From additive manufacturing and component repair to surface coating and customization of material properties, laser deposition welding has emerged as a go-to solution for businesses seeking to enhance efficiency, reduce waste, and elevate the quality of their products.
In this article, we delve into the fundamentals of laser deposition welding, exploring its applications, benefits, and key considerations for selecting the right machine.
What is Laser Deposition Welding?
Laser deposition welding (also called laser cladding) is an advanced manufacturing process built on the Laser Metal Deposition (LMD) technique. This technology uses a high-power laser beam to heat a metal surface locally while a filler metal (thin wire or fine powder) is introduced to the surface, resulting in a study bond.
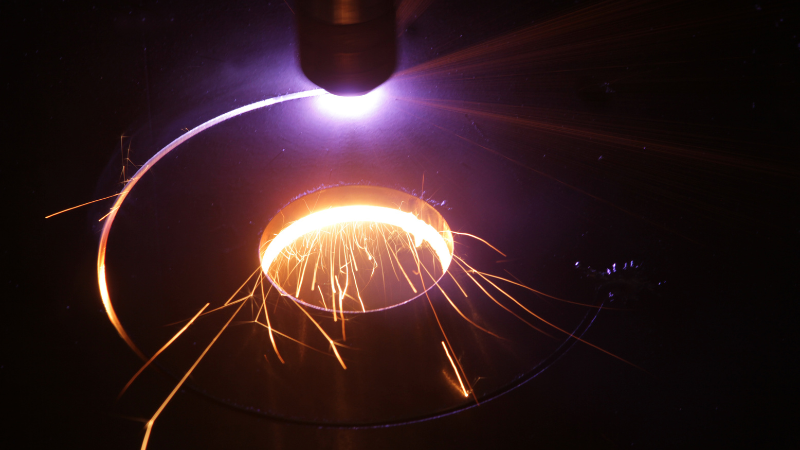
Laser deposition is primarily an automated process utilizing CNC (computer numerically controlled) technology to control the feed rate of the filler material, the intensity of the laser beam, and the path of the laser head.
The process is employed in several industrial applications, including surface coating (laser cladding), repairing, and modifying parts.

Types of Laser Deposition Welding
Laser metal deposition (LMD) driven welding can be divided into two main groups.
- Manual Laser Deposition Welding
- Automatic Laser Deposition Welding
I. Manual Laser Deposition Welding
Manual deposition welding uses a thin metal wire as the filler material. The wire thickness ranges from 0.6mm to 0.15 mm. A high laser power quickly melts the workpiece surface and the metal wire, resulting in quick and robust welds.
An inert gas (commonly Argon) jet is used to keep the weld safe from the moist ambient air. Manual laser welding quality is dependent on the welder’s skill level. Experienced welders can maintain a high weld speed while ensuring consistency throughout the process.
Wire welding can be uneven, and post-weld, grinding, milling, or EDM (Electrical Discharge Machining) is required for a cleaner finish.
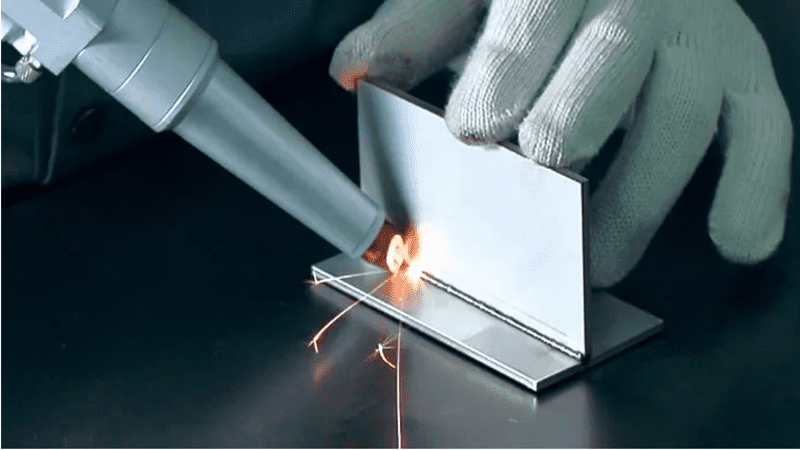
II. Automatic Laser Deposition Welding
Automatic laser welding has two or more nozzles attached to the laser head. Both the nozzle and the laser head move according to the CNC control system for consistent and accurate welds.
The nozzles spray powder metal particulates alongside a shielding gas (inert gas) at the laser contact point, fusing the filler metal as it touches the base material. As the metal powder is extremely fine, the resulting weld is without pores or cavities, providing high tensile strength at the weld joint.
Automatic laser metal deposition is commonly used to cover base metals in other tougher materials for better scratch and corrosion resistance.
Continuous layer build-up on the base material is called additive manufacturing and is a core element of laser metal deposition. Welding is only a small part of the LMD process.
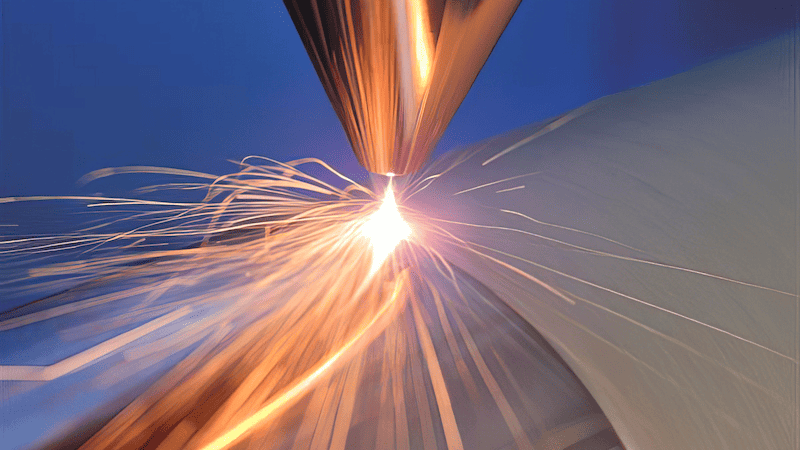
How Does Laser Deposition Welding Work?
Laser deposition welding is a complex process that requires a lot of preparation work before the laser is turned on.
Following are some key steps involved in the process.
Step 1 – Surface Preparation
Metal billets and ingots come with protective surface coatings. These coatings are typically oils for rust prevention, metal plating, or oxides, in the case of Aluminum.
You need to clean unwanted compounds and impurities off of the metal and rough up the surface. A rougher surface leads to better metal adhesion during the welding process. The microscopic bumps and cavities in the surface provide excellent anchor points for the molten filler metal to attach itself.
Step 2 – Filler Metal Delivery
The filler metal, typically a fine metal powder, flows out of an air jet nozzle with an inert gas (Nitrogen or Argon). The inert gas prevents oxidation, blows away unwanted surface impurities, and keeps the welds clean and slag-free.
Creating a fine and consistent metal powder is an expensive process. It typically takes more effort to create the metal powder than the laser deposition welding itself.
Hence, many laser deposition machines use a thin metal wire instead. The metal wire can be manually fed by hand or automatically through a motor and roller system adjacent to the laser head.
It should be noted that the filler metal can be the same as the workpiece for welding and different for surface coating.
Step 3 – Localized Laser Heating
A high-powered laser beam is directed at the desired location using a precise CNC system. The laser melts the workpiece surface and the incoming filler metal in a fraction of a second.
Laser beams input a fixed amount of energy into the workpiece, which is determined by the wattage of the laser source, and the spot diameter controls the deposit area of the energy. The laser spot diameter is the size of the laser contact point with the workpiece.
A larger spot size means the energy is more spread out, and it takes more time to melt the surface. While a smaller spot diameter means all of the laser energy is concentrated into a tiny point, decreasing the melt time.
Smaller spot size means higher precision and faster welding times. It also minimizes material warping as the heat is concentrated in a single spot, and no excess heat radiates to the surroundings.
Step 4 – Layering and Multiple Passes
Laser metal deposition (LMD) isn’t limited to welding, and it is often used for manufacturing components from the ground up. After the initial laser pass, the laser head makes another round and deposits a new material layer over the first one. This process is repeated until a desired height is achieved.
For additive manufacturing, the layers keep going until a full part is constructed. In contrast, welding only takes one or two passes (layers).
The layer thickness and number of layers help control the amount of metal deposition.
Step 5 – Cooling and Solidification
Since the heat is localized, the weld area also cools relatively quickly, almost immediately after the laser moves away from the point.
The LMD process involves direct energy deposition to a small point on the workpiece. The smaller contact point means energy is used more efficiently, and therefore, the laser can move at a faster pace.
Faster lasers mean less overall energy and heat is deposited into the workpiece. Less heat deposited means faster cooling. Rapid cooling comes with an additional side effect, better microstructures.

7 Benefits of Laser Deposition Welding
Laser metal deposition (LMD) is an accumulation of years of research into additive manufacturing technology. Every aspect of laser metal deposition is designed with a single goal in mind – an improvement over traditional processes.
Here are some of the biggest benefits laser deposition welding has brought to the modern manufacturing process.
1. Faster Welding Times
High-wattage lasers quickly melt the workpiece, and a CNC controller rapidly moves the laser head from one point to the other, resulting in incredibly fast welding times.
Automatic material feed enables continuous welding without any stops in the process. Computer-controlled welding also minimizes errors, saving even more time on the production floor.
Managing and optimizing the various process parameters of laser metal deposition can improve welding efficiency and reduce production time.
2. Higher Precision and Control
Almost every laser metal deposition machine is automated and computer-controlled, except for a few handheld models. The high precision and control enable more complex welds at a faster speed.
Very few experienced welders can match the accuracy and precision of an automated laser welding machine.
3. Higher Quality Welds
The fine powder particles of the filler material fill the gap more efficiently, leading to a stronger weld. Since everything is pre-measured and computer-controlled, the amount of deposited metal is exactly as needed, meaning the weld pool stays consistent throughout the process.
Additionally, the use of an inter-gas jet prevents slag formation and metal oxidation and blows away small bits and pieces of vaporized metal.
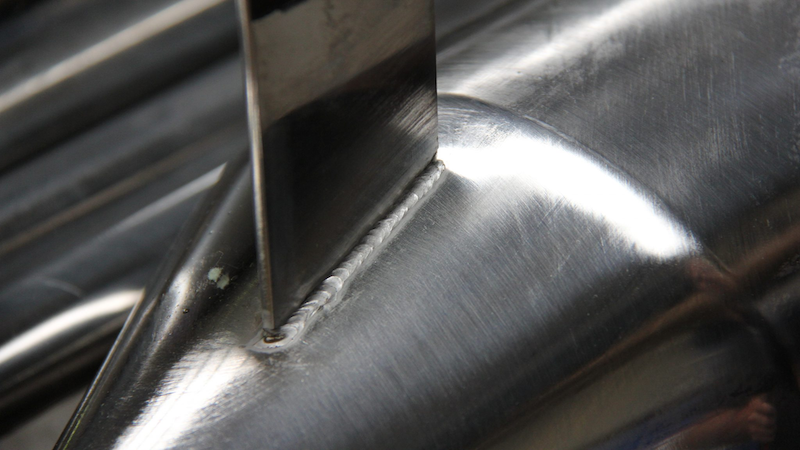
4. Zero Distortion from the Heat Source
Traditional welding processes introduce a bunch of unwanted heat to the base material. A small amount of heat goes to the welding point, while the rest seeps into the surroundings, resulting in metal distortion (warping).
Laser metal deposition is an incredibly precise process, the laser beam melts a small section of the workpiece and nothing more. In fact, the process is so efficient that it is often used for full surface welds as there is no fear of material distortion.
Surface welding is the process of coating a material with another material (or multiple materials) for improved surface finishing and wear resistance.
5. Wider Material Compatibility
Welding gets significantly harder as you move to higher quality and rarer materials. Traditional processes work with common materials like iron, copper, stainless steel, and even aluminum alloys. But struggle with specialized cases involving tough metals like tungsten, volatile metals like magnesium, and soft metals like gold.
Laser metal deposition supports a diverse range of metals, alloys, and even some ceramics. Using LMD, you can weld the following materials.
- Nickel Alloys
- Tungsten Carbide
- Magnesium Alloys
- Cast Iron
- Aluminum Alloys
- Cobalt Based Alloys
- Titanium Alloys
- Copper
- Steels
- etc.
6. Reduce Material Waste
Laser welding results in minimum material waste. The metal powders are fed to the workpiece at a controlled feed rate to avoid over/under deposition. Unlike traditional welding, which uses filler sticks, laser deposition welding uses continuous metal wires and powder particles.
Only the required amount of filler is used, while the rest is saved for the next weld.
7. Reduced Post Processing Work
Since laser metal deposition produces cleaner welds, often, you don’t even need to perform any post-processing. No need to clean the workpiece with a wire brush, grind down the excess weld pool, or straighten out distortions from the welding process.
Reduced post-processing saves a lot of time on the production floor and boosts productivity significantly.
Applications of Laser Deposition Welding
Following is a simple chat outlining the various industrial applications of laser metal deposition.
Industry | Application |
---|---|
Automotive Industry | Repairing and coating engine parts, transmission components, etc. |
Medical Devices | Repair and customization of metal implants. |
Tool and Die Industry | Repairing and refurbishing of old worn-out tools, molds, and dies. |
Oil and Gas Equipment | Repair and manufacturing of components used such as drilling tools, valves, and pump components. |
Electronics Manufacturing | Repair and modification of delicate electronic components and connections. |
Aerospace Maintenance | Repairing and manufacturing components such as turbine blades, engine parts, and other high-value and complex structures. |
Aerospace Manufacturing | To apply protective coatings on components, enhancing properties such as wear resistance, corrosion resistance, and hardness. |
Due to the outstanding material compatibility of laser deposition welding, there are many applications in the industry, especially among manufacturers. You can contact our experts for details by clicking on the button below.

How to Choose a Laser Deposition Welding Machine?
Here is a list of important factors that will help you choose the right laser metal deposition machine for welding.
1. Laser Source
Laser metal deposition supports fiber and diode laser sources. Fiber lasers use more expensive components and can reach higher wattage.
Laser wattage determines the maximum heat generation of your machine. You need higher-wattage lasers to reach the high melting temperature of metals such as titanium and tungsten. 2-3 Kilowatt lasers are standard for high-volume productions and cover most applications.
2. Precision and Control
The laser spot diameter determines the welding precision of your machine. The laser head speed, measured in mm per second, determines the overall welding capacity.
You want as small of a spot diameter as possible and the fastest laser head speed available for maximum production efficiency.
3. Work Bed Size
A large work bed size results in higher machine and shipping costs. Carefully choose the appropriate bed size according to your needs.
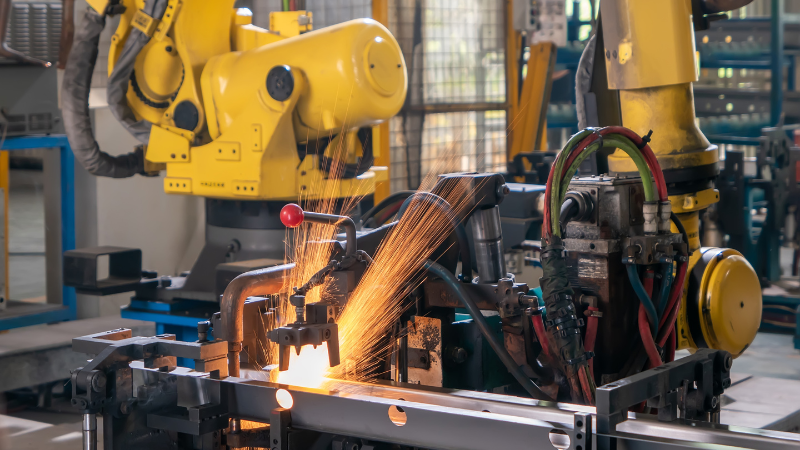
4. Cooling System
High-wattage lasers generate a lot of heat, especially around the power delivery system. If the cooling solution isn’t adequate, your laser metal deposition machine won’t operate at full capacity during longer work sessions.
5. Safety Features
Common safety features include a polarized glass shield covering the laser bed, a fume hood, and emergency shut-off controls.
6. Operator Training and Support
Operator training is always a crucial step in the industrial setting. Most reputable laser welding machine manufacturers offer free online and on-site training. Proper training reduces safety hazards and increases productivity.
FAQs
1. What Materials are Compatible with Laser Metal Deposition Welding?
Laser metal deposition is compatible with almost every type of Copper, Aluminum, Titanium, Steel, Magnesium, and Nickel-based alloys.
2. What is Laser Deposition Welding Used For?
Laser metal deposition welding is used for welding metals, repairing damaged metal parts, coating softer metals, and fabricating parts using additive manufacturing.
3. How Expensive is Laser Deposition Welding?
Manual laser deposition welding using metal wires is relatively inexpensive (<$8,000). However, automated welding using metal powder is significantly more expensive (>$100,000).

Conclusion
Laser Metal Deposition (LMD) is a unique additive manufacturing process that enables several different applications, from welding to surface coating to full-on parts manufacturing. This technique is a one-stop solution for small to medium-sized businesses looking to automate their manufacturing workload. It’s a faster, more precise, and safer way to weld complex parts.
Experience Laser Precision with Baison!
Baison is the premiere laser welding systems manufacturer in China, serving international clients in over 100 countries and regions for the past 20 years. Our state-of-the-art Laser Welding Robot is designed to tackle all manufacturing challenges.
We also offer Free Application Evaluation so you get the best laser machine according to your needs. With each sale, we offer robust Customer Training courses to help you get running as quickly as possible. Take your business to the next level with Baision. Contact us Today!