-1.5 | 1.08 | |
40 | 0.3-0.5 | 0.3-0.6 | 0.45 | |
50 | 0.1-0.2 | 0.2-0.5 | 0.26 | |
Carbon steel | 12 | 3-5(air) | 6-8(air) | 3.94 |
14 | 2.5-4(air) | 5-6.5(air) | 3.44 | |
20 | 1.2-1.5(O2) | 2.2-2.8(air) | -2.5 | |
25 | 0.5-1.6(O2) | 1.0-1.6(O2) | 1.9 | |
30 | 0.3-0.7(O2) | 0.8-2.0(O2) | 1.5 |
2. Cutting Quality Comparison
Laser Cutting:
- The laser cutting slit is small (at about 0.5mm), and the cut surface can be used directly for cutting and welding without grinding.
- Minimal cutting deformation, low surface roughness, and small taper. For instance, high-power laser cutting machines have narrow cut widths (generally 0.1-0.2mm), high precision (0.05-0.1mm), good surface roughness, and kerfs ready for welding without further processing.
- High precision in cutting, with positioning accuracy reaching 0.05mm and repeat positioning accuracy up to 0.02mm.
- Due to high laser energy density and fast piercing cutting speed, the thermal effect is minimal.
Plasma Cutting:
- Plasma cutting has wider kerfs than laser cutting, about 2mm larger.
- Plasma cutting precision is around 1-2mm. The cut surface has a tilt of 0.5º-1.5º and the cut hardens, making further processing difficult.
- Plasma cutting is slower with wider kerfs, leading to significant thermal effects and thermal deformation.
3. Environmental Comparison
Laser Cutting: Smaller kerf, less heat impact, faster cutting speed, higher precision, and better dust removal.
Plasma Cutting: Larger kerf, more cutting dust, and poor dust removal.
4. Safety Comparison
- The laser cutter with surround is guarded so that the person does not have to look directly at the laser. Ground rail laser cutter with safety guard grating will not cause impact injury to the person.
- Plasma cutting and flame cutting are open, generally without safety grilles, and there’s a risk of arc radiation causing harm to the human body.
Parameter | Laser Cutting | Plasma/Flame Cutting | Laser Advantage |
Positioning accuracy | 0.1mm(@10m bed) | 0.4mm(@10m bed) | High accuracy |
Perpendicularity of section | 0.2mm(@40mm thick) | 5mm(@40mm thick) | No finishing required |
Slit width | 0.2-1.6mm | 2-5mm | Save 5-7% of materials |
Margin and Common Edge | 3-4mm | 10mm | |
Heat-affected zone | 0.1-0.4mm | 0.5-2.0mm | Less heat absorption, small deformation |
Section Quality | Excellent, less hanging slag | Average | No grinding required |
Cutting speed(medium sheet) | Very fast | Average | High productivity |
Cutting small holes | Diameter to depth ratio of 20% | Unable to cut small holes | Saves on drilling and transportation |
Working environment | Clean | Smoky | Healthy and eco-friendly |
Cost Advantages of Adopting Laser Cutting for Ships
Now, let’s learn more about how laser cutting saves project costs.
- The use of laser processing can reduce labor costs, reduce the process, and improve efficiency. From drawing to laser processing in a single molding, including marking. Plasma or flame processing is also required after the completion of the CNC drilling machine to hit the eye, with manual trimming, with a stone pen marking number. Using laser cutting systems can generally save 4 to 6 workers, and according to each worker $50,000 / year expenditure, can save about $200,000-300,000 / year.
- Laser processing can improve the material utilization rate. For plasma or flame, the material utilization rate is 70-85%. According to the comparison of our old customers in about 1 year, the material utilization rate of laser cutting can be increased by 5-8%. Relative to the annual processing volume of 10,000 tons of steel processing plant, laser cutting volume accounted for 1 / 3, that is, more than 3,000 tons, which can increase the revenue of 150 tons. Calculated at $800 per ton, that is, $120,000 / year.
- Increase assembly speed on site. Per diem wages for outdoor assembly workers are in the range of $300/day. The speed of assembling workpieces with a laser cutting system can be increased by 100%- 200%. The main reason is that the laser cut workpiece has high precision and small deformation. At present, workers are basically using the piecework system, more willing to use the laser cut workpiece for assembly, improve income, and improve installation efficiency.
- Laser cutting has a narrow slit, high precision, good cross section and small taper. The cutting seam of plasma and flame is between 1mm-5mm, while the cutting seam of laser is between 0.3 mm-1.5mm. The traditional way of undercutting into pieces of scrap is more. Laser cutting has less scrap and high value.
Below we compare 10,000-watt laser cutting with plasma cutting, using carbon steel as the material for comparison.
Cost Items | Laser Cutting(12KW) | Laser Cutting(20KW) | Plasma Cutting(300A) |
Equipment Consumables ($/hour) | 0.7 | 0.7 | 9.7 (Electrodes, nozzles, eddy current rings, etc.) |
Average equipment power consumption ($/hour) | 8.3 | 11 | 11 |
Oxygen consumption ($/hour) | 1.4 | 1.4 | 1.4 |
Handling (1 person) and grinding (2 persons) costs | 0 | 0 | 8.3 |
Drilling & positioning, transfer, etc. (3 people plus equipment, etc.) | 0 | 0 | 8.3 |
Fixed cost (USD/hour) | 9(10.4) | 11.7(13.1) | 38.7 |
Cutting speed (14mm carbon steel) | 4m/min | 6m/min | 3.4m/min |
Running cost per meter | 9/60/4m=0.0375$/m | 11.7/60/6m=0.0325$/m | 38.7/60/3.4m=0.19$/m |
Cutting speed (30mm carbon steel) | 0.41m/min | 1.2m/min | 1.5m/min |
Running cost per meter | 10.4/60/0.41m=0.41$/m | 13.1/60/1.2m=0.18$/m | 38.7/60/1.5m=0.43$/m |
From the above analysis, you know that laser cutting technology can bring great advantages in terms of cutting quality and cost.

Applications of Laser Cutting in the Shipbuilding Industry
The applications of laser cutting technology in the shipbuilding industry involve all aspects of ships. Specific shipbuilding applications are listed below:
- Hull Fabrication: Laser cutting is extensively used for cutting the marine steel plates and sections that form the ship’s hull. Its ability to handle thick materials with precision is essential for the overall structural integrity of the vessel.
- Framework and Structural Components: Internal structures like ribs, frames, and bulkheads are laser cut to ensure exact dimensions and fit. This precision is crucial for maintaining the strength and stability of the ship.
- Deck Construction: Decks of ships consist of numerous steel sheets and intricate components. Laser cutting provides the accuracy needed for these parts to align correctly during assembly.
- Superstructure Elements: The ship’s superstructure, which includes parts like the bridge, navigation rooms, and living quarters, requires precise cutting for various components. Laser cutting allows for intricate designs and precise dimensions.
- Door, Window, and Hatch Frames: Accurate cutting of frames for doors, windows, and hatches is crucial for ensuring watertight and secure closures, which laser cutting can achieve effectively.
- Engine and Machinery Components: In the engine room, various metal parts and components can be laser cut to meet specific requirements for machinery installation and maintenance.
How to Choose a Laser Cutting Machine?
Choosing the right laser cutting machine for the shipbuilding industry involves considering several key factors to ensure that the machine meets the specific demands of ship construction. So that you don’t miss anything, we’ve put together a comprehensive list of criteria to consider:
- Material Compatibility: The chosen laser cutter should be capable of handling the types of materials commonly used in shipbuilding, such as thick steel plates, aluminum, and composites. It should efficiently cut through these materials with the desired quality.
- Laser Power and Type: Higher laser power is needed for thicker and harder materials. Typically, a laser with higher wattage will be more effective for cutting thick steel plates. Choose between CO2 lasers, which are common and efficient for a wide range of materials, and fiber lasers, which are more effective for metals and offer higher energy efficiency.
- Cutting Bed Size: Given the large size of the materials used in shipbuilding, the cutting bed of the laser machine should be large enough to accommodate these sizes. Ensure that the machine’s cutting bed or working area can handle the typical dimensions of materials used in ship construction.
- Precision and Accuracy: The machine must offer high precision and accuracy to ensure the components fit perfectly during the ship assembly process. This is crucial for maintaining the structural integrity and safety of the ship.
- Speed and Productivity: Evaluate the cutting speed of the machine. Faster cutting speeds increase productivity, which is vital in large-scale manufacturing processes like shipbuilding.
- Durability and Reliability: The shipbuilding environment can be demanding. Choose a laser cutter that is robust and reliable, and capable of operating under challenging conditions and for extended periods without significant downtime.
- Ease of Use and Control: User-friendly interfaces and robust software control are important for efficient operation. Compatibility with CAD/CAM software and programmable CNC systems is essential for precise and complex cuts.
- Safety Features: Safety is paramount. The machine should have built-in safety features like fume extractors, fire suppression systems, and safety interlocks to protect operators and the work environment.
- Technical Support and Maintenance: Consider the availability of technical support, maintenance services, and spare parts from the manufacturer. Reliable after-sales support is crucial for minimizing downtime and maintaining the machine’s performance over time.
- Cost-Effectiveness: Finally, evaluate the total cost of ownership, including initial purchase price, operating costs, maintenance, and potential savings in terms of increased productivity and reduced waste.
Product Solutions for the Shipbuilding Industry
After understanding how to choose the right laser cutter, you can make a better judgment. Of course, if you want to buy directly, we offer product solutions for the shipbuilding industry.
1. GX-T High Power Laser Cutting Machine
The GX-T high-power laser cutting machine stands out as an optimal choice for the shipbuilding industry due to its advanced features and capabilities. This machine is equipped with an intelligent bus control system and a high-efficiency, high-power laser cutting head, tailored specifically for demanding tasks.
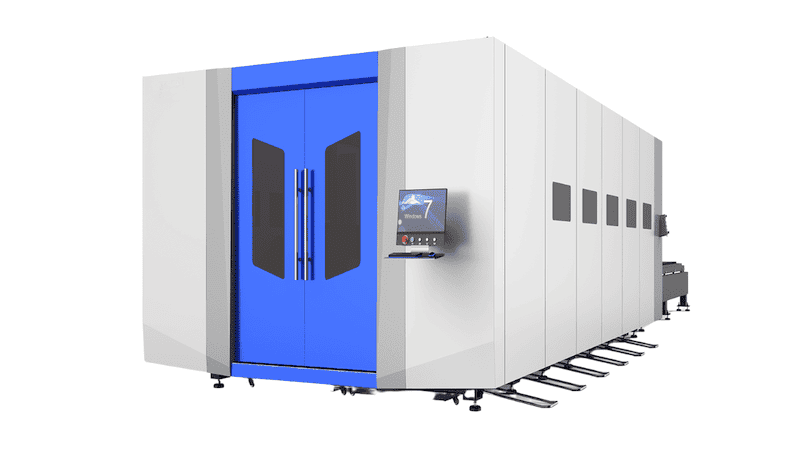
Key features of the GX-T include:
- Power Range: The fiber laser cutting machine offers a wide range of power options, from 6000W to 30000W. This flexibility allows it to handle various thicknesses and types of materials commonly used in shipbuilding with ease.
- Large Processing Area: The GX-T can accommodate large workpieces, which is essential in shipbuilding. It offers several options for the processing area, including 6000×2000 mm, 8000×2500 mm, and 1200×3000 mm. This capability ensures that large ship components can be cut with precision.
- Intelligent Bus Control System: This system enhances the overall efficiency of the machine. It ensures seamless communication between different components, leading to precise control and faster processing times, which is critical in large-scale production like shipbuilding.
- Sophisticated Laser Cutting Head: The cutting head is designed for high-power operation, making it ideal for cutting thick materials used in shipbuilding. Its design ensures high precision and quality in the cutting process, reducing the need for secondary finishing.
- Versatility and Efficiency: The combination of power, size, and intelligent control makes the GX-T highly versatile and efficient, capable of handling a wide range of cutting tasks in the shipbuilding industry with high precision and speed.
The GX-T high-power laser cutting machine is not only remarkable for its cutting capabilities but also for its innovative bed design, enhancing its durability and functionality, especially for demanding environments like shipbuilding. Key aspects of its bed design include:
- Semi-Hollow Bed Structure: Utilizes a 30mm thick cold-drawn plate as the main beam with graphite protection, reducing heat exposure and minimizing deformation risks.
- Detachable Rear Frame Design: Facilitates easier transportation and container loading, enhancing its portability for global shipping needs.
- Detachable Crossbeam Design on Cutting Platform: Allows for easy replacement of parts affected by heat deformation, ensuring efficient maintenance.
- Single Motor for Dual Platform Translation Exchange: Simplifies the machine’s mechanical structure, ensuring smooth operation and reduced maintenance.
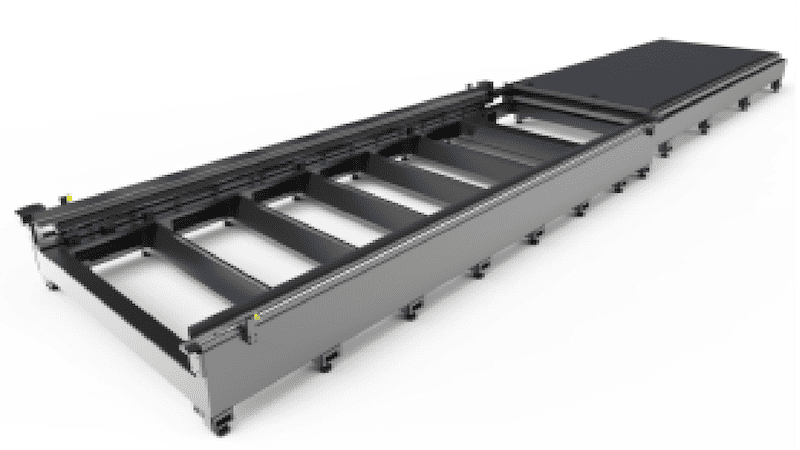
These design features collectively enhance the GX-T machine’s efficiency, durability, and ease of maintenance, making it a highly suitable choice for the rigorous demands of the shipbuilding industry.
2. H26030G Ground Rail Bevel Laser Cutting Machine
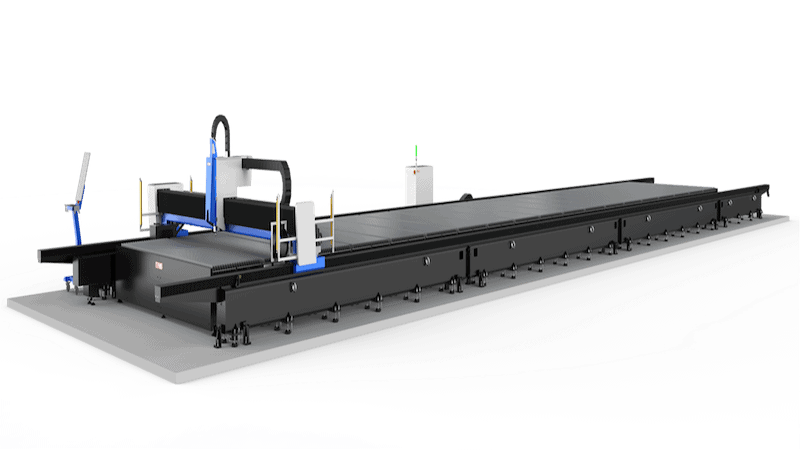
The H26030G Ground Rail Bevel Laser Cutting Machine is a highly recommended equipment for the shipbuilding industry, offering customized features for enhanced efficiency and precision. Key features include:
- Customizable Processing Area and Bevel Cutting: Allows for custom specifications in the processing area, with the capability for ±45° bevel cutting, accommodating various shipbuilding requirements.
- Power Options: Available in a range of 12000W to 40000W, providing flexibility and power to handle different materials and thicknesses.
- Modular Design: The machine’s platform and bed are modularly designed, enabling easy maintenance and reducing the risk of heat deformation during prolonged laser cutting.
- Durable Bed Design: Features a spliced bed design, effectively reducing heat deformation and extending the bed’s lifespan up to 30 years. The bed’s separation from the working table minimizes impact during heavy material loading, preserving precision.
- Advanced Beam Construction: Utilizes high-quality steel and mechanical data analysis to ensure the beam’s rigidity and minimal deformation at high speeds, addressing the issue of precision in large-area cutting.
- Safety Features: The moving beam is protected by a grating to prevent collisions, ensuring both machine and operator safety.
- Efficient Smoke Extraction System: Adopts a costlier but more effective right-blow-left-suction smoke extraction system, improving dust removal and ensuring a cleaner working environment.
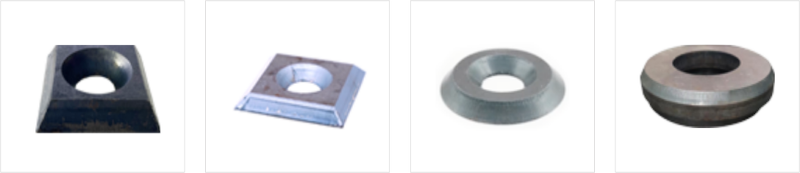
This combination of features makes the H26030G an adaptable, precise, and durable choice for the complex demands of the shipbuilding industry.

FAQs
1. How does laser cutting technology benefit the maritime and shipbuilding industry as a whole?
Laser cutting technology offers significant benefits to the maritime and shipbuilding industry, such as improved welding speed, high-quality cuts, and reduced production costs, contributing to the overall efficiency and competitiveness of the industry
2. What role does laser cutting technology play in reducing the need for secondary processing in shipbuilding?
Laser cutting technology’s high precision and accuracy eliminate the need for secondary processing, such as edge deburring or finishing, streamlining the manufacturing process and reducing the overall time and resources required for production
3. Can laser cutting technology be integrated with other welding processes in the shipbuilding industry?
Yes, laser cutting technology can be integrated with other welding processes such as arc welding, hybrid welding, and gas metal arc welding, offering a comprehensive solution for the fabrication and assembly of components in shipbuilding.
Conclusion
Laser cutting technology is significantly transforming the shipbuilding industry by offering unparalleled precision and speed in processing. This advanced method allows for efficient cutting of thick staples in ship construction, reducing errors and the need for secondary finishing. Adopting laser cutting not only accelerates production but also proves cost-effective in the long run. Overall, laser cutting stands as a crucial technological advancement, shaping the future of efficient and innovative shipbuilding.
Don’t Miss Out on Baison Laser Solutions!
Ready to revolutionize your shipbuilding projects with cutting-edge laser technology? Discover how Baison Laser can elevate your projects with unparalleled precision and efficiency. Contact us today to learn more and take the first step towards transforming your shipbuilding capabilities with the power of laser cutting and laser welding. Your future in advanced maritime construction starts with Baison Laser!