There are several techniques to cut various materials, but what’s the best method? This article will examine two of the most prevalent techniques: plasma cutting and laser cutting. Continue reading to learn about each strategy’s advantages and disadvantages and determine which is best for you.
What Is Laser Cutting?
“Laser cutting” refers to cutting through any material with a laser employed in industrial manufacturing applications. An optical laser focused beam of light makes up a laser cutter. When it comes into contact with the material, the high-power laser causes that substance to heat up and melt quickly.
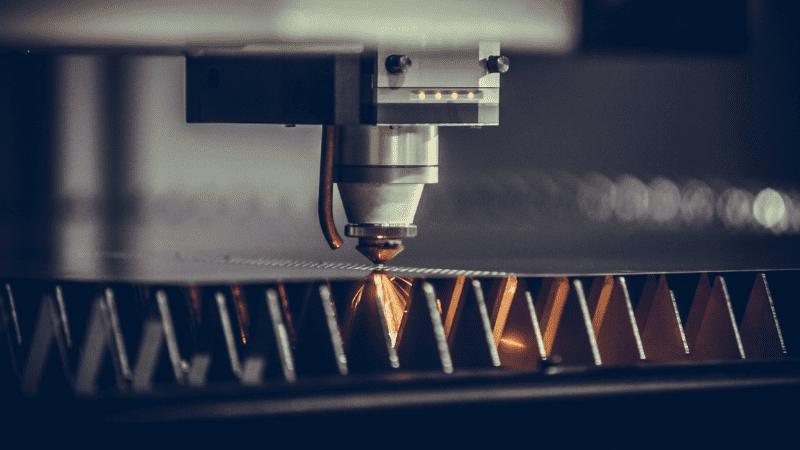
Using a CNC to operate the laser optics from a distant location is possible, which stands for computer numerical control. This process allows the beam to be directed toward the material effectively to cut it. The method is widespread in various fields, including microelectronics and many others concerned with minute particulars.

What Is Plasma Cutting?
Plasma Cutting is a technology that combines precision with high speed and employs the melting process to cut through the material. The plasma-cutting machine uses a concentrated stream of electrically conductive gas to transmit energy from the source to the material. It is achievable because of the plasma torch, which assists in producing the hot jet of plasma.
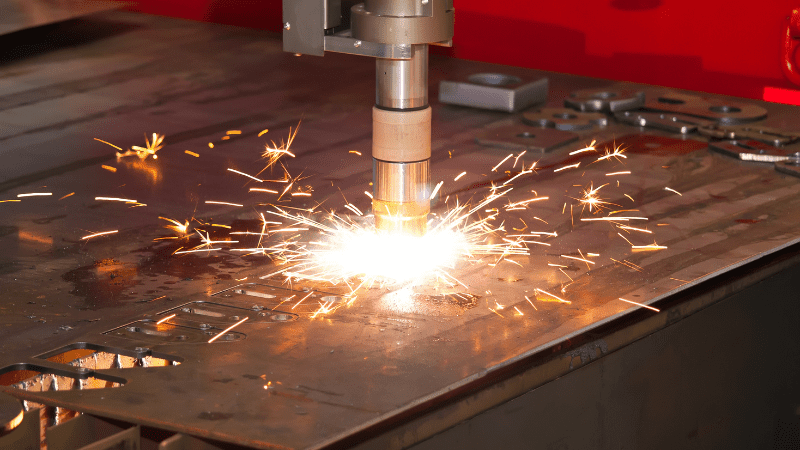
Plasma Cutting finds widespread use in cutting conductive metals, such as brass and titanium, which are relatively affordable, contributing to their widespread usage and popularity.
In addition, the presence of nitrogen and oxygen enables the concentrated stream to cut at high speed. This procedure uses other gases, including compressed gas, oxygen, nitrogen, and argon-hydrogen.
How Do Laser Cutters Work?
The internal dynamics of how laser cutting works are pretty fascinating. They function by generating powerful laser beams with the use of laser cutting machines. The laser optics computer numerical control redirects the laser beam toward the material processed.
Once the energy concentrates on the material, the cutting process may officially begin. The laser optics assist the laser beam in passing through a nozzle so that it may be directed directly at the substance. The substance instantly evaporates after coming into contact with it. The continuous processes of heating and melting produce an edge with a superior surface finish with the help of laser cutting.
How Do Plasma Cutters Work?
The plasma cutter has a very distinctive method of cutting through materials. Plasma cutters perform their function by driving a rapid stream of heated plasma through the conductive substance to be cut. It is essential to remember that the passage of an electric arc through a gas produces this scorching plasma.
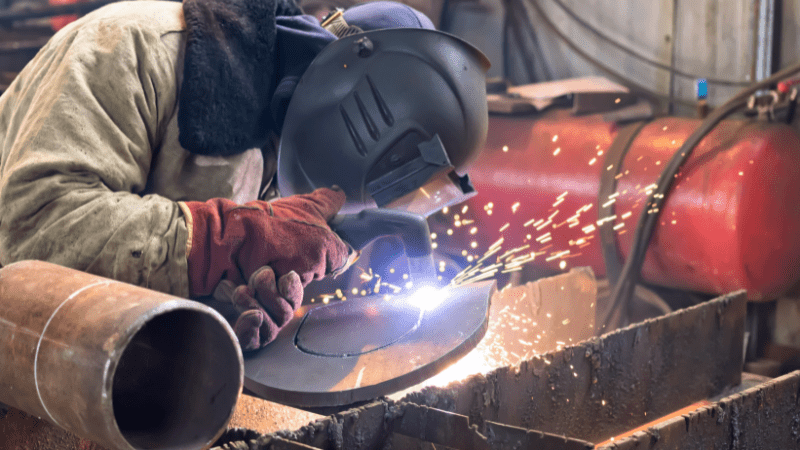
This electrically conductive gas is what a plasma cutter will use to transport energy from a power source to the conductive material, resulting in a clean cut. Remember that the exact cut is possible because the plasma arc development starts when the gas passes through a tiny nozzle.

Types of Laser Cutting
When it comes to laser cutting machines, the market will likely provide you with several alternatives. Flame cutting, Fusion cutting, and Fiber Laser cutting are the three primary types of laser cutting machines.
- Fiber Laser Cutting: In this stage, the metals and other materials are melted and pierced by a specific solid-state laser. Which not only helps you create a precise cut but also helps you cut it efficiently. It is also the technique of laser cutting that is popular and primarily used in industrial applications.
- Laser Flame Cutting: Oxygen functions as an assist gas during this procedure. During the interaction, this method produces an exothermic reaction, increasing the amount of energy transferred into the material, which results in a precise and clean cut.
- Laser Fusion Cutting: Nitrogen or argon, which inhibits reactions, is used as the shield gas in this method. After that, the gas is forced through the kerf at very high pressure, anywhere between 2 and 20. Which ultimately leads to precise cuts.
Types of Plasma Cutting
Similarly to the laser cutting machine, the plasma machine is available in quite a few distinct versions. Plasmas such as air plasma, CNC plasma, and oxygen plasma are a few examples.
- Air Plasma Cutting: This approach is the most flexible of all the gases used in the plasma cutting process. Compressed air is used in operation, enabling it to cut through various materials, including aluminum and carbon steel. This process is well-suited for industrial enterprises that produce smaller volumes.
- Oxygen Plasma Cutting: Cutting using oxygen plasma is better than standard air plasma cutting. The cutting procedure that utilizes oxygen will be much quicker than the other option.
- CNC Plasma Cutting: This plasma cutting procedure is carried out entirely via a plasma torch managed by a computer numerical control. This method is far more precise and accurate than a handheld plasma cutter.
Difference Between Laser Cutting and Plasma Cutting
Laser and Plasma cutting are wonderful pieces of equipment with widespread application in various industrial and manufacturing settings. They are responsible for the same tasks, yet several variations set them apart and make them distinctive. Let’s look at a few ways each is unique from the others.
1. Application
Even though they perform a similar function, their applications in industrial production are pretty distinct from one another. Anyone can use plasma cutting machines to cut almost any material, although they specialize in cutting medium-thick plates that bring 1.5 inches. However, you should choose laser if it is thin sheet cutting.
2. Compatibility
Laser cutters can cut through many materials, including wood, plastic, glass, aluminum, etc. On the other hand, plasma cutters can only cut through materials that conduct electricity. This constraint makes them less flexible. The reason for this is that plasma cuts materials by the use of an electrically conducting gas.
In addition, lasers are hard to cut reflecting materials, but plasma cutters can make clean cuts through any conductive substance.
3. Tolerance
An excellent tolerance level is essential when you want accurate results from utilizing the tools for an extended period. The laser cutting machine offers a more precise tolerance of 0.002 inches, which makes it the most effective for precision cutting. Laser cutting materials provide a higher tolerance level than plasma cutting.
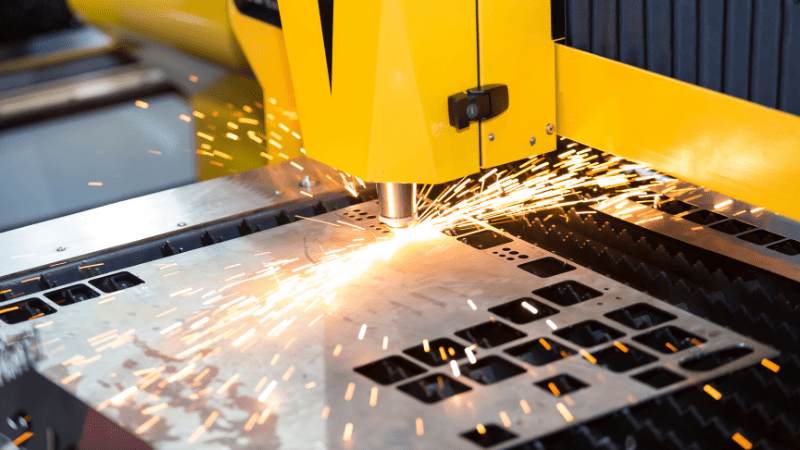
4. Budget
Before using any of the tools, it is essential to have a good understanding of your budget. Plasma cutting is often less costly to operate than lasers, making lasers a more expensive option. Therefore, if you want accurate cuts and have enough budget, you might consider using laser cutting. Plasma cutting is when your cuts are straight and your budget is limited.
Laser Cutting | Plasma Cutting | |
---|---|---|

The Advantages of Laser Cutting Over Plasma Cutting
The use of laser cutting is becoming increasingly common in commercial and industrial settings. Laser cutting tools are prioritized primarily due to the many incredible advantages these tools offer. When compared to plasma cutting, laser cutting has a considerable number of benefits.
If you often cut materials, not having access to a high-powered laser will likely be a source of incredible frustration for you.
In this very day and age, almost everything we use is high-powered. A laser cutter with a lot of power could be handy when cutting through various sorts of material. If you use a high-powered laser, such as the flame cutter machine, then the laser can cut through plates of a reasonable thickness.
- Cutting Material Range
Plasma can only cut through conductive materials; therefore, certain limitations exist. They cannot make a clean cut through rigid materials such as leather, wood, and other similar substances.
However, this is not the case with a machine that uses a laser to cut the material. They can cut almost any material; however, the thickness of the material must be kept in mind.
- Variety
It might sound odd, but having the option to do different tasks with the same machine increases its value. The only thing you can do with plasma cutters is to cut materials, but with lasers, you can cut, wield, and engrave, allowing you to perform many different things with the same instrument.
- Easy Setup
When comparing the various cutting tools that are now on the market, you will find that laser cutting is the one that requires the least amount of time and effort to set up. For its operation, laser cutting does not call for any form of tedious setup or additional input from the outside. Anybody can carry out the method since it is straightforward to understand.
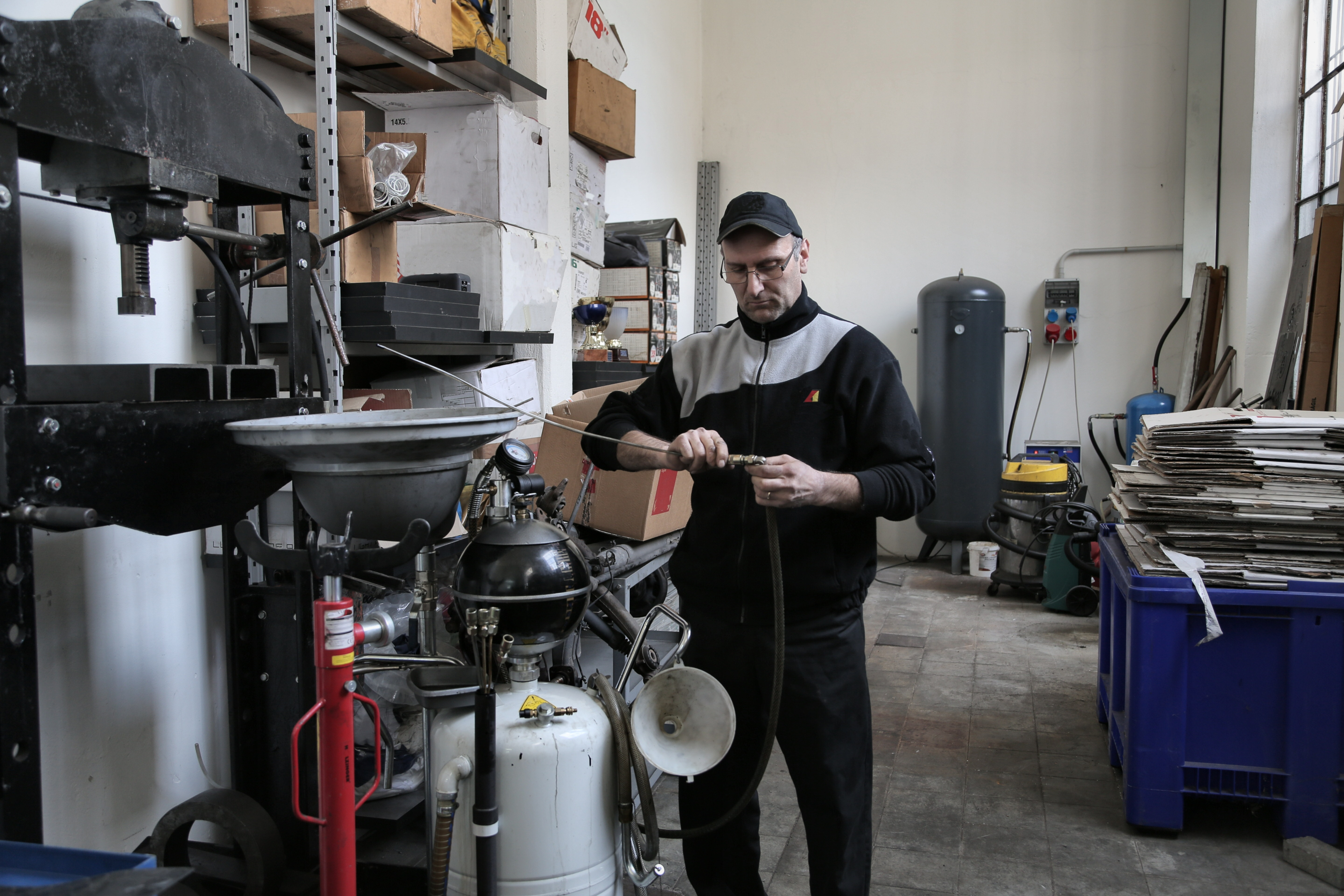
The Disadvantages of Laser Cutting Over Plasma Cutting
Even though laser cutting might appear to be an upgrade, a few drawbacks are associated with owning one. It is sometimes an issue that many individuals find to be very difficult to deal with such problems. Let’s detail the drawbacks of choosing laser over plasma cutting.
- Too Expensive
Laser cutting is excellent cutting equipment with remarkable features, but there is a price to pay. Cutting using a laser requires a far higher power consumption than cutting with some plasma models. It means that you wind up spending a significant amount of money on operations.
Depending on the model, the cost of the machine by itself might range anywhere from $4,000 to $16,000. In comparison, cutting with plasma consumes minimal energy and is substantially less expensive than using lasers.
- Dangerous
You might wonder how something as seemingly harmless as a laser cutter could pose a risk. Well! The results might be very harmful if the laser beam touches a person’s skin. When not handled correctly, it has the potential to inflict severe burns and wounds. Plasma cutting, on the other hand, does not result in bodily injury; nonetheless, you must be very careful about fumes and gases.
You can read our article on laser class and safety.
- Handling
You might hear this from different workers who may tell you that laser cutters have complicated handling requirements. Given the laser beam’s high sensitivity, even the slightest error in its handling might result in the material being scorched or discolored.
- Requires Expert
If you don’t have any protective gear or a constant presence, you should avoid using the machine since it poses a risk. During the initial days of using the equipment, an expert must monitor the process and ensure it works without any issues. Employing a specialist often comes at a high price and may be demanding on the person running the business.
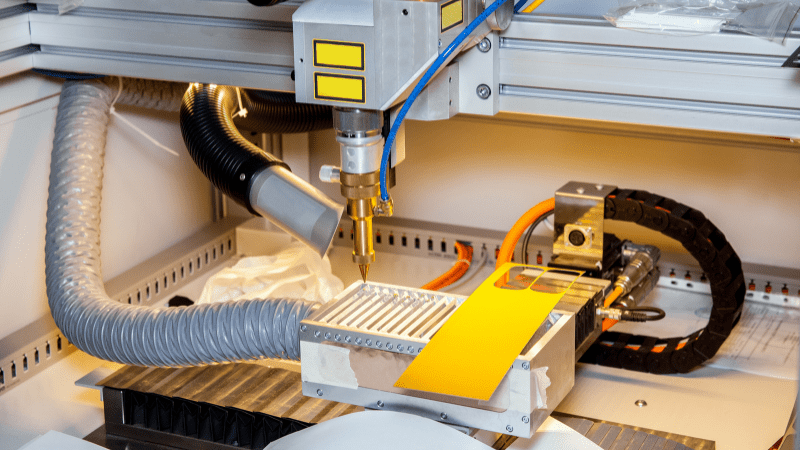
Are Laser Cutting and Plasma Cutting Machines Durable?
When deciding between laser and plasma cutting, durability is essential. The device’s durability will give you an idea of its quality and how long you will be able to use it. Laser cutters typically have a lifespan of more than 2,000 hours, approximately eight hours of continuous daily usage.
Plasma cutters are machines with a high level of durability and can withstand continuous use for many years. Engineers developed these devices to handle several users at the same time.
Laser cutters incur much higher operating costs than other cutting methods due to the consumable nature of their laser tubes, which you must change periodically. These pieces of equipment will be with you for a long and productive year.

Application of Laser Cutting and Plasma Cutting
Laser or plasma cutting is quite common in a wide range of different manufacturing and industrial settings. Tools that cut using lasers and plasma are becoming more prevalent due to the rapid advancement of technology, improving productivity and efficiency. These technologies are likely used in hundreds, if not thousands, of different industries throughout the globe today to improve overall efficiency.
These are some examples of such industries that utilize such types of equipment:
- Manufacturing Industry
- Automotive Repair Shops
- Industrial Construction
- Fabrication Stores
- Salvage Yards
- Junkyards
Cutting by laser and plasma is also used in other sectors, such as the pharmaceutical and arms industries. Cutting using a laser or plasma is performed because it eliminates the need for numerous engineers and workers to do machining. By doing this, you can significantly cut down on manufacturing expenses. These machines are always better and more precise than people, which makes them much more effective.
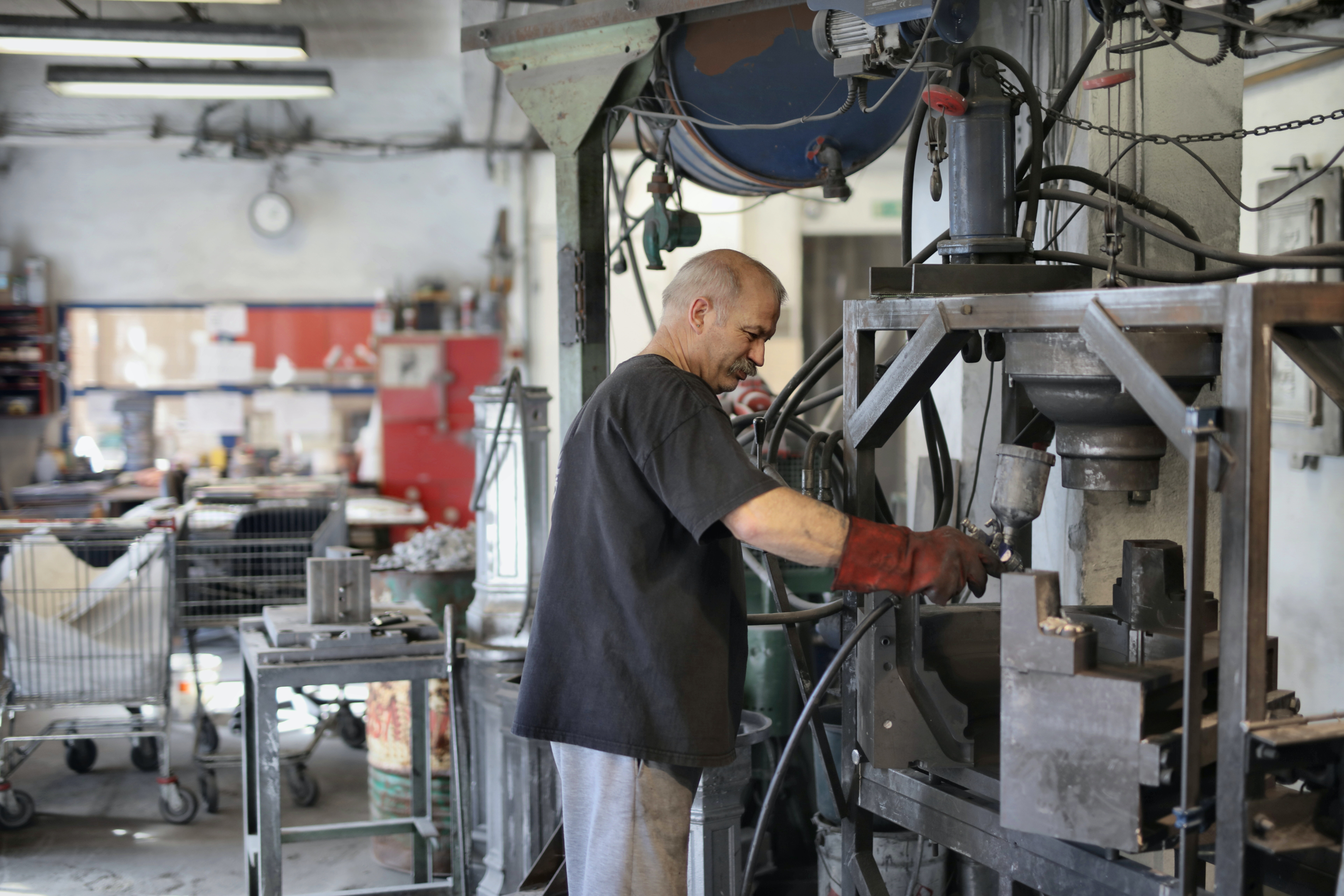
Which Type of Cutter Is Best for Your Project?
Since these tools’ functions are so comparable, most individuals find it quite tough to choose a suitable technique. However, quite a few characteristics set each of them apart. Although identical, many individuals have difficulty selecting one over the other.
If you are still facing trouble picking between laser cutting and plasma cutting, then you should make sure to consider the following while making your decision:
1. Material
Be careful to determine the reason behind your requirement for a new cutting tool before going out and purchasing one. Plasma cutting is a technique utilized in a much smaller number of applications than laser cutting. Laser cutting is an option to cut wood, rubber, leather, and other materials. However, the decision is entirely up to you. Plasma is the superior choice for cutting conductive materials.
2. Precision Level
Cutting tools are utilized in numerous industries and applications today, including personal use. That is why the level of precision that the instrument has is significant, considering the task that you will be doing.
Laser cutting is the technique to use when you want the utmost precision and accuracy in cutting anything. The plasma cutter is the tool to use when cutting anything, but it’s not something that requires a lot of precision.
3. Cost Efficiency
When selecting these devices, you need to make sure that you are aware of your budgetary constraints. These machines may cost you considerable money, so you will want to be sure you choose the proper one for the job.
If you have a minimal budget, the best option would be to go with a plasma cutting machine because of how much cheaper and budget-friendly they are. Although laser cutting machines are more expensive, they are ideal for you if you want to use cutters in your business.

Conclusion
This article delves into the intricacies of laser cutting versus plasma cutting, providing a comprehensive comparison to help you understand which cutting method is more suited to your specific needs.
It covers the advantages and disadvantages of each technology, including precision, materials compatibility, cost-effectiveness, and operational requirements. By highlighting key factors such as cutting speed, material thickness, and finish quality, the article aims to equip you with the knowledge to make an informed decision.
Unlock Cutting Precision with Baison Laser!
Ready to elevate your cutting projects with unmatched precision and efficiency? Discover the perfect cutting solution tailored to your needs with Baison Laser. Explore our range of cutting-edge laser cutting machines today and start transforming your ideas into reality. Contact Baison Laser for expert advice and begin your journey to cutting excellence now.