Unique cuts with sleek designs enable you to achieve artistic results. Working with thick plates often requires precise techniques. Bevel cutting is one of the fundamental techniques for producing exquisite products with smooth edges. It is employed in various industries for manufacturing numerous products.
In this blog post, you’ll explore creating a bevel cut. You’ll also learn about the benefits and various applications of the bevel cut. So, let’s get into it.
What is a Bevel Cut?
A bevel cut is an angled cut made at an angle along the edge of the material. The angle between a material’s edge is 90° to its surface. However, in bevel cut, the cutting angle is less than 90°, creating a slop on the material. The cutting angle between the edge and the material’s surface depends on your project’s specifications. Usually, this angle is 45°. However, bevel angles can be less or greater than 45°.
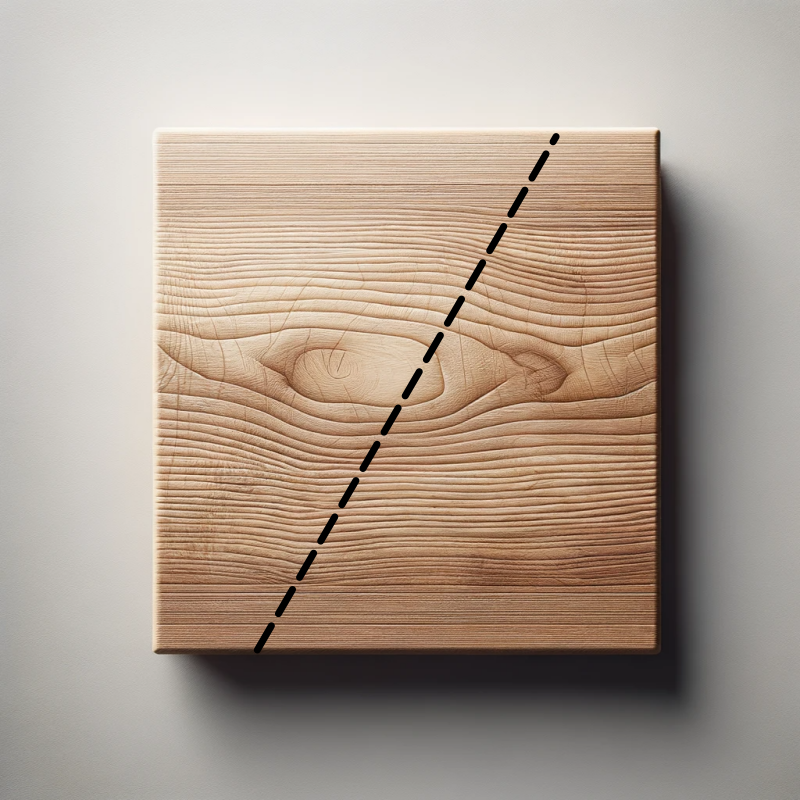
According to the Hunker, you can create bevel cuts through various tools, including a circular saw, table saw, miter saw, jigsaw, or router. You can make this slopped cut along the edge or entire side of the working plate.
Techniques for Bevel Cutting
Bevel cutting is a vast practice that employs various techniques. The following are some useful techniques to get a perfect bevel cut:
1. Manual Bevel Cutting
Manual bevel cutting employs hand-held tools, including grinders, hacksaws, or chisels. It is a basic technique, and you don’t need heavy machinery or software. The precision of this technique depends on your cutting skills.
You also need to be cautious, as any mistakes can lead to severe injuries and damage your workpiece. A significant drawback of manual cutting is that it is time-consuming and can only be used for small projects.
2. Portable Bevel Cutting
Portable cutting is the most widely used technique. It employs various portable cutting tools, like circular saws, miter saws, and table saws, to create bevel cut on metal or wood plate. This technique gives you more consistent and smooth cuts than manual cutting. However, you need to invest in quality tools and blades for the best results.
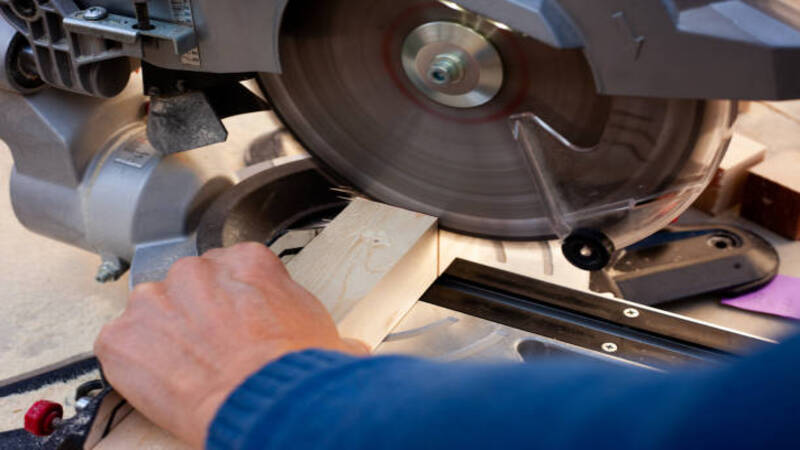
3. Automatic Bevel Cutting
Automated cutting uses computer-aided machinery. The machinery employs special software for optimal operation. This technique is used for large-scale industrial projects. It enables you to make multiple bevel cuts simultaneously, saving time and increasing efficiency.
Moreover, it is a safer technique as it eliminates and minimizes the risks of damage due to manual handling. However, automatic bevel requires significant investment in machinery and software.
4. Plasma Bevel Cutting
Plasma arc cutting is another popular technique for cutting metal plates. This technique is perfect for cutting hard materials and thick plates. Plasma-cutting employs ionized gas to cut metals.
This technique also employs automation to increase precision, making it ideal for industrial use. However, this method generates heat and fumes and requires proper ventilation for safety.
5. Laser Bevel Cutting
Laser cutting uses intense laser beams to cut metals, wood, and other materials. This technique produces precise, clean cuts for materials that are hard to cut with traditional techniques. As the laser beam falls onto the material, it melts and vaporizes, resulting in a smooth cut. Laser cutting also minimizes wastage as it focuses on a specific material area.
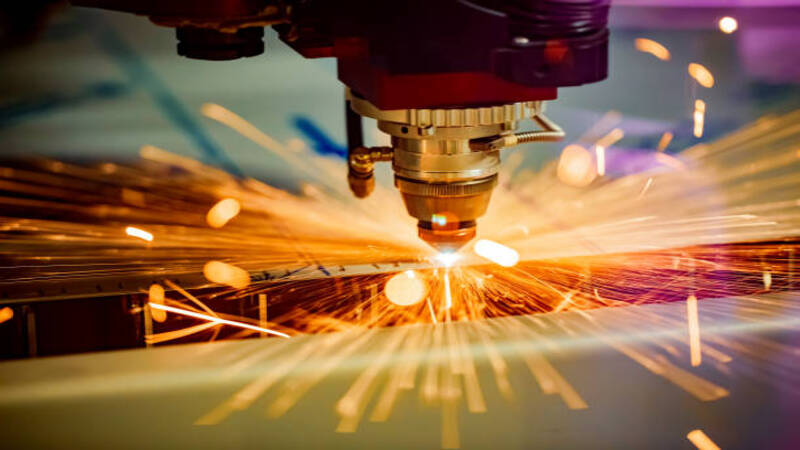
6. Water Jet Bevel Cutting
Water jet cutters employ high-pressure water streams to cut material. It is also a great way to cut thick plates and hard-to-cut materials. This technique is also safe as it utilizes regular water and does not produce heat or fumes.
7. Ultrasonic Bevel Cutting
The ultrasonic cutting technique utilizes high-frequency vibrations to create smooth bevel cuts. However, it is not suitable for thick materials. It best suits thin and delicate materials, like glass and ceramics. This technique is widely used on an industrial scale to produce small, intricate parts.
The Benefits of Bevel-Cut Thick Plates
Bevel cutting is a precise technique and offers several advantages. Here are some benefits of using bevel cutting for thick plates:
1. Better Structural Strength
Structural strength is a paramount factor for fabricating a perfect end product. Irregularly cutting a workpiece can reduce strength, leaving you with a weaker product. Bevel-cutting thick plates eliminate this issue by evenly distributing the tension on the material. It minimizes the stress in weak points and creates a stronger overall structure.
2. Improved Joint Stability
Creating strong and seamless joints is a fundamental requirement for many industries. The inclined surface increases the joint surface area. It offers better connection, resulting in enhanced adhesion and joint stability. Furthermore, the smoother cut edges make joining pieces easier without gaps.
3. Aesthetic Design
Bevel cuts are known for providing precise and clean edges. It adds a touch of elegance and enhances the overall aesthetic of the workpiece. According to SAWINERY, bevel cutting can effectively hide the seams of two different parts. You can use this technique to give your product a professional look.
4. Minimal Material Wastage
Various cutting techniques result in significant material wastage, especially when working with thick plates. Bevel cutting offers efficient utilization of material by cutting a slop edge. It removes less material from the sheet and increases the yield of your production process. It is a useful tactic if you are dealing with expensive materials.
07 Steps to Bevel Cut Thick Plate
Bevel cutting is an efficient way to create angled edges on thick plate materials. The following are the steps involved in bevel-cutting thick plate:
1. Inspection of Material Thickness
Before entering the process, you need to inspect the material’s thickness. Different bevel-cutting techniques are designed for working with specific material thicknesses. Therefore, it is important to know the thickness of your plate to select the appropriate technique.
Thick plates are often hard to cut and need strong cutting techniques for clean cuts. Laser, plasma, and oxy-fuel torch cutting are the most suitable techniques for creating bevel cuts on thick plates.
2. Machine Setup
Setting up your machine for cutting requires a high level of accuracy to ensure precise cuts. A machine might need a different setup for bevel and miter cuts. Adjust the settings, including cutting speed, angle, and gas flow rate, based on the plate thickness.
According to The Fabricator, the importance of the human element cannot be overstated. If you are using a laser-cutting technique, you have to choose the appropriate lens and gas pressure for the material thickness. Moreover, ensuring the machine’s safety features, such as proper ventilation and protective gear, is vital.
3. Determine The Cutting Length
Cutting length depends on the thickness of the material. As the bevel cut is inclined, its cut length is not the same as the thickness of the material. The length should be calculated by dividing the thickness of the material by the cosine of the cutting angle.
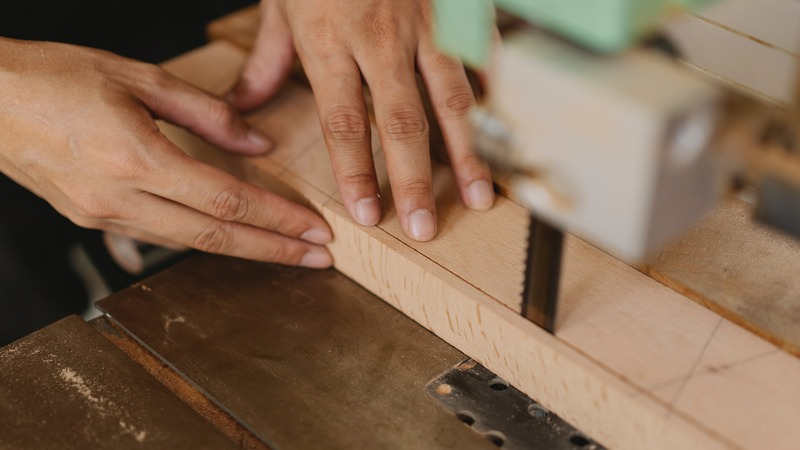
For instance, if you cut a 2-inch thick plate at a 45-degree angle, the cutting length would be approximately 2.83 inches. According to the Messer Cutting System, thick materials give you a longer cutting length.
4. Material Preparation
Material preparation ensures smooth cutting and accurate results. Cleaning the material surface is crucial as debris or birt can leave burning marks or unwanted cuts. To prevent this, use a solvent to remove any oil or grease that might be present on the plate’s surface.
In addition, clamp your workpiece on a sturdy and flat surface to avoid any movement during the cutting process. It prevents the material from warping and producing undesirable results.
5. Practice On a Small Piece
Before dealing with the workpiece, testing the machine setting on a small piece is better. Rushing into the process without practice can result in errors and waste of materials. This step is crucial for new operators who are unfamiliar with the machine. It allows them to adjust the settings and familiarize themselves with the cutting process. It also boosts your confidence, limiting nervousness and ensuring a smooth operation.
6. Create Bevel Cuts
After setting up the materials, it’s time to make the bevel cuts. Operate the machine and start the process by cutting an inclined line. Keep in mind the manufacturer’s instructions for a consistent cut and to prevent machine damage. Don’t push the material into the saw blade, laser beam, or cutting machine you are using. Wear safety equipment to prevent any accidents and injuries.
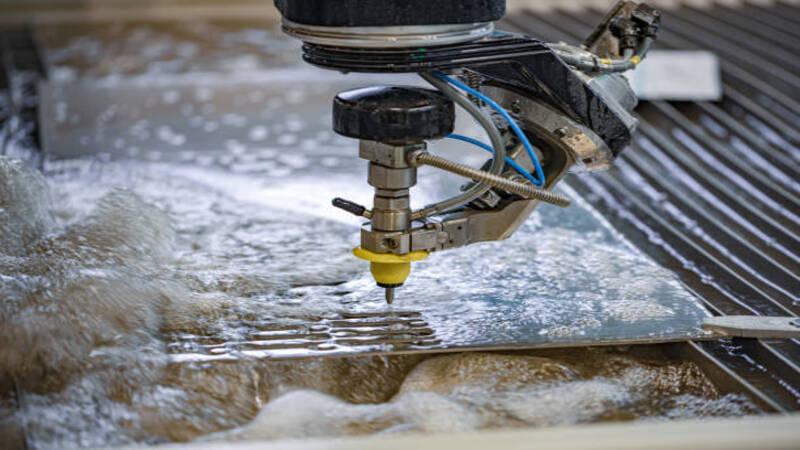
7. Post-Processing
Sometimes, bevel cuts are not smooth and require post-processing. If you observe irregular edges or rough-cut surfaces, refine it using sandpaper or a grinder. It gives a smooth finish to your workpiece. It ensures that your plates fit together smoothly, especially during welding.
The Application of Bevel-cut Thick Plate
Bevel-cut thick plates are employed for various purposes. Here are some applications of bevel-cut thick plates:
- Metal welding often requires smooth surfaces and perfect angles at the edges to create perfect welds. Bevel cuts offer you the right angles at the point of joining. According to the Timber 2U Direct, bevel cutting is a necessity for carpentry and joining materials.
- The woodworking industry also employs bevel cuts to create unique frames and furniture. You can create aesthetically pleasing products by using bevel cuts.
- The construction industry also relies on bevel cuts to fabricate strong and stable structural joints.
- It is also used for remodeling and renovation purposes. Cutting thick plates with bevel angles allows for precise fitting of materials, resulting in a seamless finish.
Why Choose Baison for Thick Plate Bevel Cutting?
Laser cutting is a precise technique that enables you to achieve refined cuts with thick plates. It is an efficient process and a preferred choice for many industries, including construction and metalworking. Laser cutting is also precise and does not lead to material deformation. However, not all laser-cutting service providers can handle thick plates precisely and accurately.
Baison Laser is one of the top laser-cutting machine providers. Our laser cutters are equipped with advanced technology that enables you to create seamless cuts. We offer a 12000W large format sheet metal cutting machine with graphite and fireproof brick design. It also comes with an all-round armored bed to prevent the platform from being damaged by laser cutting. One machine dual-use, and it can also be used for bevel cutting tubes.
You can customize its processing format according to your requirements. Its anti-collision safety grating ensures the safety of operators while cutting. This machine enables you to cut any bevel angle ranging from 0°. to 45°. You can achieve perfect Y, X, or V-shaped bevel cuts with our laser cutter.
Thick Plate Bevel Cutting Common Problems and Solutions
Though bevel cutting offers strong joints, creating them is a tricky task. Here are some challenges you may encounter while bevel-cutting thick plates and how you can solve them:
1. Inaccurate Bevel Angle
Bevel cutting often leads to inaccurate bevel angles. It might not seem to be a trouble. However, when you weld the plates, it leads to unstable joints. You have to spend extra time and effort to fix the issue. To avoid this, make sure to use advanced cutting techniques. Moreover, calibrate your equipment before cutting to ensure precise angles.
2. Tool Efficiency
The perfection of a bevel cut also depends on your tool. If your tool is not sharp enough, you may be left with uneven cuts. Check your tool to see if it is sharp enough to cut a thick plate. If you use automatic cutting machines, adjust all the settings before cutting.
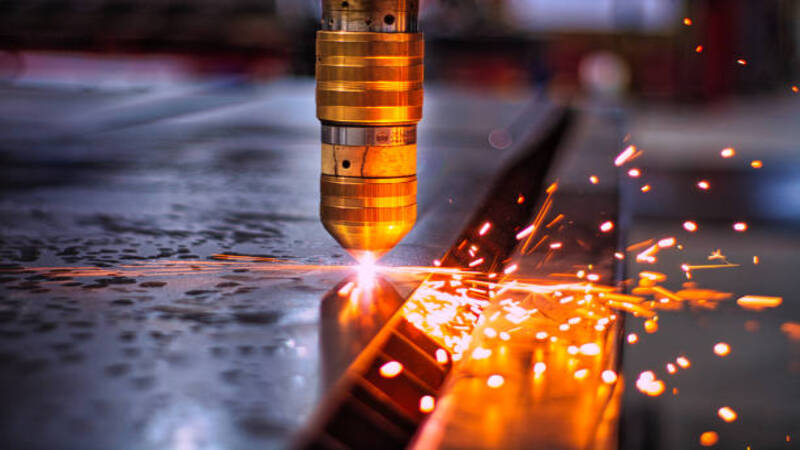
3. Distorted Edges
Bevel cutting might lead to distorted edges, especially when you cut thick plates. Your workpiece might get wrapped if you use plasma or laser cutting techniques. Refine the edges and use anti-warping techniques, such as preheating or cooling the metal, to avoid this issue.
FAQs
FAQ 1: Why is a thick plate beveled for welding?
A bevel cut offers a large surface area between joints. You can increase the welding area by cutting the pieces at an angle less than 90°. It results in a strong joint with better penetration.
FAQ 2: What is the difference between miter cut and bevel cut?
Both a bevel and miter cut are made at an angle less than 90°. However, the main difference between the two is the cutting site. A miter angle is made across the width of the plate, while a bevel cut is made along the edge.
FAQ 3: How do you make a perfect bevel cut?
You need a sharp cutting tool and a steady hand to make perfect bevel cuts. Prepare the surface of your material and make sure it is clamped securely. Tilt the blade of your cutting tool to the desired angle and carefully cut along the edge. If you are using an automatic cutting tool, adjust its settings.
FAQ 4: What are the different types of bevel cuts?
Bevel cuts are of five types, including A, K, V, X, and Y bevel cuts. These are named based on the shape of the beveled edge they create.
Conclusion
Bevel-cut is an amazing way to create seamless products with strong joints. Employing this type of cut on thick plates can help you fabricate stable joints. With various cutting techniques, you can create perfect bevel cuts for various products. Laser cutting is the best technique for bevel cuts. With an efficient laser cutter, you can achieve smooth bevel cuts.
Get a Laser Cutter for Perfect Bevel Cuts With Baison Laser!
Elevate your bevel-cutting experience with the best laser cutters. Baison Laser offers you high-quality laser tools for various purposes. Our products offer unique features that enable you to complete your projects efficiently. Contact us today for a laser cutter to make bevel cuts and intricate patterns.