Laser cutting was introduced to the market two decades ago and is already hailed as the state-of-the-art technology that changed the material cutting game for numerous industries. It’s a fascinating technology that keeps evolving each day. Learning about the parameters involved in optimum working is essential to grasp its applications and uses better.
This detailed guide will walk you through all the crucial parameters of the laser system and their importance in machine processing. We will also expand on how you can optimize each parameter to your benefit and scale up your business.
What is Laser Cutting?
Laser cutting is the latest and most prevalent cutting technology. It uses a high-power, focused laser beam to cut material by melting and vaporizing it at the cut edge. The resultant residues are either blown away using a jet gas during the process or machined and cleaned after the operation.
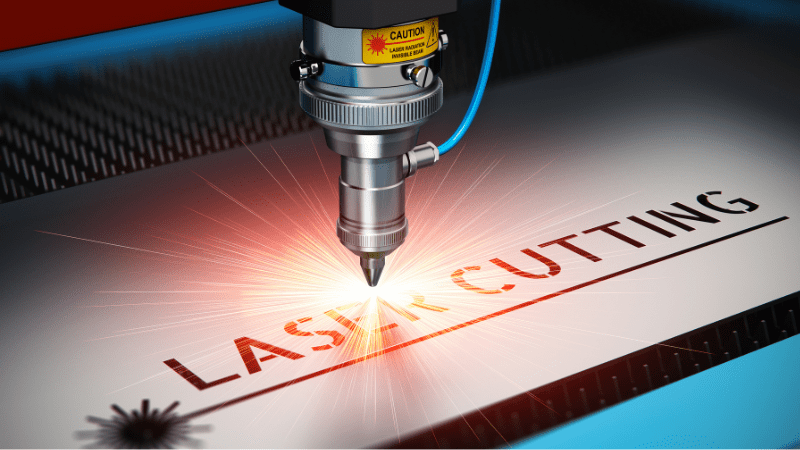
Laser cutting is now taking the lead in many industrial manufacturing processes due to its superb efficiency, cost-effectiveness, precise results, and ability to process various materials with varying thicknesses.
There are three main types of laser cutting: CO2 laser, Neodymium (Nd) and Neodymium Yttrium-Aluminium-Garnet laser (Nd: YAG laser), and Fiber laser cutting. As technology advances, laser cutting is on par with plasma cutting on many fronts.
Do You Have Any Questions?
Let Us Solve Your Problem
What are the Parameters of Laser Cutting?
As with any technology, understanding and setting parameters is crucial in determining product quality. For laser cutting technology to process designs with varying complexities, its cutting capabilities must be flexible enough. This is where parameters come into play. Adjusting and optimizing parameters opens a door for thousands of applications in the military, medical, and other industries.
The laser parameters include laser cutting quality, beam polarization, wavelength, power and intensity, cutting speed, processing gas, focal point, and material specifications.
Importance of Laser Cutting Parameters
Laser cutting depends on optimizing several parameters that directly or indirectly affect the product quality, ultimately contributing to profits in a business.
Simply put, laser-cutting parameters are important for determining the quality of the cut. It defines the processed material’s life and cutting performance in the respective application. Parameters can be adjusted while working with different materials and varying designs. So, the parameters of the machine ultimately define what materials it can process and to what level of precision and accuracy.
Let’s get into the most important parameters that determine the cut edge quality and the kerf size (the width of the groove or slit formed while cutting) of the processed material.
7 Crucial Parameters of Laser Cutting
First, we will discuss beam parameters that cover the beam qualities in the laser operation, such as beam type, wavelength, beam polarization, and beam power and intensity.
Second, we’ll get into process parameters that include cutting speed, focal length, focal position relative to the surface, assist gas, and gas pressure. We can adjust the process parameters to achieve the desired cutting quality.
1. Laser Wavelength
The three types of laser cutting, CO2, crystal, and fiber lasers, use different base materials to produce lasers with different wavelengths.
Every material absorbs and reflects different wavelengths, so choosing the right laser for your workpiece is the first crucial step.
CO2 Laser Cutting: In the CO2 laser cutter, electricity is passed through a gas chamber filled with carbon dioxide, helium, hydrogen, and nitrogen. The mirror on the end of this tube focuses the laser beams to a single point. CO2 lasers fall in the “infrared” or invisible region on the wavelength spectrum (0.6µm).
At room temperature, long infrared wavelengths, such as CO2 lasers, are reflected off the shiny surfaces of aluminum, gold, silver, and copper. While steel can absorb up to 10% of the laser energy. CO2 laser cutting is not suitable for cutting reflective and conductive surfaces, but it’s perfect for insulating materials such as wood, paper, and plastics.
Crystal Laser Cutting: Neodymium Yttrium-Aluminum-Garnet (Nd: YAG) laser beams lie on the shorter range of infrared radiations (1.06µm) that absorb better in reflective metals. High-power Nd: YAG lasers can cut metallic and non-metallic surfaces and, in some cases, even process ceramics.
One thing to understand is both CO2 lasers and Nd: YAG lasers at high power intensities can overcome reflectivity and process a broader range of materials. This can also be achieved by changing the external parameters, such as heating the material to be cut.
Fiber Laser Cutting: Fiber lasers originate from silica glass and rare earth metals. With a wavelength of 1.064µm, fiber lasers have far higher beam power and narrow focal diameter, making them superior to CO2 and crystal beams in many respects. A fiber laser cutting machine is versatile and can handle metals, nonmetals, glass, and other insulating materials. It also has solutions for reflective metals.
2. Laser Power and Intensity
Laser power and laser intensity are often used together and sometimes interchangeably, but they mean different things.
The amount of energy emitted per second is called laser power. At the same time, the laser intensity is the power divided by the unit area of the material. Don’t confuse a high-power beam with a high-intensity beam. Intensity depends on the width of the focal point—the narrower the laser beam, the higher the laser intensity.
Low-power laser beams reflect off the surfaces of metals. For thicker materials, you need high-power beams that can penetrate deeper and faster into the material.

A high-intensity laser beam directed sharply to a small, focused diameter is perfect for obtaining a high-quality cut edge and small kerf width. In addition, the high-intensity laser heats a small area quickly, reduces burr formation, and improves the cutting speed, leaving little to no time for the material to melt around the edges and form dross (the residual re-solidified metal that is not completely removed from the kerf).
Like high-power beams, high-intensity beams can cut thicker materials more efficiently than low-intensity beams.
Note that beam power and intensity should be optimized according to the melting point and thickness of the processing material. For example, a very high beam power can result in increased heat dissipation around the edges of the cut and, consequently, a bigger kerf width.
3. Beam Polarization
The reflectivity of laser light on the melted surface of the cut material depends on the beam polarization, which is the orientation of the electric field concerning the direction of propagation.
Depending on the field orientation, there is plane polarization, circular, elliptical polarization, and random polarization. Each of these is absorbed and reflected differently off the surface. Circular polarisation results in uniform kerf width instead of elliptical or linear polarisations that produce variations in kerf inclinations.
Beam polarisation affects the quality of the cut kerf, depending on the polarisation surface and cutting direction. You can understand it better from the figure below. We get a smaller kerf width when the cutting is done in the direction of polarization (a), compared to cutting at 90 degrees to polarization (c).
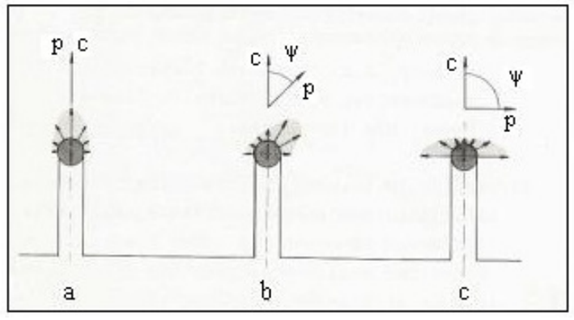
4. Focal Position Relative to the Workpiece Surface
The focal setting (also called the z-offset) allows for the maximum utilization of laser power for cutting material. If the focal length is too low or too high, it won’t cut the material effectively because of the reduction in energy density. And if your beam is out of focus, it will not cut anything.
Ideally, your focus point should be in the center of the material thickness so the laser doesn’t form a tapered cut edge and cut the workpiece unevenly from top to bottom. However, you may need to increase or decrease the focal position in other applications like laser engraving.
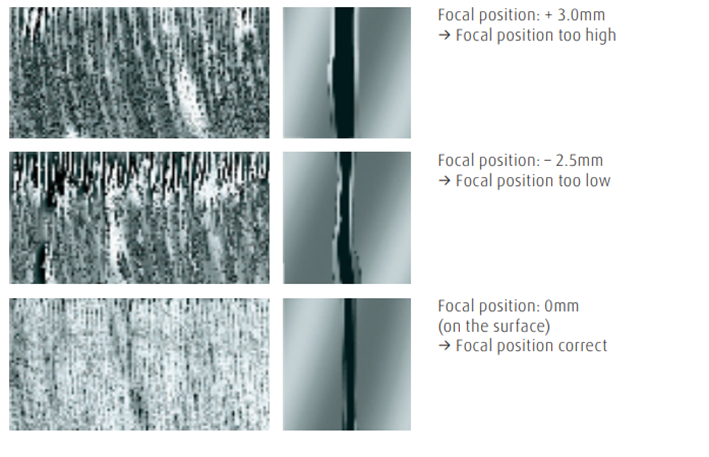
The focal length is determined according to the thickness of the material. A short focal length for a thin workpiece (less than 4mm) effectively cuts the material uniformly. For thicker materials, you need a longer focal length and a larger focal depth to penetrate deep into the material for an even cut edge.
A shorter focal length results in a smaller spot size and focal depth. While a longer focal length means a slightly bigger spot size and longer focal depth. But, nowadays, newer technologies allow us to keep the spot size small while increasing the focal length.
Generally, the focal position should be kept constant throughout the processing of a material.
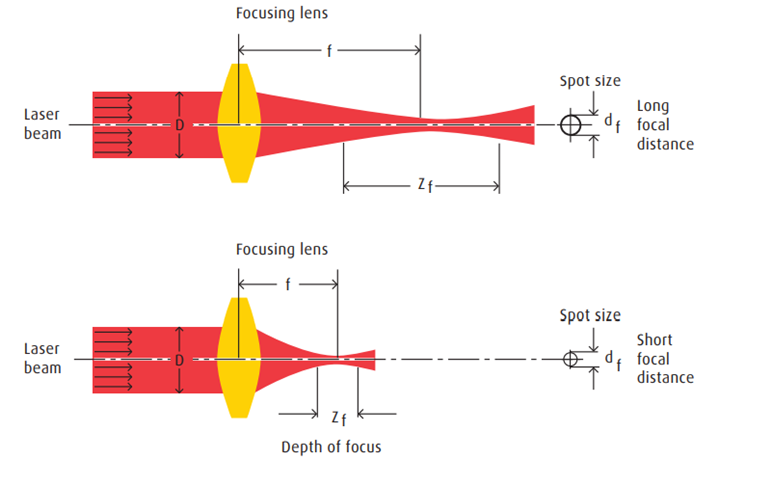
The focal position is also subject to the laser beam shape, mode, contamination on the lens, and temperature of cooling water. All of these parameters define the quality of the final cut piece.
5. Laser Cutting Speed
Cutting speed is another important laser parameter and is optimized according to the thickness of the workpiece.
Cutting speed is related to energy losses during the process. Faster speed means lesser energy loss and more efficient operation. Slow speed leads to higher energy losses and, as a result, inefficient procedure.
Refer to the figure below to better understand how cutting speed changes with the thickness of a material.
Slow cutting speed results in dross and burning of the material, resulting in a bigger heat-affected zone (HAZ). In comparison, high cutting speed may cause striations on the cutting edge. It is best to find a perfect balance between the cutting speed and laser power to process a specific material.
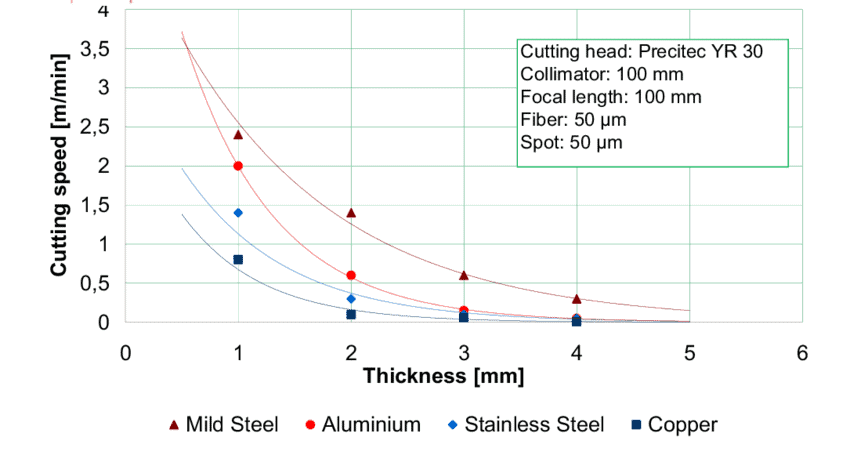
6. Assist Gases and Gas Pressure.
The assist gas—also called auxiliary gas—used during the laser cutting operation plays an important role in determining the cutting speed, the quality of the cutting edge, and the life of the laser lens. Generally, cutting speed is proportional to laser power. The higher the laser power, the greater the cutting speed, and vice versa.
The main purpose of the assist gas is to remove the molten metal from the edges and protect the optical components from any damage during the processing. The gas also cools down the material to prevent larger HAZ.
Nitrogen, argon, compressed air, and oxygen are the most common types of assist gases. Each type has its pros, cons, and applications. The choice of gas and pressure ultimately decides the quality of cut edges.
Nitrogen (inert) gas is typically used when processing stainless steels, aluminum and nickel alloys, and high alloyed steel. Nitrogen gas at higher pressure provides extra mechanical support to remove residual molten material from the surface.
Oxygen is an active gas that starts an exothermic reaction and helps cut thicker materials. Oxygen cutting forms an oxidizing layer in mild steel and carbon steel, both good and bad for the workpiece. Good in the way that oxides increase the absorption rate and melt the material faster, aiding in the cutting speed. And bad in the sense that oxide layers create defects and affect the post-processing of the material.
Want to learn about choosing nitrogen or oxygen? Read our post.
Compressed air is the cheapest choice out of all the assist gases, but its uses are limited.
7. Nozzle Diameter and Standoff Distance
The nozzle carries the assist gas and is coaxial to the laser beam. It is responsible for providing the assist gas to the cut region and stabilizing the pressure on the surface to minimize molten metal splattering. The nozzle diameter is an important parameter to select according to the material type and thickness.
Standoff distance is the distance between the nozzle and the workpiece. It determines the gas flow pattern and, ultimately, the cut quality. Large standoff distances often result in high turbulence and pressure variations. It’s recommended to keep the distance no greater than 1mm. In addition, the distance should be smaller than the nozzle diameter.
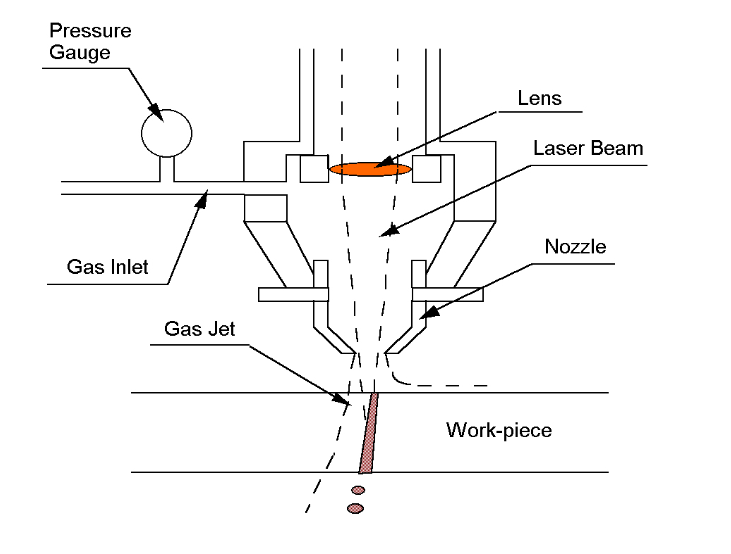
Nozzle misalignment can result in unwanted defects, cut burns, and dross that can be detrimental to the cutting quality. It’s imperative to have the nozzle diameter in complete alignment with the laser beam to avoid directional gas flow across the material’s surface.
Do You Have Any Questions?
Let Us Solve Your Problem
How are Parameters Set in a Laser-Cutting Machine?
Many latest laser cutting machines have pre-set parameters for various materials in the software database. These pre-determined values for parameters are tried and tested by the company and can be implemented automatically. It can reduce your workload and make processing easier. However, if you need slight alterations, you can manually edit and input your numbers into the software that controls the laser-cutting machine.
If you need to set your parameters from scratch, the general rule is to start with high speed and low power for engraving and cutting the material. As you begin the job, the software can change the parameters to achieve the best result. You can alter the parameters while cutting a test piece to attain a burr-free and perfect cut edge.
The operator should be trained to deal with any complications during the process. For instance, he should know the consequences of increasing or decreasing cutting speed, gas pressure, and laser power. The relationship between how laser parameters interact with the material is paramount.
Here’s an example: If an operator sees a burr in stainless steel, his immediate reaction will be to reduce the cutting speed and adjust the assist gas accordingly. But what he observes is an even bigger burr. A slower rate caused greater heat accumulation in the area. As a result, the molten material solidified before the gas could blow it away, forming dross. The key is the relationship between assisting gas and speed with stainless steel. The right amount of molten metal should be removed at the right time to attain the perfect cut edge.
Parameters | Stainless steel | Stainless Steel | Aluminum | Aluminum |
Thickness (mm) | 10 | 10 | 5 | 10 |
Gas Type | O2 | N2 | N2 | N2 |
Power (kW) | 5 | 5 | 5 | 5 |
Cutting speed (mm/min) | 680 | 1200 | 7000 | 2400 |
Gas pressure | 10.5 | 12 | 15 | 15 |
Focal (mm) | -3 | -7.2 | -1.1 | -2.4 |
Standoff (mm) | 0.6 | 0.6 | 0.6 | 0.6 |
Nozzle diameter (mm) | 2.5 | 3 | 2.5 | 3 |
Frequency (Hz) | 5000 | 5000 | 5000 | 5000 |
What are the Tolerances for the Laser Cutting Process?
It depends on the quality of the laser machine and the operator’s expertise. But a laser machine can generally cut to extremely tight tolerances, up to 0.25mm.
In addition, it largely depends on the application of your component. High tolerances are often required for components that have high-end applications. The cost for high tolerance levels is very high, so one should consider the budget, application, and requirements before going for tighter dimensional tolerances.
Do You Have Any Questions?
Let Us Solve Your Problem
Concluding Thoughts
Laser cutting is a top-notch technology, capable of processing a wide array of materials in all forms and shapes. A thorough understanding and study of the machine are essential to make the most out of it.
All parameters in laser cutting are crucial in determining what you get after material processing. For instance, laser power, nozzle’s standoff distance, and cutting speed significantly affect the kerf width. While parameters, like assist gas type and pressure, are not largely responsible for kerf width.
Before cutting material, the parameters must be adjusted and studied to minimize striations, kerf width, dross, and other defects that hinder the part’s post-processing and affect the final quality.
Baison Laser Provides the Best Laser Cutting Solutions
Biason laser cutting machines will cut your work time and double the revenue. You can adjust the machine’s parameters or select pre-fed parameters from the database with minimal effort. Ordering from Biason means you’ll get free assistance from start to finish and the best prices on the market.
Our team of experts is always available for assistance and is just one call away. Contact us now and get a free consultation and application evaluation from our experts. We love to hear your concerns and specialize in finding the best solution in the shortest possible time.