Laser cutting is one of today’s critical processes that help manufacture various components using different materials. However, the significance of assessing the cost of this process is equally important.
This guide below provides a detailed insight into the factors that impact laser cutting costs, so, let’s dive into this guide below and understand them in detail. This guide will also help you learn why laser-cutting experts rely on the Baison Laser equipment and how it helps with cost savings.
Understanding Laser Cutting
In order to assess the cost of laser cutting, understanding the basic principles, types of laser, and steps involved in laser cutting is very important, these essential aspects are discussed below.
Basic Principles of Laser Cutting
Laser cutting is a comprehensive process involving various details and aspects that need to be understood for a better outcome. Below, we have discussed in detail some of the most important basic principles involved in the laser cutting process, and these are as follows:
1. Unified Source of Light
The laser cutting comprises the most essential part of the equipment, the laser beam. This laser beam contains photons with a common wavelength, producing a unified light source that helps with precision cutting.
2. Flexible Material Absorption
Laser cutting involves various materials being cut and used. Every material has a different absorption rate for the laser light, which is one of the fundamental aspects. However, laser cutting can adjust laser energy based on the nature of the material and its requirement for vaporization, burning, and melting.
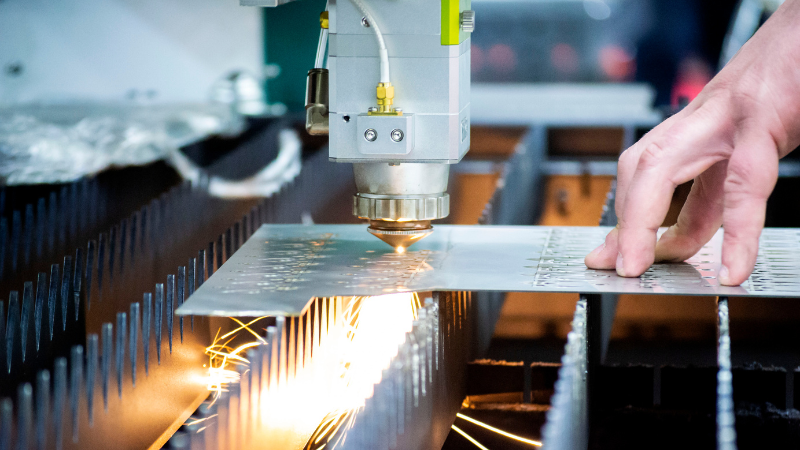
3. Focused Heat Concentration
The laser power emits a concentrated light, light consists of photos, and they produce heat; through this concentrated heat, even the smallest area can be subjected to laser cutting, and hence, this process ensures precise cuts are carried out without impacting the material in the surroundings.
4. Optical Precision
The laser cutters comprise lenses and mirrors; these help focus the laser beam and ensure that the beam offers sharpness and precision that helps cut materials appropriately.
Process of Laser Cutting
Laser cutting involves various stages, and each step plays a significant role in cutting the various materials for components. The stepwise process of laser cutting is provided below:
- The process of laser cutting starts with feeding the design in a digitized manner to CAD software that helps automate the process of laser cutting machines.
- The laser cutting machine’s source laser generates the focused laser beam on the material that is supposed to be cut down.
- The laser cutting machine uses mirrors and lenses that help direct the laser beam toward the substrate material. This helps to maintain a steady and precise beam of light.
- The interaction of the laser beam and material is the point that leads to cutting the material. The material heats immediately as it comes into contact with the laser light, leading to the melting and burning of material and sometimes vaporizing.
- An assist gas is introduced to have a neat and clean cut with excessive material removed from the surroundings, which helps to ensure a clean and tidy cut with no imperfections.
- Heat generation is very high during laser cutting; hence, to ensure the durability of the cutters, the laser cutting machines are equipped with cooling systems. These cooling systems help to dissipate unnecessary heat, and the temperature of the components is maintained.

4 Methods of Laser Cutting
The laser cutting process has multiple methods; each method is different in processing, outcome, and application. The commonly used methods of laser cutting are discussed below.
1. CO2 Lasers
The CO2 laser is a type of laser that generates from a mixture of gases having carbon dioxide in abundance. These lasers emit a high-energy beam that burns or vaporizes the material, leading to detailed cuts.
2. Fiber Lasers
Fiber laser uses optical fiber that is doped in materials like ytterbium, which is a rare-earth element. It is widely used for cutting and engraving materials like aluminum and steel because they have a very fine beam quality.
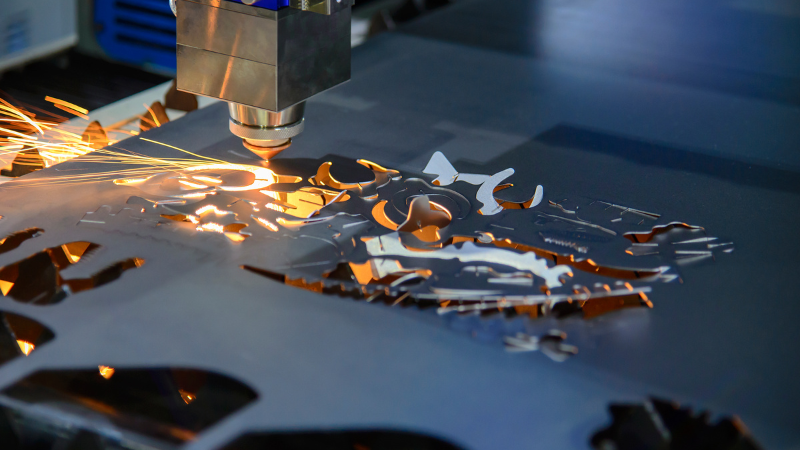
3. Fusion Cutting
Fusion cutting uses the principle of using a focused laser beam to melt the material. When the material has reached its melting point, a high-pressure gas is introduced, and the molten metal is removed.
Factors Affecting Laser Cutting Costs
The laser cutting costs depend on various factors and not just the laser cutter cost. However, the factors involved in identifying the overall cost of laser cutting are discussed below.
1. Laser Cutting Machine Cost
The initial cost is the cost of the laser cutting machine; this investment is the introductory price to pay, and along with this cost, the machine’s maintenance cost is also associated.
2. Material Thickness
The thickness of the material also has an impact on the total cost of laser cutting. When the material is thick, the time taken for the laser to penetrate it and it is down is also longer; hence, the overall cost may increase. It happens because the longer the time machine runs, the higher prices are incurred.
3. Complexity of Design
Design complexity also adds to the cost; a simpler design will be quick, and hence, the machine operation time will be less, which helps in cost savings. However, if the design is complex, the time taken to get done with it is longer, leading to an increase in the cost of cutting.
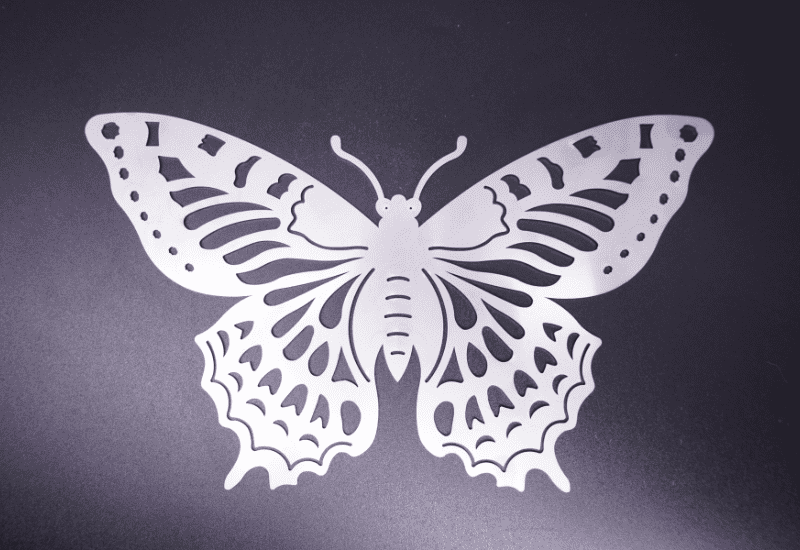
4. Material Strength
Some materials are very strong, so cutting them is more difficult through lasers. Due to this, cutting them down takes a lot of time and power. The strength of the material also plays a vital role in increasing or decreasing the cost of the laser-cutting process.

Machine Costs
Machine cost is the first component and the initial cost that affects the pricing of the laser-cutting process. However, there are different factors on which the price of a laser cutter depends. These factors include the machine’s size and the component’s characteristics.
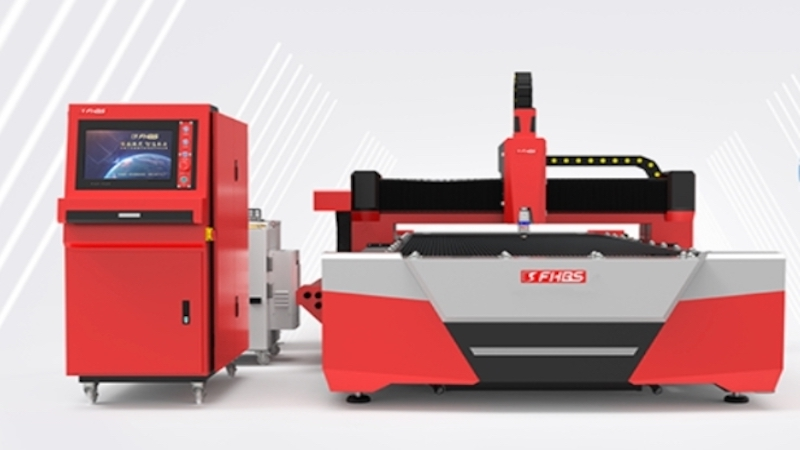
There are three main types of lasers used commonly to cut down various materials, and these include CO2 lasers, diode laser cutters, and fiber lasers. The prices for the different types of laser cutters vary and are as follows:
- CO2 laser cutter costs around $8000 to $50,000, and the power output ranges between 100W and 500W. It is commonly used for non-metal materials.
- Fiber laser cutters, on the other hand, are priced between $20,000 and $500,000, and the power output ranges between 500W and 20kW. High-power fiber laser is on the higher side of the price.
- Diode lasers are affordable and priced between $5000 and $20,000, and they offer mid-range power that makes them suitable for various operations.
Operational Costs
The laser cutting machine operating costs prove to be equipped with multiple other expenses. Such expenses include power consumption, gas, overhead, and labor expenses. A detailed breakdown of all these costs has been discussed below:
1. Labor Costs
Various aspects need to be analyzed in labor cost, which comprises assessing skill level and the experience labor may have. In cases where specialized equipment for laser cutting is used, labor expertise matters, which may increase the cost.
When calculating labor costs, some of the essential aspects to keep in mind are as follows:
- Labor costs encompass wages, benefits, overtime, insurance, and other benefits.
- Skilled and experienced labor can demand higher wages but also improve productivity and efficiency, potentially reducing the cost per production unit.
- Efficient operation minimizes time and supervision needs, lowering overall labor expenses. Regular training can further enhance productivity and cost-effectiveness.
2. Energy Consumption
The energy consumption of laser-cutting machines is also one of the several factors that require attention. The energy usage depended on the cutting speed, operation span, and machine power.
Machine operating costs can be reduced by monitoring and optimizing the energy system, which may comprise using energy-saving equipment and reducing idle time.

3. Cost of Laser Gas
Laser cutting also uses assist gases like nitrogen, oxygen, etc., which offers clean cuts and improved efficiency. The cost of these gases also adds to the operational cost. Hence, comparisons must be made between different gas suppliers to attain a better price when it comes to lowering operating costs.
4. Depreciation of Machine
The life of laser cutting machines is limited; hence, with time, the value of these machines decreases, and their useful life needs to be proportioned accurately. Therefore, the initial investment costs of this machine need to be divided by the machine’s useful life to identify the depreciation costs.
5. Overhead Costs
Overhead expenses include rent for the space housing laser cutting equipment and utilities like water and electricity.
Additional overheads comprise insurance premiums, taxes, and salaries for support staff and administration, all of which are integral to the laser cutting process.
The laser cutting cost can also be estimated with the help of laser cutting calculators. You need to add the power input, and it will calculate the cost per hour incurred on that power range. For instance, the following cost will be calculated if you opt for a power input of 2200 kW.

Maintenance Costs
Laser cutting also has various other components needed, including nozzles, lenses, cooling fluids, and others, and their consumption must also be tracked to achieve cost savings.
The cost of each component varies; some need a replacement daily, some need weekly, and some may be changed monthly. Below, we have insight into the price range of specific essential components associated with laser cutting.
- Protective lens covers need a daily replacement, and the cost of each of these ranges between $10 and $20.
- Nozzles require changing monthly or weekly depending on the production capacity; each cost is between $5 and $15.
- Lens cleaning kits are also essential, and they need a weekly replacement; the price per kit is around $15 to $25.
- Sacrificial slats for the work table need a replacement based on the production levels; sometimes, they need a change after 2 to 3 days, and sometimes once a month. The cost of these ranges between $1 to $1.5.
- Filters for air assist systems must be replaced monthly, and their cost ranges between $10 to $20.
- Belts and bearings can be replaced twice in one month, and their price range is between $20 and $50.
Apart from this, there may be unexpected breakdowns in the machine and this also leads to incurring costs for repairs which must also be budgeted beforehand under maintenance expenses.
Material Costs
Laser cutting is carried out on multiple materials, ranging from metals to plastics, textiles, leather, and more raw materials. However, which material to choose depends on the requirements of the product, and it is essential that an appropriate material is chosen when it comes to optimizing the costs, including assessing the material’s strength, durability, and thickness.
Securing high-quality materials at competitive prices is essential. Researching suppliers who offer the best value is key.
Material costs vary based on the type and supplier. It’s important to consider not just the purchase price but also factors like material waste, processing time, and the efficiency of the laser with the chosen material to ensure cost-effectiveness.
Software and Technology
Advanced software and technology infrastructure are also essential for the efficiency of business operations. The software implementation, maintenance costs for software, and other associated overhead expenses affect the pricing of laser cutting.
Software with advanced features like CRM, inventory management systems, and other tools also help with time-saving; hence, the overall cost of production may be reduced.

Cost Comparison with Other Cutting Methods
There are multiple methods used for cutting, and when it comes to comparing the different cutting methods and laser cutting, the table may help you with this. However, the cost of methods depends on various factors like the type of material opted for, the thickness of the material, etc.
Features | Laser Cutting | Plasma Cutting | Waterjet Cutting |
Cutting Speed | High | High | Medium |
Precision | High | Moderate to High | High |
Range of Material Thickness | Multiple options, wood, plastics, metals etc, | Metals | Glass, Metal, Stone etc. |
Cost of Equipment | High | Moderate | High |
Cost of Operation | Moderate to High | Moderate to High | Moderate to High |
Material Waste | Low to Moderate | Moderate | Low to Moderate |
Maintenance | High | Moderate | Moderate |
FAQs
1. Can I use a laser cutter on any material?
Yes, laser cutting is suitable for cutting wood, steel, acrylic, plastic, and various other materials.
2. Is outsourcing laser cutting an affordable option?
The decision to outsource laser cutting services depends on the frequency of projects you come across; if these are rare, then it is cheaper to outsource. However, if you have a consistent laser-cutting project, you should do it in-house and look forward to lowering operational costs.
3. What Are the Cheapest Laser Cutting Machines That Can Cut All Materials?
CO2 laser machines are the cheapest and can cut almost all the materials.
4. How can we reduce material waste and optimize laser-cutting costs?
There are various ways to reduce material waste and optimize laser cutting costs; these include design optimization and using relevant software tools that help minimize waste and improve the material utilization rate.
Conclusion
The guide above must have provided insight into how laser cutting costs can be calculated and what impacts that cost. So, irrespective of whether the readers are large-scale manufacturers or own small businesses, the provided details greatly help when analyzing laser cutting costs. Maybe you’re already planning to get your hands on a laser cutting machine, and we’ve picked the best manufacturers for you to enjoy.
Elevate Your Laser Cutting Operation with Baison Laser!
Have you decided to invest in a new laser-cutting machine for your business? Well, in that case, your go-to place should be Baison Laser. You will get your hands on seamless quality laser cutting machines that are affordable and equipped with the latest features and offer clean laser cut components for your clients. So, save time searching for devices here and there and get in touch with Baison Laser.