Are you in the manufacturing industry and struggling with the choices of laser and ultrasonic cutting? We’ll help you choose the right machine for your project by exploring their differences, pros and cons, and industrial applications of each.
According to a report by Global Market Insights, the laser cutters market size was valued at over $5.5 billion in 2022. The report shows that this is expected to grow by a CAGR of more than 7.5 percent.
What is Laser Cutting?
Laser cutting is a processing technology that uses a laser beam to vaporize the workpiece, leaving a cut edge. Although it’s typically an industrial manufacturing application, laser cutting is now used in many areas, including schools and creative industries.
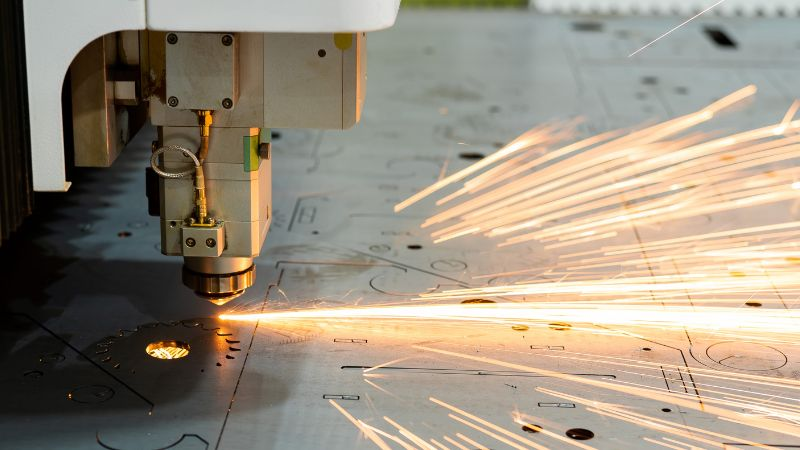
Laser Cutting Working Principle
Laser cutting uses a high-power laser beam directed through fiber optics and computer numeric control (CNC) to direct the laser beam to the workpiece.
The process uses a motion control system to follow the G-code of the vector design that you intend to cut. The focused high-power density laser beam vaporizes, burns, melts, or is blown away by a jet of gas, resulting in a high-quality, finished surface.
What is Ultrasonic Cutting?
Ultrasonic cutting is a technique that uses cutting tools vibrating at high frequencies to cut through various materials. Applying ultrasonic vibration to the cutting knife creates a cutting effect with minimal friction.
With minimal friction, ultrasonic cutting can cut many types of materials. When used in food processing, it can cleanly cut foodstuffs with vegetables and meat without smearing. The minimal resistance also makes ultrasonic technology the ideal cutting process for small slices.
The Working Principle of Ultrasonic cutting
Like ultrasonic welding, ultrasonic cutting uses a sonotrode, an oscillating tool that creates ultrasonic vibrations and applies this vibrational energy to the workpiece. In cutting processing, this vibrating tool is called a cutting sonotrode.
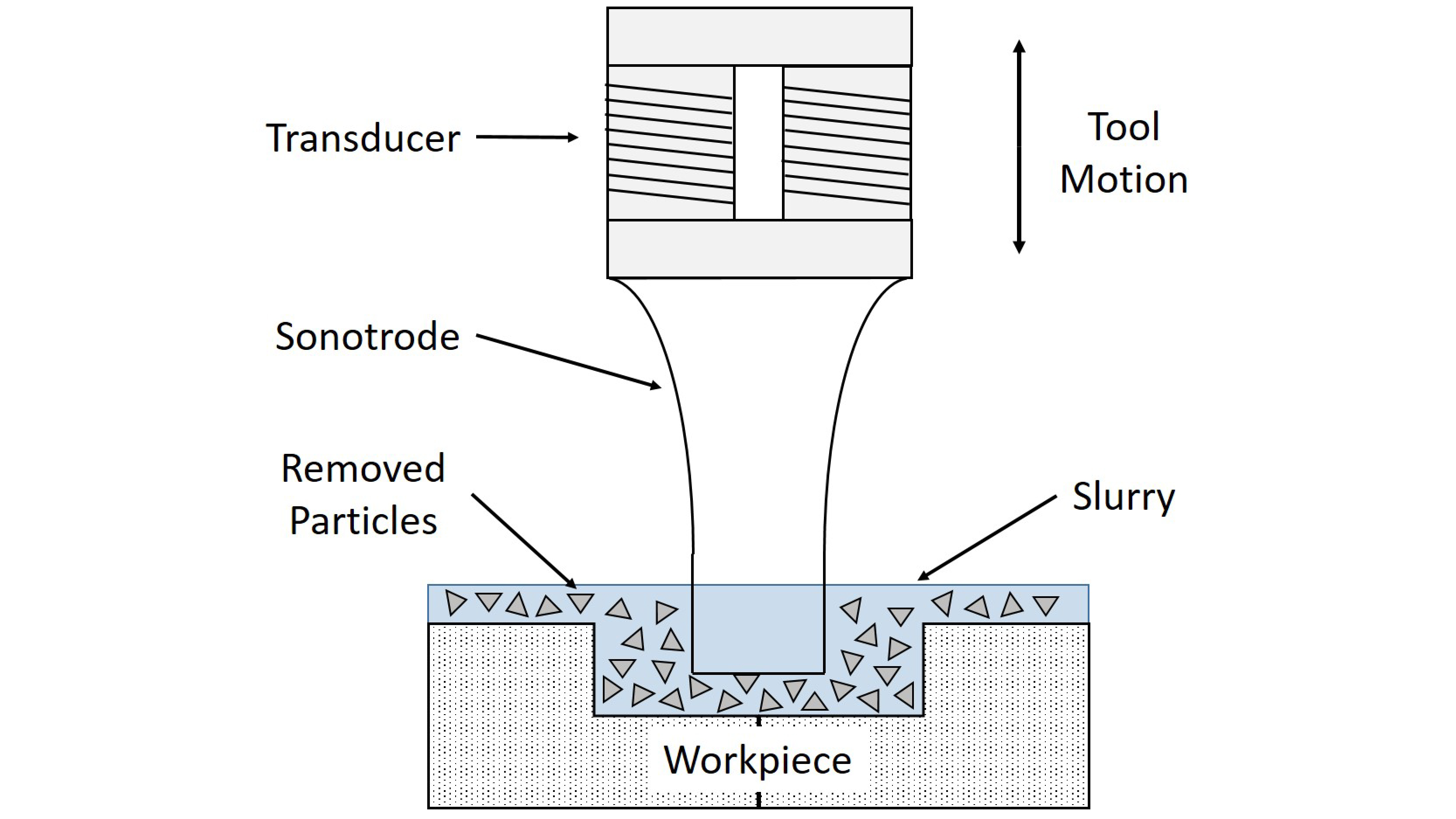
In ultrasonic cutting, the blade glides through the workpiece almost effortlessly, thanks to the oscillating motion created by the vibrations. The ultrasonic cutting knife faces minimal resistance from the material, hence producing a clean cut edge without deformation or smudge.
The energy transmitted by the ultrasound is the only energy that melts the workpiece. This is a huge advantage to food processing factories as this technology can produce clean cuts to pressure and temperature-sensitive products.
Advantages of Laser Cutting
Laser cutting has multiple advantages and disadvantages. Here are some of the advantages.
1. High Degree of Precision
A laser cutting machine produces a narrow laser beam that can produce an extremely high-quality, smooth cut. The precision with which the optics can be moved or controlled is exceptional. The process combines laser and computer technology, allowing you to cut the exact design you have on your computer.
Laser machining allows the execution of complex designs and shapes, even on the most difficult and fragile workpieces.
2. Fast Processing Speed
While choosing a traditional cutting method may seem advantageous cost-wise, a laser cutting device makes up for this with its extremely fast processing speed. While both a laser cutter and a saw are made for cutting materials, their cutting speeds are quite different. An oxygen-assisted laser cutter with a 12kW motor can cut a 4mm metal sheet ten times faster than a bandsaw machine.
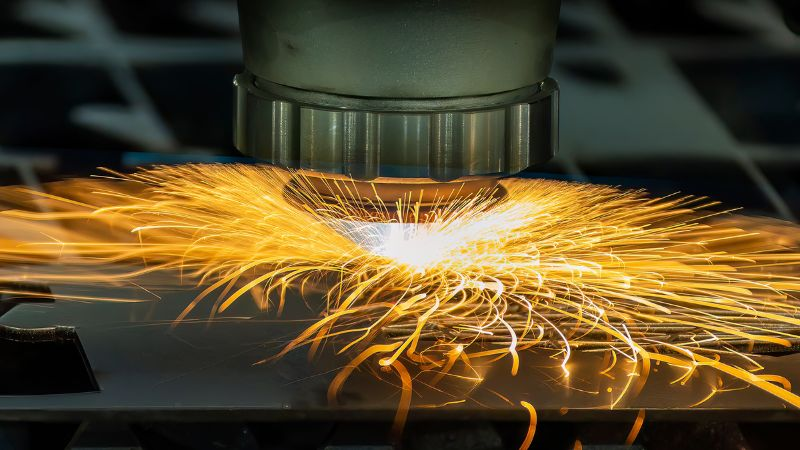
3. Do Not Contaminate the Cut Material
If you have used any traditional cutting method, you know how hectic it is to degrease cut edges after cutting. The machine’s lubricant and coolant contaminate the cut edges, giving you the extra work of cleaning them up.
Cutting methods that use contact cutting tools leave carbide granules on the cut edges, which is hazardous to the quality of your finished material. Laser processing involves energy and gases. As a result, it poses a minimum risk of contaminating your excellently cut workpiece.
4. Compatible with Various Materials
The laser cutting technology is quite flexible and can be used on various materials in different industries. You can use laser processing to cut stainless steel, acrylic and other polymer materials, mild steel, and titanium, among other materials. This technique gets more versatile as technology grows. For instance, you can cut carbon fiber-reinforced composites with double-frequency laser cutters.
5. Automation
Though you require an operator with the right expertise to get the best from laser cutting, the technology has a high degree of automation. This reduces the workforce required to operate it, thus reducing its operation cost.
6. Wide Range of Industrial Applications
We will share more of this as we discuss the application industries of laser cutting.
Disadvantages of Laser Cutting
Here are a few disadvantages of laser cutting technology.
1. High Investment Cost
Although laser cutting has found its way into nearly every industry, it is still a huge challenge for many small businesses due to its high upfront costs. For instance, most top-rated laser cutters cost between $1,500 and $6,000. The prices go as high as $250,000 for higher power machines. This is a big disadvantage to a small business enterprise that does not have access to funds.
2. Limitations of Material Thickness
While laser cutting is the most accurate thermal cutting method, it is not ideal for thick metal sheets compared to its counterparts. The thickest metal sheet you can laser cut depends on the power rating of your machine. That said, the most powerful laser cutters draw the line at 20mm.
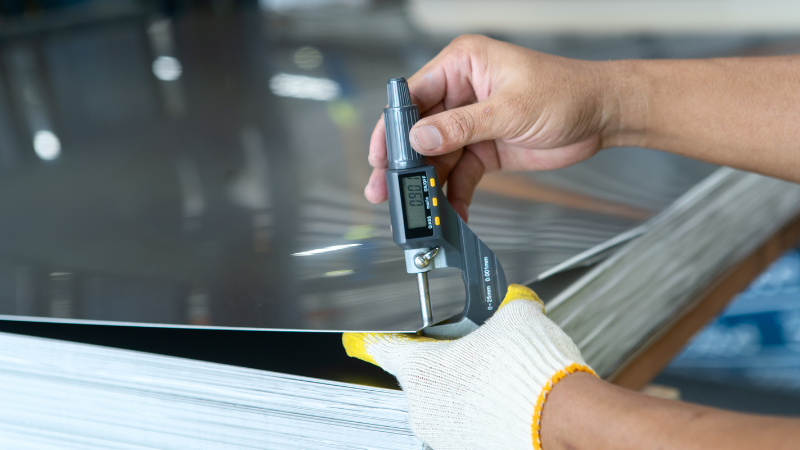
3. Dangerous Gases
This is a dangerous disadvantage as it affects the health of the operators and people around the operation room. During the cutting process, the workpiece is melted and blown away by a jet of gas. This process produces a harmful environment due to the gases and fumes emitted.
Advantages of Ultrasonic Cutting
What is so appealing about ultrasonic cutting? Read on to find out.
1. Fast and Precise
When using ultrasonic cutting in the textile industry, you get faster, cleaner, and more precise results compared to laser cutting. The ultrasonic cutting knife glides through the material with minimal resistance. The cuts are highly reproducible, and the process does not generate dust.
2. No Deformation
Ultrasonic cutting machines are perfect for the food processing industry. The vibrating ultrasonic knife cuts through any food product with near-zero resistance. This enables the technology to cut through sensitive food products without deforming their edges. It is possible to cut even the smallest slices with this technique.
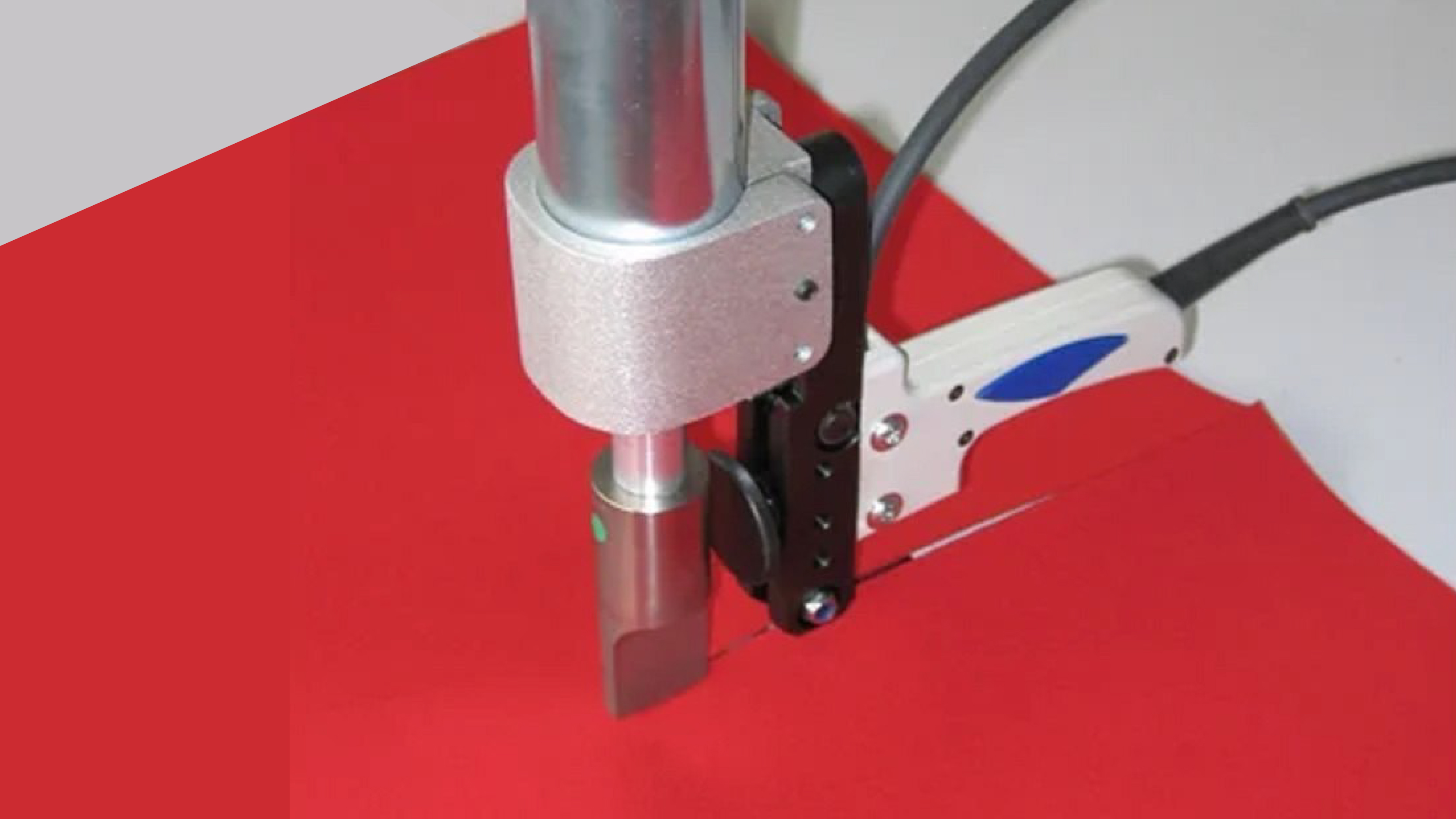
3. Minimal Production Waste
Due to its high precision and reproductivity, ultrasonic cutting allows for minimal production waste. The cutting process does not leave food residues stuck on the cutting blade.
4. Cut and Seal/ Join in a Single Step
Another advantage of ultrasonic cutting in the textile and rubber industries is its ability to cut and seal in a single step. This prevents the material from deforming and also saves time. During the cutting process, the ultrasound technology melts the edges to prevent fraying. The technology also allows you to cut and join two layers in one step.
Disadvantages of Ultrasonic Cutting
Inevitably, there are some drawbacks to ultrasonic cutting technology that need to be understood.
- Ultrasonic cutting has a low material removal rate. This makes it unideal for applications requiring a high material removal rate.
- Ultrasonic processing cannot be used to drill deep holes due to the movement restriction of the abrasive slurry. An ultrasonic cutter will not reach the bottom of the hole effectively.
- The constant impact of the vibrating cutting knife causes a fast wear and tear. This means you will incur tool replacement costs regularly.
Application Industries of Laser Cutting
Laser cutting is used to cut a wide range of materials. It is popular in metal, plastic, wood, and glass industries. The following are some of the industry applications of laser cutting.
1. Automotive
The vehicle manufacturing industry has embraced the benefits of laser cutting technology. Laser processing is highly flexible and capable of cutting the most intricate designs and shapes. Besides car parts and components, the auto manufacturing industry uses laser technology to cut die-castings, stampings, and forgings.
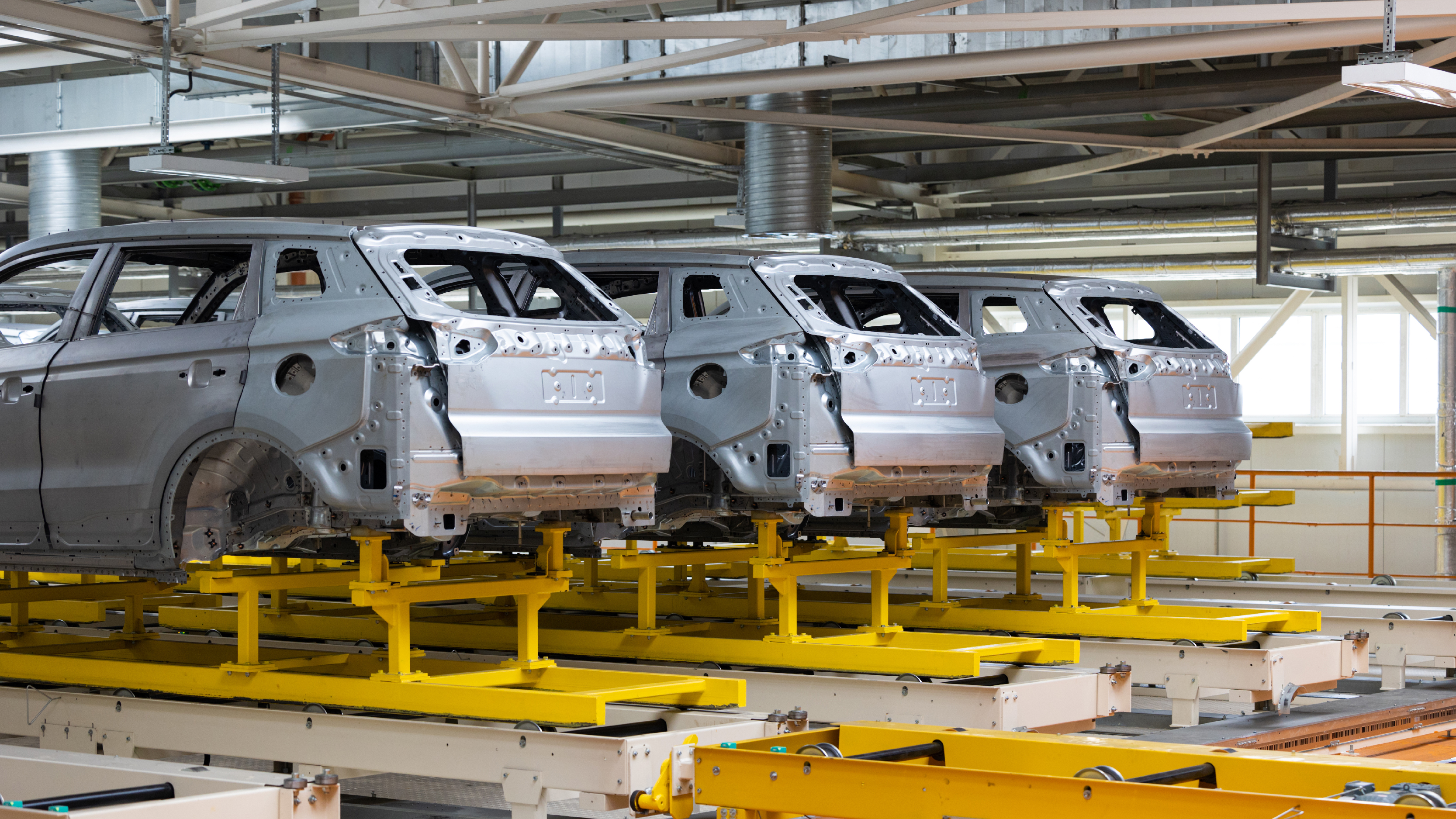
2. Medical Industry
The medical industry uses laser processing to manufacture devices such as pacemakers, stents, and catheters. The laser technique is used to create devices with complex designs that are used inside the human body.
3. Jewelry and Artistic Applications
Laser cutting has been creatively integrated with art and design. In creative and artistic applications, laser technology can be used to create stationery invitations, brick pavers, and glassware, among other applications.
In the jewelry industry, laser cutting has revolutionized the whole jewelry-making process. Jewelry made with laser technology is more intricate compared to those made with traditional manual methods. Laser is also used to cut precious stones such as gemstones.
Application Industries of Ultrasonic Cutting
Ultrasonic processing is suitable for cutting various materials, including food products, rubber, and plastic. The following are some of the industrial applications of ultrasonic cutting.
1. Food Industry
Ultrasonic cutting is mostly used in the food processing industry. The cutting process has a high degree of accuracy and precision. As such, it does not cause deformation or distortion when cutting food products such as cakes, confessionary bars, cheese, and more.
2. Textile
Another popular application of ultrasonic cutting is in the textile industry. Besides the fast and precise cutting, ultrasonic cutting has the ability to cut and seal textile edges in a single cut. The vibrating cutting knife easily cuts through the material. At the same time, the ultrasound energy produced by the ultrasonic vibration melts the edges of the cut textile, causing them to seal permanently.
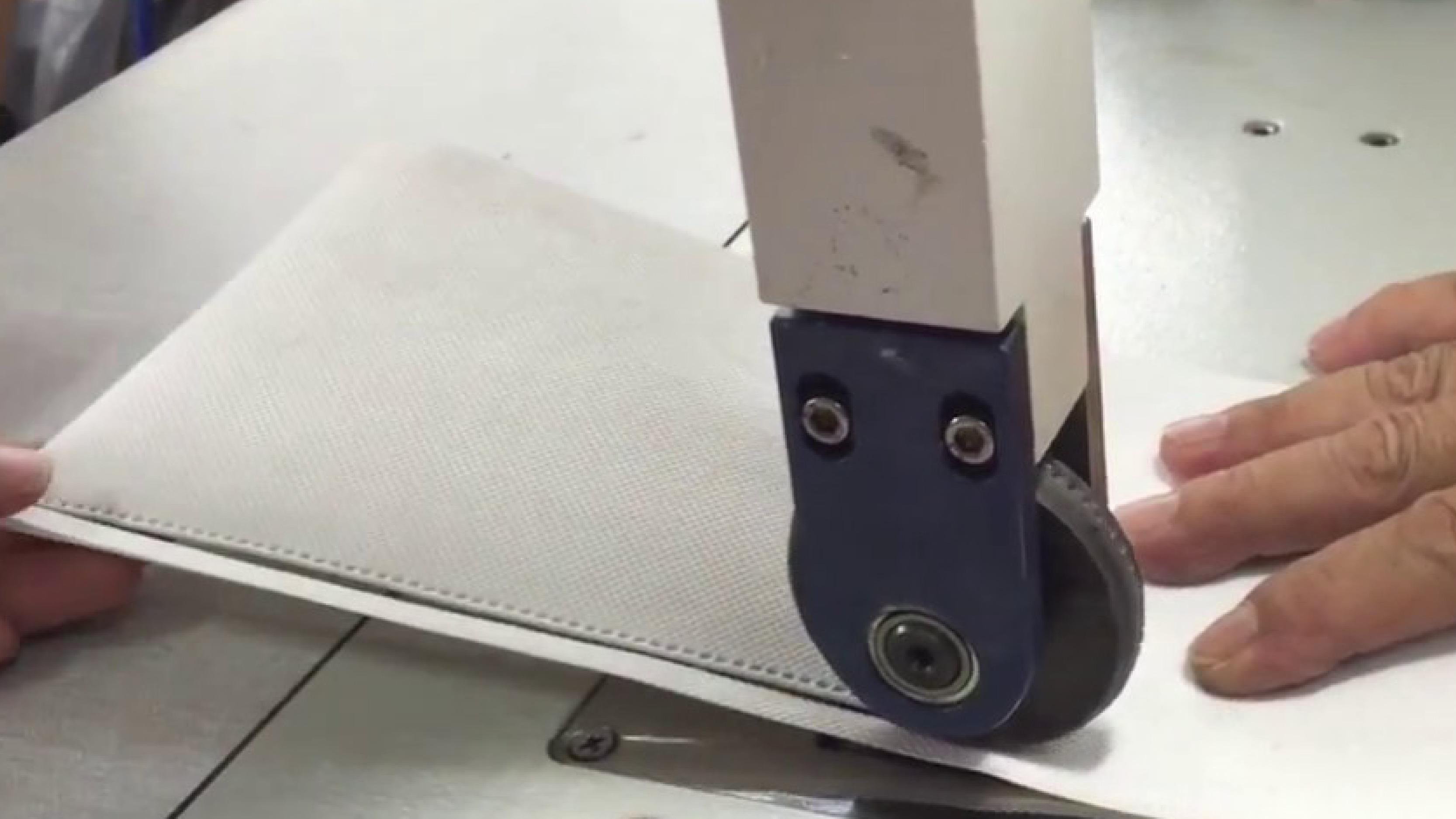
Comparison of Laser Cutting and Ultrasonic Cutting
Below we have put together a comprehensive comparison of laser cutting and ultrasonic cutting, from which you can prepare for your choice.
Characteristics | Laser Cutting | Ultrasonic Cutting |
Cutting principle | High-power density laser | Vibrating ultrasonic blade |
Efficiency | Highly efficient | Less efficient |
Automation | Fully automated | Not fully automated |
Quality and accuracy | Good cutting edges. | Smooth and accurate incision. Clean finish. |
Industry applications | Popular in the automotive, aerospace, and medical industries. | Popular in the food processing, textile, and rubber industries. |
1. Their Working Principles Are Different
A laser cutting machine uses the principle of a highly focused high power density laser beam to cut its intended workpiece. The laser beam irradiates the material so that it quickly vaporizes, burns, or melts. Then, a high-speed airflow coaxial blows away the molten material, leaving a clean laser-cut finish.
Ultrasonic cutting, on the other hand, uses an ultrasonic cutting tool with a high vibrating frequency. During the cutting process, the ultrasonic vibrator generates forward and backward vibrations that are then transmitted to the outer section of the grinding wheel blade.
The vibrations are transmitted through the abutment of the primary shaft and the grinding wheel blade and are converted into the expansion motion in the radial direction. The radial direction conversion of this ultrasonic vibration results in the ultrasonic cutting process.
2. The Features
Laser cutting, once exclusive to manufacturing, is now widely used due to its impressive features. It’s fast, precise, and low-maintenance compared to other methods. Laser cutting applies no pressure on the material, ensuring high-quality outcomes with minimal manpower due to its automation. It’s ideal for complex designs, thanks to its integration with computer technology.
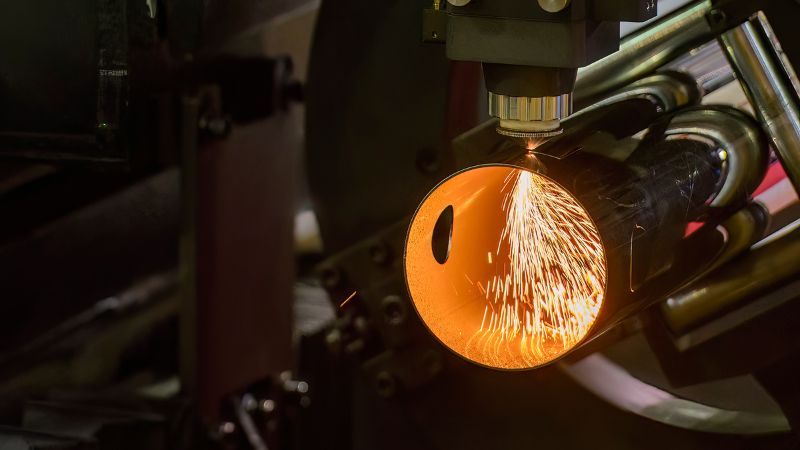
An ultrasonic cutting machine provides the advantages of smooth and reliable incision and accurate cutting that does not deform or wrinkle the cut edges. On the other hand, laser cutters do not offer the precision and firm incision that ultrasonic cutting devices offer.
3. Efficiency
Laser cutters have a high degree of automation. As such, they are much simpler to operate and do not require many operators. The processing speed of this cutting process is impressively high. Because it uses computer numeric control, you can design and process your artwork immediately.
Ultrasonic cutting is less efficient than laser cutting. Its automation is much more difficult compared to laser. As such, it leaves the laser cutting process as the more efficient cutting technique.
Laser Cutting VS. Ultrasonic Cutting: Which One to Choose?
Before deciding which machine to acquire, it’s important to look at the factors that affect your decision. These are some of the factors that’ll help you decide between laser cutting and ultrasonic cutting.
- The industry you are in is the first factor affecting your choice of machine. Your industry determines the materials you’ll cut with your newly acquired cutting machine.
For instance, laser cutting is the best option for automotive manufacturers. It is highly flexible and can cut intricate shapes of car parts and components. Ultrasonic cutting can achieve smooth and firm incisions that most food products require. - The thickness of the materials you intend to cut will also help you determine the type of technology to choose. Laser cutting can cut through materials as thick as 20 mm. Ultrasonic processing, on the other hand, can only cut materials 5 mm thick.
- The required accuracy and precision levels are other determinants of cutting technology. Ultrasonic cut edges do not warp or wrinkle from pressure exalted by the cutting tools in traditional cutting methods. Laser cutting is accurate and precise, but its degree cannot match ultrasonic cutting.
Which One to Choose?
The choice of cutting technology depends on the business you are involved with. Understand your primary business cutting needs before going into the market for a cutting machine.
Laser cutting is perfect for sheet metal cutting, wood, plastic, and other materials. It is the perfect cutting method for intricate and artistic designs. Laser cutting is the perfect technology if your cutting involves complex shapes and designs, such as car components.
Ultrasonic cutting allows for high precision and reliable incision cutting. If your cutting needs require these levels of accuracy and precision, you will need an ultrasonic cutting machine. Food production and other materials affected by pressure and temperature will require ultrasonic cutting technology.
FAQs
1. Can a laser be used for drilling?
Laser can be used in various applications, including drilling holes in metallic materials, wood, and ceramics. Examples of laser-drilled holes are the holes in fuel-injection nozzles.
2. Why is laser cutting better?
Laser cutting stands out for its precision and speed, suitable for complex designs and diverse materials, with the added benefit of low maintenance.
3. Why should you choose ultrasonic machining?
One of the primary reasons for choosing ultrasonic cutting is its ability to cut hard and soft materials without deforming the cut edges. Its smooth and reliable incision makes the technique ideal for food products such as confectionery bars.
Conclusion
Laser and ultrasonic cutting are excellent techniques that can help take your business to the next level. The machines are perfect in different manners. However, to get the right machine, consider the comparisons to determine the exact machine that best fits your project. Use top-notch cutters from globally recognized manufacturers to achieve the most desired results.
Baison Laser Has The Best Cutting Solutions For Your Project!
At Baison Laser, we understand that efficiency and output are what you need. Designed and built in-house with durability at heart, our cutters are top-of-the-line and ready for your project. Whether cutting metal sheets or intricate materials, Baison Laser has the perfect cutting solution.
We are always ready to answer your questions. Contact us today for application evaluation. We offer free consultations.