Understanding Wet Laser Tube Cutting
In the world of laser tube cutting, precision is paramount. This process, crucial in manufacturing industries, employs a potent laser beam to carve tubes with remarkable accuracy. Let’s delve into the machining method known as wet laser tube cutting, a technique that adds a touch of fluid finesse to the beam machining process.
The Wet Laser Cutting Process
Wet laser tube cutting involves the incorporation of a coolant into the cutting process. The process works by directing a high-powered laser beam onto the material while a finely controlled flow of a coolant is directed onto the material being cut. This water serves multiple purposes: it aids in cooling the material and reduces heat buildup during the laser ablation process. The coolant also acts as a suppressant for dust and debris, contributing to a cleaner and more controlled cutting environment.
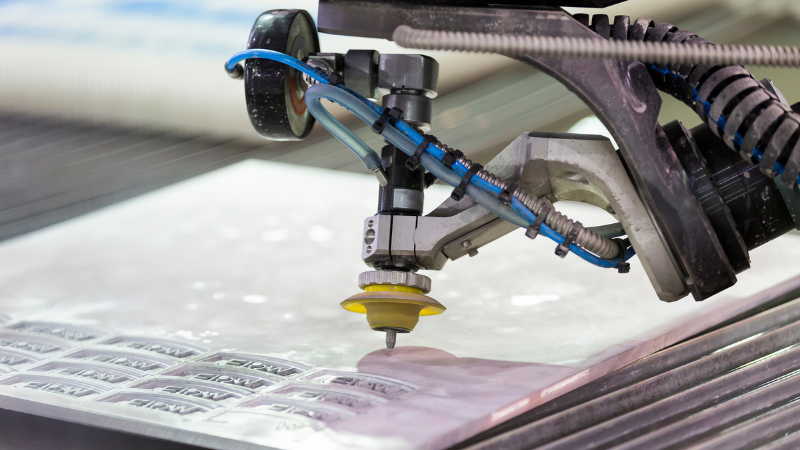
Applications and Considerations
In terms of practical application, wet laser tube cutting finds widespread use across various industries where precision is paramount. Laser cutting proves particularly effective when dealing with thick-walled tubes or intricate profiles that require intricate cuts. The cutting quality is significantly improved with laser cutting technology.
Wet laser tube cutting finds its niche across various industries, particularly where precision and material integrity are vital. Industries such as automotive, aerospace, and medical device manufacturing benefit from the meticulous cutting facilitated by wet methods and laser machining.
To summarize, wet laser tube cutting involves utilizing a coolant for machining to cool down materials during the cutting process. This method helps with suction and dust removal, particularly when working on stents. This laser cutting method offers advantages such as reduced heat distortion, protection against damage, and improved cut quality.
Pros and Cons of Wet Laser Tube Cutting
Wet laser tube cutting offers several advantages and disadvantages that need to be considered before deciding on the most suitable process for your needs. Let’s take a closer look at the pros and cons:
Advantages of Wet Laser Tube Cutting
- Reduced heat distortion: One of the major benefits of wet laser tube cutting is its ability to minimize heat distortion. By using a coolant and suction during the cutting process, the temperature remains controlled, preventing excessive heat and dust from affecting the material. This is especially important when working with delicate stents. This results in more precise cuts without warping or deformation.
- Improved cut quality: The use of coolant also contributes to improved cut quality. It helps to reduce dust, burrs, and rough edges, resulting in cleaner and smoother cuts for stents. Meanwhile, heat-affected zone (HAZ), kerf width, surface roughness, and dross deposition have also been improved compared with dry cutting. This is particularly beneficial when working with materials that require high precision, such as those used in medical or aerospace industries.
- Suitable for thick materials: Wet laser tube cutting is well-suited for handling thicker materials. The presence of coolant aids in dissipating heat generated during the cutting process, allowing for efficient cutting even with thicker tubes or pipes.
- Effective removal of debris: The use of coolant not only cools down the material but also helps in flushing away debris created during the cutting process. This ensures better visibility and prevents any obstruction that could affect the accuracy of subsequent cuts.
Disadvantages of Wet Laser Tube Cutting
- Increased setup time: Implementing wet laser tube cutting requires additional setup time compared to dry processes. The inclusion of coolant systems and ensuring their proper functioning adds complexity to the setup process, which can result in longer preparation times.
- Higher operating costs due to coolant usage: The use of coolants increases operational costs as they need to be continuously supplied and maintained. Coolant consumption adds an ongoing expense that should be considered when evaluating cost-effectiveness.
- Limited compatibility with certain materials: While wet laser tube cutting works well with many materials, it may not be compatible with all types. Some materials may react negatively to the coolant or exhibit other issues that make wet cutting less suitable. It is important to consider material compatibility before opting for this process.
Considering these pros and cons will help you make an informed decision about whether wet laser tube cutting is the right choice for your specific requirements.
Understanding Dry Laser Tube Cutting
Dry laser tube cutting is a process that involves cutting tubes using a laser without the use of any coolant. This method offers several advantages and is often preferred for thinner materials and simpler profiles. Here’s what you need to know about dry laser tube cutting:
- The process: Dry laser tube cutting, especially fibre laser cutting, utilizes a high-powered laser beam focused on the material to be cut. The laser beam melts or vaporizes the material along the desired cutting path, resulting in a clean and precise cut. The use of fiber lasers and YAG lasers ensures precise cuts, while suction is employed to maintain a clean working environment.
- Key components: The key components of dry laser tube cutting include the laser source, focusing optics, and motion control system. These elements work together to deliver accurate cuts without the need for additional cooling.
- No coolant required: Unlike wet laser tube cutting, which relies on coolants or water jets to dissipate heat during the cutting process, dry laser tube cutting does not require any external assistance for heat dissipation. The generated heat is naturally dissipated through the material itself.
- Faster processing times: One of the significant advantages of dry laser tube cutting is its faster processing times compared to wet cutting methods. Since there is no need for coolant application or drying time, this process can significantly reduce production cycle times.
Pros and Cons of Dry Laser Tube Cutting
Dry laser tube cutting offers several advantages and disadvantages that are important to consider. Let’s take a closer look at the pros and cons.
Advantages of Dry Laser Tube Cutting
- Faster processing times: Dry laser tube cutting boasts quicker processing times compared to its wet counterpart, allowing for increased productivity.
- Lower operating costs without coolant usage: By eliminating the need for coolant, dry laser tube cutting reduces operating costs associated with purchasing, maintaining, and disposing of coolants.
- Suitable for thin materials: This method is particularly well-suited for cutting thin tubular metallic materials like medical coronary stent fabrication as it minimizes the risk of warping or damaging them. The use of fiber laser and yag laser in laser machining enhances these benefits. Its versatility makes it an ideal choice for working with various materials and complex profiles.
- Simpler setup process: Dry laser tube cutting requires less setup time and equipment compared to wet cutting methods, making it more convenient and efficient.
Disadvantages of Dry Laser Tube Cutting
- Higher risk of heat distortion: One drawback of dry laser tube cutting is the increased risk of heat distortion during the cutting process, which can affect the overall quality of the cut. However, with the right control of peak pulse power, these drawbacks can be managed.
- Potential for reduced cut quality in some cases: While generally effective, there may be instances where dry laser tube cutting produces cuts with slightly lower quality compared to wet methods.
- Limited application on complex profiles: Dry laser tube cutting may face limitations when dealing with intricate or complex profiles due to its reliance on heat-based processes.
Considering these pros and cons will help you make an informed decision about whether dry laser tube cutting is suitable for your specific needs. Keep in mind factors such as material thickness, desired precision, and complexity of profiles when evaluating which method to choose.
By understanding these key points about dry laser tube cutting, you can weigh its benefits against potential drawbacks to determine if it aligns with your requirements effectively.
Choosing the Best Method for Laser Tube Cutting
Navigating the realm of laser tube cutting demands an informed decision on the process that suits your specific application. Whether you’re in the automotive sector, aerospace industry, or crafting medical devices, finding the right fit between wet and dry methods is key. (This article is a specific comparison of the two cutting methods used in medical devices) Let’s dive into the factors that influence this crucial choice.
Material Type and Thickness
One of the initial considerations is the material you’re working with. Different materials respond differently to wet and dry cutting. For instance, metals prone to oxidation might benefit from wet cutting’s protective shield against rust. On the other hand, materials like plastics or composites might favor dry cutting for quicker and cleaner results.
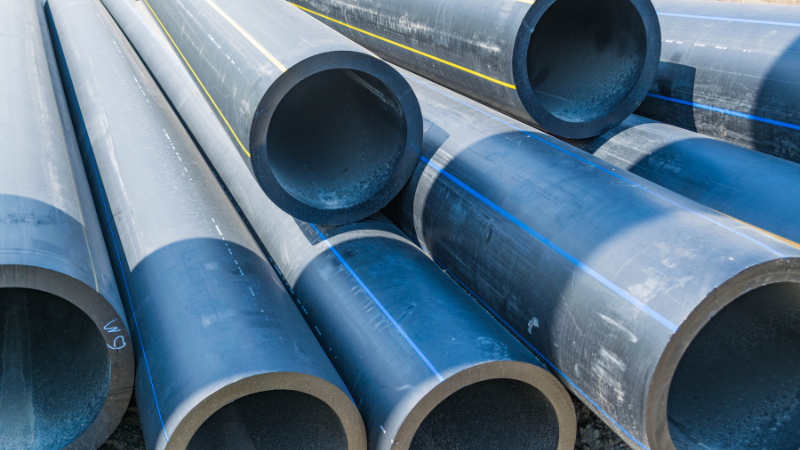
Precision Requirements
The level of precision your application demands is another crucial factor. Wet cutting, with its heat control and reduced material distortion, often shines in projects where precision is paramount. The smoother surface finish achieved through wet cutting is especially valuable in applications where aesthetics play a role.
Production Volume
Production volume plays a pivotal role in the choice between wet and dry methods. Wet cutting, while offering meticulous results, might be more time-consuming due to the need for water cooling and potential post-processing. In high-volume scenarios, dry cutting’s quicker processing times could prove more efficient.
Cost-effectiveness
Finally, cost-effectiveness weighs heavily. Wet cutting might demand additional resources such as water supply, waste disposal, and maintenance. Dry cutting, on the other hand, could lead to quicker turnaround times and potentially fewer post-processing steps, affecting the overall cost.
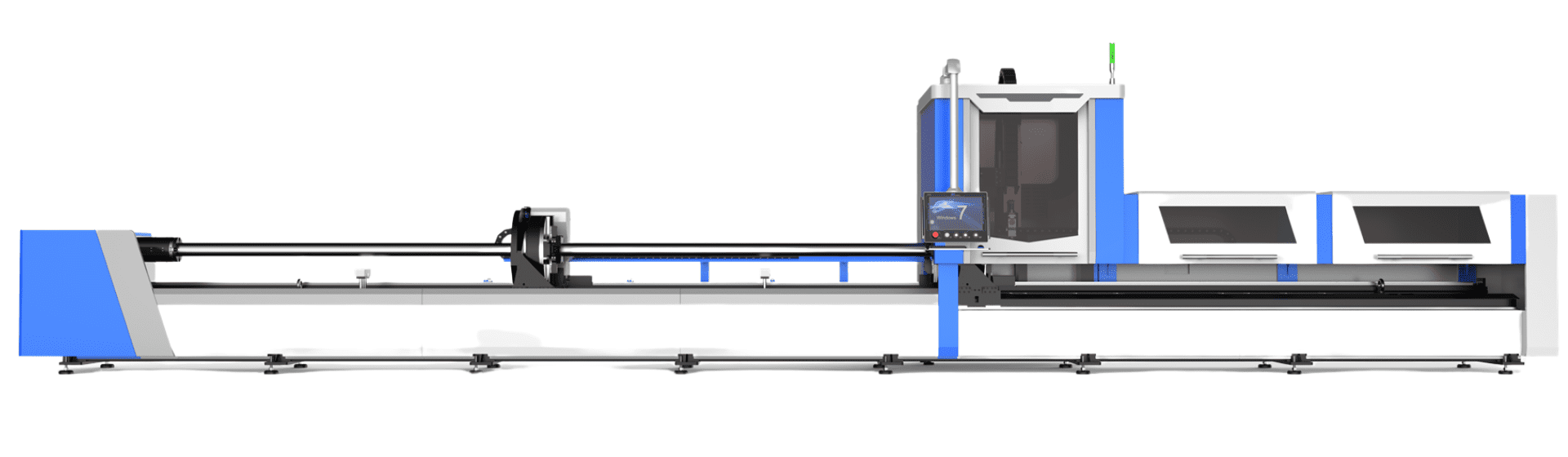
Decision-making Framework
- Identify the material type and assess its compatibility with wet or dry laser cutting.
- Determine the thickness of the tube and evaluate which method provides optimal results.
- Consider precision requirements and select the method that meets those specifications.
- Evaluate production volume and choose a process that aligns with efficiency needs.
- Assess cost implications associated with each method (e.g., equipment, maintenance) and factor them into the decision-making process.
- Explore case studies or seek expert advice if unsure about which method is best suited for specific needs.
Evaluate whether your application benefits from the intricacies of pulsed laser cutting or the rapidity of dry cutting with high peak pulse power. By considering these factors and following this decision-making framework, individuals can determine whether wet or dry laser tube cutting is most appropriate for their unique requirements.
Factors to Consider for Successful Laser Tube Cutting
Embarking on a successful journey in laser tube cutting requires more than just choosing between wet and dry methods. It demands a keen understanding of various factors that collectively shape the outcome of your cutting endeavors. Let’s delve into the essential considerations that pave the way for triumph in this precise art.
Material Selection
The foundation of any laser cutting project lies in the material you’re working with. Understand the properties of your chosen material – be it metal, plastic, or composite – and how it interacts with both wet and dry cutting methods. Material thickness, hardness, and thermal conductivity all play a role in determining the ideal approach.
Design and Precision
The design of the cut is a pivotal aspect. Ensure that your design is optimized for the laser cutting operation you’ve selected. Pay close attention to corners, edges, and intricate details that might require additional considerations for either wet or dry cutting. Precision in design translates to precision in results.
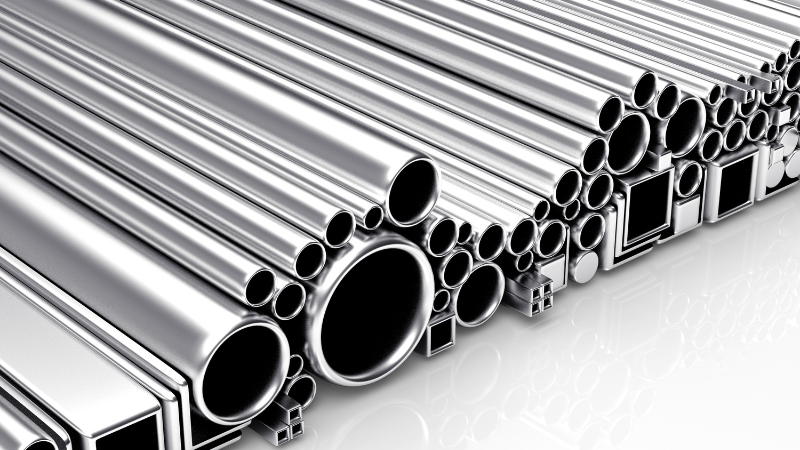
Laser Power and Speed
Laser parameters namely laser power, pulse frequency, and cutting speed significantly affect the cutting qualities. Balancing laser power and cutting speed these two laser process parameters is a delicate dance. Higher laser power might be preferable for thick materials, while lower power might suit thinner ones. Similarly, cutting speed impacts heat buildup – a crucial factor in both wet and dry methods. Striking the right balance ensures clean, efficient cuts.
Nozzle and Focus
In wet cutting, the nozzle’s role in water delivery is vital. Ensure proper alignment and clearance to prevent interference with the laser beam. In dry cutting, achieving the right focus point is essential for optimal beam intensity. Calibration and regular maintenance of these components are crucial for consistent results.
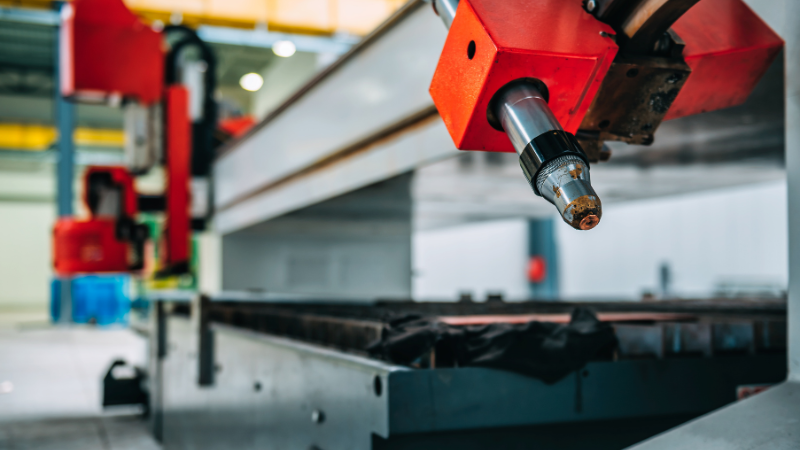
Exhaust and Dust Collection
Efficient exhaust and dust collection are often overlooked but integral for a smooth operation. Both wet and dry cutting generates byproducts that need to be managed. Adequate systems to remove waste, fumes, and dust contribute to a cleaner work environment and better end results.
As you traverse the intricate landscape of laser tube cutting, remember that each factor contributes to the holistic success of your endeavor. The fusion of technical know-how and practical application is what propels your journey towards excellence.
FAQs
What materials can be cut using laser tube cutting?
Laser tube cutting is suitable for a wide range of materials including metals like steel, stainless steel, aluminum, brass, and copper as well as non-metallic materials like plastic or wood.
Can I achieve complex shapes with laser tube cutting?
Yes! Laser tube cutting allows you to achieve intricate designs and complex shapes with high precision. The versatility of laser technology enables you to create customized cuts according to your specific requirements.
How fast is laser tube cutting compared to traditional methods?
Laser tube cutting like fibre lasers is significantly faster than traditional methods such as sawing or milling. The advanced technology of lasers enables quick and precise cuts which can greatly improve productivity in manufacturing processes.
Conclusion
In the intricate realm of laser tube cutting, where precision meets innovation, the choice between wet and dry methods holds the power to redefine manufacturing outcomes. This exploration has unveiled the distinct advantages each approach offers, from wet cutting’s heat control and surface finesse to dry cutting’s efficiency and speed.
With a keen eye on factors like material selection, design, power density, and safety, we can carve a path toward successful laser tube cutting endeavors. In this evolving landscape, the interplay of considerations and techniques paves the way for excellence, enabling us to create with accuracy and efficiency, delivering results that resonate across industries and application scenarios.
Ready to Elevate Your Laser Tube Cutting? Discover Baison Laser’s Expertise!
At Baison Laser, we’re your partners in precision and innovation. If you don’t know how to improve the cutting level, our expertise can guide you towards optimal results. Uncover the power of cutting-edge technology combined with industry insights. Reach out today and let’s transform your laser cutting journey together. Contact us to learn more about how Baison Laser can enhance your production processes.