Welding is an essential skill in various industries, yet even the most experienced welders can encounter challenges when using handheld equipment. Understanding and addressing these common issues is crucial for maintaining efficiency and ensuring high-quality welds.
This blog post delves into ten prevalent handheld welding problems and offers practical solutions to overcome them. We aim to guide both novice and seasoned welders, ensuring smooth and productive welding experiences.
What Is a Handheld Welding?
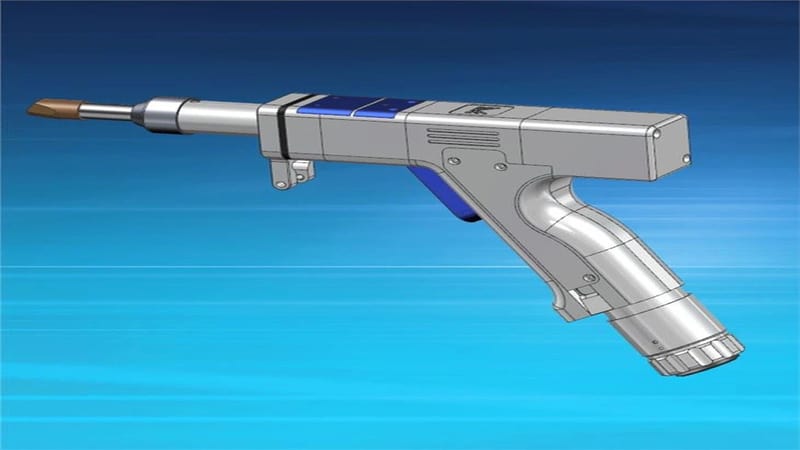
Handheld welding refers to a process where a welder manually operates welding equipment to join molten metal pieces. This technique demands skill and precision from the operator, who controls the welding device directly to create strong, durable bonds between materials.
Handheld welding is commonly employed across various industries and offers versatility in tackling various projects.
In the realm of handheld welding, operators have access to a variety of equipment types. These include gas metal arc, arc welding, mig welding, shielded metal arc welding, and laser welding devices. Each piece of equipment has its own benefits and challenges, catering to specific applications and materials.
The versatility of handheld welding allows professionals to work across multiple sectors, such as automotive, construction, and manufacturing. Learn about some common applications of handheld welding machines in various industries.
Gaining expertise in this skill not only enhances work quality but also expands opportunities for welders to tackle diverse projects and contribute to the growth of their industries.
Ready to Get Your Own Laser Machines?
Boost your operations with Baison Laser's advanced, customized technology!
How Do You Know If a Weld Is Bad?
Recognizing a bad weld is essential for ensuring safety and structural integrity.
Common indicators of a poor weld include porosity, which results in tiny holes or cavities due to trapped gas flow; undercutting, where the base metal melts away, creating a groove and weakening the joint; lack of fusion, where the weld metal inadequately bonds with the base metal, causing weak joints; and cracks, which can appear on the surface or within the weld.
These issues compromise the strength and durability of the welded joint, making it essential to address them promptly.
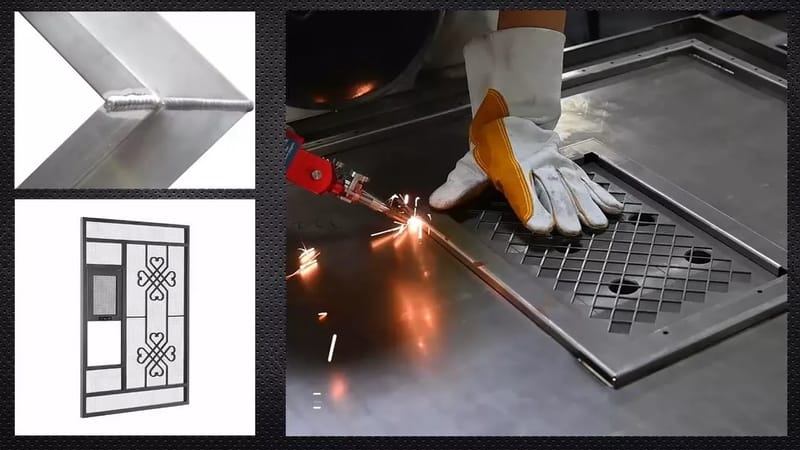
Common Handheld Welding Problems and Solutions
Below are listed some of the most common problems that welders face when using handheld welding machines:
1. Inconsistent Welding Bead
Inconsistent welding beads compromise joint strength and appearance. Common causes and solutions include:
- Improper electrode angle: Adjust the electrode angle, typically between 10-30 degrees, based on the welding technique.
- Uneven travel speed: Maintain a steady, consistent speed while moving the torch to create a uniform bead.
- Incorrect heat setting: Modify the heat settings according to material thickness and guidelines for optimal results.
2. Porosity in the Weld Bead
Porosity weakens welds and undermines their appearance. Common causes and solutions include:
- Contamination on the metal surface: Thoroughly clean metal surfaces to remove dirt, rust, or grease before welding.
- Incorrect shielding gas: Select the appropriate shielding gas for your specific welding process and material for the right arc length.
- Incorrect electrode: Choose the right electrode for the material and welding technique to minimize porosity. Also, the filler metal’s tensile strength must be accurate.
3. Undercutting
Undercutting weakens welds and negatively impacts joint integrity. Common causes and solutions include:
- Excessive current: Lower the welding current to prevent excessive melting of the base metal.
- Improper weaving technique: Refine your weaving technique to distribute the weld metal evenly across the joint.
- Improper electrode angle: Adjust the electrode angle according to the welding technique for optimal results.
4. Over-Welding
Overwelding leads to unnecessary material usage and increased costs. Common causes and solutions include:
- Excessive heat or current: Decrease the heat or current settings to avoid excessive weld metal deposition.
- Incorrect electrode angle: Adjust the electrode angle according to the welding technique to control the weld pool.
- Unsteady electrode: Hold the electrode steady throughout welding to maintain a consistent weld bead.
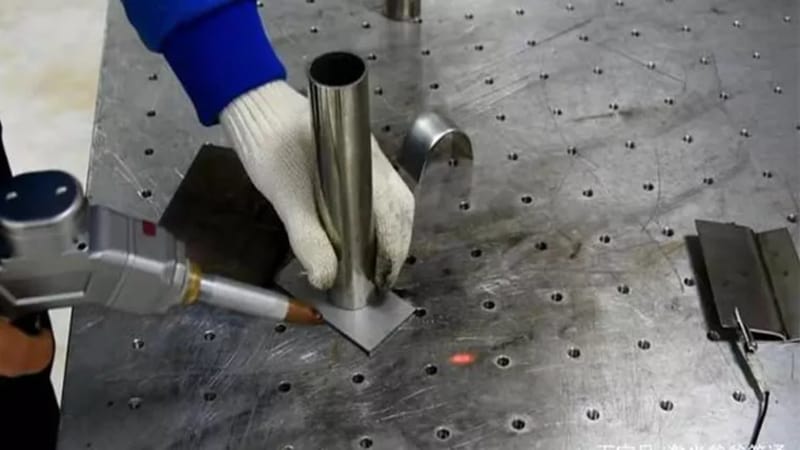
5. Burn-Through
Burn-through compromises weld integrity and can result in material damage. Common causes and solutions include:
- Excessive heat or current: Lower the heat or current settings to prevent base metal from burning or melting.
- Incorrect electrode angle: Adjust the electrode angle based on the welding technique to control the weld pool and avoid burn-through.
- Welding thin materials: Employ suitable techniques, such as pulse welding or using a backing strip, when working with thin materials. Also, make sure the filler metal deposited is suitable. You must also look for metal-grade matches.
6. Warping of Welded Materials
Warping can distort the shape of welded materials and affect their functionality. Common causes and solutions include:
- Uneven heat distribution: Adjust the welding process to ensure even heat distribution, reducing the risk of warping.
- Improper clamping or holding: Implement appropriate clamping or holding techniques to secure materials in place and minimize distortion during welding.
7. Incomplete Fusion
Incomplete fusion weakens welded joints and can lead to potential failure. Common causes and solutions include:
- Incorrect electrode-to-metal distance: Adjust the distance between the electrode and metal surface to achieve proper fusion.
- Excessive electrode angle: Reduce the electrode angle based on the welding technique to ensure adequate heat input and fusion.
- Incorrect electrode size: Select the appropriate electrode size for the material and welding process to achieve optimal fusion.
8. Distortion in the Weld
Distortion can negatively impact the appearance and functionality of welded components. Common causes and solutions include:
- Inadequate fixture: Utilize proper fixtures to hold materials in place and maintain their alignment during welding.
- Poor fit-up of metal surfaces: Ensure accurate fit-up of the metal surfaces to minimize distortion and improve joint quality.
- Excessive welding speed: Adjust the welding speed to maintain proper heat input and control material distortion and avoid concave weld beads.
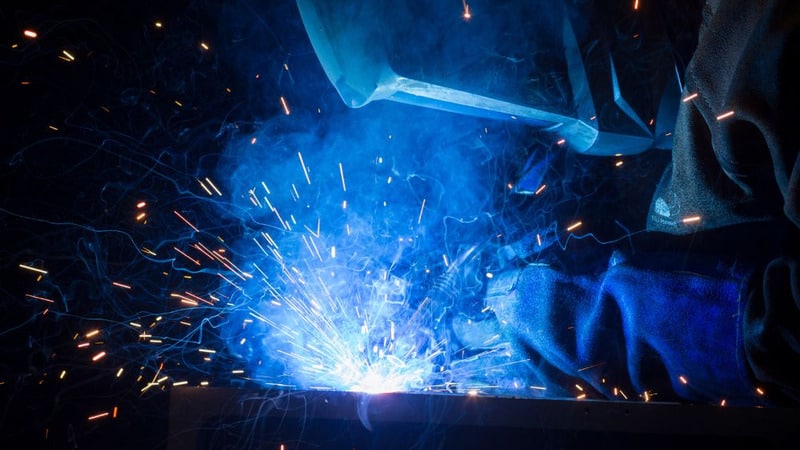
9. Lack of Penetration
Lack of penetration can weaken welded joints and compromise their structural integrity. Common causes and solutions include:
- Inadequate current or heat settings: Increase the current or heat settings to ensure sufficient penetration into the base metal.
- Incorrect electrode size: Select the appropriate electrode size for the material and welding process to achieve optimal penetration.
- Improper electrode distance: Adjust the distance between the electrode and the workpiece for consistent heat input and improved penetration.
10. Poor Weld Appearance
A visually unappealing weld can indicate underlying issues and affect the overall welding quality of the joint. Common causes and solutions include:
- Incorrect heat, current, or speed settings: Adjust these settings to achieve a smoother, more consistent weld appearance.
- Dirty or oxidized welding areas: Thoroughly clean the welding areas to remove dirt, grease, or oxidation before welding to enhance the weld’s appearance. This helps avoid concave weld beads.
- Improper electrode angle: Correct the electrode angle based on the welding technique to ensure a visually appealing and structurally sound weld. For instance, if you want to achieve a high crown weld bead.
Ready to Get Your Own Laser Machines?
Boost your operations with Baison Laser's advanced, customized technology!
Advantages of Handheld Welding Machines
The handheld laser welding machine presents numerous benefits, making it an appealing choice for businesses and individual welders. Some of the primary advantages include:
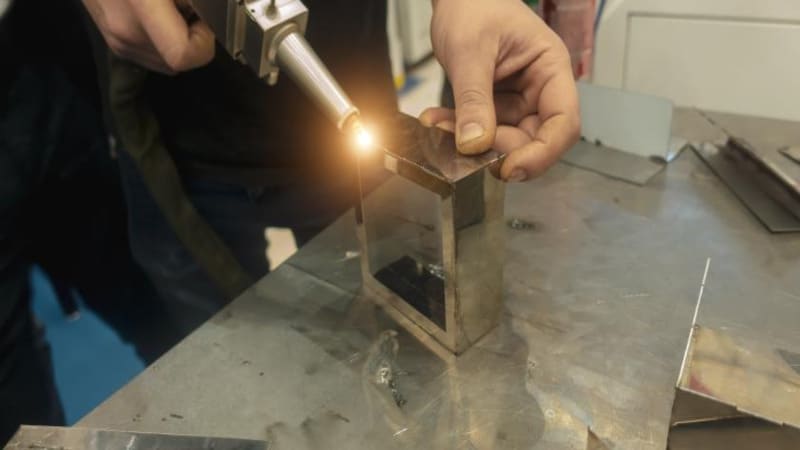
1. Increased productivity: The ability to swiftly transition between tasks and effortlessly access hard-to-reach areas with handheld welding machines can contribute to overall productivity gains.
2. Mobility: Handheld welding machines are compact and lightweight, allowing for easy transportation to different job sites and maneuverability in tight spaces.
3. Minimal setup time: Handheld machines generally require little setup, enabling welders to commence work more rapidly and efficiently.
4. User-friendliness: Handheld welding machines typically feature intuitive controls and functions, making them accessible to seasoned welders and novices alike.
5. Economical: These machines tend to be more affordable than their larger, stationary counterparts, providing a cost-effective option for businesses and individuals.
6. Accurate control: The handheld design offers welders enhanced control over the welding process, resulting in higher-quality and more consistent welds.
7. Flexibility: These devices can accommodate a wide variety of materials and welding techniques, enabling welders to undertake a diverse array of projects using a single machine.
8. Versatile applications: Thanks to their mobility and adaptability, handheld welding machines can be utilized in a range of environments, including outdoor job sites and restricted spaces.
Conclusion
In conclusion, understanding and addressing common handheld welding problems is crucial for ensuring high-quality and durable welded joints. By implementing the solutions discussed in this post, welders can overcome these challenges and improve their skills, regardless of their experience level.
Always remember that proper technique, attention to detail, and regular practice are key to mastering the art of welding.
We encourage you to explore our website for additional resources and insights that will help you further enhance your welding skills and knowledge. Keep honing your abilities, and you’ll become a laser welding expert in no time.
Uncover the Ideal Solution for Your Enterprise with Baison
Experience the difference Baison’s laser welding machines can do for your business by providing customized solutions tailored to your specific requirements. Our advanced welding technology and innovative engineering empower businesses to tackle challenges and ensure welding success.
By choosing Baison‘s welding equipment, you’ll benefit from our industry expertise and state-of-the-art features that enhance productivity and improve molten weld metal quality. Contact us today!