What Is Portable Welding?
Portable welding is an advanced approach that employs compact and mobile welding machines. Welders can conveniently transport portable welding equipment anywhere, making them a crucial asset for the welding industry. A portable welding machine commonly employs electricity or a battery-operated power supply. However, some portable welding machines also use generators or invert technology as a power source.
This versatile technique offers the same quality and precision as traditional welding units. Moreover, its portability gives it an edge over conventional techniques, as welders can use portable welding equipment at difficult-to-access spots.
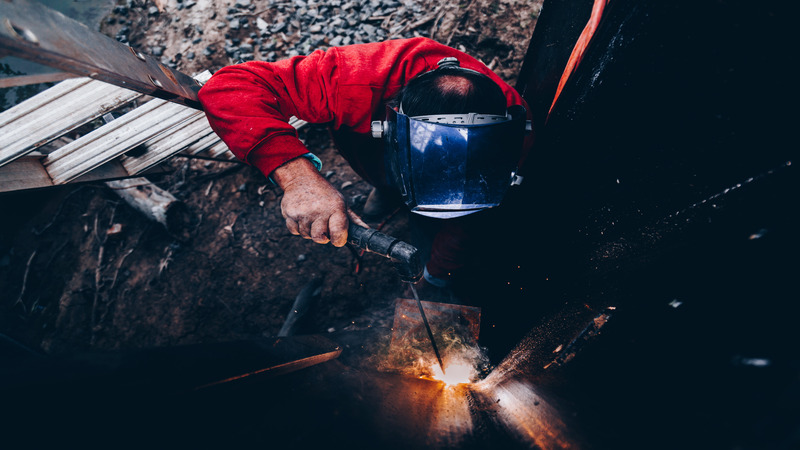
Origin and Rise of Portable Welding
Welding is not a new concept; it has been used for a long time. However, portable welding came up in the 20th century. The rising demand for greater accessibility and enhanced flexibility led to the development of portable welding.
The introduction of electricity in the 19th century started a revolution in every industry, including welding. Charles L. Coffin patented the arc welding method by utilizing electricity. This invention laid the foundation for portable welding.
The rise of battery and inverter technology boost the idea of portability. This technology minimizes the size and weight of the machines, making them more accessible. The popularity of portable welding machines increased in the mid-20th century. It was used at construction sites and industrial manufacturing in its early development. However, with advancement, this approach has become a primary tool for repairs and maintenance.
Today, portable welding has become a key element of the metalwork industry. Portable welding machines are available on online sites as well as in local stores. You can purchase one for your portable welding projects.
The rising demand for welding projects is escalating the need for welders. According to Austin Community College, the American Welding Society has warned about the shortage of welding experts in the future. This increasing demand for welders has made welding an excellent career choice.

What Are the Types of Portable Welding?
Portable welding is a vast technique. Here are some commonly used portable welding methods in the welding industry:
1 – Shielded Metal Arc Welding (SMAW)
Shielded Metal Arc Welding (SMAW) employs manual welding. It uses a consumable electrode coated in flux to create an arc between the electrode and the workpiece. The arc produces substantial heat energy. When the temperature approaches 6500°F, the electrode and workpiece melt, causing them to fuse.
As the electrode melts, the flux coating disintegrates and releases gases. These released gases create a shield to prevent the weld pool from various gases in the surroundings. They also protect the weld pool from contaminants, providing you with a clean weld.
2 – Metal Inert Gas (MIG) Welding
MIG is another popular portable welding technique. It employs a wire electrode for welding. The electrode is automatically fed through a welding gun. The electric current between the wire electrode and the metal piece generates an arc. This arc melts the wire and fuses it to the metal, creating a weld.
In this technique, a welding gun generates shielding gases. Commonly, MIG welding releases a mixture of argon and carbon dioxide to protect the weld from contaminants. Their compact and lightweight structure makes them ideal for repairs and manufacturing.
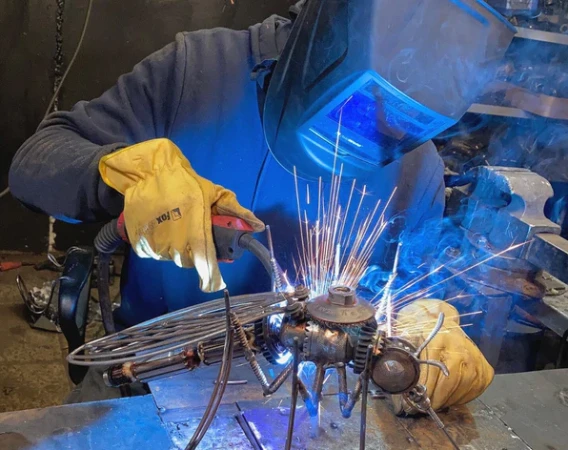
Why not learn the difference between MIG welding and laser welding?
3 – Tungsten Inert Gas (TIG) Welding
TIG is a superior welding technique that offers exceptional control and greater precision. Like laser welding, TIG doesn’t produce any smoke or spatter. It uses a non-consumable tungsten electrode for welding arc generation. An inert gas, like argon, protects the tungsten electrode and the melted weld. The gas also assists in cooling the weld.
Unlike SMAW and MIG, this technique is complex. It requires skills and practice to create a perfect weld. TIG welders have to hold the torch in one hand and manually feed the filler metal with the other one to create a weld.
Check out our article on TIG welding and laser welding to learn more.
4 – Flux-Cored Arc Welding (FCAW)
FCAW is a semi-automated process. Like MIG, it also utilizes a flux-cored arc welding approach. However, it uses a consumable tubular wire electrode with constant voltage. The flux generates a shielding gas as well as a deoxidizer. Portable welders don’t have to use additional shielding gases. This feature makes it an excellent portable shielding technique.
It is widely used due to its high weld-metal deposition rates. It is a perfect technique for welding thick materials and heavy equipment repair.
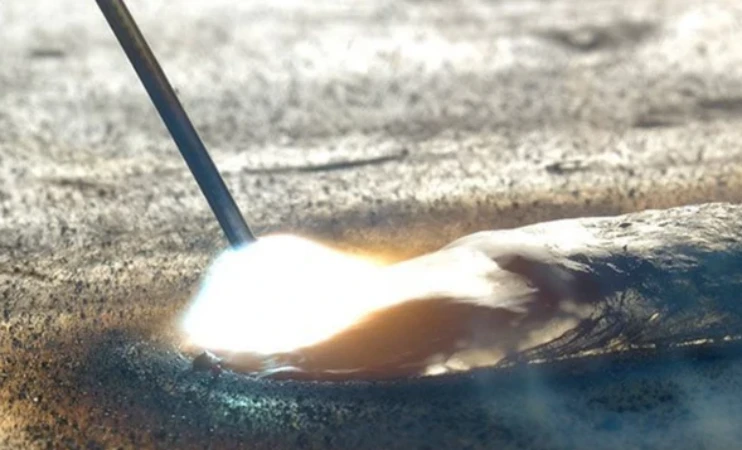
5 – Fiber Laser Welding
Fiber laser welding is a modern welding technique that utilizes a high-powered fiber laser beam. Fiber optics in this machine amplifies the light beam and transforms it into a high-energy laser. The intense, concentrated beam melts the materials, which, on cooling, creates a strong weld.
This technique is free of smoke, splatter, and fumes. In addition, it has low distortion rates, making it a suitable technique for jewelry repair and other intricate tasks.
6 – Portable Friction Welding
It is another advanced welding technique. It employs heat, pressure, and rotational force to create seamless joins. It creates friction heat between two workpieces or metal surfaces. They are rubbed until they melt. On melting, they are pressed to create a strong weld without any additional material. It’s an efficient approach as you don’t need any filler or shielding gas.
Applications of Portable Welding
Portable welding is widely used in several industries. According to the research of the Bureau of Industry and Security, in the year 2000, welding-related professions employed more than one-half million people in the US. Here are some common applications of portable welding:
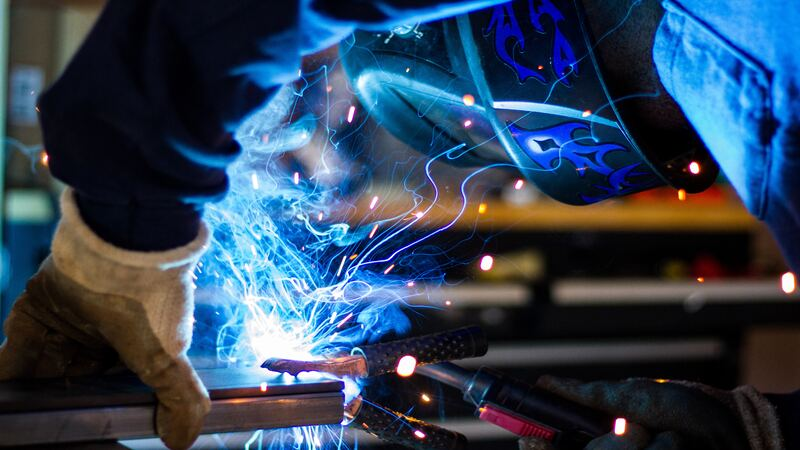
- Portable welding has become crucial for the construction industry. This technique makes it accessible to fabricate and repair various structural components. Whether it’s a bridge or a residential building, portable welding equipment enables welders to join various components and ensure structural integrity.
- The intricate design of automobiles also utilizes portable welding for repair purposes. Fixing cracks and breaks in vehicle parts requires precise work. Portable welding covers such repairs and offers accurate welding with minimal damage to the component.
- Shipbuilding and repair rely on this approach. Repairing the complicated structures of a ship is quite challenging without a portable welding machine.
- This technique is a life-saver under disastrous conditions. Recovering power lines, bridges, and other infrastructure without heavy machinery is almost impossible. However, the portable welding process can quickly repair damages and enable you to restore the system.
- In addition, artists also utilize this innovative technique. Using a portable welding machine, you can create delicate metalwork, sculptures, and artwork. You can unleash your creativity and push the boundaries with this approach.
Click here to see the top 10 industries where handheld laser welders, one of the portable welding devices, are used most.

Benefits of Portable Welding for Seamless Joins
Portable welding is an effective way to join different materials and ensure a strong bond. Here are some benefits of portable welding technology:
1. Versatility
A prominent advantage of utilizing portable welding is its versatility. Portable welding can fuse various metals, including steel, aluminum, brass, and cast iron. You can use various materials to create intricate designs and shapes. Moreover, some portable welding machines are developed to perform various welding techniques, like Submerged Arc Welding (SAW), MIG (Metal Inert Gas), TIG (Tungsten Inert Gas), and Stick welding.
2. Conveniently Manoeuvre
You can easily take it to diverse locations without any hassle and weld various materials. Portable welding machines are not heavy, and you can comfortably carry them. This aspect enables you to use them for repair processes in remote locations, confined spots, and high-rise buildings.
Moreover, this feature of portable welding enables you to work in tight spaces and industrial applications. You can easily take portable welding machines anywhere and accomplish your task.
3. Energy-Efficient
While considering the usefulness of portable welding machines, we often neglect their energy efficiency. Traditional welding machines are not only heavy but also energy-intensive. They require notable energy to operate. In contrast, portable welding machines are designed to function by consuming less power.
Their advanced power management systems optimize energy and reduce electricity bills. Moreover, portable welding machines come with inverter technology, which converts power into AC current. It enables the machine to utilize less energy, saving energy.
4. Safety
Portable welding machines not only make your tasks easier but also offer more safety than conventional welding. They have built-in thermal overload protection to avoid overheating. Portable welding machines shut down when it exceeds a certain temperature.
Incorporating advanced IGBT (Insulated Gate Bipolar Transistor) technology allows you to use the machine. This safety feature prevents electric shocks and arcing. Its robust casing feature also protects you from sparks, slag, and spatter, which are common side effects of welding. Moreover, portable welding machines come with easy-to-read digital displays and adjustable settings. It enables you to adjust the voltage and feed speed according to your requirements.
5. Enhanced Precision
Portable welding is renowned for its exceptional precision. Traditional welding machines lack advanced features. Controlling their temperature is quite challenging as they don’t come with any adjustable setting feature. In contrast, portable welding machines have advanced control systems to precisely set the required temperature. You can also control the depth and width of welding beads. It ensures accuracy in intricate designs and seamless joins.
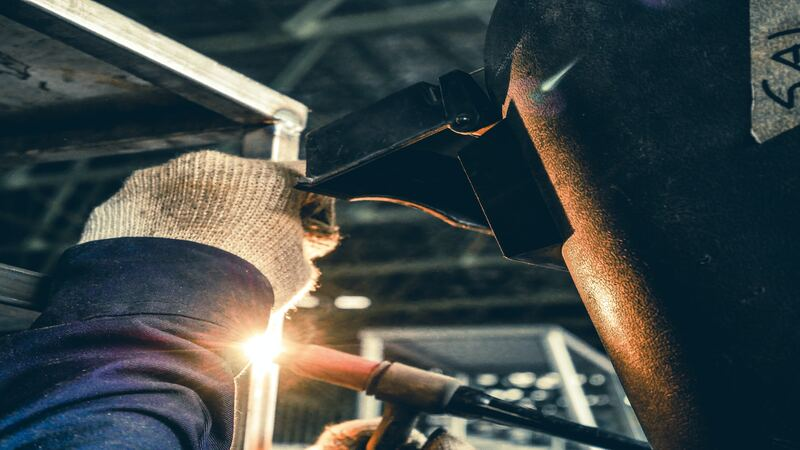
The latest portable welding machines have pulse welding and waveform control technology. Pulse welding enables you to maintain the stability of the arc. It leads to perfect welds. Waveform control technology allows you to adjust the welding parameters. It helps you provide precise results even in complex shapes.
6. Cost-Effectiveness
Another significant advantage of using portable welding is cost-effectiveness. Setting up a bulky conventional welding machine in a workshop or construction site is a costly pursuit. In addition, various associated costs, like maintenance, shipping, and installation, increase the overall cost. On the other hand, portable machines don’t need extra space and effort. This practical alternative saves your transport and storage costs.
(Click to find out how much a laser welding machine costs.)
You can keep your portable welding machine in a small bag and carry it wherever you need it. According to a report by Wright State University, a DC-DC power converter design offers a cost-effective portable welder system.
Moreover, portable welding machines are not complicated. They come with a detailed manual that lets you understand how it works. You can learn to use it and weld metal surfaces. In this way, you can cut off labor costs. According to USA Today, the welding jobs are increasing due to a shortage of welders. It makes portable welding services an excellent career choice.
7. Increased Durability
Durability is a prominent feature of any machine. No matter how attractive a machine is, you will have to replace it quickly if it’s not durable. Portable welding machines have stronger welds than conventional machines. Portable welding machines are manufactured with great attention and care. They provide quality results even in rough conditions. They are designed to withstand heavy usage and maintain the quality of welds.
Equipped with innovative features and premium materials, portable welding machines can withstand high pressure and harsh weather. With a longer lifespan, you can use the same product for years. It also makes it a good choice as shifting to the new product after a few months is not necessary.
8. Increased Productivity
Portable welding machines significantly boost productivity due to their design and functionality. The accessibility of moving them transportation time saves you from hauling them to and from the location of your project. Unlike traditional welding machines, which may require a significant time for setup, you can operate the portable welding machine in a few minutes.
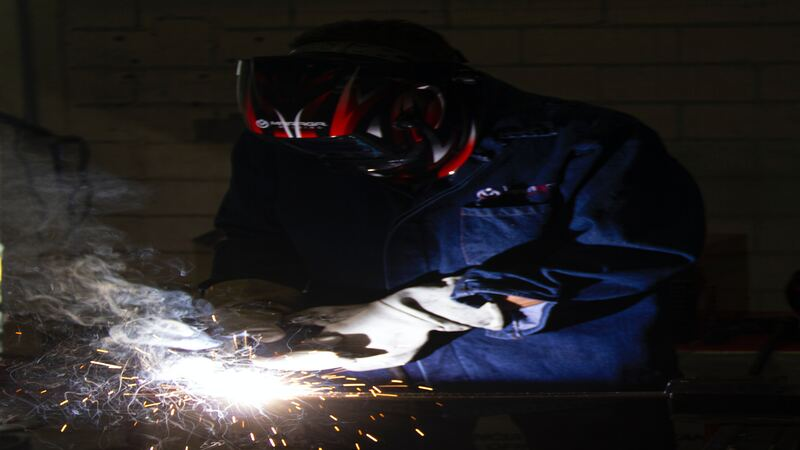
Novice welders can learn to operate them without much experience. Within a few days, you can learn to use it efficiently. Thus, it increases the efficiency of workers. Moreover, portable welding machines can quickly heat up and cool down times, significantly reducing the time spent waiting for the machine to reach the appropriate temperature. This efficiency saves time and energy, making it a cost-effective alternative.
Conclusion
Portable welding is transforming welding tasks. Advanced technology revolutionizes complicated welding procedures, making them straightforward with easy-to-use portable welding machines.
These machines ensure quick and precise results with effective usage and greater durability. With continuous innovation, portable welding is becoming more and more advanced. So, whether you are starting a small project for artwork or working on a large-scale industrial task, portable welding can assist you in getting seamless joins.
Baison Offers the Best Portable Welding Machines!
If you are searching for a reliable and cost-effective portable welding solution, then don’t worry. Baison Laser can provide you with the best laser welding. It offers you premium-quality laser machines to make your projects hassle-free. The specialist of Baison Laser get to you in a short time. So, request an instant quote and get your durable portable laser welding machine.