Laser cutting is one of the most common processes observed for many applications. However, as much as the process is necessary, the edge quality obtained after the cut is equally significant. In cases where the quality of the edge is not smooth and fine, it may not be able to achieve the required purpose and function in an application.
This guide below provides detailed information on getting smooth edges after a laser cut. By going through this guide, you will explore how Baison‘s laser cutting machines offer a wide range of cuts with smooth edges.
The Basics of Laser Cutting
Laser cutting technology uses a laser beam and cuts through different materials with high precision and accuracy. The process of laser cutting starts by first designing the cut, and then the laser is guided through the material’s surface. The process generates heat that leads to melting the material, providing a precise and clean cut.
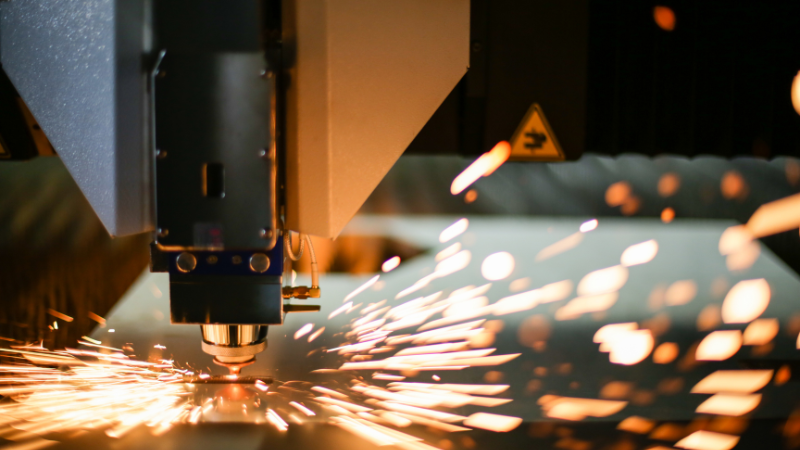
The application of laser cutting is seen in various industries. The main aim of lasers for the cuts is to achieve intricate designs with delicate materials, ensuring a smooth finish.
Multiple materials can be used for laser cutting: acrylic, plastics, wood, metals, paper, textiles, and many more fall in the list.
Do You Have Any Questions?
Let Us Solve Your Problem
The Importance of Smooth Laser Cut Edges
The significance of perfectly smooth edges cannot be disregarded, and it brings with itself various benefits; the significance of smooth edge quality is discussed below:
- The smooth edge of the laser cut provides an aesthetic beauty to the overall component; it ensures precision and accuracy in dimension.
- When the components are to be fixed with one another, the smooth cut edge allows for better compatibility and perfect fixation.
- Once the accurate cuts are achieved, the need for additional finishing processes is eliminated.
- Smooth edges even reduce the risk of injuries from the uneven cuts.

What is a Good Cutting Edge?
The criteria for assessing the edge quality comprises various aspects, and some of these are discussed below:
1. Smooth Surface
When the cut is of high quality, it is equipped with a smooth edge, and the surface is also even, which adds to the functionality and appearance of the component produced after the cut.
2. Precision and Accuracy
The cuts’ accuracy and dimension precision are critical and must be adhered to; there is a margin of minimal deviation in a perfectly cut piece.
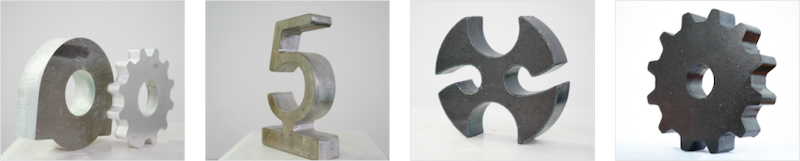
3. Smaller Heat Affected Zone
The heat-affected zone of a good cut is always smaller, which helps avoid unrequired alternations in the material property.
4. No Burrs and Aligned Angles
The absence of burrs and the alignment of the angle of the cut plays a huge role in ensuring that the cut is smooth and the edge is of good quality.
3 Factors Affecting Laser Cut Edges
Multiple factors play a significant role in the quality of the laser-cut edges, and some of these factors are discussed below:
1. Material Thickness
The quality of the cut edge depends on the material’s thickness because if the material’s thickness is higher, the prominence of the irregular lines is high. These irregularities comprise the area where the molten material meets the cooled material; hence, the quality is compromised.
The thicker material features more of these irregular lines than the thinner one; hence, the cut edge quality must be assessed at all times in the context of thickness.
2. Laser Power
Using high-power lasers can eliminate the appearance of the jagged edges from the thicker materials. It cuts the metal quickly due to its high speed, improving the edge quality.
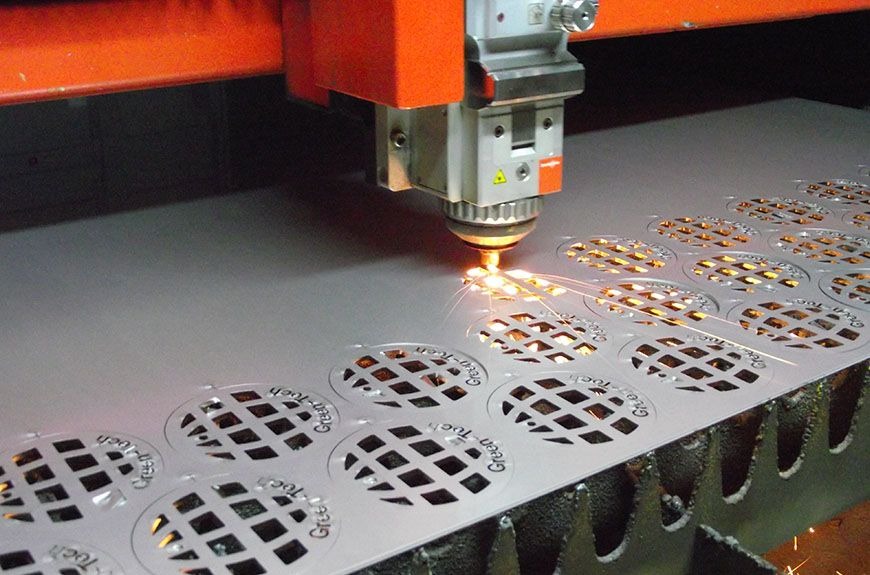
3. The technology of Laser
Laser technology for cutting the material is also vital in edge quality. Technological innovations have led to improvements in laser technologies like fiber laser, solid-state laser, and CO2 laser. Due to this innovation, the laser cuts improve, and the speed of the process ensures that the cuts are created with high pressure and helps to eliminate the chances of rough edges.
Do You Have Any Questions?
Let Us Solve Your Problem
How to Get Smoother Laser Cut Edges?
To get smoother laser-cut edges, there are various applicable methods, some of which are as follows:
1. Opting for Good Quality Material
When achieving good-quality edges for the components subjected to laser cutting, the chosen material is a matter to consider.
Materials manufacturers keep an eye on ensuring that laser-grade quality is attained in material preparation. Even if the sheets are thicker, the quality of the cut achieved is smooth due to the composition of the material being of the laser grade.
2. Opting for Good Quality Nozzles
As high-power laser machines have evolved to help cut thicker material, the cutting nozzles have also advanced. The use of coaxial flow nozzles, which help to cut steel with oxygen, has taken place. During this type of cut, the assist gas is very low; hence, a good-quality edge can be produced.
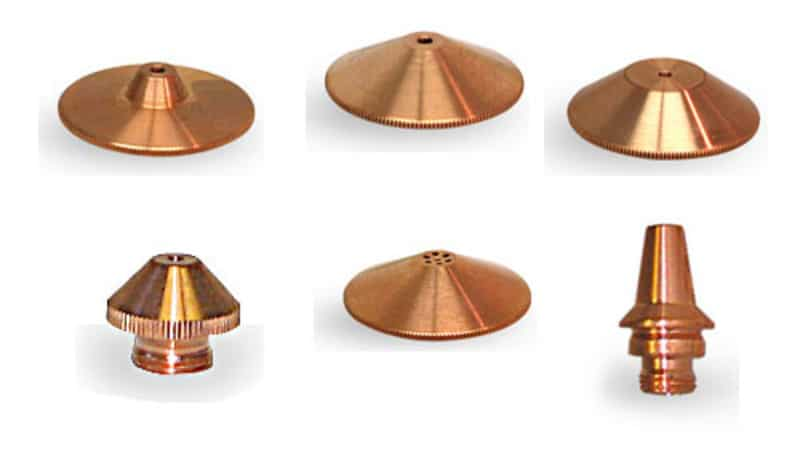
However after this technology evolved, nitrogen gas cutting attained popularity because the high power laser could cut thin materials at high speed. This leaves behind an oxide-free edge, which can be pointed right away due to the absence of oxygen.
Nitrogen, however, requires a very high gas flow and a large diameter nozzle to cut the material. To address these issues, nozzles were improved to create optimal flow dynamics.
3. Opting for Better Processing
Processing the laser cutting task to achieve neat and clean cuts is very important; however, this previously took a lot of work. Due to the processing issues, the edges of the components have uneven rough patches and very sharp corners.
Due to the uneven edges, there is a need for further processing to get rid of it; however, to eliminate this, more efficient processing methods were discovered. The controllers have automated everything in today’s time. They help calculate the power, duty, and frequency to ramp down based on the laser head‘s speed.
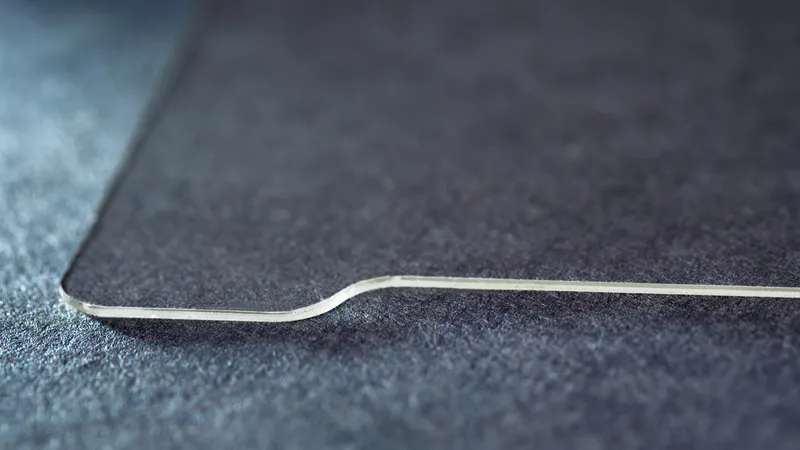
4. Opting for Improved Beam Parameters
The quality of the beam may help to offer better edge quality as well after a laser cut. The evolution of CO2 lasers has also changed the game of solid-state and fiber lasers. The innovations in the fiber laser cutting process have made it possible to cut thick steel with the finest quality, and hence, the fabricators can purchase a full range of material types and thicknesses, and there is no need for a lens change as well.
The edge quality offered by CO2 lasers in the fiber laser machine is accomplished by using a special lens that helps to change the kerf width and allows more assist gas to be incorporated in the cut.
Secondary Treatment of Laser Cut Edges
Although various technologies are in place nowadays that have made laser cutting machines capable of offering smooth edges, further finishing may be needed in some cases. The secondary treatments that may be posted in such cases are discussed below:
- In cases where rough and uneven edges are to be converted into polished edges, sanding and grinding can be opted to attain a smooth finish, usually observed in electronic or medical equipment.
- Where there are burrs and raised edges, the process of deburring proves to be helpful; burr removal can be attained through abrasive tumbling, manual deburring, or some special tools that can be used for burr removal.
- Some processing may be needed to get rid of the trash and slag through milling and machining, and this is usually carried out in cases where thicker materials are used.
- Abrasive cleaning processes, primarily used in medical device manufacturing, may remove the residues on the cut edges.
- In the case of laser cutting acrylic, the unfinished or rough edges may be fixed through flame polishing. The edge in question is subjected to open fire that melts the material and smoothens the flame-polished edge.
Do You Have Any Questions?
Let Us Solve Your Problem
FAQs
1. Can the condition of the laser cutter affect edge quality?
Absolutely. Regular maintenance, such as cleaning lenses and mirrors and ensuring proper calibration, is crucial for achieving consistent, smooth cuts.
2. Is it more expensive to achieve smoother edges?
Achieving smoother edges might require using higher-quality materials or spending more time on post-processing, which can increase costs. However, efficient machine setup and operation can help balance cost and quality.
3. How is the burr in laser-cut edges reduced?
Ans. The gas purity can be improved, or the gas pressure may be adjusted. For example, in the case of stainless steel laser cutting, a nitrogen case is recommended to be used for laser cutting so that the burrs can be reduced.
Conclusion
The guide above would have provided sufficient information about the laser-cut edges and how you can smoothen them differently. To achieve clean edges, the need to invest in a good quality, high-power laser cutting machine is critical, and for that, choosing a leading manufacturer is always very important.
Experience Smooth Precision with Baison Laser Cutting Machine!
Baison Laser understands the importance of having neat and clean edges after laser cutting. Hence, we incorporate advanced technologies in our laser cutting machine. It helps you achieve the finest cuts. Contact our team today if you need to invest in a good-quality laser-cutting machine.