Laser cutting is an incredibly versatile and precise means of manufacturing. From cutting thin sheets of aluminum to cutting thick rubber foam, nothing can stand up to the might of the laser beam. Different laser-cutting processes can be employed depending on your application, material choice, laser power, and desired outcome.
In this article, we will explore the different types of laser cutting processes, highlight their applications, and help you choose the best one for your business.
What is Laser Cutting Technology?
Laser cutting is a non-contact manufacturing process that utilizes a focused laser beam to selectively melt the workpiece. The laser cutting head is controlled by a CNC (computer numerically controlled) system that accurately and precisely directs the laser.
This process is compatible with several material options, such as metals, plastics, fabrics, ceramics, wood, etc. In stark contrast to conventional material processing techniques, laser cutting is fast, accurate, requires less post-processing, and is more reliable.
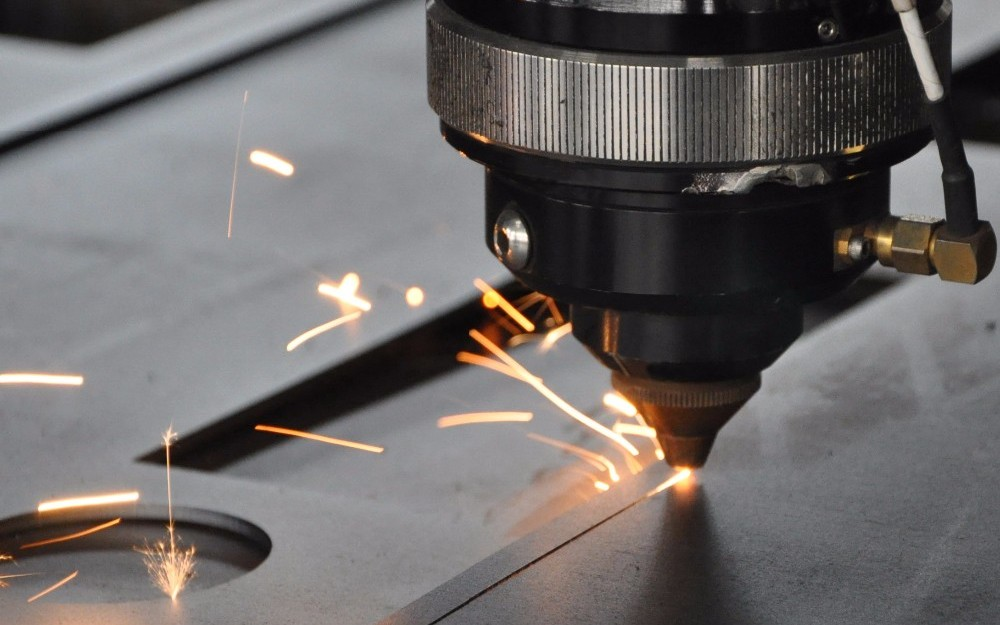
Types of Laser Cutters
Laser cutting equipment is generally classified based on the laser source.
- Gas Lasers (CO2 Lasers)
- Fiber Lasers
- Solid State Lasers (Nd: YAG Lasers)
- Direct Diode Lasers
Carbon Dioxide (CO2) laser cutters are an older technology but are still relevant for their affordability, power, and convenience. Nd: YAG lasers(neodymium-doped yttrium aluminum garnet lasers) are low-power and high-reliability options primarily used in the medical industry for skin treatment. Solid state cutters are often branded as crystal laser cutters, since Nd: YAG is classified as a crystal.
Direct Diode Laser cutters are compact machines that can output an impressive amount of energy from a small form factor. Finally, we have Fiber Laser, the technology with the most versatility and potential. Fiber laser cutters are the best of both worlds, matching the high power of CO2 and the compact design of diode laser cutters.
Do You Have Any Questions?
Let Us Solve Your Problem
7 Different Types of Laser Cutting Processes
Laser cutting is a diverse and versatile manufacturing technique that can be modified to adapt the process to different applications.
1. Fusion Laser Cutting (Melt Cutting)
Laser fusion cutting is the standard mode of operation for a laser cutter. It uses a high-intensity laser beam to input lots of heat into a small area on the workpiece until the metal reaches a molten state. At this point, a jet of inert gas (Nitrogen, Helium, or Argon) blows away the molten metal.
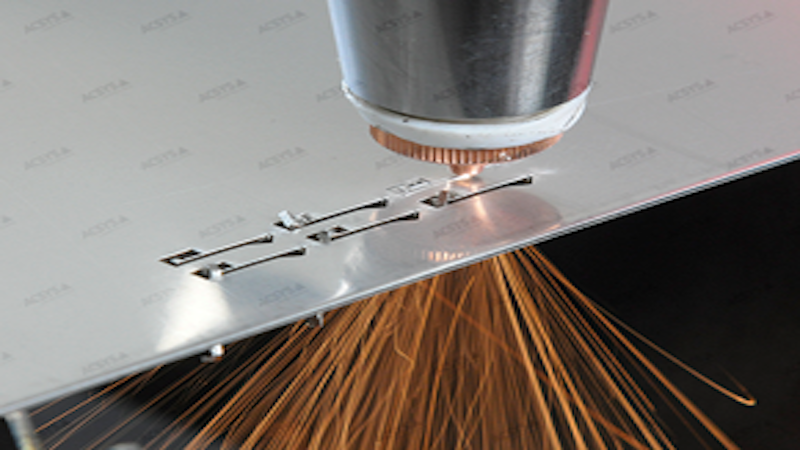
The process requires the laser beam to stay in one place for a long time until melting starts. Since the molten material is a lot softer, the gas jet can easily slice through. The gas or gas mixture must be inert to prevent metal oxidation. It is also called a shielding gas as it shields the working material from the surrounding oxygen.
Applications
- Cutting metal materials (aluminum, copper, steel, nickel, titanium, etc.).
- Typically used for large volume low accuracy productions.
2. Vaporization Laser Cutting (Laser Sublimation Cutting)
Vaporization is a non-metal cutting process that holds the laser beam in one place until the work material heats and vaporizes away. It also uses an inert gas jet. However, the primary goal is to blow away the vaporized particles and not prevent oxidation.
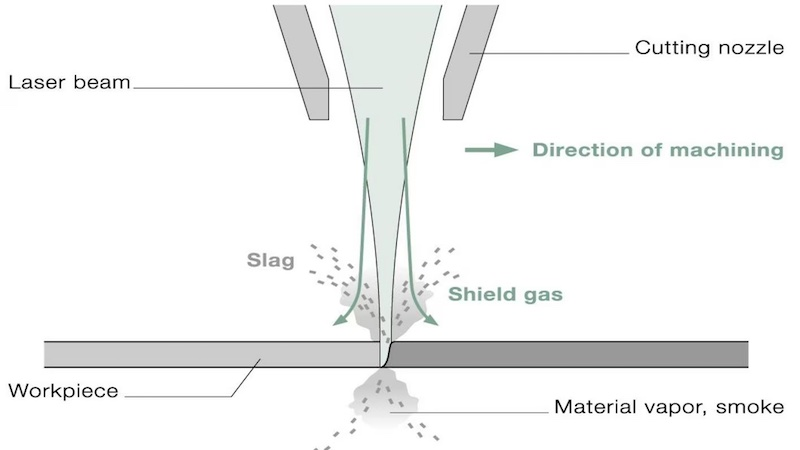
Thicker materials require more heat and longer laser exposure times, leading to greater vaporization and, thus, greater material loss. Laser Vaporization can be used for low-melting point metals like Tin or Lead. However, these metals are better suited to traditional processing techniques.
Applications
- Cutting non-metallic materials (paper, fabrics, wood, plastic, rubber, etc.).
- Used for non-industrial design and fabrication work, such as art, furniture design, etc.
3. Remote Laser Cutting
Remote Laser Cutting is a sublimation-based manufacturing process that vaporizes metal material without requiring a gas jet. As there is no gas jet to assist with material removal, remote-cutting machines are primarily limited to thin sheets of metal.
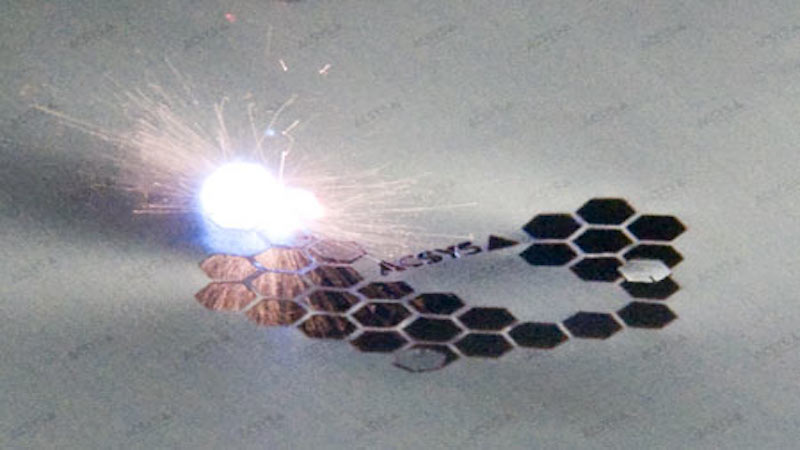
Applications
- Sheet metal cutting (aluminum and steel).
- Cutting simple geometric designs.
4. Oxygen Laser Cutting
Standard melt laser cutting is limited to a material thickness of 0.6″ (15mm) at sub 2kW laser power and 1″ (25mm) for anything above 2kW. Laser Assisted Oxygen Cutting (LASOX) enables standard 2kW laser cutters to cut extra thick materials 2″-4″ (50mm to 100mm).
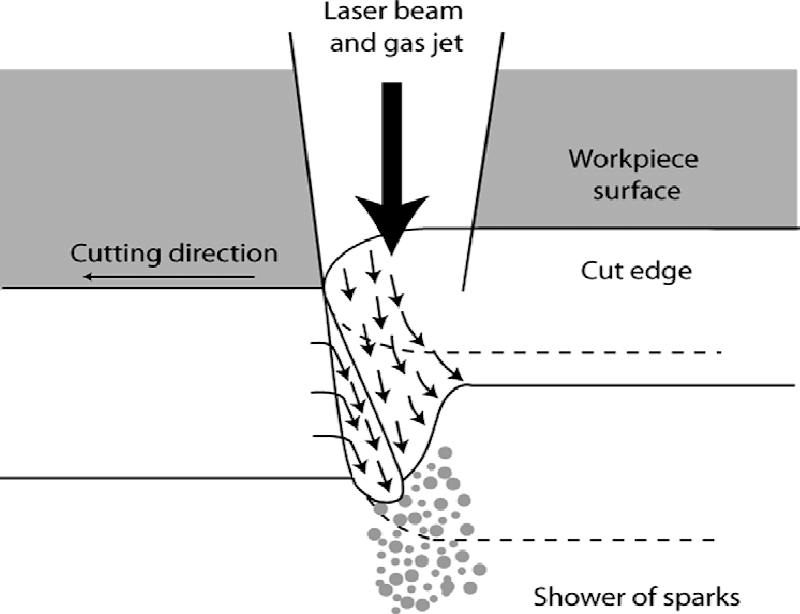
Image source: ResearchGate
As the name suggests, oxygen replaces the standard inert gasses used in laser cutting here. Oxygen acts as a fuel, increasing the laser’s heat at the focal point and significantly raising the temperature. LASOX also improves the overall cutting speeds for thick materials.
Applications
- Cutting thick materials (steel, stainless steel, and aluminum).
- Manufacturing metal blanks (rough shapes for further processing).
- Heavy machinery manufacturing.
5. Flame Laser Cutting
Laser flame cutting uses a jet of oxygen fuel gas mixture to increase the heating and vaporization capabilities of the laser cutter. Common gas fuel options include propane, natural gas, or acetylene. This process is also known as oxy-acetylene or oxy-fuel laser cutting.
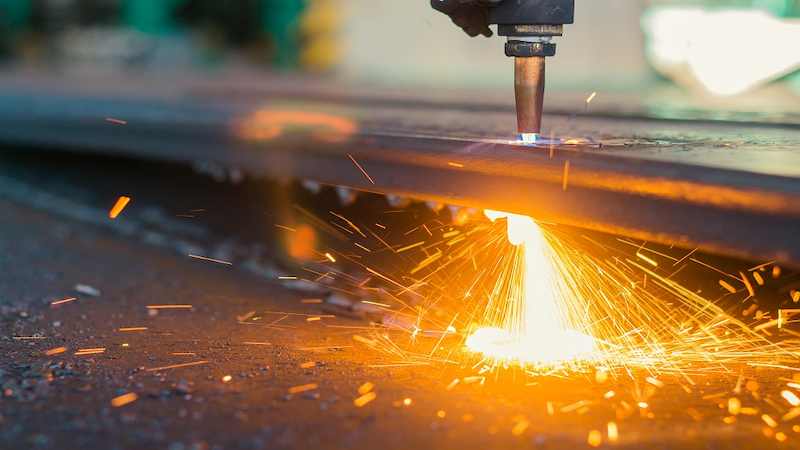
Unlike LASOX, a proprietary manufacturing technique that only uses oxygen, flame cutting is a generic, non-trademark process compatible with various fuel mixtures. The key difference here is the gas mixture used to augment the laser beam.
The oxygen and acetylene mixture produces a hotter flame, matching plasma cutting capabilities. Flame cutting supports a maximum material thickness of 10″ (270mm).
Applications
- Cutting thick materials (steel and aluminum).
- Processing metal billets and ingots.
6. Zero Width Laser Cutting (Thermal Stress Laser Cutting)
Zero Width Laser Cutting (ZWLC) uses fiber lasers (controlled bursts) in conjunction with a cooling jet (water or coolant) to initiate internal thermal stresses in the material to initiate micro-cracks. These controlled micro-cracks shatter the material along the desired scribe line (zero-width) without any material loss.
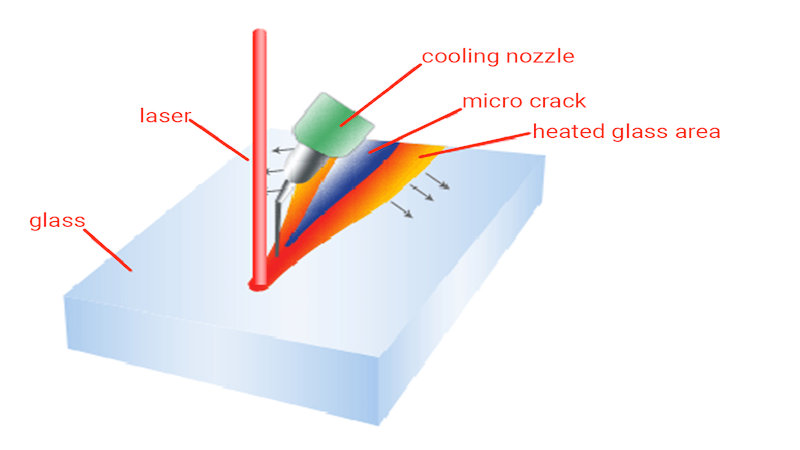
Micro cracks are generated from a difference in the expansion rate of a material. Zero-width heats up materials like glass just enough to initiate thermal expansion. The accompanying cooling jet then cools down the glass, creating a gradient between the hottest and coldest parts, resulting in high internal thermal tensile stresses.
Laser melt cutting removes (vaporizes) material equal to the spot diameter (focus point of the laser). This material loss decreases the overall cutting accuracy of the laser cutter. Hence, zero-width laser cutting is used for high-dimensional accuracy projects.
Applications
- High dimensional accuracy application.
- Brittle materials like glass sheets and ceramics.
7. Controlled Fracture Laser Cutting
Controlled fracture laser cutting machines work by inducing thermal stresses in brittle materials. Unlike ZWLC, it initiates cracks without needing a coolant. It will occasionally require a mechanical shock to separate the two sides of the material.
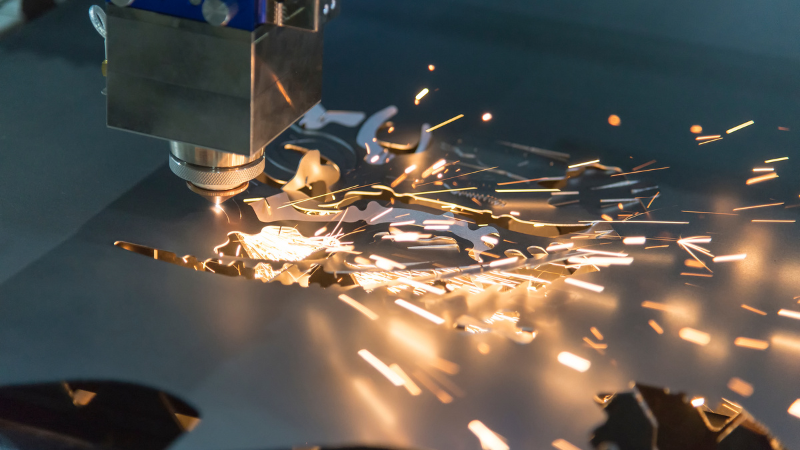
Standard controlled fracture laser cutters use carbon dioxide (CO2) lasers to heat the material, causing it to expand and inducing compressive stress. On cooldown, the heater material contracts and ends up in a state of tensile stress.
An alternate technique involves the use of CO2 and fiber lasers in conjunction. Fiber lasers produce a powerful focused laser beam that easily scores through the toughest materials. CO2 lasers provide a more gentle heat that heats up the workpiece without initiation.
Applications
- High-hardness materials (alumina ceramics, glass, silicone carbide, etc.)
- Cutting Gems (Zirconia, Ruby, etc.)
Do You Have Any Questions?
Let Us Solve Your Problem
Choosing the Right Laser Cutting Process
Picking the right laser-cutting process is all about application preference and material compatibility. Here are a few important factors that will help you decide.
1. Application and Material Properties
Outline your business’s current applications and identify future needs as you expand and grow. Businesses primarily dealing in metal-cutting applications will benefit from fusion and flame-cutting processes. For everything else, vaporization cutting will be perfectly adequate.
2. Material Thickness
Material thickness is typically not a concern for most industries. Laser-cutting machines can handle most materials with ease. However, the only suitable option for metal plates with a thickness of 1″ or greater is a gas-accelerated laser cutting process such as oxygen or flame cutting.
3. Laser Source
Carbon dioxide and fiber lasers are the two most common sources of laser cutters. CO2 is generally recommended for low-cost and high-performance applications. Fiber lasers are better for high precision, versatility, and reliability-oriented tasks.
4. Operating Costs
Flame cutting offers better versatility and can cut a more diverse range of metals. But the operating costs are significantly higher mainly due to the fuel gas. Consumables like oxygen or acetylene lose efficacy while stagnant in a gas tank and require frequent monitoring.
5. Laser Cutting Machine Size
Some processes require a larger work bed, which has its own logistical challenges. Ensure that your chosen laser-cutting process is compatible with your factory floor space.
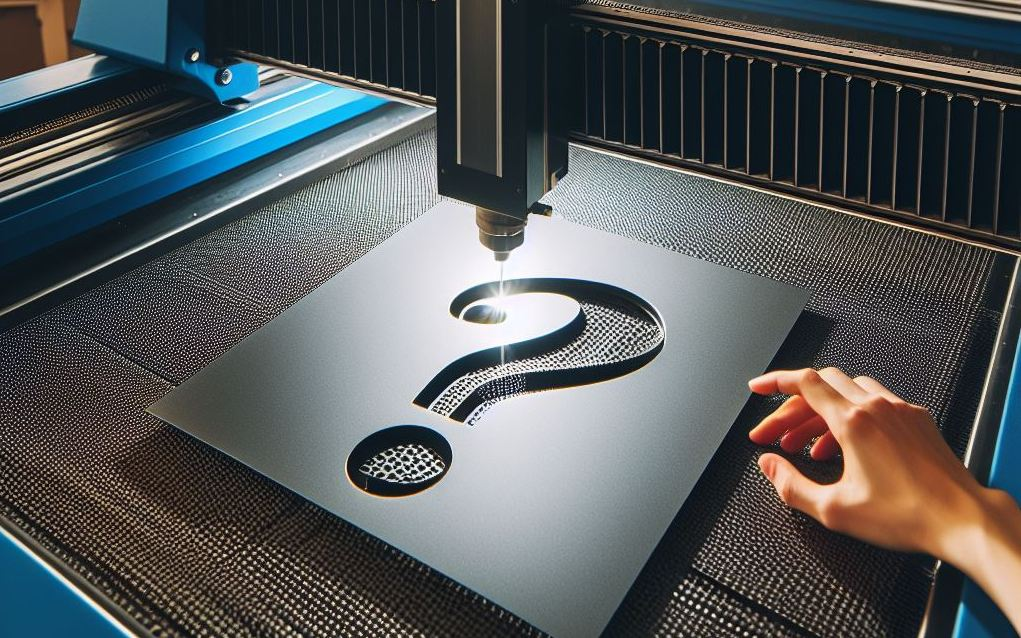
6. Return on Investment (ROI)
The initial investment into a specific laser-cutting process will always be significantly higher. A good ROI for a single laser cutter is roughly 30%, but for a large factory dealing with multiple laser cutters, an annual ROI of 10% is acceptable.
FAQs
1. Which Gas is Used in Laser Cutting?
Most laser cutting machines offer an inert gas (Nitrogen or Argon) jet that prevents metal oxidation. Some laser cutters use an oxygen and fuel gas (acetylene, propane, or natural gas) mixture to increase the heat output of the laser cutter. Click here to learn more about gases for laser cutting.
2. What is the Full Form of LASER?
LASER stands for Light Amplification by the Stimulated Emission of Radiation. The type of laser is determined by its means of amplification. For example, fiber lasers refer to light amplified by an optical fiber system.
3. Why is Nitrogen Used in Laser Cutters?
Nitrogen is a non-reactive gas that doesn’t interfere with the laser-cutting process. It prevents oxygen from entering the cutting area, which prevents discoloration and oxidation.
Do You Have Any Questions?
Let Us Solve Your Problem
Conclusion
Laser cutting is a whole field of laser-based manufacturing techniques. It offers many benefits over traditional manufacturing processes, such as smaller form factor, broader material compatibility, and excellent precision.
Laser cutting further increases your productivity by offering an expansive selection of cutting processes that cater to different markets. Hence, it’s unsurprising that almost every modern industrial manufacturing process utilizes a laser cutting machine.
Experience the Best of Laser Technology with Baison Laser!
Baison is the leading manufacturer and supplier of laser solutions across the globe. With over 300 patents and a large R&D staff, we stand atop the mountain of laser technology. Baison laser cutters are equipped with the finest components and come in CO2 and Fiber varieties.
Our FREE Application Evaluation program will help you choose the right laser-cutting process for your business. Let Baison be your guide to success. Contact Us Now!