Laser machines are known for their efficiency, speed, and precision. They offer a fast-paced production system. Loading and unloading systems are essential for these machines to match fast-paced production.
Manual loading and unloading have become obsolete as it takes longer, increasing downtime between jobs. A fast and efficient loading and unloading system speeds up production and is safer, cost-effective, and more efficient.
This article will discuss some loading and unloading systems for laser cutting machines. We will discuss several loading and unloading systems that are in use and will also compare these methods to understand which one is the best loading or unloading system.
Before discussing loading and unloading systems types, let’s understand what they are and how they work.
What Is a Loading and Unloading System?
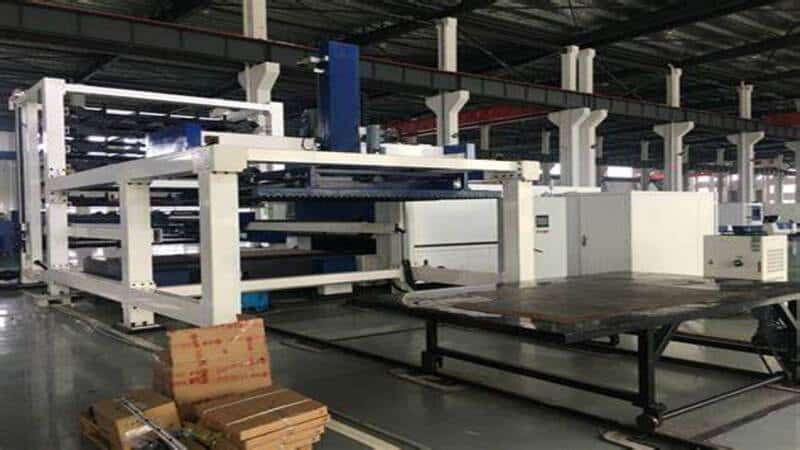
The loading system loads raw material into the laser cutting machine. It can be metal sheets, tubes, or other raw materials. It consists of a storage area and a material handling system. Unloading is collecting the cut material and scrap from the cutting area. Both loading and unloading systems can be manual, partially, or fully automated.
Types of Loading and Unloading Systems of a Laser Cutting Process
Here are a few loading and unloading systems of laser cutting systems.
Manual Loading/Unloading
Manual Loading and unloading are the traditional way to load a laser cutting system. It means the machine operator load or unloads the machine.
An operator lifts the raw material for the manual system and positions it in the laser cutting machine’s designated containers. He ensures the right placement, position, and angle in the optimal cutting position. He removes the parts when the machine is finished and separates scrap from the cut material.
Advantages of Manual Loading System
Here are a few advantages of a manual loading system.
- Lower Initial Cost: The manual loading and unloading system is low-cost. Manufacturers do not have to buy expensive automated loading systems. It may seem like saving money, but it has lots of disadvantages.
- Flexible Material Handling: Manual loading provides flexible material handling. An operator can adjust the sheet or tower to a specific angle, which may be essential for working on irregular shapes.
Disadvantages
- The manual system requires an operator always on the machine to load or unload the material. It causes high labor costs.
- Manual loading and unloading have a high risk of operating errors. The operator may not position the raw material in the optimal position.
- It’s a time-taking process unsuitable for high-volume production, requiring an automated loading and unloading system.
Semi-Automatic Loading/Unloading
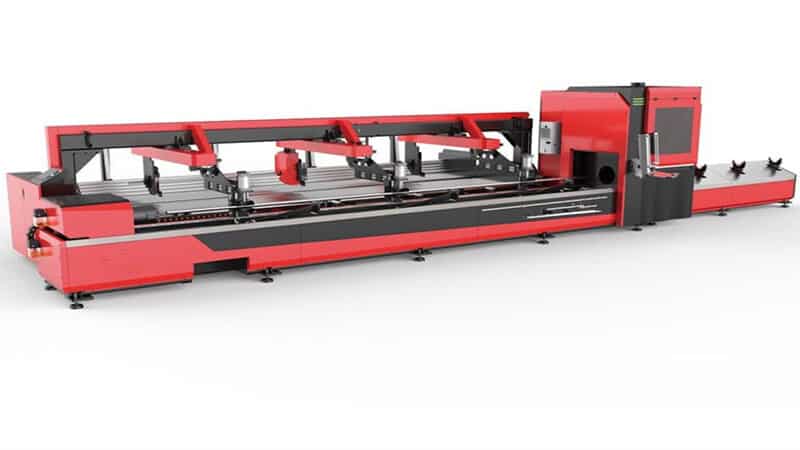
Semi-automatic loading and unloading system is a combination of automatic and manual systems. In this loading system, some aspects are automatic, while others require manual intervention.
The operator loads the material into the laser cutting machine in a semi-automatic loading and unloading system. They can load the maximum capacity of raw material all at once. The semi-automatic system can adjust the tube or sheet to an optimal position, and the operator is not required to adjust the material to the correct position.
Once the material is cut, the machine’s operating system signals the loading equipment to transfer the material to the unloading area. The operator removes the finished product at a separate storage area, collecting scrap in the bin.
Advantages
- The semi-automatic system offers better productivity.
- It causes less labor cost than a manual system.
- Less operator intervention means less operating error possibility.
- Offers some flexibility in material handling.
- Less expensive system.
Disadvantages
- Still, some labor is required for this system.
- Expensive than manual loading and unloading.
Automatic Loading/Unloading
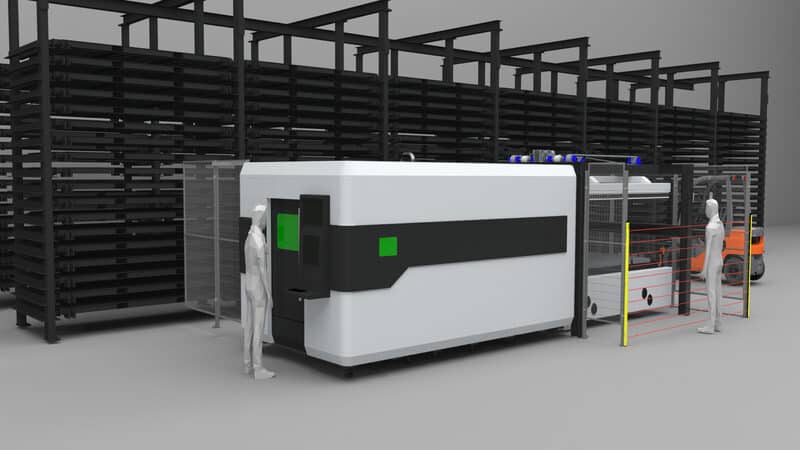
A fully automatic loading and unloading system requires no operator for material loading or unloading. It’s a fast-paced system that suits high-volume production. The process allows a long period of laborless production process.
In an automatic system, the material is loaded by a vacuum lifter. Material is organized into stacks or pallets. The automatic system consists of a material handling system and an automated vehicle transporting the material to the cutting bed.
Sheet metal or tube is held onto its place in a clamp. The machine automatically positions the material in its position. After the laser machine has cut the material, the suction cup picks it up and places it on a conveyer or stack. The process is repeated unless all sheets are cut and stacked.
The automatic loading and unloading system may or may not have a storage unit. Some types of automatic loading are:
- Loading and unloading carts
- Loading and unloading towers
- Loading and unloading robots
Benefits of Automatic Loading System
- Reduce the labor cost.
- The production process can continue for a long time without needing any intervention; thus, it boosts production volume.
- An automatic loading/unloading system is a fast process that increases productivity. No time is wasted in emptying raw materials or collecting the finished product.
- It’s an automatic system that optimizes the material for the laser cutter. The room for error is less as machines are more accurate than manual positioning.
- No risk of accidents is invloved when material is handled with the machines. There is no risk of labor handling the material, which reduces the risk of accidents.
Disadvantages
- Small-scale or lower-volume production may not justify the cost of investment.
- It may require some flooring space for the loading and unloading machine.
- A loading and unloading machine may be restricted to a specific raw material size or thickness.
Want to learn more about automation system that can boost your laser cutting efficiency? Click the button below!
Shuttle Table System
The shuttle table system consists of two or three tables. These tables rotate in an endless loop for loading, cutting, and unloading simultaneously. One table loads and moves to the processing zone.
After the cutting and unloading process, it moves to the stacker or conveyer, while the other table moves for the loading, cutting, and unloading process. This way, it is a seamless cycle continuous nonstop that increases productivity without any downtime.
These tables can further be combined with the automatic handling system.
Advantages
- The shuttle system offers nonstop production of large batches with no downtime.
- It includes a storage system or scraps collecting wagons to collect cut parts and scrap.
- It fits with the production facility and may not always need to stand on the floor.
Pellet Changer System
The Pellet changer is another automatic system. It can be a fully or semi-automated system. It uses a pellet to store the raw material. Once the material is cut, it is changed with another pellet without any operator. The Pellet changer system can be fully automatic or semi-automatic.
Which Type of Loading and Unloading System Is Your Best Choice?
Choosing one loading and unloading system depends on different factors, including the type of material and desired production rate. A vacuum and automatic material feeder are suitable for light materials like aluminum sheets or plastic.
A pallet changer and sheet metal storage system is suitable for heavy materials like thick metal sheets and tubes. Shuttle tables or robotic handlers are suitable for delicate materials like glass or ceramic, allowing easy loading and unloading systems.
Things to Consider While Choosing a Loading and Unloading System?
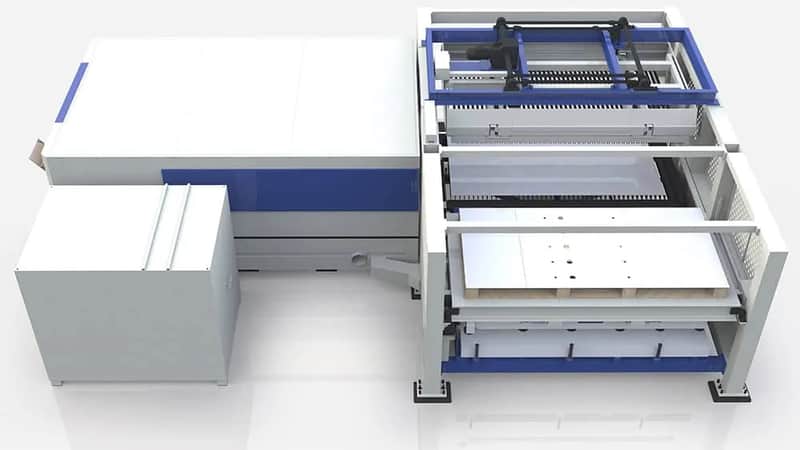
Here are a few things you should consider while selecting a loading/unloading system for a laser machine:
Material Type
Not all loading and unloading machines are built for one material type. Check the specifications to ensure it is built for a specific type of material.
Material Thickness
Loading and unloading systems can deal with specific thicknesses of material. So consider the specific material thickness capacity of the machine before buying.
Floor Space
Some machines come with huge storage units and are difficult to accommodate. Some automatic loading/unloading system comes with a multi-layer storage unit that saves space and improves the utilization rate of the site.
Automation Level
As we said, if you don’t need a fully automated loading and unloading system for material flow, semi-automatic systems can require some material handling by labor. Fully automatic system; no time is wasted waiting for the next sheet.
Integration with Laser Cutting Machine
Make sure you check before buying if the loading/unloading system can be seamlessly integrated with your cutting table. For example, some special loading and unloading systems exist for fiber laser machines. The loading/unloading system should integrate with the laser machine’s control panel to increase productivity and efficiency.
Customer Care and Maintainenece
Choose a loading/unloading system that is easy to maintain. Look for a brand that offers good support and services after purchasing.
Storage Option
Loading/unloading systems provide some storage for raw materials and gather finished products. Make sure you check the storage option whether it suits your manufacturing needs. Some systems have a multi-layered storage option that covers less space yet provides better storage options.
Scrap Handling
A part of the loading/unloading system separates scrap from the finished parts. Ensure you check the mechanism and understand how and where the loading-unloading system will stack the scrap and how efficiently it is.
Conclusion
Whether using a pellet changes site or a robotic loading or unloading, automation solutions for loading/unloading is designed to speed up the production process and reduce manual intervention. The level of intervention differs with different loading and unloading systems.
The loading and unloading system is an important process of production. It can slow down or increase the productivity of your laser-cutting machine. A seamless, integrated system may suit the high production level but may be overkill for medium to slow production.
Consider all your options before selecting a loading and unloading system. Even semi-automatic and automatic machines have different types, like Robotic material handlers, that suit a specific application.
Speed Up the Production Level with Baison’s Laser Cutting Machines
Laser machines are the most efficient and time-saving way of metal fabrication. Baison offers high-tech quality fiber laser cutting and other machines built on modern technology.
These machines are available for any business size and suit the need for production on small, medium, and large scales. Our laser cutting, welding, and engraving machines are user-friendly and require minimal maintenance.
Baison offer free application evaluation to help customers choose the laser system that suits their manufacturing needs. Don’t hesitate to click the button below to contact us!