What Is the Tower Automation System (TAS)?
As the name suggests, Tower Automation System (TAS) helps automate laser cutting operations. This includes automating the material loading, handling, cutting, and unloading.
As a result, it reduces the amount spent on each task by speeding up the process. Moreover, it also reduces the required labor, leading to significant savings for the manufacturer.
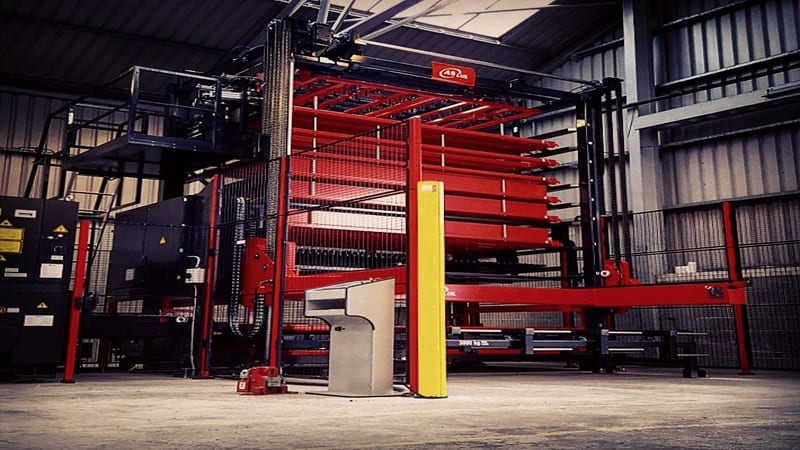
Many manufacturers around the globe use TAS and warehouse automation systems integrated with their laser machines to enjoy the benefits. They eliminate the need for manual labor and can achieve continuous cutting processes, enhanced product quality, higher working speeds, and overall efficient productivity.
How Does TAS Improve Laser Cutting Efficiency?
Coming to the technical bit, the TAS handles several things at once to speed up the whole process. These include:
- Material Loading: it has multiple levels of material stored in the tower. This allows the system to load a large chunk of material at once and provide it on demand while the laser-cutting machines work.
- Material Handling: the TAS also has robotic arms which handle the material by transporting it from the material loader to the laser cutter.
- Cutting Automation: this is the part where the TAS system directs the laser cutting machine to cut the material automatically. Hence, there is no need for manual intervention.
- Material Unloading: this is the final step, where the laser-cut material is unloaded from the machine. The robotic arms then deliver cut sheets to the output stations or the next production step, whichever is the case.
The Benefits of TAS in Laser Cutting
Manufacturers who use TAS integrated with laser cutting machines have talked about several benefits that come with it. The most prominent ones that have helped businesses increase production speeds and quality include:
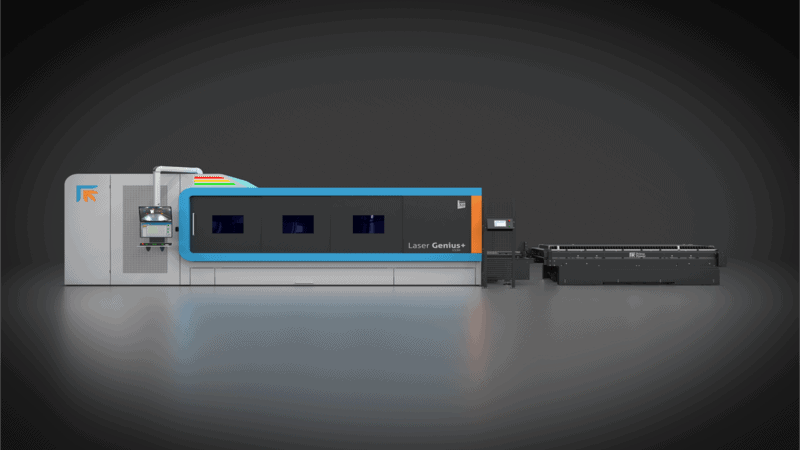
- Versatile and Flexible Automation: the TAS gives manufacturers complete control over the cutting shape and size. On top of it, it also allows them to control the sheet metal material volume for cutting for flexible automation systems.
- Improved Safety: TAS doesn’t necessarily have safety features of its own. However, it improves workplace safety as it eliminates the need for manual labor to transport or handle heavy and bulky material. This reduces injury risks significantly.
- Cost Reductions: as TAS automates and speeds up the whole fiber laser cutting process, it generates more output in less time and uses less labor. Both of this help reduce production costs for the manufacturer.
- Improved Material Flow Continuous: TAS eradicates all bottlenecks in the continuous material flow. Hence, the whole process starting from loading, handling, cutting, and unloading, becomes highly efficient and productive. In fact, a TAS system can also integrate multiple laser-cutting machines for greater efficiency.
- Higher Quality: the system also helps improve the overall product quality with its precision, consistency, and accuracy. Moreover, efficient product handling also contributes to waste reduction.
The Technical Details of TAS
The TAS consists of several components that work in sync to provide the results. These include:
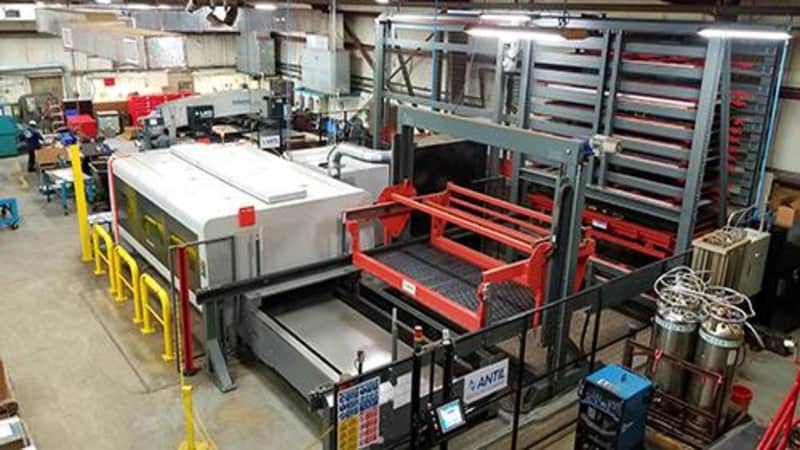
- The control panel acts as the system’s brain, allowing manufacturers to input commands and monitor the process.
- Tower, which has multiple levels for material storage. Some TAS also has a double tower storage system to accommodate material in bulk.
- The transportation of the raw material takes place with the help of a conveyor system.
- For material handling, the TAS has robotic arms that help load and unload when required.
TAS Software
The TAS software is specifically designed to convert manufacturer commands into instructions. It then makes the whole system act in sync to ensure optimal material flow at efficient speeds. The software comes packed with several features, including:
- Job Scheduling
- Machine Health
- Material Tracking
- Job Progress
Integrating TAS into a Laser-Cutting System
To integrate TAS into a laser cutting system, it is vital that the TAS is specifically designed for the specific laser cutter. Typically, the integration process is similar for all kinds of laser-cutting machines:
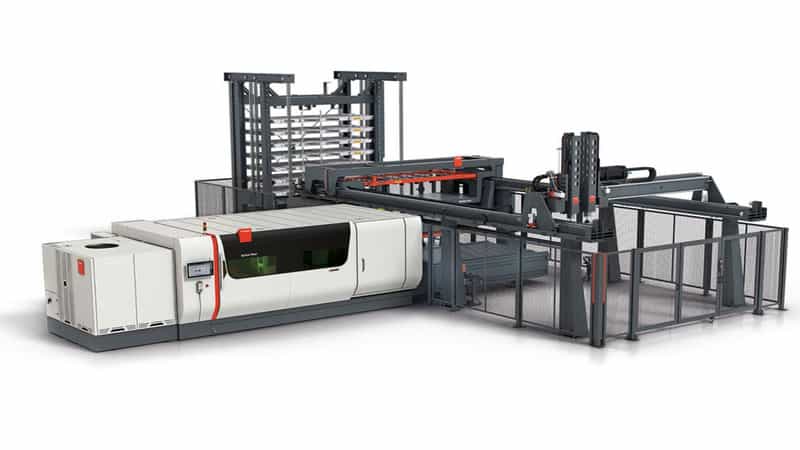
- Design: first, the manufacturer creates a design layout for the TAS. This includes all components of the TAS as well as the laser cutter for optimal material flow.
- Configuration: the next step involves configuring TAS with the laser cutter for effective communication between the two.
- Testing: once configuration is done, the manufacturer tests the integrated system to see if everything works in the right order.
All of this has to happen with perfect planning beforehand. Hence, the manufacturer needs to have a solid understanding of TAS and how the laser cutter works for perfect integration.
The Cost of TAS and Return on Investment (ROI)
Unfortunately, there is no fixed cost for a TAS. This is because the cost varies based on several factors, such as the system capacity, size, customizations, automation, and the brand you work with.
Hence, the typical costs for a TAS can range from a few thousand dollars to a few hundred thousand dollars, just like an extensive warehouse automation system.
Typically, the cost goes higher as you opt for more complex automation systems. For example, if you choose a double row configurations TAS for your fiber laser, the price will be higher. Similarly, if you want full lights-out production, you will have to pay a lot more to create robust automation systems.
The ROI Should Be the Focus
Despite such a high cost, manufacturers still go for TAS integration because it has a high return on investment in the long run. It helps save labor costs, speed up the production process, as well as improve product quality which helps retain clients and build long-term relationships.
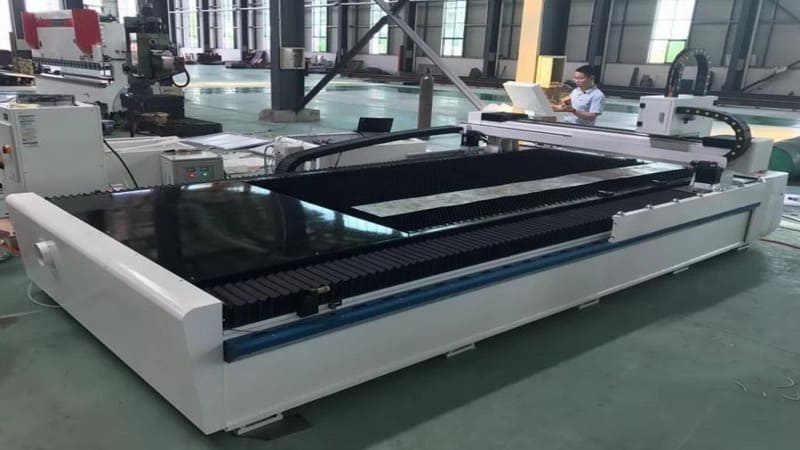
Application Examples of TAS in Action
Many industries take advantage of TAS’s fast and efficient products for their laser-cutting machines. Common examples include:
- Aerospace Industry: complex aircraft require highly precise cut components such as wings, fuselage panels, and sheet metal parts. Here the TAS integrated laser cutter ensures there is no room for mistakes, and the final output is of premium quality.
- Automotive Industry: the automotive industry uses a variety of laser-cut sheet metal parts. Given the high demand for automobiles in the world, TAS comes in handy for speeding up the process to ensure order delays are minimized.
- Industrial Equipment Industry: this industry produces machinery for other industries. Hence, they need efficient and accurate laser-cutting machines that can work at high speeds. TAS helps solve the problem with minimal human input and process automation.
- Medical Device Industry: medical devices, including surgical instruments and stents, require precision cutting. On top of it, the world has an ever-increasing demand for them. TAS laser-cutting machines help reduce material waste and increase these devices’ production capacity and precision quality.
What Are the Challenges and Considerations When Implementing TAS?
Tower Automation Systems sure have their benefits for laser cutting machines. However, all of it does not come without any challenges.
Potential Challenges When Implementing TAS:
- Machine Compatibility: this has to do with TAS integration with a laser cutter. Sometimes integrating TAS software with existing machinery software can pose a great challenge. Hence, manufacturers have to invest hours and money to create perfect integrations.
- Cost: integration of TAS with a laser cutter calls for high initial investment. This comes off as a challenge for some manufacturers who are tight on budget or relatively new in the market.
- Space Limitations: when the TAS is integrated with a laser cutter, the manufacturer has to develop a whole layout for the system to work. This can take up a lot of space as many components, including robotic arms, laser cutting machines, conveyor systems, and storage towers, are in play.
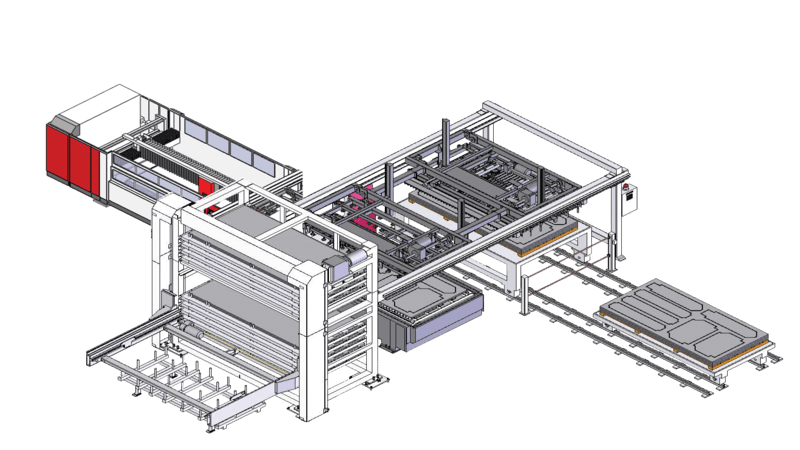
Tips and Considerations for Successful Implementation of TAS:
Here are some key things to keep in mind for the successful implementation of TAS:
Worked With Reputed Manufacturers
Working with an integrated TAS and laser cutter is a complex process. Especially if the TAS in question has a double-tower storage system integrated with multiple laser-cutting machines, it may not require manual labor.
However, it would be best if you had an expert’s technical assistance to ensure everything works in the right order. Hence, working with a reputed manufacturer who provides reliable technical support is vital.
Employee Training
Make sure all employees working around the TAS laser cutting machine get regular training to stay updated with the latest technology.
Long-Term Planning
This is important at the time of TAS integration. Manufacturers must know the potential increase in capacity they will face. Hence, the TAS system should be integrated in a way that it can easily modify it for expansion when required.
Regular Maintenance
TAS-integrated laser-cutting machines also require regular maintenance like any other complex system integration. This ensures long life and optimal functionality at all times.
Conclusion
In conclusion, TAS is an incredible revolution for fiber laser cutting technology. It speeds up the process for manufacturers enabling them to produce finer quality products in less time, with less cost, and with less labor. Anyone who is not making use of this technology and its benefits is missing out.
Are you experiencing increased laser business demand? Do you need precision cutting in less time and less cost? Upgrade to the Tower Automation System (TAS) by Baison Laser and watch your productivity skyrocket. Don’t let your competitors leave you in the dust – invest in TAS today and dominate your industry. Contact Us Today.