From significant cost reductions to enhanced precision and speed, laser cutting is the key to unlocking your business’s next project potential. Join us as we delve into this transformative technology, providing professional insights and valuable information on laser-cutting projects.
What is Laser Cutting Machine?
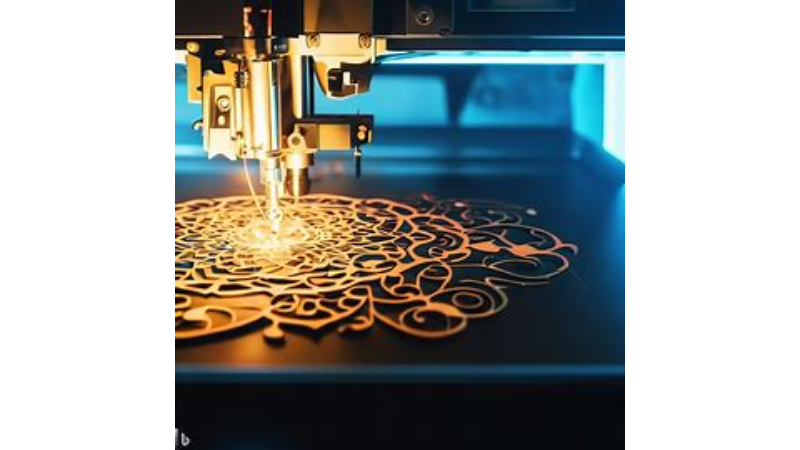
Laser cutting machines or lasers are advanced manufacturing tools that utilize a high-powered, focused laser beam to laser cutters through, engrave, or etch various materials with extreme precision and accuracy.
The term “laser” stands for “Light Amplification by Stimulated Emission of Radiation.” In essence, a laser is an amplified light source that emits photons in a highly concentrated, coherent beam.
Working Principle of Laser Cutting Machine:
The working principle of a laser cutting machine involves three primary components: a laser source, a focusing system, and a CNC (Computer Numerical Control) system. The laser source generates the laser beam, which is then focused by the focusing system (usually a lens or a mirror) onto a specific point on the material’s surface.
The CNC system directs the movement of the laser head, guiding the laser beam across the material in a predetermined pattern based on digital designs.
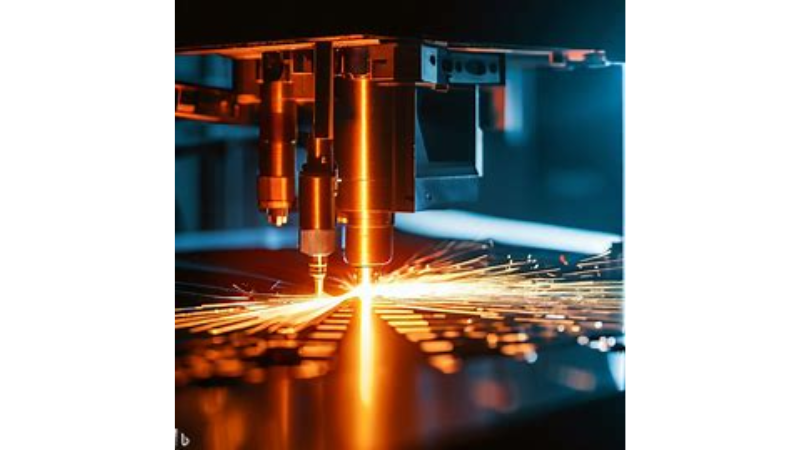
As the laser beam interacts with the material, it rapidly heats, melts, or vaporizes it, creating a clean, precise cut. The process is highly controlled, resulting in minimal material distortion and waste.
Laser-cutting machines are versatile and can work with a wide range of different types of materials, including metals, plastics, wood, glass, textiles, and more. Their precision, speed, and efficiency make them ideal for various applications, from intricate design work to large-scale industrial production.
Advantages of Laser Cutting Machines
Here are some of the advantages and new possibilities of laser-cutting machines that can revolutionize your small business and set you apart from the competition:
1. Precise Cuts:
Laser-cutting machines provide unparalleled precision and accuracy, allowing for intricate designs and complex geometries that would be difficult or impossible with traditional cutting methods. The focused laser beam ensures clean, smooth edges with minimal kerf, resulting in high-quality finished products.
2. Reduced Waste:
The precision of laser cutting leads to minimal material waste, as cuts can be made very close to one another without compromising the structural integrity of other lines of the material. This reduction in waste translates to cost savings, as you’ll use less raw material and require less time for post-processing.
3. Versatility:
Laser-cutting machines can work with a wide variety of materials, including metals, plastics, wood, glass, textiles, and more. This versatility allows small businesses to expand their product offerings and explore new creative possibilities, catering to a broader range of customers.
4. Faster Production:
Laser cutting is a highly efficient process that can significantly reduce production time compared other cutting methods or to traditional cutting methods. The CNC system ensures rapid, accurate movement of the laser head, allowing for swift completion of complex designs and large-scale projects.
5. Automation:
Laser-cutting machines operate using digital designs and CNC control, enabling automated production with minimal human intervention. This automation reduces the likelihood of errors and allows for consistent, high-quality output, which is essential for maintaining a competitive edge in the marketplace.
By embracing laser-cutting technology, your small business can benefit from increased efficiency, cost savings, and a competitive edge in the market.
Applications of Laser Cutting Machines

- Automotive Manufacturing: Laser cutting plays a crucial role in the automotive industry, where precision, efficiency, and high production volumes are essential. From cutting body panels and engine components to creating custom automotive parts, laser-cutting machines deliver exceptional quality and performance.
- Appliance Manufacturing: Household and commercial appliances often require intricate components and precise assembly. Laser-cutting machines allow for the creation of accurate, complex parts and contribute to the overall aesthetic and functional appeal of appliances, such as refrigerators, washing machines, and air conditioners.
- Heavy Industry & Transport: Laser-cutting machines are widely used in the manufacturing of heavy machinery and transportation equipment, such as trains, trucks, and cranes.
- Aerospace: The aerospace industry relies on laser cutting to produce lightweight, high-strength components with intricate geometries. The precision and accuracy offered by laser-cutting machines are critical for meeting strict aerospace standards and ensuring the safety and reliability of aircraft and spacecraft.
- Fashion and Textile: Laser cutting machines are used in the fashion and textile industry to cut intricate patterns, create unique designs, and even engrave custom logos or artwork onto fabrics. The precision and speed of laser cutting enable designers to push the boundaries of their creativity and produce innovative products.
By showcasing the numerous applications of laser cutting technology across various industries, you can further emphasize their potential to revolutionize small businesses and drive growth in diverse sectors.
How Small Businesses Save Costs with Laser Cutting Machines
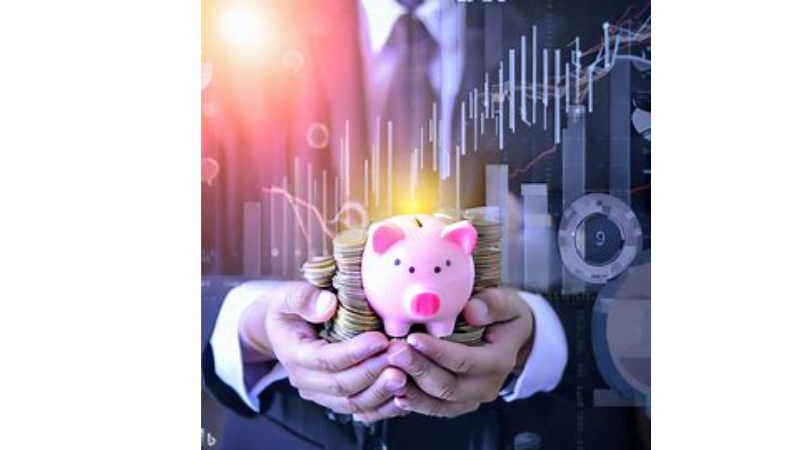
Laser-cutting technology has transformed the way small businesses create and manufacture products. It offers various advantages that enable businesses to save on costs while maintaining high quality and efficiency. You can this article to learn how to choose laser cutters for small businesses.
Here are some ways small businesses can save money on laser-cutting costs even with laser-cutting machines:
1. Reduced Material Waste:
Laser cutting is a highly precise process allowing large quantities of intricate and detailed designs to be cut with minimal material waste. The machine’s software optimizes laser cutters’ cutting patterns to use the material efficiently, leading to reduced scrap and offcuts. This saves on material costs and contributes to a more sustainable production process.
2. Faster Production Times:
Laser-cutting machines can operate at high speeds, cutting complex shapes and patterns in a fraction of the time it would take using traditional methods. This increased efficiency leads to faster production times, allowing businesses to meet tight deadlines and handle larger volumes of work.
3. Reduced Labor Costs:
Since laser-cutting machines are automated and require minimal human intervention, small businesses can save on labor costs. The machine can run continuously without requiring multiple operators or frequent breaks and regular maintenance. This also minimizes the risk of human error and ensures consistent quality across all products.
4. Enhanced Product Quality:
Laser-cutting technology provides highly accurate and clean cuts, resulting in products with a superior finish. This increased quality can lead to higher customer satisfaction and fewer returns or reworks, which ultimately saves businesses money in the long run.
5. Scalability and Flexibility:
Laser-cutting machines can be easily scaled up or down to meet changing production needs. Small businesses can use this flexibility to adapt to market demands, reducing the need for expensive retooling or investing in additional equipment.
Costs of Laser vs. Plasma vs. Traditional Mechanical Cutting
Here’s a table comparing the costs of laser cutting, plasma cutting, and traditional mechanical cutting based on operational costs, cutting time, and machine costs:
Cutting Method | Operational Costs (per hour) | Machine Costs |
Laser Cutting | Operational costs typically average around $20/hour. | The cost of a new laser cutter starts from 350,000 USD and can go all the way up to a million USD, depending on the features of the machine |
Plasma Cutting | Operational costs usually average around $15/hour. The machines themselves can be less expensive than laser cutters. | Plasma cutters can range from several hundred dollars for basic hobby units all the way up to five figures for industrial-grade systems capable of high-precision cuts on thick materials |
Traditional Mechanical Cutting | The cost of traditional mechanical cutting can vary widely depending on the specific method used and the materials being cut. | The machines themselves can be less expensive than laser cutters and plasma cutters |
It’s worth noting that while the laser cutting process may have higher operational costs than plasma cutting, it offers a much higher level of precision. Additionally, plasma cutting can only be used on conductive materials, while laser processes can cut a wider range of materials, including wood and plastics.
How Can Small Businesses Improve Efficiency with Laser Cutting Machines?
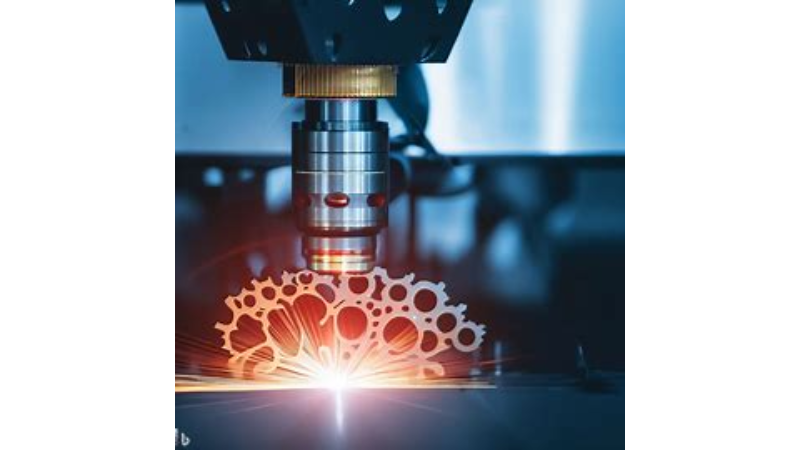
Small businesses can significantly improve efficiency by adopting laser-cutting machines in various aspects, such as speed, accuracy, and consistency. Here’s how laser-cutting technology enhances efficiency:
- Faster Production Speed: Laser-cutting machines operate at high speeds, completing complex shapes and patterns in a fraction of the time it would take using traditional methods. This increased efficiency leads to faster production times, enabling businesses to meet tight deadlines and handle larger volumes of work.
- Higher Accuracy: Laser cutting technology provides highly accurate and clean cuts, resulting in products with a superior finish. The precision of laser cutting machines ensures that even the most intricate designs can be achieved, minimizing the need for additional finishing processes and reducing overall production time.
- Consistency and Quality: Laser cutting machines are automated and require minimal human intervention, minimizing the risk of human error and ensuring consistent quality across all products. This level of consistency means fewer reworks or rejected products, saving time and resources.
- Reduced Labor Costs: Since laser cutting machines are automated, they require fewer operators than traditional cutting methods. The machine can run continuously without the need for multiple operators or frequent breaks, reducing labor costs and increasing overall efficiency.
Small businesses can significantly improve their efficiency and stay competitive in the market by leveraging the speed, accuracy, consistency, and other benefits of laser-cutting machines.
How can laser cutting machines increase efficiency in the manufacturing process?
Laser-cutting machines can significantly increase efficiency in the manufacturing and simple design process, providing numerous benefits to small businesses. Here’s how these how laser cutting machines can help small businesses reduce costs and increase efficiency, enhance productivity, and enable businesses to take on more projects and improve turnaround times:
- Faster Production Speeds: Laser cutting machines operate at high speeds, allowing businesses to complete projects more quickly than with traditional cutting methods.
- Improved Turnaround Times: With faster production speeds and minimal setup times, laser-cutting machines enable businesses to deliver products to customers more quickly. This can lead to improved customer satisfaction and a stronger reputation for prompt delivery and service.
This ultimately leads to increased revenue, growth, and a more competitive position in the market.
How can laser cutting machines improve operations and quality?
Laser-cutting machines can significantly improve business operations and product quality in various ways, leading to increased efficiency, reduced costs, and enhanced customer satisfaction. Here’s how laser-cutting technology can benefit businesses:
- Enhanced Product Quality: Laser cutting technology provides highly accurate and clean cuts, resulting in products with a superior finish. The precision of laser cutting ensures that even the most intricate designs can be achieved with minimal errors, leading to higher customer satisfaction and fewer returns or reworks.
- Versatility Across Industries: Laser-cutting machines can cater to a wide range of industries, including automotive, aerospace, electronics, medical, and consumer goods. This versatility allows businesses to serve a broader client base and easily explore new markets.
- Improved Safety: Laser cutting is a non-contact process, reducing the risk of injuries and accidents associated with traditional cutting methods. This improves worker safety and helps businesses avoid potential downtime and costs related to workplace injuries.
Factors to Consider when Choosing a Laser Cutting Machine
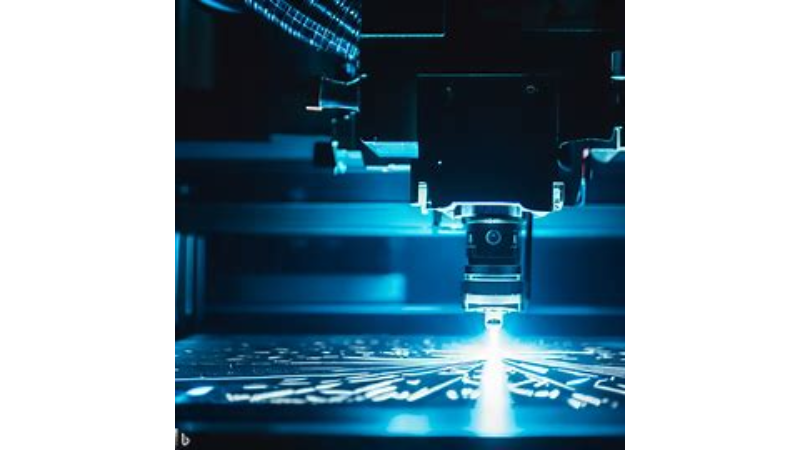
When choosing a laser cutting machine, several factors must be considered to ensure that the machine meets your business’s specific needs and requirements. Here are some key factors to keep in mind:
1. Cutting Line:
The width of the cutting line, or kerf, is essential for producing precise cuts. A smaller kerf ensures better accuracy and minimizes material waste. Consider the type of laser (CO2, fiber, or crystal) and its power, as these factors will influence the cutting line width.
2. Edge Quality:
The quality of the cut edge is critical for the final appearance and functionality of the product. Examine the machine’s ability to produce clean, burr-free edges with minimal heat-affected zones, which can affect the material’s properties. Higher-quality edges reduce the need for additional finishing processes, saving time, energy, and resources.
3. Sheet Metal Thickness:
Different laser-cutting machines are designed to handle various sheet metal thicknesses. Ensure that the machine you choose can handle the range of material thicknesses you work with most frequently.
4. Cutting Speed:
The cutting speed directly impacts production efficiency and turnaround times. Compare the cutting speeds of different machines to ensure that the chosen laser cutter can meet your production demands.
5. Material Compatibility:
Some laser-cutting machines are better suited for specific shapes and materials, such as metals, plastics, or wood. Ensure that the laser cut-out machine you choose is compatible with the materials you plan to work with most frequently.
6. Initial Investment and Operating Costs:
Evaluate the machine’s initial cost, maintenance, and operating costs. While a more expensive machine might offer better performance, ensure that it aligns with your budget and offers a reasonable return on investment.
Conclusion
Embracing laser cutting: laser technology is a game-changer for small businesses, providing unmatched efficiency and cost savings that revolutionize the way you operate.
Investing in a laser cutting machine can streamline production processes, minimize material waste, and deliver high-quality products with faster turnaround times. This cutting-edge technology allows your business to take on more projects, expand your offerings, and ultimately increase revenue.
Transform Your Small Business with Baison Laser’s Cutting-Edge Technology
Don’t let your small business fall behind in today’s competitive market. Embrace the future of manufacturing with Baison Laser‘s state-of-the-art laser cutting machines, designed to deliver unmatched efficiency and cost savings.
Investing in our cutting-edge technology can revolutionize your company’s production processes, improve product quality, and exceed customer expectations. Contact us now!