This article will discuss practical strategies to relieve stress in laser welding machines, helping businesses maximize ROI and maintain optimal performance.
What Is laser welding?
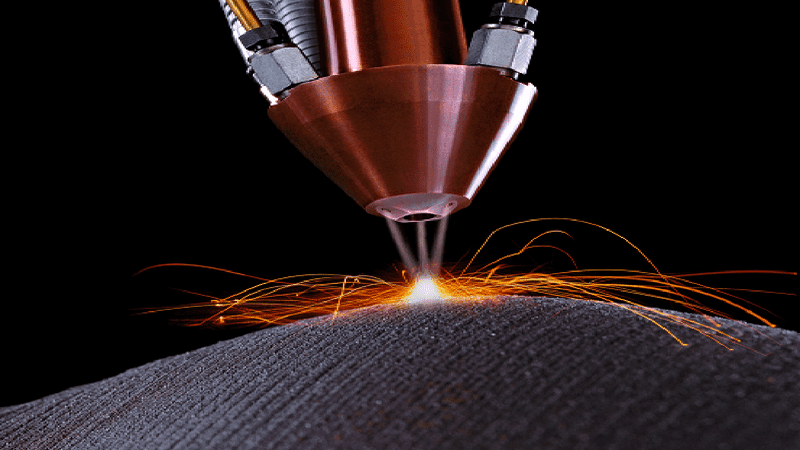
Laser welding uses a focused laser beam to join metal or thermoplastic pieces. The beam melts the material at the contact point, creating a bond. It’s precise and efficient, making it popular in the automotive, aerospace, medical, electronics, and even fitness industries.
Laser welding offers several benefits compared to traditional welding methods, such as TIG or MIG. It creates a narrow and deep weld, increasing joint strength and durability. Moreover, it produces less heat and distortion, reducing the risk of damage to surrounding parts.
Additionally, modern laser welding comes with automation, improving productivity and reducing labor costs in mass production. Overall, it’s a versatile and effective process for meeting various industrial demands.
What Is Stress Relieving in Laser Welding?
Stress relieving in laser welding is crucial for minimizing residual stresses. This can cause material distortion and cracking over time due to thermal expansion and contraction during welding.
The Process
The welded parts are heated to a specific temperature below the metal’s melting point to relieve stress. Once done, they are cooled slowly, which helps redistribute internal stresses and reduces the risk of failure.
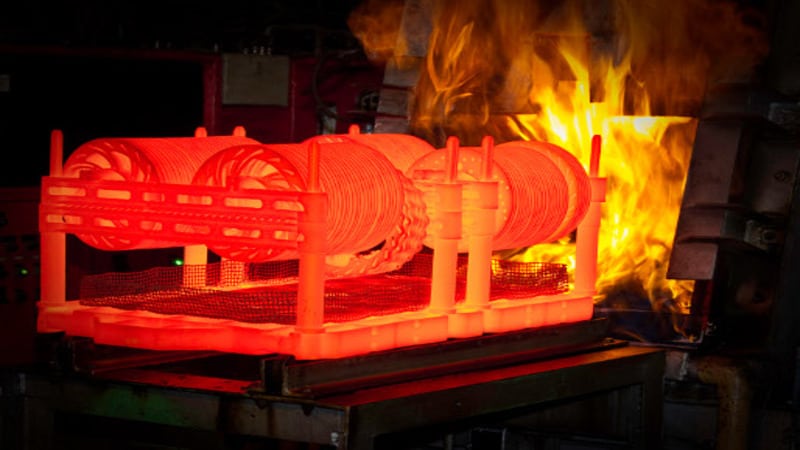
It is vital to note that the temperature and time required for stress relief depend on the material and welding parameters used. Stress relieving process plays a pivotal role in ensuring the quality and integrity of welded parts, leading to cost savings and increased customer satisfaction by enhancing the overall product quality.
Why Is Stress Relief Performed in Laser Welding?
These bullet points outline the importance of stress relief in laser welding. Residual stress can cause structural issues in welded materials, but stress relief can help redistribute internal stresses, improve durability, and ensure compliance with industry standards.
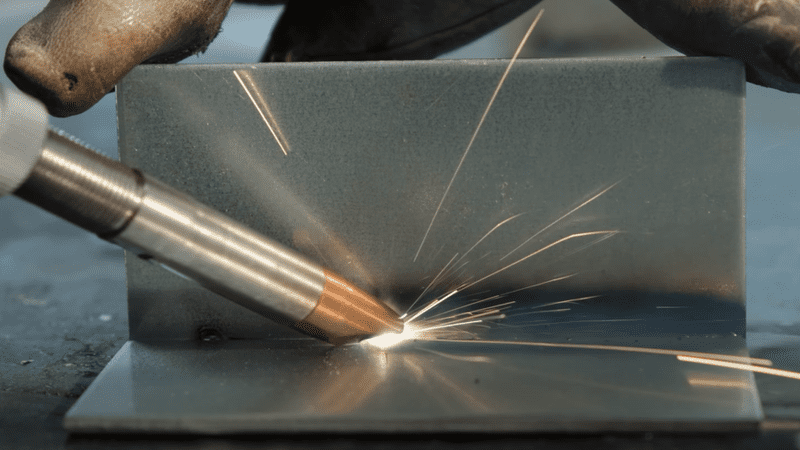
- Countering Thermal Expansion: Thermal expansion and contraction during welding can lead to residual stresses in the metal.
- Preventing Distortion: Residual stresses can cause warping, cracking, and distortion if not addressed.
- Stress Redistribution: Laser welding stress relief redistributes and reduces internal stresses, improving structural integrity and preventing issues.
- Improving Fatigue Strength: Fatigue strength can be improved, extending the lifespan of welded parts.
- Industrial Requirements: Some industries require stress relief per standards and specifications, such as aerospace, automotive, and medical fields.
- Quality Requirements: Laser welding stress relief ensures quality and compliance with industry regulations.
6 Ways to Reduce Stress in Laser Welding
If you have struggled with laser welding stress relief at your production site, the following 6 ways will help you:
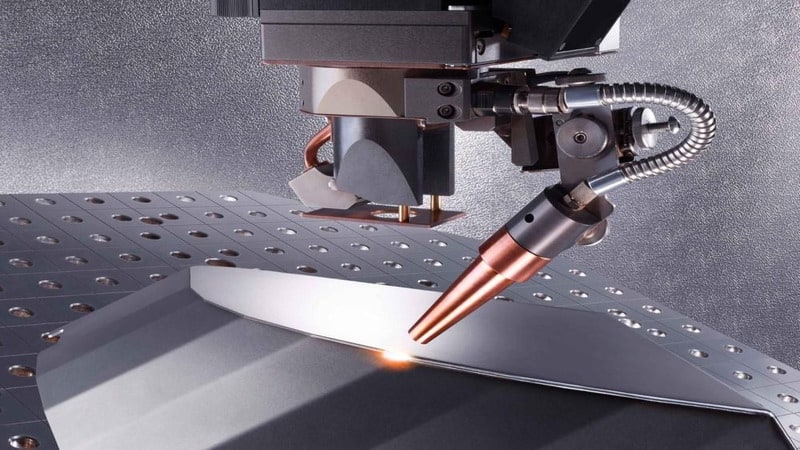
- Adjust Welding Parameters: Adjusting the welding parameters, such as the laser power, welding speed, and focal length, can help to minimize stress. You can optimize the welding conditions for the specific material and welding thickness.
- Preheat The Material: Preheating the material before welding helps reduce thermal gradients and minimize residual stress. Just make sure the preheating temperature stays below the material’s melting point but high enough to reduce the temperature gradient.
- Use Filler Materials: Using filler materials during welding also helps reduce residual stress by controlling the material’s cooling rate. Hence, filler materials with a lower thermal expansion coefficient than the base material can help minimize thermal gradients and reduce stress.
- Post-weld Heat Treatment: Applying post-weld stress relief heat treatment, such as stress relief annealing, helps reduce residual stresses in the welded material. This involves heating the material to a specific temperature, holding it for a specific time, and then slowly cooling it.
- Use Proper Clamping And Fixturing: stress-induced distortion is another issue that comes with welding. Proper clamping and fixturing of the material being welded can reduce this distortion and minimize stress. It does so by holding the material in place during welding, preventing warping or bending.
- Use Laser Beam Oscillation: Laser beam oscillation is another way to reduce residual stresses. This process achieves this by spreading the heat over a wider area, thereby reducing the temperature gradient. This can be done by oscillating the laser beam during welding or using a beam with a larger spot size.
What Is the Most Common Method of Stress-Relieving Welds?
The most common method of stress-relieving welds is post-weld heat treatment (PWHT). This involves heating the welded material to a specific temperature, typically below the melting point, and holding it at that temperature for a set amount of time before slowly cooling it down. Let’s have a look at this stress relief heat treatment step by step:
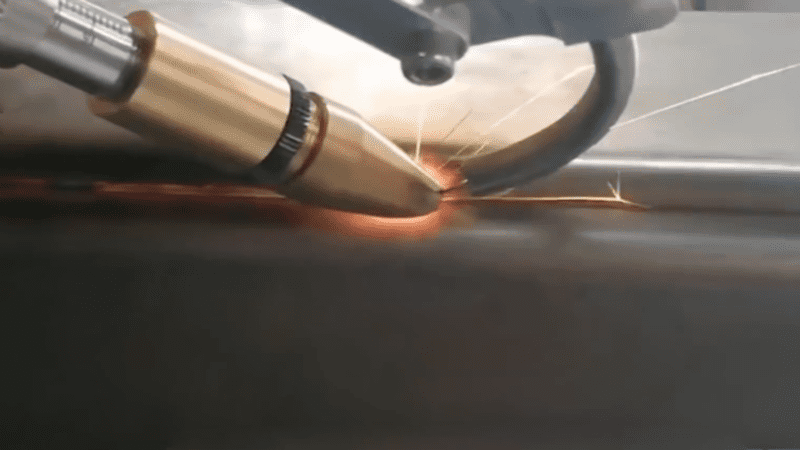
Determine the Appropriate Temperature and Hold the Time
The specific temperature and hold time for PWHT depend on the material being welded and its parameters. These include the thickness, industry standards, and specifications for the application. You can check the welding codes and standards for this information, use the material data sheets, or consult with the manufacturer.
Clean the Welded Material
Make sure to clean the welded material must be cleaned thoroughly to remove any surface contaminants. These can range from oils to grease or dirt that can interfere with the PWHT process.
Heat the Material
The next step involves heating the welded material using an oven or furnace to the specific temperature required for stress relief. Make sure the heating rate is slow and consistent throughout to prevent thermal shock and distortion.
Hold the Material at the Specified Temperature
Once the material reaches the specified temperature, it is held at that temperature for the specified hold time. The hold time allows the internal stresses to redistribute and reduces the residual stresses.
Cool the Material Slowly
After the hold time, allow the material to cool down slowly in the oven or the furnace. Also, make sure to have a steady and controlled cooling rate to prevent thermal shock and minimize residual stresses.
Inspect the Material
Once the material has cooled to ambient stress-relieving temperature, it should be inspected for any signs of defects or cracks. If you find any defects, make sure to repair them before further use.
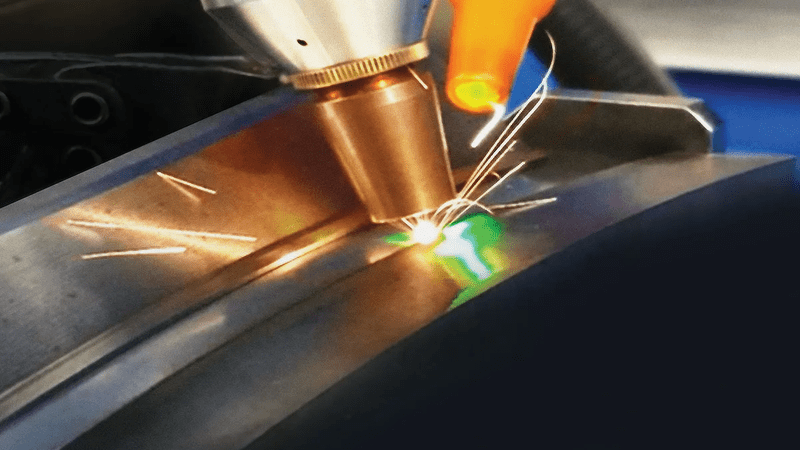
When Should You Relieve Stress After Laser Welding?
Ideally, the stress relief process must come after the laser welding process. Most manufacturers and industry experts believe it is the most practical approach. This is because residual stresses in the material can lead to a variety of problems, such as stress corrosion, cracking, warping, and distortion, particularly if the welded material is subjected to further processing or use.
In some cases, manufacturers also relieve stress during the welding process itself. For instance, residual stresses can be particularly high when welding thick or complex structures. This is known as in-process stress relief. It involves heating the material with a local heat source during welding to reduce residual stress.
However, in most cases, manufacturers perform stress relief as a separate operation after completing the welding process. This allows the material to cool down and stabilize before being subjected to the stress relief process.
It’s important to note that stress relief is only sometimes necessary or practical for every welding application. The need for stress relief depends on the welding material and the welding process used, the application requirements, as well as the industry standards and specifications. Consulting with a welding engineer or metallurgist can help determine if stress relief is necessary for a specific welding application.
What Are the Effects of Stress on the Laser Machine?
Here are some of the potential effects of stress on the laser machine:
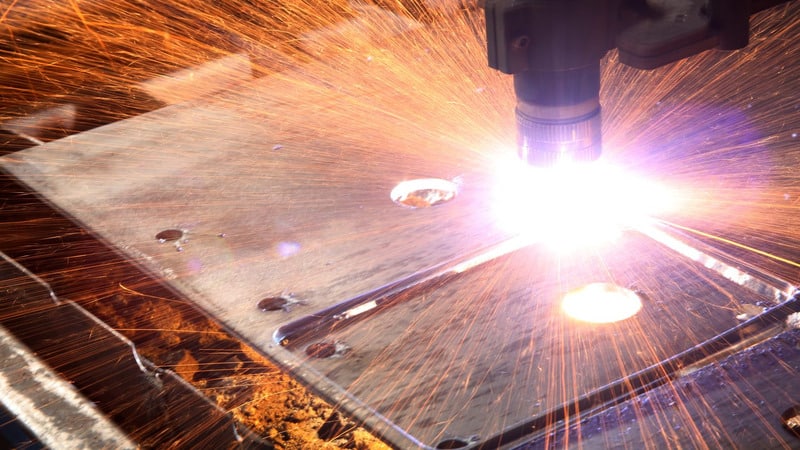
- Shorten Machine Lifespan: Residual stress can cause material fatigue, leading to cracks and other damage that can shorten its lifespan.
- Low Accuracy And Precision: Stress in the machine can cause it to warp or distort, leading to reduced accuracy and precision in the laser welding process.
- Reduced Productivity: If the machine is damaged or not working properly due to stress, it can lead to downtime and reduced productivity.
- Safety Concerns: If stress leads to cracks or other damage in critical parts of the machine, it can pose a safety risk to operators and other personnel working with the machine.
- Increased Maintenance Costs: If stress leads to damage in the machine, it can increase maintenance costs as parts need repair or replacement more frequently.
Conclusion
In conclusion, the stress relieving process is an essential step in the laser welding process that helps to minimize residual stress and improve the quality and durability of the welded parts.
By implementing the methods discussed in this article, businesses can reduce the potential negative effects of stress on the laser machine, such as reduced accuracy, productivity, and lifespan.
With proper stress relief processes and techniques, businesses can achieve cost savings and increased customer satisfaction through improved product performance and durability.
Discover the Perfect Solution for Your Business with Baison
Baison offers a wide range of laser welding solutions that can help your business achieve high-quality welds with minimal stress. Our team of experts can work with you to design and implement a customized laser welding solution that meets your specific needs.
With Baison, you can enjoy improved efficiency, reduced costs, and increased customer satisfaction. Contact us today to discover the perfect solution for your business.