Understanding Laser Cutting Gaskets
Gaskets are used to seal off an intersection. A powered laser is used to cut the sheets of different materials in the laser cutting technique. A computer-aided program (CAD) guides the laser along the path to cut a particular shape. This method is particularly useful in cutting complex structures with precision and accuracy compared to the traditional methods.
Laser-cutting services allow you to form the sealing gaskets in a more precise way that can bear tremendous pressure and provide tighter tolerances on the seal. Laser-cutting services save a lot of time and effort by creating their work directly from the CAD file, unlike the traditional die cutting method, which requires a lot of tooling costs and time.
(Here is a detailed comparison guide for laser cutting and die cutting.)
Numerous intricate geometric shapes are necessary to cut out, which can be complex. Still, a laser cutting machine will be able to do it with an accuracy of +/- 0.002″ regardless of what the shape is in terms of accuracy. Fast, accurate results and a speedy process make this process ideal for those who are looking to batch-produce large quantities.
Advantages of Laser Cut Gaskets
Laser cutting is one of the most advanced cutting methods. There are the following advantages associated with laser cut gaskets.
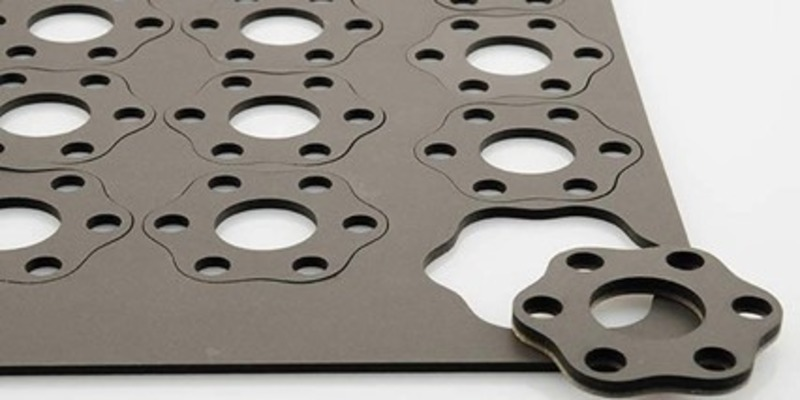
Precision & Accuracy
The formation of laser-cut gaskets requires high-tech laser-cutting technology. This laser-cutting technology ensures precise and accurate gaskets for various purposes.
Since gaskets are the major components in many devices for preventing leaks and maintaining pressure, precision, and accuracy in their cutting are the significant components. Laser-cutting technology undoubtedly fulfills this requirement to provide the best products different industries require.
Material Efficiency
Laser-cut gaskets are available in different materials and used according to their requirements. These materials include a wide variety of rubbers, composites, metals, and plastics. Laser-cutting technology does not produce any waste during the cutting of different materials.
Versatility
Laser cut gaskets are versatile and can be formed in different shapes and designs using different materials, including metal, non-metal, plastics, and other materials.
Consistency
Precision and accuracy are the two most important features that laser-cut gaskets provide to their best laser cutting technology. This means it is possible to maintain uniformity across the production of large batches. The precise cutting process shows high tolerances towards the exerted pressure to prevent leakage.
General Materials for Laser Cutting Gaskets
A wide range of gasket materials are available, each of which offers unique properties suitable for a variety of applications and situations. Materials we frequently use for gaskets include:
- Rubber: The rubber product line is available in a variety of formulations and grades, like rubber gaskets, making it suitable for various applications with widely varying operating conditions and environmental conditions. The parts and production specifications can dictate the type of manufacturing process used.
- Rubber molding compounds: Various shapes and sizes of gaskets are created using rubber molding compounds in processes such as compression molding, transfer molding, and injection molding.
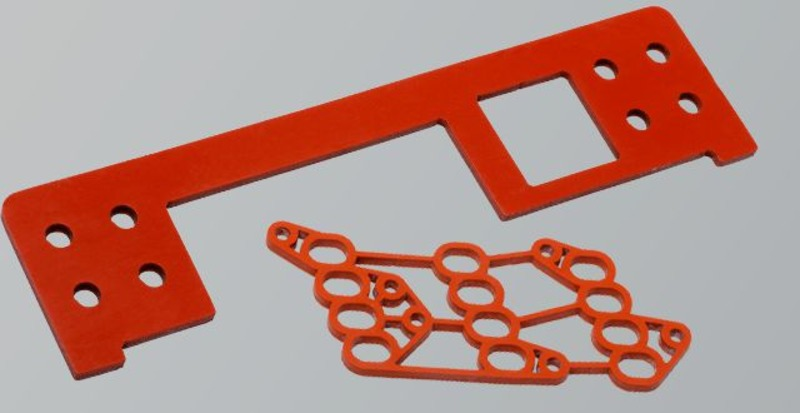
- Foam: Lasers produce clean cuts on these materials, but attention must be given to prevent excessive melting or burning, especially with closed-cell foams.
- Felt: Depending on the density and the binder used in the felt, laser cutting can produce clean edges. Some felt types may burn or char at the edges.
- Plastics: It is a composition of polymers combined with other substances, primarily to give them a unique or enhanced characteristic.
- Electrical insulation: Electrical insulation refers to materials used in electrical applications for their lack of electrical conductivity.
- High-temperature materials: A high-temperature material has been designed with the intention of withstanding the high temperatures. They can be cleanly cut with lasers, but settings must be optimized to prevent burning.
- Metallic Gaskets: For gasket applications, thin metal sheets are often used, like copper, and brass, and they cut cleanly with lasers. Laser cutting metal requires higher power lasers like fiber lasers or Nd: YAG lasers, and there’s often an oxide layer on the cut edge that might need post-processing.
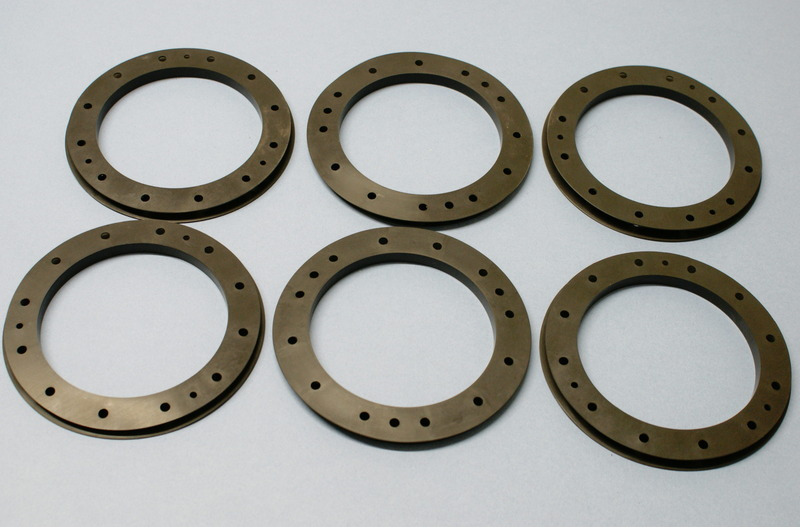
Applications of Laser Cut Gaskets
Laser-cut gasket serves a broad range of different applications in different industry, and their demands and importance also vary. There are the following applications of laser cut gasket:
Automotive
Laser-cutting gaskets play an important role in maintaining the pressure in various parts of engines of automotive. It prevents the leakage of fluid, supports pressure, and also helps keep the car engine cool. Learn about the use of gaskets in automotive engines.
Electronics
Laser-cut gaskets used in the electronic industry consist of different materials, including conductors or insulators. They serve a prominent role in providing a protective seal for sensitive components of electronic devices. Depending upon its material, it can prevent the flow of electrons and other components for the safety of electronic devices.
Aerospace
Aerospace components are made to bear the high external and internal pressure in extreme conditions. Laser cut gaskets serve their purpose of maintaining the closed seals of aircraft. Laser-cut gaskets are important components used for sealing the exposed components of aircraft in extreme conditions.
Industrial Machinery
Gaskets help the high-tech machinery in performing heavy-duty operations without showing any strain on the engines. Moreover, laser-cut gaskets also play a vital role in reducing the vibration and sound of engines used in heavy-duty operations in industrial machinery.
Laser Cut Gaskets Vs. Waterjet Cut Gaskets
Laser cutting is one of the most efficient methods to cut the gasket, now take a look at the difference between it and water jet cutting. The difference between these methods can assist you in getting a better understanding of the different methods used for cutting gaskets.
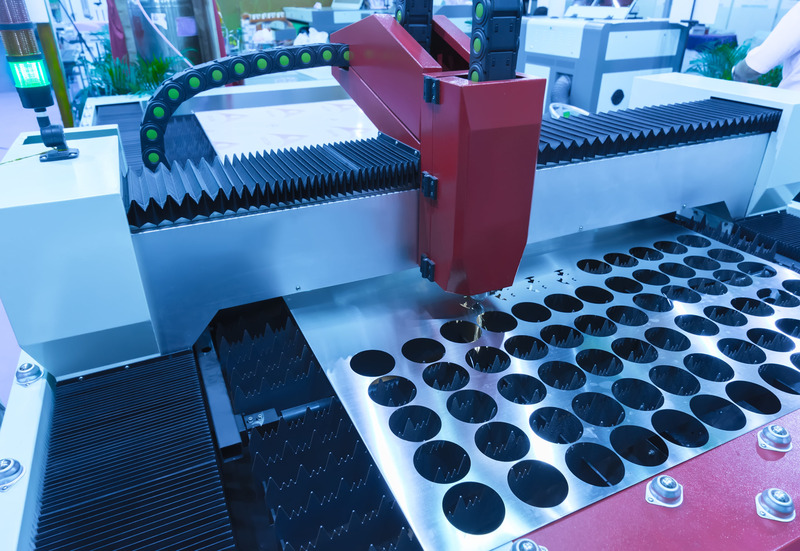
Laser Cutting Gaskets
By using laser cutting, clients are offered the advantage of immediate receipt of their components with tolerances up to +/- 0.002″ with no tooling needed. This makes laser cutting an effective manufacturing method for both low- and high-volume production runs due to its versatility. We can achieve intricate designs using our laser cutting systems without the distortion caused by compression and without the delays caused by tooling.
Lasers often produce a very clean edge with minimal burr. Due to its precision, laser cutting can often result in less wasted material. However, some materials emit fumes when laser cut, requiring proper ventilation.
Waterjet Cutting Gaskets
Waterjet cutting allows for the creation of complex and intricate parts without the use of tooling or compression distortion. A waterjet cutting machine uses a thin, high-pressure stream of water to cut material, so it is ideal for applications where a laser or blade would cause excessive heat. It produces fewer defects than die-cutting and cuts through more layers.
However, the kerf (cut width) of a waterjet is wider than that of a laser, which can result in more waste. The waterjet cutters require more maintenance due to the abrasive nature of the process.
(If you are interested, here is our comparative article on laser cutting and water jet cutting.)
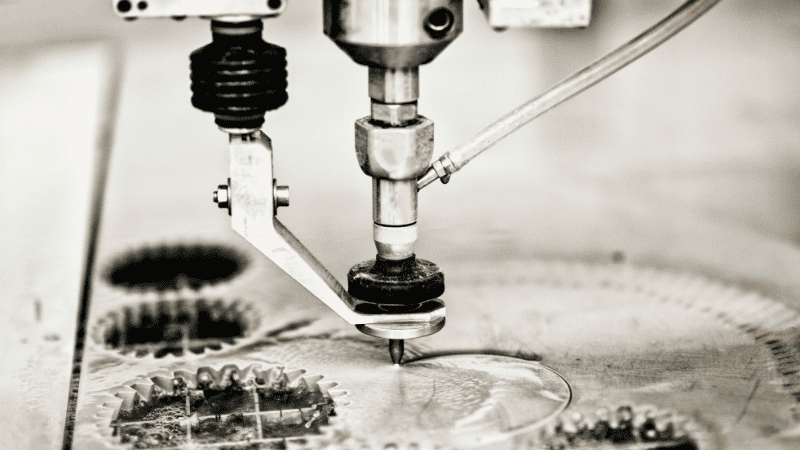
In short, both methods work precisely to cut the complex and custom gaskets without distortion and excessive tooling. Moreover, waterjet cutting can be considered more efficient for materials that are heat-sensitive as compared to the laser cutter. Other than that, both cutting methods provide more precise and accurate results as compared to traditional cutting methods.
Factors to Consider for Laser Cutting Gaskets
Many types of applications require the use of gaskets in order to prevent the escape of fluids or air from leaking out. As gaskets come in many different materials, sizes, and styles, it can sometimes be very challenging to produce the right gasket for your needs. In making this decision, several factors should be considered, including
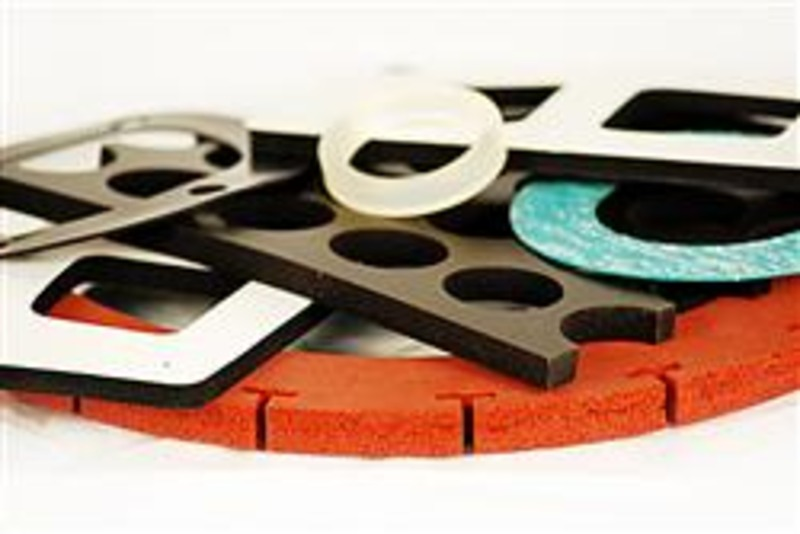
- Gasket materials: the choice of the suitable gasket material depends upon the application environment. You can choose the gasket material that can withstand environmental factors, including water, chemical exposure, etc.
- Laser Type and Power: Different lasers have distinct characteristics, wavelengths, and power outputs. The right laser type and power setting are crucial to efficiently and cleanly cut various gasket materials.
- Cutting Speed: The pace at which the laser moves across the material can profoundly influence the quality of the cut. Too slow, and the material might burn; too fast, and the cut might not go through entirely. The optimal speed depends on material type, thickness, and laser power.
- Heat Affected Zone (HAZ): The HAZ is the area around the cut where the material’s properties may have changed due to the heat from the laser. For some materials, especially those sensitive to heat, this can alter performance or appearance. Minimizing the HAZ is often crucial in gasket applications.
Conclusion
In conclusion, laser cutting offers a precise and efficient method for producing gaskets tailored to specific applications. As with any technology, understanding its capabilities, limitations, and the factors affecting its operation is crucial. When these elements are taken into account, laser-cut gaskets can deliver unparalleled accuracy, consistency, and quality, ensuring optimal performance in their intended applications.
Uncover the Truth About Laser Cutting Gaskets with Baison!
Baison Laser is ready to serve you with their amazing laser cutting services and high-tech laser-cutting technology. At Baison Laser, our professional team provides their best to make custom products according to your needs. By contacting Baison Laser, you can rest assured about the precision and accuracy of the products, not only gaskets. Contact Baison Laser today for a free application evaluation. Our team will be pleased to provide you with a free quote at Baison Laser.