In this post, we’ll discuss the key differences between these two technologies, identify which industry sectors can benefit the most from each method, and provide a comprehensive guide on choosing the best cutting solution for your business needs.
Stay with us as we delve into the world of cutting technologies and help you make an informed decision for your company.
What Are Laser Cutting Methods?
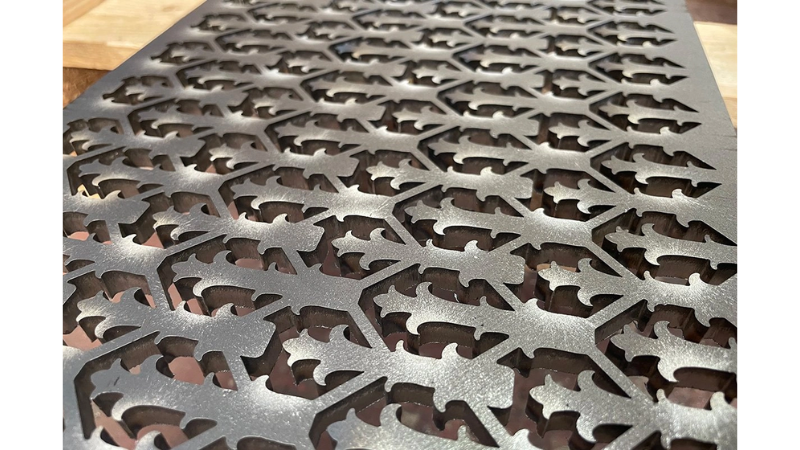
Laser cutting techniques are modern manufacturing processes that employ concentrated laser beams to accurately cut, engrave, or etch a wide range of materials. These techniques have gained popularity due to their capacity to generate clean, polished, and intricate cuts, particularly in complex patterns.
Two primary categories of laser cutting techniques exist CO2 laser cutting and fiber laser cutting. CO2 lasers are frequently employed to cut non-metal materials such as acrylic, wood, and plastic. In contrast, fiber lasers are designed to cut metals like stainless steel, aluminum, and brass.
Laser cutting techniques offer several advantages over conventional cutting methods. Some of the main benefits include:
- Exceptional precision and accuracy.
- Quicker cutting speeds.
- Minimal material waste.
- Enhanced design flexibility.
- Reduced maintenance and operational expenses.
The Role of Cutting Machines in the Metal Processing Industry
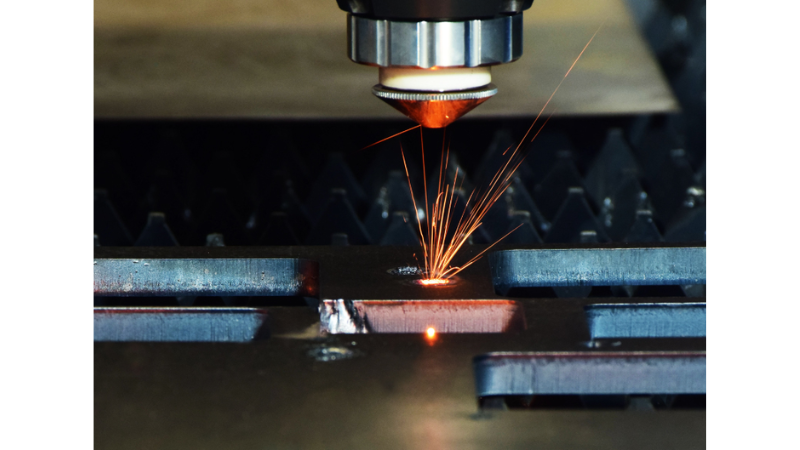
Cutting machines are critical in various stages of the metal processing industry, from raw material preparation to final product fabrication. They enable businesses to produce highly precise, intricate, and complex designs, which is especially important when working with metals that require exact dimensions and tight tolerances.
Reduced Material Waste
One primary advantage of cutting machines, such as fiber laser cutters, is their ability to reduce material waste. Traditional cutting methods can result in significant waste due to the cutting process itself and the need for secondary operations to clean up rough edges.
On the other hand, laser-cutting machines offer a cleaner and more precise cut, minimizing the need for further processing and reducing waste.
Greater Efficiency and Speed
Cutting machines provide greater efficiency by allowing for faster cutting speeds and shorter production times. This translates to increased output and a quicker turnaround for clients, which is essential in today’s fast-paced market.
A Competitive Advantage
By investing in advanced cutting machines, businesses in the metal processing industry can streamline their operations, save on material and labor costs, and ultimately deliver a higher-quality product to their clients. In a competitive market where every advantage counts, the role of cutting machines in the metal processing industry cannot be overstated.
Laser Cutting Process
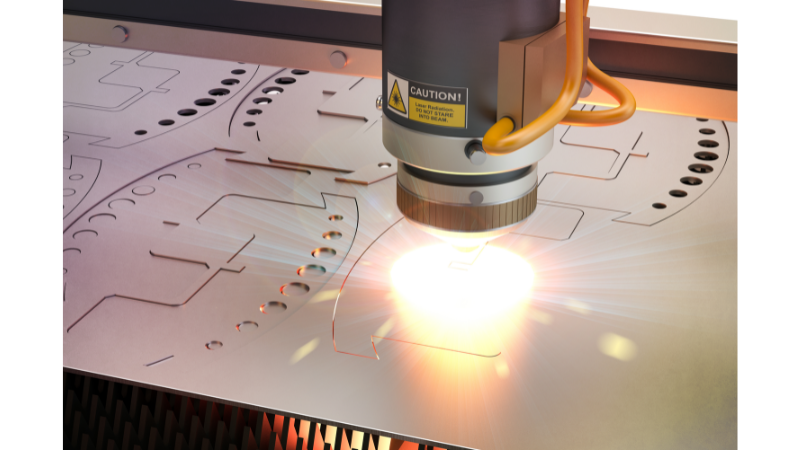
The laser cutting process is an innovative manufacturing technique known for its precision, minimized waste, and ability to create intricate designs.
How Laser Cutting Works
Laser cutting operates by:
- Directing a powerful, concentrated laser beam onto the material’s surface
- Heating the material with the laser beam’s energy causes it to melt or vaporize, resulting in a clean cut
- Using a computer numerical control (CNC) system to control the cutting process based on a digital design file
Role of the Laser Beam and Laser Cutting Head
The laser beam and cutting head play essential roles:
- The laser beam provides the energy needed to heat, melt, or vaporize the material
- The cutting head contains the focusing lens and other optical components, guiding and focusing the laser beam onto the material’s surface
- The cutting head is mounted on a CNC-controlled motion system, ensuring accurate movement and positioning during the cutting process
- The cutting head often features a nozzle that directs the best assist gas toward the laser cutting area, such as oxygen or nitrogen
Molten or Vaporized Metal Removal
Removing molten or vaporized metal is a critical aspect of the laser-cutting process:
- The assist gas helps expel molten or vaporized metal from the kerf, preventing it from solidifying and negatively affecting the cut’s quality
- The choice of assist gas depends on the type of material being cut and the desired edge quality
- Oxygen is commonly used for cutting mild steel, while nitrogen is often used for cutting stainless steel and aluminum to achieve a clean, oxide-free edge
Types of Laser Cutting Machines

Laser-cutting machines have become indispensable tools in various industries due to their precision, speed, and versatility. Several types of laser cutting machines are available, each designed for specific applications and materials.
Fiber Laser Cutting Machines
Fiber laser cutting machines utilize a fiber optic cable for laser beam generation and direction, making them ideal for cutting metals.
Their benefits include enhanced energy efficiency due to a higher electrical-to-laser energy conversion rate, faster cutting speeds compared to other technologies, low maintenance requirements, and versatility in handling various metals like stainless steel, aluminum, copper, and brass.
Metal Laser Cutting Machines
Metal laser cutting machines, including CO2 laser cutting machines, are designed for metal processing.
Key features of these machines are exceptional precision, resulting in high-quality products, flexibility in handling a wide range of metal materials and thicknesses, clean and polished cuts with minimal post-processing, and a non-contact cutting approach that minimizes tool wear and material distortion risks.
Laser Cutting vs. Traditional Cutting Methods

Various industries have used traditional cutting methods to shape and process materials for years. Though effective in many cases, these methods may lack the precision, efficiency, and versatility offered by modern laser cutting techniques. Some common traditional cutting methods include:
Laser Cutting vs. Plasma Cutting
This method uses a high-velocity stream of ionized gas, or plasma, to cut through electrically conductive materials. The plasma’s heat melts the material while the gas flow blows away the molten material, creating a cut.
Plasma cutting generates high levels of heat, which can cause distortion, warping, and melting of the material around the cuts. Plasma cutting is widely used for cutting metals, but it may not be suitable for thin materials or intricate designs due to the heat-affected zone and lower precision compared to laser cutting.
Laser Cutting vs. Mechanical Cutting
Mechanical cutting encompasses a variety of techniques that involve physically removing material using tools such as saws, shears, or drills. These methods can be effective for cutting a wide range of materials but often require more labor and time, resulting in higher production costs.
Additionally, mechanical cutting techniques may not achieve the same level of precision as laser cutting, especially for complex geometries.
Laser Cutting vs. Waterjet Cutting
Waterjet cutting uses a high-pressure stream of water, sometimes mixed with abrasive particles, to erode and cut through materials. This method can cut various materials, including metal, stone, and glass, without generating heat.
However, waterjet cutting can be slower and less precise than laser cutting, and the equipment and operating costs may be higher.
Laser Cutting vs. Die Cutting
Die cutting is a process that uses a custom-shaped cutting die to cut materials by applying pressure. This method is widely used for cutting various materials, including paper, plastic, and textiles.
While die cutting can be efficient for high-volume production runs of identical parts, it lacks the flexibility and precision of laser cutting for intricate or custom designs.
Fiber Laser Cutting Machines: Advanced Technology
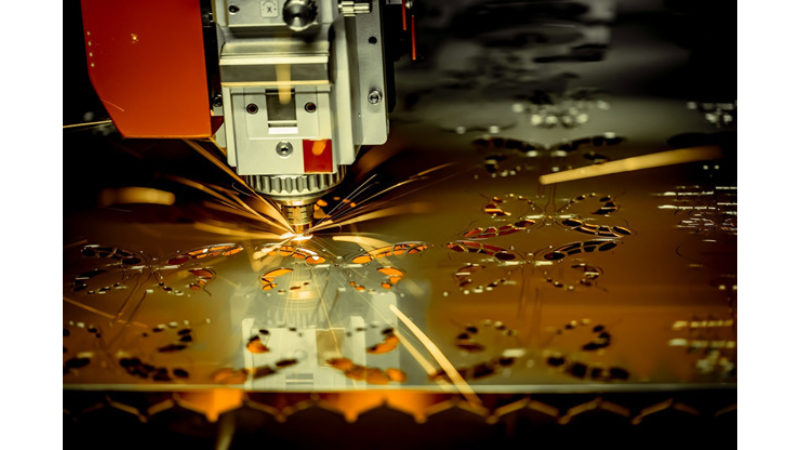
Fiber laser cutting machines represent the latest advancements in laser cutting technology, offering a range of benefits for various industries, particularly those working with metals.
Fiber Laser Generator and Laser Power
The fiber laser generator is a crucial component of fiber laser cutting machines, as it generates and delivers the laser beam via a fiber optic cable. This technology results in the following:
- High energy efficiency: Fiber lasers convert electrical energy into laser energy with high efficiency, lowering operating costs.
- Scalable laser power: Fiber lasers can be easily scaled to provide the desired cutting power, making them adaptable to various applications and materials.
Cutting Speed and Precision
Fiber laser cutting machines are known for their speed and precision, offering significant advantages over traditional cutting methods:
- Rapid cutting speeds: Fiber laser machines can cut metals faster, increasing productivity and reducing lead times.
- High precision: Fiber laser cutting provides high precision, tight tolerances, and intricate designs, ensuring high-quality end products.
Sheet Metal Processing
Fiber laser cutting machines excel in sheet metal processing, offering several benefits:
- Versatility: Fiber lasers can cut a wide range of metals, including stainless steel, aluminum, copper, and brass, making them suitable for numerous applications.
- Minimal waste: The high precision of fiber laser cutting machines results in reduced material waste, contributing to cost savings and eco-friendliness.
- Reduced post-processing: The clean and smooth cuts produced by fiber laser cutting machines often require minimal post-processing, further reducing production time and costs.
Advantages Of Fiber Laser Cutting Machines
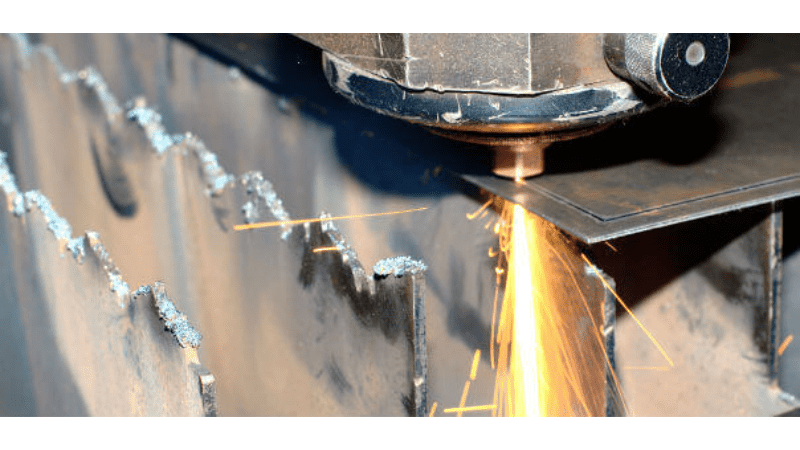
Fiber laser cutting machines have become increasingly popular due to their numerous benefits over traditional cutting methods. Some of the key advantages include:
Quality of Cutting Surface
Fiber laser cutting machines provide a high-quality cutting surface with smooth, clean edges that often require minimal post-processing. The precision and accuracy of the cuts result in an excellent finish, contributing to the overall quality of the final product.
Cutting Process Efficiency
Fiber laser cutting machines are known for their high efficiency in terms of cutting speed, energy consumption, and material usage. The fast cutting speeds can significantly reduce production time, while the high energy efficiency helps lower operating costs. Additionally, the precision of fiber laser cutting reduces material waste, further contributing to cost savings and sustainability.
Rapid Development of Laser Cutting Technology
Fiber laser cutting technology has seen rapid advancements in recent years, leading to continuous performance, reliability, and capabilities improvements. These advancements have resulted in more versatile machines that can cater to a broader range of applications and materials, making them a valuable asset in various industries.
Factors to Consider When Choosing a Cutting Method
Selecting the right cutting method for a specific project involves considering various factors to ensure optimal results. Some key factors include:
Type of Material Being Cut
The material being processed plays a significant role in determining the most suitable cutting method. Fiber laser cutting machines are particularly effective for metal cutting, while alternative methods like waterjet cutting might be more appropriate for materials such as glass or stone. Evaluating the material’s properties and understanding each cutting method’s limitations is crucial for making an informed decision.
Desired Cutting Speed and Precision
Different cutting methods provide varying levels of speed and precision. A fiber laser cutting machine could be the ideal choice if a project demands quick production with high precision and intricate designs. Conversely, traditional methods like mechanical cutting might be better suited for projects with simpler designs and lower precision requirements.
Applicability of a Fiber Laser Cutting Machine for Different Projects
Before opting for a fiber laser cutting machine, consider its suitability for your specific projects and applications. Factors to take into account include the machine’s cutting capabilities, power requirements, and compatibility with the materials you plan to process.
Ensure that the machine can accommodate your current projects while offering flexibility to adapt to future needs.
How to Make the Right Choice for Your Business?
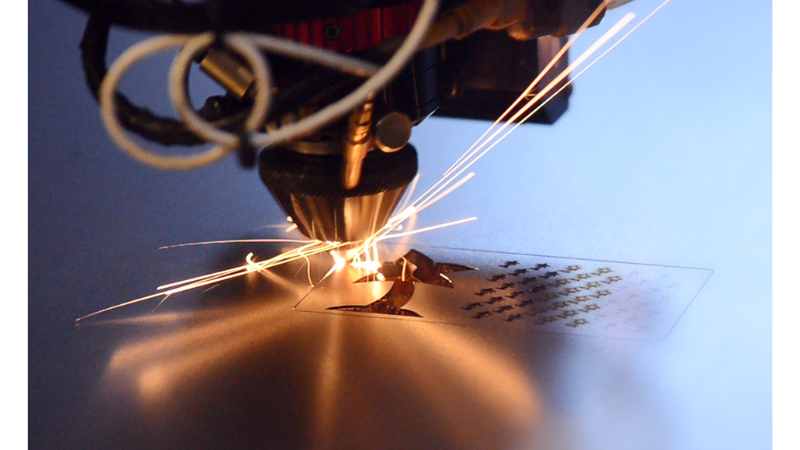
To make the right choice for your business, carefully assess your production needs, budget, and desired outcomes. Analyze the materials you frequently process, the level of precision and speed required, and the versatility needed for various projects.
Research and compare the capabilities, limitations, and costs of different cutting methods, such as fiber laser and traditional cutting machines.
Lastly, consider consulting with industry experts or machine manufacturers to ensure you select a cutting solution that aligns with your business goals, maximizes productivity, and provides a strong return on investment.
Conclusion
In conclusion, choosing the right cutting method, such as fiber laser cutting machines or traditional techniques, is crucial for your business’s success and productivity. Remember to consider factors like material type, cutting speed, precision, and machine applicability for various projects.
Explore our website for additional resources and guidance to understand further how these cutting solutions can benefit your business and optimize your production processes.
Unlock Your Business’s Full Potential with Baison Laser Cutting Solutions
Elevate your production capabilities and efficiency with cutting-edge technology from Baison Laser. Our fiber laser cutting machines and comprehensive solutions are tailored to meet your unique business requirements, ensuring unparalleled precision, speed, and reliability. Let Baison Laser help you stay ahead in today’s competitive market.