Laser welding is a process that uses a concentrated laser beam to fuse two pieces of metal. It has many advantages over other welding methods, such as arc welding. However, it also has some drawbacks. In this post, we’ll take a look at the pros and cons of laser welding.
What is Laser Welding?
Laser beam welding is a modern technique in which two pieces of the same or different metals are joined to form one part. The laser machine provides a precise heat source focused on the gap between metal pieces. The heat source from the laser beams connects the holes at high speed.
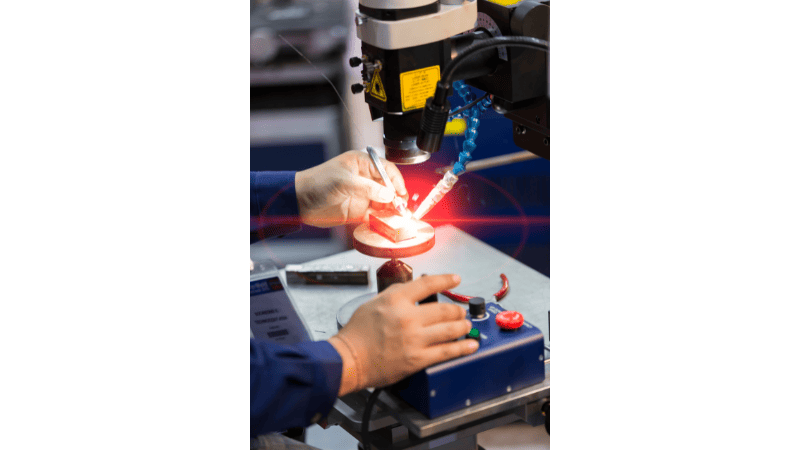
How Does Laser Welding Work?
Laser welding works in two modes: conduction and keyhole. The welding setup can switch between conduction and keyhole modes according to the energy density.
Let us explore how the conduction and keyhole modes work for different materials.
I. Conduction
The laser covers a large surface area in conduction mode, but the power density is maintained at the lower settings. The conduction mode works somewhat like TIG welding. Conduction limited welding works best for welds such as the front sides because you get aesthetic weld seam.
The energy beam’s focus area reduces as the power level goes up. For example, a 2 mm spot gets reduced to 0.6 mm in diameter to provide deep penetration. This intense, deeper penetration creates a keyhole phenomenon.
II. Keyhole Mode
You can use the keyhole modes to percolate two or more pieces of materials piled up on each other to make a strong weld. When the laser hits the top of the targeted surface, it penetrates through the stacked sheets. It vaporizes, filling the welds at an incredible speed.
Keyhole mode is an excellent choice for stacked materials and can replace spot welding. Unlike keyhole welding, you cannot automate spot welding. The automation feature for laser welding is a win over traditional welding methods.
Note: A laser welding setup has both keyhole and conduction modes. Power intensity and surface area adjustment help you switch between the modes.

Traditional versus Laser Welding – Which is Better?
If you are in the manufacturing industry, you must wonder if laser welding is the next big thing for your business. Why should you even consider traditional methods if laser welding has such accurate results? Selecting the best welding method depends on your usage and application. If you are curious to get answers to your queries about laser welding systems, stay with us and keep reading.
As far as traditional welding methods are concerned, we know about the three most common techniques.
- Metal-inert gas (MIG)
- Tungsten-inert gas (TIG)
- Spot welding (Resistance Spot Welding)
These three methods are the most widely used welding techniques, but laser technology is slowly replacing them.
A) Metal-inert Gas (MIG)
MIG welding is best for large and thick materials and uses a metal wire to complete the welding process. During the welding, the wire acts as both the electrode and the filler material. Additionally, the automation process for MIG welding is easier to design. Factors such as working speed, welding angle, and amperage can be preset to use the automated process.
MIG is fast when compared to TIG, resulting in lower production costs. Although the MIG produces welds at a faster rate and lower price, the welds are not precise and neat compared to TIG welding.
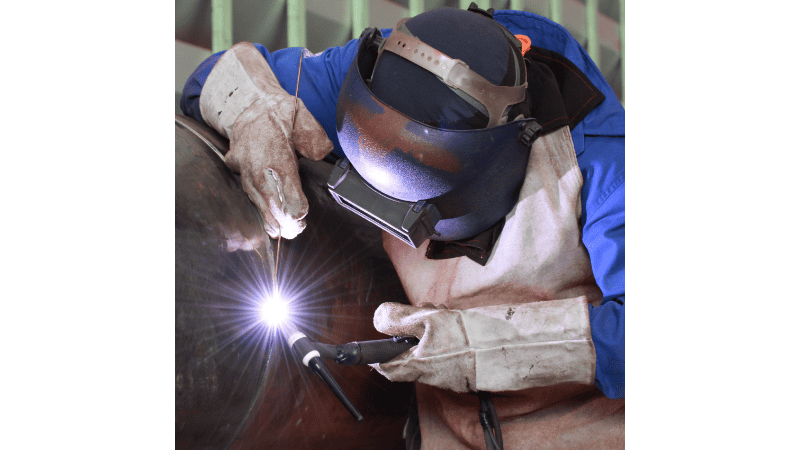
B) Tungsten-inert Gas (TIG)
TIG welding works best when dealing with a wide range of small and thin materials. In TIG welding, a Tungsten electrode heats the metal and welds it. However, the Tungsten electrode does not melt down during the welding process.
TIG welding is durable but expensive, resulting in high production costs and time consumption. Additionally, only skilled welders can perform TIG welding to get precise and seamless results. However, when done right, TIG welding produces precise and aesthetically pleasing results.
C) Spot Welding (Resistance Spot Welding)
Spot welding is one of the oldest methods for welding two or more metal sheets together without needing any filler material. A resistance welding process fuses metal sheets by applying pressure and heat from an electric current supplied to the targeted area.
In spot welding, pressure, and electric current are applied to produce heat by passing a current through resistive materials such as low-carbon steels. The targeted material’s meltdown and the constant pressure after switching off the current solidify the fused metals.
Advantages of Laser Welding Over Traditional Welding Methods
Laser welding is more precise and cost-effective in the long run than traditional welding methods. Hence, replacing traditional welding methods in modern manufacturing industries. Let us explore some major advantages of contemporary laser welding.
1. Less Thermal Impact
Laser welding works by focusing an intense heat source onto the subject material. The high heat fuses the two pieces of metal without impacting the non-focused areas. The heat from the laser beam doesn’t raise the temperature of the surrounding material. That’s why the subject material doesn’t lose its physical properties. Moreover, laser welding works in the same principle for dissimilar materials giving precise results.
Low heat input supplied to narrow regions results in minimal thermal damage and doesn’t affect the physical properties of the parent material adjacent to the weld. This characteristic of laser beam welding makes it more suitable than other welding techniques, such as electron beam welding.
2. Suitable for a Wide Range of Materials and Thicknesses
With the latest laser welding technology, you can weld materials such as stainless steel, aluminum, titanium and nickel alloys, thermoplastics, and other textures such as wood. The laser welding system allows you to weld materials ranging from 1-30 mm. However, the laser welding technique also impacts the final product.
3. Low Post Welding Cost
Laser welding eliminates the post-welding costs. As discussed above, a controlled heat input helps to join the two metals in a single workpiece that doesn’t require any post-processing, such as grinding. Due to no post-processing downtime, you save production time and cost. The whole laser process results in a low-cost but high-quality workpiece.
4. High-speed Process and Time-saving
Laser welding is known to produce excellent results at high welding speeds in comparison to gas welding. Thin materials such as small-diameter wires can also be welded at high rates. For instance, up to 60 meters of thin wires can be welded in a minute. The laser keyhole welding process is used for thicker sections, which complete a joint in a single attempt.
5. Deep and Narrow Welds Due to High Aspect Ratio
Laser welding joins materials at a high aspect ratio. The aspect ratio is the ratio of keyhole depth to its width in terms of surface area. Laser welding is suitable for custom configurations that MIG/TIG welding techniques fail to produce. Moreover, in keyhole laser welding, the aspect ratio can be huge, which helps easily weld the materials with greater depth.
6. Quality Assurance in Laser Beam Welding
Due to precise results, laser beam welding guarantees consistent quality. Laser welding is a non-contact process in which a precise laser beam does the job without making physical contact with the components.
Since laser beam welding is used mainly in the aerospace, automobile, and shipbuilding industries, these systems use a digital system to carry out a laser-guided manufacturing process. Advanced laser beam welding systems have an integrated measuring mechanism to monitor the manufactured products’ dimensions.
7. Automated process
Laser welding is an automated process using beams from Nd: YAG, disk lasers, optical fiber, etc. Moreover, you can use multi-axis robotic systems to develop a flexible manufacturing process. Automated welding setups have four main advantages.
- High-quality weld
- Increased output
- Less wastage
- Low variable labor costs
You don’t need to hire a group of skilled welders to operate the welding machinery, reducing your labor cost. Due to the benefits mentioned above, the automobile and shipping industry uses automated laser welding setups in their production.
8. No Electrode Required
In arc welding, electrodes are an essential part of the welding system. Welding electrodes are long wires connected to your welding machine. These wires/electrodes create an electric arc. The electrodes meltdown by heat and fuse the metals.
However, you do not need to use electrodes in the case of laser welding. The laser welding systems use intense heat to join the parent metals together without the help of an electrode. The weld doesn’t contain traces of melted electrodes, giving a superior finish to the final product.
9. Fusion of Metals with Dissimilar Physical Properties
The laser welding system is aligned and guided by optical instruments for accurate results. The laser beam can be set at the desired focal length for the product you’re working on. The focal length of the laser beam is adjustable to use different laser welding modes. While using arc welding systems, customization is impossible due to a lack of versatility and low-speed processing.

Disadvantages of Laser Welding Compared to Traditional Welding Methods
Laser welding is a superior method compared to other welding techniques. However, laser welding has a couple of minor disadvantages, which you would like to know before choosing the best laser welding setup for your business.
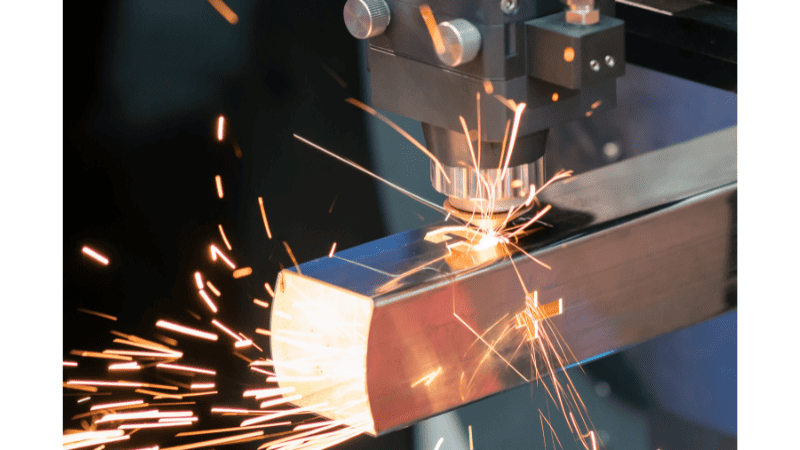
1. High Initial Cost
Laser welding seems like a tailor-made solution for large and medium-scale industries. However, an automated laser welding system can cost you a fortune initially. A regular laser welding setup can cost up to 3 times more than old-school welding setups. That’s why small businesses always feel reluctant to invest huge capital in one technology. However, if you are considering a long-term investment, laser welding can lower your per-unit cost.
2. Strict Supervision
Laser welding gives results with precision and accuracy. Still, this precision can also become a curse if the settings of the welding machine are not adjusted accurately. The automated laser welding setups have preset instructions, which must be applied carefully to avoid blunders in production.
Therefore, you need to make sure your production team actively follows the guidelines provided for high-quality manufacturing. You may have to hire expert technicians to monitor the welding process.
Now you know the advantages and disadvantages of laser welding over traditional welding methods. Now, what’s next? We will show you how you can find a reliable laser welding setup.
How to Choose the Right Laser Welding Machine for Your Business?
Suppose you are convinced that laser welding is the right option for your business. In that case, it is time for you to choose the suitable welding machine among the thousands of available variants. Before buying the laser welding setup, let us consider the four most crucial factors.
A) Type of Laser Welding Machines
Laser welding machines are of two categories: automatic 3D Laser and manual handheld welding machines. Robotic 3D setups are a match made in heaven if you need bulk production. Handheld laser welding machines are best suited for small and medium-scale business units. Moreover, you will need training and skills to use a handheld laser welding machine like a professional.
B) Power of Laser Welding Machine
Laser is the backbone of laser welding setup. Naturally, higher-power lasers will cost more than low-power lasers because high-power lasers require more efficient machinery and cooling systems.
For instance, if you need welds anywhere between 0.5 mm-3 mm, a 1000W laser will do the job efficiently. But for deeper welds, you will need a machine that ranges from 1500W to 6000W. Remember that high-power laser penetrates deeper than low-power lasers.
C) Laser Configuration
It would be best if you chose the laser configuration according to the needs of your business. For instance, laser welding for jewelry operates differently than galvanometer welding. Similarly, the laser machine prices vary according to their configuration and usage.
Laser welding setups are expensive, but they are beneficial for bulk manufacturing. If you want to reduce the overall manufacturing cost for your production unit, a laser welding system is your best bet. When buying the laser welding setup, you should always get help from customer service to choose the configuration.

Final Takeaway
In conclusion, laser welding presents a unique set of advantages and disadvantages that make it suitable for various applications.
While it offers unparalleled precision, speed, and versatility, it also requires careful consideration of its limitations, such as equipment cost and technical requirements. Ultimately, the decision to use laser welding should be based on a thorough evaluation of your specific needs and the nature of your projects.
Embrace the Future of Laser Welding with Baison Laser!
As you weigh the advantages and disadvantages of laser welding, remember that the right tools and expertise can significantly impact your results. Baison Laser offers state-of-the-art laser welding solutions tailored to your specific needs, ensuring precision, efficiency, and quality in every project. Reach out to Baison Laser today, and let’s revolutionize the way you weld!