Imagine you’re welding, your mig welder and mig gun at the ready, when the weld spatter starts disrupting your work. This common issue is more than superficial; it risks contamination and the integrity of your welds. Achieving minimal spatter involves refined welding techniques, appropriate filler materials, a stable arc via pulsed MIG, and gas shielding for protection.
So let’s buckle up and discover effective ways to minimize spatter in your welding process. Stay tuned for expert tips that will help you achieve cleaner welds without compromising efficiency or quality.
What is Weld Spatter?
Weld spatter refers to the droplets of molten metal wire that are expelled during the welding process. These droplets can land on nearby surfaces, causing damage or creating an unsightly appearance. Weld spatter typically occurs when the temperature of the weld pool is high enough for small bits of molten metal wire to break away and be propelled outward.
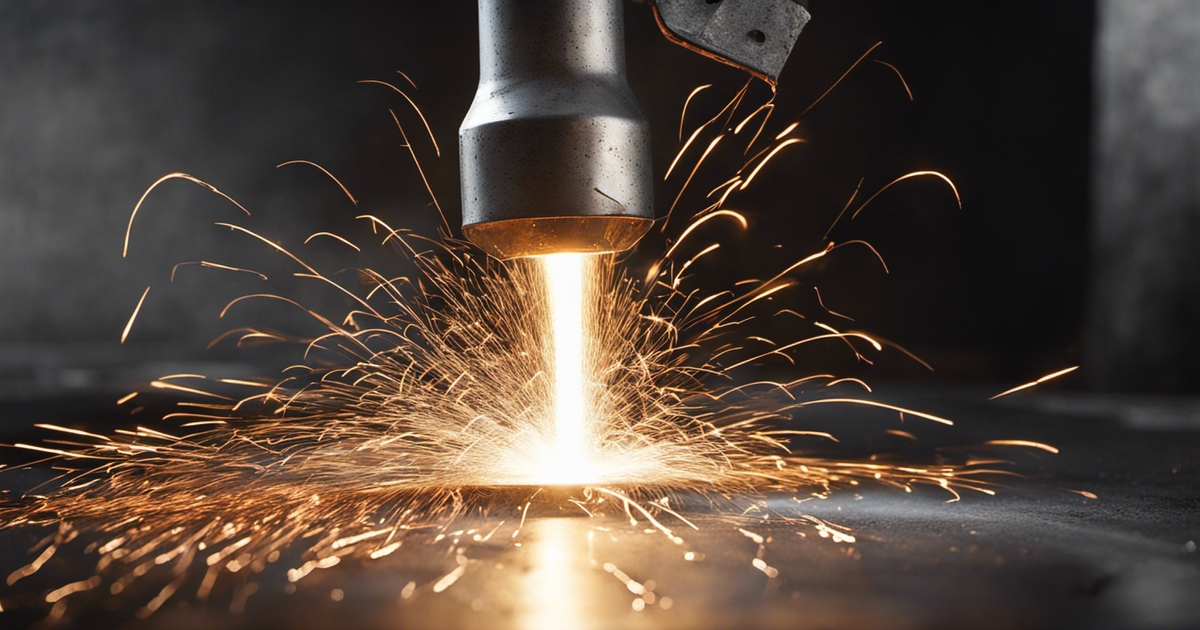
Weld spatter can take various forms, depending on the welding process used. In MIG welding (Metal Inert Gas Welding), for example, it often appears as small beads or splatters of metal that stick to the surrounding area. On the other hand, in TIG welding (Tungsten Inert Gas Welding), it may manifest as fine sparks or particles that scatter around the weld area.
What Causes Welding Spatter?
Welding spatter, those annoying blobs of molten metal that fly off during the welding process, can be a real pain in the neck. But what exactly causes this excessive spatter? Well, there are several factors at play.
1 – Inappropriate Selection of Shielding Gases
Improper shielding gas is one culprit. When the welding arc isn’t properly shielded or restricting gas flow, it can lead to an increase in splatters. The shielding gas acts as a protective barrier between the weld pool and the surrounding air, preventing contaminants from entering and causing spatter.
2 – Incorrect Parameter Setting
Another factor to consider is the relationship between voltage, current, and welding speed. If these parameters are not balanced correctly, it can result in excessive spatter. Too high or too low voltage and current levels can cause erratic arcs and lead to more splatters.
3 – Improper Electrode Angle or Technique
The way you hold your welding torch and position your electrode also plays a significant role in preventing or causing weld spatters. Improper electrode angle or technique can disrupt the smooth flow of molten metal and result in more splatters. It’s essential to maintain a consistent angle and use proper techniques to minimize spatter.
Why is It Important to Prevent Welding Spatter?
Preventing welding spatter is crucial for several reasons. Let’s take a closer look at these reasons and problems.
1 – Effects of Welding Spatter on Equipment and Tools
Welding spatter may seem harmless, but it can wreak havoc on your equipment and tools. The small droplets of molten metal that splatter during the welding process can accumulate on surfaces, causing damage and reducing the lifespan of your equipment. Over time, this buildup can lead to poor performance, decreased efficiency, and even costly repairs or replacements.
- Welding spatter can clog up essential components such as nozzles, tips, and electrodes.
- Accumulated spatter can interfere with the smooth operation of moving parts in welding machines.
- It can cause blockages in gas lines or cooling systems, affecting the overall functionality.
2 – Safety Hazards Associated with Welding Spatter
Apart from damaging your equipment, welding spatter poses significant safety hazards. Those tiny metal droplets are not just a nuisance; they can cause serious injuries if proper precautions are not taken.
- Molten metal fragments can fly off at high speeds and land on unprotected skin or clothing, resulting in burns.
- Spatter can also ignite flammable materials nearby if they come into contact with sparks.
- Inhaling fumes generated by burning spatter is hazardous to respiratory health.
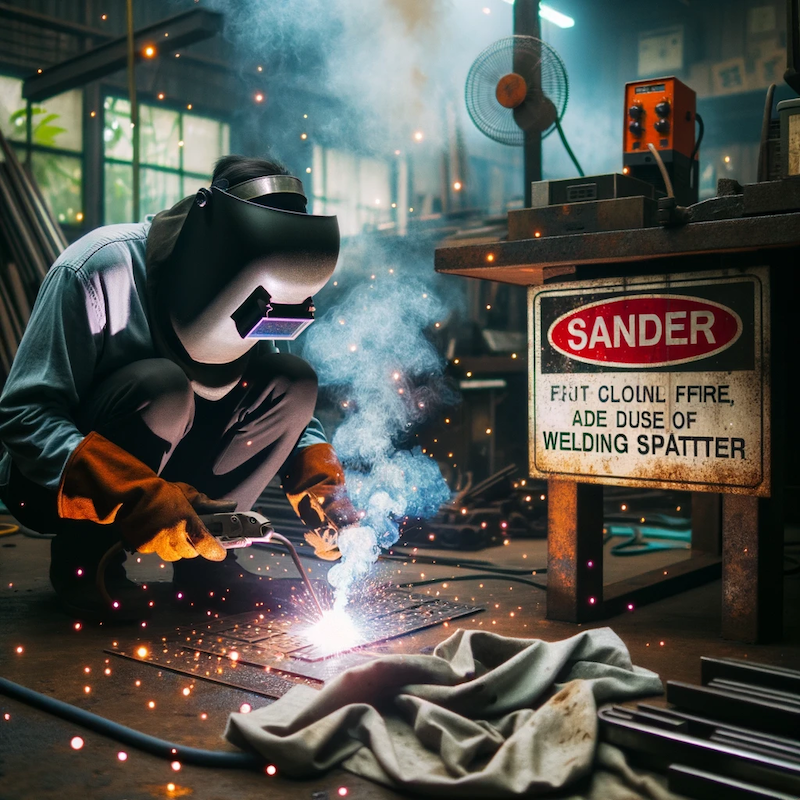
3 – Impact on Welded Product Aesthetics & Quality
In addition to its detrimental effects on equipment and safety, welding spatter affects the aesthetics and quality of welded products. Excessive spatter leaves behind unsightly marks that compromise the appearance of welds. This is particularly crucial for industries where visual appeal matters or when welds need to be painted or coated.
- Spatter interferes with achieving clean welds with smooth edges.
- It creates rough surfaces that may require additional grinding or finishing work.
- High-quality welds free from excessive spattering ensure structural integrity and longevity.
Preventing welding spatter is crucial for maintaining equipment performance, ensuring safety, and producing aesthetically pleasing and high-quality welds. By using appropriate shielding gas and implementing proper welding techniques, you can minimize spatter and enjoy the benefits of cleaner, safer, and more efficient welding.
How to Prevent Weld Spatter? — 7 Tips
Reducing spatter is essential for achieving high-quality welding and ensuring safety. You can’t miss this checklist where we list different ways to avoid excessive weld spatter.
1. Proper Selection and Maintenance of Equipment
To prevent weld spatter, it’s crucial to choose the right equipment and keep it well-maintained. Ensure that your welding machine is in good condition, with a properly functioning wire feeder and contact tip. Regularly inspect and clean these components to avoid any blockages or obstructions that can lead to spatter.
2. Adequate Cleaning and Preparation Before Welding
Before starting the welding process, make sure to clean the metal surface thoroughly. Remove any dirt, rust, paint, or grease using a wire brush or a TIG brush specifically designed for cleaning. Proper cleaning ensures better adhesion between the metal surfaces and reduces the chances of spatters during welding.
3. Apply the Correct Welding Parameters
Using appropriate welder settings is essential in preventing weld spatter. Adjust your welding parameters like voltage, amperage, and welding wire feed speed according to the thickness of the material being welded. Incorrect settings can result in excessive heat or poor arc stability, leading to increased spatter.
Use digital welding machines with preset parameters or consult welding charts to ensure precise settings for materials and weld types.
4. Use Anti-Spatter Sprays or Gels
Applying anti-spatter sprays or gels on the workpiece before welding can significantly reduce spatter. These products create a protective barrier that prevents molten material from sticking to the surface. Simply spray or apply them evenly on the metal surface prior to welding.
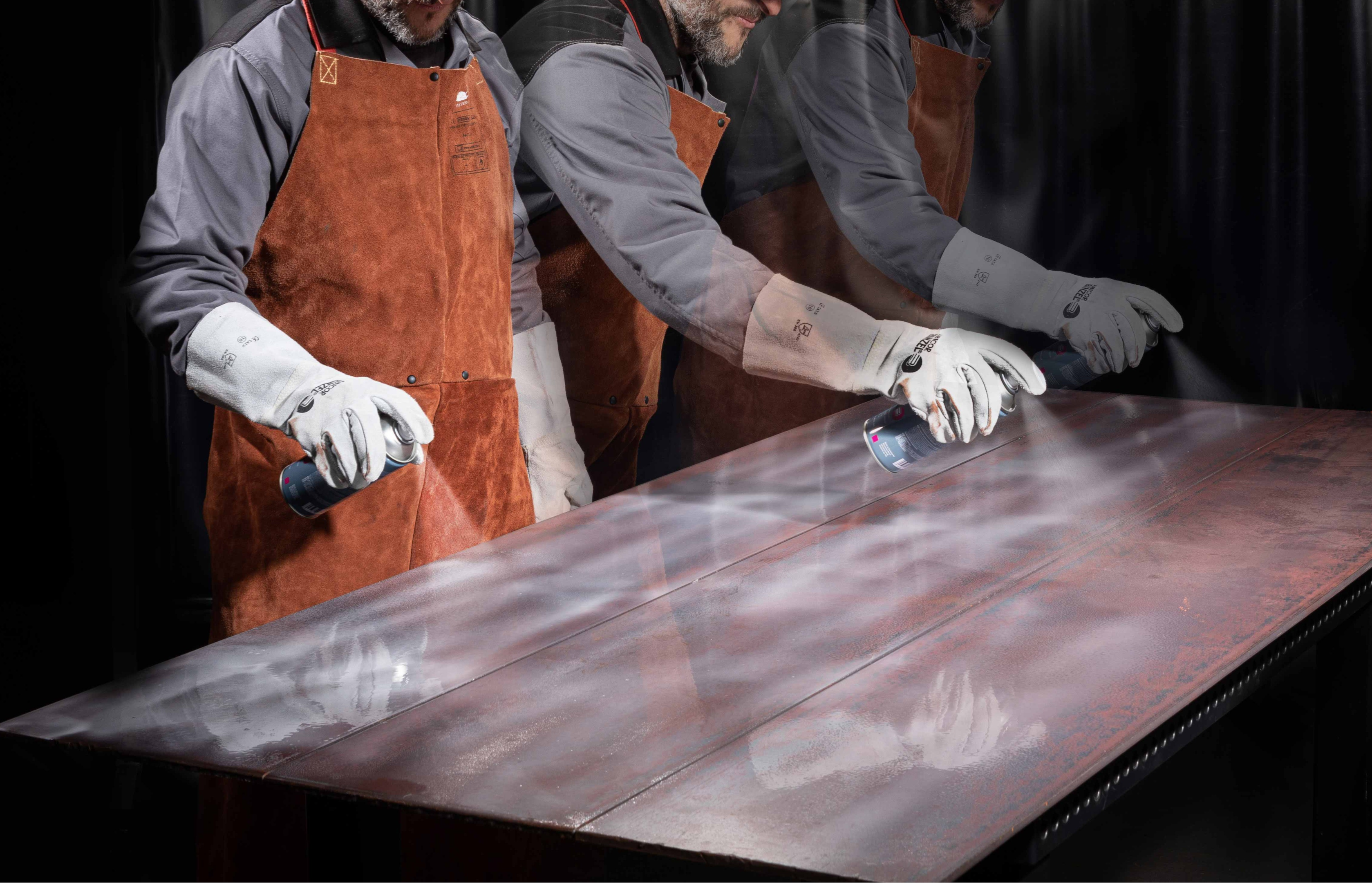
5. Utilization of Proper Shielding Gases
Shielding gases play a crucial role in preventing weld spatter during gas metal arc welding (GMAW). Choosing an appropriate shielding gas helps create a stable arc and protects against atmospheric contaminants that can cause splattering.
Using a higher percentage of CO2 can increase spatter in MIG welding. Argon-rich in the shielding gas mixture or pure argon often results in less spatter, such as a 90% Argon/10% CO2 blend in MIG welding, known for reducing spatter.
6. Optimization Techniques During the Welding Process
Implementing optimization techniques during the welding process can help minimize splatters.
Techniques like pulse welding can reduce spatter by modulating the welding current. Familiarize yourself with the capabilities of your welding machine and utilize these advanced modes when appropriate.
Maintaining proper travel speed, maintaining consistent stick-out length, and using the push technique (for MIG welding) are some effective ways to reduce spatter. Ensuring a proper fit-up and joint preparation can also help minimize spatter formation.
7. Ensure Stable Ground Connection
A proper and stable ground connection is essential. Use magnetic or clamp-style ground connectors directly on the workpiece, ensuring that the workpiece has a good electrical connection with the welding machine to prevent intermittent arcs, which can produce spatters.
By addressing these factors effectively, you’ll be able to reduce welding spatter significantly during your welding projects. So keep these tips in mind next time you’re firing up that welder!
How to Remove Existing Welding Spatter?
Tips for reducing spatter are listed above. But if the spatter has formed, in order to make the workpiece get a clean surface for the next step of finishing, we can use some methods to remove the existing welding spatter.
1. Mechanical Methods
To tackle existing welding spatter, mechanical methods like chipping can be effective. Utilize a chipping hammer for larger spatter particles and wire brushes for smaller ones. This method requires some elbow grease but can be quite satisfying when you see the spatter being scraped away.
2. Chemical Solutions
For stubborn spatters that are difficult to remove with mechanical methods alone, chemical solutions come in handy. There are various commercial products available specifically designed for removing welding spatter. These solutions contain chemicals that help dissolve and break down the splatters, making them easier to wipe away.
3. Grinding and Plasma Cutting
For larger spatter or for situations where a smooth finish is essential, an angle grinder with a flap disc or grinding wheel can be used to remove the spatter and smooth the surface.
In extreme cases, where large blobs of spatter interfere with the component’s function, a plasma cutter can be used to carefully cut away the unwanted material.
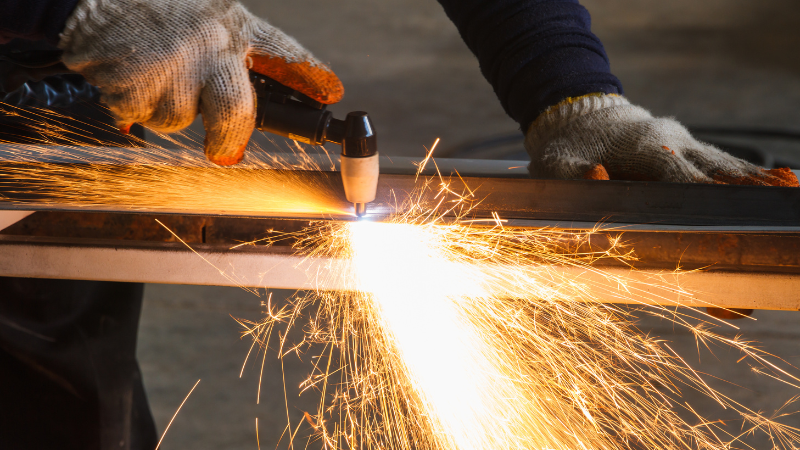
When using these tools, it’s important to exercise caution and wear appropriate protective gear such as gloves and safety glasses. Always follow the manufacturer’s instructions regarding usage and safety precautions.
FAQs
FAQ 1: How do I choose the right anti-spatter spray?
Select anti-spatter sprays designed for welding to ensure maximum protection. Evaluate their application ease, durability, and fit with your welding method. Customer reviews and peer suggestions can guide your choice.
FAQ 2: Can I reuse anti-spatter nozzles?
While it may be tempting to reuse anti-spatter nozzles to save costs, it is generally not recommended. Over time, these nozzles can become clogged or worn out, reducing their effectiveness in preventing spatter. It’s best practice to replace them regularly or clean them thoroughly after each use for optimal performance.
FAQ 3: How often should I inspect and clean my welding equipment?
As a general rule, it’s recommended to inspect and clean your equipment before each use. This includes checking for loose connections, cleaning the nozzle, removing any debris or spatter buildup, and replacing worn-out consumables. By maintaining your equipment diligently, you can minimize the risk of weld spatter and extend the lifespan of your welding tools.
Conclusion
Now you have enough measures to prevent excessive backweld spatter. By using these techniques correctly, you can minimize their impact. With attention to welding detail and continuous improvement techniques, you will master the art of spatter-free welding and achieve excellent results. Happy welding!
Elevate Your Welding with Baison Laser!
Looking for state-of-the-art welding solutions that minimize spatter and boost efficiency? At Baison Laser, we’re committed to providing you with top-tier welding equipment and expert advice. Dive into a spatter-free welding experience with us. Contact Baison Laser today and let’s elevate your welding game!