Laser cutting has revolutionized the way materials are shaped and transformed in today’s fast-paced world. This intricate process relies on a multitude of parameters that determine its effectiveness and efficiency.
In this article, we will explore all parameters that affect laser cutting to help you understand their influence so they can be manipulated for optimal results. From power density and cutting speed to the material’s properties and gas pressure, these elements can significantly alter the quality of your final product.
Our goal is to demystify these factors, offering a comprehensive guide to mastering the laser cutting process.
What Is Laser Cutting?
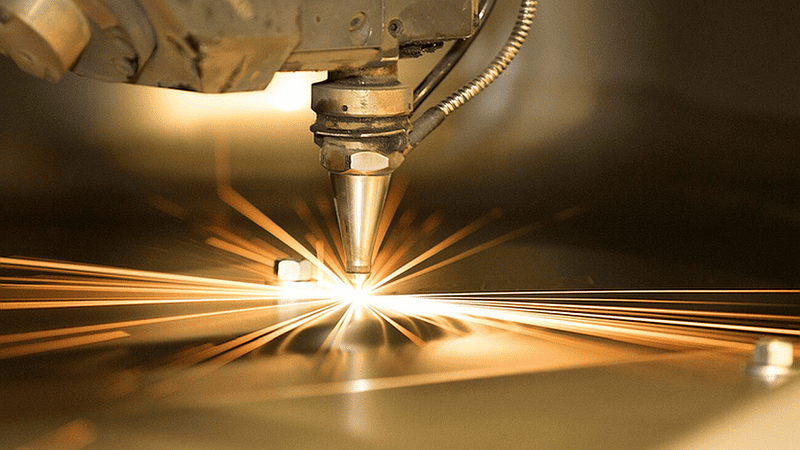
Laser cutting utilizes a high-power laser to cut various materials. The laser beam moves across the material, causing it to melt and vaporize. Then, a pressurized assist gas removes the cut part, producing a fine, high-quality cut.
To ensure precision, a computerized numeric control supervises the laser cutting process (CNC) machine that moves the focused laser head along the desired path. A CAD or vector file created using laser cutter software often defines this path.
The versatility of laser cutting enables its application across a wide range of materials, including metal, plastic, wood, glass, and even fabric.
Different types of laser cutting machines, such as CO2 lasers, fiber lasers, neodymium (Nd) lasers, and neodymium yttrium-aluminum-garnet (Nd: YAG) lasers, are available in the market; each specifically designed for various materials and specific applications.
What Are the Parameters of Laser Cutting?
Since laser cutting is a highly precise method, it relies on numerous parameters. Each parameter directly influences the quality and overall efficiency of the process.
Let’s explore these in more detail:
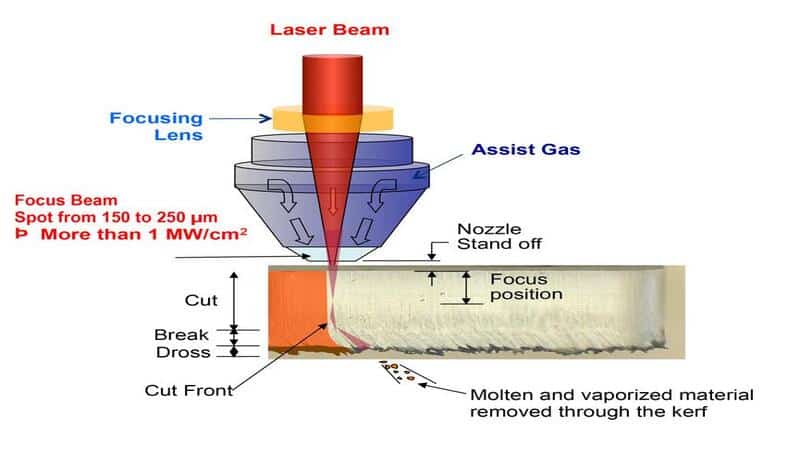
Laser Power
Laser output power is the energy output of the laser cutter. Usually, higher power allows cutting through thicker materials and quicker operation. However, too much power can damage the material.
Power, as mentioned earlier, is a function of material and thickness. For instance, an output power of 1 kW would be sufficient to cut stainless steel having a thickness of 5mm. However, a 12 mm thick sheet of the same steel would require a laser power of 3 kW.
Beam Diameter
It is the size of the laser beam, also referred to as spot size. A smaller beam diameter results in a more focused beam, enabling more precise cuts.
Cutting Speed
This is the speed at which the laser head moves across the material. Faster speeds lead to quicker operation but may affect the cut’s quality, especially in thicker material.
Nozzle Type and Size
Mostly, laser cutters come as either single-layer or double-layer nozzles. However, some customized short nozzles are also available. The single-layer nozzles lack an inner core and are typically used for cutting stainless steel, brass, and aluminum with nitrogen as an assist gas. In contrast, double-layer nozzles have an inner core and are used for cutting carbon steel with oxygen.
Assist Gas and Its Gas Pressure
Assist Gas, often known as ‘cutting gas,’ helps to expel molten material, cool the cut, and prevent oxidation.
The assist gas, purity, and pressure can influence the cut’s quality. Compressed air, nitrogen, and oxygen are among the gases that are commonly used in laser cutting.
Wave Mode
A laser macher machine emits laser in two ways, continuous wave mode and pulse processing wave. In the first case, the laser cutting machine emits a laser continuously like a stream of water.
While in the second case, laser pulses are generated. Continuous wave laser machines are best suited for cutting straight lines, while pulsed lasers are great for creating holes.
Laser Focus Position
This is the point where the laser beam is most focused. The alignment and placement of this point with the surface of the material are crucial for efficient cutting.
Standoff Distance
The distance between the nozzle and the material is the standoff distance. It directly impacts the accuracy of the cut.
Kerf Width
Kerf refers to the width of the material removed by the laser cut. Knowing the kerf width is essential for precise cuts, especially when dealing with intricate designs.
Material Type
Different materials respond differently to laser cutting, with certain materials requiring specific laser types, power levels, or assist gases.
Thickness
The thickness of the material affects the required laser power and cutting speed. Thicker materials generally require slower cutting speeds and higher laser power.
Why Laser Cutting Parameters Important?
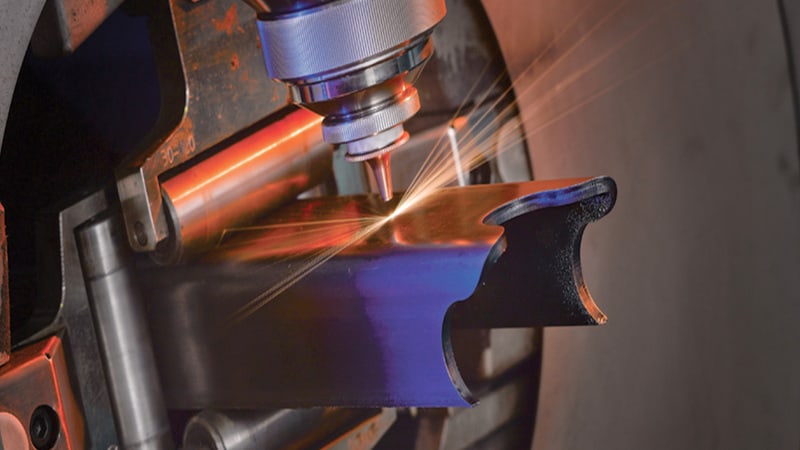
The parameters of laser cutting are integral to the success of the process as they dictate the overall quality, speed, and efficiency of the cut.
By manipulating these parameters, laser-cutting machine operators can fine-tune the procedure to cater to specific materials and thicknesses to ensure precise and high-quality results.
Furthermore, understanding these parameters is essential in avoiding common pitfalls, maintaining equipment longevity, and ensuring safety during operation.
How do Laser Parameters Influence Laser Cutting quality?
The chosen of laser cutting parameters directly affect the laser cutting quality. Here’s how each parameter contributes to laser cutting quality:
Power: Less power won’t be able to cut through sheets. In comparison, an overpowered laser will damage the material surface. Either way, you will obtain a poor-quality cut and poor surface finish.
Cutting Speed: In general, higher cutting speeds tend to result in improved cut quality. However, it is important to balance cutting speed and laser power. The material may not completely cut through if the speed is too high relative to the power. Conversely, excessive heat buildup can occur if the speed is too slow, damaging the material.
Assist Gas: Since assist gases prevent oxidation and are responsible for chipping the removed part, choosing the right gas and optimal pressure is crucial for obtaining the desired cut quality. Additionally, gas purity also affects cut quality. The assist gases should typically be >95% pure for generating a quality cut.
How to Choose Laser Parameters for Different Materials?
The selection of appropriate parameter values depends on the nature of the job and the type of material. Some materials require higher power and low cutting speed, while others may need lower power.
Metal
Metals generally require high-power lasers (beyond 1KW), such as fiber lasers or CO2 lasers, along with slower cutting speeds due to their high thermal conductivity and reflectivity. An assist gas like oxygen or nitrogen is typically used.
When cutting carbon steel, oxygen is advantageous as it triggers an exothermic reaction that aids in the process. However, nitrogen is used for a “clean” cutting approach for stainless steel and aluminum, where oxidation is undesirable.
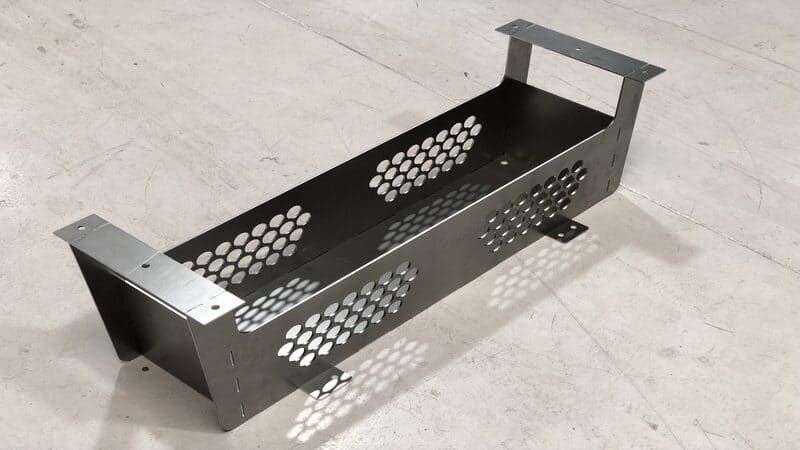
Plastics
Plastic materials can be cut with lower power settings (25-100W) compared to metals at faster speeds. However, care must be taken to avoid excessive heat, which can melt the plastic and lead to poor edge quality.
Wood
Wood can be cut like plastics at lower power settings and higher speeds. However, different types of wood may respond differently to the laser, and the laser can cause charring or burning of the wood, which may or may not be desirable depending on your application.
How to Optimize Laser Parameters for the Best Cutting Quality?
Optimizing laser cutting parameters requires a mix of knowledge, experience, and sometimes trial and error. Nonetheless, consider the following suggestions when fine-tuning the settings of your laser-cutting machine:
Understand Your Material
Different materials respond differently to laser cutting. For example, metals require high-power lasers, while plastics and wood can be cut with low-power lasers. Similarly, some materials may also require specific types of assist gases.
Always start by understanding the properties and requirements of the material you’re working with.
Choose the Right Laser Cutting Machine
The choice of laser machine must be based on your application. For instance, if you plan to cut thin metal sheets or plastics, CO2 laser-cutting machines are ideal. However, fiber laser machines are a better option for cutting reflective and thick plates.
Ensure that the machine you choose can handle the materials and cut the complexity you’re working with.
Find the right combination between Power and Speed
Generally, thicker materials require more power and slower cutting speeds, while thinner materials can be cut with less power and at faster speeds. But remember, too high power can cause the material to distort, and too low power may not cut through the material. You’ll often need to experiment to find the optimal balance.
Select Suitable Assist Gas
Assist gases can significantly affect the quality of your cut. Oxygen, nitrogen, and compressed air are the most commonly used assist gases. Usually, nitrogen is the safest choice.
Focus on the Laser Beam
The focus point of the laser beam affects the quality of the cut. If the focus is too high or too low, the cut may be of poor quality, or the laser may not cut through the material at all. Adjust the focus point of the laser beam until you get a clean and precise cut.
Test and Adjust:
Always start by making some test cuts and then adjust your parameters based on the results. This is often the best way to find the optimal settings for your specific machine, material, and application.
Common Misconceptions about Laser Parameters
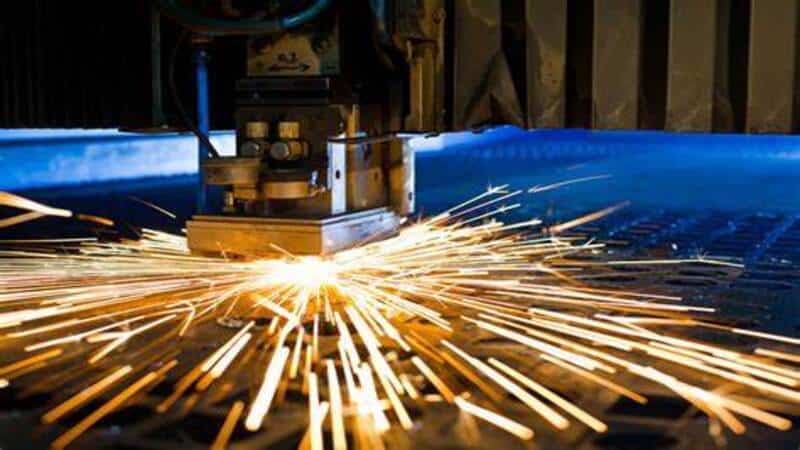
Misunderstandings of laser parameters can lead to suboptimal results or even damage to the laser cutter. Here are a few misconceptions you must be aware of:
Power Equals Quality
Many people believe that higher power in laser cutting always equates to superior quality cuts. While it’s true that a powerful laser is necessary for cutting through thicker or denser materials, it’s not always the case that more power leads to better results.
Using excessive power can, in fact, damage the material. It can also negatively impact the precision of the cut and potentially harm the machine itself.
One-Size-Fits-All Parameters
Another common misunderstanding is the assumption that the same laser-cutting parameters can be universally applied across all materials.
Each material has unique properties that respond differently to laser cutting. Factors such as thickness, density, and heat sensitivity need to be taken into account.
Faster Cutting Speeds are Always Better
Although faster cutting speeds can increase productivity, they can also lead to incomplete cuts or poor edge quality if the speed is too high for the laser power or the material being cut.
Conclusion
Grasping the key variables involved in laser cutting and their influence on the procedure is necessary for obtaining precise and high-quality results. It is essential to dispel common misconceptions, such as the belief that higher power always results in better cuts or that the same parameters apply to all materials.
Each material demands unique settings for optimal results, and excessive power can often cause more harm than good.
By comprehending these factors and adjusting them accordingly, operators can enhance efficiency and improve the quality of cuts.
Remember, with knowledge comes power, and in the realm of laser cutting, this power is wielded through the careful adjustment of parameters for each unique task at hand.
Discover the Perfect Solution for Your Business with Baison
In the intricate field of laser cutting, finding the perfect partner that understands your unique needs can make all the difference. We at Baison Laser are committed to helping you find the perfect solution for your laser-cutting business.
To understand how Baison can help elevate your business, we encourage you to contact our team of experts and discuss your business requirements. We offer Free Sample Proofing, so you can see our quality work firsthand before making a commitment.
Do you want to get more information about Baison? Click the button below!