Are you looking for a welder robot manufacturer that fits your requirements? Are you interested in finding out who the market leaders of this industry are? Then you are in luck! This informative article will unveil the top 10 welding robot manufacturers in the world for 2024, each a titan in their own right, ready to forge your path to success.
An Overview of Industrial Welding Robots
Industrial welding robots are six-axis articulated arms equipped with welding torches and sensors. They are programmed to follow specific weld paths and execute precise motions, ensuring consistent and high-quality welds.
According to the International Federation of Robotics, the global industrial robot market is expected to reach USD 71.1 billion by 2026, with welding robots accounting for a significant share, and the Asia Pacific region is the largest market for welding robots, driven by the automotive and electronics industries.
Do You Have Any Questions?
Let Us Solve Your Problem
Top 10 Welding Robot Manufacturers in the World
Here is a table with the top 10 welding robot manufacturers in the world.
Rank | Brand Name | Year Founded | Location | Employee Size |
1 | Fanuc Corporation | 1955 | Japan | 8,256+ |
2 | Kuka | 1898 | Germany | 15,000+ |
3 | Baison Laser | 2004 | Guangdong Province | 500+ |
4 | ABB Robotics | 1974 | Switzerland | 11,000+ |
5 | Yaskawa Global | 1977 | Japan | 13,090+ |
6 | Kawasaki Robotics | 1969 | Japan | 200+ |
7 | Cloos | 1919 | Germany | 950+ |
8 | OTC DAIHEN, Inc. | 1919 | Japan | 500+ |
9 | Hyundai | 1984 | Korea | 500+ |
10 | Comau | 1970 | Italy | 300+ |
This table contains information about the top 10 welding manufacturers in the world. The ranking decision is based mainly on product quality, market share, customer satisfaction, and product variety.
Let’s dive into a brief discussion of the unique selling points of each of these companies. The competition is fierce in the world of industrial robotics companies, with each company having its unique selling points.
But there’s more to the story! Explore to gain a comprehensive understanding of the welding robots manufacturing industry and its key players across the globe.
1. Fanuc Corporation
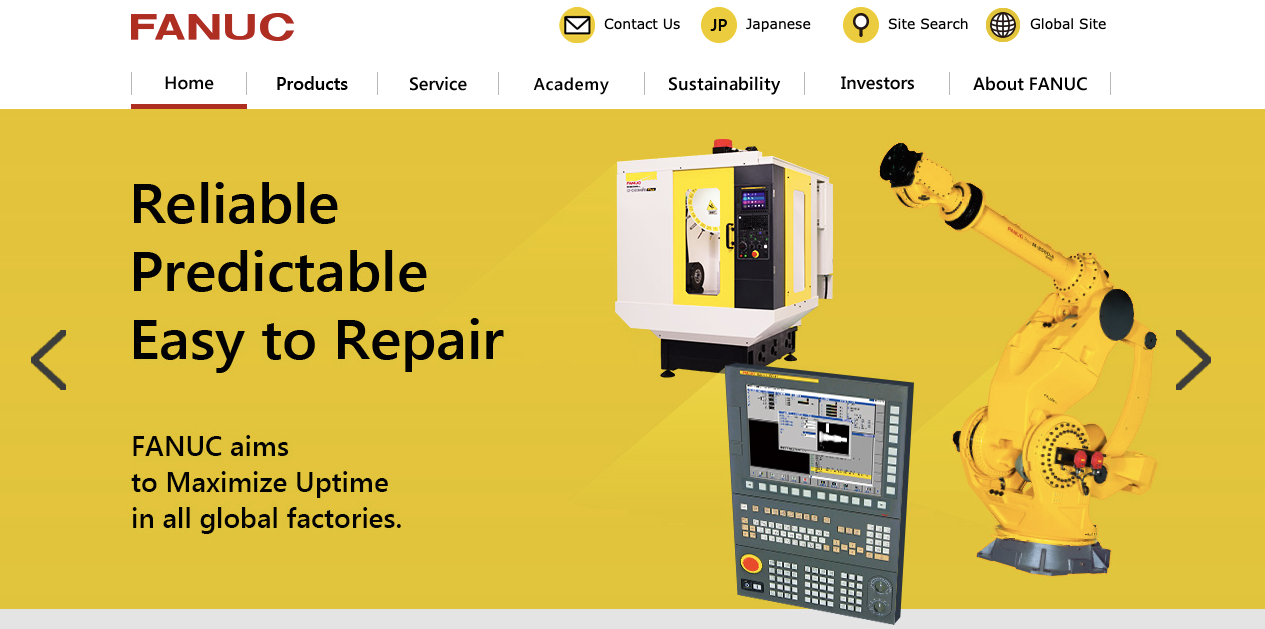
Fanuc Corporation is the name of the leading and most diverse welding robot titan. They started their journey in 1955 in Japan. Today, over 750,000 of their industrial robots hum in factories worldwide, claiming a 40% market share.Fanuc isn’t just about machines; they offer a complete welding solution, from design to maintenance.
They are famous for their diverse portfolio. The nimble ARC Mate series tackles small jobs, while the M-710iC conquers heavy-duty tasks. Robots like the R-2000iA handle arc welding, Fanuc lasers, spots, and even plasma cuts. From Harley-Davidson hogs to Boeing Dreamliners, these robots shape the products we use daily.
Funac is constantly innovating, integrating AI and sensors, paving the way for even smarter, more adaptable robots. They also have a global service network system that ensures customers’ investments and trust in them.
Pros
- High-quality products.
- Excellent customer service.
- Wide range of products.
Cons
- Expensive products.
- Limited customization options.
2. Kuka
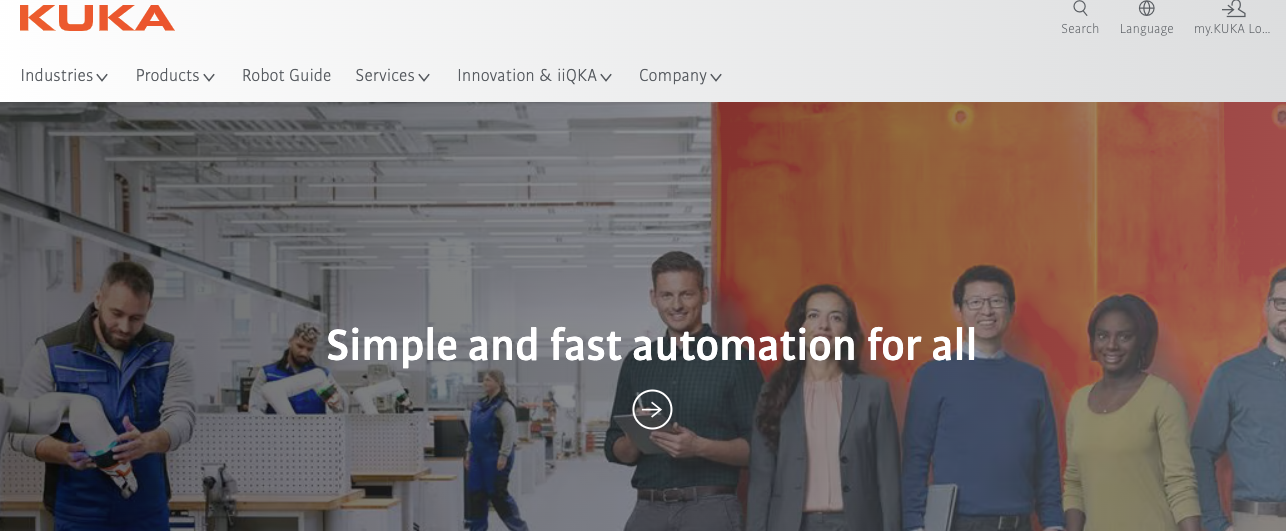
Kuka is a German robotics giant established in 1898, making it a pioneer in the field of industrial robotics companies. Their robots are known for their precision, speed, and reliability, consistently exceeding industry standards.
While Kuka excels in welding robots, they also offer a diverse range of robots for various industrial applications, including material handling, painting, and assembly. Kuka has a robot to suit every need, from the nimble KR Agilus series, perfect for intricate work in tight spaces, to the heavy-duty KR QUANTEC robots capable of handling massive payloads.
Kuka’s robots are at home in diverse industries, including automotive, aerospace, and construction. They focus on areas like artificial intelligence and sensor technology. They also offer a comprehensive range of after-sales services, including maintenance and training.
Pros
- Unmatched performance.
- Diverse product range.
- Comprehensive customer care support.
- Industry expertise.
Cons
- Premium price range.
- Complex programming.
3. Baison Laser
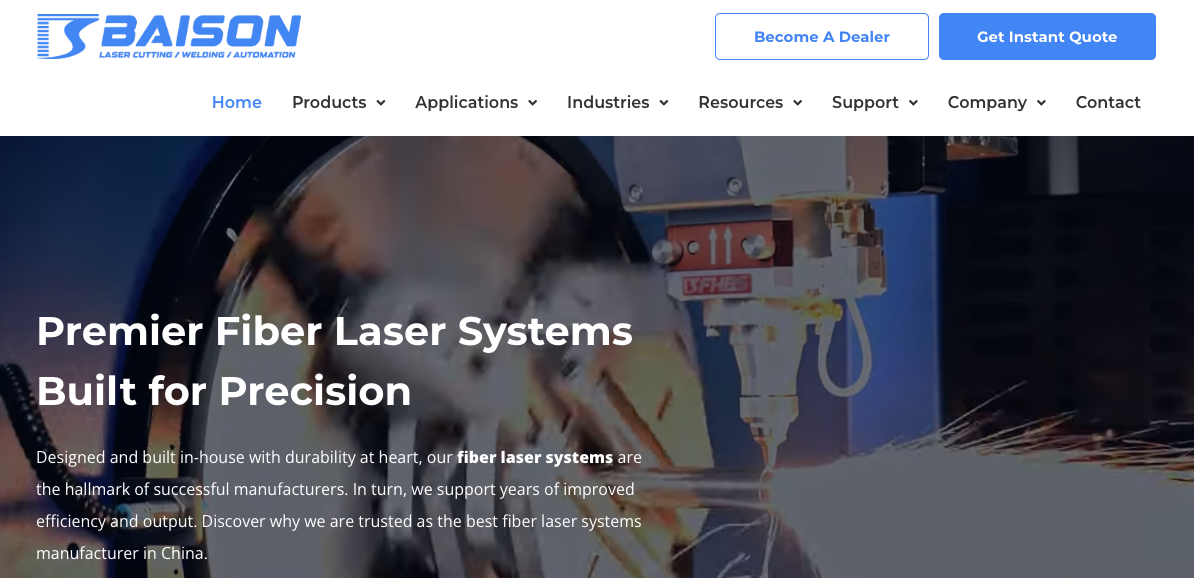
Baison Laser is a professional manufacturer engaged in the research, production, sale, and service of laser equipment that started operating in 2004. We are located in Guangdong Province, China. We have more than 500 employees working at their facility with as many as 300+ numbers of patents. Our factory incorporates sheet metal fabrication, a beam milling workshop, a spray painting workshop, and an assembly workshop.
Handheld welding machines and laser cutting machines are Baison’s primary products. Our fully articulated robots ensure repeatable precision welding on any scale required.
The product categories offered by the company include more than 60 models and include laser engraving, cutting, welding, and cleaning. Baison Laser’s welding robots might be designed to handle a variety of materials and complex welding tasks, suitable for industries like electronics, automotive, and aerospace.
Pros
- Innovative product designs.
- High-quality products.
- Provides customer training.
- Easy to get a quote.
- Wide range of applications.
- Affordable and long-lasting.
Cons
- Limited Marketing and Outreach.
4. ABB Robotics
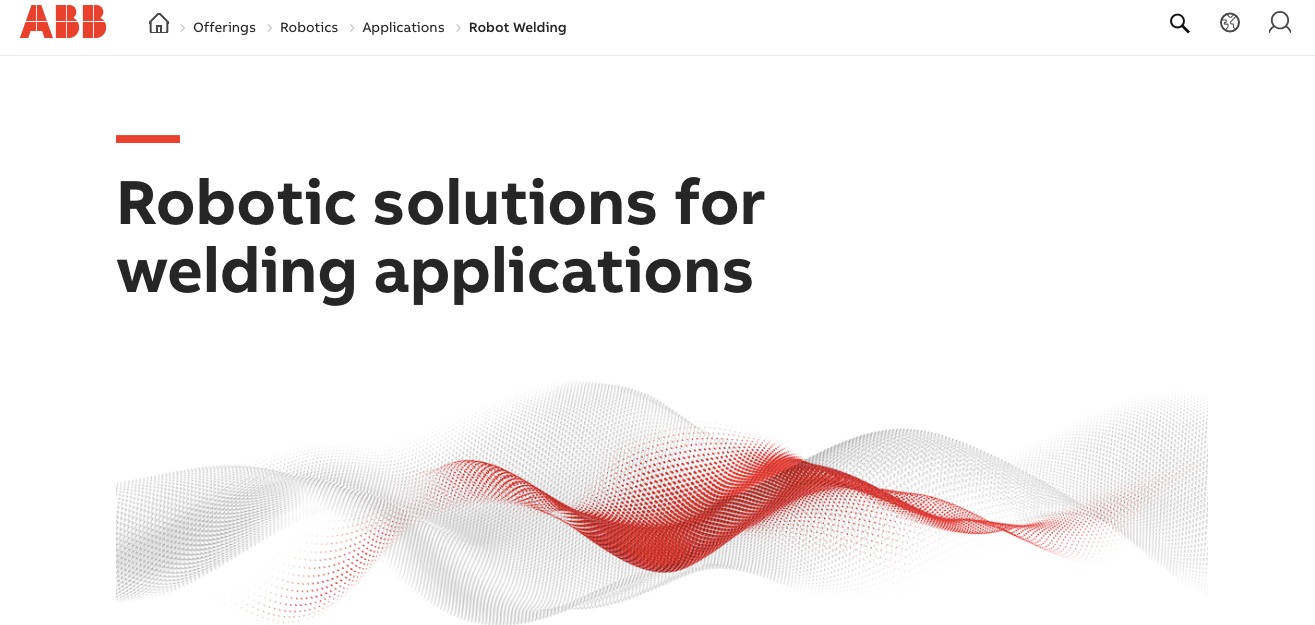
ABB Robotics is located in Zurich, Switzerland. They are the company that created the first industrial robot in history back in 1974. They also offer the widest range of robot technologies, products, and services. They offer a comprehensive suite of welding solutions, encompassing power sources, sensors, software, and application expertise.
ABB Robotics is now concentrating on the study and advancement of mobile robots, automation manufacturing, and electric power technologies.With decades of experience in robot R&D, manufacturing, and technical support, ABB Robotics has installed around 300,000 robots globally.
Pros
- High precision.
- User-friendly programming.
- Extensive product range.
Cons
- Focus on high-end solutions.
- Complex software licensing procedure.
5. Yaskawa Global
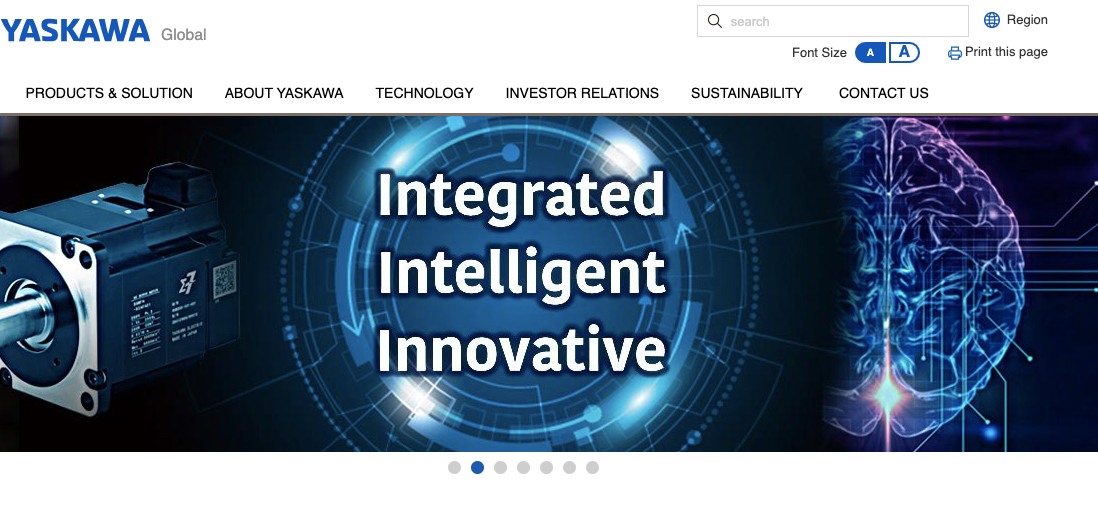
Under the MOTOMAN brand, Yaskawa introduced the first all-electric industrial robot in Japan in 1977. Since then, they have supplied close to 500,000 units worldwide. Around the world, more than 2.7 million industrial robots work not only as welding robots but also to produce cars, home appliances, PCs, smartphones, and other items in factories and other locations that are not often encountered in daily life.
Yaskawa is pushing i³-Mechatronics as an idea for a solution to bring about a new industrial automation revolution in response to developments like Industrie 4.0, IoT, and artificial intelligence (AI). Their product lineup includes arc welding robots, spot welding robots, collaborative robots, laser machining robots, and deburring robots.
Pros
- Offers optimum robotic structures and functions.
- Improved productivity.
- Fast and efficient process.
Cons
- Expensive products.
- Complexity of software.
6. Kawasaki Robotics
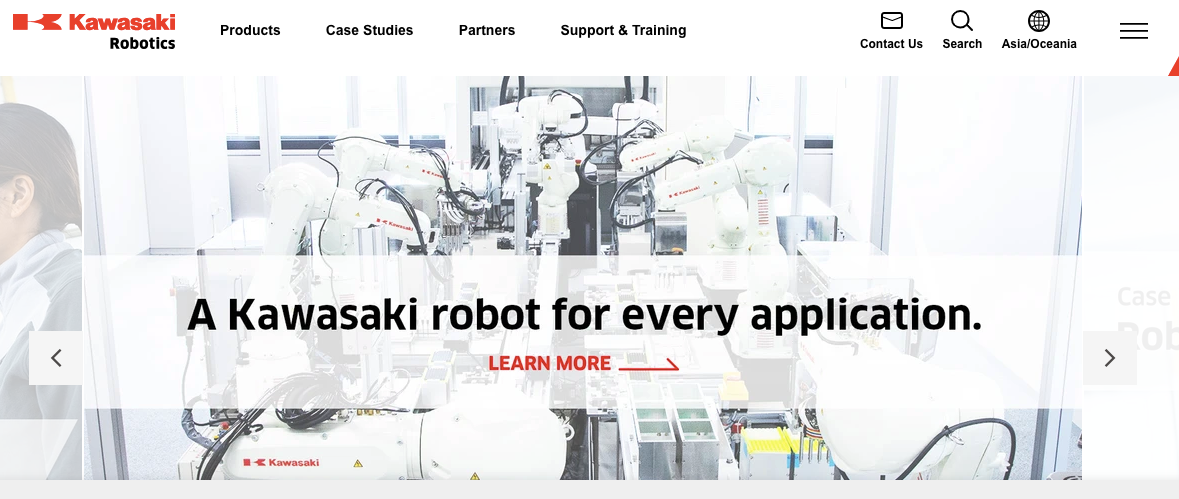
Since 1969, when Kawasaki Heavy Industries launched the first industrial robot in Japan, they have maintained their position as one of the world’s top robot producers while also advancing the automotive and other industries both domestically and internationally. Their manufacturing sectors include engines, motorbikes, aerospace equipment, industrial robots, and many more. With over 45 years of experience in robotics research and development, Kawasaki has installed over 120,000 robots globally.
Kawasaki’s arc welding robots are divided into two series, the BA series and the RA series. While the BA series involves a built-in welding cable and connection with a single cable between the robot and the welder, the RA series has a full lineup for a wide range of workpieces and an easy one-cable connection between the robot and welding equipment.
Pros
- Easy accessibility.
- High-quality products.
- Supportive customer care team operating globally.
Cons
- Focus on specific industries, such as automotive and metalworking industries.
- Limited customization options.
7. Cloos
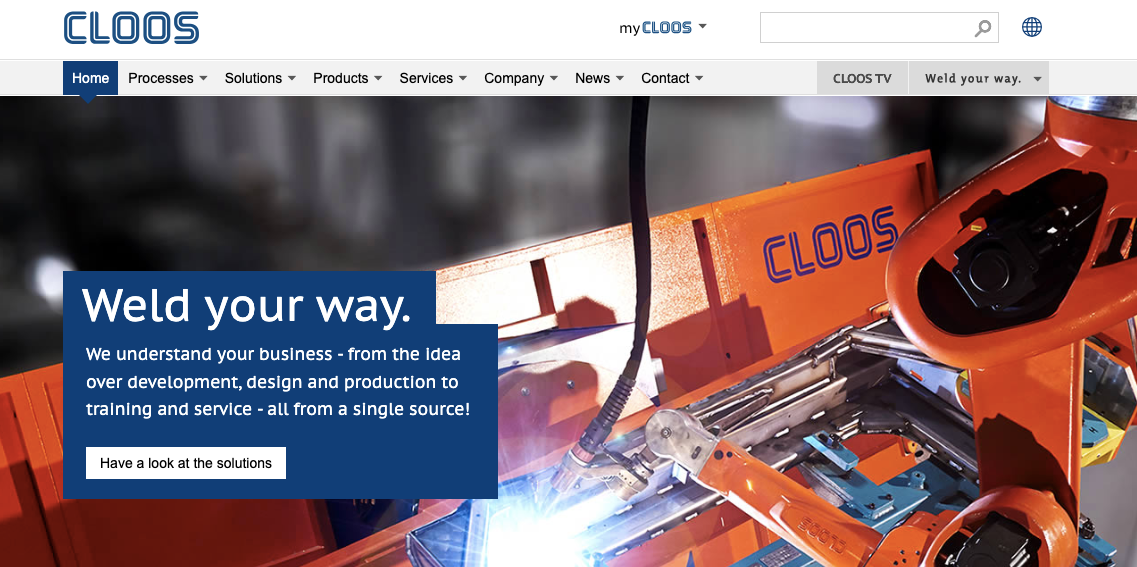
Cloos was founded in 1919 by Eng. Carl Cloos. They have a glorious history of over 100 years operating in more than 40 countries worldwide.
Their product portfolio includes the whole range of arc welding technology with the QINEO, the next generation of welding machines for both manual and automated applications, and QIROX, the automated welding and cutting system. Their product line consists of sensors, safety technology, industrial automation systems, and intelligent software solutions, all of which can be tailored according to your demands.
Cloos’ welding robots are versatile and can be used for a variety of welding processes, including MIG/MAG, TIG, and laser welding, catering to a wide range of industries from automotive to heavy machinery.
Pros
- Superior quality.
- Customized products.
- High level of engineering competence.
- High level of global service quality.
Cons
- Expensive.
- Need expert assistance.
- Complex process.
8. OTC DAIHEN, Inc.
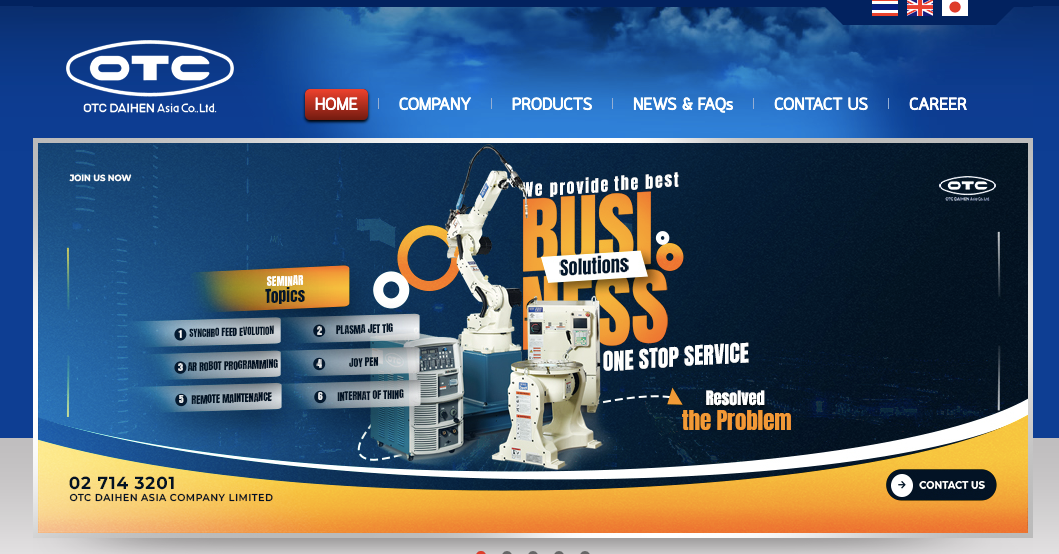
OTC Daihen was founded in 1919 in Osaka, Japan. OTC robots are used in a variety of industries, including automotive, aerospace, and shipbuilding. OTC Daihen focuses on creating systems that are easily integrated into existing manufacturing processes. Their robots can be seamlessly incorporated into existing production lines, enhancing efficiency without significant disruptions.
Their main products include arc welding robots, spot welding robots, laser welding robots, and material handling robots. The company’s robots are known for their quality, reliability, and precision. OTC also offers a wide range of services to its customers, including installation, training, and maintenance.
Pros
- High quality.
- Affordable prices.
- On-time delivery.
Cons
- Limited options for customization.
- Frequent and costly maintenance.
9. Hyundai
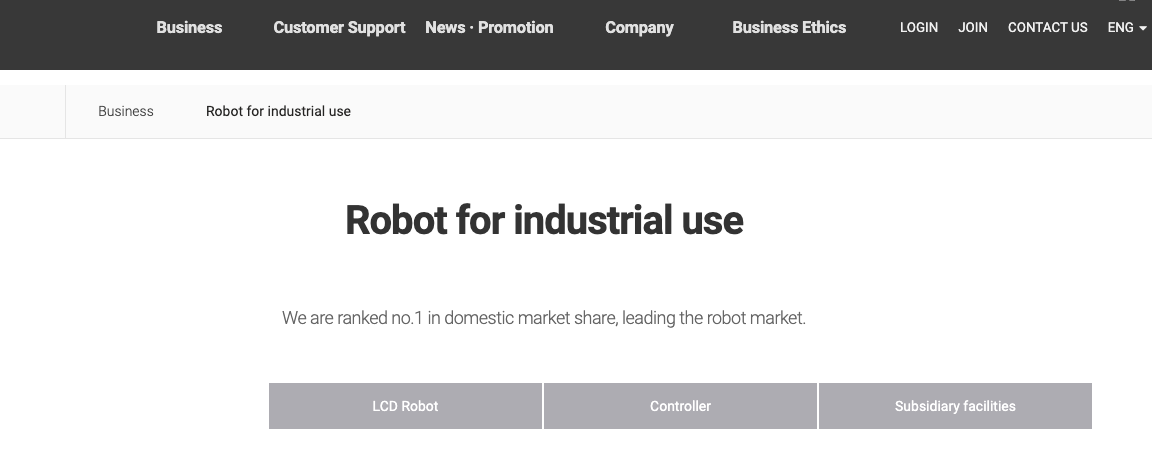
In 1984, Hyundai Heavy Industries conducted independent research and development to create the most advanced industrial robots in the world. The company has been granted several essential patents related to automation systems. Hyundai offers a large selection of robots for production processes and automated material loading, handling, sealing, robotic arc, and spot welding.
Known for their durability, Hyundai’s welding robots are designed to withstand the rigors of industrial environments, ensuring long-term reliability and consistent performance. In 2021, they introduced Construction Robotics Technology, which includes both anchor ring automation robots and field patrol robots.
Pros
- High-quality products.
- Globally connected customer care services.
- Encourages sustainable energy ecosystem.
- Incorporation of green ocean energy with electrification technology.
Cons
- Expensive products.
- Not easily accessible.
- Need expert knowledge for handling the products.
10. Comau
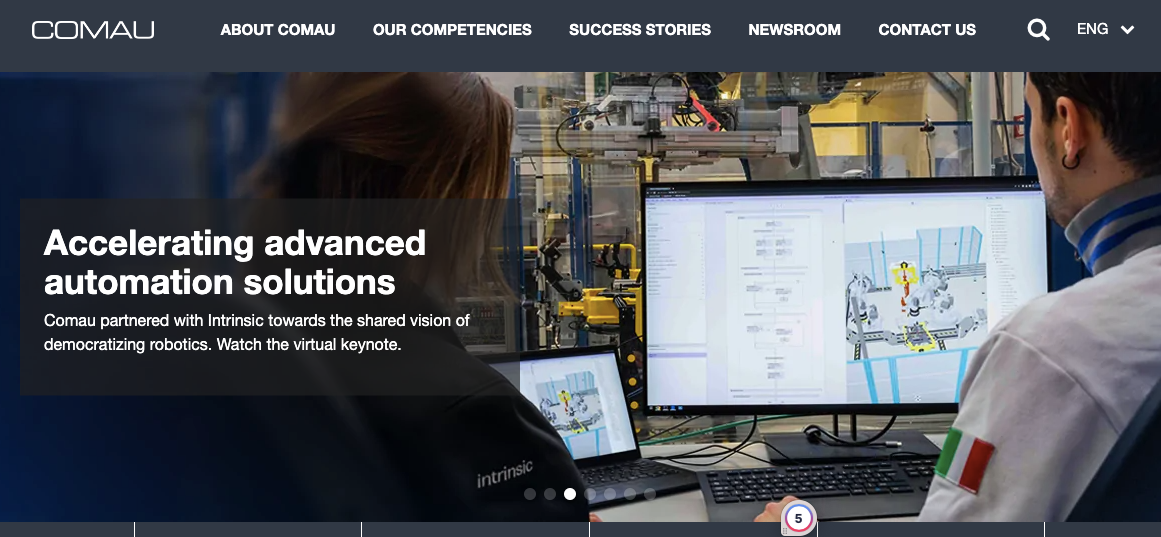
Comau began its journey in 1970 as the Consorzio Macchine Utensilias. During the 1990s, they started expanding globally. Today, they are driving innovation and excellence into the factories of the future with their products HUMANufacturing, which is supposed to be a collaborative path to Industry 4.0.
A story that begins with the introduction of the robotics industry and progresses through the technologies of the 1980s and 1990s, which enabled Comau to usher in a more sophisticated and adaptable era of automation. From the successful worldwide expansion that brought their business into the new millennium to the creation of ever-more-intriguing systems and products to the latest cutting-edge robotics, digital, and e-mobility solutions.
Pros
- Industry 4.0-enabled solutions with real-time data transfer.
- Easy to use products.
- Innovative and sustainable products.
Cons
- No customization options are available.
- High product and process cost.
- Advanced robotics technology is not suitable for everyday use.
Do You Have Any Questions?
Let Us Solve Your Problem
Emerging Trends in Welding Robotics
It is now much simpler to use robotic welding technology to help with everyday tasks with the help of the most recent advancements in the field. Here are three emerging trends in the welding robotics industry that influence better production and efficacy.
1. Automated Sensing
Robotic welders can adjust their operations based on the size of each particular workpiece with the help of automated sensing technologies. As a result, output is increased, and each weld is of greater quality. This also speeds up welding processes.
2. Real-Time Data Acquisition
Robotic welding systems are rapidly enhancing their operational data-collecting and analysis capabilities in addition to autonomous sensing. These tools enable the validation of the joint strength, weld penetration, and seal of each seam during the weld operation, which is essential for every weld joint to pass the quality control procedure.
3. Integration Processes
Welding robots are frequently used directly on production lines, where quality checks upstream and inspections downstream are important to the process. To maintain production line productivity, modern robotic welding systems must be integrated with other information management systems. Operators can increase productivity and minimize poor welds to downstream operations by integrating the component transfer systems with the weld cells.
Final Thoughts
In conclusion, the top 10 welding robot manufacturers of 2024 are leading the way in the rapidly evolving welding technology sector. Their advancements in efficiency, precision, and innovation are significantly influencing the industry.
As automated and advanced manufacturing becomes more prevalent, these companies play a crucial role. Industries like automotive, aerospace, and construction will benefit from keeping abreast of these leaders to stay competitive. Looking ahead, it’s exciting to see how these manufacturers will continue to innovate and shape the future of welding.
Why Choose Baison Robotics for Your Welding Projects?
Choosing the right laser welding system for your robot welding projects is important for ensuring efficiency, precision, and cost-effectiveness. While there are many options available, the Baison Laser stands out for several compelling reasons. We have been offering the most innovative and reliable products for the last twenty years. Besides, our products are budget-friendly and customizable.
Baison Laser has a strong reputation for quality and customer satisfaction. We provide comprehensive technical support with our team of experienced engineers, who are available to assist you with system selection, installation, training, and ongoing maintenance, ensuring you get the most out of your investment. Feel free to contact Baison Laser if you have any queries.