This article will explore several methods for quickly analyzing the strength of a welded junction. Let’s begin the journey through laser welding and the finest practices employed by Baison Laser Equipment.
Understanding Laser Welding
The evolution of laser welding has made high quality possible. Now, welding is a process in which two metals are joined together by utilizing high power and welding speed. In laser welding, a laser beam is used to combine the metal pieces with high welding speed.
Here, the standalone laser welding unit is used to direct a laser beam toward the metal. Because of high welding speed, the laser’s point of contact melts and is welded in a robust manner. Laser welding is revolutionizing and it is making advances. A laser beam is often produced via CO2 laser welding or fiber laser welding.
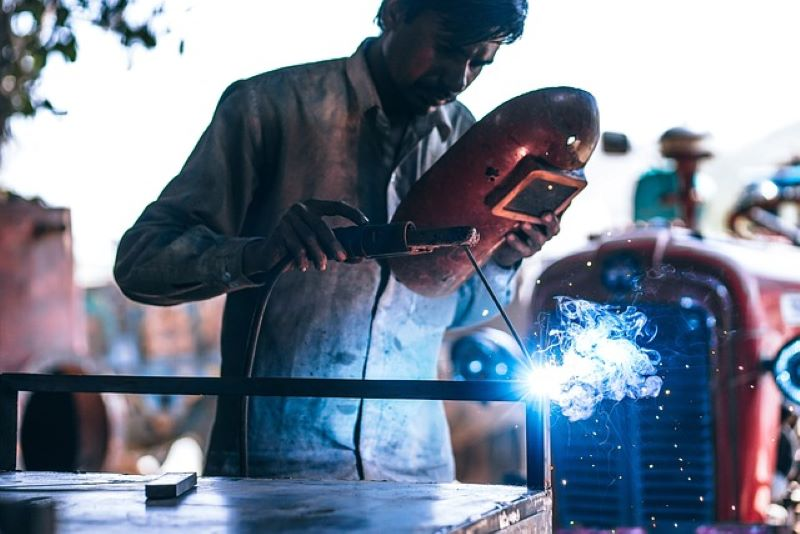
Why Laser Welds Strength Testing is Crucial
Laser welding is a positively efficient and precise metal joining technology that has various advantages, such as low deformation, a restricted heat-affected zone, and the ability to weld various materials. However, the quality and integrity of the welded joints can deteriorate over time. Here are some of the reasons why laser welding strength testing is crucial.
- You will be pleased to know that it can ensure that the joints are able to withstand the strain without falling.
- Using these tests, you can, without fail, validate the laser welding process and determine whether it meets the mechanical qualities of the production process.
- With a welding test, you can make course corrections in your welding process.
- You can demonstrate the efficacy of welding process factors such as welding speed, laser beam welding power, etc.
Different Types of Welding Joints
There are five basic laser welding joint types used in the industry:
Type 1 – Butt Junction Welding
When two pieces of metal are joined together, and their sides are welded, a butt junction is formed. Butt joints are commonly employed in plumbing systems and can be single, double, or many. To gain a better understanding, consider the thickness and welding method.
Type 2 – Tee-junction Welding
A tee joint forms when one piece of metal is perpendicular to another, leading to the formation of a T shape. Considering the structure, it is made when a pipe is welded onto a base plate. However, you must ensure that there is effective penetration into the roof of the weld metal.
Type 3 – Edge-joint Welding
Edge junction is a sort of laser welding joint in which the metal parts are placed together so their edges are even and such welds are used in sheet metal manufacturing. The goal of weld metal is to create a junction with distributed tension that can withstand a load, which is what happens with edge joints.
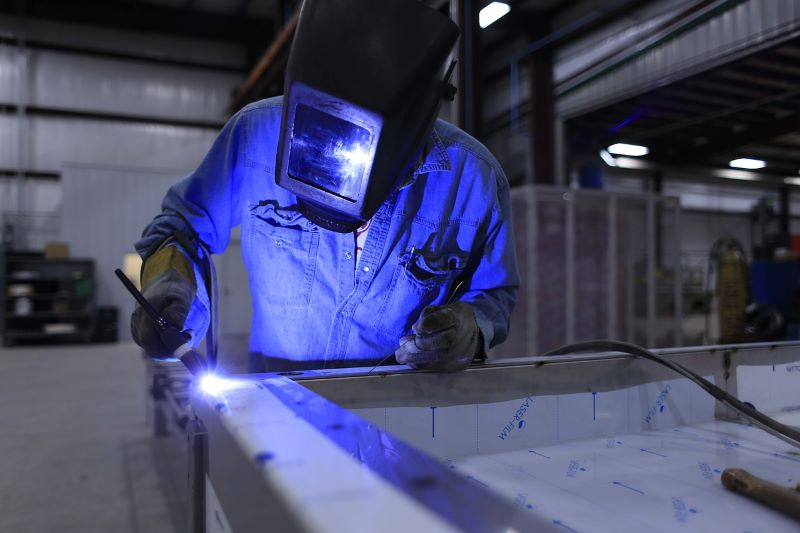
Type 4 – Lap Joint Welding
The lap joint is simply another type of butt joint. The two metal pieces are arranged in an overlapping pattern. They may be welded to make a flawless laser welding junction.
Type 5 – Corner Joint Welding
Corner joint welding is similar to tee joint welding but differs in metal positioning. The only difference is that the metal is welded in a L shape in the corner. These are most commonly used in the manufacture of frames, metal boxes, and so on.
These are some of the most frequent laser welding joints. The type of connection chosen is determined by criteria such as the weld metal, the needed strength, the welding method such as the laser beam welding method, etc. With each joint having its own advantages and disadvantages, you must select the best type to provide strong and durable welded joints.
Factors Influencing Weld Strength
Uniformity of the laser weld per the length of the base metal ensures quality laser welding. Therefore, if one factor is missed out, the quality hampers. Here are certain factors that influence laser weld strength:
- The quality of the welds in metallic materials ensures the longevity of the weld joints. Therefore, you must check the material quality and thickness of the base material for better welding strength. You must also pay attention to the concentration of stress on joints to determine the effectiveness of the design on weldability.
- The process parameters used for laser welding play an important role. If you use a different welding method for different base metals, there might be an impact on the weldability. In case you have high-strength steel, you may use plasma arc welding to prevent overheating.
- For effective results, use a high-power source for a high-power laser beam. You can also include a shielding gas to protect the laser welding junction from outside contaminants. However, always keep the welding metal in a free state of contraction and expansion during the entire laser welding process.
- Welding speed has an effect on overall weld quality and the heat-affected zone. As a result, for laser welding, ensure that the speed and laser power of the laser beam are balanced. Another crucial factor to consider for proper energy distribution and heat concentration is controlling the focus and spot size of the laser beam.
- There are times when the material is corrosive, then you have corrosion resistance while working in such mediums. However, we insist on conducting quality control tests to ensure the durability of laser welding joints.
6 Ways to Assess the Strength of Laser Joints
With the increasing loading and unloading activities, it has become crucial to check the strength of laser welds in all manufacturing processes by ensuring that all laser welding parameters are met. Here are six tests that can provide you with a better path:
1. Tensile Testing
The tensile test is done in the initial state to test the weld metal performance. It is done to determine the best filler metal for the laser welding application. A demo piece of the exact same measurement is loaded and stretched to test the tensile strength and ductility of the weld.
After the test, the tensile strength is displayed. Manufacturers perform tensile strength testing procedures per the specific requirements of the base metal plates.
Tensile tests can be conducted in various ways. One, you can pull apart the laser weld until it reaches a breaking point. Secondly, you can place it in shear until it reaches its extreme breaking point. You can also do a compression test to check the tensile strength of the laser welding joint.
2. Bend Testing
Bend testing is usually done in the butt welded joints where the ductility and cracking resistance of the laser welding joint are assessed. The process is simple and qualitative. Therefore, you could either conduct it under guidance or on your own. Common bend tests include the guided bend test and the side bend test.
3. Microhardness Testing
In this test, the welded joints are assessed in-depth. You can gain knowledge about the microstructure and mechanical properties of the welded joints at a microscopic level. While forming a joint, the heat is localized, and a heat-affected zone (HAZ) is formed adjacent to the weld. This is where microhardness testing helps. It checks for variations within the HAZ and identifies if there is any chance of cracking or reduced strength.
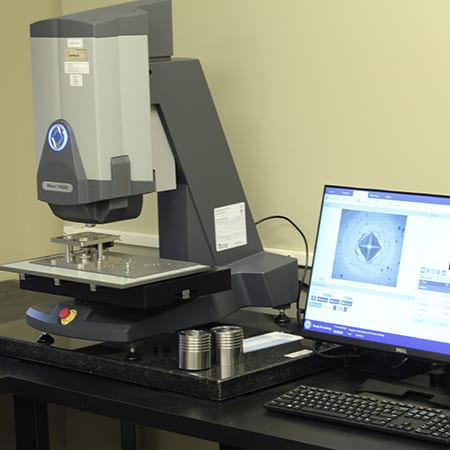
4. Fatigue Testing
In manufacturing industries, there is a cycle of multiple loading and unloading of objects. There are chances that when you repeat the cycle, your joint or object might break into pieces and that can cost you money and time. That is why fatigue testing is important for you to conduct to avoid any potential future failure. The immediate purpose of this testing is to identify the endurance limit of the laser welding joint.
The result is based on the number of loading cycles a component can endure. The process is simple; all you have to do is get a specimen identical to the weld. After that, you have to load the material and perform a loading & unloading cycle. For every weld, the specifications or weight measurements are different, so you must consider them before proceeding with the testing.
You must continue the fatigue testing cycle until you have a proper stress-life (S-N) curve and endurance limit of the joint.
5. Impact Evaluation
Impact testing helps you determine the toughness and resistance of the material you are planning to use for laser welding. There are times when your object might face external forces, and to your surprise, it is intact. The fortunate reason behind this is the positive result in impact evaluation. It can withstand that load, and others will fail. In simple words, the main objective is to check the material’s energy absorption capacity to avoid any future failure.
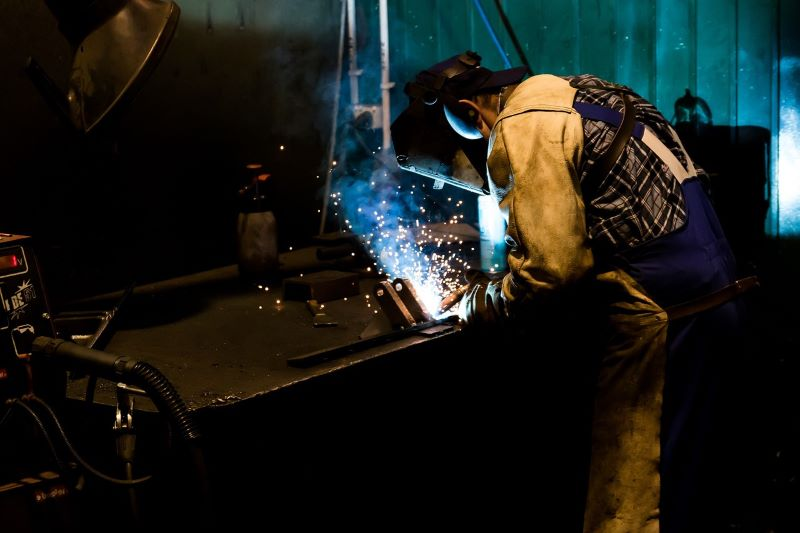
Learning about each test is no piece of cake, but you must know that the impact test is divided into two categories: the Charpy impact test and the Izod impact test. The specimen is placed in a pendulum-type machine, and the pendulum is discharged from a specified height during the Charpy impact test. The outcome is determined by the amount of energy released following the strike, which is used as an indicator of toughness.
In the Izod impact test, on the other hand, the specimen is held in a vertical posture, and the pendulum is struck from the opposite side. In this case, the absorbed energy represents the toughness factor in laser welding.
6. Non-Destructive Testing (NDT)
Welded components are prioritized in non-destructive testing. They are not harmed, and the quality of the laser welding junction is also evaluated. The major goal of this procedure is to detect any defects as well as to evaluate the weld quality.
There are some NTD methods carried out to perform this testing effectively. They are called visual inspections, radiographic testing (RT), ultrasonic testing (UT), phased-array ultrasonic testing (PAUT), magnetic particle testing (MT), etc. If you combine some of the NDT techniques, you might get some extra favorable answers.
Best Practices in Testing Weld Strength
There are several key points to consider if you wish to follow the best practices for proper weld strength testing. They are as follows:
1. Standardization and Documentation
The beginning of any test is the most crucial stage and if you want to execute a structured test, then you must follow industry-specific standards and guidelines, such as AWS standards or ISO guide. Focus on documenting test procedures and conditions.
2. Reproducible Testing Conditions
You must maintain consistent and controlled testing conditions, including temperature, humidity, and equipment calibration. The next step is to select the appropriate test techniques based on the type of weld and the information required (for example, tensile, bend, shear, hardness).
3. Destructive vs. NDT
You can choose non-destructive testing methods like ultrasonic or radiographic testing when applicable. Another method is the reserve destructive testing technique. It is used in cases requiring ultimate strength assessment.
4. Specimen Alignment
Ensure that specimens are aligned correctly with applied forces to avoid introducing bending or shear forces. After that focus on setting up a testing environment. Replicate real-world conditions during testing to simulate service conditions. Always consider extreme conditions to get optimal results.
5. Data Recording and Analysis
Record load-displacement curves, failure modes, and any deviations from expected behavior. Analyze data to determine relevant parameters (e.g., yield strength, ultimate strength). Follow established welding procedures, including parameters like heat input, technique, and filler material. Maintain precise control over the welding process.
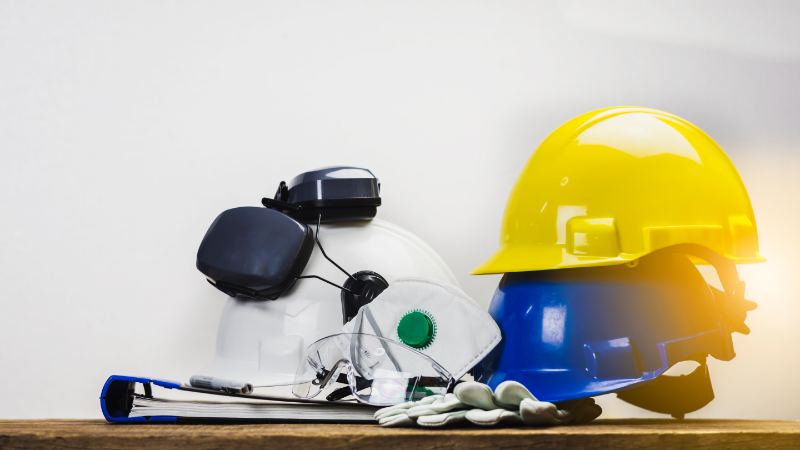
6. Statistical Analysis
Use statistical analysis for multiple tests or batch assessments to understand weld strength distribution and variability. You must also adhere to safety protocols during destructive tests, especially when involving high forces or pressures. Provide appropriate personal protective equipment (PPE).
7. Post-Test Examination
Examine fractured specimens to identify failure mode and any signs of defects, such as lack of fusion, porosity, or cracks. Prepare comprehensive test reports, including details of test methods, results, observations, and conclusions. Clearly communicate weld strength values and their implications for the component’s fitness for purpose. Use test results to inform process improvements and quality control measures, aiming for consistent, strong, and reliable welds.
FAQs
1 – What is the Most Common Post Weld Heat Treatment (PWHT) to perform the Herculean Task of Ensuring the Strength of Laser Welding?
To avoid any future nuisance, the most common treatments used in PWHT are Past heating and stress relieving. Post-heating is used to reduce the hydrogen release, which is responsible for cracking in joints. Whereas stress relieving is used to remove the stress locked in the structure.
2 – What is the Formula to Measure Laser Welding Strength?
It is critical that you are not confused and that you understand that the formula selection is dependent on the type of joint and the testing method employed. If you are still having any second thoughts, be cautious, because the strength of a laser-welded connection can also be affected by different factors such as welding conditions, material qualities, and joint design.
3 – What effect does weld size have on the strength of a laser-welded joint?
A laser-welded joint’s strength is affected by a number of parameters, including:
- A larger weld has a higher strength value.
- Weld length and width have an effect on joint strength.
- The strength of the joint is also affected by laser power and overlap length.
4 – Is laser welding as strong as TIG welding or arc welding?
Laser welding is celebrated for its precision and reduced heat-affected zones, making it ideal for thin or sensitive materials.
In contrast, arc welding, due to its deep penetration abilities, often results in stronger welds in thicker and more robust materials. The ultimate strength and suitability of the weld, however, will depend on the specific application, material, and expertise of the welder.
It’s Time to Wrap Up!
The glossary list of welding strength tests is explained in detail to make it easy for you. It goes like NDT, Tensile laser joint strength evaluation test, Fatigue testing, etc. These are some of the well-known tests to assess the strength of the laser welding joint.
Learn about them in detail and understand how they help in getting rid of any future failure in advance. The results are promising and can help you in a million ways in pre-welding and post-welding sessions.
Let’s Get Started With Quality Laser Welding Right Away!
Have you already started working on your next welding project and want to test the strength of your laser-welded joints? Baison Laser is the perfect solution for you. We give customized solutions per your specific requirements. Contact us now, and our professional team will assist you without any compromise. Get in touch with us right away to know the financial quotation.