When it comes to fiber laser machines, selecting the right laser parameters is crucial for achieving optimal results. However, with so many variables to consider, it can be challenging to determine the ideal settings for your specific application.
In this guide, we’ll walk you through the process of selecting the right laser parameters for your fiber laser cutting machine. By following our tips and guidelines, you can ensure that your machine is operating at its full potential, delivering high-quality and precise results every time. So, let’s get started!
What Are Laser Parameters?
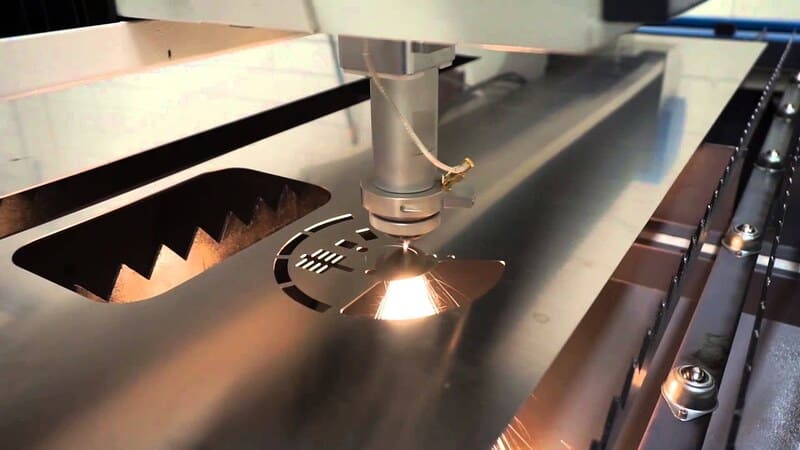
Fiber laser settings are the key characteristics that define the behavior and output of a laser. These parameters include the following:
- Wavelength: The distance between two consecutive peaks or troughs of the laser beam’s electromagnetic wave. The wavelength determines the laser’s color and affects its interaction with materials.
- Power: The amount of energy per unit of time the fiber lasers deliver. A laser cutter’s power determines its cutting or engraving speed and ability to penetrate or heat up materials.
- Pulse duration: The time interval over which the laser emits a pulse. Pulse duration affects the laser’s material removal rate and thermal effects.
- Repetition rate: The number of pulses emitted per unit of time. Repetition rate affects the laser’s throughput and efficiency.
- Beam quality: A measure of how closely the laser beam’s properties match that of an ideal, single-mode Gaussian beam. Beam quality determines the laser’s focusability and spot size.
- Polarization: The orientation of the electric field vector of the laser beams. Polarization affects the laser’s interaction with certain materials and optical components.
- Mode structure: The spatial distribution of the laser beam’s intensity across its transverse dimensions. Mode structure determines the laser’s cutting or drilling pattern and the quality of its edges.
Some Additional Parameters to Look for
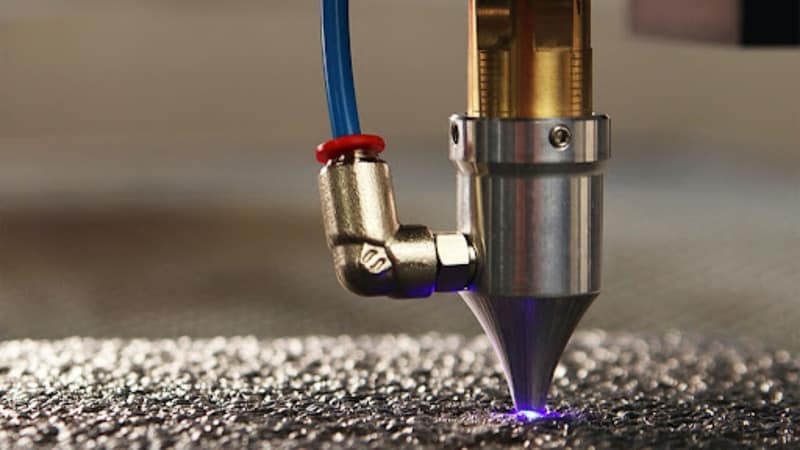
- Focus position: The distance between the laser’s focal point and the workpiece surface. The focus position affects the laser’s depth of focus and the quality of its cuts or engravings, so finding the ideal focus position is important.
- Gas flow rate: The rate at which assist gas is supplied to the cutting or engraving zone. The gas flow rate affects the quality of the laser’s edges and the removal of debris.
- Beam diameter: The diameter of the fiber laser at its focus. The beam diameter affects the laser’s spot size and its intensity at the workpiece surface.
- Beam divergence: The angle at which the laser beam spreads out as it travels away from the laser source. Beam divergence affects the laser’s focusability and depth of field.
- Pulse overlap: The degree of overlap between successive laser pulses. Pulse overlap affects the laser’s material removal rate and the quality of its edges.
- Duty cycle: The fraction of time that the laser is in the “on” state during a given period. The duty cycle affects the laser’s average power and its thermal effects on materials.
- Scanning speed: The rate at which the laser beam is moved across the workpiece surface. Scanning speed affects the laser’s throughput and the quality of its cuts or engravings.
Do You Have Any Questions?
Let Us Solve Your Problem
How to Measure Laser Parameters in a Fiber Laser Machine?
Measuring the fiber laser setting is an essential step in optimizing the performance of your fiber laser cutting machines. Here are some common methods for measuring the laser parameter:
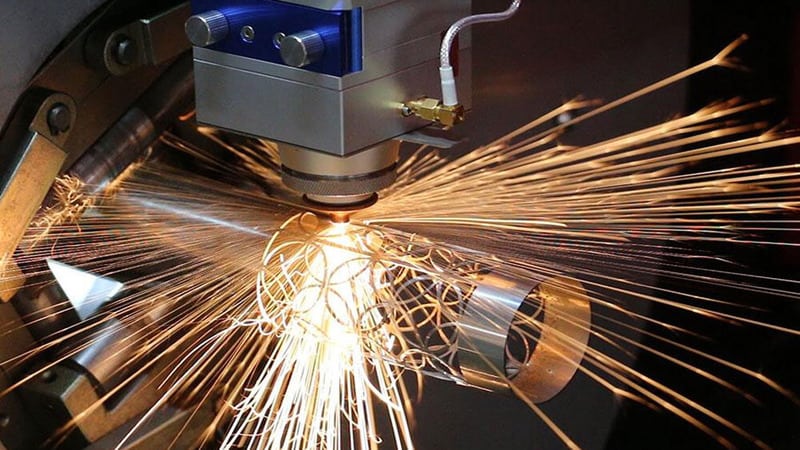
- Power meter: A power meter measures the output power of the laser beam in watts or milliwatts. This is a critical parameter to measure as it affects the laser’s cutting or engraving speed and its ability to process certain materials.
- Spectrometer: A spectrometer measures the wavelength of the laser beam in nanometers. This parameter is important for choosing the right laser for your application and for ensuring the laser’s output is within the specified range.
- Beam profiler: A beam profiler measures the intensity profile of the laser beam, allowing you to visualize the beam shape and size at the focus. This is important for ensuring the laser is properly focused and for optimizing cutting or engraving quality.
- Autocorrelator: An autocorrelator measures the pulse duration of the laser beam in femtoseconds or picoseconds. This parameter is important for optimizing laser-material interactions and for achieving precise cuts or engravings.
- Polarimeter: A polarimeter measures the polarization state of the laser beam. This parameter is important for applications where polarization affects the quality of the cutting or engraving, such as with certain materials.
- Interferometer: An interferometer measures the beam quality of the laser by analyzing the phase and intensity of the beam. This parameter is important for ensuring the laser’s beam is uniform and for optimizing cutting or engraving quality.
In summary, measuring laser parameters involves using various instruments and methods to determine the laser’s power, light wavelength, pulse duration, beam shape, polarization, and beam quality.
By measuring these parameters accurately, you can optimize the performance of your fiber laser cutting machine and achieve better results in your laser processing tasks.
How do Laser Parameters Influence Laser Cutting quality?
Laser parameters play a crucial role in determining the quality of laser cutting. Here are some ways in which fiber laser settings can influence the cutting quality:
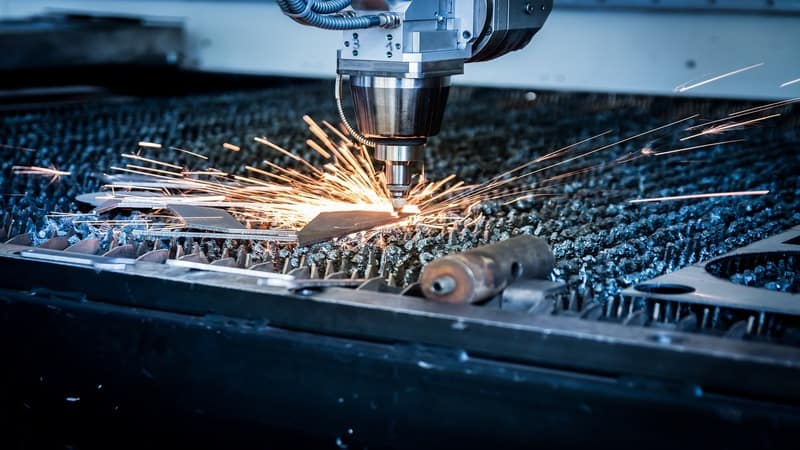
1. Power
Laser power affects the cutting speed and quality. Higher power can increase the cutting speed but also cause more thermal damage to the material, resulting in a rougher edge quality. Lower power settings can provide finer control and higher edge quality.
2. Pulse Frequency
Pulse frequency determines how many laser pulses are fired at the material per second. Higher pulse frequency can result in smoother and more precise cuts but may also increase the likelihood of thermal damage. Lower laser pulse frequencies can provide better control over the cutting process.
3. Wavelength
The wavelength of the laser beam determines the absorption characteristics of the material being cut. Different materials have different absorption properties, which means that the optimal wavelength for cutting will vary depending on the material being cut.
For example, CO2 lasers with longer wavelengths of 10.6 microns are commonly used for cutting non-metallic materials, while fiber lasers with shorter wavelengths of 1 micron are better suited for cutting metals. In order to choose the right laser technology, you need to understand the difference between CO2 and fiber laser technology.
4. Lens Type
The focusing lens used in the laser cutting system can affect the beam quality and focal spot size, which in turn can affect the cutting quality. Different lens types are available for different cutting applications, such as focusing lenses for general-purpose cutting and collimating lenses for marking and engraving.
5. Laser Beam Diameter
The diameter of the laser beam affects the focusability and intensity of the laser beam. Smaller beam diameters can provide higher precision and finer detail in the cutting process but may also be more prone to deflection or beam distortion.
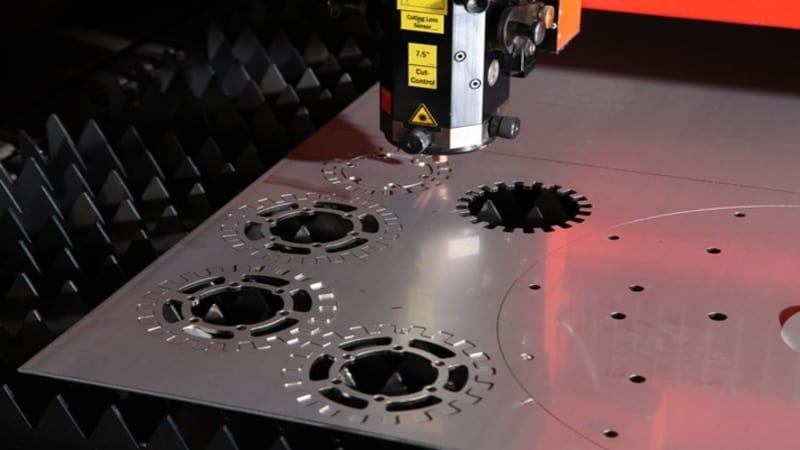
In summary, selecting the right fiber laser settings for your cutting application can significantly impact cutting speed, precision, and quality. By understanding the influence of power, pulse frequency, wavelength, lens type, and beam diameter, you can optimize your laser cutting process and achieve better results.
Do You Have Any Questions?
Let Us Solve Your Problem
How to Choose Laser Parameters for Different Materials?
Here are two tables to help you choose the right parameters for different cutting materials:
Material | 1000W | 2000W | 3000W | 4000W | 5000W | 6000W |
Aluminium | 2 mm | 4 mm | 6 mm | 8 mm | 10 mm | 12 mm |
Brass | 1 mm | 3 mm | 5 mm | 7 mm | 9 mm | 11 mm |
Carbon Steel | 0.5 mm | 2.5 mm | 5 mm | 7.5 mm | 10 mm | 12.5 mm |
Stainless Steel | 1 mm | 3 mm | 5 mm | 7 mm | 9 mm | 11 mm |
Material | 7000W | 8000W | 9000W | 10000W | 11000W | 12000W |
Aluminium | 14 mm | 16 mm | 18 mm | 20 mm | 22 mm | 24 mm |
Brass | 13 mm | 15 mm | 17 mm | 19 mm | 21 mm | 23 mm |
Carbon Steel | 15 mm | 17.5 mm | 20 mm | 22.5 mm | 25 mm | 27.5 mm |
Stainless Steel | 13 mm | 15 mm | 17 mm | 19 mm | 21 mm | 23 mm |
Note: The tables provide a general guideline, and the actual performance may vary depending on the specific laser machine and its configuration. It is always recommended to consult the laser cutting machine manual or the laser cutting machine manufacturers for the most accurate settings.
How to Optimize Laser Parameters for the Best Cutting Quality?
Here are some steps to help you optimize your fiber laser settings:
1. Determine the Optimal Laser Power
Start with the recommended power settings for the cut material, then gradually increase or decrease the power to find the optimal setting for the desired cutting quality. Keep in mind that higher power can result in faster cutting, but it may also cause more thermal damage to the material.
2. Adjust Pulse Frequency
Pulse frequency determines the number of laser pulses per second and can impact the cutting quality and precision. Higher pulse frequencies can provide smoother and more precise cuts but may also increase the likelihood of thermal damage. Adjust the pulse frequency to find the optimal setting for the desired cutting quality.
3. Select the Appropriate Lens Type
The type of lens used in the laser cutting system can affect the beam quality and focal spot size, which can impact the cutting quality. Choose the right lens type for your cutting application, such as focusing lenses for general-purpose cutting and collimating lenses for marking and engraving.
4. Determine the Optimal Laser Beam Diameter
The diameter of the laser beam can affect the focusability and intensity of the laser beam, which can impact the cutting quality. Choose the optimal beam diameter based on the desired cutting quality for your cutting application.
5. Ensure Proper Beam Alignment
Proper beam alignment is critical for achieving optimal cutting quality. Check and adjust the beam alignment regularly to ensure that the laser beam is properly focused on the material.
6. Monitor and Maintain the Laser System
Regular laser system maintenance and cleaning can help ensure optimal cutting quality. Monitor the system for any signs of wear or damage, and replace any worn or damaged components as needed.
By following these steps and continuously monitoring and adjusting your fiber laser settings, you can optimize your laser cutting process for the best cutting quality.
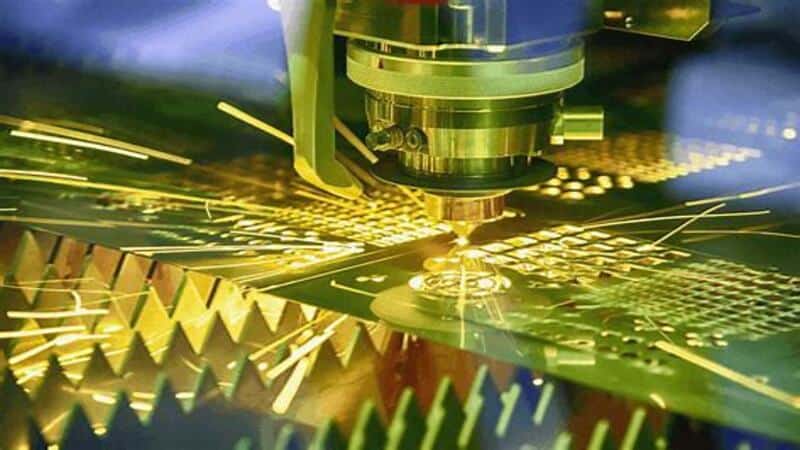
Common Misconceptions About Laser Parameters
Laser parameters play a crucial role in laser cutting, but some common misconceptions can lead to suboptimal cutting quality. Here are some misconceptions to watch out for:
- “More power always equals better cutting quality.” While increasing the laser power can increase the cutting speed, it can also increase the risk of thermal damage to the material. Finding the optimal power setting for the desired cutting quality is important rather than simply cranking up the power.
- “The higher the pulse frequency, the better the cutting quality.” While higher pulse frequencies can provide smoother and more precise cuts, they can also increase the likelihood of thermal damage to the material. Hence, the optimal pulse frequency for the desired cutting quality and material being cut is essential.
- “Beam quality doesn’t matter as long as the laser is powerful.” Beam quality can greatly impact the cutting quality, as it determines the focusability and intensity of the laser beam. A poor-quality beam can result in poor cutting quality, even if the laser power is high.
- “All lenses are the same.” Different lens types can impact the beam quality and focal spot size, which can greatly impact the cutting quality. Choosing the right lens type for the desired cutting application is crucial.
- “Laser parameters don’t need to be adjusted once they’re set.” Fiber laser settings should be regularly monitored and adjusted to ensure the optimal cutting quality. Factors such as material type, thickness, and cutting speed can all impact the optimal fiber laser settings for a given cutting job.
By avoiding these common misconceptions and regularly monitoring and adjusting laser parameters, you can achieve optimal cutting quality in your laser cutting process.
Do You Have Any Questions?
Let Us Solve Your Problem
Fine-Tuning Laser Parameters for Different Applications
When it comes to laser applications, different jobs require different laser parameters. For example, laser engraving requires different parameters than laser cutting, and laser marking requires different parameters than welding. Here are some tips for fine-tuning fiber laser settings for different applications:
I. Laser Engraving
Engraving requires a high pulse frequency and low power setting to achieve a precise, shallow cut. Short pulse duration and low repetition rate are also important for achieving a high level of detail. The optimal laser parameters will vary depending on the material being engraved.
II. Laser Marking
Laser marking requires a lower pulse frequency and higher power setting to achieve a deeper mark using the fiber laser marking machine. The pulse duration should be longer than in engraving, and the repetition rate should be high to ensure consistency.
The optimal laser parameters will depend on the material being marked and the desired mark depth of the fiber laser marking system.
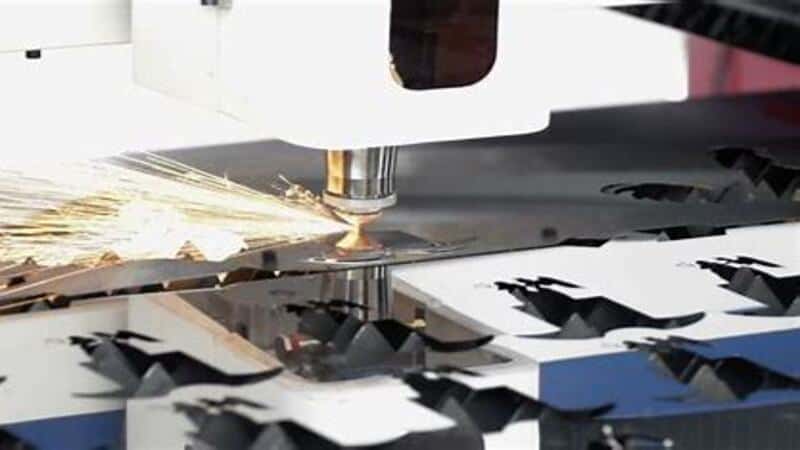
III. Laser Cutting
Laser cutting requires a high power setting and low pulse frequency to achieve a clean, efficient cut. The pulse duration should be shorter than in engraving or marking, and the repetition rate should be moderate. The optimal laser parameters will depend on the material being cut and the desired cut quality.
IV. Laser Welding
Laser welding requires a high power setting and long pulse duration to achieve a deep, strong weld. The pulse frequency should be low, and the repetition rate should be moderate to allow for cooling between pulses. The optimal laser parameters will depend on the welded material and desired weld strength.
Here is a table summarizing the optimal laser parameters for different applications:
Application | Power Setting | Pulse Frequency | Pulse Duration | Repetition Rate |
Engraving | Low | High | Short | Low |
Marking | High | Low | Long | High |
Cutting | High | Low | Short | Moderate |
Welding | High | Low | Long | Moderate |
You can fine-tune your fiber laser machine to achieve the best results by understanding the optimal laser parameters for different applications and materials. We also have plasma cutting machines, just like laser marking machines. They work similarly to a fiber laser cutter using laser light.
Conclusion
In conclusion, choosing the right laser parameters is crucial for achieving optimal cutting quality and efficiency.
By understanding the various parameters of fiber laser technology, such as power, wavelength, pulse duration, repetition rate, beam quality, and mode structure, one can fine-tune their fiber laser machine to suit the specific requirements of their application.
It’s also important to keep in mind that different materials have different properties and require specific laser parameters for cutting. Using the guidelines and tables in this blog, one can select the appropriate laser parameters for their specific application and material, resulting in high-quality and precise cuts.
Invest in Our Advanced Fiber Laser Machines Today
At Baison, we are committed to providing advanced fiber laser machines tailored to meet our client’s unique needs. Our machines are designed to offer exceptional performance and versatility, allowing businesses to increase their productivity and stay ahead of the competition.
We understand that investing in a laser-cutting machine is a significant decision, which is why we strive to offer affordable rates without compromising on quality. Contact us today!