This article summarizes the key things about handheld laser welding machines, including their features, operation mode, advantages and disadvantages, and major applications in various settings.
We also answer some of the most common FAQs of handheld laser welding machines. So, let’s get started.
What Are Handheld Welding Machines?
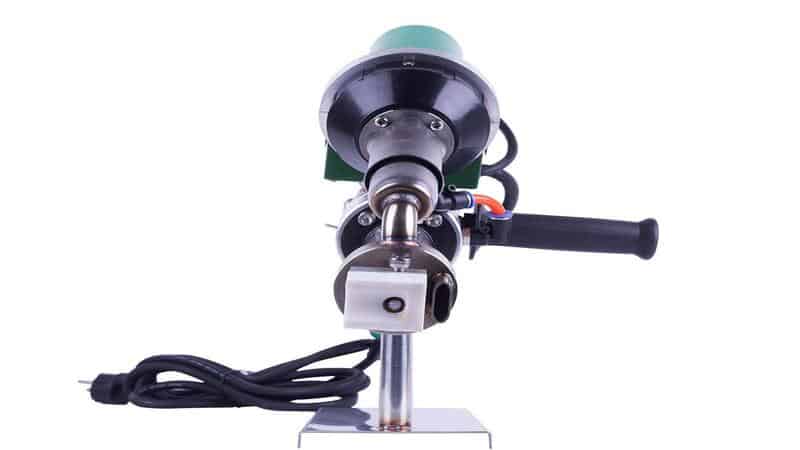
Handheld welding offers convenience, speed, and efficiency in one place. It is a form of non-contact welding that delivers results across multiple industries.
The emergence of this welding technique has simplified the complex and cumbersome traditional methods of welding stainless steel, kitchenware, shelves, and ovens.
Handheld laser welding isn’t an entirely new concept, even though it only became popular about a decade ago.
It is loved because of its precision, bringing many advantages over traditional welding techniques.
Operating Mode: How do Handheld Welding Machines Work?
Handheld welding machines use a laser and a modulated or continuous emission to complete the welding process.
During operation, radiation from the laser engine is transmitted to the welding gun through an optical fiber. With the welding gun focused on the targeted weld area, the laser beam melts the surrounding materials, joining the two parts as it cools.
Features of Handheld Welding Machines
Handheld laser systems comprise the laser engine, welding gun, and optical fiber. The welding gun has a trigger button, a temperature monitor, and a spray head. These components work together to give a streamlined, efficient, and convenient welding process without subsequent weld polishing or grinding.
10 Applications of Handheld Welding Machines in Various Industries
Here are the top 10 applications of handheld laser welding machines in various industries;
1. Kitchen Ware
Welding kitchenware comes with an increased need for aesthetic appeal and tightness. This is only guaranteed by handheld laser welding machines, providing beautiful welds and effective sealing performance post-welding, which every homeowner appreciates.
2. Metal Cabinet
Handheld laser systems weld metal sheets for making computer cases, communication, and electrical cabinets. With the never-ending demand for aesthetics, many people turn to handheld laser welding for its precision, beautiful welds, and other technical benefits over traditional welding.
3. Door and Window Guardrails
Most door and window guardrails are made of aluminum alloy and stainless steel, which makes handheld welding the method of choice for fusing these parts in case of damage.
Laser welding gives beautiful, firm, and easy-to-polish door and window guardrails. As a non-contact method, it can be done outdoors or onsite, making it a convenient method for installing new guardrails.
4. Automotive and Aviation Industries
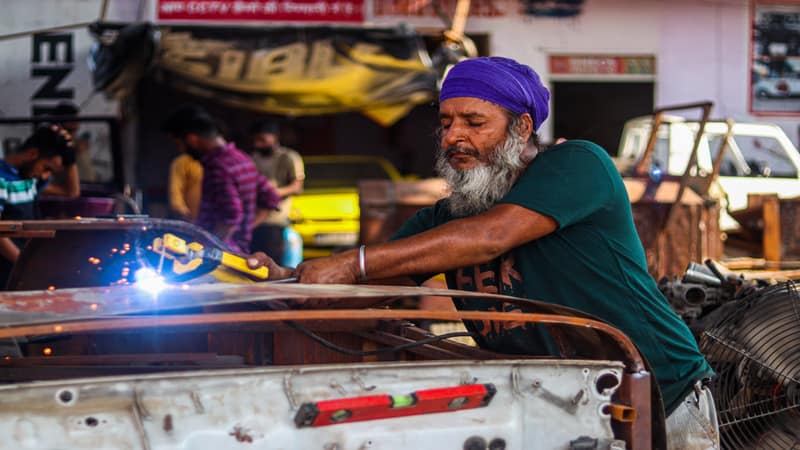
Automobile brands use handheld welding because of its efficiency, speed, and convenience.
For example, the vehicle doors and hoods are all made of thin metal sheets, which benefit from edge welding using a laser beam in case of damage. This gives it better strength and a more beautiful appearance than traditional welding.
In the aviation industry, laser welding is the preferred method for joining different components made of stainless steel, such as exhaust systems, landing gear, and jet engine parts.
5. Metal Furniture
Metallic furniture has become increasingly popular in recent years, with the constant need for ergonomic chairs and desks.
Different parts can be customized with a focused laser beam to suit the design requirements, making it the method of choice for welding these parts.
The welding seam coming from handheld laser welding machines satisfies the varied needs of the consumers, including flexibility, shape, design, and appearance.
6. Stainless Steel Products
There are countless stainless steel products in the market.
That means these parts are always going to break at some point. Again, handheld laser welding fits the bill because of the beautiful welds it creates, its flexibility, and its convenience.
7. Medical and Dental Industries
As a non-contact method, handheld laser welding ensures consistent welding and overall cleanliness of medical devices that must always remain sterile.
The small and precise laser beam can fuse thin materials such as components of surgical instruments. The aesthetic component of handheld laser welding also comes into play, with the welded parts always appealing to the end user.
8. Precision Parts Welding
Handheld welding is accurate and generates minimal heat, making it the best method for fusing thin and delicate parts.
9. Welding Areas with Limited Access
Handheld laser welding machines are non-contact and the most suitable for welding the hard-to-access parts that conventional welding techniques won’t reach.
10. Tool Manufacturing
The versatility of handheld laser welding makes it the method of choice in tool manufacturing. The laser beam is used to join different parts in this field to achieve the desired design requirements.
Advantages of Handheld Laser Welding
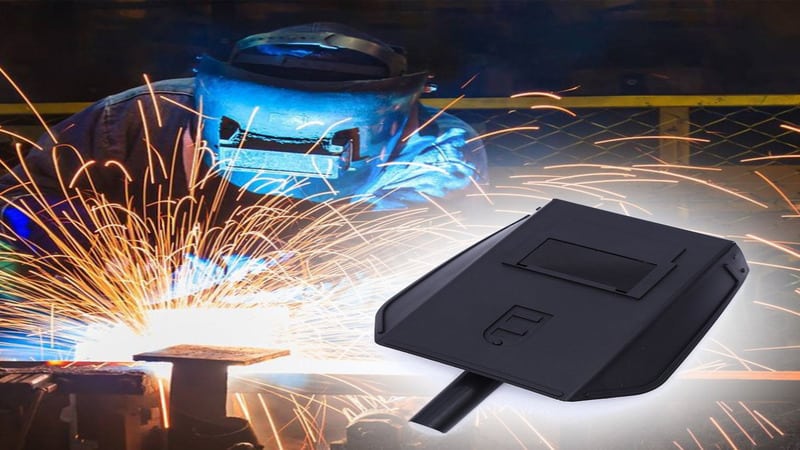
Handheld laser welding presents many advantages over traditional welding techniques, including the following;
Speed
Handheld laser welding machines can fuse thin materials up to 5 times faster than traditional welding. The quick turnaround increases productivity.
Convenience and Flexibility
Handheld laser welding machines have movable wheels, ensuring easy transportation and adjustment when necessary. It is flexible enough to be used in multiple scenarios.
Good Welding Effect
Handheld laser welding yields better weld results than traditional welding, thanks to its high energy density. The welding seam strength penetrates the base metal, which would be impossible to achieve with conventional welding machines.
No Polishing/Grinding
The welding point must be polished using traditional welding techniques to create a smooth surface.
Handheld welding eliminates such needs with its laser component. These machines create beautiful welds without defects or scars, saving the clients from follow-up grinding or polishing.
Supports Different Welding Methods
Handheld laser welding can be done at any angle, including vertical welding, butt welding, flat fillet welding, overlap welding, and external and internal wire-filler welding. This gives it a wide range of applications in various industries.
Increased Welding Range
Handheld welding machines have a 10mm optical fiber, giving them a wider range of welding than traditional techniques. The machines are perfect for long-distance welding, eliminate the workbench space issue, and can be used outdoors.
Accuracy
Laser precision allows for easy conjoining of the welded parts under low heat and with no defects.
Versatility
Handheld laser machines can weld anything from metal sheets to precious jewelry, aluminum, and copper. It’s even thought that these machines can weld the traditionally hard-to-weld ceramics.
Reduced Heat Impact on the Surrounding Surfaces
Both traditional and handheld laser welding rely on heat to join the welded components. Unfortunately, conventional welding methods transmit this heat to the surrounding surfaces, leading to stress and bending of the welded parts.
On the other hand, laser welding focuses the heat on the seam without damaging the surrounding surfaces or creating defects.
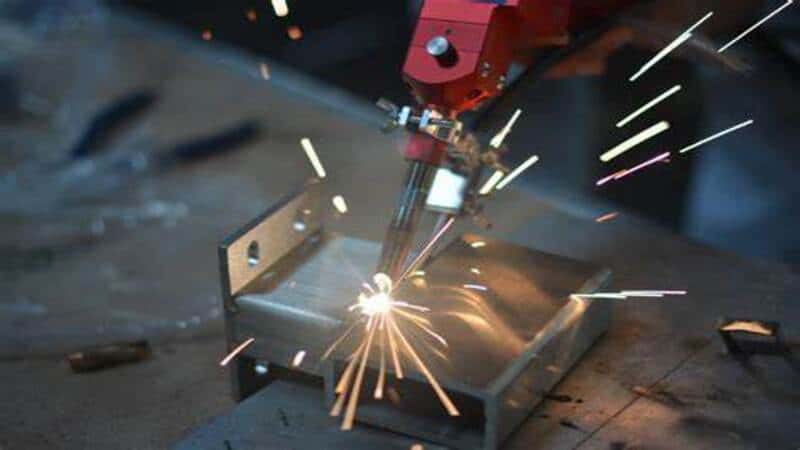
Limitations of Handheld Welding
Here are a few disadvantages of handheld laser welding machines;
Inconsistent Quality
The laser beam must be positioned correctly at the welding point, which requires high-level skill and concentration. New welders may struggle to achieve consistent beam size, strength, and penetration, resulting in inconsistent quality and welding defects.
Limited Accessibility
Handheld welding may not be the best method for welding hard-to-reach surfaces, limiting its effectiveness in certain settings. Welders may turn to traditional welding techniques to reach inaccessible areas.
Limited Joint Thickness
Welders have limited joint thickness to weld using the laser beam. They may need alternative welding techniques if the penetration thickness exceeds 19mm.
Safety
Potential health risks are associated with handheld laser welding, especially if the beam comes into contact with the body or eyes. The high heat poses a significant risk if the welder ignores the standard safety requirements.
FAQs
Are Handheld Laser Machines Easy to Operate?
Yes. Handheld laser welding machines have simple controls for setting the desired parameters and completing the welding process instantly. You can learn everything quickly and get better results.
Which Metal Materials can be laser welded?
As the perfect alternative to traditional welding, handheld laser welding can fuse a wide range of materials, including chemically active metals, refractory metals, magnesium, nickel, titanium, copper, aluminum, carbon steel, low alloy steel, alloy steel, and structural steel.
Also, handheld laser welding allows the joining of similar materials, such as aluminum-aluminum.
Must I be a Laser Expert to Operate a Handheld Laser Welding Machine?
The simple answer is no.
Handheld laser welding machines have simple controls for easy operation by anyone. You only need the right material type and thickness before setting the controls to complete the welding process.
Are the Welds Strong?
We already know that handheld laser welding gives aesthetically satisfying results. But how strong are the welds?
The welded materials have no cracking, porosity, incomplete fusion, or other defects. Besides, handheld laser welding machines provide no underfill, with strong enough welds, just like you’d expect from conventional welding techniques.
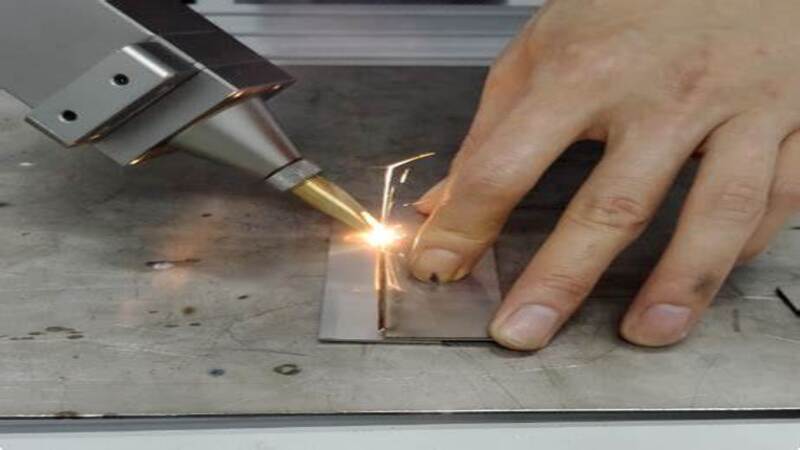
Are There Any Safety Guidelines Around Handheld Laser Welding Machines?
Handheld laser welding machines are powerful equipment that must be handled carefully throughout welding. The laser beams are invisible but can be dangerous when they come into contact with the body or eyes.
Fortunately, these machines have fully integrated safety features to protect users from harmful beams. Welders can take extra caution by adopting the standard safety requirements such as:
- Performing the welding tasks within a designated, laser-controlled area.
- Putting on non-inflammable clothes and welding clothes.
- Wearing other protective gear, such as a welding helmet and safety goggles.
Another important safety tip is reading the instructions before using a handheld laser welding machine.
Should You Consider Handheld Laser Welding Machines?
Anybody can use handheld welding machines to streamline the naturally cumbersome and complex welding process.
Handheld laser welding is fast, easy to learn, and efficient, making it the method of choice for many industries.
You will undoubtedly benefit from this form of welding if you want to stay competitive in the manufacturing industry.
Implementing this welding method lowers operating costs by simplifying the welding process while improving the weld quality. Ultimately, handheld laser welding gives you the shortest route to success and profitability, even without experience using these machines.
Conclusion
Handheld laser welding machines have distinct advantages over traditional welding, including fast processing speed, convenience, less heat, and versatility.
Laser precision provides aesthetically appealing results, eliminating the need to polish or grind the welds. This explains the many applications of handheld welding machines in various industries.
Companies can use handheld laser welding machines to reduce operating costs and achieve better results. Baison can help you choose the best fiber laser system for your company.
So contact us, and we will provide a durable, cost-effective, and reliable laser product built from the heart to satisfy your needs.