Laser welding is a method of joining metals and even glass to metal by using heat produced by laser beams. It is used in the manufacturing and construction industries. The method is effective; however, it comes with radiation risk without preventive measures.
Therefore, laser welding is done by trained professionals in a strictly regulated environment to ensure minimum radiation risk. Along with several safety standards in place, safety strategies may also be added during laser welding. As a business owner, it’s essential to operate responsibly.
Understanding Radiation Risks in Laser Welding
During the fusion of metals using laser beams, radiation impacting skin and eyes is released. As you read, laser safety standards are needful, which can be classified as per the amount of optical emission and radiation. Overall, the hazard potential of the laser used determines the risk and required safety measures.
Radiation Risks to Operators
One of the most significant risks related to laser radiation is its ability to penetrate human skin and eyes. A high-power laser is capable of burning the human retina, damaging the cornea, burning skin, and even starting a fire on the premises.
Regular exposure to lasers may cause cataracts and retinal injury. Besides, the UV radiation wavelength 290-320 nm may cause cancer after chronic exposure.
For instance, infrared emitted from fiber lasers can be dangerous to the eyes and is undetectable even while causing active damage. Lack of safety gear, misdirected laser, and equipment failure may result in permanent damage.
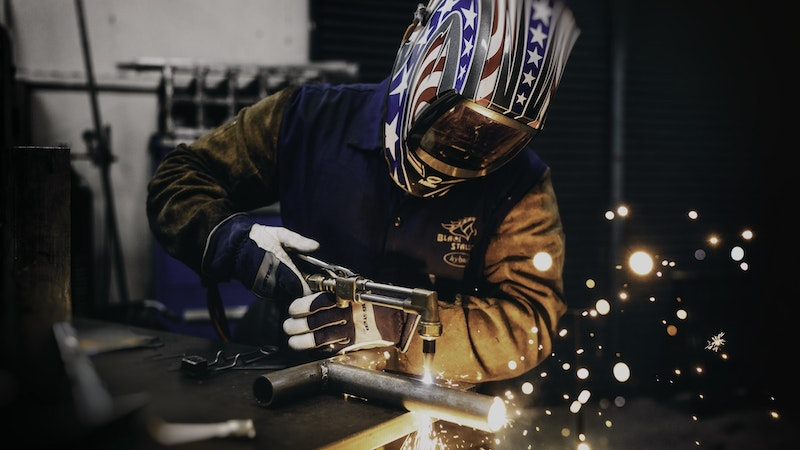
Chemical Exposure
Operators may need to use toxic dyes and excimer lasers for welding, posing a great risk to health and the environment. The high UV radiation from the excimer laser can cause vision problems.
Fumes and Dust Generated
Welding combines two solid substances by liquifying them, which generates fumes and dust in the air. There may be an inhalation risk associated with the process. If inhaled, these toxic fumes may lead to permanent skeletal and respiratory damage.
Carbon particle release is also linked with DNA damage.
Electrode welding can generate the maximum amount of dust penetrating the respiratory system. Therefore, the use of protective masks and suction machines is recommended.
Fire Risk
Flash lamps, high-voltage lasers, direct laser beams, and flammable materials like dyes are a recipe for disaster when security protocols aren’t followed. Any combustible material is susceptible to fire during laser welding.
As you read various risks related to laser welding, the implementation of regulations for use and safety design features will safeguard everyone present. Moreover, it aids in reducing laser accidents, injuries, and permanent damage.
What Types of Radiation Are Associated With Laser Welding?
Laser beam welding generates different types of traditions. We classify them into ionizing and non-ionizing radiation. Ionizing radiation is high-frequency electromagnetic radiation such as x and y rays. It has ample photon energy to alter the DNA chemical bond. In simple words, it can cause genetic changes in the cells via the ionization process.
On the other hand, non-ionizing radiation has a weak frequency to impact the cell molecules. However, laser welding uses amplified radiation to generate a reaction. It makes the radiation more potent and damaging. Laser welding is known to emit high levels of blue light and ultraviolet radiation.
The radiation wavelength from welding may range from 200-1400 nm. These may include infrared radiation, ultraviolet, and visible light. The short-wavelength optical from laser beams of 8kW power can emit 200 nm to 550 nm radiation.
UV radiation is further classified into:
- UV-A (315 to 400 nm – passes through the cornea and lens)
- UV-B (280 to 315 nm – absorbed in the cornea)
- UV-C (100 to 280 nm – absorbed in the cornea)
The UV and IR radiation that finds its way into the human eye retina causes damage.
Do You Have Any Questions?
Let Us Solve Your Problem
Now you know the basics of laser radiation. To safeguard workers from harmful laser welding radiation, it’s crucial to take protective measures.
1 – Use of Protective Equipment
The use of protective equipment is the simplest and most effective measure against radiation. Let’s take a closer look at protective equipment.
Safety Clothes
Wearing woven clothes, preferably from wool or cotton, effectively blocks UV radiation. High-necked or buttoned shirts, long sleeves, and full pants shield the skin. A sturdy fabric head covering, like a thick woolen hood, protects the scalp from UV exposure. Layer with fire-resistant aprons for added safety and ventilation. Always use a welder’s helmet and UV-protected safety goggles. Ensure the helmet is snug and opaque to fully shield the face.
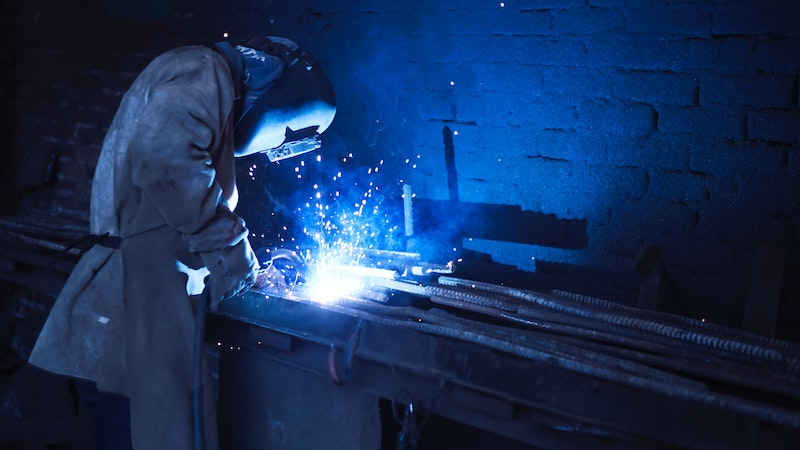
Fire Retardant Protection
For safety clothing to remain effective, adherence to care instructions is vital. Flame-retardant and heat-resistant garments enhance safety. Due to potential exposure to oils and fumes, these clothes might be at risk of ignition.
Regular cleaning to remove spills and contaminants is essential. Always follow cleaning guidelines to maintain the fabric’s protective quality. Avoid reflective attire; opt for dark-colored safety wear. Regularly inspect safety garments for damage or contamination, repairing or discarding as necessary.
Respiratory Protection
Breathing in toxic fumes and gasses can turn out to be lethal. In addition, lack of ventilation and oxygen may also pose a risk to the welder. Therefore, sufficient ventilation and regulated respirators must be in use at all times during the welding process.
Headgear and Hand Protection
We cannot emphasize enough on head and hand protection. The use of a strong helmet and face shield will protect and keep the worker alert and functioning. Materials such as polycarbonate plastic, filter lenses, and retainer lenses are recommended. Use dark filters to limit light exposure.
A face shield and helmet will not only protect the face from radiation but also prevent any flying dust and debris from hitting. Leather, latex, PVC, and wool can work great when working with electrical components. You may use cuffed gloves that are tight on the wrists, protecting the arms.
Eye Protection
Eye protection may be included in headgear while also paying extra attention to vision safety. The helmet’s protection can be enhanced with additional filters, as discussed above. It is ideal to add a cover lens along with a dark filter lens to avoid an eye injury.
Any scratched lens must be discarded and replaced to prevent damage to the cornea and retina of the eyes. The helmet should fit snugly with a tight gasket, preventing the entrance of harmful radiation.
2 – Enclosing the Laser Work Area
Keeping an enclosed space for laser welding prevents harmful radiation emissions and air pollution. One of the major key factors is to prevent outside elements from impacting the expensive laser welding equipment.
Since high temperatures and good ventilation are required for laser welding, having a safe and modular laser work area will keep everyone safe. The room or building must have a fully functioning HVAC system to ensure heat is dissipated adequately. In addition, glass used for windows should be safe for welding.
The area must have safety interlocks at entry and exit points. This will ensure the welding is carried safely behind closed doors and stopped when doors are open. The area should be equipped with safety warning lights to keep the area enclosed from any unapproved visitors. All the equipment and light switches must be within control workstations.
Most importantly, the laser workstations should be enclosed to create a radiation and heat barrier. This may include using fire retardant construction and protective materials.
3 – Beam Safeguarding
Laser beam welding involves scattering and diffusion of light. Due to this, several risk calculations go into the process of finding the effective welding laser beam. In addition, laser beam specular reflection is also considered during the calculations. This is where beam safeguarding comes in. The laser systems have to be designed in a controlled way to prevent direct reflection.
Laser beam safeguarding can be done via covered blinds and using shades as fire-retarding barriers. These barriers also ensure low maximum permissible exposure for laser wavelength. Another crucial thing is to test the laser beam welding for operation inaccuracy and fire hazard accidents. The laser users may test fire and keep a record of the laser beam.
4 – Routine Maintenance and Checks
The enclosed space, laser systems protocol, and safety gear remain at the risk of equipment or laser user failure. Therefore, routine maintenance and checks are essential, ensuring the safety gear is working and there are no faults in the equipment. Appropriate control measures can save everyone from exposure and accidents with the help of these maintenance checks.
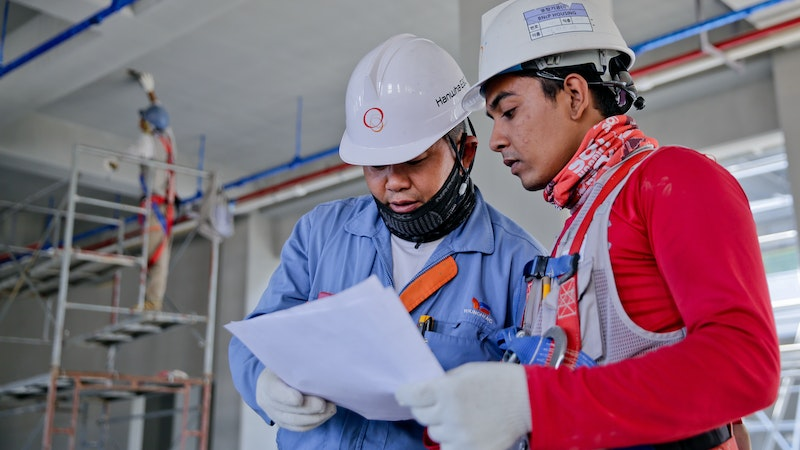
The routine maintenance check may include the following:
- Equipment inspection
- Checking window glass for cracks
- Inspecting head and eye gear filters for scratches and discoloration
- Checking tears and spills on laser users’ uniforms
- Cleaning the lenses with proper tools before operation
- Safety audits for laser welding procedures
- Auditing the number of staff and their skills
- Checking emergency supplies for worst-case scenarios
- Equipment inventory check
- Assessing and monitoring processes regularly for improvement
- Check all cables, insulation, and live parts of the wires
- Maintain no direct contact with live welding equipment and electrical parts
- Insulate yourself from live welding equipment and handle it with dry hands and body
5 – Restricted Access
A sensitive area, such as laser beam welding, cannot be accessible to all. Special attention is needed to ensure restricted access so that only trained professionals are present on the premises. Using RFID cards, face recognition, and access key cards can be helpful in preventing unauthorized access.
This will ensure the workers are safe and any unauthorized person is not susceptible to radiation exposure. Moreover, special signs and light signals must be present at all times in laser welding facilities. Dedicated security staff may also be appointed to double-check the facility entry points. Remote access solutions may be ideal, considering the worst-case scenarios during and after operations.
6 – Safety Interlock Systems
An on-duty laser safety officer and team can emphasize the safety interlock systems at the entrances and exits. Adding a safety interlock feature protects the workers as well as others present in the same building. The harmful emission radiation can be kept in check with an interlock system.
You may hire commercial interlock system providers for entrances of laser welding rooms and buildings. A custom fit will ensure the provision of radiation containment. Choose from a non-locking type interlock for easy access in case of accidents. Moreover, add override features that automatically take place as a fail-safe and are time-limited in case of radiation emission risk. Lastly, add an emission warning sign for a full-proof safety interlock system.
7 – Optimal Power Usage
Laser safety also depends on optimal power use. As we know, laser welding machines require high power for operation. It may range between 5,000 to 30,0000 watts. The power consumption may also depend on the size of the job and the metals used. With that said, laser welding equipment should be able to keep up with the power requirements within a budget.
Focus on the efficiency of the machine and use it with appropriate transformers to prevent any failure in the parts of the equipment. You may find a professional to help increase the wire feed speed in case there is less heat and arc with the current setup.
Additionally, compare single-phase and three-phase power supplies and choose the one that fits your needs. You may hire professionals to convert single-phase power to three-phase power as it’s more efficient and cost-effective.
8 – Continuous Monitoring
The work precautions, following of regulations, and documentation enforce safety during welding. Keeping a close check on repair and maintenance needs along with operational requirements will help the welding team continuously monitor everything.
There should be a log of operative regulations, live video records, reports, and policies to ensure the team and officials work on the same page. Being proactive in monitoring operations can prevent any cause of mishaps or delays in operations. It may also help in managing laser hazards with appropriate control measures. The new protocols may also be developed after a risk assessment and monitored as needed.
Do You Have Any Questions?
Let Us Solve Your Problem
Emerging Technologies for Reducing Radiation Exposure
Laser safety requirements have become a lot more than just wearing safety goggles to avoid direct exposure. With the use of emerging technologies, workers can rely on safety procedures that are backed by artificial intelligence and robotics. Furthermore, AI and robotics can add to the risk management perspective. It may assist in laser light calibration, minimizing laser exposure, and getting the best results.
If you are looking for welding robots, you can choose from automation robots. Some of the fine models include gantry, cylindrical, cartesian, and articulated for specific works. A variety of robots may also have a YAG laser for precision work. Robots and AI also prove to be significant ways to minimize the cost of labor and operations. This can also aid in work quality and improving efficiency.
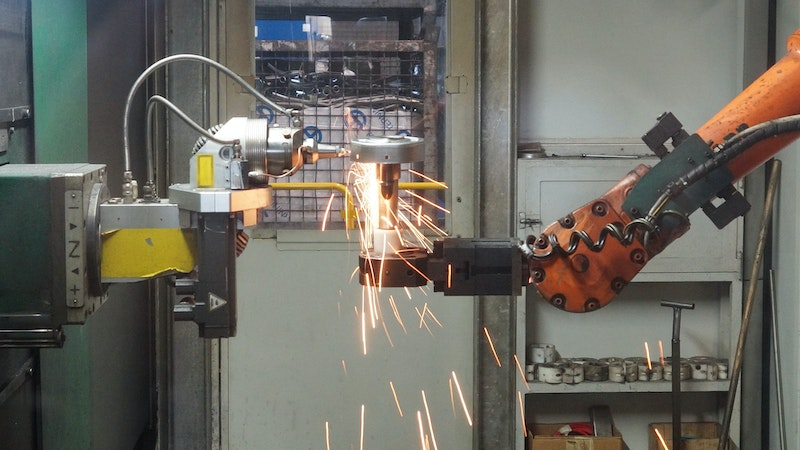
The AI may easily calculate the beam path, nominal ocular hazard area for the laser class, and maximum permissible exposure without any errors. Employing welding robots can minimize the distance from the radiation source and reduce the exposure. In addition, the robot will be precise and advanced for delicate work.
Removing human force from hazardous laser exposure and extreme heat also shows that you care about your employees. Robotics and AI, hand in hand with human resource, is the future of laser welding.
Augmented reality may also be used to improve efficiency and safety at work sites. It may be used for laser beam safeguarding, projecting welding jobs, and processing information in real time. In addition, better testing methods, such as ultrasonics, radiography, and magnetic particle inspections, may be included for quality checks.
Conclusion
Being proactive with laser welding risk reduction can go a long way. The right strategies will safeguard your workers and prevent any accidents on work sites. You can succeed in avoiding operational hiccups by following the above strategies. Look into upgrading the current operations and level up the safety measures. If your laser welding business requires an upgrade, hire professionals for tailor-made solutions.
Connect with Baison Laser for Your Custom Welding Business Needs!
Contact Baison Laser and Get a Free Application Evaluation for your laser system. We offer individualized solutions from an advanced laser catalog. You may specify your requirements and let our experts customize effective strategies. With our expert guidance and cutting-edge products, you can have a blend of modern tools with efficient design.