Laser cutting has slowly taken over all sectors of the manufacturing space with its incredible accuracy and efficiency. However, along with its countless benefits, a common challenge is laser cutting dust. The fine particles and fumes generated during the cutting process can not only compromise the quality of your work but also pose health and safety risks.
In this article, we will explore the composition, causes, and effective strategies to remove laser cutting dust.
What is Laser Cutting Dust?
Laser cutting dust refers to the small particles and material remnants generated during the laser cutting process. As the high-power laser beam selectively melts and vaporizes the workpiece, it gives rise to a cloud of toxic fumes, burnt-off material pieces, and metal oxides.
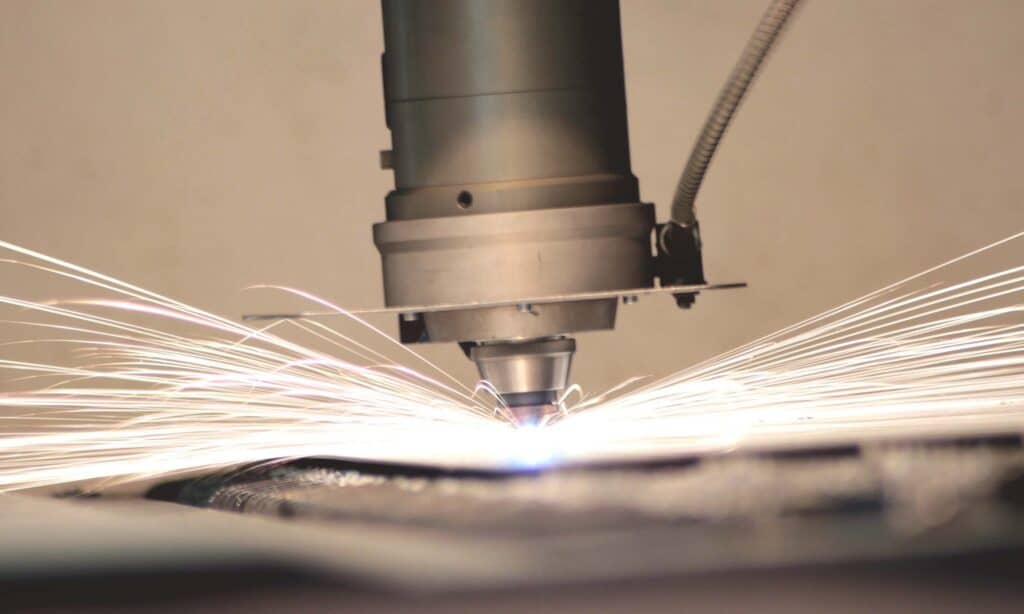
The dust cloud’s exact composition depends upon the laser type, cut material, and environmental impurities. Commonly, the dust will consist of tiny particles of the material itself and any coatings or contaminants on its surface.
Laser generated dust poses health and safety concerns, as it may contain potentially harmful substances or irritants, especially when cutting materials like plastics or metals with coatings. Considering this the American National Standards Institute (ANSI) has developed safety protocols for proper and safe use of lasers.
Proper ventilation and exhaust systems are essential for removing dust and fumes from the cutting area to protect the health of operators and maintain the integrity of the laser cutting equipment.
Additionally, it’s important to collect and properly dispose of the dust in an environmentally responsible manner, as some materials may be hazardous or require special handling for disposal.
What Causes Laser Cutting to Generate Dust?
Lasers are commonly used to cut, weld, engrave, clean, and mark various materials, ranging from soft plastics to hard tungsten. Between the vast material variety and the different laser processing techniques, several factors arise that contribute to dust and fume generation.
For example, laser cutting stainless steel plates without any gas assistance will lead to iron oxide formation. The heat radiating from the laser causes the metal oxides to disintegrate into fine dust. Additionally, surface impurities on the steel plate, like organic matter, trace elements, or oils, will burn off and generate potentially toxic fumes (or smoke).
But if you switch to a non-metal workpiece, the variables change, and a completely different set of factors is responsible for the dust generation.
We break down these complex factors into six categories for operator convenience and ease of understanding.
1. Material Properties
The material’s composition and properties are the biggest influence on laser cutting dust. Different materials produce different types of dust. For example, cutting metals will create metal shavings and oxides, while a piece of laser-engraved wood will produce wood particles and carbon dust.
Additionally, materials like plastics or composites may release fumes and residues alongside the dust.
2. Surface Coatings and Impurities
Manufacturing materials usually have surface coatings or contaminants, such as paint, rust, or lubricants. Laser cutting vaporizes and removes these coatings, adding to the dust generated during the process.
These coatings may sometimes contain harmful substances, making proper ventilation and filtration crucial.
3. Gas Assistance
Laser cutting processes commonly use a gas or gas mixture (typically nitrogen or oxygen) to jet away metal slag and dust generated from the cutting process and prevent oxidation and material ignition.
This gas can react with the material itself or its surface coatings to generate more dust, as well as fumes, depending on the specific process and material being cut.
Additionally, the high-pressure gas jet pushes unwanted waste material (dust or slag) away from the workpiece and into the air. Hence, a laser cutter with gas assistance must be used in conjunction with a laser dust collection system.
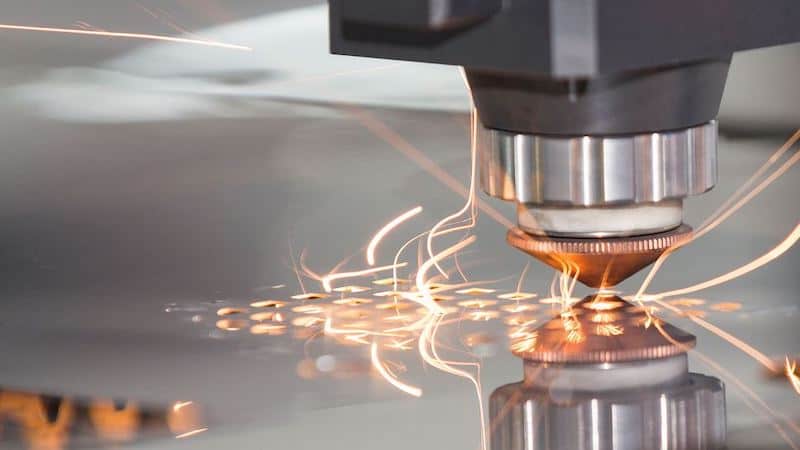
4. Laser Speed and Power
The operating parameters of laser cutting, including the cutting speed and power of the laser beam, can influence the size, nature, and amount of dust produced. Higher power output and a slower cutting speed will result in more extensive vaporization, creating more dust.
As the laser beam slowly moves across the workpiece, more dust particulate accumulates on the surface.
5. Laser Beam Focus
The laser beam spot diameter is the size of the contact point of the laser. A smaller spot diameter results in higher precision and less heat input into the workpiece.
Poor beam focus results in a larger spot diameter, which can lead to excessive melting and vaporization of the material, increasing the dust generated.
6. Laser Engraving or Cleaning
Moving on to other laser processes, we see a higher chance of dust generation. The laser engraving process selectively vaporizes the material’s surface to create a design, pattern, or text.
The dust that accumulates from the engraving process is directly proportional to the size of the engraving design. Larger designs mean more material is removed, which means more dust generation.
Laser cleaning follows a similar principle. Here, instead of a small pattern, the laser vaporizes the entire top surface of the workpiece.
7. Fiber Laser vs CO2 Laser
While the source of the laser isn’t the biggest factor responsible for the dust particles, it still plays a major role in dust prevention.
A fiber laser cutting machine is more accurate and precise due to its smaller spot diameter and faster cutting speed, resulting in better dust control. When it comes to dust generation, fiber lasers are highly recommended for all sorts of cutting and engraving operations.
However, in rare scenarios like metalworking shiny metal surfaces (stainless steel or brass), CO2 lasers perform better and generate less dust.
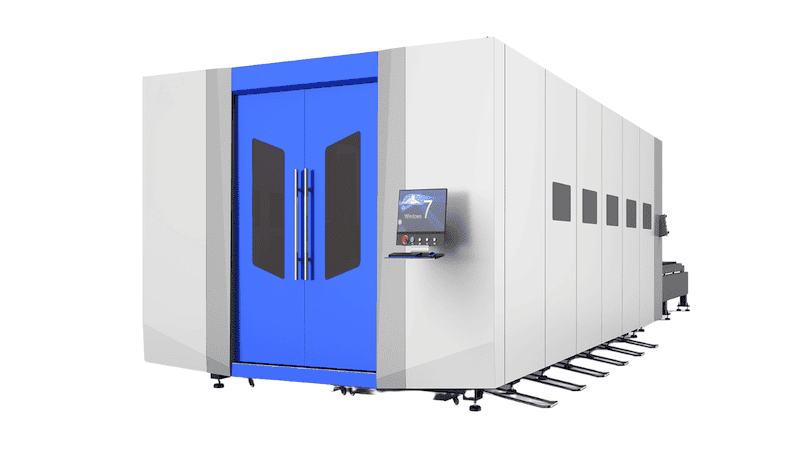
What are the Risks Associated with Laser Dust?
Laser dust can cause a number of health, equipment, and operational challenges, depending upon the material type and cutting conditions.
Following is a short list of the biggest potential risks of laser dust.
1. Respiratory Issues
By far, the most obvious and biggest danger associated with laser dust is inhalation hazards that can lead to respiratory issues. Dust particles are often so fine that they remain suspended in the air for long durations, increasing the risk of inhaling by a machine operator.
Prolonged exposure to laser dust and fumes can result in asthma, bronchitis, or other lung disorders.
2. Eye and Skin Irritation
Irritation and discomfort from dust contact are related to dust particulate size. Larger bits and debris are easier to remove from the skin surface. But finer dust particles can adhere to the skin or enter the eyes, causing intense irritation.
Metal cutting, in particular, can generate unwanted fine dust that is difficult to remove.
3. Fire Safety Risks
Metal dust is flammable and can have explosive characteristics. Aluminum, a popular laser cutting material, has a much higher chance of ignition in dust form.
Poor ventilation leads to lower air quality and increases dust accumulation. Thus increasing the risk of dust ignition.
4. Toxic Substance Exposure
Materials like composites contain plastic-based resins that can result in toxic substances when cut by a laser. Exposure to these substances can have serious health consequences.
Similarly, coatings, paints, and surface treatments on materials can release chemical fumes when exposed to the high temperatures of laser cutting.
Operators may be exposed to potentially harmful substances if proper precautions are not taken. Therefore, it is crucial that you identify and manage the risks associated with processing specific materials or their coatings.
5. Equipment Damage
A laser machine requires a clean work environment to operate at peak performance. Dust accumulation within the laser cutting equipment can lead to reduced efficiency at best and serious damage to optical components at worst. Resulting in increased maintenance and downtime.
6. Increase in Operational Cost
Dust accumulation leads to equipment damage and increases operator health risks. Leading to production downtime due to laser maintenance and medical checkups.
High-performance laser cutting machines work on tight tolerances; their expensive laser sources are susceptible to dust damage.
A lack of dust removal methods can lead to long-term operational costs for the business.
5 Ways to Remove Laser Cutting Dust
Removing laser dust is essential for maintaining a safe and clean working environment, preventing equipment damage, and ensuring equipment longevity.
Following are some of the most common dust removal methods for laser cutters.
1. Integrated Ventilation and Dust Collection
Most laser cutting machines come with integrated dust filtration and ventilation systems. These machines usually have a closed-up design and a built-in vacuum that pulls all the dust and cutting fumes from the work bed and deposits it into a dust collection bin.
Unfortunately, larger industrial laser cutters trade in the integrated ventilation system for a larger work bed and production flexibility.
2. External Dust Collectors
External dust collectors are by far the best method of dust removal. They come in various sizes, with a built-in filter material separating the solid particulates and properly containing harmful cutting fumes.
Dust collectors are a must-have for workspaces with limited airflow or large businesses with multiple laser cutters on the factory floor.
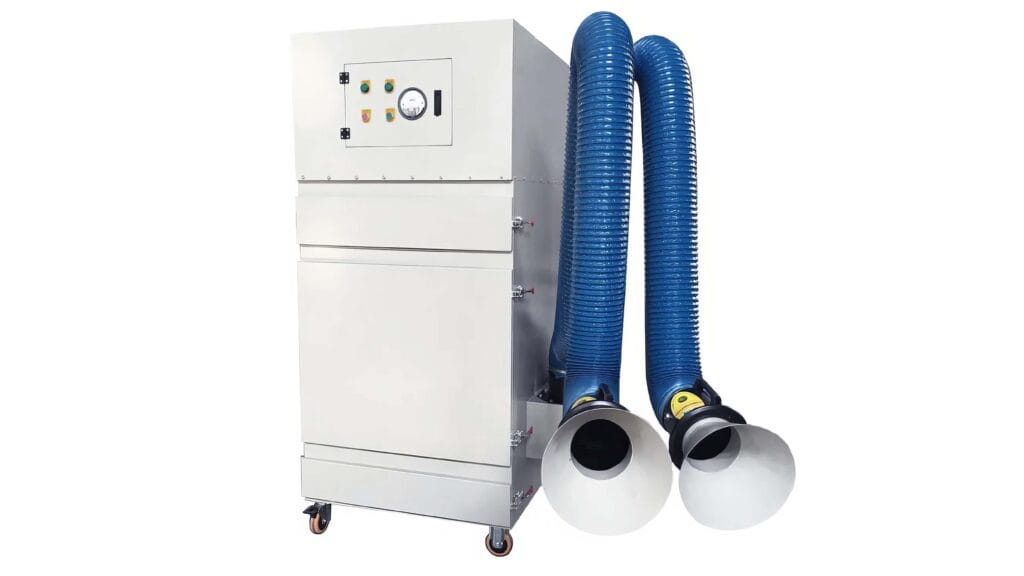
3. Workshop Vacuum Cleaners
A low-cost solution to laser dust removal is the use of shop vacuums. Operators can manually use these vacuums during cutting operations. However, manual dust collection using shop Vacs is impractical for large-volume productions.
4. Fume Extraction Hoods
The fume extraction hood is a top-mounted ventilation system that goes directly above the laser cutter and efficiently removes toxic fumes from the workspace.
5. Manually Clean Your Laser Cutter
Finally, the simplest means of dust removal is manually cleaning your laser cutter. You can use brushes, compressed air jets, and rags to clean your laser cutting machine and ensure consistent maximum performance.
Considerations for Selecting the Right Dust Collector
Choosing the right dust filter for your factory or small workshop is all about assessing your business needs and production requirements. Here are 5 factors to consider:
1. Airflow Requirements
Estimate the required airflow or air volume (measured in cubic feet per minute, CFM) for your workspace. or air volume (measured in cubic feet per minute, CFM). Consultation from an HVAC expert is crucial in this regard,
Ensure that the dust collector has sufficient capacity to handle the anticipated airflow.
2. Filtration Efficiency
Filter efficiency refers to the filtration system’s ability to capture and filter tiny particles. Choose a dust collector with a filtration system that matches the size and nature of the dust particles.
Depending upon your specific applications, a HEPA (High-efficiency particulate air) filter may be necessary for fine or hazardous dust.
3. Space and Installation
Industrial dust collectors take up a lot of floor space, and the installation process is anything but simple. Alternative dust removal methods often take up less space or are mounted on the ceiling.
Select a dust filter that doesn’t disrupt your factory’s day-to-day operations.
4. Maintenance Requirements
Dust collectors have their own set of maintenance requirements. Some require frequent filter changes, while others need to be cleaned out occasionally.
Industrial units often can only be serviced by trained professionals, which leads to production downtime.
5. Cost of Ownership
The flat price of a dust collector is generally inconsequential compared to the hundreds of thousands of dollars businesses spend on industrial laser cutting machines.
However, shipping, installation, maintenance, and energy consumption costs can often exceed the initial price of the machine.
5 Tips to Avoid Dust in a Laser Cutting Machine
Avoiding dust in your laser cutting machine is easy once you know these simple tricks.
- Proper ventilation and filtration near your laser cutter is crucial.
- Keep your workpiece clean and avoid unnecessary laser fumes.
- Use inert gas jets to improve the cutting process and prevent dust accumulation.
- Minimize reflective surfaces as they can scatter the laser beam and create additional dust.
- Optimize your cutting parameters by adjusting laser power, cutting speed, and focus settings.
FAQs
FAQ 1: Is Laser Cutting Dust Hazardous?
Laser cutting dust can be hazardous, especially when inhaled. Certain materials also release toxic fumes when cut.
FAQ 2: What PPE is Needed for Laser Dust?
PPE (personal protective equipment) should be worn even when using a dust collector. Use safety glasses and a face mask when operating a laser cutter.
FAQ 3: What is Laser Cutting Metal Dust Made Of?
Metal dust generated from laser cutting comprises small metal particles, oxides, and burnt impurities.
FAQ 4: Are Dust Collectors for Laser Cutters Expensive?
Dust collectors for laser cutting machines start at $2,000, with high-performance models going for $25,000 or more.
Conclusion
Laser cutting is an excellent tool for manufacturers around the world. However, like any tool, it needs proper care and maintenance. Cutting materials can often lead to dust and fume generation, which can have severe negative consequences. But, proper practices can help mitigate dust accumulation and avoid future accidents.
Experience the Best Laser Machines with Baison!
At Baison, we’re dedicated to delivering cutting-edge fiber laser solutions that set new industry standards. With its unmatched precision, efficiency, and versatility, our state-of-the-art laser technology enables the business to achieve greater success.
Take advantage of our FREE Application Evaluation and Customer Training and see which laser-cutting products are best for your business needs.
Explore the future of laser technology with Baison! Contact us Now!