Knowing different Laser Cleaning methods and procedures is critical if you want the cleaning process to be effective, efficient, and economical.
Our easy-to-follow guide will help you choose the most suitable laser cleaning system for your project by enabling you to communicate your needs with the machine manufacturers. Here is the list of laser cleaning methods you need to know.
Basics of Laser Cleaning
Light Amplification by Stimulated Emission of Radiation (laser) is a monochromatic, high-intensity, and uni-directional light beam with vast applications in our daily lives. One such example is the revolutionary laser cleaning technology that has made the industrial cleaning process fast, efficient, profitable, and, most importantly, eco-friendly.
The basic mechanism of laser cleaning is that high-temperature laser light burns (laser ablation) and evaporates the contaminants layer, leaving a smooth surface finish and preparing the material for further industrial processes.
Laser cleaning is the best alternative to older chemical and abrasive cleaning technology because it’s cost-effective, sustainable, and less labor-intensive.
10 Types of Laser Cleaning Methods for Effective Cleaning
There are various laser cleaning methods, and it all boils down to how you categorize the features of a laser cleaning machine. So, we’ve divided the laser cleaning methods into easy-to-understand categories. It will help you better communicate with the manufacturer at the time of purchase.
Methods Based on Cleaning Processes
1. Dry Laser Cleaning
Dry laser cleaning is the most basic laser cleaning process in which a high-intensity beam heats the unwanted layer on the surface of a material and vaporizes it. The vaporized contaminants are then blown away or extracted using exhaust machines. Commonly used for laser rust removal.
Pros
- Simple and effective
- Easy to operate
Cons
- Struggles in case of deep cleaning
2. Wet Laser Cleaning
In the Wet Laser Cleaning method, also called “Steam Cleaning”, the liquid film is applied on the surface of the uncleaned material. The laser beam heats the liquid, vaporizing it and creating an intense shockwave that detaches the contaminant layer from the surface. Also, the laser beam itself doesn’t come in contact with the material.
However, caution is needed to prevent the liquid layer from reacting with the contaminated layer, which limits its application.
Pros
- Effective for deep cleaning at a micro level
- Efficient and sustainable
Cons
- Limited application
If you want to know the difference between these two methods in more detail, here is an article that takes removing contaminants from artwork as an example.
3. Shock Laser Cleaning
In the shock laser process, the high-powered laser beam breaks down the air near the surface, turning it into plasma. This plasma generates an intense shockwave, disrupting the unwanted layer on the surface or substrate and effectively removing it. The shockwave penetrates much deeper than dry cleaning, making it a highly effective laser cleaning method.
Pros
- Effective for deep cleaning at a nano level
- High cleaning speed
- Lower ablation threshold fluence
Cons
- High cost
Methods Based on Laser Modes
4. Continuous Laser Cleaning
Continuous Wave (CW) lasers emit high-intensity laser beams of constant output over a specific interval. CW laser cleaners are suitable for heavy-duty cleaning, like removing rust from large stainless steel cylinders. Typically, they have a higher output of order 2000 W and more. Because of the intense power, they can sometimes create unwanted heat-affected zones, potentially damaging the surface material.
Pros
- Highly effective
- Heavy duty
Cons
- Intense heat may damage sensitive material.
5. Pulsed Laser Cleaning
In pulsed laser mode, the machine emits laser pulses at regular intervals. There is an intense peak and then a pause, also known as “Dwell Time”, and the cycle repeats. Pulsed laser cleaning is better suited for sensitive materials than CW lasers, as it creates minimum heat-affected zones.
For instance, using a 100 W hand-held pulsed laser is easier and less likely to cause damage when removing mold from a tire than a CW 1000 W laser cleaner. The pulsed laser beam can hit a peak output of 10,000 W, and its pulsating nature prevents the material from overheating.
Pros
- Extremely versatile
- Highly effective
- Risk-Free
Cons
Not much
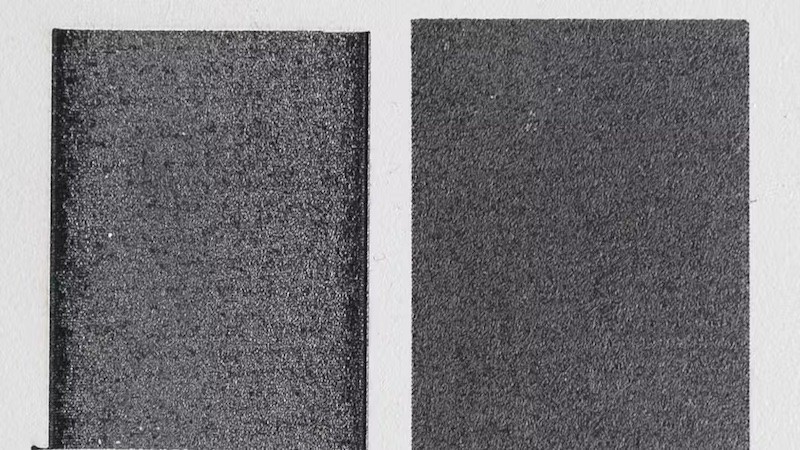
Learn about the cleaning performance using CW and pulsed fiber lasers from this article.
Methods Based on Laser Source
6. Fiber Lasers
Fiber laser technology is the most advanced laser source technology in modern times. You can say it’s an upgrade to typical Nd: YAG lasers. In fiber lasers, optical fibers are used as the gain medium doped with rare earth metals.
In simpler words, using optical fibers makes laser travel much more efficient, resulting in better overall performance. Fiber laser cleaners are available in both continuous wave and pulse laser modes. Also, it can be used on a wide range of materials, effectively zapping away oxidizing layers, paint, corrosion, rust, and oils.
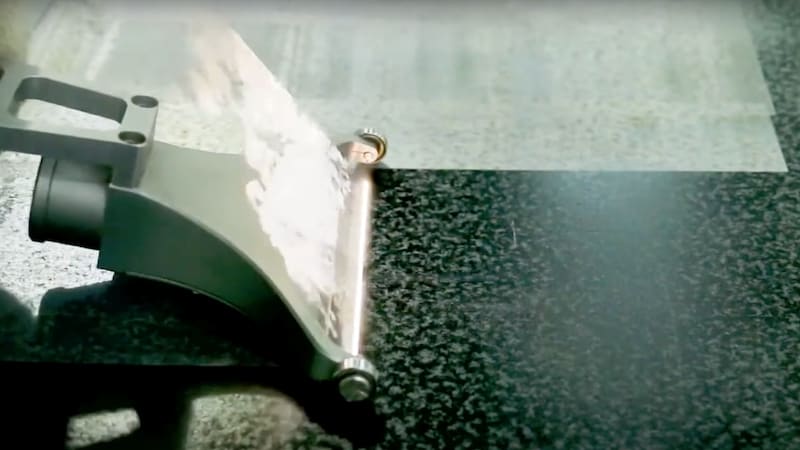
Pros
- Modern laser treatment
- Extremely efficient
- Good for metal surface cleaning
Cons
Not much
7. CO2 Laser Cleaners
In CO2 laser cleaning machines, the CW laser beam is generated when a high-intensity current passes through a glass chamber full of carbon dioxide gas, exciting the atoms and producing infrared rays, which are then focused using mirrors. They are good for removing paints, oil, and corrosion from materials like ceramics and polymers.
Pros
- Older but established technology
- Good for non-metals and polymers
Cons
- Not suitable for metal surface cleaning
8. Nd: YAG Lasers
Nd: YAG laser, otherwise known as solid-state laser cleaners, uses a crystal gain medium to generate laser beams. They are available in both CW and pulse laser modes, which makes them highly versatile. Q Switched Nd: YAG cleaners can remove more material per pulse than their counterparts.
Pros
- Most Effective
- Extremely Reliable
Cons
- Less controllability
9. High Power Diode Laser
A high-power diode laser originates from a p-n junction diode, which lights up when it gets hit by a high voltage. Such focused laser beams are easy to use and offer better controllability.
Pros
- Small beam size results in better control
Cons
- Clean limited materials
Methods Based on Techniques
10. Perpendicular and Angular Laser Cleaning
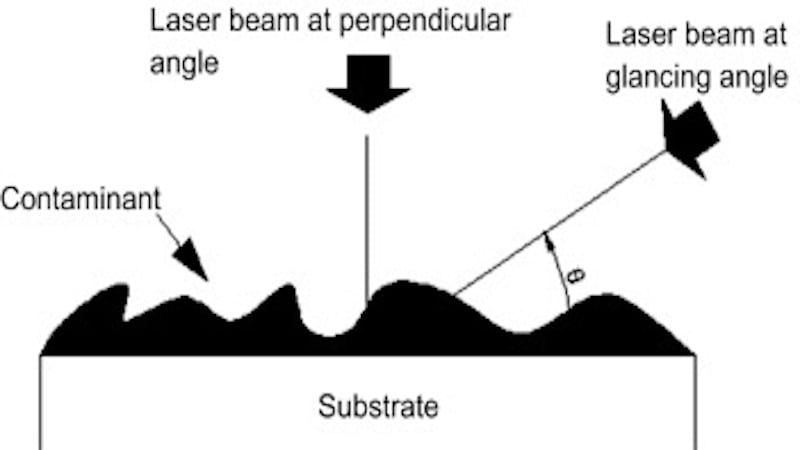
Conventional laser cleaning is done by directing the laser beam at 90 degrees to the surface. This method is good and does produce results.
However, applying the laser at a slight glancing angle results in higher cleaning speed and less risk of damage to the material. Angular laser cleaning depends on adjusting the glancing angle of the incident beam, which requires skills and training.
Do You Have Any Questions?
Let Us Solve Your Problem
Which Laser Cleaning Method to Choose?
Each Laser cleaning method we’ve discussed so far has some unique aspects that make it effective in certain scenarios. Consider the following factors to choose the perfect laser cleaning system for your project.
Factors Affecting the Laser Cleaning Performance
Understanding which aspects of laser cleaning performance are affected will help in the selection.
1. Type of Contaminant Layer and the Material
The two most deciding factors during the purchase are the type of unwanted layer and the material you want it to be removed from. Rust, corrosion, mold, paints, and grease are common contaminants. Even the color of the paint can significantly affect the machine’s performance. An ideal laser cleaner is one that effectively removes the dirt layer without harming the material underneath.
2. Effect on Substrate
The substrate is the outermost surface of any material on which the dirt layer forms. Laser cleaning has the potential to cause damage, like cracking or cratering. The damage to surface topology can be on a microscopic scale, so you should effectively communicate this with the machine manufacturer.
3. Distance of Laser Gun from the Source
Portable or hand-held laser machines are quite convenient. However, make sure the area that needs to be cleaned is not too far from the source, as the beam intensity is lost when traveling long distances. Which means you might end up with lower power at the point of action than the source. Thankfully, Fiber laser cleaners are more efficient in this regard and offer more flexibility.
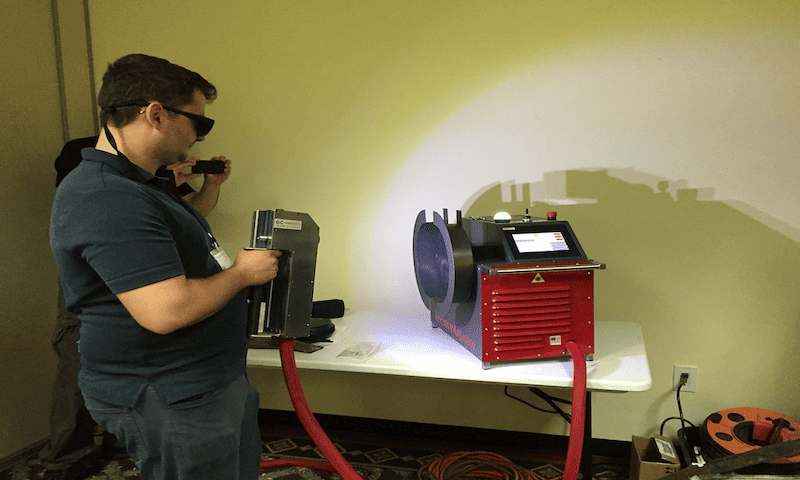
Things to Consider While Buying the Laser Cleaning Machine
After knowing the influencing factors, the configuration of the cleaning machine is now considered from these aspects.
1. Laser Type and Power
Higher-wattage lasers are more powerful. However, care must be taken while adjusting the beam intensity setting to avoid any material damage. Laser cleaning machines are typically rated in Watts (W) or Killo Watts (KW). Secondly, choosing the right laser type is critical for project efficiency. We’ve delved into this in detail in the previous section.
2. Exhaust System
Laser cleaning in close space requires a proper exhaust system to extract fumes. A well-ventilated place is also recommended.
3. Scanning System
Some advanced laser cleaning systems have automated scanners that can detect contaminants and redirect lasers to them, making cleaning extremely efficient and time-saving.
4. Cost Analysis
Laser cleaning setups are relatively costly, so you must make a clear financial feasibility report before investing in these setups. Some industries leverage laser cleaners for finishing and polishing materials to boost profitability.
Do You Have Any Questions?
Let Us Solve Your Problem
Comparison Between Different Laser Cleaning Machines
Earlier, we discussed different laser cleaning technologies and methods. Now, let’s dive into a brief comparison of various laser cleaning machines available in the market. Some of these machines may have similar sources but differ in wavelength, mode, or approaches, creating distinctions in their cleaning applications.
Laser Cleaner | Wavelength | Remove and Cleans |
ArF excimer | 193 nm | Particles composed of SiO2, along with polymers. |
KrF excimer | 248 nm | Polymer materials, ceramic coating, Al2O3, SiO2 particles, and oil and grease residues. |
XeCl | 308 nm | Silicon, aluminum oxide, and iron oxide. |
XeF excimer | 351 nm | Aluminum oxide, copper oxide |
Q-switched Nd: YAG | 355 nm | Impurities, metal particles, corrosion |
Nanosecond fiber laser Nd: YAG | 532 nm | Rust, oil, grease, paint, metallic powders, oxides, and stains. |
Nanosecond fiber laser Nd: YAG | 1.06 μm | Preparing the surface, removing surface layers, oxides, stains, pollutants, rust, metallic powders, oil, and grease. |
Nanosecond fiber laser Nd: YAG | 9.6 μm | Removing surface layers, eliminating oil and grease, and addressing oxides. |
TEA CO2 | 10.6 μm | Aluminum oxide, silicon carbide (SiC), dirt, resin, iron, silicon, particles, oil and grease. |
Advantages of Laser Cleaning Technology
Haven’t made up your mind yet? Here, we’ve listed some of the advantages laser cleaning can bring to your project.
1 – Eco-friendly Technology
The use of laser doesn’t involve any chemical residue or toxic exhaust, which can harm the environment. It’s a completely safe and eco-friendly process. Traditional methods like dry ice blasting or sand blasting create high levels of dust and noise, which is inefficient and creates a rough surface finish. It’s also harmful to the worker. On the contrary, laser cleaning creates a smooth finish, which makes welding and other joining processes much more effective.
2 – Precision Cleaning
Laser cleaning is extremely precise and can access hard-to-reach areas. Selective cleaning makes it a desired method for cleaning sensitive equipment.
3 – No Consumables
Traditional cleaning methods either require chemicals or abrasive material, which is consumed during the process. Making the cleaning process slower and more expensive. Plus, you’ll have to maintain the stock of consumables for uninterrupted operation, which is just an added hassle. Laser cleaning is ready to go at any time without any prior arrangement.
4 – High Cleaning Speed
Whether you use hand-held laser cleaners or industrial-grade large laser cleaning machines, both are, on average, faster than traditional cleaning methods.
5 – Material Versatility
Since there are many different types of laser technology, they can be easily customized for a wide range of materials. Moreover, the operator has the option to dial in laser cleaning parameters in real time, making it adapt to any specific scenarios.
Disadvantages of Laser Cleaning Technology
Even though laser cleaning is becoming the go-to technology for cleaning in the industry, it does have some caveats. Here are a few things to look out for.
1 – Expert Training Required
The working staff must be trained in laser safety and operation before working for protection against laser radiation. This may become costly, especially for smaller-scale industries. However, the learning curve of laser cleaning isn’t steep, making it an easy-to-adapt technology.
2 – Higher Setup Cost
The upfront cost of laser cleaning machines is higher, but thanks to their efficient working, the cost is covered within a year.
Industrial Applications of Laser Cleaning Technology
Laser cleaners are seen in almost every industry these days. But the unique characteristics of Laser make it most suitable for these industrial applications.
1 – Artifact Preservation
Laser cleaning work is best for historical stone or marble artifacts, which are sensitive to harsh chemicals and abrasive cleaning.
2 – Electronics
Semiconductors, PCBs, and other electronics require selective and delicate cleaning, which is best done by a Laser system.
3 – Automotive Industry
Lasers are well-suited to remove the phosphate layer on car components, which is applied for corrosion resistance. It’s also used to remove mold and debris from tire rubber.
4 – Aerospace and Maritime Industry
The use of harsh cleaning chemicals and abrasive materials is restricted in the aerospace and maritime industry for safety reasons, so lasers play a pivotal role in removing rust, algae, paint, and oil from the parts.
Do You Have Any Questions?
Let Us Solve Your Problem
FAQs
1. What Are The Different Types Of Laser Cleaning Machines?
Laser cleaning machines come in various types, each suited for a specific industrial application. Here are some common machines you’ll find in the market.
- Handheld Laser Cleaners
- Manually Loaded Laser Cleaning Workstations
- Conveyor Laser Cleaners
- Robot Laser Cleaning Machine
2. What Materials Can Be Laser Cleaned?
Laser cleaners are compatible with almost all the materials available. You just have to communicate with the manufacturer and get the right type suited for your project. Some common materials cleaned include.
- Metals Surfaces
- Non-metals
- Glass
- Composites
- Ceramics
- Stone
- Concrete
3. Which Laser Method Is Best?
Dry laser cleaning is used in most industries and is generally the most effective. Wet and Shock laser cleaning is generally good for removing layers at the micro or nano level.
The field of Laser cleaning is vast, and many cleaning methods and procedures have been devised by researchers for effective cleaning. To find the best laser system, discuss all the available options with your manufacturer effectively.
4. What Power Is Needed For A Laser Cleaner?
Laser cleaners vary from 100 W to 2000 W power rating, and each comes with unique features. The selection of the right laser power in machines generally depends on your project requirements.
Conclusion
We’ve covered in detail all the basic Laser cleaning methods commonly used in industries. You can compare the pros and cons of each method of cleaning and try to come up with the most feasible solution for your project. Thankfully, there’s active research going on in the field of laser cleaning, making the new machines target multiple contaminants at once.
Precision and Power – Baison Laser, Your Industrial Cleaning Solution!
If you’re on the hunt for a high-tech and premium laser cleaning machine, you’re already in the right place. Here at Baison Laser, we’ve been delivering cutting-edge and affordable industrial laser cleaning machines to clients worldwide for over two decades. We specialize in fiber laser cutting and CO2 laser cutting, laser welding, laser cleaning, and marking machines.
Our industry-leading experts design customized products tailored for your project’s success. Not sure what to expect? Grab a FREE Application Evaluation and Sample Proofing to kickstart your project. Contact Us Now!