This blog is your roadmap to optimal cutting practices, unveiling eight strategies to elevate your cutting process. We’ll navigate through choosing the right cut-off wheel, managing feed speed, warding off overheating, and more.
Our goal? To ensure your large piece cutting operations are as smooth, precise, and cost-effective as possible. Let’s embark on this journey to perfecting your cutting process.
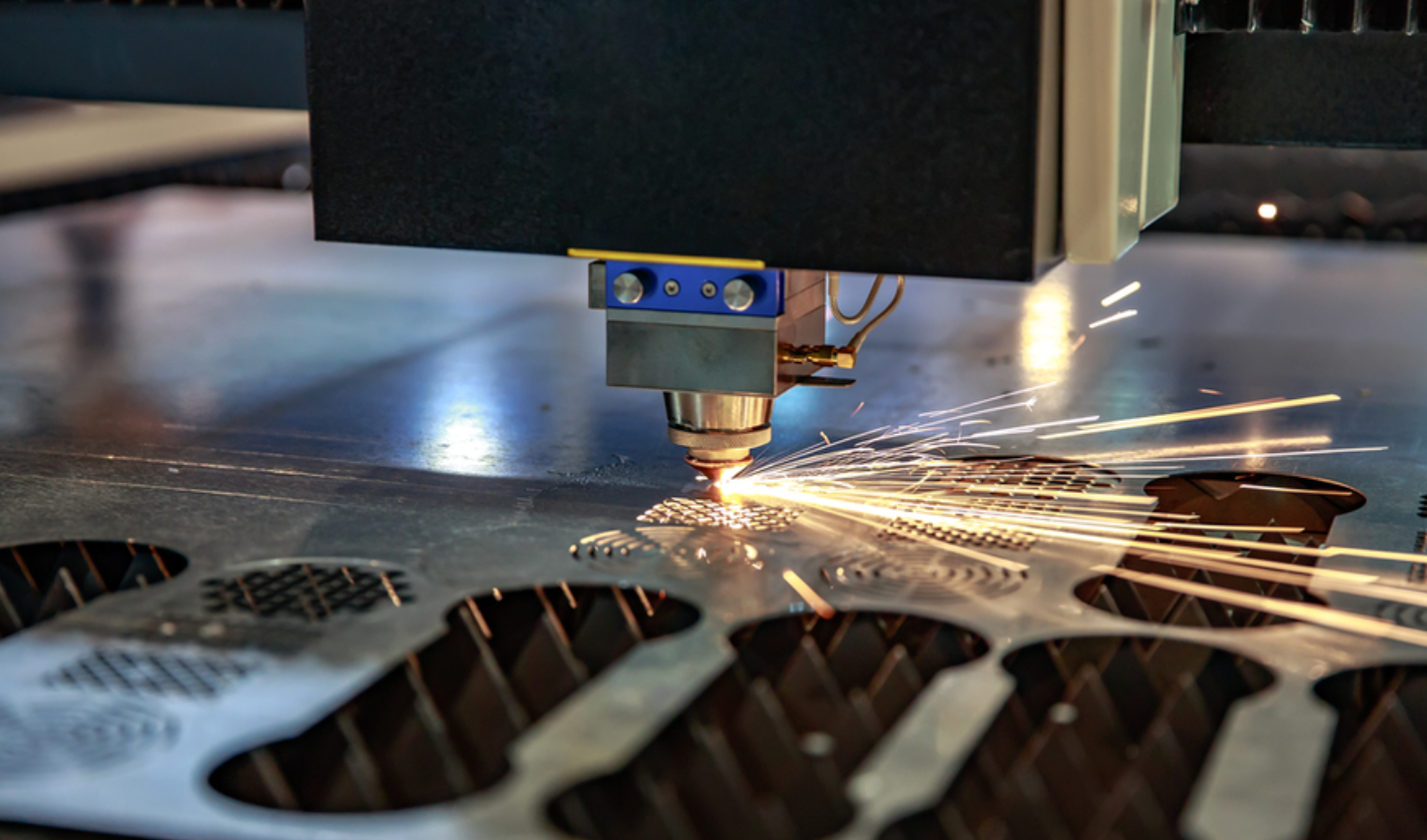
What Are the Difficulties When Cutting Large Pieces?
Handling large pieces for cutting in a manufacturing setting isn’t as straightforward as it might seem. In fact, it presents an intricate set of challenges that require meticulous strategies and fine-tuned execution. Let’s delve into these challenges and what they mean for your operations.
Maintaining Accuracy
Cutting large pieces to precise dimensions is a high-stakes endeavor. Using the wrong cut-off machine or wheel can result in inaccuracies, altering the integrity of the final product. Therefore, finding the right cut-off wheel that can withstand the rigors of large-piece cutting.
More so, the harder cut-off wheels might seem like a go-to choice for rigid materials, but it’s crucial to match the wheel’s hardness to the material’s properties to prevent compromising accuracy. Also, avoid using the conventional cut-off wheel as they aren’t the right cut-off wheel for today’s materials.
Reducing Waste
A single misstep with the cut-off wheel means wasted material. And it’s not just about squandered resources. Each wrong cut adds to the cleanup time, disposal efforts, and overall project costs. Selecting the premium cut-off wheel suited for your specific task can significantly reduce waste, saving both materials and time.
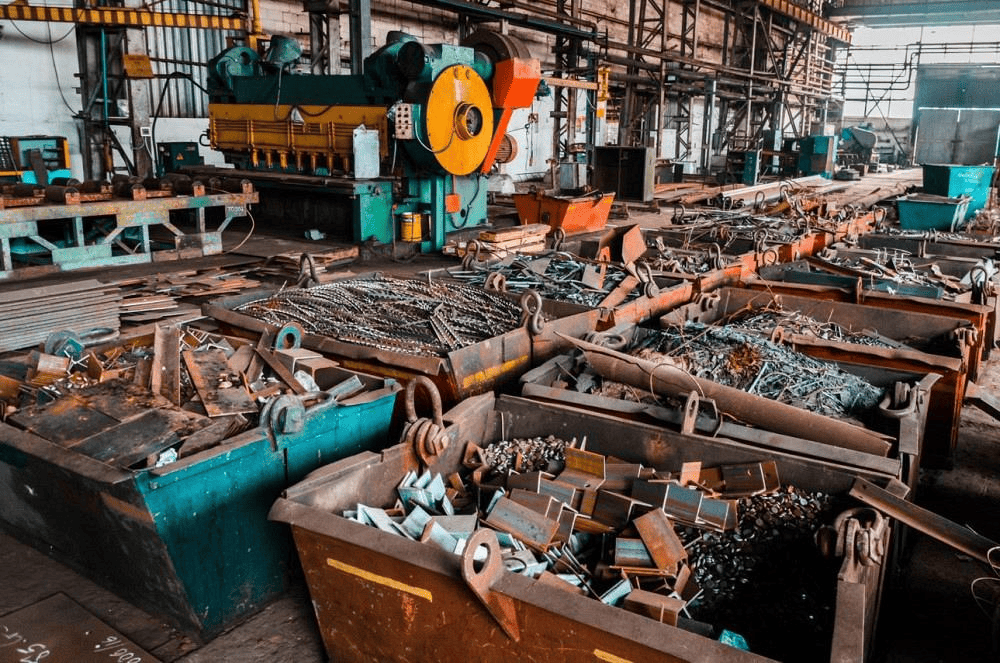
Improved Efficiency
The cut-off wheel’s performance directly influences the cutting operation’s efficiency. A wheel that wears quickly or doesn’t provide a clean cut will slow down the entire process. Conventional cut-off wheels might be cost-effective initially but can lead to lower overall efficiency. Conversely, a premium cut-off wheel can improve the cutting process’s speed and effectiveness, directly impacting your project’s timelines and productivity.
Keeping the Equipment Running
Cut-off wheel wear and tear is a typical part of the cutting process, but excessive wear leads to frequent pauses for maintenance and replacements. This downtime can disrupt the production workflow and lead to delayed deliveries. To prevent this, regular inspections and timely replacements of the cut-off wheel can ensure your equipment keeps running smoothly.
Safety
Large-piece cutting involves inherent risks. There’s always the potential for cut-off wheel deflection or even breakage, which poses significant safety hazards. Therefore, the use of safety equipment and adherence to operational guidelines is crucial to prevent accidents and cut-off wheel wears.
Cost
The economic aspect of large-piece cutting cannot be overstated. Using the wrong cut-off machine or the incorrect cut-off wheel can spike up operational costs. The trick is to balance price and quality—ensuring optimal wheel economy while maintaining cutting standards. In essence, investing in the right equipment upfront can lead to significant savings down the line.
Common Cutting Machines for Cutting Large Pieces
Different businesses employ a range of cutting machines to transform large workpieces into their desired shapes and sizes, catering to their unique manufacturing requirements. From woodworking industries using circular saws to aerospace manufacturers employing laser cutters, the choice of machinery plays a pivotal role in the process. Let’s take a closer look at some of these cutting machines and their different aspects, including accuracy, efficiency, cost, and suitability for different factory sizes.

- Circular Saws: Circular saws, including miter saws and table saws, are commonly used for cutting large pieces of wood, metal, and other materials. They are efficient and provide accurate cuts with good precision.
- plasma cutter: A high-power cutting machine that uses a stream of superheated gas (plasma) to cut through a wide variety of materials, including metal, stone, and wood.
- Waterjets Cutter: Waterjets use high-pressure water jets to cut materials, including metal, glass, and stone. They are high-precision machines used for cutting metal and other materials and can handle materials up to 3 inches thick.
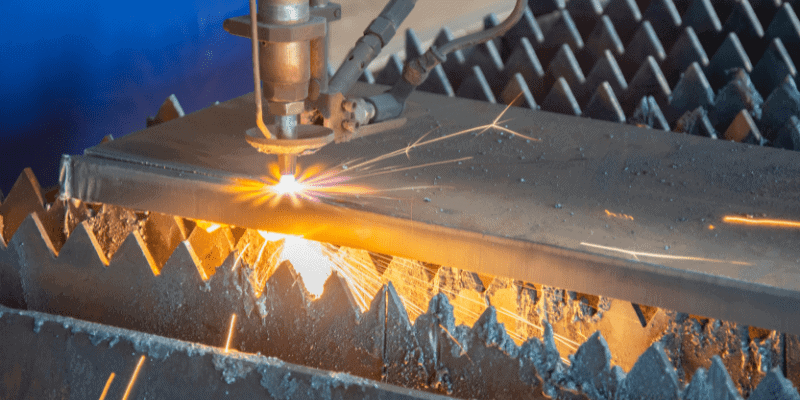
- Laser Cutting Machines: Laser cutting machines use high-powered lasers to cut materials with great precision. They are commonly used to cut acrylic, plywood, and other materials and are especially useful for intricate designs.
- Wire EDM: A type of machine tool that uses a thin electrode wire to create extremely accurate and complex shapes from a variety of materials, including metals, plastics, and composites. This electrical current causes the wire and the material to be separated, creating a cut in the material with extreme precision and accuracy.
Various factors should be considered when choosing the right cut-off machine for large-piece cutting. You need to balance accuracy with efficiency, cost implications with factory size compatibility, and, most importantly, the specific needs of your manufacturing process. Having a comprehensive understanding of these standard cutting machines will guide you toward the most suitable choice, optimizing your production process.
8 Ways to Improve Your Process When Cutting Large Pieces
As a business, you should always look for ways to improve your cutting process. This should apply to both small and large pieces. However, for this article, we have come up with eight practical ways to help you achieve better cutting results when dealing with large pieces.
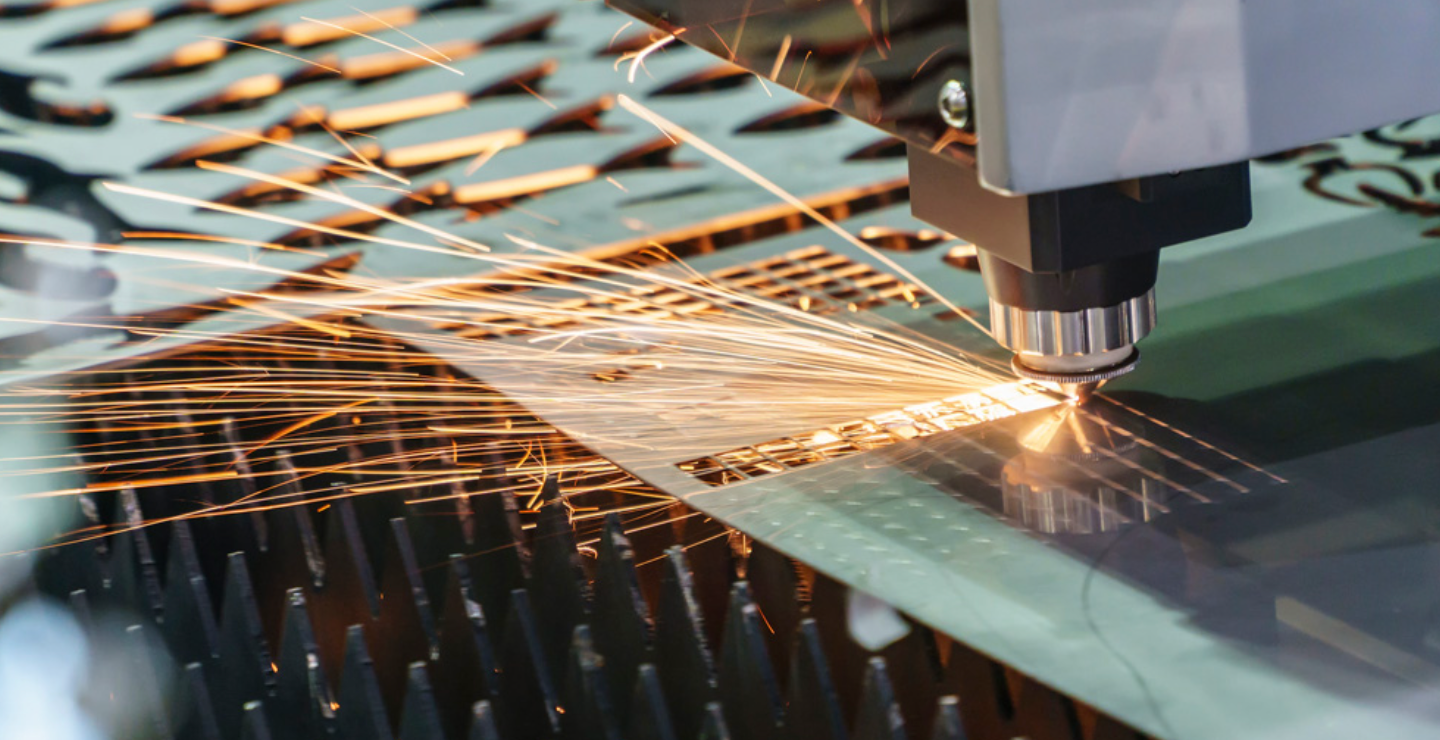
Optimize Your Cutting Equipment
Utilizing the right cut-off wheel is crucial to ensure less wheel wear, avoid overheating and thermal damage, and maintain efficient cut-off wheel performance. Consider upgrading to a premium cut-off wheel if you’re working with tough materials, as they are designed to withstand more challenging conditions and improve longevity.
Implement a Cutting Strategy
Plan your cuts to maximize the use of materials and minimize waste. Use special automatic cutting modes if your cut-off machine has them. These modes often optimize the feed speed and cutting wheel movement to provide the best performance.
Practice Good Maintenance
Regular servicing of your cut-off machines prevents unexpected breakdowns and ensures optimal performance. This includes checking for cut-off wheel deflection, correctly calibrating the machine, and replacing worn-out components.
Ensure Optimal Feed Speed
The feed speed significantly affects the cut-off wheel wear and overall efficiency. Experimenting with different speeds can help determine the optimal feed speed for your particular process and materials, reducing wheel wear and improving overall productivity.
Educate Your Team
Well-trained operators can significantly improve the efficiency of cut-off machines. Regular training programs are highly recommended to keep your team updated on best practices and safety standards.
Invest in Customized Clamping Tools
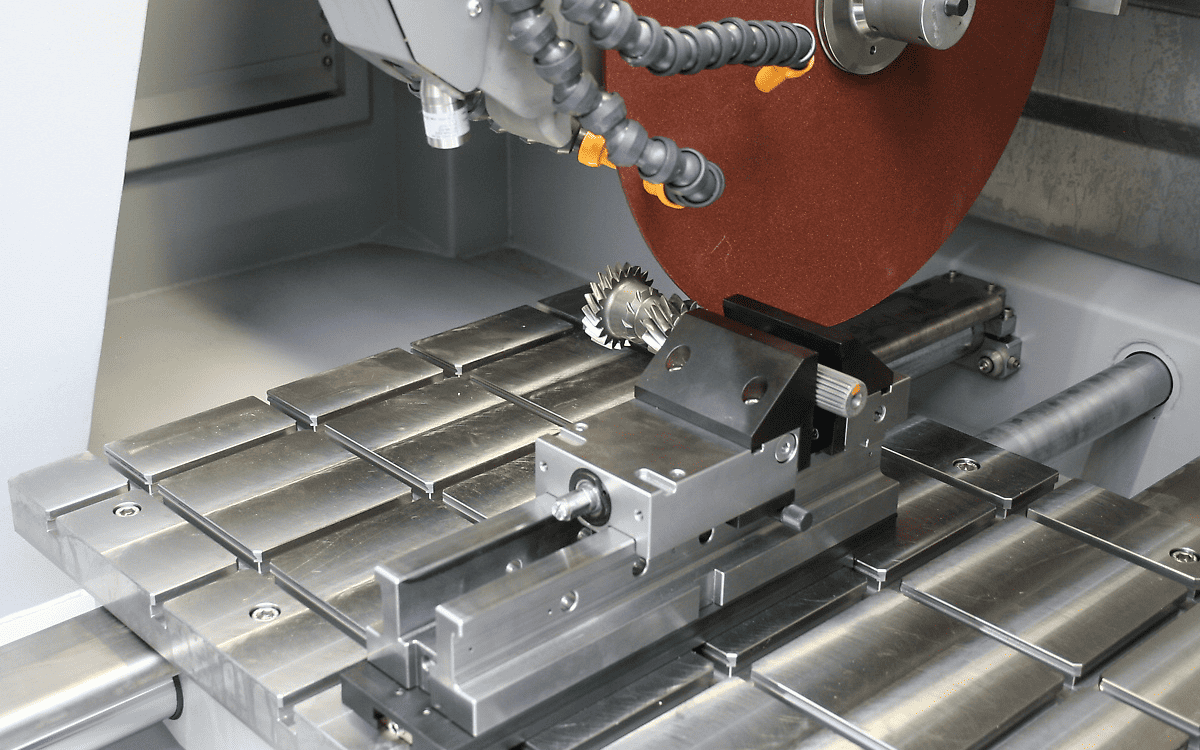
Spending time clamping large workpieces can be significantly reduced.
How? A Customized clamping tool saves you both time and money. Hence, always make sure you use the right clamping tools for the job, especially when dealing with large contact surfaces.
Use the Correct Cut-Off Machine
Not all cut-off machines are created equal. Make sure to use the correct machine for the type of material and cut you’re making. For example, plane grinding might be more effective for some materials and cuts.
Reduce Overheating
Overheating can lead to thermal damage and a reduction in cut-off wheel performance. Ensuring your cut-off wheel moves at the right speed can reduce overheating, prolonging the wheel’s lifespan and ensuring clean, accurate cuts.
Tips in the Process of Cutting Large Pieces
When cutting large pieces, being strategic can save you time and material and reduce risks. Here are some tips to help you streamline the process:
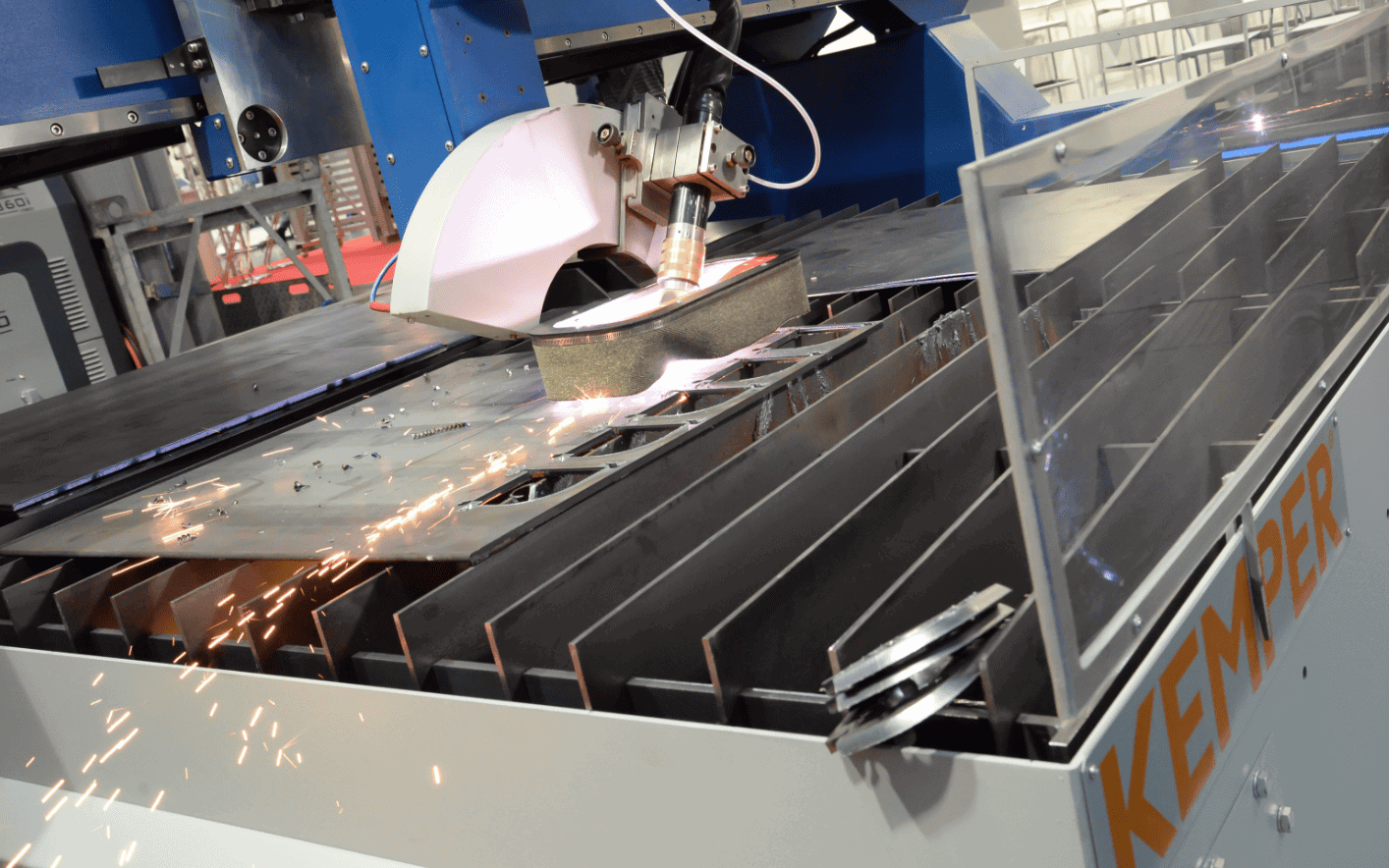
- Plan Ahead: Before you make the first cut, plan your cuts ahead. This minimizes the risk of errors, reduces waste, and can even save time in the long run.
- Use the Right Tools: Ensure that you use the correct cut-off machine and wheel for your task. Using the wrong cut-off wheel or machine can lead to inefficient cuts and even damage to your tools and workpiece.
- Consider Using a Jig or a Template: A jig or a template can ensure consistency and accuracy for repetitive cuts or complex shapes. This improves efficiency and ensures that every piece is cut perfectly.
- Use Appropriate Safety Measures: Cutting large pieces can pose safety risks. Always wear appropriate safety gear, and ensure that the cut-off machine is in good working order before use.
- Monitor the Process: Keep a close eye on the cut-off wheel wear and the overall process. Monitoring can help you spot issues early, allowing you to adjust your process and avoid potential problems.
By following these tips, you can significantly improve the process of cutting large pieces, ensuring efficiency, accuracy, and safety in your operations.
Types of Large Pieces
In the vast world of manufacturing and construction, large pieces come in a variety of materials, each presenting unique challenges and opportunities when it comes to cutting. Let’s delve into some commonly encountered types:
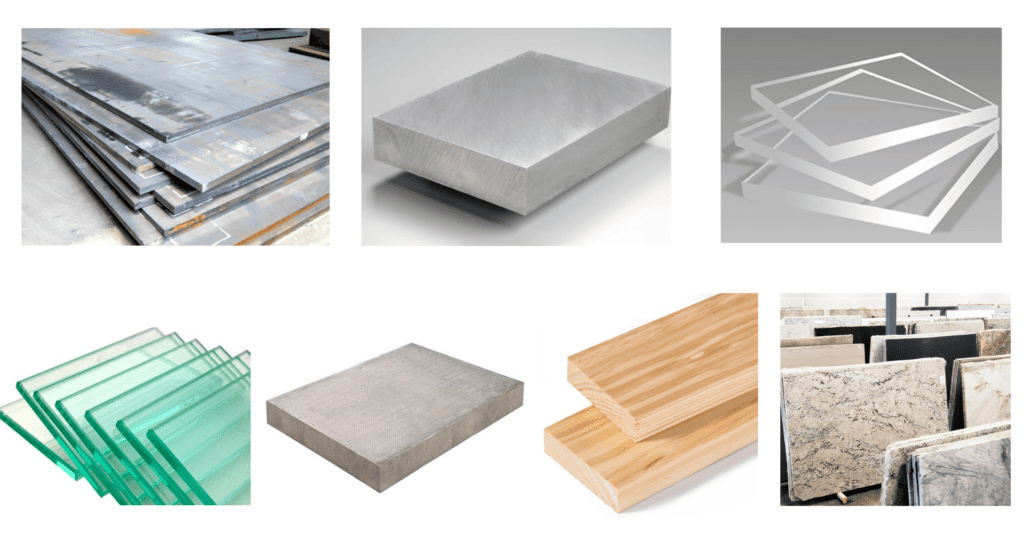
- Steel Plates: Renowned for their strength, steel plates require a cutting wheel that can withstand the hardness of the material. Ensure optimal feed speed to prevent overheating and thermal damage.
- Aluminum Sheets: While softer than steel, aluminum sheets can be tricky. It is crucial to choose the right cut-off wheel and ensure it doesn’t wear too quickly.
- Plastic Sheets: These require a different approach. Too much heat can melt the material, so a premium cut-off wheel that produces less heat is often a wise choice.
- Glass Panels: Precision is the name of the game when cutting glass. The wrong cut-off wheel could lead to breakages, making this a task that requires meticulousness.
- Concrete Slabs: These tough materials require a robust cut-off machine and cut-off wheel, capable of withstanding concrete’s rough and abrasive nature.
- Wood Planks: A staple in construction and woodworking, wood planks can be cut easily with many cut-off machines. However, the correct cut-off wheel must be chosen to prevent splintering and rough edges.
- Marble Slabs and Granite Slabs: Both of these stones are very hard materials. They demand a cut-off wheel that can handle their toughness without wearing out too quickly or causing unwanted chipping.
How to Choose a Cutting Machine to Improve the Process of Cutting Large Pieces
Selecting the right cutting machine is critical to improving efficiency and quality in the process of cutting large pieces. Let’s delve into key considerations that can help guide this significant decision:
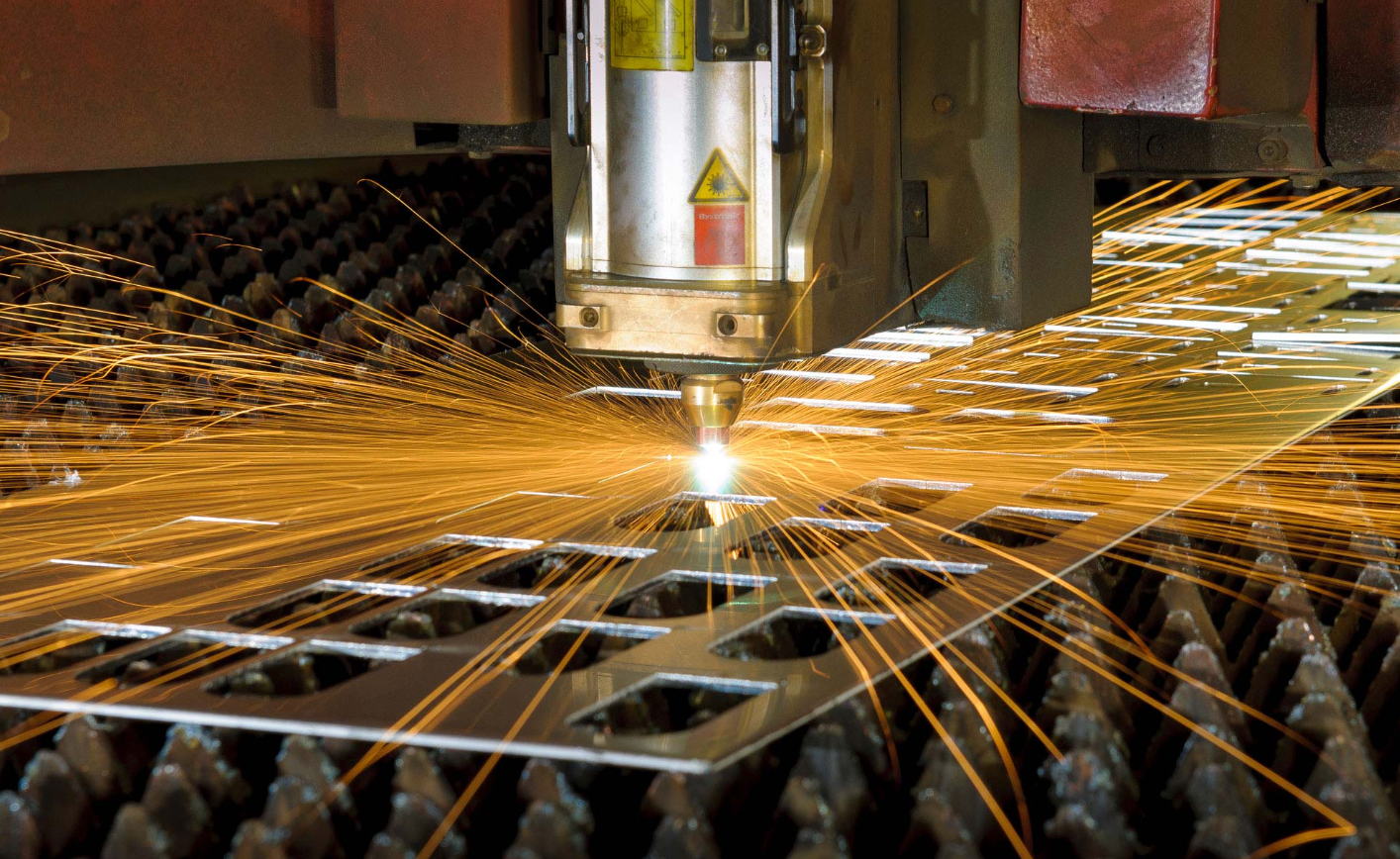
Type of Material
The type of material to be cut is the first consideration. For instance, a waterjet cutter would be perfect for very hard materials like granite slabs, while a plasma cutter would be more suitable for cutting steel plates.
Size of Material
The size of the pieces to be cut should align with the machine’s capacity. For large pieces, a machine with a larger bed size, such as a table saw or a CNC machine, may be preferable.
Desired Accuracy
If the project requires high precision, a laser cutter or wire EDM machine, known for its precise cuts, might be the best choice.
Production Speed
For businesses focusing on high production volumes, it’s important to consider the machine’s cutting speed. Here, laser cutters often excel, as they can maintain high feed speeds without compromising cut quality.
Cost
The initial cost of the machine, ongoing maintenance costs, and the cost of consumables (such as cut-off wheels) are all important financial considerations. A conventional cut-off machine might be cost-effective for a small business, while a larger company might opt for a more expensive but higher-performing model.
Ease of Use
The complexity of operation can impact efficiency and safety. Machines with special automatic cutting modes can simplify the process and minimize the potential for errors.
Remember, there is no one-size-fits-all solution when it comes to choosing the right cutting machine. Understanding your specific needs and circumstances will help you make an informed decision that can significantly enhance your cutting process.
Q&A: Common Questions about Improving the Process of Cutting Large Pieces
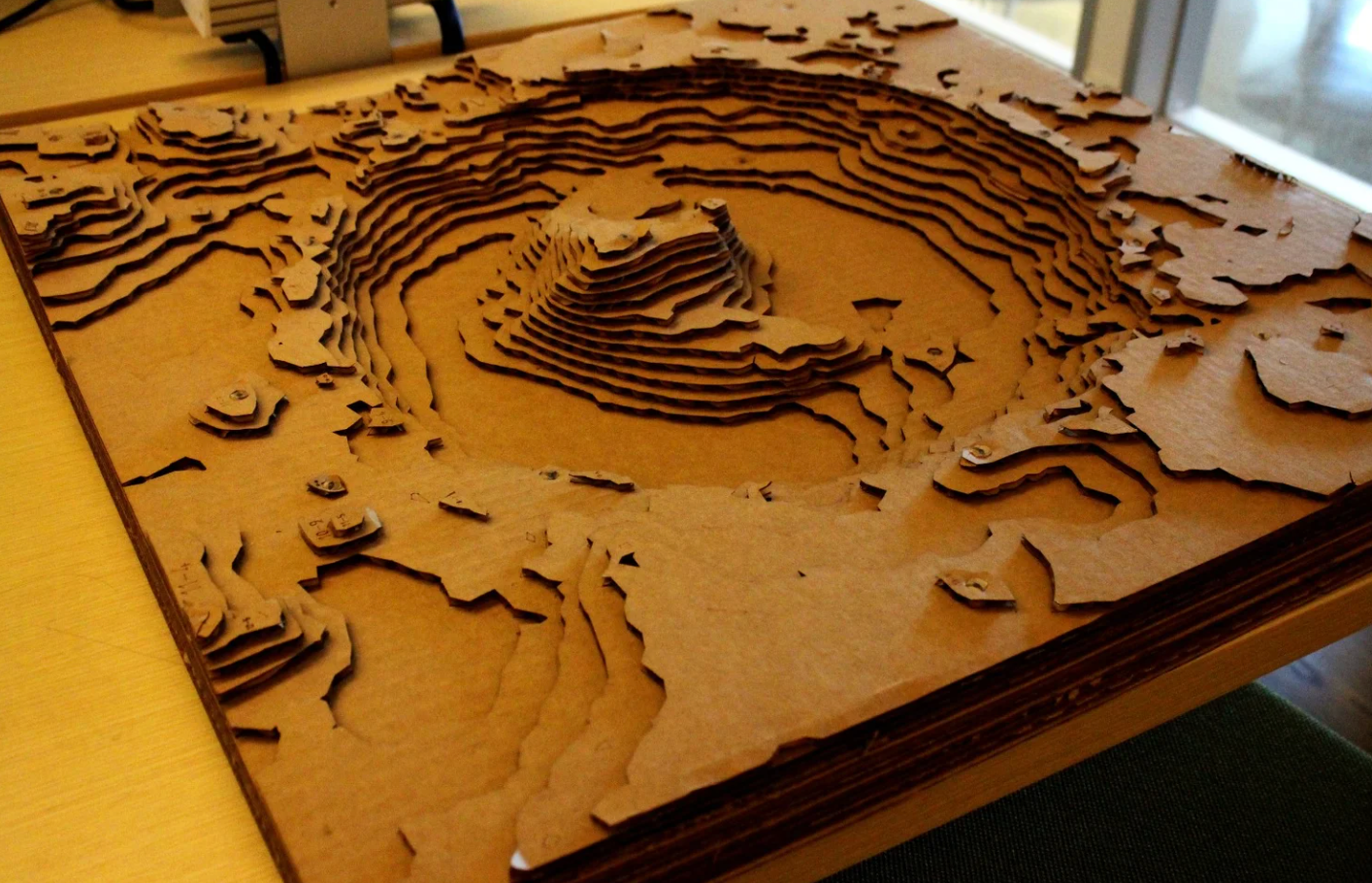
Q: How can I reduce cut-off wheel wear?
Ensure optimal feed speed, and select your material’s cut-off wheel. A premium cut-off wheel can handle harder materials and offer less wheel wear. Maintenance and proper usage also prevent premature wear.
Q: How can I prevent wrong cut-offs in large pieces?
Implement a clear-cutting strategy, ensure the correct cut-off machine is used, and verify measurements before cutting. Customized clamping tools can also save from making wrong cuts, especially for large pieces.
Q: Can cut-off wheel deflection affect my large piece cuts?
Yes, cut-off wheel deflection can cause inaccurate cuts. Using a harder cut-off wheel and ensuring your machine is properly aligned can help to mitigate this issue.
Conclusion
This comprehensive guide explored the ins and outs of cutting large pieces, emphasizing the importance of precision, efficiency, and safety. As we’ve seen, selecting the right tools and strategies is crucial for success, which lies in balancing cost, efficiency, and accuracy. For more insights, feel free to explore other resources on our website, where our commitment lies in empowering your business journey with valuable knowledge.
Discover Your Ideal Cutting Solution with Baison Laser
Unearth the perfect cutting technology for your large piece processing needs with Baison Laser in just one click. With a dedication to precision, efficiency, and smooth operation, our laser cutting machines can handle various materials from metals to plastics, ensuring perfect cuts every time. Ready to transform your manufacturing process? Request an Instant Quote today. Or, if you’re still deciding, experience the superb quality of our machinery first-hand with our Free Sample Proofing.