In this article, we will explore the role played by ceramic rings in optimizing laser cutting performance and the numerous benefits they bring.
What Is Laser Cutting?
Laser cutting technology generates a high-powered laser beam to cut or engrave materials. To achieve this, the laser cutter uses a laser head and nozzle to focus the laser beam on a small spot. This helps melt, burn, or vaporize the material precisely.
This technology can cut various materials for automotive, aerospace, construction, shipbuilding, and other industries.
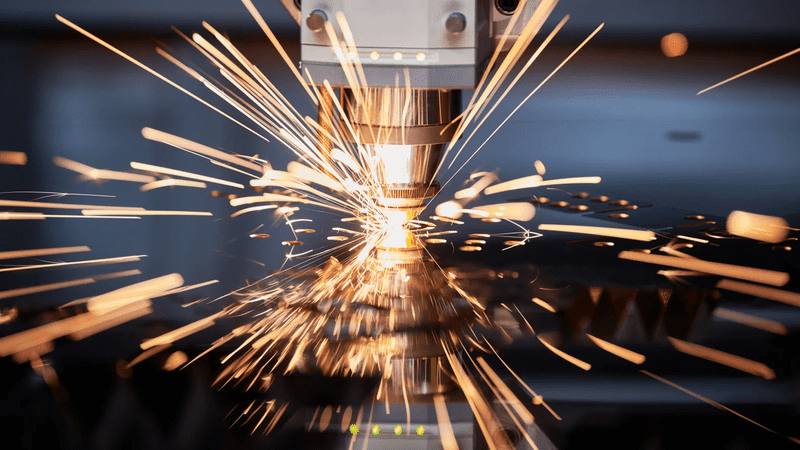
An important aspect of laser cutting is precision and accuracy. Credit to this, laser cutting offers intricate design cutting and tight tolerances. However, businesses have to use proper cutting parameters to achieve this precision.
These include laser power, cutting speed, and focus. Failing to optimize these parameters with the right components can lead to burrs, warping, or even rough edges on the cut.
What Are the Factors That Affect Laser Cutting Performance?
The laser cutting process parameters that affect laser cutting performance include:
- Laser Power: The higher the laser power, the higher the cutting speed. In simple terms, you can define laser power as the energy delivered by the laser onto the material being cut. However, one important thing to remember is that higher laser powers threaten the cutting material as they can cause warping or thermal damage.
- Material Type: All materials have their own capacities to absorb laser beams. This depends on their thermal properties. For example, higher laser powers are suitable to cut through materials, including metals aided by oxygen gas for debris removal. On the other hand, non-metallic materials like plastics require low-power beams assisted by CO2 gas.
- Material Thickness: Again, the thicker the material, the higher the laser power should be. For instance, a thick material needs high laser power with slow cutting speed for precise results.
- Cutting Speed: This is the speed that determines how fast the laser beam moves across the material being cut. As a result, it affects the cut width and depth. In industrial terms, a slower cutting speed equates to a broader kerf (width of the cut) and vice versa.
- Focal Length: This is the distance between the material being cut and the lens inside the laser head. The focal length impacts the shape and size of the laser spot, which means the smaller the length, the larger the spot size, and vice versa.
- Auxiliary Gas: The pressure and type of auxiliary gas ensure all unwanted debris is blown away. It also helps prevent oxidation. Usually, manufacturers use nitrogen or argon for non-metals and oxygen for metals.
- Laser Beam Quality: This also affects the cut quality as a higher quality laser beam equates to a smaller spot size and higher precision.
- Workpiece: To achieve a stable and clean cut, the workpiece needs to be positioned and oriented at the right angle. Otherwise, you will fail to achieve precision quality and laser-cutting process efficiency.
What Is the Role of Ceramic Rings in Laser Cutting?
Ceramic rings are used as a crucial accessory in laser-cutting machines. They help optimize machine performance and cut quality and provide protection for vital machine components.
Moreover, these rings are typically made from high-purity ceramic materials, such as alumina or zirconia. Here are some of the key roles that ceramic rings can play in improving laser cutting process performance:
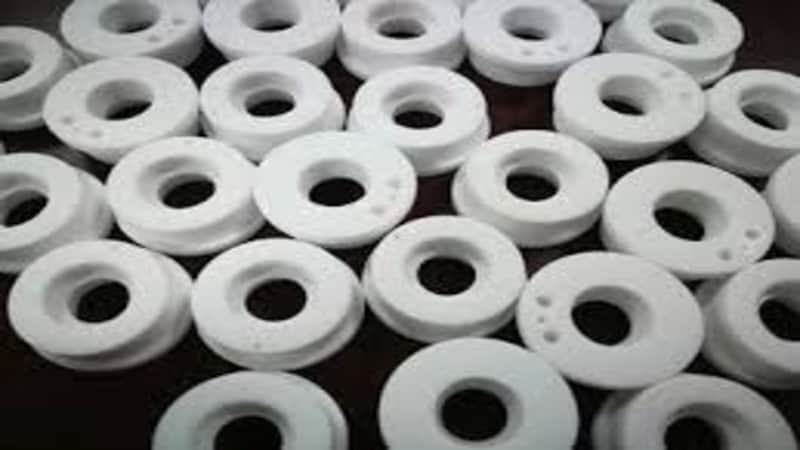
Lens Protection
The laser head in each laser cutter has a dedicated lens that focuses the laser beam on the cutting spot. Ceramic rings primarily protect this lens by keeping all the debris and damage at bay.
Focal Length Optimization
ceramic rings also help fine-tune the focal length of the laser beam for optimal cutting process results. This comes in handy when you are working with materials with varying thickness levels.
Enhancing Laser Beam Quality
achieving a uniform and precise laser beam isn’t as easy as you might think. Fortunately, the addition of ceramic rings to any fiber laser-cutting machines can make this easier. How come?
The high-purity ceramic material used in the ring uses its low thermal expansion to resist extreme thermal shocks. This allows for a stable laser beam flow during cutting, even countering surface roughness.
What Are the Benefits of Using Ceramic Rings in Laser-Cutting Machines?
Now you must be wondering how ceramic rings can help boost laser cutting performance. Well, here are some ways how it benefits your laser-cutting machine:
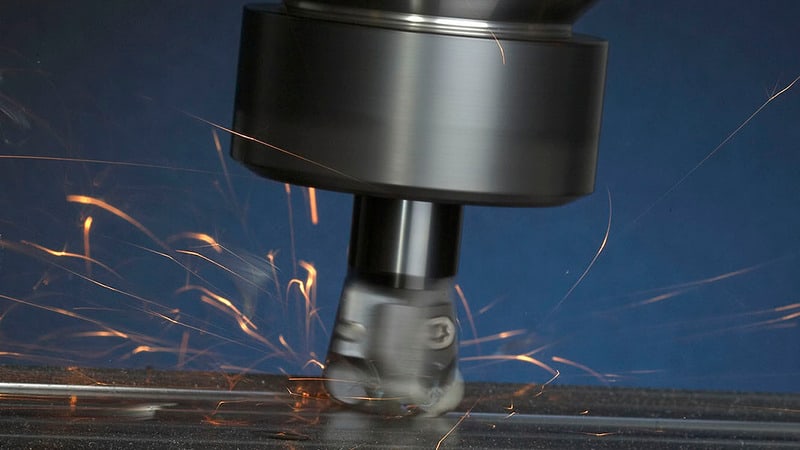
- Wear Resistance: ceramic rings use high-purity materials and have good wear resistance. This comes in handy as they can withstand repeated use without suffering any damage, even to the laser cutting machine during the cutting process.
- Thermal Stability: Given ceramic rings’ high thermal expansion coefficient, they can withstand great thermal shocks without degrading or warping. Therefore, they are ideal for use in laser cutting machines which often generate intense thermal energy during the cutting process, such as the 40kW machine.
- Precision Cutting: as we discussed earlier, ceramic rings serve two main purposes: enhancing laser beam quality and focal length optimization. Both of these aid in achieving highly precise cuts, especially when working on uneven surfaces with laser materials processing.
- Reduced Splatter: all the excessive debris that comes out of the material being cut can get in the way of the cutting process. Ceramic rings reduce this splatter, especially during metal cutting, paving the way for finer and cleaner cuts along the cutting edge.
- Chemical Resistance: another good thing about ceramic rings is that they show incredible resistance to degradation and corrosion. Therefore, they help improve the longevity and safety of the laser cutting machine even when working with corrosive materials.
- Cost Saving: all of the benefits discussed above prove that ceramic rings act as a protective barrier that enhances laser machine performance. Hence, you won’t have to invest in new parts or a new machine anytime soon if you use ceramic rings as an accessory for your laser machines.
Types of Ceramic Rings for Laser Cutting
Here are the four main types of ceramic rings for laser cutting:
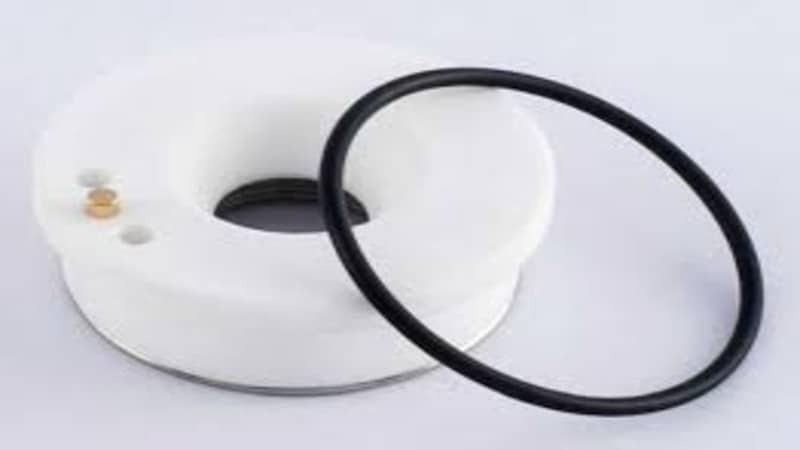
Zirconia
These ceramic rings are known for their excellent mechanical properties. This includes commendable strength, wear resistance, corrosion resistance, and general toughness. Moreover, zirconia rings can withstand sudden temperature changes smoothly.
The only drawback with these ceramic rings is that they are usually more expensive than other options. Hence, only use them for when needed for your laser metal cutting machine.
Alumina
Manufacturers often use these ceramic rings with their laser cutting machines for their electrical insulation, wear resistance, and excellent thermal conductivity. And on the brighter side, they are much more economical compared to zirconia.
But there’s a catch. Alumina ceramic rings are vulnerable to cracking when put through rapid temperature change conditions which often happens in a laser metal cutting machine.
Silicon Nitride
Again, a relatively more expensive option. However, the higher cost does come with its benefits, such as great temperature stability, superior fracture toughness, and low thermal expansion. Additionally, these rings show great resistance to oxidation, corrosion, and regular wear.
Silicon Carbide
Even though silicon carbine rings are prone to breaking or cracking upon stress or impact, they do have a fair share of advantages. This includes good wear resistance, brilliant hardness, and thermal conductivity. Also, you can rely on these rings to withstand temperature changes with ease.
Advantages and Disadvantages: A Comparative Analysis
Ceramic Ring Type | Pros | Cons |
Alumina ceramic rings | – High thermal conductivity – Electrical insulation – Wear resistance – Affordable | – Brittle and prone to cracking – Not suitable for rapid temperature changes |
Zirconia ceramic rings | – High mechanical strength – Toughness -Wear and corrosion resistance -Suitable for rapid temperature changes | – More expensive |
Silicon nitride ceramic rings | – High fracture toughness High-temperature stability – Low thermal expansion – Wear, corrosion, and oxidation resistance | – More difficult to manufacture – More expensive |
Silicon carbide ceramic rings | – High hardness – Wear resistance – Thermal conductivity – High temperature and thermal shock resistance | – Brittle and prone to cracking – Not suitable for impact or stress |
Factors to Consider When Choosing the Right Ceramic Ring for Your Laser Cutting Machine
Anyone out there to get ceramic rings for their laser cutting machines must consider the following:
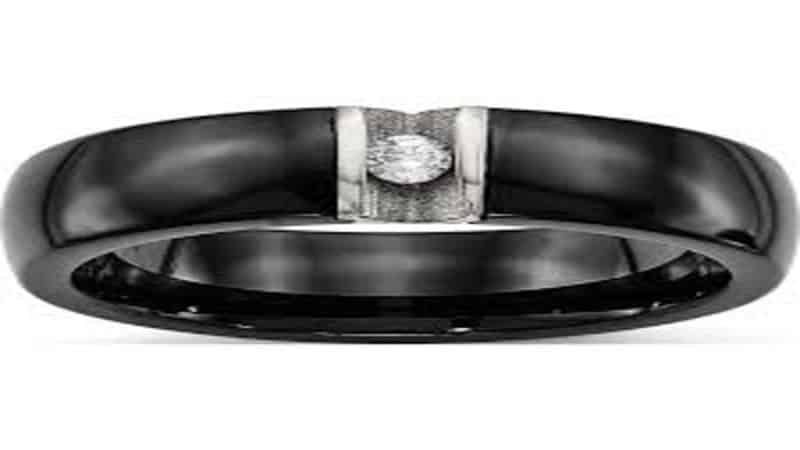
- Cutting Materials: different materials are compatible with certain types of ceramic rings. For example, silicon carbine rings are best suited for hard materials such as metal alloys. On the other hand, zirconia ceramic rings are more compatible with delicate materials such as glass or ceramic itself.
- Laser Power: high laser power generates high heat. As a result, you will need to work with a ceramic ring that has good thermal stability. For instance, silicon nitride has excellent thermal stability, which works best with high laser powers.
- Cutting Speed: here again, a higher cutting speed requires ceramic rings with high thermal conductivity. You can opt for either silicon nitride or alumina ceramic rings.
- Nozzle Design: different nozzle types are compatible with different types of ceramic rings. For example, if you are working with a conical nozzle, then you have to get a matching conical shape ceramic ring for proper alignment and minimal splatter.
- Maintenance and Cost: Ceramic rings come at different costs, as discussed earlier. While some are more expensive and require high maintenance, others can balance those well. It would be best if you made an informed decision based on your business needs.
What Are the Common Problems Encountered in the Ceramic Ring of Laser Cutting Machines?
- Wear and Tear: despite having good resistance to regular wear and tear, prolonged and excessive use can cause damage to the rings. This affects their performance as well as reduces service life.
- Cracking or Chipping: Ceramics on its own is a brittle material. As a result, it is prone to chipping or cracking, especially when put under stress or sudden temperature changes. Now, this won’t happen every time, but it can happen if you have used a ceramic ring for a long time.
- Clogging: with laser cutting comes the clogging problem, and ceramic rings are not foreign to it. Clogging, in fact, impacts their performance and requires frequent cleaning for efficient cutting.
- Warping: laser cutting puts ceramic rings through extremely high temperatures. When this keeps happening for prolonged periods, the ceramic rings eventually become prone to warping. This poses a threat to the cutting nozzle and also impacts cutting precision.
- Thermal Shock: if a ceramic ring goes through rapid thermal shocks repeatedly without any breaks for a long time, it can crack or break depending on the quality you get.
- Contamination: the existence of foreign particles can contaminate ceramic rings leading to poor cutting precision and the need for replacements sooner than required.
Future of Ceramic Rings in Laser Cutting
Laser cutting is a hallmark of the future of manufacturing. As a result, the future of ceramic rings in laser cutting is equally bright. In fact, new evolvements and innovations are expected, such as nanoceramics which are designed to have improved wear resistance and even greater strength.
For instance, a study conducted by the University of Delaware concluded that nanoceramic coatings on steel could reduce wear by up to 90%.
Additionally, other studies have solved problems previously encountered with cutting CFRPs. The Fraunhofer Institute for Laser Technology recently developed a ceramic nozzle that significantly reduces delamination when cutting through carbon fiber-reinforced polymers (CFRPs).
More technology recently showcased how sensors can be incorporated into ceramic rings to detect potential cracking in real time. The credit goes to the University of Sheffield, which developed a fiber-optic-equipped ceramic ring that has crack-detection capabilities.
Conclusion
Ceramic rings are undoubtedly one of the best accessories for your laser-cutting machines. Whether you wish to improve machine performance or add a layer of protection to certain components, it does the job well. Additionally, with more research and development, ceramic rings are bound to become a must-have accessory for this industry.
Optimize Your Laser Cutting Productivity with Our Leading Edge Machines
Baison is an industry leader in laser metal cutting machine manufacturing. Our two decades of experience working with customers in more than 100 countries has only taught us one thing: every customer is unique. Hence, we offer customizable laser–cutting solutions to suit your business needs. Ask for a Quote.