Metal fabrication workers, including those who work with tubing and pipes, and those who work with metal sheets, will find this information useful. After reading this blog post, you will better understand the nuances of tube and metal sheet cutting thickness, and you will be able to make more informed-cutting decisions.
What Are Tube and Metal Sheet Cutting?
Metal fabrication processes include tube cutting and sheet metal cutting. The tube-cutting process involves cylindrical or rectangular tubes to specific lengths or angles. On the other hand, a metal sheet cutter cuts large sheets of metal into the desired shape or size.
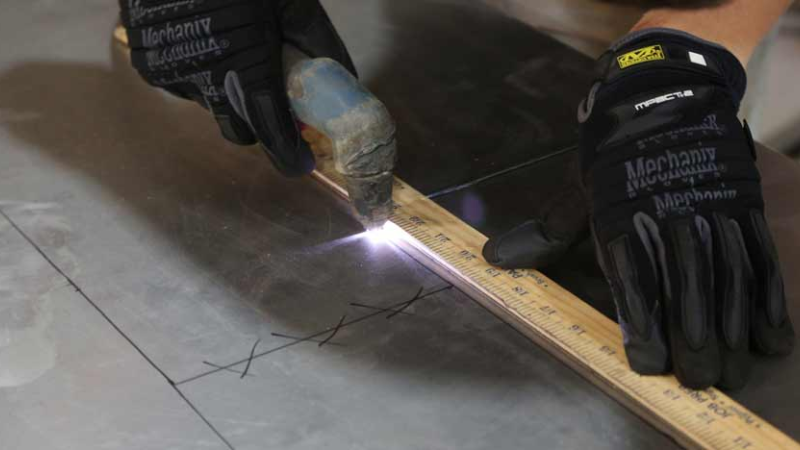
The final product must meet the specified specifications by using precision and accuracy during both cutting processes. A variety of tools and techniques can be used to cut tubes and sheet metal, including laser cutting, plasma cutting, and waterjet cutting.
Moreover, cutting techniques and tools will vary depending on the type of metal, the thickness of the material, and the level of precision required.
Why Is Cutting Thickness So Important?
Metal fabrication depends heavily on cutting thickness, impacting the final product’s quality and accuracy. It is important to note that depending on the thickness of the material to be cut, the amount of heat and pressure required will vary, as well as the tools and techniques used.
Furthermore, the thickness of a material determines the speed at which it can be cut, the contour size that can be cut, and the consistency of the entire process.
A lack of consideration of cutting thickness can result in rough edges, warping, and inaccuracies in the final product. Moreover, faulty cutting can result in problems during assembly or welding, which can lead to further problems.
Therefore, to ensure that the final product meets the required specifications and functions as intended, it is crucial to ensure that cutting thickness is controlled and understood.
Benefits of Precision Cutting
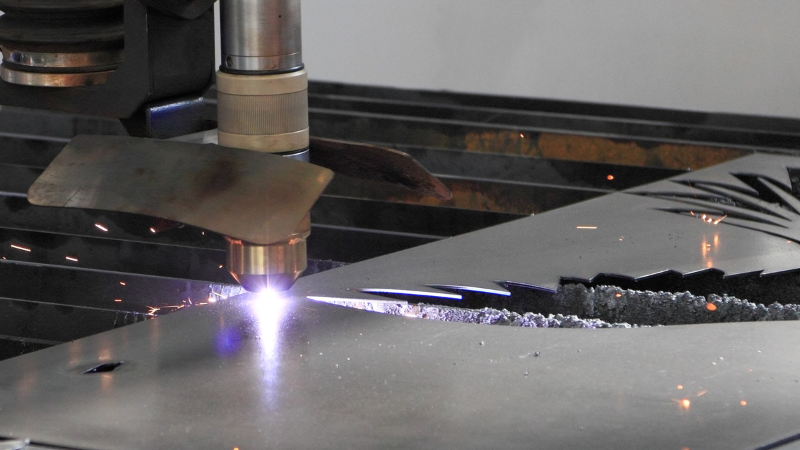
Precision cutting has several benefits, including:
1. Improved accuracy:
Precision cutting allows for greater accuracy in the size and shape of the final product, reducing the need for additional machining or processing.
2. Tighter tolerances:
It enables tighter tolerances to be achieved, which is important in industries where small differences can affect performance or safety.
3. Consistency:
Precision cutting allows for consistent results, which is important for large-scale production and in maintaining consistent quality and control standards.
4. Reduced waste:
It can reduce material waste, as it allows for better nesting of parts and more efficient use of raw materials.
5. Faster production times:
Precision cutting can increase production rates, allowing faster and more efficient cutting of materials.
Overall, precision cutting is an essential process in industries that rely on accurate and consistent results, and it can lead to cost savings, improved quality, and increased productivity.
Factors that Affect Tube Cutting Thickness
There are some factors that can affect tube cutting thickness. Here is some more information about these factors:
1. Tube diameter:
The diameter of the tube is a critical factor in determining the cutting thickness. As the diameter of the tube increases, the amount of material being cut also increases, which can impact the precision and accuracy of the cut.
Larger diameter tubes may require different cutting tools and techniques than smaller diameter tubes to achieve the desired thickness.
2. Wall thickness:
The wall thickness of the tube also plays a role in determining cutting thickness. Thicker walls require more heat and pressure to make a clean cut, and the cutting tool or technique used will depend on the thickness of the wall. The maximum cutting thickness is determined by the substance and laser type.
Choosing the right wall thickness for a specific application is essential to ensure that the tubing is cut efficiently with minimal damage or deformation while also ensuring optimal strength and corrosion resistance.
3. Material type:
The material type can significantly affect tube cutting thickness due to different material properties. For instance, materials with higher melting points or hardness may require more heat or pressure to cut, which can impact the cutting process.
Also, some materials may be more brittle or prone to warping than others, which can impact the precision and accuracy of the cut.
Different cutting tools and techniques may be required for different materials to achieve the desired cutting thickness. Therefore, understanding the properties of the material being cut is crucial to achieving the desired cutting-edge thickness.
Is the Thickness of the Cut Pipe the Same for the Same Material?
The thickness of the cut pipe may not necessarily be the same for the same material, as it can depend on various factors, such as the diameter and wall thickness of the pipe, as well as the cutting method and tools used.
Different metal pipe cutting methods and tools may produce different results in terms of the thickness and quality of the cut, even when used on the same material. Therefore, it is important to take into account all relevant factors when determining the cutting thickness for a specific material and application.
Types of Tube-Cutting Machines
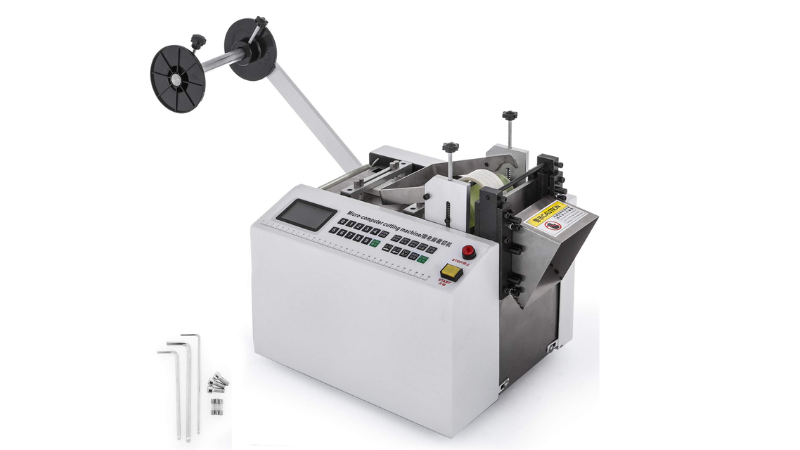
The following are some of the types of tube-cutting machines used in the industry:
1. Laser cutting:
Laser cutting is a popular tube-cutting method that uses a high-powered laser to melt and vaporize the material. The laser beam is guided by a computer-controlled system that follows a programmed path to cut the tube to the desired shape and size. Laser tube cutting is fast, precise, and produces clean edges, making it suitable for a wide range of tube materials and thicknesses.
2. Abrasive cutting:
Abrasive cutting is a tube-cutting method that uses a high-speed stream of abrasive particles, such as garnet or aluminum oxide, to cut through the material. The abrasive particles are mixed with water and then accelerated to high speed through a nozzle, which cuts the tube to the desired shape and size.
3. Saw cutting:
Saw cutting is a tube-cutting method that uses a circular saw blade to cut through the material. The saw blade can be a circular blade, a band saw blade or a reciprocating saw blade, depending on the material being cut and the desired cutting method.
Saw cutting is typically used for cutting materials in straight lines or angles, and is commonly used in construction, manufacturing, and fabrication industries. Saw cutting can produce accurate and clean cuts, but may not be suitable for all materials or cutting applications.
Other types of tube-cutting machines include plasma cutting, waterjet cutting, and rotary laser cutting machines. The choice of tube-cutting machine will depend on factors such as the material being cut, the desired precision and accuracy, and the production volume.
Differences Between Tube and Metal Sheet Cutting Thickness
The following are some of the main differences between tube and metal sheet cutting thickness:
1. Material properties:
One of the key differences between laser tube cutting and metal sheet cutting is the way material thickness is measured and treated.
When cutting metal sheets, the thickness is measured in gauge or millimeters, and the entire sheet is typically cut to a uniform thickness. The thickness of the sheet is a critical factor in determining the cutting method, as thinner sheets can be cut using less powerful methods such as waterjet cutting, while thicker sheets require more powerful methods such as laser cutting.

On the other hand, with tube cutting, the wall thickness is the key measurement. Tubes come in a range of diameters and wall thicknesses, which can vary along the length of the tube. The thickness of the tube walls is a critical factor in determining the cutting method, as thicker walls require more heat and pressure to cut through cleanly.
This means that different cutting tools and techniques may need to be used to achieve the desired thickness, depending on the wall thickness of the tube.
2. Equipment requirements:
The equipment needed for the metal laser cutting tubes and metal sheets can also differ, depending on the cutting method and the material properties. For example, saw cutting may require a different type of blade or saw than laser cutting, and the size and shape of the cutting equipment may vary for tubes and metal sheets.
3. Cutting method:
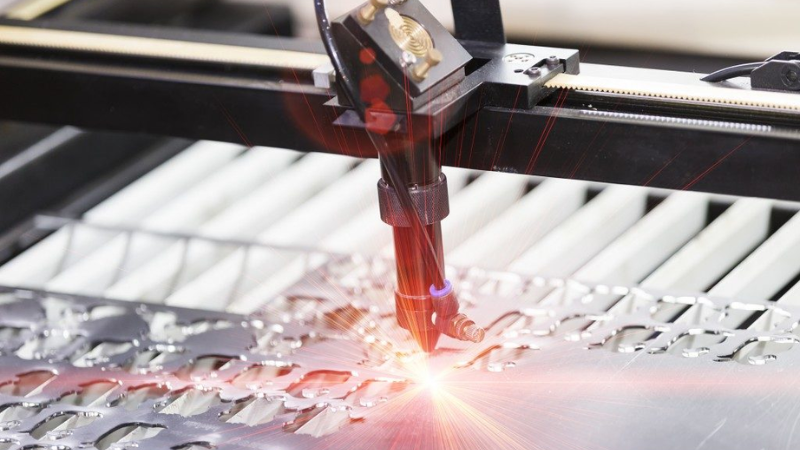
Different cutting methods may be used for tubes and metal sheets, which can also impact the cutting thickness. For example, the laser cutting process is commonly used for both tubes and metal sheets, but other methods such as shearing, saw cutting, or abrasive cutting may be used more frequently for tubes.
4. Tolerances and accuracy:
The tolerances and accuracy required for the cut may also differ between tubes and metal sheets. Tubes may require more precise cuts to ensure a tight fit or to prevent leaks, whereas metal sheets may have more lenient tolerances depending on their application.
Choosing the Right Cutting Method for Precision Cutting
The following are some important factors to consider when choosing a cutting method for precision cutting:
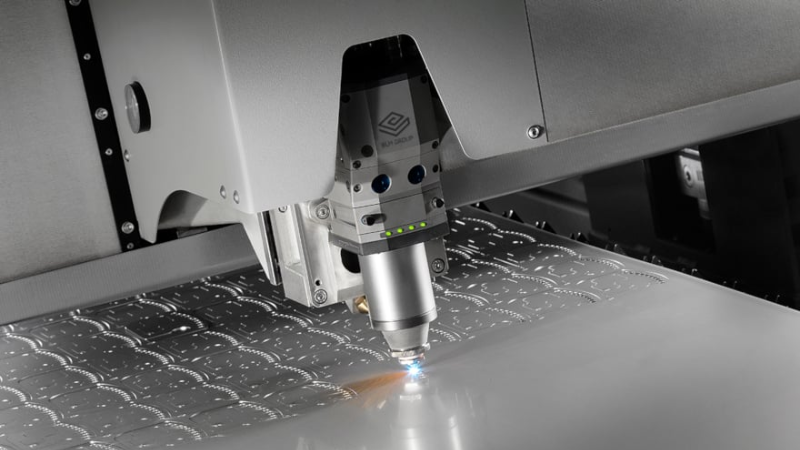
1. Factors to consider when choosing a cutting method:
When choosing a cutting method for precision cutting, it’s important to consider factors such as the material being cut, the thickness of the material, the required precision and accuracy, the production volume, and the desired edge quality. Each cutting method has its own advantages and disadvantages, so it’s important to weigh these factors when making a decision.
2. Matching the cutting method to the material and thickness:
Different cutting methods are better suited for different materials and thicknesses. For example, laser cutting is often used for thin materials or materials that require high precision, while saw cutting or abrasive cutting may be better suited for thicker material or harder materials.
3. Importance of selecting the right cutting service provider:
Choosing the right cutting service provider is also important for precision cutting. A reputable provider will have experience with a variety of cutting methods and materials and will be able to recommend the best method for your specific needs. They should also have the appropriate equipment and expertise to ensure that the cuts are made accurately and with high-quality edges.
Advancements In Precision Cutting
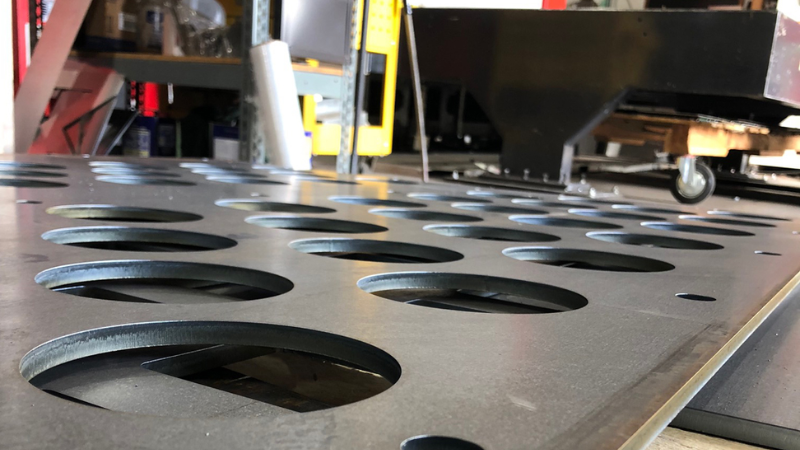
Advancements in precision laser cutting systems have been driven by the increasing demand for higher quality, faster turnaround times, and more efficient manufacturing processes. Here are some examples of recent advancements in precision laser-cutting technology:
1. Automation:
Advancements in automation technology have allowed for more efficient and precise cutting processes. Automated cutting machines can perform complex cuts with high accuracy and consistency, reducing the need for manual labor and improving productivity.
2. Laser technology:
Laser cutting has been used for precision cutting for decades, but recent advancements in fiber laser and technology have made it more efficient and accurate. Fiber laser cutters, for example, have higher power and can cut thicker materials with higher precision and faster speeds than previous laser technologies.
3. Waterjet cutting:
Waterjet cutting has become increasingly popular for precision cutting due to its ability to cut a wide range of materials and thicknesses with high accuracy and minimal heat distortion. Advancements in waterjet technology, such as faster water jet cutting top speeds and improved software control, have made it even more efficient and accurate.
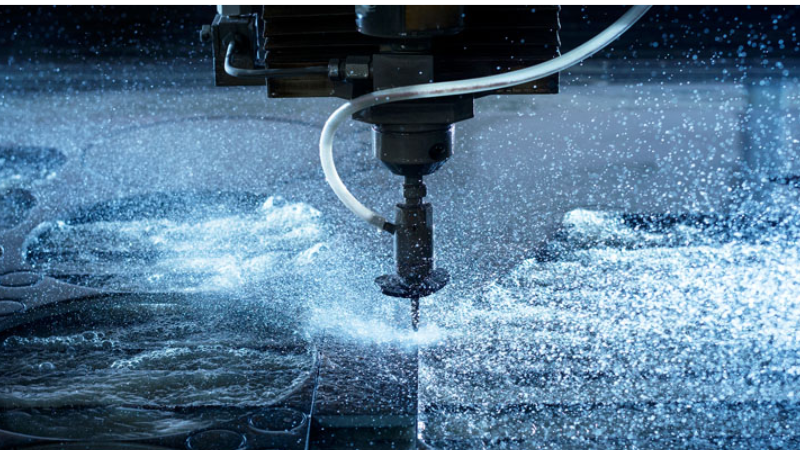
4. 3D printing:
While not technically a cutting method, 3D printing has become a popular alternative to traditional precision cutting methods for producing complex parts and components. 3D printing can produce parts with high accuracy and precision, and can also create parts that would be difficult or impossible to produce using traditional cutting methods.
Laser cutting and 3D printing are two different techniques with distinct uses. Overall, advancements in precision cutting have allowed for more efficient, accurate, and cost-effective manufacturing processes, helping companies to meet the increasing demand for high-quality products with faster turnaround times.
Conclusion
In conclusion, precision cutting is a critical component of many manufacturing processes, particularly in industries that require high-quality parts and components with tight tolerances. When it comes to tube and metal sheet cutting, there are key differences in thickness and cutting methods that must be considered to achieve the desired results.
Choosing the right cutting method for your specific needs is important and working with an experienced cutting service provider who can recommend the best approach for your particular material and thickness.
Advancements in precision cutting technology continue to drive innovation and efficiency in the manufacturing industry, and staying up to date with these developments can help companies stay competitive and meet the demands of their customers.
If you’re interested in learning more about precision cutting or other manufacturing processes, be sure to check out the other resources on our website. Thank you for reading, and we hope you found this post informative and helpful!
Ready to Take Your Precision Cutting to the Next Level?
Contact us for a consultation with our cutting experts and discover how we can help you improve your manufacturing processes and achieve better results with our state-of-the-art equipment and expertise. Don’t settle for anything less than the best regarding precision cutting – contact us today to learn more!