The laser-cutting technology has catapulted specialty industries to greater heights with its revolutionary efficiency in cutting quality and manufacturing. However, just like any technology, there will always be inevitable issues to encounter.
In this article, we are going to delve into the possible laser-cutting problems and bottlenecks you might come across during your operations and further discuss the causes and solutions. Learn more about laser cutting woes and how to avoid bad cuts to ensure that your materials won’t be wasted and boost your productivity.
What Is Laser Cutting?
Before we proceed with preventative measures and solutions for bad laser cutting, let us first define what laser cutting is.
Although self-explanatory, laser cutting uses a laser beam to cut through a variety of materials, such as metal sheets, pipes, and others. It doesn’t just involve cutting. Laser-cutting machines are also used for engraving, etching, and other industrial and artistic applications.

The Process of Laser Cutting
Laser cutters function mainly from thermal processing. It uses a laser-focused beam that melts the material in a localized area, comparable to the principle of a magnifying glass under sunlight that can burn the grass. In laser cutting machines, an air assist ejects the melted parts to reveal a clean and precise cut.
It requires less contact as opposed to conventional cutting, stamping, and punching processes.
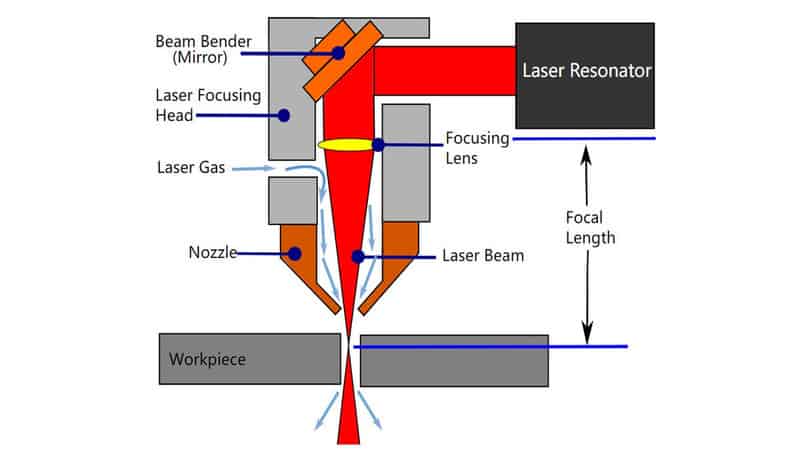
What Metal Materials Can a Laser Cutting Machine Cut?
A laser cutter can cut through several metal materials, which include:
Stainless Steel: This metal is among the most popular types in manufacturing with its higher oxidation and heat-resistant properties. A laser cutter has to have a power of at least 4000 watts to cut through stainless steel.
Aluminum: This high-strength alloy can be cut with a laser cutting machine. It is an extremely versatile material that can be formed, melted, extruded, or cast into a variety of shapes and other fabrication techniques.
Carbon Steel: One of the most widely used metal materials for different specialty industries, carbon steel is highly durable and has the ability to be heat treated.
Copper: It is non-magnetic because of its non-ferrous properties, making it ideal for various manufacturing applications. This metal type is extensively used in different industries because of its ability to conduct electricity and heat extremely well.
Brass: This copper and zinc combination alloy metal is a popular material too. It can be easily managed with a machine designed for the cutting task, and laser cutters can do it. This material is also perfect for engraving.
Titanium: Popular among luxury watches, jewelry, aerospace manufacturing, and other meticulous and exquisite industrial applications, titanium is a very durable metal material that can be cut by a laser cutting machine.
Nickel Alloys: They are frequently used in manufacturing chemical reactors, storage tanks, water heaters, vessels, and even in the aerospace sector for their corrosion-resistant properties, adhesion, and hardness.
Inconel: Despite its high-temp strength (considered one of the strongest alloys on earth), an Inconel can also be cut by a high-power laser cutting machine.

What Are the Common Laser Cutting Problems You Might Encounter?
Here are 5 of the most common problems with the laser cutting process:
I. Material Warping
The unintentional twisting, bending, and misshaping of your materials as you cut through them, are quite common when laser cutting, especially if you don’t know how to avoid them.
There are multiple reasons a metal material you are cutting could warp. Fundamentally, it occurs when there are unbalanced internal stresses. Any imbalance will contribute to the stress of the entire material, and that’s when it will start to bend.
The flat parts will be held as that because of compression. However, the other parts of the material may start to go uneven if internal stress becomes imbalanced again. The more you introduce new stresses to the equilibrium, the more it will warp.
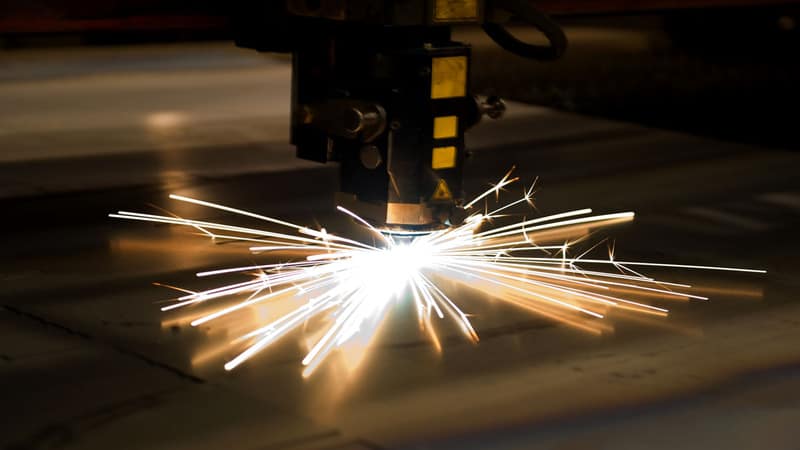
Material-wise, stainless steel is more susceptible to warping than aluminum and carbon steel. You can also rely on composite materials to be more resistant.
Some warped materials can be bent back into shape, but it can be a lot of work. There is also a big chance that your machine may get damaged.
II. Material Thickness Limitations
It is understandable that thicker materials are harder to cut than thinner ones. A lot of factors need to be considered in this situation too, such as heat conductivity, surface reflection, alloy type, laser focus, and so on.
For example, carbon steel of about 0.4 inches in thickness may encounter difficulty when laser cut, especially if there is not enough power.
III. Presence of Burrs
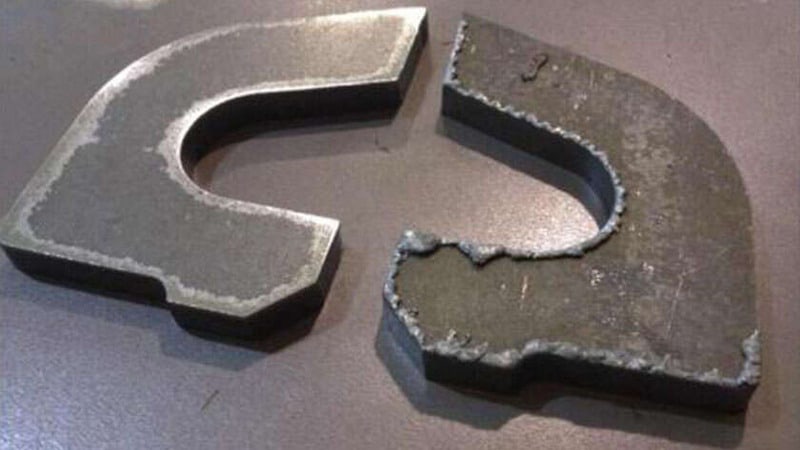
What are these burrs? They are the rough or uneven edges that sometimes happen to our materials when we laser cut. These burrs cause unwanted results, and further consequences on the finished parts can occur if you will not address them sooner. The good thing is these burrs are completely avoidable.
IV. Small Holes
Another common problem in laser cutting is charring, and forming small holes can be a big challenge, especially if you aim for an intricate design requiring perfect precision.
This happens when deformations are affected by small diameters and part thickness, leading to high energy concentration until the material becomes charred.
V. Reflective Materials
Too much reflection can directly affect the overall quality of the laser processing, the precision, and worse, damage the laser optics.
However, fiber laser cutting technology can handle reflective surfaces such as gold, bronze, copper, and brass.
What Are the Causes of Bad Cuts?
There are a lot of factors that contribute to bad cuts in the laser cutting process. You have to pay close attention to the key elements that can affect the finished product for your business.
We are all aware of how much a bad cut can cost us (operation and time-wise), so it is only logical to know what causes these mishaps to better address the next steps you need to take.
I. Incorrect Laser Power Settings
One of the many causes of bad cuts is improper laser power settings. You cannot just cut through a thick material like carbon steel without adjusting the power.
You will get poor-quality cuts if the laser power setting is too low when working with thick metals. Most of the time, it will never cut through molten material.
II. Improper Laser Beam Focus
Another cause of bad cuts is incorrect laser beam focus. You will often end up having uneven cuts, incomplete design, or precision cutting errors when the focus is not set properly.
Using scrap metal to create sample cuts would be a great way to prevent wasting materials.
A simple principle to consider when focusing a lens is the thicker the material, the higher the focus position must be.
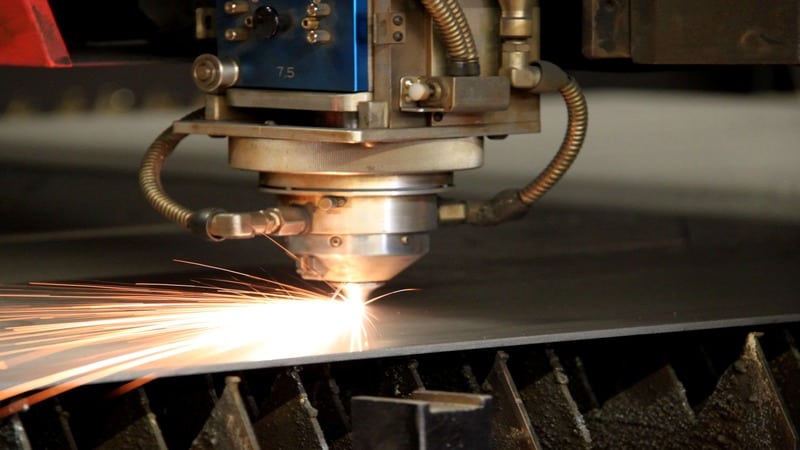
III. Material Properties
While all laser cutters generally work with metal materials, some properties can affect the quality of laser cutting. These include the reflective properties and thickness of the metal material.
IV. Incorrect Cutting Speed
Just like laser power, the cutting speed setting must be adjusted accordingly. Cooperating alongside laser power for better cutting control is a very important parameter.
The surface may not be completely cut through if it is too fast.
If it is too slow, the area of focus can be overheated, which can disrupt the edge quality and precision of your desired shape.
V. Insufficient Auxiliary Gas Pressure
Not enough air pressure to remove the melted parts can also affect the quality of your cuts. Clogged cuts are never going to give you a satisfying final output.

7 Surefire Tips to Prevent Bad Cuts in Laser Cutting
Initial cutting attempts can be immensely challenging, especially if you are new to laser-cutting machines, not to mention the time and money it will cost you and your business.
This is why we have listed top tips for preventing bad cuts and ensuring you stay on top of your operations smoothly.
Get the most out of your laser cutting system with these surefire tips.
1. Set the Correct Laser Power Setting
Laser power and speed settings are crucial to the success and quality of your cutting process. First, to determine the right setting, you have to consider the material you are cutting and the wattage of your laser cutting machine.
Greater power means stronger force, and this is often used for thicker materials.
2. Adjusting Cutting Parameters
To prevent edge burrs and ensure that your desired shape is cut precisely without errors, you need to carefully check the parameters of your laser cutter.
The operator must have a deep knowledge and understanding of how the laser beam interacts with the workpiece and the gas assist for an accurate cut.
These parameters include the cutting speed, laser output power, focus position, auxiliary power supply gas pressure, and nozzle distance.
3. Maintain Proper Focus
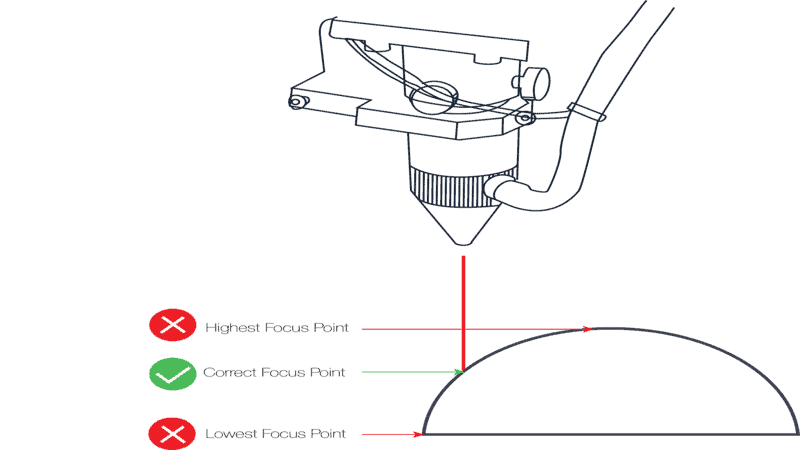
Most of the time, uneven, incomplete, and rough-cut designs are caused by improper laser beam focus.
You must adjust the laser beam focus to prevent bad cuts and avoid wasting materials.
4. Keep Lenses Clean
At all times, you need to maintain the cleanliness of your lenses. They can get easily dirty with all their work and the materials they come across whenever you operate them for cutting or engraving.
Do not touch the lens’s optical surface by hand to prevent scratching and corrosion.
If dust or oil is present on the mirror surface, just use a clean lens tissue to gently wipe it.
Never use water or detergent for cleaning the lens and never leave the lens in a humid and dark environment because this will lead to its deterioration.
Clean your laser optics with lens tissue with some acetone on the paper. Do it gently and repeat as needed until your laser source and optics are clean.
Lenses are usually already dirty after 8 hours of continuous and solid use.
5. Choose the Right Material
Is your machine apt for cutting reflective materials? Does it have enough power to deal with thicker materials? Determining the capability of your machine is the first step to choosing the right material.
A fiber laser cutter can cut through gold, silver, brass, bronze, and copper, but some CO2 laser cutting machines may have difficulty with them.
6. Regular Machine Maintenance
Never disregard maintenance. It is among the crucial aspects you have to consider on a regular basis to prevent your system from declining and to make sure that your cuts are always top-quality.
7. Proper Operator Training
The biggest way to prevent bad cuts is to undergo proper operator training. The lack of this can easily result in material waste, delays, and even physical danger.
At Baison, one of the leading providers of high-quality laser cutting machines, provide comprehensive operator training to equip clients with a deeper understanding of their cutters.
Things You Need to Consider Before Buying a Laser Cutter
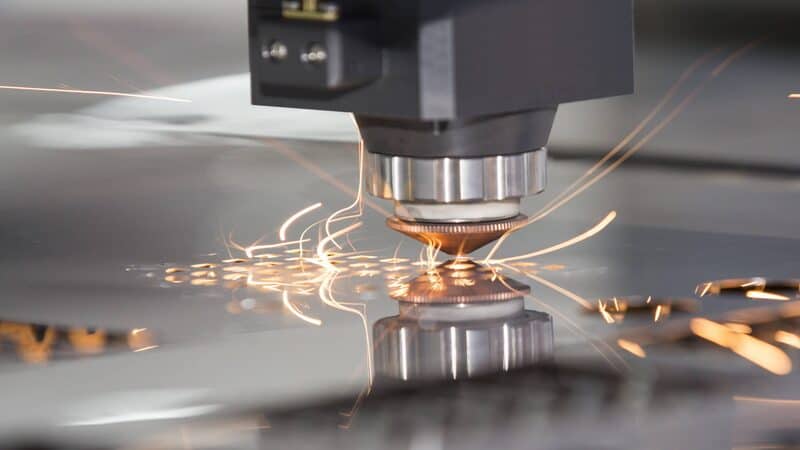
Staying relevant in your specialty industry requires continuous innovation, and tapping into the power of laser technology can take your business to new heights. You need to consider many things when buying the perfect laser cutter that can meet the demands of your business.
I. Material Preference
What materials do your business consume? Determining your material preference is the first step to finding the appropriate laser-cutting machine for your organization. The thickness of the material also plays a pivotal role in your search. The thicker and the harder the material is, the more power you need.
II. Workspace
You need to consider your workspace too. Is it big enough to accommodate a laser-cutting machine? Choose the machine that can meet your project requirements and is compatible with your workspace.
III. Production Capacity
How much work or laser-cutting output do you need daily or weekly? Make sure that the machine you want to buy is strong enough and can do the work.
IV. Budget
Consider your budget too. After determining your project requirements, setting a budget for your laser cutting machine acquisition is time. Following your budget will allow you to efficiently manage your finances without going overboard.

Conclusion
Equipping yourself with a deep understanding of how laser cutting machines work and taking the time to learn the roundabouts of your chosen laser machine can save you time and money whilst increasing the efficiency of your manufacturing operations.
You should pay close attention to adjusting the laser beam and focus parameters, considering the material thickness and properties, maintaining your machine regularly, undergoing extensive operator training, and keeping your laser cutter in tip-top shape to prevent unwanted laser cutting woes.
Discover the Perfect Solution for Your Business with Baison!
Suppose you are looking for a reliable and professional supplier of laser-cutting equipment. In that case, Baison is one of the leading providers of laser technology. Our laser cutting machines with cutting edge technology allow you to avoid many cutting problems. If you have any questions, don’t hesitate to contact us!